Page 1564 of 1938
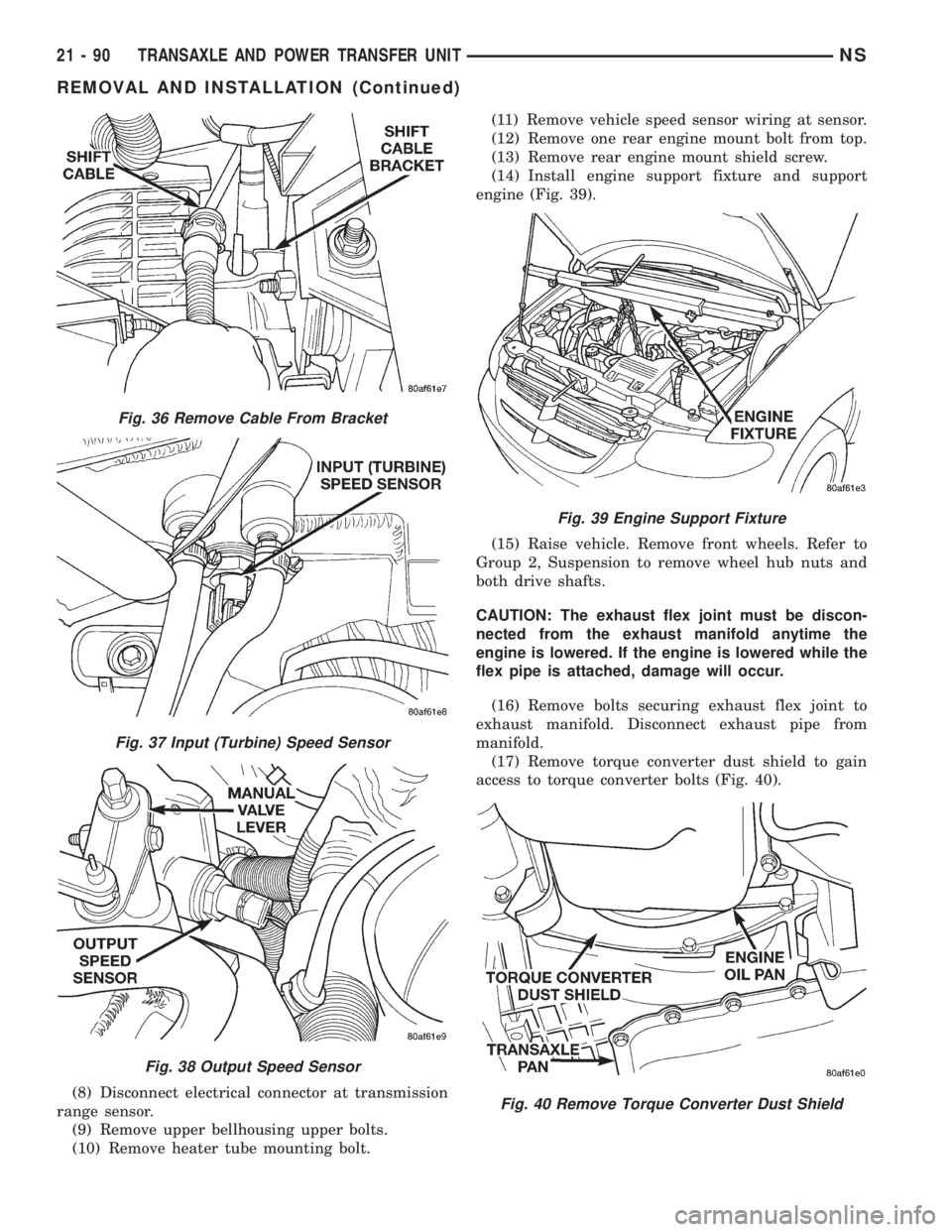
(8) Disconnect electrical connector at transmission
range sensor.
(9) Remove upper bellhousing upper bolts.
(10) Remove heater tube mounting bolt.(11) Remove vehicle speed sensor wiring at sensor.
(12) Remove one rear engine mount bolt from top.
(13) Remove rear engine mount shield screw.
(14) Install engine support fixture and support
engine (Fig. 39).
(15) Raise vehicle. Remove front wheels. Refer to
Group 2, Suspension to remove wheel hub nuts and
both drive shafts.
CAUTION: The exhaust flex joint must be discon-
nected from the exhaust manifold anytime the
engine is lowered. If the engine is lowered while the
flex pipe is attached, damage will occur.
(16) Remove bolts securing exhaust flex joint to
exhaust manifold. Disconnect exhaust pipe from
manifold.
(17) Remove torque converter dust shield to gain
access to torque converter bolts (Fig. 40).
Fig. 36 Remove Cable From Bracket
Fig. 37 Input (Turbine) Speed Sensor
Fig. 38 Output Speed Sensor
Fig. 39 Engine Support Fixture
Fig. 40 Remove Torque Converter Dust Shield
21 - 90 TRANSAXLE AND POWER TRANSFER UNITNS
REMOVAL AND INSTALLATION (Continued)
Page 1565 of 1938
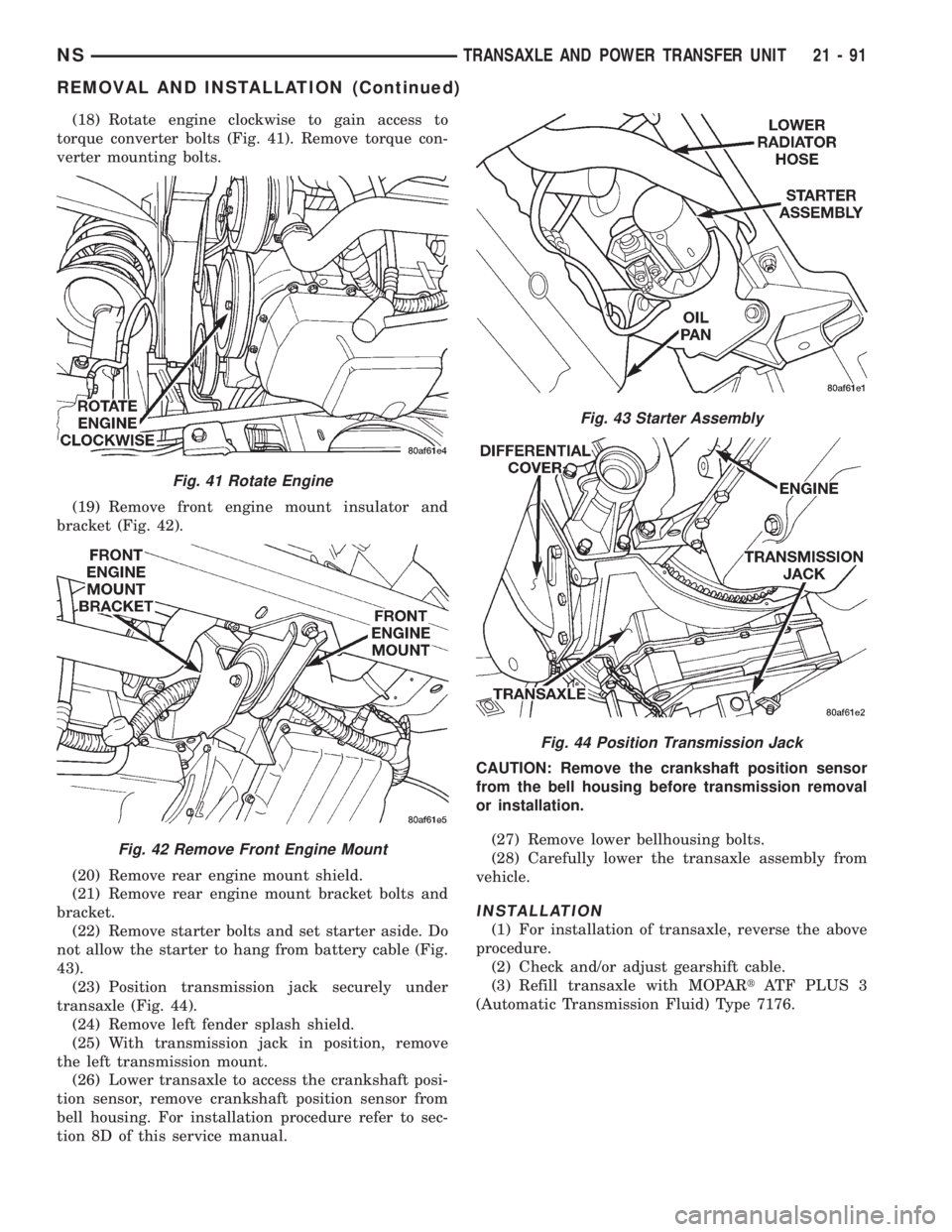
(18) Rotate engine clockwise to gain access to
torque converter bolts (Fig. 41). Remove torque con-
verter mounting bolts.
(19) Remove front engine mount insulator and
bracket (Fig. 42).
(20) Remove rear engine mount shield.
(21) Remove rear engine mount bracket bolts and
bracket.
(22) Remove starter bolts and set starter aside. Do
not allow the starter to hang from battery cable (Fig.
43).
(23) Position transmission jack securely under
transaxle (Fig. 44).
(24) Remove left fender splash shield.
(25) With transmission jack in position, remove
the left transmission mount.
(26) Lower transaxle to access the crankshaft posi-
tion sensor, remove crankshaft position sensor from
bell housing. For installation procedure refer to sec-
tion 8D of this service manual.CAUTION: Remove the crankshaft position sensor
from the bell housing before transmission removal
or installation.
(27) Remove lower bellhousing bolts.
(28) Carefully lower the transaxle assembly from
vehicle.
INSTALLATION
(1) For installation of transaxle, reverse the above
procedure.
(2) Check and/or adjust gearshift cable.
(3) Refill transaxle with MOPARtATF PLUS 3
(Automatic Transmission Fluid) Type 7176.
Fig. 41 Rotate Engine
Fig. 42 Remove Front Engine Mount
Fig. 43 Starter Assembly
Fig. 44 Position Transmission Jack
NSTRANSAXLE AND POWER TRANSFER UNIT 21 - 91
REMOVAL AND INSTALLATION (Continued)
Page 1566 of 1938
OIL PUMP SEAL
REMOVAL
INSTALLATION
DISASSEMBLY AND ASSEMBLY
VALVE BODY RECONDITION
Fig. 45 Remove Oil Pump Seal
Fig. 46 Install Oil Pump Seal
Fig. 47 Transmission Range Sensor Screw
Fig. 48 Transmission Range Sensor Removed
Fig. 49 Manual Shaft and Rooster Comb
21 - 92 TRANSAXLE AND POWER TRANSFER UNITNS
REMOVAL AND INSTALLATION (Continued)
Page 1569 of 1938
TRANSAXLE DISASSEMBLE
NOTE: Tag all clutch pack assemblies, as they are
removed, for reassembly identification.
CAUTION: Do not intermix clutch discs or plates as
the unit might then fail.
(1) Remove input and output speed sensors.
(2) Remove transaxle solenoid pack (Fig. 59).
Fig. 58 Low/Reverse Switch Valve And T/C Limit
Valve
Fig. 59 Remove Solenoid Pack
Fig. 60 Remove Oil Pan Bolts
Fig. 61 Remove Oil Pan
Fig. 62 Remove Oil Filter
NSTRANSAXLE AND POWER TRANSFER UNIT 21 - 95
DISASSEMBLY AND ASSEMBLY (Continued)
Page 1572 of 1938
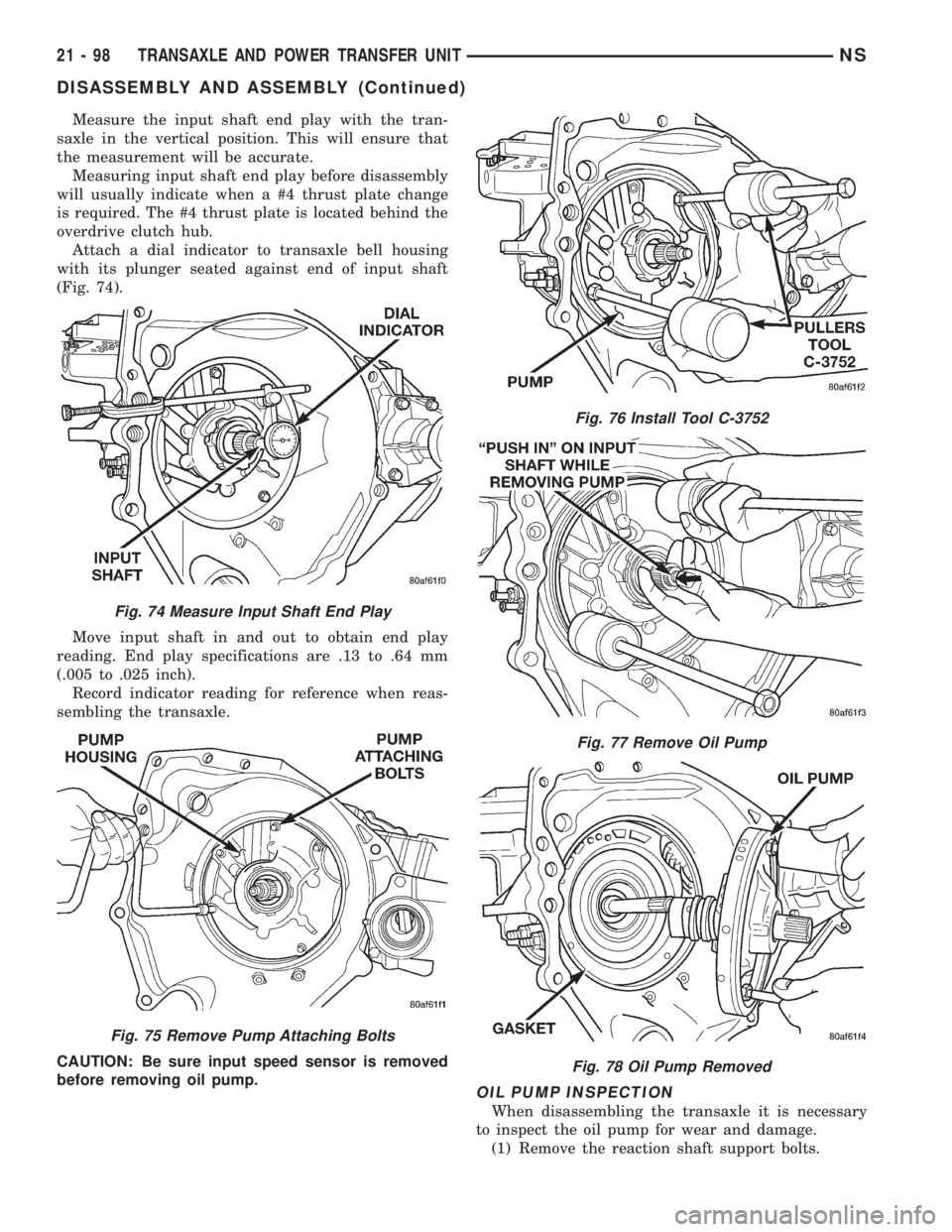
Measure the input shaft end play with the tran-
saxle in the vertical position. This will ensure that
the measurement will be accurate.
Measuring input shaft end play before disassembly
will usually indicate when a #4 thrust plate change
is required. The #4 thrust plate is located behind the
overdrive clutch hub.
Attach a dial indicator to transaxle bell housing
with its plunger seated against end of input shaft
(Fig. 74).
Move input shaft in and out to obtain end play
reading. End play specifications are .13 to .64 mm
(.005 to .025 inch).
Record indicator reading for reference when reas-
sembling the transaxle.
CAUTION: Be sure input speed sensor is removed
before removing oil pump.
OIL PUMP INSPECTION
When disassembling the transaxle it is necessary
to inspect the oil pump for wear and damage.
(1) Remove the reaction shaft support bolts.
Fig. 74 Measure Input Shaft End Play
Fig. 75 Remove Pump Attaching Bolts
Fig. 76 Install Tool C-3752
Fig. 77 Remove Oil Pump
Fig. 78 Oil Pump Removed
21 - 98 TRANSAXLE AND POWER TRANSFER UNITNS
DISASSEMBLY AND ASSEMBLY (Continued)
Page 1608 of 1938
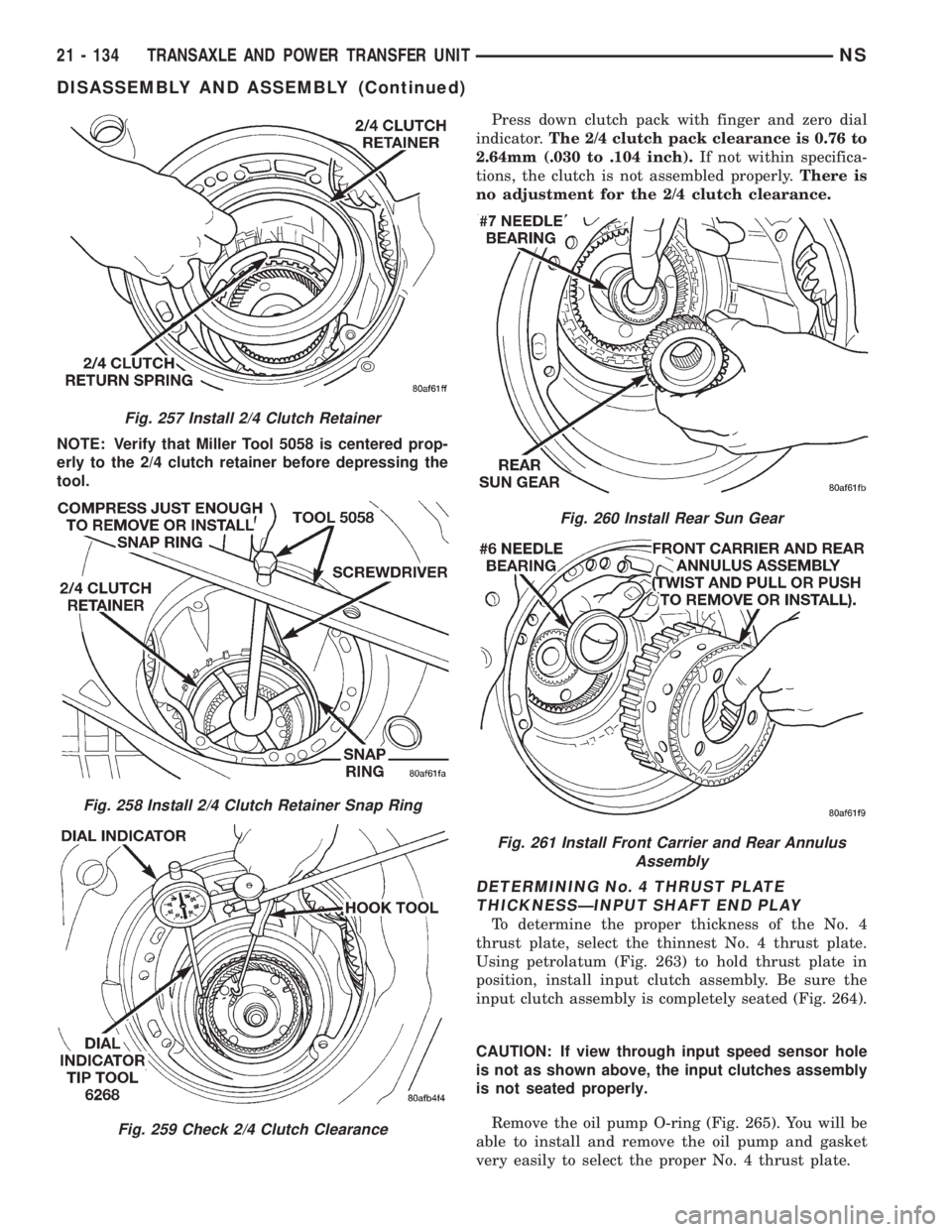
NOTE: Verify that Miller Tool 5058 is centered prop-
erly to the 2/4 clutch retainer before depressing the
tool.Press down clutch pack with finger and zero dial
indicator.The 2/4 clutch pack clearance is 0.76 to
2.64mm (.030 to .104 inch).If not within specifica-
tions, the clutch is not assembled properly.There is
no adjustment for the 2/4 clutch clearance.
DETERMINING No. 4 THRUST PLATE
THICKNESSÐINPUT SHAFT END PLAY
To determine the proper thickness of the No. 4
thrust plate, select the thinnest No. 4 thrust plate.
Using petrolatum (Fig. 263) to hold thrust plate in
position, install input clutch assembly. Be sure the
input clutch assembly is completely seated (Fig. 264).
CAUTION: If view through input speed sensor hole
is not as shown above, the input clutches assembly
is not seated properly.
Remove the oil pump O-ring (Fig. 265). You will be
able to install and remove the oil pump and gasket
very easily to select the proper No. 4 thrust plate.
Fig. 257 Install 2/4 Clutch Retainer
Fig. 258 Install 2/4 Clutch Retainer Snap Ring
Fig. 259 Check 2/4 Clutch Clearance
Fig. 260 Install Rear Sun Gear
Fig. 261 Install Front Carrier and Rear Annulus
Assembly
21 - 134 TRANSAXLE AND POWER TRANSFER UNITNS
DISASSEMBLY AND ASSEMBLY (Continued)
Page 1609 of 1938
NOTE: Use screw-in dowels or phillips-head screw-
drivers to align pump to case.CAUTION: Be sure to reinstall O-ring on oil pump
after selecting the proper No. 4 thrust plate.
Measure the input shaft end play with the tran-
saxle in the vertical position. This will ensure that
the measurement will be accurate.
NOTE: Input shaft end play must be .005 to .025
inch.
For example, if end play reading is .055 inch, select
No. 4 Thrust Plate which is .071 to .074 thick. This
should provide an input shaft end play reading of
.020 inch which is within specifications.
Fig. 262 Install Front Sun Gear Assembly
Fig. 263 Select Thinnest No. 4 Thrust Plate
Fig. 264 View Through Input Speed Sensor Hole
Fig. 265 Remove Oil Pump O-Ring
Fig. 266 Measure Input Shaft End Play
NSTRANSAXLE AND POWER TRANSFER UNIT 21 - 135
DISASSEMBLY AND ASSEMBLY (Continued)
Page 1613 of 1938
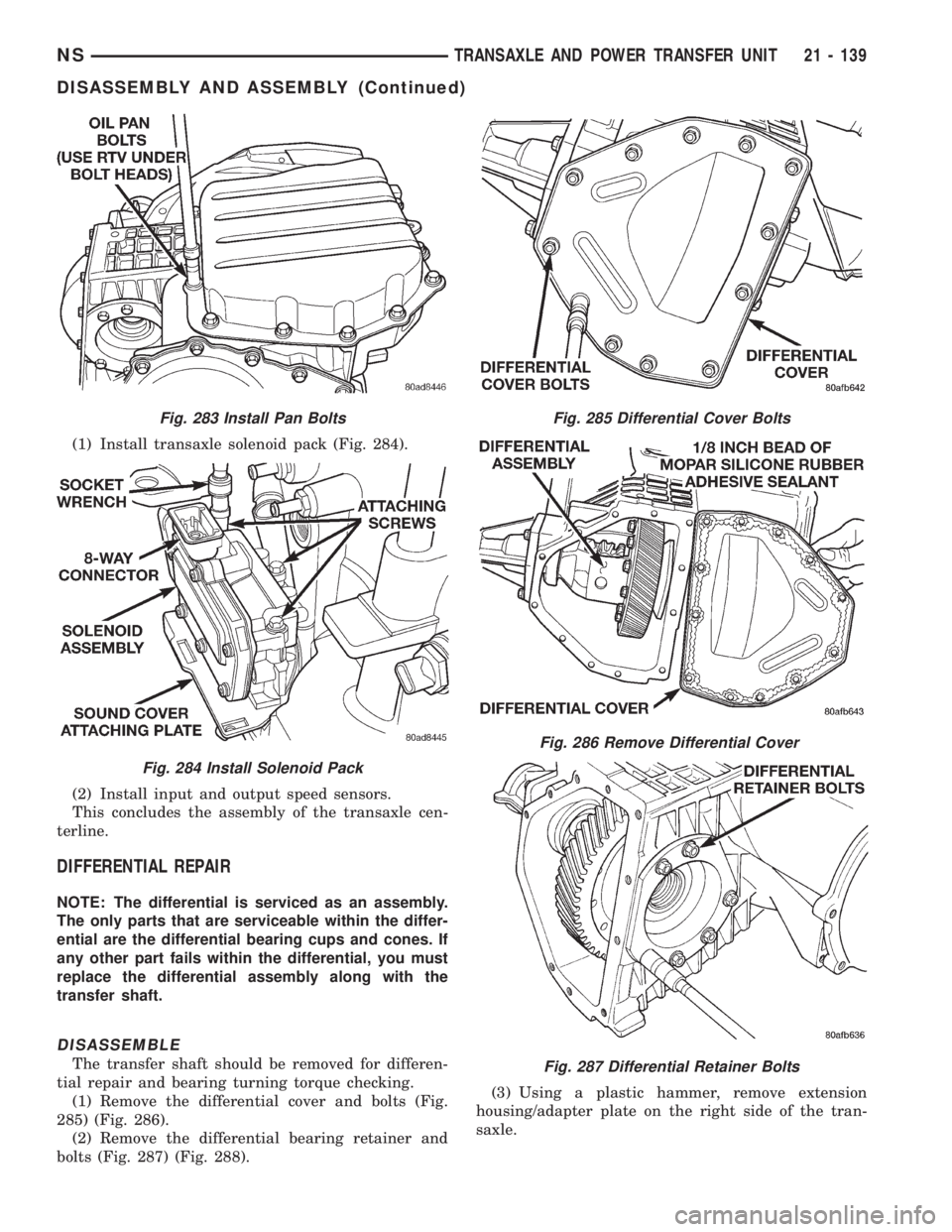
(1) Install transaxle solenoid pack (Fig. 284).
(2) Install input and output speed sensors.
This concludes the assembly of the transaxle cen-
terline.
DIFFERENTIAL REPAIR
NOTE: The differential is serviced as an assembly.
The only parts that are serviceable within the differ-
ential are the differential bearing cups and cones. If
any other part fails within the differential, you must
replace the differential assembly along with the
transfer shaft.
DISASSEMBLE
The transfer shaft should be removed for differen-
tial repair and bearing turning torque checking.
(1) Remove the differential cover and bolts (Fig.
285) (Fig. 286).
(2) Remove the differential bearing retainer and
bolts (Fig. 287) (Fig. 288).(3) Using a plastic hammer, remove extension
housing/adapter plate on the right side of the tran-
saxle.
Fig. 283 Install Pan Bolts
Fig. 284 Install Solenoid Pack
Fig. 285 Differential Cover Bolts
Fig. 286 Remove Differential Cover
Fig. 287 Differential Retainer Bolts
NSTRANSAXLE AND POWER TRANSFER UNIT 21 - 139
DISASSEMBLY AND ASSEMBLY (Continued)