Page 546 of 2053
GENERAL ENGINE INFORMATION 1A3 -- 11
D AEW OO M Y_2000
COMPRESSION PRESSURE TEST
1 Test Adapter
2 Flexible Connector
3 Compression Pressure Recorder
Service Data
Normal Compression Pressure28bar
Minimum Compression PressureApprox.18bar
Permissible Pressure Difference Between Individual CylindersMax. 3bar
DEngine at normal operating temperature of 80_C
Tools Required
000 589 65 09 00 Socket
001 589 73 21 00 Hand Vacuum Pump
Page 547 of 2053
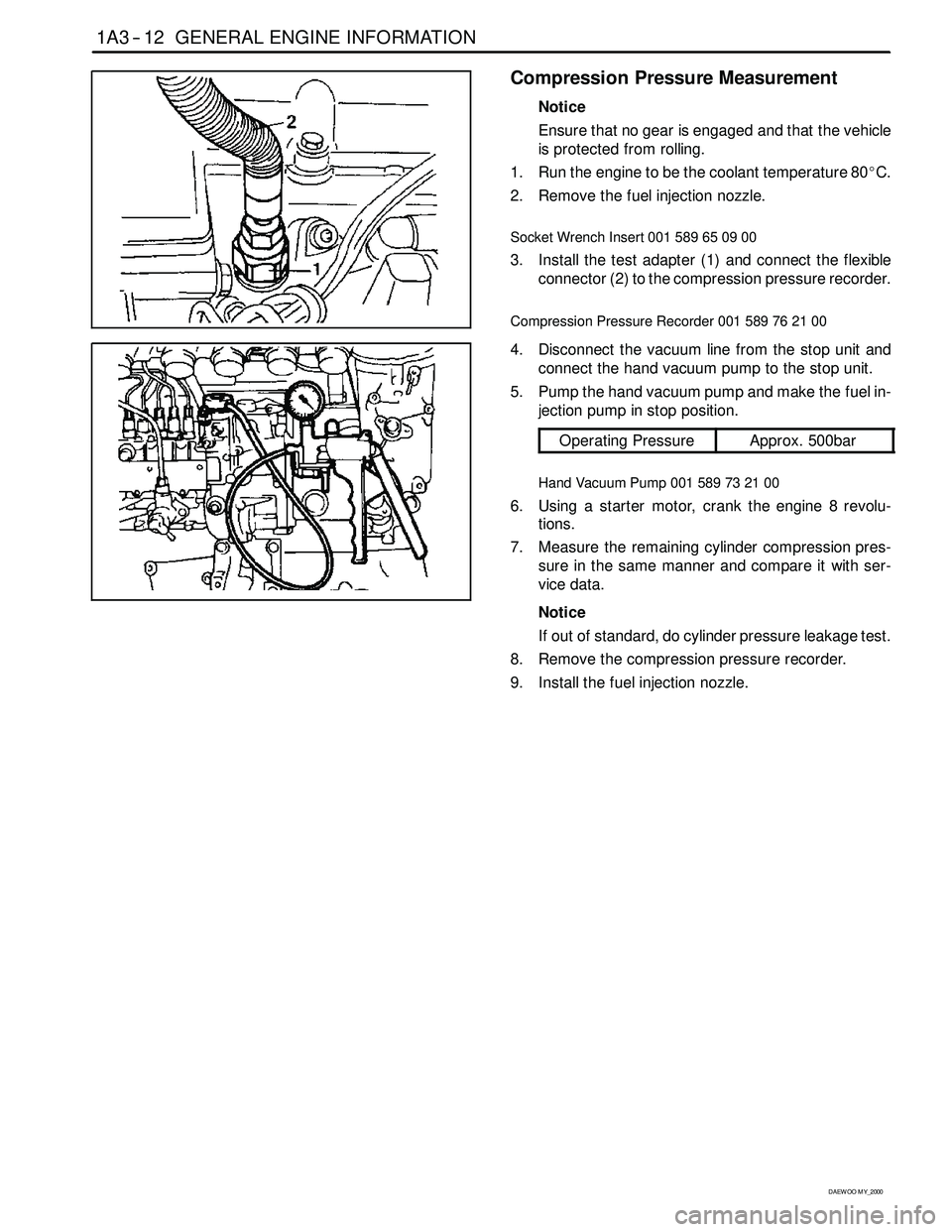
1A3 -- 12 GENERAL ENGINE INFORMATION
D AEW OO M Y_2000
Compression Pressure Measurement
Notice
Ensure that no gear is engaged and that the vehicle
is protected from rolling.
1. Run the engine to be the coolant temperature 80_C.
2. Remove the fuel injection nozzle.
Socket Wrench Insert 001 589 65 09 00
3. Install the test adapter (1) and connect the flexible
connector (2) to the compression pressure recorder.
Compression Pressure Recorder 001 589 76 21 00
4. Disconnect the vacuum line from the stop unit and
connect the hand vacuum pump to the stop unit.
5. Pump the hand vacuum pump and make the fuel in-
jection pump in stop position.
Operating PressureApprox. 500bar
Hand Vacuum Pump 001 589 73 21 00
6. Using a starter motor, crank the engine 8 revolu-
tions.
7. Measure the remaining cylinder compression pres-
sure in the same manner and compare it with ser-
vice data.
Notice
If out of standard, do cylinder pressure leakage test.
8. Remove the compression pressure recorder.
9. Install the fuel injection nozzle.
Page 548 of 2053
GENERAL ENGINE INFORMATION 1A3 -- 13
D AEW OO M Y_2000
CYLINDER PRESSURE LEAKAGE TEST
1 Connector
2 Connection Piece
3 Connection Hose
Permissible Pressure Leakage (Engine at Normal Operating Temperature of 80_C)
At Whole EngineMax. 25 %
At Valve and Cylinder Head GasketMax. 10 %
At Piston and Piston RingMax. 20 %
Commercial Tools
Cylinder Pressure Leakage testerBOSCH, EFAW 210 A or SUN CLT 228
Connection PieceBOSCH order no. 1 687 010 016
Page 549 of 2053
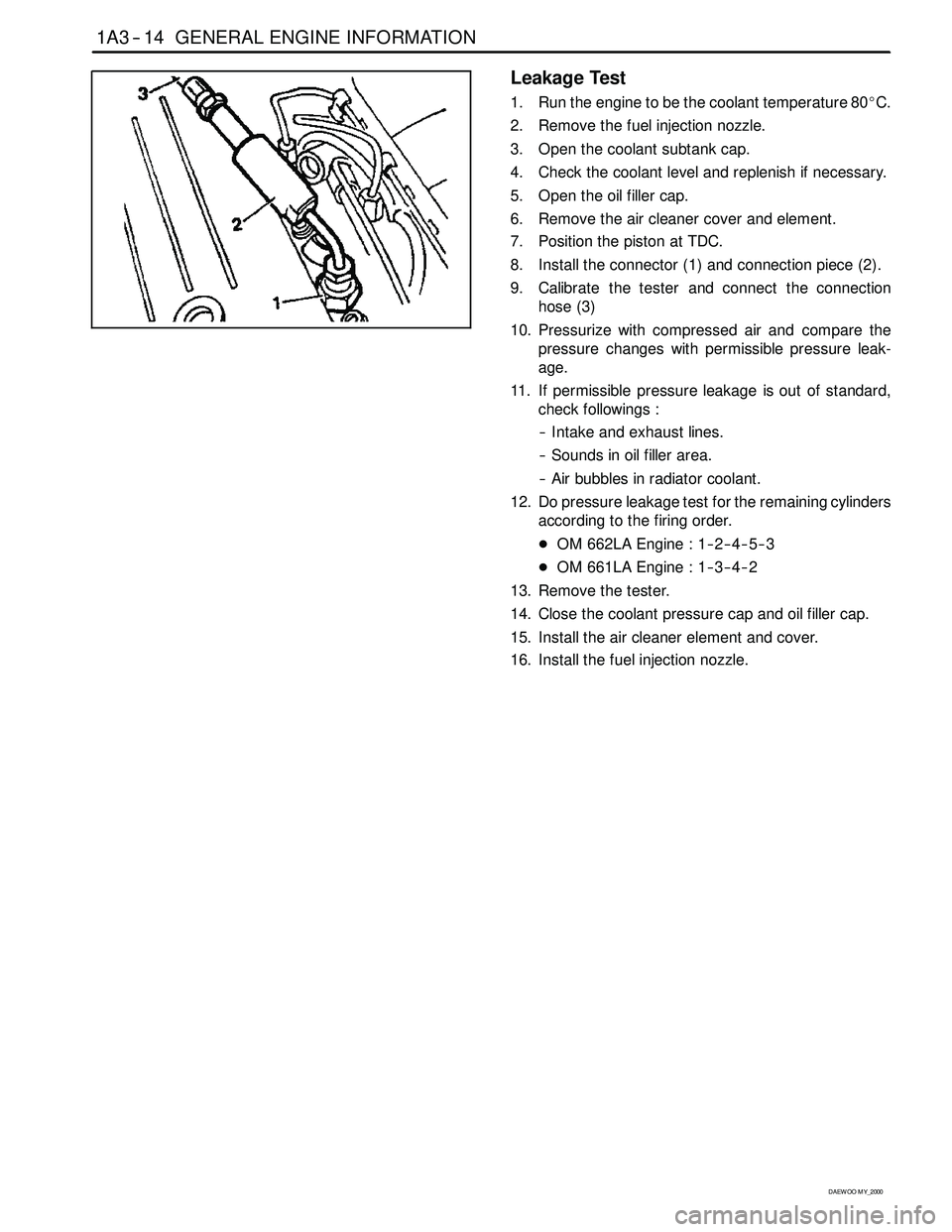
1A3 -- 14 GENERAL ENGINE INFORMATION
D AEW OO M Y_2000
Leakage Test
1. Run the engine to be the coolant temperature 80_C.
2. Remove the fuel injection nozzle.
3. Open the coolant subtank cap.
4. Check the coolant level and replenish if necessary.
5. Open the oil filler cap.
6. Remove the air cleaner cover and element.
7. Position the piston at TDC.
8. Install the connector (1) and connection piece (2).
9. Calibrate the tester and connect the connection
hose (3)
10. Pressurize with compressed air and compare the
pressure changes with permissible pressure leak-
age.
11. If permissible pressure leakage is out of standard,
check followings :
-- Intake and exhaust lines.
-- Sounds in oil filler area.
-- Air bubbles in radiator coolant.
12. Do pressure leakage test for the remaining cylinders
according to the firing order.
DOM 662LA Engine : 1-- 2-- 4-- 5-- 3
DOM 661LA Engine : 1-- 3-- 4-- 2
13. Remove the tester.
14. Close the coolant pressure cap and oil filler cap.
15. Install the air cleaner element and cover.
16. Install the fuel injection nozzle.
Page 550 of 2053
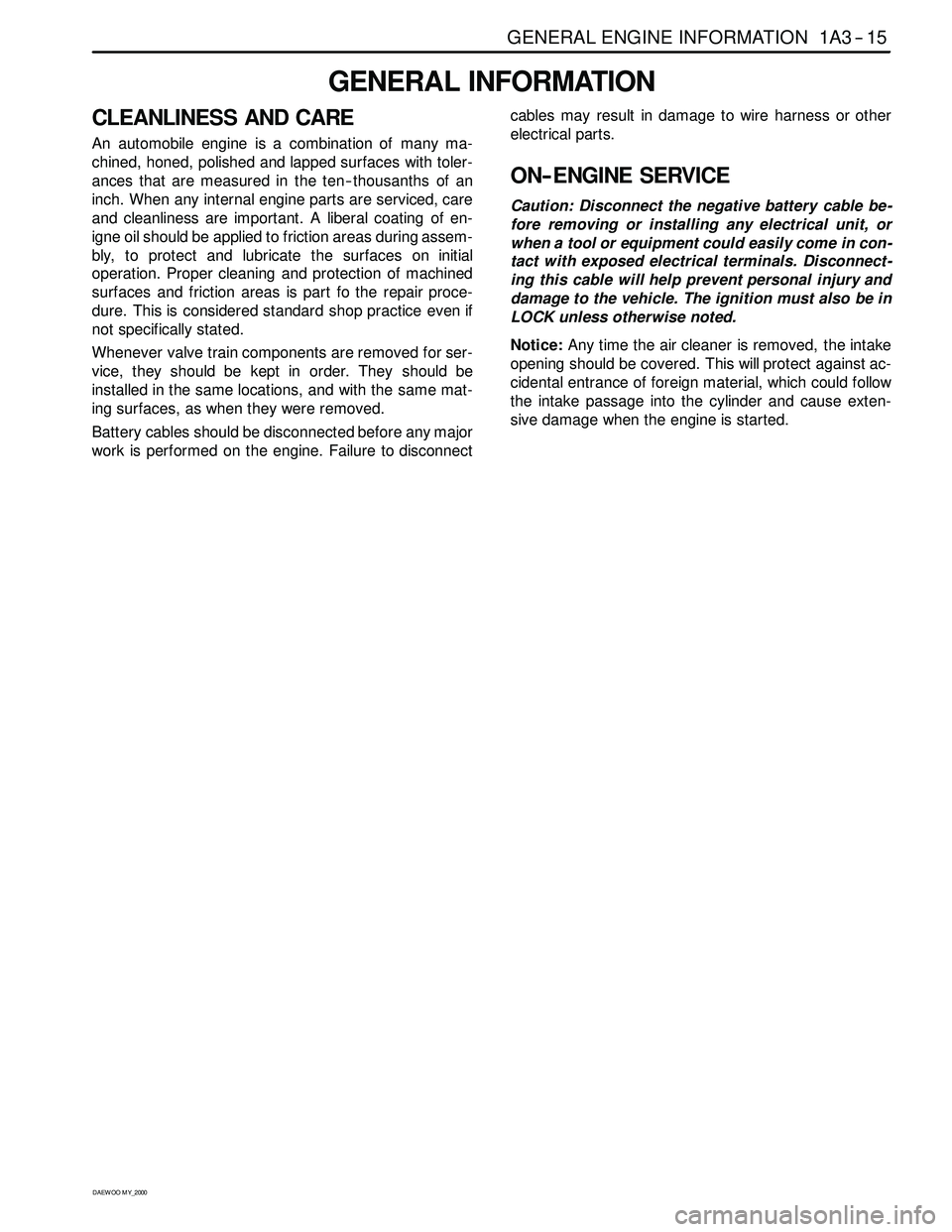
GENERAL ENGINE INFORMATION 1A3 -- 15
D AEW OO M Y_2000
GENERAL INFORMATION
CLEANLINESS AND CARE
An automobile engine is a combination of many ma-
chined, honed, polished and lapped surfaces with toler-
ances that are measured in the ten-- thousanths of an
inch. When any internal engine parts are serviced, care
and cleanliness are important. A liberal coating of en-
igne oil should be applied to friction areas during assem-
bly, to protect and lubricate the surfaces on initial
operation. Proper cleaning and protection of machined
surfaces and friction areas is part fo the repair proce-
dure. This is considered standard shop practice even if
not specifically stated.
Whenever valve train components are removed for ser-
vice, they should be kept in order. They should be
installed in the same locations, and with the same mat-
ing surfaces, as when they were removed.
Battery cables should be disconnected before any major
work is performed on the engine. Failure to disconnectcables may result in damage to wire harness or other
electrical parts.
ON-- ENGINE SERVICE
Caution: Disconnect the negative battery cable be -
fore removing or installing any electrical unit, or
when a tool or equipment could easily come in con-
tact with exposed electrical terminals. Disconnect -
ing this cable will help prevent personal injury and
damage to the vehicle. The ignition must also be in
LOCK unless otherwise noted.
Notice:Any time the air cleaner is removed, the intake
opening should be covered. Thiswill protect against ac-
cidental entrance of foreign material, which could follow
the intake passage into the cylinder and cause exten-
sive damage when the engine is started.
Page 551 of 2053
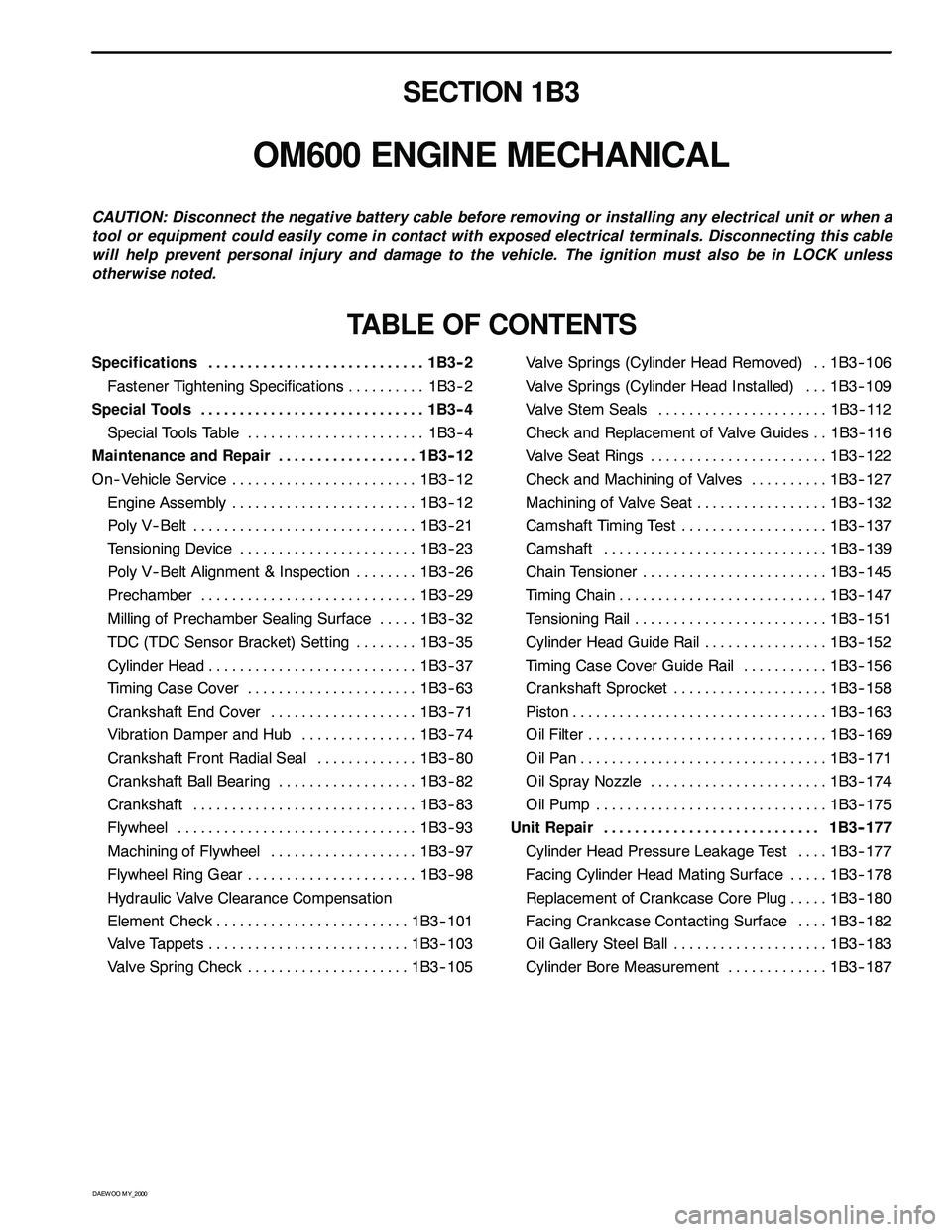
D AEW OO M Y_2000
SECTION 1B3
OM600 ENGINE MECHANICAL
CAUTION: Disconnect the negative battery cable before removing or installing any electrical unit or when a
tool or equipment could easily come in contact with exposed electrical terminals. Disconnecting this cable
will help prevent personal injury and damage to the vehicle. The ignition must also be in LOCK unless
otherwise noted.
TABLE OF CONTENTS
Specifications 1B3 -- 2............................
Fastener Tightening Specifications 1B3 -- 2..........
Special Tools 1B3 -- 4.............................
Special Tools Table 1B3-- 4.......................
Maintenance and Repair 1B3 -- 12..................
On-- Vehicle Service 1B3-- 12........................
Engine Assembly 1B3-- 12........................
Poly V-- Belt 1B3 -- 21.............................
Tensioning Device 1B3-- 23.......................
Poly V-- Belt Alignment & Inspection 1B3-- 26........
Prechamber 1B3-- 29............................
Milling of Prechamber Sealing Surface 1B3 -- 32.....
TDC (TDC Sensor Bracket) Setting 1B3 -- 35........
Cylinder Head 1B3-- 37...........................
Timing Case Cover 1B3 -- 63......................
Crankshaft End Cover 1B3-- 71...................
Vibration Damper and Hub 1B3-- 74...............
Crankshaft Front Radial Seal 1B3-- 80.............
Crankshaft Ball Bearing 1B3-- 82..................
Crankshaft 1B3-- 83.............................
Flywheel 1B3 -- 93...............................
Machining of Flywheel 1B3-- 97...................
Flywheel Ring Gear 1B3 -- 98......................
Hydraulic Valve Clearance Compensation
Element Check 1B3-- 101.........................
Valve Tappets 1B3-- 103..........................
Valve Spring Check 1B3-- 105.....................Valve Springs (Cylinder Head Removed) 1B3-- 106..
Valve Springs (Cylinder Head Installed) 1B3-- 109...
Valve Stem Seals 1B3-- 112......................
Check and Replacement of Valve Guides 1B3-- 116..
Valve Seat Rings 1B3-- 122.......................
Check and Machining of Valves 1B3-- 127..........
Machining of Valve Seat 1B3-- 132.................
Camshaft Timing Test 1B3-- 137...................
Camshaft 1B3-- 139.............................
Chain Tensioner 1B3-- 145........................
Timing Chain 1B3-- 147...........................
Tensioning Rail 1B3-- 151.........................
Cylinder Head Guide Rail 1B3-- 152................
Timing Case Cover Guide Rail 1B3-- 156...........
Crankshaft Sprocket 1B3-- 158....................
Piston 1B3-- 163.................................
Oil Filter 1B3-- 169...............................
Oil Pan 1B3-- 171................................
Oil Spray Nozzle 1B3-- 174.......................
Oil Pump 1B3-- 175..............................
Unit Repair 1B3 -- 177............................
Cylinder Head Pressure Leakage Test 1B3-- 177....
Facing Cylinder Head Mating Surface 1B3 -- 178.....
Replacement of Crankcase Core Plug 1B3-- 180.....
Facing Crankcase Contacting Surface 1B3 -- 182....
Oil Gallery Steel Ball 1B3-- 183....................
Cylinder Bore Measurement 1B3-- 187.............
Page 552 of 2053
1B3 -- 2 OM600 ENGINE MECHANICAL
D AEW OO M Y_2000
SPECIFICATIONS
FASTENER TIGHTENING SPECIFICATIONS
Engine Assembly
ApplicationNSmLb-- FtLb-- In
Skid Plate Bolt28 -- 4721 -- 35--
Drain Plug Bolt3022--
Coolong Fan Shroud Bolt3--7--27 -- 62
Control Linkage Nut8--186--13--
Clutch Linkage Cylinder Nut20 -- 3415 -- 25--
Exhaust Manifold Bolt3022--
Propeller Shaft Bolt & Nut (Axle)70 -- 8052 -- 59--
Propeller Shaft Bolt & Nut (T/C)81 -- 8960 -- 66--
Engine Mounting Nut50 -- 7537 -- 55--
Crankshaft Assembly
ApplicationNSmLb-- FtLb-- In
Cooling Fan Belt Pulley Bolt10--89
Socket Bolt2317--
Tighten The Bolt200 / 90_148 / 90_--
End Cover Bolt10--89
Crankshaft Bearing Cap Bolt55 / 90_41 / 90_--
Ball Bearing45 / 90_33 / 90_--
Camshaft Sprocket Bolt25 / 90_18 / 90_--
Oil Pump Sprocket Bolt2518--
Piston
ApplicationNSmLb-- FtLb-- In
Connecting Rod Bolt35 / 90_26 / 90_--
Flywheel
ApplicationNSmLb-- FtLb-- In
12-- Sided Stretch Bolt45 / 90_33 / 90_--
Page 553 of 2053
OM600 ENGINE MECHANICAL 1B3 -- 3
D AEW OO M Y_2000
Cylinder Head
ApplicationNSmLb-- FtLb-- In
Prechamber Threaded Ring13096--
Cylinder Head Cover Bolt10--89
Fuel Injsction Pipe Nut1813--
Socket Bolt2518--
Fuel Filter Pipe Bolt2518--
Idle Pulley Bolt2317--
Damper Bolt2115--
Camshaft Bearing Cap Bolt2518--
Camshaft Sprocket Bolt25 / 90_18 / 90_--
Exhaust Pipe Bolt& Nut2518--
Chain Tensioner8059--
Injection Nozzle4030--
Intake Manifold Not2518--
Injection Nozzle Pipe Not1813--
Oil Dipstick Tube Bolt10--89
Screw Plug M18 x 155037--
Cam Support & Shaft
ApplicationNSmLb-- FtLb-- In
Stud Bolt12--106
Exhaust Manifold Not2518--
CamShaft Bearing Cap Bolt2518--
12-- Sided Bolt (M11)25 / 90_18 / 90_--
Timing Cover
ApplicationNSmLb-- FtLb-- In
Oil Pan Bolt -- Socket Bolt10--89
Oil Pan Bolt--M610--89
Oil Pan Bolt--M232317--
Belt Pulley Bolt3224--
Guide Pulley Bolt4--35
Guide Pulley Bracket Nut2317--
Chain Tensioner8059--
Tesioning Lever Bolt2317--