Page 660 of 2189
Synchro Sleeve, Synchro Hub
Inspection
1,Inspect gear teeth on all synchro hubs and synchro
sleeves for rounded off corners. which indicates
Install each synchro hub in its mating synchro
sleeve and check for freedom of movement.
NOTE: lf replacement is required, always replace
the synchro sleeve and synchro hub as a set.
Installation
When assembling the synchro sleeve and synchro hub,
be sure to match the three sets of longer teeth (120
degrees apart) on the synchro sleeve with the three sets
of deeper grooves in the synchro hub.
CAUTION: Do noi install tho synchro sleeve with its
longer toeth in the synchro hub slots, because it will
damage the spring ring.
SYNCItROSLEEVCLONGER TEETH
13-80
Page 661 of 2189
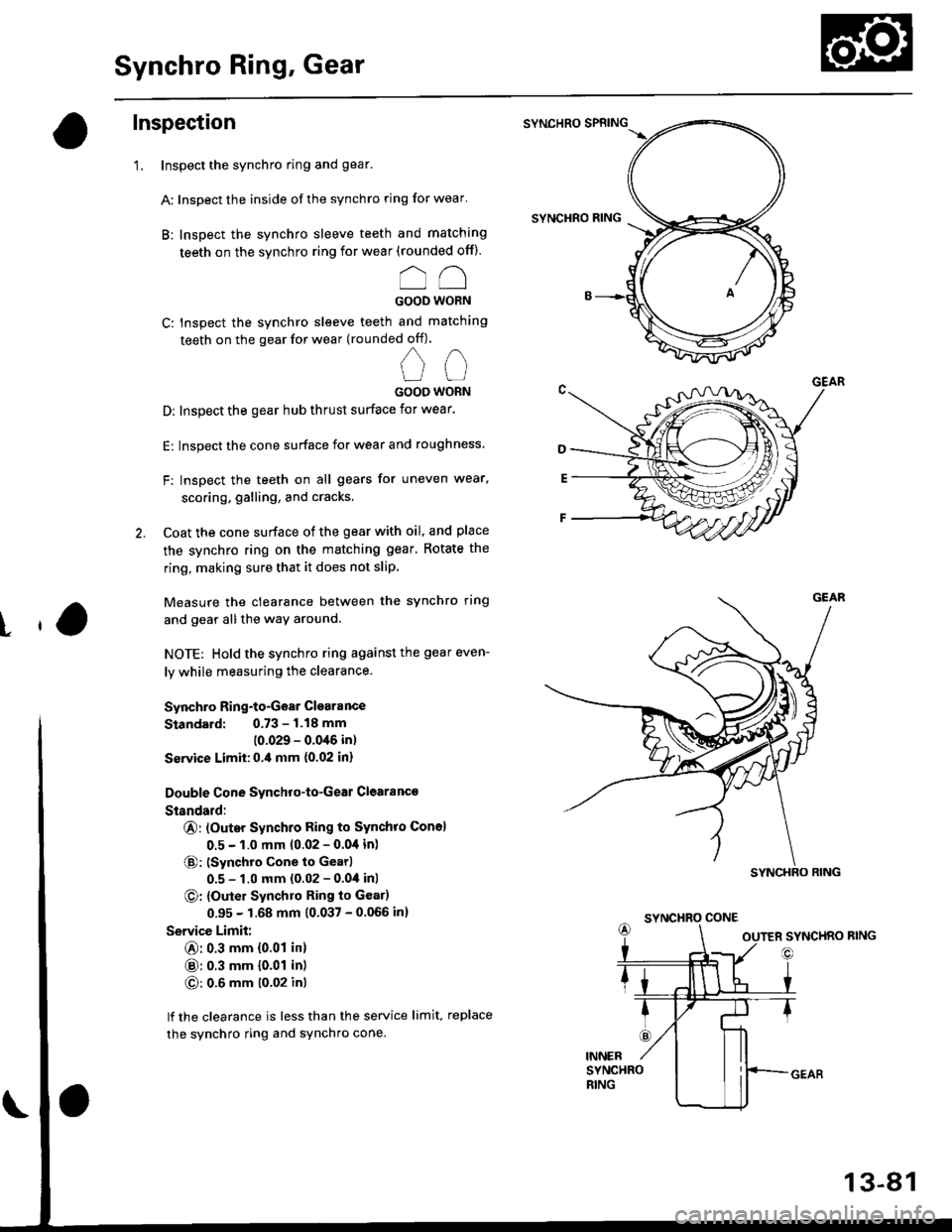
Synchro Ring, Gear
Inspection
'1. Inspect the synchro ring and gear.
A: Inspect the inside of the synchro ring for wear'
B: Inspect the synchro sleeve teeth and matching
teeth on the synchro ring for wear (rounded off).
oo
GOOD WORN
C: Inspect the synchro sleeve teeth and matching
teeth on the gear for wear (rounded off).
nn
UUGOOO WORN
D: Inspect the gear hub thrust surface for wear.
E: Inspect the cone surface for wear and roughness.
F: Inspect the teeth on all gears for uneven wear,
scoring, galling, and cracks'
2. Coat the cone surface of the gear with oil, and place
the synchro ring on the matching gear. Rotate the
ring, making sure that it does not slip
Measure the clearance between the synchro ring
and gear allthe way around.
NOTE: Hold the synchro ring against the gear even-
ly while measuring the clearance.
Synchro Ring-to-Gear Clearance
Standard: 0.73 - 1.18 mm
(0.029 - 0.0'16 in)
Ssrvice Limit:0.,0 mm {0.02 in}
Double Cone Synchro-to-Geal Clearanc€
Standald:
@: (Outer Synchro Ring to Synchro Con6l
0.5 - 1.0 mm 10.02 - 0.04 in)
@: (Synchro cone to Gearl
0.5 - 1.0 mm (0.02 - 0.04 inl
O: {Outer Synchlo Ring to Gear)
0.95 - 1.68 mm (0.037 - 0.066 in)
Service Limit:
@: 0.3 mm {0.01 in}
@: 0.3 mm {0.01 in)
O: 0.6 mm t0'02 inl
lf the clearance is less than the service limit, replace
the synchro ring and sYnchro cone.
SYNCHRO SPRING
SYNCHRO RING
t
SYNCHRO CONE
13-81
Page 662 of 2189
Differential
Index
FINAL DRIVEN GEARInspect tor wear and damage.
80 mm SHIMSelection, page'13,84
101 N.m {10.3 kgtm,74.5 lbf.ft)Left-hand threadsBALL BEAFINGInspect foa wear and ooeration.
13-82
Backlash Inspection
1. Place the differential assembly on V-blocks and installboth axles.
Measure the backlash of both pinion gears. lf thebacklash is not within the standard, replace the dif,ferential carrier.
Standard (New): 0.05 - 0.15 mm (0.002 - 0.006 inl
DIAL INDICATOR
Page 663 of 2189
rla
Final Driven Gear Replacement
'1. Remove the bolts in a crisscross pattern in several
steps, and remove the final driven gear from the dif-
ferential carrier.
NOTE: The final driven gear bolts have left-hand
threads,
12 x 1.0 mm101 N.m {'10.3 kgf.m,74.5 lbf.ftlLeft hand
FINAL DRIVEN GEARChamfer on inside daameter offinal driven gear faces carrier.
2. Install the final driven gear by tightening the bolts
in a crisscross pattern in several steps.NOTE: Drive the bearings squarely until they bot-
tom against the carrier.
BALL BEARING
13-83
Bearing Replacement
NOTE: Check the ball bearings for wear and rough rota-
tion. lf bearings are OK, removal is not necessary.
1. Remove the ball bearings using a standard bearing
puller and bearing separator as shown.
BEARING PULLER
BEARING SEPARATOR
lCommerciallyavailab16)
BALL BEARING
2. Install new ball bearings using the special tool as
shown.
Page 666 of 2189
Clutch Housing Bearing
Replacement
Mainshaft:
L Remove the ball bearing using the special tools asshown.
3/81_ 16 SLIDE HAMMER{commercially available)
ADJUSTAELE BEARINGPULLER, 25 - 40 mm07736 - A01000A
2. Remove the oil seal from the clutch housino.
13-86
CLUTCH HOUSING
BALL BEARING
(
3. Drive the new oil seal into the clutch housing usingthe special tools as shown.
HANOLE07749 - 0010000
ATTACHMENT, 42 x 47 mm07746 - 0010300
4.
OIL S€ALReplace.
Drive the ball bearing into the clutch housing using
the specialtools as shown.
HANDLE07749 - 0010000ATTACHMENT, 52 x 55 mm07746 - 0010il{)0
PILOT, 28 mm07746 - 0041100
Page 667 of 2189
Countershaft:
1. Bend the tab on the lock washer down, then remove
the bolt and bearing retainer plate.
BEARING RETAINER PLATE
cLutcH tlouslNG
Remove the needle bearing using the special tools
as shown, then remove the oil guide plate'
3/8' - 16 SLIOE HAMMER(CommerciallY available)
^ LOCK WASHERg Reolace.
d---""-
t
ADJUSTABLE BEARING
PULLER,25 - {o mm07736 - Aolmo A
3. Position the oil guide plate and new needle bearing
in the bore of the ctutch housing, then drive in the
needle bearing using the special tools as shown
NOTE: Position the needle bearing with the oil hole
facing up.
NEEDLE
OIL HOLE
NEEDLEBEARING
Install the bearing retainer plate and new lock wash-
er, then bend the tab against the bolt head'
8x10mm15 N'm (1.5 kgt'm, rl |bt'ft)
LOCKWASHERReplace.
13-47
Page 671 of 2189
Transmission
ReassemblY
1. Install the new oil seal
2. Set the change Piece.
3. Install the shift rod
4. Install the steel ball' the spring, and the set screw'
5. Install the spring washer and change piece attach-
ing bolt.
6. Install the shift rod boots.
8x1.0mm31 N.m 13.1 kg-m,22lb-ltl
CHANGEPIECE
@:4OIL SEALReplace.SPRINGWASHER
7. Install the oil chamber Plate'
6 x '1.0 mm12 N.m (1.2 kg-m,9lb-ft|
SPRING
, /L.256fim B()(
@ / t't o'ti"l I
{zw"y-6@
q
10.
Set the spring washer and the washer'
lnstall the mainshaft, the countershaft, and the shift
fork assemblies.
NOTE: Align the finger of the interlock with the
groove in the shift fork shaft.
SHIFT FORKS
13-91
Page 676 of 2189
Oil Seals
Replacement
Trrn3mirdon Housing:
1. Remove the oil seal from the transmission housing.
Install the oil seal into the transmission housingusing the sp€cial tools as shown,
HANDLE07149 - d)l(xxto
OIL SEALReplace.
HOUSING
13-96
OIL SEALReplace.
{
Clutch Housing:
1. Remove the oil seal from the clutch housing.
OIL SEALReplace.
Install the oil seal into the clutch housing using thespecialtools as shown.
HANDTI0t?a9 - 001o(xto