Page 91 of 396
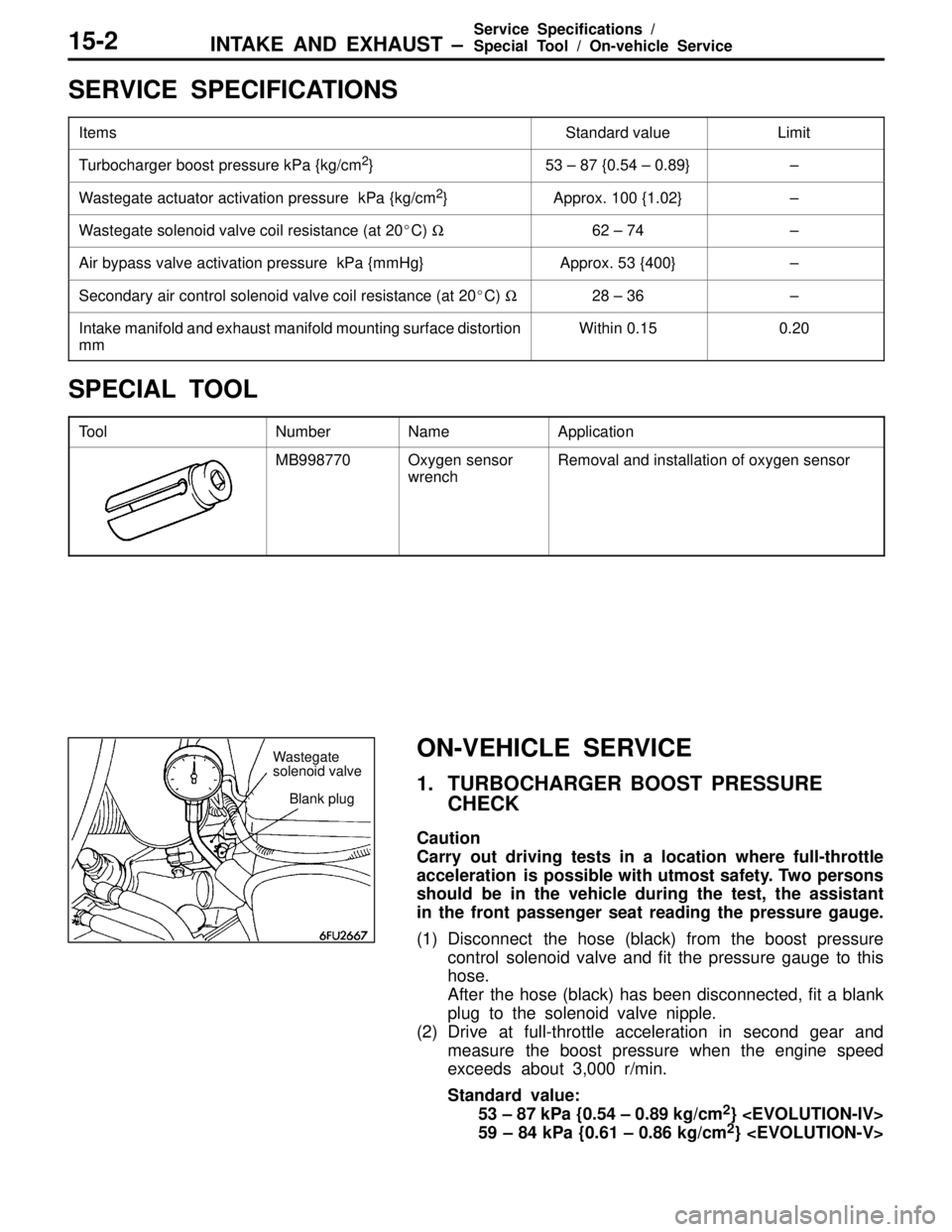
INTAKE AND EXHAUST –
Service Specifications /
Special Tool / On-vehicle Service15-2
SERVICE SPECIFICATIONS
ItemsStandard valueLimit
Turbocharger boost pressure kPa {kg/cm2}53 – 87 {0.54 – 0.89}–
Wastegate actuator activation pressure kPa {kg/cm2}Approx. 100 {1.02}–
Wastegate solenoid valve coil resistance (at 20C) Ω62 – 74–
Air bypass valve activation pressure kPa {mmHg}Approx. 53 {400}–
Secondary air control solenoid valve coil resistance (at 20C) Ω28 – 36–
Intake manifold and exhaust manifold mounting surface distortion
mmWithin 0.150.20
SPECIAL TOOL
ToolNumberNameApplication
MB998770Oxygen sensor
wrenchRemoval and installation of oxygen sensor
ON-VEHICLE SERVICE
1. TURBOCHARGER BOOST PRESSURE
CHECK
Caution
Carry out driving tests in a location where full-throttle
acceleration is possible with utmost safety. Two persons
should be in the vehicle during the test, the assistant
in the front passenger seat reading the pressure gauge.
(1) Disconnect the hose (black) from the boost pressure
control solenoid valve and fit the pressure gauge to this
hose.
After the hose (black) has been disconnected, fit a blank
plug to the solenoid valve nipple.
(2) Drive at full-throttle acceleration in second gear and
measure the boost pressure when the engine speed
exceeds about 3,000 r/min.
Standard value:
53 – 87 kPa {0.54 – 0.89 kg/cm
2}
59 – 84 kPa {0.61 – 0.86 kg/cm2}
Wastegate
solenoid valve
Blank plug
Page 92 of 396
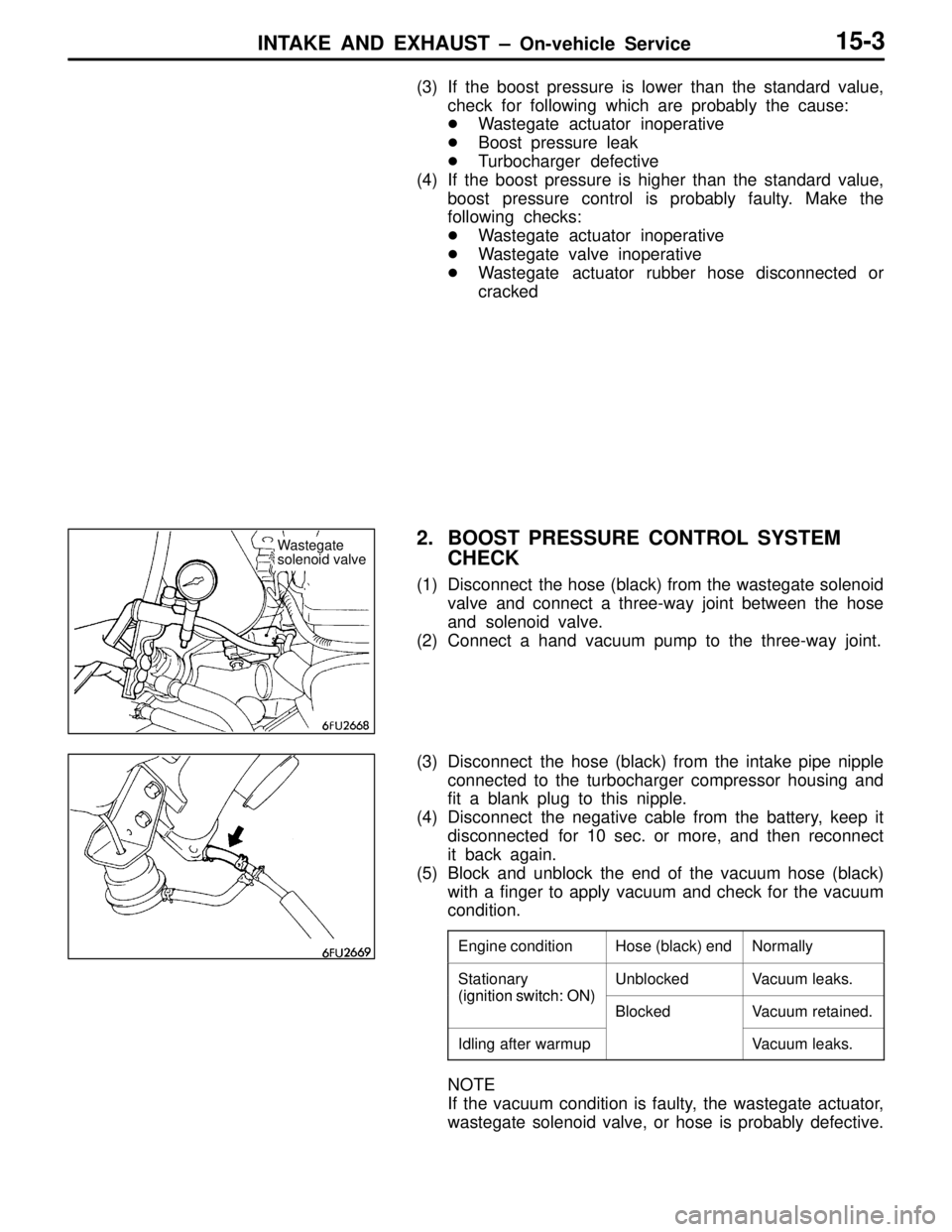
INTAKE AND EXHAUST – On-vehicle Service15-3
(3) If the boost pressure is lower than the standard value,
check for following which are probably the cause:
Wastegate actuator inoperative
Boost pressure leak
Turbocharger defective
(4) If the boost pressure is higher than the standard value,
boost pressure control is probably faulty. Make the
following checks:
Wastegate actuator inoperative
Wastegate valve inoperative
Wastegate actuator rubber hose disconnected or
cracked
2. BOOST PRESSURE CONTROL SYSTEM
CHECK
(1) Disconnect the hose (black) from the wastegate solenoid
valve and connect a three-way joint between the hose
and solenoid valve.
(2) Connect a hand vacuum pump to the three-way joint.
(3) Disconnect the hose (black) from the intake pipe nipple
connected to the turbocharger compressor housing and
fit a blank plug to this nipple.
(4) Disconnect the negative cable from the battery, keep it
disconnected for 10 sec. or more, and then reconnect
it back again.
(5) Block and unblock the end of the vacuum hose (black)
with a finger to apply vacuum and check for the vacuum
condition.
Engine conditionHose (black) endNormally
Stationary
(ignition switch: ON)
UnblockedVacuum leaks.
(ignition switch: ON)
BlockedVacuum retained.
Idling after warmupVacuum leaks.
NOTE
If the vacuum condition is faulty, the wastegate actuator,
wastegate solenoid valve, or hose is probably defective.
Wastegate
solenoid valve
Page 94 of 396
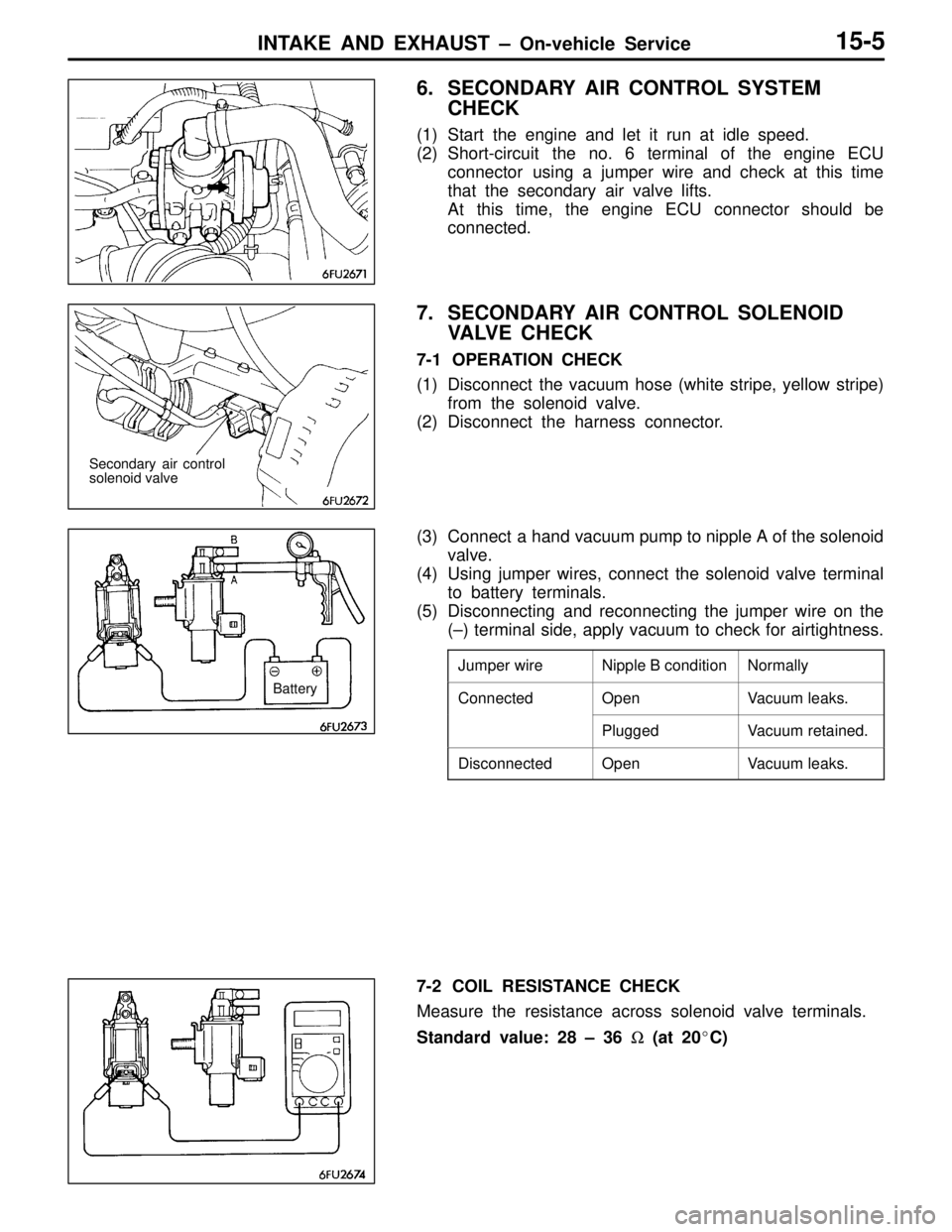
INTAKE AND EXHAUST – On-vehicle Service15-5
6. SECONDARY AIR CONTROL SYSTEM
CHECK
(1) Start the engine and let it run at idle speed.
(2) Short-circuit the no. 6 terminal of the engine ECU
connector using a jumper wire and check at this time
that the secondary air valve lifts.
At this time, the engine ECU connector should be
connected.
7. SECONDARY AIR CONTROL SOLENOID
VALVE CHECK
7-1 OPERATION CHECK
(1) Disconnect the vacuum hose (white stripe, yellow stripe)
from the solenoid valve.
(2) Disconnect the harness connector.
(3) Connect a hand vacuum pump to nipple A of the solenoid
valve.
(4) Using jumper wires, connect the solenoid valve terminal
to battery terminals.
(5) Disconnecting and reconnecting the jumper wire on the
(–) terminal side, apply vacuum to check for airtightness.
Jumper wireNipple B conditionNormally
ConnectedOpenVacuum leaks.
PluggedVacuum retained.
DisconnectedOpenVacuum leaks.
7-2 COIL RESISTANCE CHECK
Measure the resistance across solenoid valve terminals.
Standard value: 28 – 36 Ω (at 20C)
Secondary air control
solenoid valve
Battery
Page 97 of 396
INTAKE AND EXHAUST – Air Control Valve15-8
AIR CONTROL VALVE
REMOVAL AND INSTALLATION
1
Unit: Nm {kgfm}
22 {2.2}
35 {3.6}49 {5.0}
24 {2.4}4 {0.4}10 – 12 {1.0 – 1.2}
4 {0.4}10 – 12
{1.0 – 1.2}
24 {2.4}
22 {2.2}
2
3
8 7 64 5
12 – 15 {1.2 – 1.5}
Removal steps
1. Control harness connection
2. Vacuum pipe hose assembly
3. Air pipe assembly
A4. Gasket5. Air hose
6. Air control valve
7. Engine hanger
8. Air control valve bracket
INSTALLATION SERVICE POINT
AGASKET INSTALLATION
Install the gasket so that its protrusion is located as shown.Protrusion
Page 98 of 396
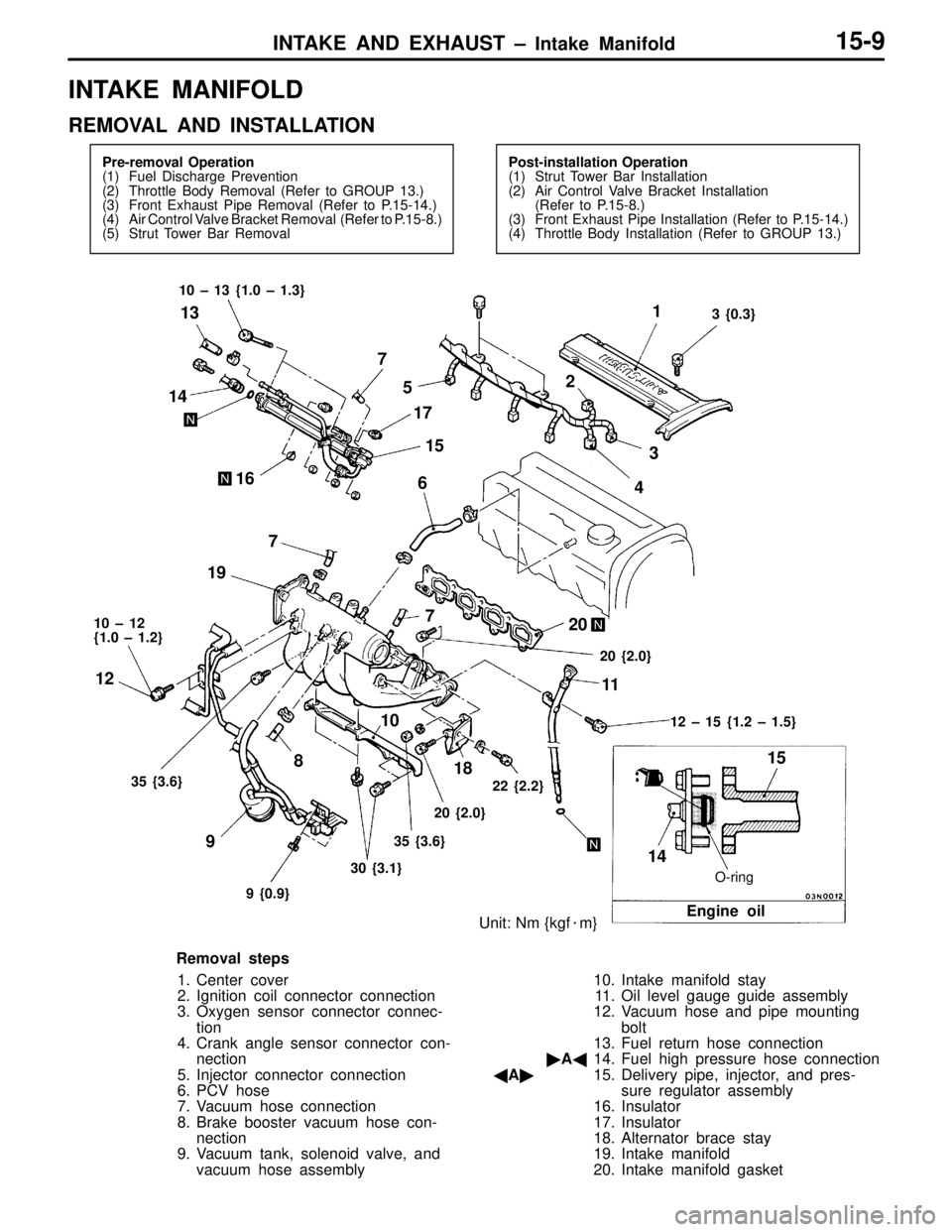
INTAKE AND EXHAUST – Intake Manifold15-9
INTAKE MANIFOLD
REMOVAL AND INSTALLATION
Pre-removal Operation
(1) Fuel Discharge Prevention
(2) Throttle Body Removal (Refer to GROUP 13.)
(3) Front Exhaust Pipe Removal (Refer to P.15-14.)
(4) Air Control Valve Bracket Removal (Refer to P.15-8.)
(5) Strut Tower Bar RemovalPost-installation Operation
(1) Strut Tower Bar Installation
(2) Air Control Valve Bracket Installation
(Refer to P.15-8.)
(3) Front Exhaust Pipe Installation (Refer to P.15-14.)
(4) Throttle Body Installation (Refer to GROUP 13.)
O-ring
Unit: Nm {kgfm}
15
Engine oil
3 {0.3} 10 – 13 {1.0 – 1.3}
10 – 12
{1.0 – 1.2}
12 – 15 {1.2 – 1.5}
35 {3.6}
9 {0.9}30 {3.1}35 {3.6}20 {2.0}22 {2.2}20 {2.0}
14 14
167
5
17
1521
3
4 6
7 7
19
20
18 8
9 12
1011
13
Removal steps
1. Center cover
2. Ignition coil connector connection
3. Oxygen sensor connector connec-
tion
4. Crank angle sensor connector con-
nection
5. Injector connector connection
6. PCV hose
7. Vacuum hose connection
8. Brake booster vacuum hose con-
nection
9. Vacuum tank, solenoid valve, and
vacuum hose assembly10. Intake manifold stay
11. Oil level gauge guide assembly
12. Vacuum hose and pipe mounting
bolt
13. Fuel return hose connection
A14. Fuel high pressure hose connection
A15. Delivery pipe, injector, and pres-
sure regulator assembly
16. Insulator
17. Insulator
18. Alternator brace stay
19. Intake manifold
20. Intake manifold gasket
Page 99 of 396
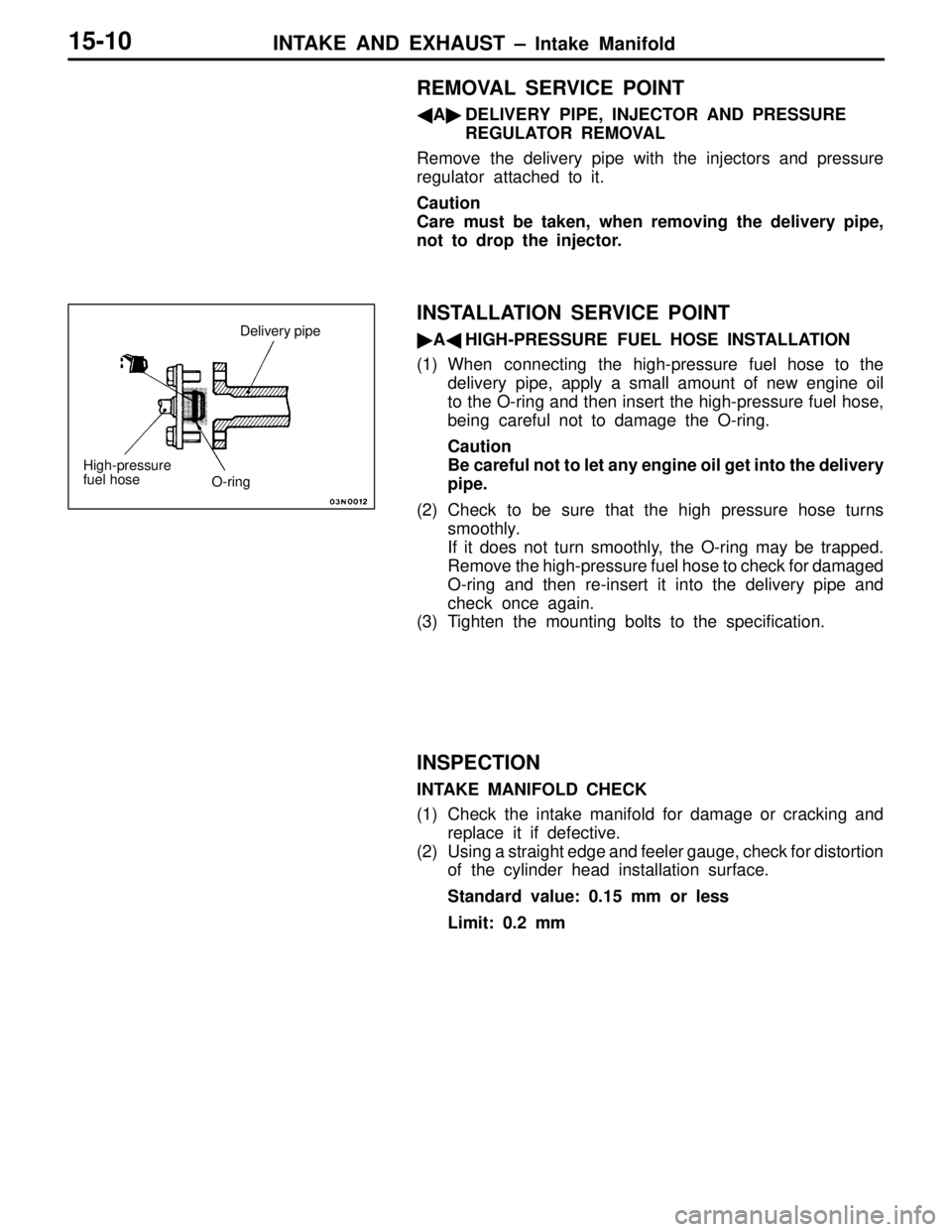
INTAKE AND EXHAUST – Intake Manifold15-10
REMOVAL SERVICE POINT
ADELIVERY PIPE, INJECTOR AND PRESSURE
REGULATOR REMOVAL
Remove the delivery pipe with the injectors and pressure
regulator attached to it.
Caution
Care must be taken, when removing the delivery pipe,
not to drop the injector.
INSTALLATION SERVICE POINT
AHIGH-PRESSURE FUEL HOSE INSTALLATION
(1) When connecting the high-pressure fuel hose to the
delivery pipe, apply a small amount of new engine oil
to the O-ring and then insert the high-pressure fuel hose,
being careful not to damage the O-ring.
Caution
Be careful not to let any engine oil get into the delivery
pipe.
(2) Check to be sure that the high pressure hose turns
smoothly.
If it does not turn smoothly, the O-ring may be trapped.
Remove the high-pressure fuel hose to check for damaged
O-ring and then re-insert it into the delivery pipe and
check once again.
(3) Tighten the mounting bolts to the specification.
INSPECTION
INTAKE MANIFOLD CHECK
(1) Check the intake manifold for damage or cracking and
replace it if defective.
(2) Using a straight edge and feeler gauge, check for distortion
of the cylinder head installation surface.
Standard value: 0.15 mm or less
Limit: 0.2 mm
High-pressure
fuel hoseDelivery pipe
O-ring
Page 100 of 396
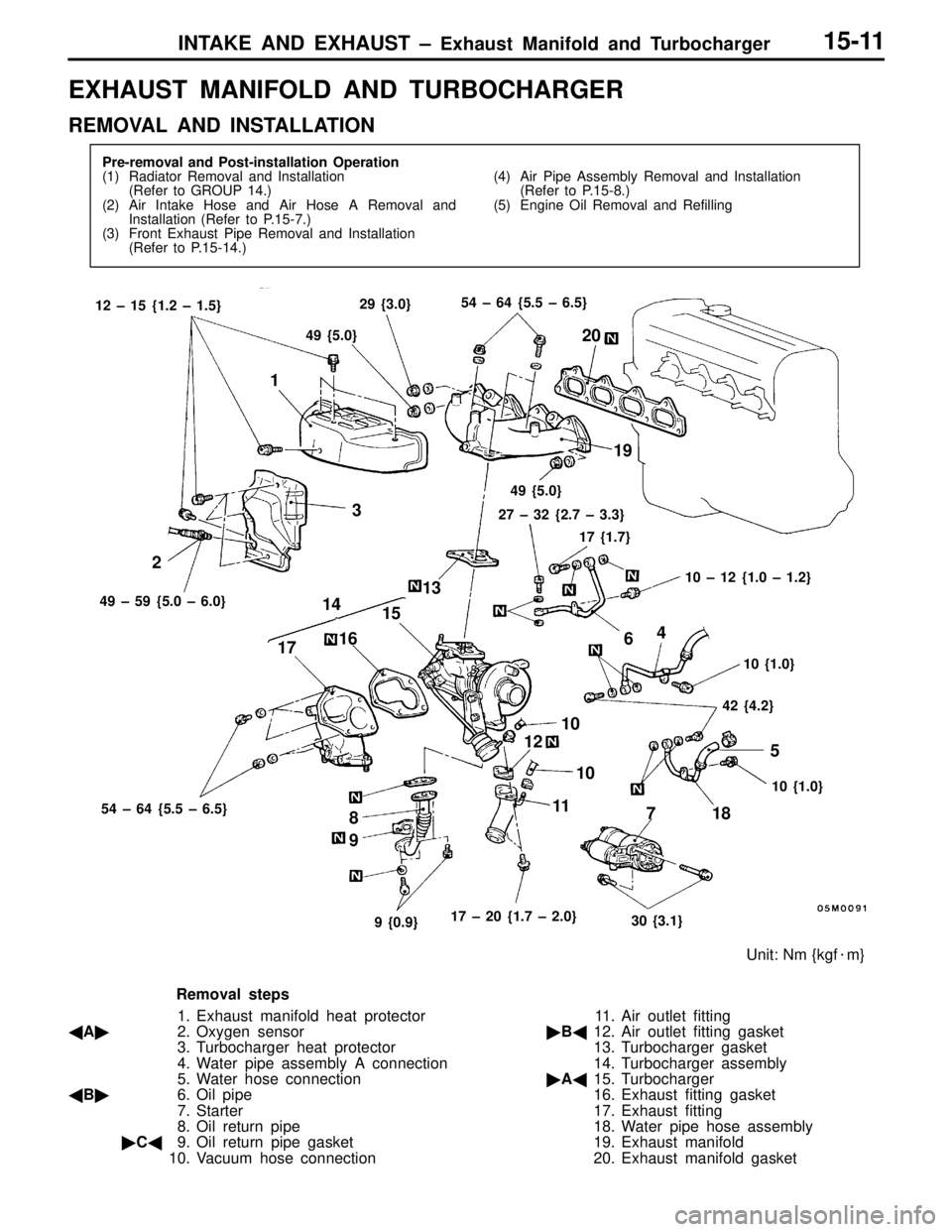
INTAKE AND EXHAUST – Exhaust Manifold and Turbocharger15-11
EXHAUST MANIFOLD AND TURBOCHARGER
REMOVAL AND INSTALLATION
Pre-removal and Post-installation Operation
(1) Radiator Removal and Installation
(Refer to GROUP 14.)
(2) Air Intake Hose and Air Hose A Removal and
Installation (Refer to P.15-7.)
(3) Front Exhaust Pipe Removal and Installation
(Refer to P.15-14.)(4) Air Pipe Assembly Removal and Installation
(Refer to P.15-8.)
(5) Engine Oil Removal and Refilling
1
Unit: Nm {kgfm}
49 {5.0}54 – 64 {5.5 – 6.5}
9 {0.9} 12 – 15 {1.2 – 1.5}
23
4
29 {3.0}
20
49 – 59 {5.0 – 6.0}
54 – 64 {5.5 – 6.5}
30 {3.1} 17 – 20 {1.7 – 2.0}10 {1.0} 42 {4.2}10 {1.0} 10 – 12 {1.0 – 1.2} 17 {1.7} 49 {5.0}
27 – 32 {2.7 – 3.3}
19
6
10
12
10
11
18 7
8
9 171615 1413
5
Removal steps
1. Exhaust manifold heat protector
A2. Oxygen sensor
3. Turbocharger heat protector
4. Water pipe assembly A connection
5. Water hose connection
B6. Oil pipe
7. Starter
8. Oil return pipe
C9. Oil return pipe gasket
10. Vacuum hose connection11. Air outlet fitting
B12. Air outlet fitting gasket
13. Turbocharger gasket
14. Turbocharger assembly
A15. Turbocharger
16. Exhaust fitting gasket
17. Exhaust fitting
18. Water pipe hose assembly
19. Exhaust manifold
20. Exhaust manifold gasket
Page 101 of 396
INTAKE AND EXHAUST – Exhaust Manifold and Turbocharger15-12
REMOVAL SERVICE POINTS
AOXYGEN SENSOR REMOVAL
BOIL PIPE REMOVAL
Caution
After the oil pipe has been removed, ensure that no foreign
matter will get into the oil passage holes in turbocharger.
INSTALLATION SERVICE POINTS
ATURBOCHARGER INSTALLATION
(1) Clean the connections between oil pipe, oil return pipe,
and water pipe.
Caution
Ensure that no foreign matter will get into the
turbocharger.
(2) Through the oil pipe mounting hole in the turbocharger,
add fresh engine oil.
BAIR OUTLET FITTING GASKET INSTALLATION
Install the gasket so that its tab is located as shown.
MB998770
Turbocharger
Ta b