Page 939 of 2490
Pinpoint test
B: P0117
I
gnition switch to position 0
1
Di
sconnect EM010
Inside E
CM housing
2
Meas
ure the resistance between the ECM connector
EM010/020 and the ECT connector PI004/001.
3
I
s the resistance < 0.5 OHM?
Yes GO to A7
No Inspect harness / connector EM010/020, PI004/001,
PI001/006 and splices EMS02 / PIS01 for corrosion,
damage, bent or pushed back pins. Repair as necessary
and reconnect all connectors.
Test the system for normal operation.
A7
: END
Perform
appropriate service drive cycle and check for the
presence of DTC.
1
Has
the fault code cleared?
Yes STOP
No Contact Jaguar Service
P
INPOINT TEST B : P0117
T
EST CONDITIONS
D
ETAILS/RESULTS/ACTIONS
B1
: RETRIEVE DTCS
•
NOTE: Battery and or ECM disconnection prior to scanning wi
ll erase all data, ensure that the correct DTC is present.
Page 941 of 2490
I
gnition switch to position 0
1
Di
sconnect EM011
Inside E
CM housing
2
D
isconnect PI004
Re
ar of top hose
3
Meas
ure the resistance between the ECM connector
EM011/009 and the ECT connector PI004/002.
4
I
s the resistance < 0.5 OHM?
Yes GO to B4
No Inspect harness / connector EM011/009, PI004/002 and
PI001/005 for corrosion, damage , bent or pushed back
pins. Repair as necessary and test the system for normal
operation.
B4: CHECK
HARNESS CONTINUITY
•
NOTE: To avoid a spurious result, disconnect connectors PI042 and PI006 (electronic throttle body) and PI035 (MAF
meter).
Page 942 of 2490
Ig
nition switch to position 0
1
Di
sc
onnect EM010
Inside E
C
M housing
2
Meas
ure t
he resistance between the ECM connector
EM011/012 and the ECT connector PI004/001.
3
I s
the resistance < 0.5 OHM?
Yes GO to B5
No Inspect harness / connector EM011/012, PI004/001,
PI001/006 and splices EMS02 / PIS01 for corrosion,
damage, bent or pushed back pins. Repair as necessary,
reconnect all connectors. Te st the system for normal
operation.
B5: CHECK HARNESS
CONTINUITY
•
NOTE
: Do not reconnect electronic thro
ttle body connectors PI042 and PI006.
Page 943 of 2490
I
gnition switch to position 0
1
Di
sconnect EM010
Inside E
CM housing
2
Meas
ure the resistance between the ECM connector
EM010/020 and the ECT connector PI004/001.
3
I
s the resistance < 0.5 OHM?
Yes GO to B6
No Inspect harness / connector EM010/020, PI004/001,
PI001/006 and splices EMS02 / PIS01 for corrosion,
damage, bent or pushed back pins. Repair as required and
reconnect all connectors. Te st the system for normal
operation.
B6:
CHECK FOR SHORT TO B+
Page 944 of 2490
Pinpoint test C: P0118
I
g
nition switch to position 0
1
Di
sc
onnect EM011
Inside E
C
M housing
2
I
g
nition switch to position II
3
Measure the
voltage betwee n pin
s 9 and 12 of the
connector.
4
Is th e volt
age > 1 V?
Yes Inspect harness / connector EM011/009, PI004/002,
PI001/005 and splices EMS02 / PIS01 for corrosion,
damage, bent or pushed back pins. Repair as required and
reconnect all connectors. Te st the system for normal
operation.
No GO to B7
B7: EN
D
Perform
a
ppropriate service drive cycle and check for the
presence of DTC.
1
Has th
e fault code cleared?
Yes STOP
No Contact Jaguar Service
PINPOINT TES
T C : P0118
T
E
ST CONDITIONS
D
E
TAILS/RESULTS/ACTIONS
C1
: RETRIEVE DTC
S
•
NOTE
: Battery and or ECM disconnection prior to scanning wi
ll erase all data, ensure that the correct DTC is present.
Page 946 of 2490
Pinpoint test D
: P1474
I
g
nition switch to position 0
1
Di
sc
onnect EM011
Inside E
C
M housing
2
Meas
ure t
he resistance betw
een pins 9 and 12 of the
connector.
3
Re si
stance < 0.5 OHM?
Yes Inspect harness / connector EM011/0012, PI004/001,
PI001/006 and splices EMS02 / PIS01 for corrosion,
damage, bent or pushed back pins. Repair as required and
reconnect all connectors. Te st the system for normal
operation.
No GO to C4
C4: END
Perform a
ppropriate service drive cycle and check for the
presence of DTC.
1
Has th
e fault code cleared?
Yes STOP
No Contact Jaguar Service
PINPOINT TES
T D : P1474
T
E
ST CONDITIONS
D
E
TAILS/RESULTS/ACTIONS
D1
:
RETRIEVE DTCS
•
NOTE
: Battery and or ECM disconnection prior to scanning wi
ll erase all data, ensure that the correct DTC is present.
Page 951 of 2490
Ignition switc
h to position II
1
Meas
ure voltage between relay socket between pin 2 and
ground EM017.
2
B+ ?
Yes
GO to D8
No GO to D7
D7: C
HECK ECM SUPPLY TO RELAY CONTINUITY
Page 1015 of 2490
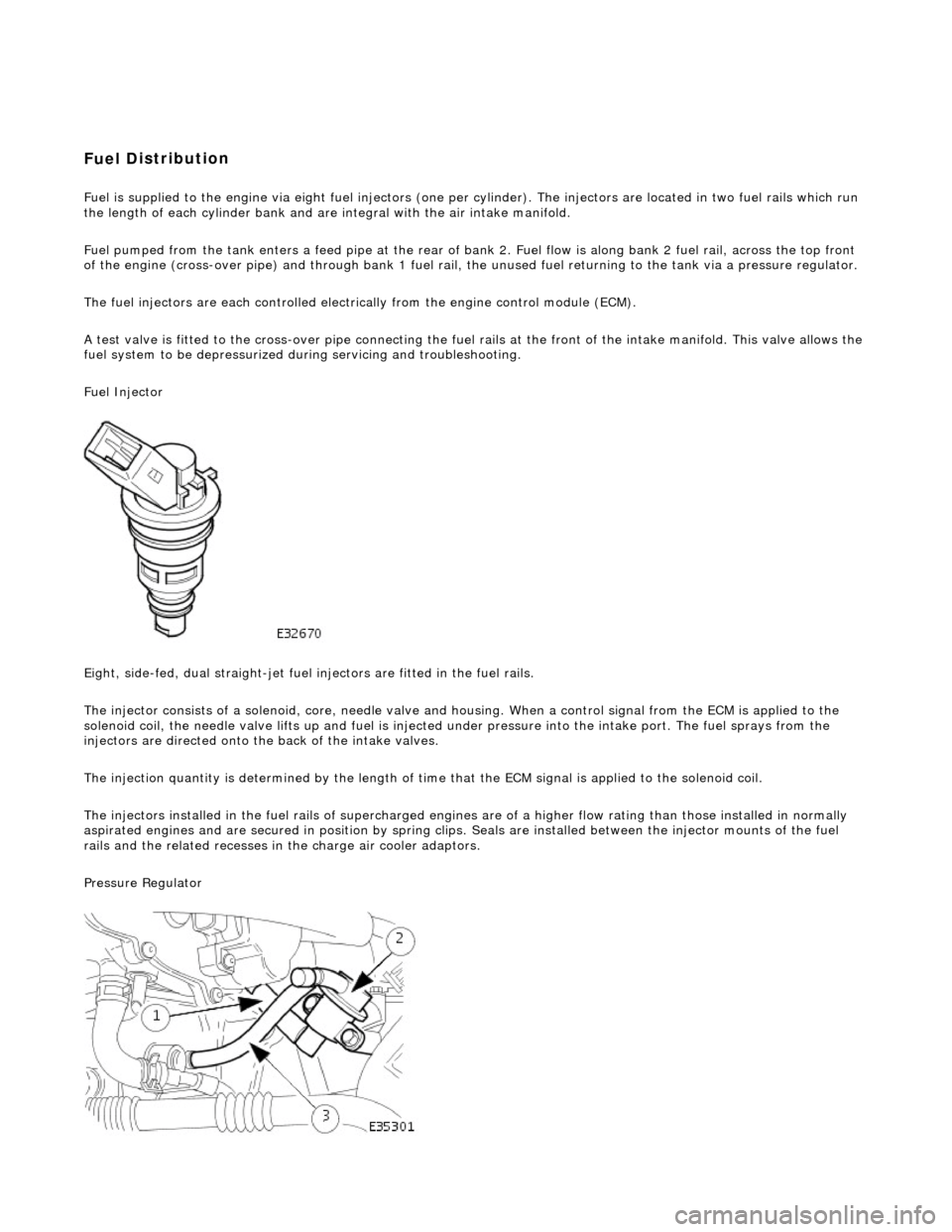
Fuel D
istribution
Fuel is supplied to th
e engine
via eight fuel injectors (one pe r cylinder). The injectors are located in two fuel rails which r un
the length of each cylinder bank and ar e integral with the air intake manifold.
Fuel pumped from the tank enters a feed pipe at the rear of bank 2. Fuel flow is along bank 2 fuel rail, across the top front
of the engine (cross-over pipe) and through bank 1 fuel rail, the unused fuel re turning to the tank via a pressure regulator.
The fuel injectors are each controlled electrically from the engine control module (ECM).
A test valve is fitted to the cross-over pipe connecting the fu el rails at the front of the intake manifold. This valve allows the
fuel system to be depr essurized during servicin g and troubleshooting.
Fuel Injector
Eight, side-fed, dual straight-jet fuel injectors are fi tted in the fuel rails.
The injector consists of a solenoid, core, needle valve and ho using. When a control signal from the ECM is applied to the
solenoid coil, the needle valve lifts up and fuel is injected under pressure into the intake port. The fuel sprays from the
injectors are directed onto the back of the intake valves.
The injection quantity is determined by the length of time that the ECM signal is applied to the solenoid coil.
The injectors installed in the fuel rails of supercharged engines are of a higher flow rating than those installed in normally
aspirated engines and are secured in position by spring clips. Seals are instal led between the injector mounts of the fuel
rails and the related re cesses in the charge air cooler adaptors.
Pressure Regulator