Page 208 of 396
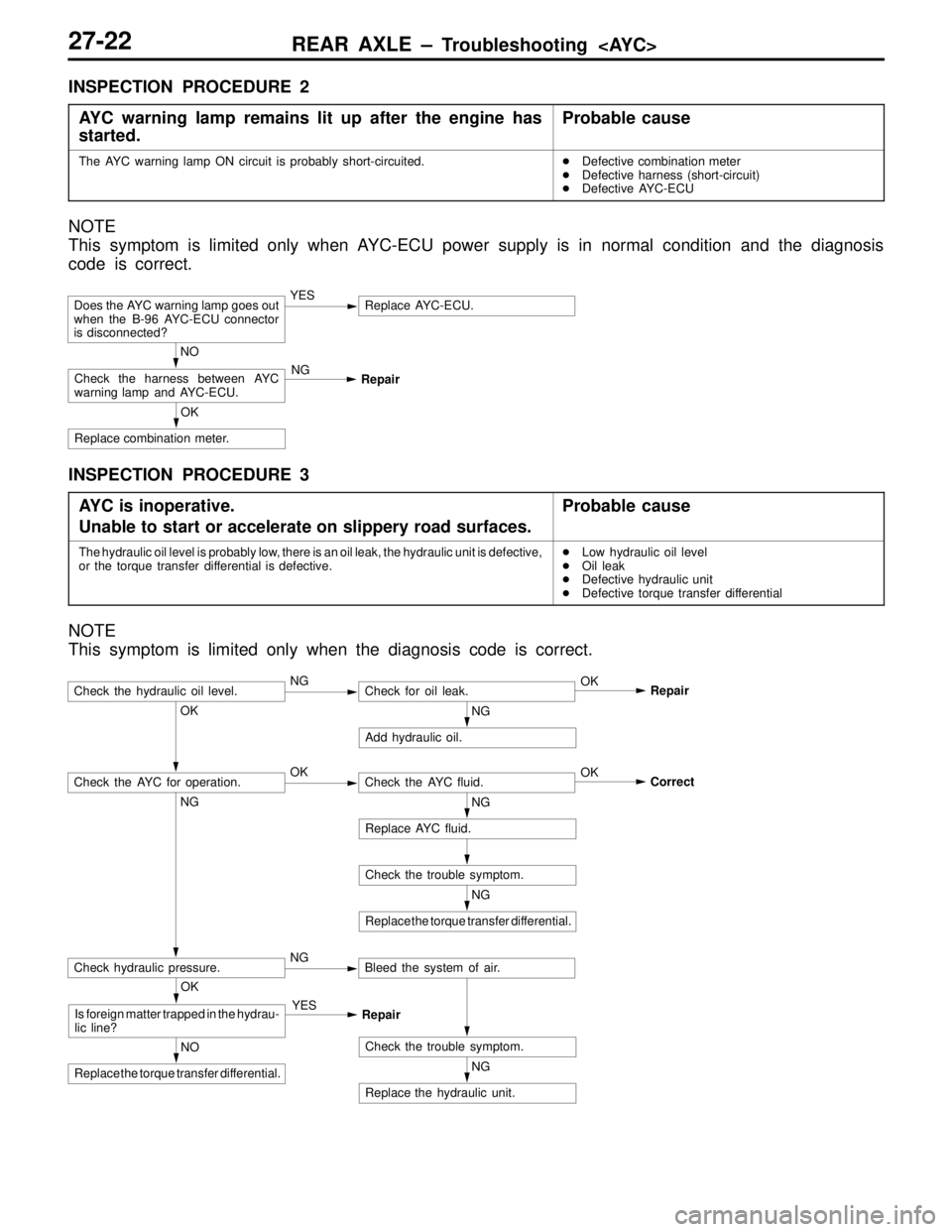
REAR AXLE – Troubleshooting 27-22
INSPECTION PROCEDURE 2
AYC warning lamp remains lit up after the engine has
started.
Probable cause
The AYC warning lamp ON circuit is probably short-circuited.Defective combination meter
Defective harness (short-circuit)
Defective AYC-ECU
NOTE
This symptom is limited only when AYC-ECU power supply is in normal condition and the diagnosis
code is correct.
OK
Replace combination meter.
NO
Check the harness between AYC
warning lamp and AYC-ECU.NG
Repair
Does the AYC warning lamp goes out
when the B-96 AYC-ECU connector
is disconnected?YESReplace AYC-ECU.
INSPECTION PROCEDURE 3
AYC is inoperative.
Unable to start or accelerate on slippery road surfaces.
Probable cause
The hydraulic oil level is probably low, there is an oil leak, the hydraulic unit is defective,
or the torque transfer differential is defective.Low hydraulic oil level
Oil leak
Defective hydraulic unit
Defective torque transfer differential
NOTE
This symptom is limited only when the diagnosis code is correct.
NG
Replace the hydraulic unit.
NG
Replace the torque transfer differential.
Check the trouble symptom.
NG
Replace AYC fluid.
OK
Correct
Check the trouble symptom.NO
Replace the torque transfer differential.
OK
Is foreign matter trapped in the hydrau-
lic line?YES
Repair
OK
Check the AYC for operation.OKCheck the AYC fluid.
NG
Add hydraulic oil.
NG
Check hydraulic pressure.NGBleed the system of air.
Check the hydraulic oil level.NGCheck for oil leak.OK
Repair
Page 210 of 396
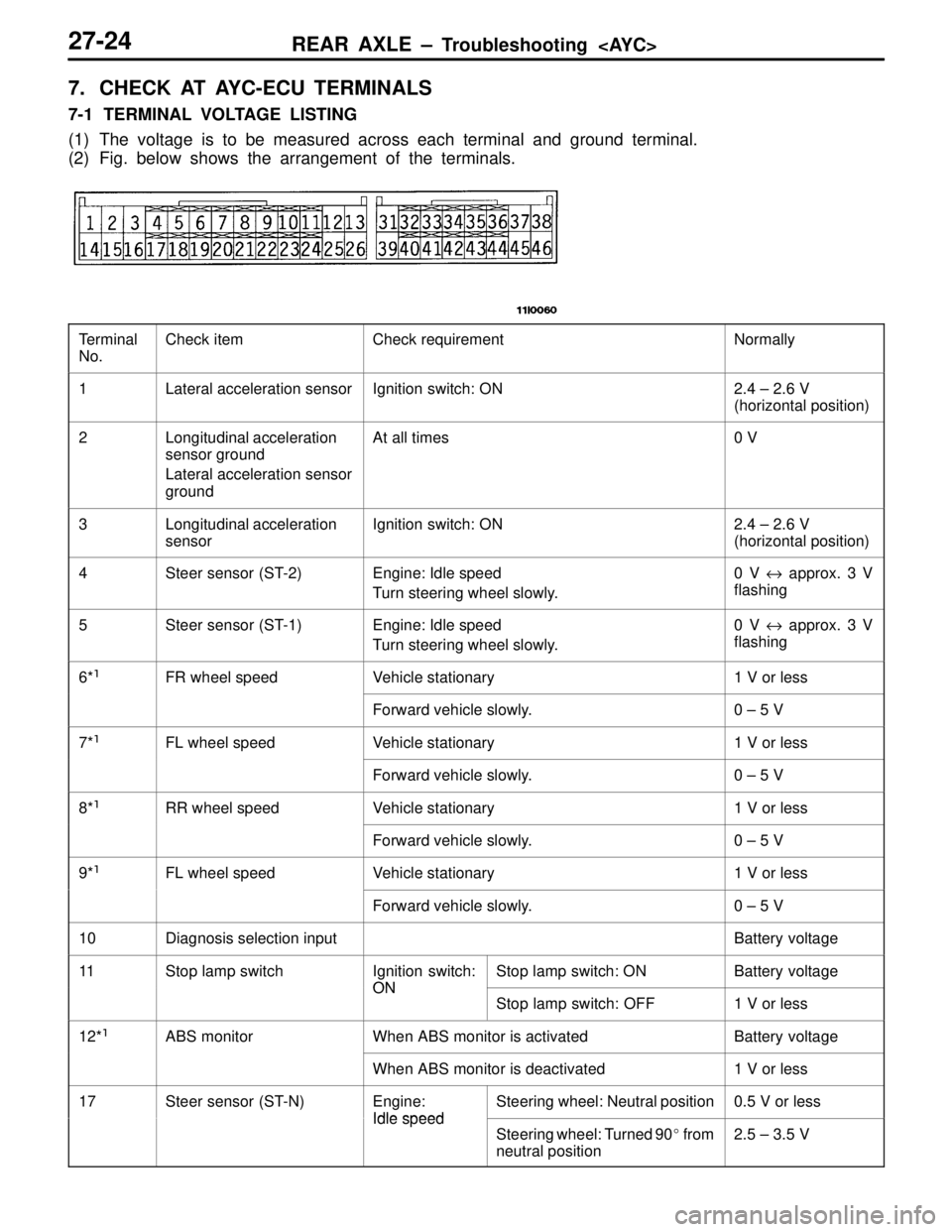
REAR AXLE – Troubleshooting 27-24
7. CHECK AT AYC-ECU TERMINALS
7-1 TERMINAL VOLTAGE LISTING
(1) The voltage is to be measured across each terminal and ground terminal.
(2) Fig. below shows the arrangement of the terminals.
Terminal
No.Check itemCheck requirementNormally
1Lateral acceleration sensorIgnition switch: ON2.4 – 2.6 V
(horizontal position)
2Longitudinal acceleration
sensor ground
Lateral acceleration sensor
groundAt all times0 V
3Longitudinal acceleration
sensorIgnition switch: ON2.4 – 2.6 V
(horizontal position)
4Steer sensor (ST-2)Engine: Idle speed
Turn steering wheel slowly.0 V ↔ approx. 3 V
flashing
5Steer sensor (ST-1)Engine: Idle speed
Turn steering wheel slowly.0 V ↔ approx. 3 V
flashing
6*1FR wheel speedVehicle stationary1 V or less
Forward vehicle slowly.0 – 5 V
7*1FL wheel speedVehicle stationary1 V or less
Forward vehicle slowly.0 – 5 V
8*1RR wheel speedVehicle stationary1 V or less
Forward vehicle slowly.0 – 5 V
9*1FL wheel speedVehicle stationary1 V or less
Forward vehicle slowly.0 – 5 V
10Diagnosis selection inputBattery voltage
11Stop lamp switchIgnition switch:
ON
Stop lamp switch: ONBattery voltage
ON
Stop lamp switch: OFF1 V or less
12*1ABS monitorWhen ABS monitor is activatedBattery voltage
When ABS monitor is deactivated1 V or less
17Steer sensor (ST-N)Engine:
Idle speed
Steering wheel: Neutral position0.5 V or less
Idle speed
Steering wheel: Turned 90 from
neutral position2.5 – 3.5 V
Page 217 of 396
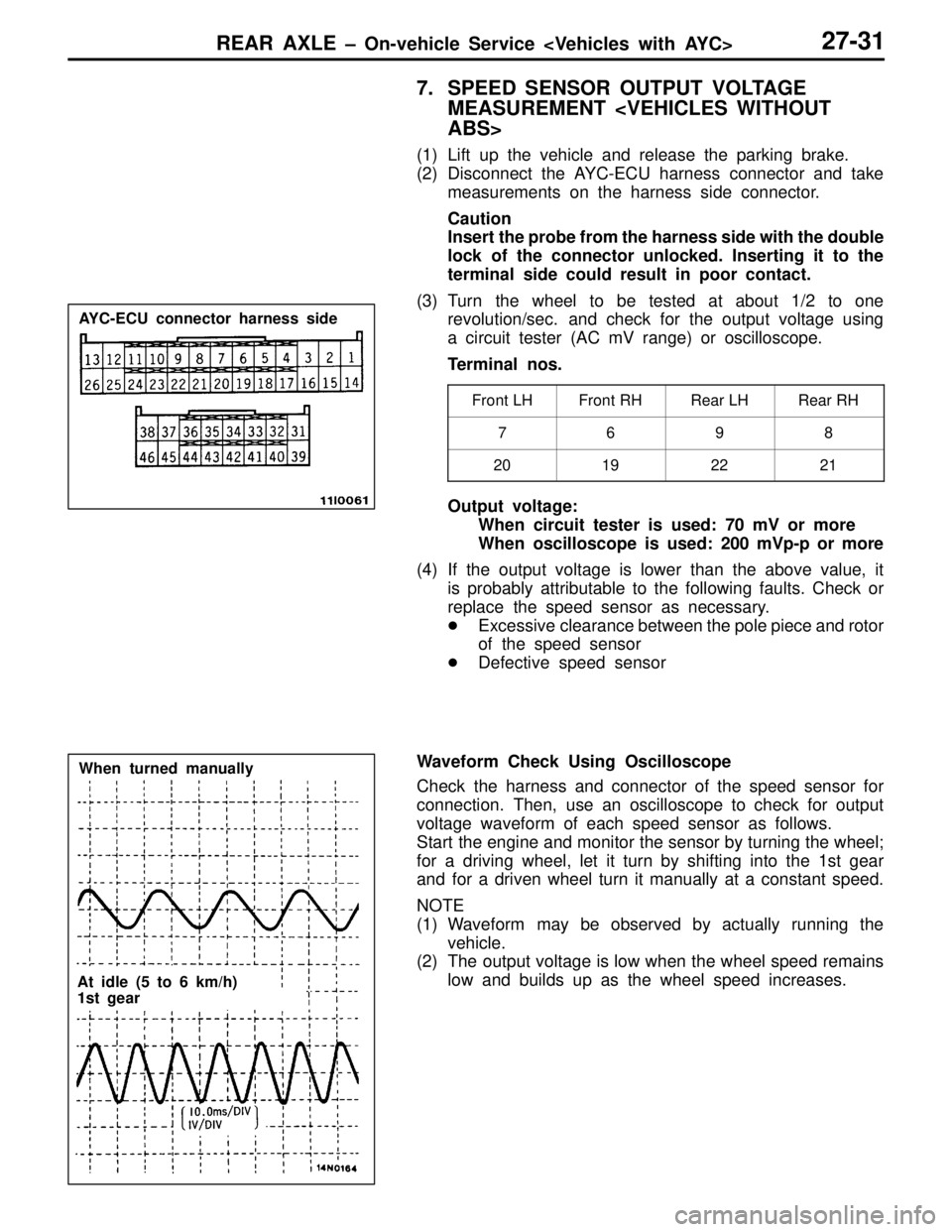
REAR AXLE – On-vehicle Service 27-31
7. SPEED SENSOR OUTPUT VOLTAGE
MEASUREMENT
ABS>
(1) Lift up the vehicle and release the parking brake.
(2) Disconnect the AYC-ECU harness connector and take
measurements on the harness side connector.
Caution
Insert the probe from the harness side with the double
lock of the connector unlocked. Inserting it to the
terminal side could result in poor contact.
(3) Turn the wheel to be tested at about 1/2 to one
revolution/sec. and check for the output voltage using
a circuit tester (AC mV range) or oscilloscope.
Terminal nos.
Front LHFront RHRear LHRear RH
7698
20192221
Output voltage:
When circuit tester is used: 70 mV or more
When oscilloscope is used: 200 mVp-p or more
(4) If the output voltage is lower than the above value, it
is probably attributable to the following faults. Check or
replace the speed sensor as necessary.
Excessive clearance between the pole piece and rotor
of the speed sensor
Defective speed sensor
Waveform Check Using Oscilloscope
Check the harness and connector of the speed sensor for
connection. Then, use an oscilloscope to check for output
voltage waveform of each speed sensor as follows.
Start the engine and monitor the sensor by turning the wheel;
for a driving wheel, let it turn by shifting into the 1st gear
and for a driven wheel turn it manually at a constant speed.
NOTE
(1) Waveform may be observed by actually running the
vehicle.
(2) The output voltage is low when the wheel speed remains
low and builds up as the wheel speed increases.
AYC-ECU connector harness side
When turned manually
At idle (5 to 6 km/h)
1st gear
Page 218 of 396
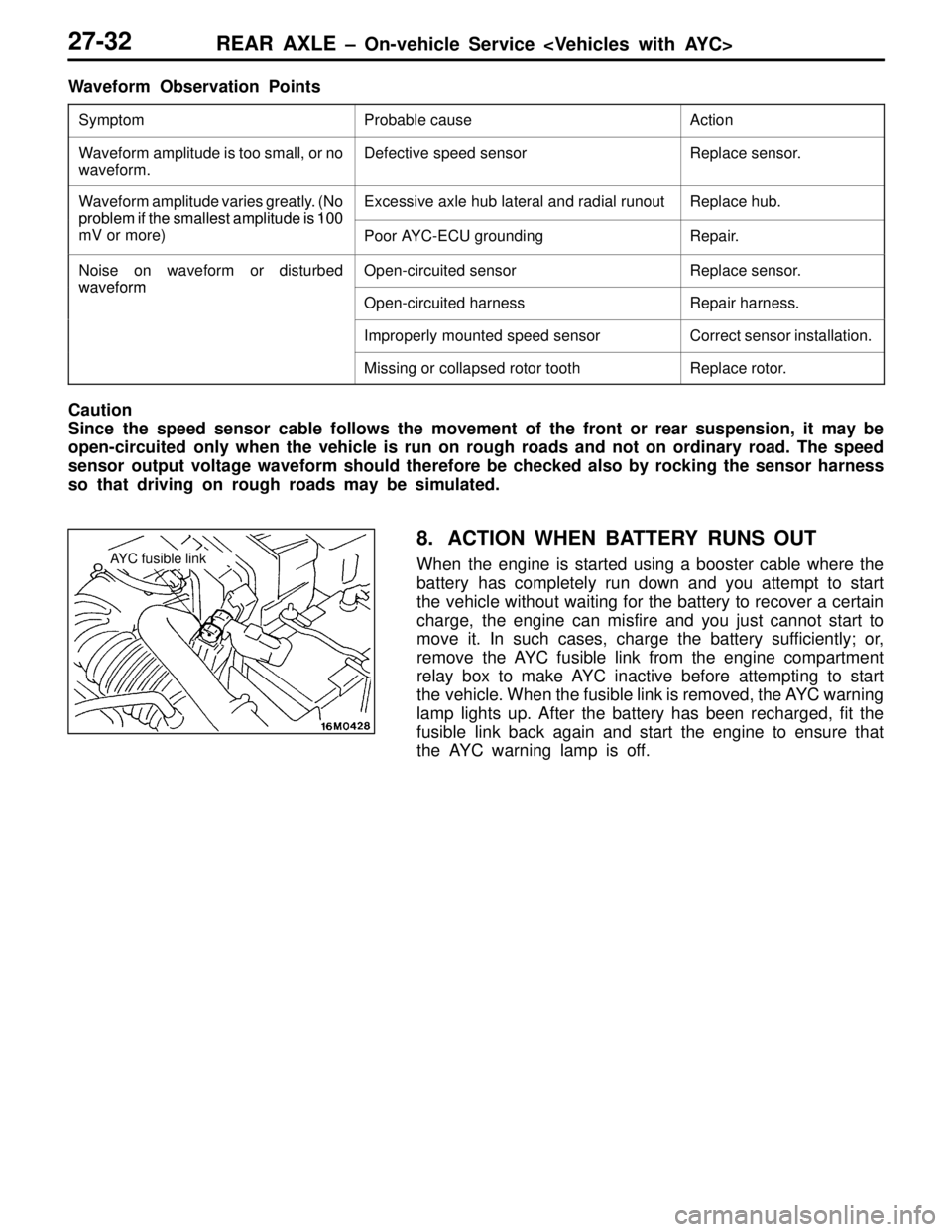
REAR AXLE – On-vehicle Service 27-32
Waveform Observation Points
SymptomProbable causeAction
Waveform amplitude is too small, or no
waveform.Defective speed sensorReplace sensor.
Waveform amplitude varies greatly. (No
problem ifthe smallest amplitude is 100
Excessive axle hub lateral and radial runoutReplace hub.
problem if the smallest amplitude is 100
mV or more)Poor AYC-ECU groundingRepair.
Noise on waveform or disturbed
waveform
Open-circuited sensorReplace sensor.
waveform
Open-circuited harnessRepair harness.
Improperly mounted speed sensorCorrect sensor installation.
Missing or collapsed rotor toothReplace rotor.
Caution
Since the speed sensor cable follows the movement of the front or rear suspension, it may be
open-circuited only when the vehicle is run on rough roads and not on ordinary road. The speed
sensor output voltage waveform should therefore be checked also by rocking the sensor harness
so that driving on rough roads may be simulated.
8. ACTION WHEN BATTERY RUNS OUT
When the engine is started using a booster cable where the
battery has completely run down and you attempt to start
the vehicle without waiting for the battery to recover a certain
charge, the engine can misfire and you just cannot start to
move it. In such cases, charge the battery sufficiently; or,
remove the AYC fusible link from the engine compartment
relay box to make AYC inactive before attempting to start
the vehicle. When the fusible link is removed, the AYC warning
lamp lights up. After the battery has been recharged, fit the
fusible link back again and start the engine to ensure that
the AYC warning lamp is off.AYC fusible link
Page 241 of 396
POWER PLANT MOUNT – Roll Stopper and Centermember32-2
ROLL STOPPER AND CENTERMEMBER
REMOVAL AND INSTALLATION
Caution
When tightening the portion marked with *, first
temporarily tighten it, then torque to specification
with the engine weight applied to the body.
1
2 34
5
Unit: Nm {kgfm}
52 {5.3}*
22
34 {3.5}34 {3.5}
93 {9.5}
69 {7.0} 93 {9.5}
2
Removal steps
1. Front crossmember bar
with 17’ wheels>
2. Bolt
B3. Front roll stopper bracket assembly
A4. Rear roll stopper bracket assembly
5. CentermemberNOTE
The conventional service procedures apply for the
installation service points.
Page 271 of 396
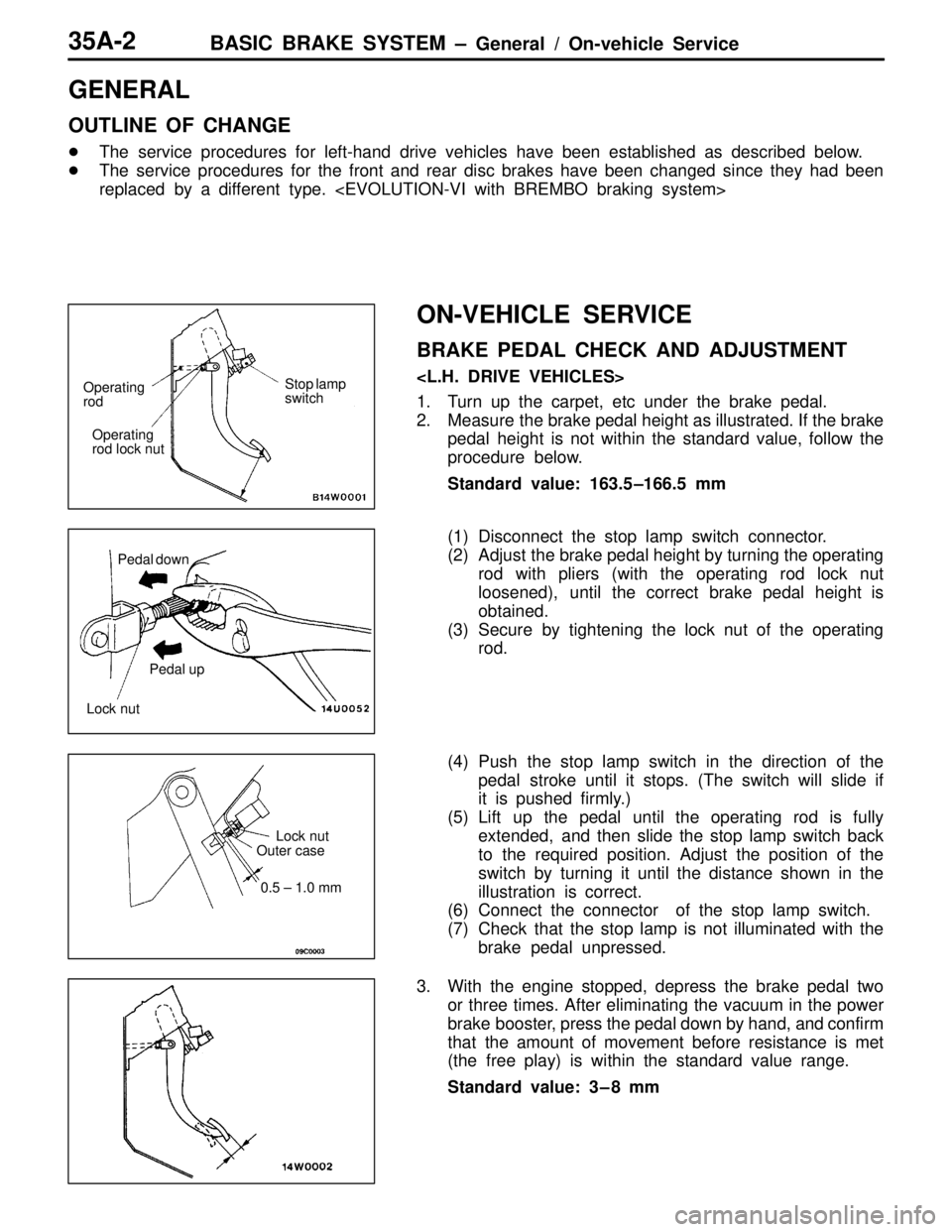
BASIC BRAKE SYSTEM – General / On-vehicle Service35A-2
GENERAL
OUTLINE OF CHANGE
The service procedures for left-hand drive vehicles have been established as described below.
The service procedures for the front and rear disc brakes have been changed since they had been
replaced by a different type.
ON-VEHICLE SERVICE
BRAKE PEDAL CHECK AND ADJUSTMENT
1. Turn up the carpet, etc under the brake pedal.
2. Measure the brake pedal height as illustrated. If the brake
pedal height is not within the standard value, follow the
procedure below.
Standard value: 163.5 –166.5 mm
(1) Disconnect the stop lamp switch connector.
(2) Adjust the brake pedal height by turning the operating
rod with pliers (with the operating rod lock nut
loosened), until the correct brake pedal height is
obtained.
(3) Secure by tightening the lock nut of the operating
rod.
(4) Push the stop lamp switch in the direction of the
pedal stroke until it stops. (The switch will slide if
it is pushed firmly.)
(5) Lift up the pedal until the operating rod is fully
extended, and then slide the stop lamp switch back
to the required position. Adjust the position of the
switch by turning it until the distance shown in the
illustration is correct.
(6) Connect the connector of the stop lamp switch.
(7) Check that the stop lamp is not illuminated with the
brake pedal unpressed.
3. With the engine stopped, depress the brake pedal two
or three times. After eliminating the vacuum in the power
brake booster, press the pedal down by hand, and confirm
that the amount of movement before resistance is met
(the free play) is within the standard value range.
Standard value: 3 – 8 mmOperating
rod
Operating
rod lock nutStop lamp
switch
Pedal down
Pedal up
Lock nut
Lock nut
Outer case
0.5 – 1.0 mm
Page 272 of 396
BASIC BRAKE SYSTEM – On-vehicle Service35A-3
If the free play exceeds the standard value, it is probably
due to excessive play between the retaining ring bolt
and brake pedal arm.
Check for excessive clearance and replace faulty parts
as required.
4. Start the engine, depress the brake pedal with
approximately 490 N of force, and measure the clearance
between the brake pedal and the floorboard.
Standard value: 80 mm or more
If the clearance is outside the standard value, check for
air trapped in the brake line, clearance between the lining
and the drum and dragging in the parking brake.
Adjust and replace defective parts as required.
5. Turn back the carpet, etc.
Page 275 of 396
BASIC BRAKE SYSTEM – Master Cylinder and Brake Booster35A-6
INSTALLATION SERVICE POINTS
AVACUUM HOSE CONNECTION
Insert securely and completely until the vacuum hose at the
engine side contacts the edge of the hexagonal part of the
fitting, and then secure by using the hose clip.
BCLEARANCE ADJUSTMENT BETWEEN BRAKE
BOOSTER PUSH ROD AND PRIMARY PISTON
Calculate clearance A from the B, C and D measurements.
A = B – C – D
Standard value: 0.65–0.85 mm
If the clearance is not within the standard value range, adjust
by changing the push rod length by turning the screw of
the push rod.
Measuring
distance BMeasuring
distance D
Block
gaugeB
AC
D