Page 248 of 873
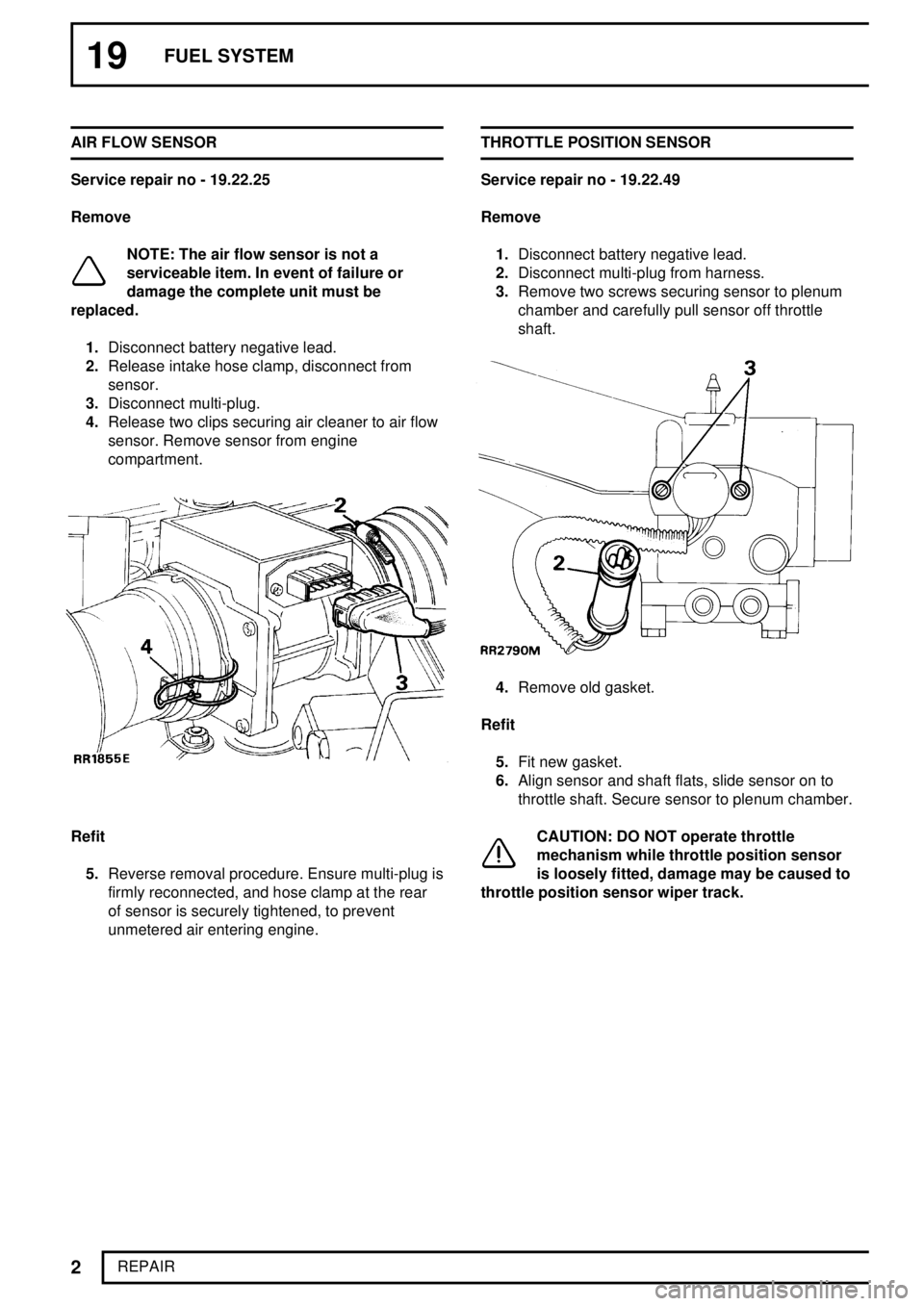
19FUEL SYSTEM
2
REPAIR AIR FLOW SENSOR
Service repair no - 19.22.25
Remove
NOTE: The air flow sensor is not a
serviceable item. In event of failure or
damage the complete unit must be
replaced.
1.Disconnect battery negative lead.
2.Release intake hose clamp, disconnect from
sensor.
3.Disconnect multi-plug.
4.Release two clips securing air cleaner to air flow
sensor. Remove sensor from engine
compartment.
Refit
5.Reverse removal procedure. Ensure multi-plug is
firmly reconnected, and hose clamp at the rear
of sensor is securely tightened, to prevent
unmetered air entering engine.THROTTLE POSITION SENSOR
Service repair no - 19.22.49
Remove
1.Disconnect battery negative lead.
2.Disconnect multi-plug from harness.
3.Remove two screws securing sensor to plenum
chamber and carefully pull sensor off throttle
shaft.
4.Remove old gasket.
Refit
5.Fit new gasket.
6.Align sensor and shaft flats, slide sensor on to
throttle shaft. Secure sensor to plenum chamber.
CAUTION: DO NOT operate throttle
mechanism while throttle position sensor
is loosely fitted, damage may be caused to
throttle position sensor wiper track.
Page 249 of 873
MFI
3
REPAIR IDLE AIR CONTROL VALVE
Service repair no - 19.22.54
Remove
1.Disconnect battery negative lead.
2.Disconnect multi-plug.
3.Unscrew valve from rear plenum chamber.
4.Remove washer.
Refit
5.FitNEWsealing washer.
NOTE: If same idle air control valve is
being refitted clean sealing compounds
from threads. Apply Loctite 241 to threads
of valve before reassembly.
6.Tighten valve to
20 Nm.
7.Reverse removal procedure.VEHICLE SPEED SENSOR
Service repair no - 88.30.14
The vehicle speed sensor is located in the LH side of
the transfer box.
Remove
1.Place vehicle on lift, apply parking brake.
2.Disconnect battery negative lead.
3.Raise lift, disconnect multiplug from vehicle
speed sensor.
4.Remove screw securing sensor to transfer box.
5.Remove vehicle speed sensor
Refit
6.Reverse removal procedure.
Page 251 of 873
MFI
5
REPAIR INERTIA FUEL SHUTOFF SWITCH
Service repair no - 18.30.35
The inertia fuel shutoff switch is located on the
bulkhead next to the washer reservoir under bonnet
[hood].
Remove
1.Disconnect battery negative lead.
2.Disconnect multiplug from inertia switch.
3.Remove 2 screws securing inertia switch to
mounting bracket.
4.Remove inertia switch.
Refit
5.Position inertia switch to mounting bracket and
secure with screws.
6.Connect multiplug to inertia switch.
7.Reconnect battery negative lead.ENGINE FUEL TEMPERATURE SENSOR
Service repair no - 19.22.08
Remove
NOTE: Fuel leakage will not occur when
sensor is removed from fuel rail, therefore
it is not necessary to depressurise the fuel
system.
1.Disconnect battery negative lead.
2.Disconnect multi-plug from sensor.
3.Release sensor from fuel feed rail.
Refit
4.Reverse removal procedure. Ensure sensor is
tightened securely in fuel rail.
Page 252 of 873
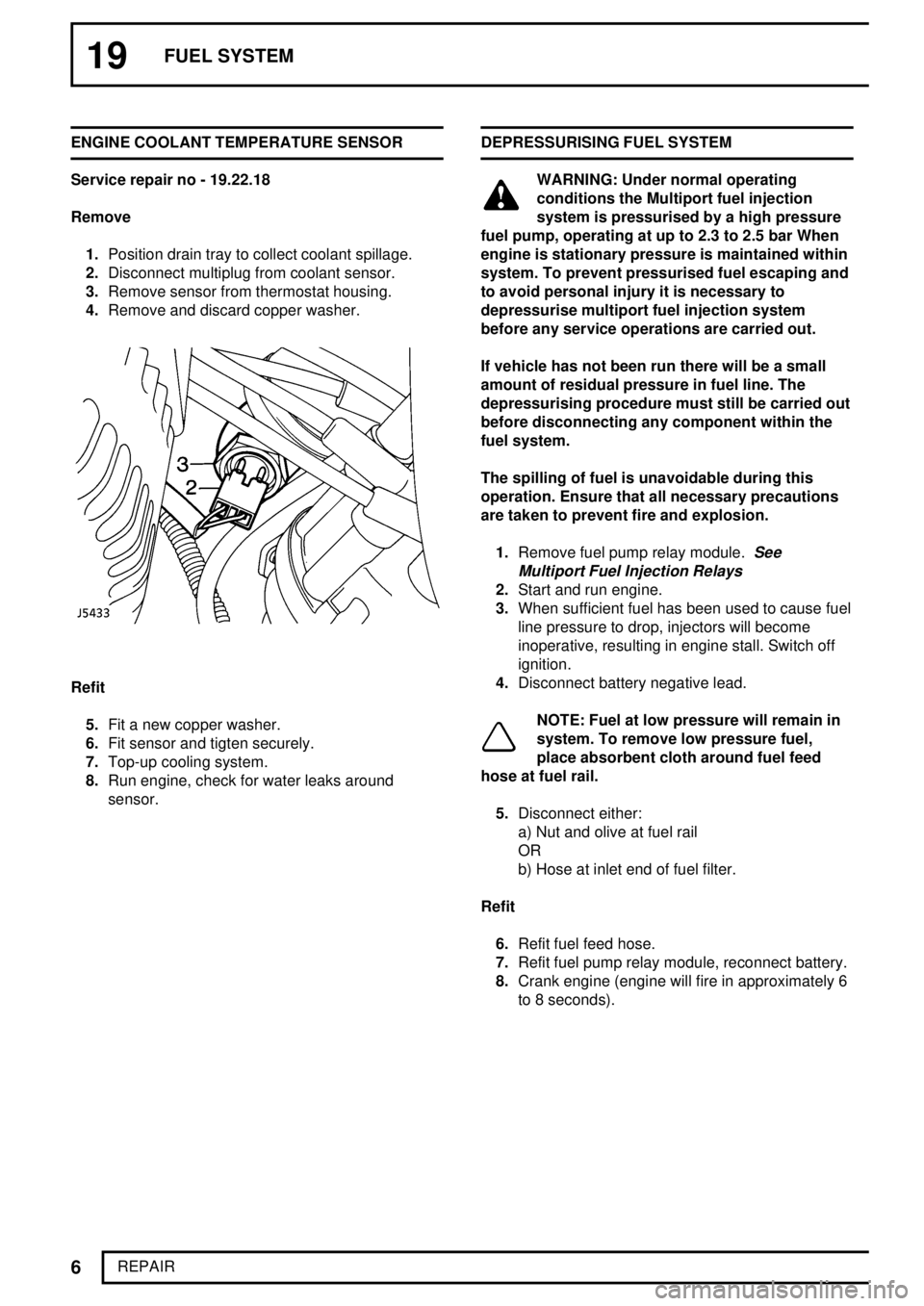
19FUEL SYSTEM
6
REPAIR ENGINE COOLANT TEMPERATURE SENSOR
Service repair no - 19.22.18
Remove
1.Position drain tray to collect coolant spillage.
2.Disconnect multiplug from coolant sensor.
3.Remove sensor from thermostat housing.
4.Remove and discard copper washer.
Refit
5.Fit a new copper washer.
6.Fit sensor and tigten securely.
7.Top-up cooling system.
8.Run engine, check for water leaks around
sensor.DEPRESSURISING FUEL SYSTEM
WARNING: Under normal operating
conditions the Multiport fuel injection
system is pressurised by a high pressure
fuel pump, operating at up to 2.3 to 2.5 bar When
engine is stationary pressure is maintained within
system. To prevent pressurised fuel escaping and
to avoid personal injury it is necessary to
depressurise multiport fuel injection system
before any service operations are carried out.
If vehicle has not been run there will be a small
amount of residual pressure in fuel line. The
depressurising procedure must still be carried out
before disconnecting any component within the
fuel system.
The spilling of fuel is unavoidable during this
operation. Ensure that all necessary precautions
are taken to prevent fire and explosion.
1.Remove fuel pump relay module.
See
Multiport Fuel Injection Relays
2.Start and run engine.
3.When sufficient fuel has been used to cause fuel
line pressure to drop, injectors will become
inoperative, resulting in engine stall. Switch off
ignition.
4.Disconnect battery negative lead.
NOTE: Fuel at low pressure will remain in
system. To remove low pressure fuel,
place absorbent cloth around fuel feed
hose at fuel rail.
5.Disconnect either:
a) Nut and olive at fuel rail
OR
b) Hose at inlet end of fuel filter.
Refit
6.Refit fuel feed hose.
7.Refit fuel pump relay module, reconnect battery.
8.Crank engine (engine will fire in approximately 6
to 8 seconds).
Page 253 of 873
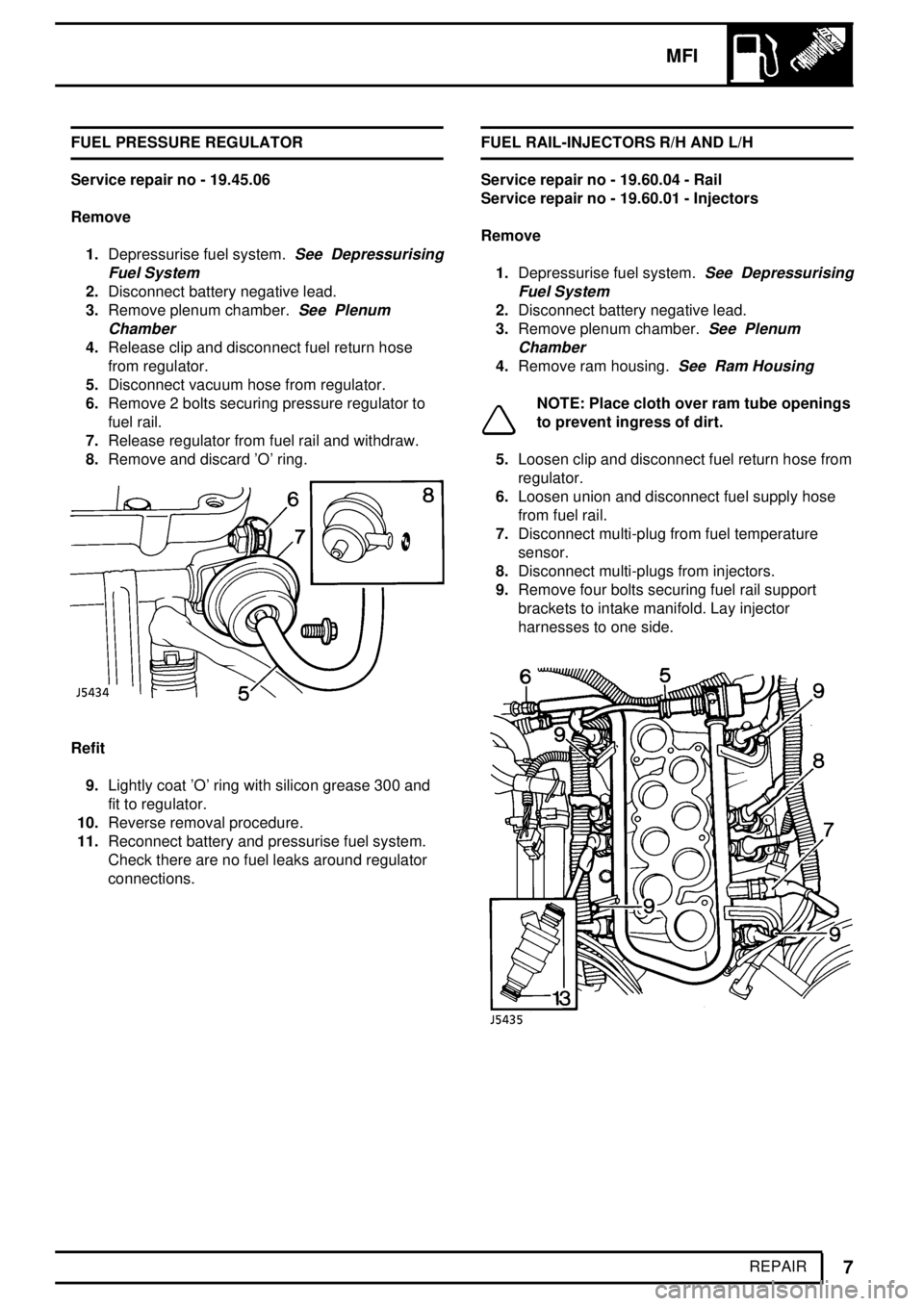
MFI
7
REPAIR FUEL PRESSURE REGULATOR
Service repair no - 19.45.06
Remove
1.Depressurise fuel system.
See Depressurising
Fuel System
2.Disconnect battery negative lead.
3.Remove plenum chamber.
See Plenum
Chamber
4.Release clip and disconnect fuel return hose
from regulator.
5.Disconnect vacuum hose from regulator.
6.Remove 2 bolts securing pressure regulator to
fuel rail.
7.Release regulator from fuel rail and withdraw.
8.Remove and discard 'O' ring.
Refit
9.Lightly coat 'O' ring with silicon grease 300 and
fit to regulator.
10.Reverse removal procedure.
11.Reconnect battery and pressurise fuel system.
Check there are no fuel leaks around regulator
connections.FUEL RAIL-INJECTORS R/H AND L/H
Service repair no - 19.60.04 - Rail
Service repair no - 19.60.01 - Injectors
Remove
1.Depressurise fuel system.
See Depressurising
Fuel System
2.Disconnect battery negative lead.
3.Remove plenum chamber.
See Plenum
Chamber
4.Remove ram housing.See Ram Housing
NOTE: Place cloth over ram tube openings
to prevent ingress of dirt.
5.Loosen clip and disconnect fuel return hose from
regulator.
6.Loosen union and disconnect fuel supply hose
from fuel rail.
7.Disconnect multi-plug from fuel temperature
sensor.
8.Disconnect multi-plugs from injectors.
9.Remove four bolts securing fuel rail support
brackets to intake manifold. Lay injector
harnesses to one side.
Page 254 of 873

19FUEL SYSTEM
8
REPAIR 10.Remove fuel rail and injectors.
11.Remove injector retaining clips, ease injectors
from rail. Remove and discard 'O' rings from
injectors.
12.Remove fuel pressure regulator if required.
Refit
13.FitNEW'O' rings, to injectors. Lightly coat 'O'
rings with silicon grease 300. Insert injectors into
fuel rail, multi-plug connections facing outwards.
14.Refit retaining clips.
CAUTION: Care must be taken when
refitting the fuel rail and injectors to intake
manifold to prevent damage to 'O' rings.
15.Fit aNEW'O' ring to pressure regulator lightly
coat 'O' ring with silicon grease 300 and secure
regulator to the fuel rail.
16.Fit fuel rail and heater pipe assemblies to intake
manifold. Secure rail and pipes in position with
five bolts.
17.Reverse removal procedure. 2 to 7.
18.Pressurise fuel system and check for fuel leaks
around injectors and pressure regulator.PLENUM CHAMBER
Service repair no - 19.22.46
Includes throttle levers and throttle disc
Remove
1.Disconnect battery negative lead.
2.Disconnect electrical multi-plug from bypass air
valve.
3.Disconnect vacuum hose adjacent to bypass air
valve.
4.Mark an identification line on throttle cable outer
to assist re-assembly.
5.Remove clevis pin from throttle cable.
6.Pry adjustment thumb wheel from throttle
bracket. Lay cable aside.
7.Remove retaining clip and clevis pin from kick
down cable (automatic vehicles).
8.Apply adhesive tape behind rear adjustment nut
on kick down cable to prevent nut moving.
9.Remove front lock nut. Remove cable and lay
aside.
10.Remove cruise control vacuum hose.
11.Remove intake hose from neck of plenum
chamber.
12.Disconnect throttle position sensor multi-plug.
13.Remove PCV breather hose.
14.Disconnect two coolant hoses and plug each
hose to prevent excessive loss of coolant.
Identify each hose for re-assembly.
Page 255 of 873
MFI
9
REPAIR
15.Remove distributor vacuum hose.
16.Release two screws and remove throttle position
sensor.
17.Remove six screws securing plenum chamber.
Remove plenum chamber.
18.Remove air idle air control valve hose.Throttle lever assembly - remove
19.If fitted - unclip cruise control actuator link. Hold
throttle fully open, release link from countershaft
assembly. Carefully return lever assembly to
close throttle.
20.Release tension on inboard throttle spring.
21.Bend back lock washer tabs.
22.Hold throttle stop lever in closed position,
release nut from throttle shaft.
23.Release tension on outboard throttle spring.
24.Remove overtravel spring.
Page 260 of 873
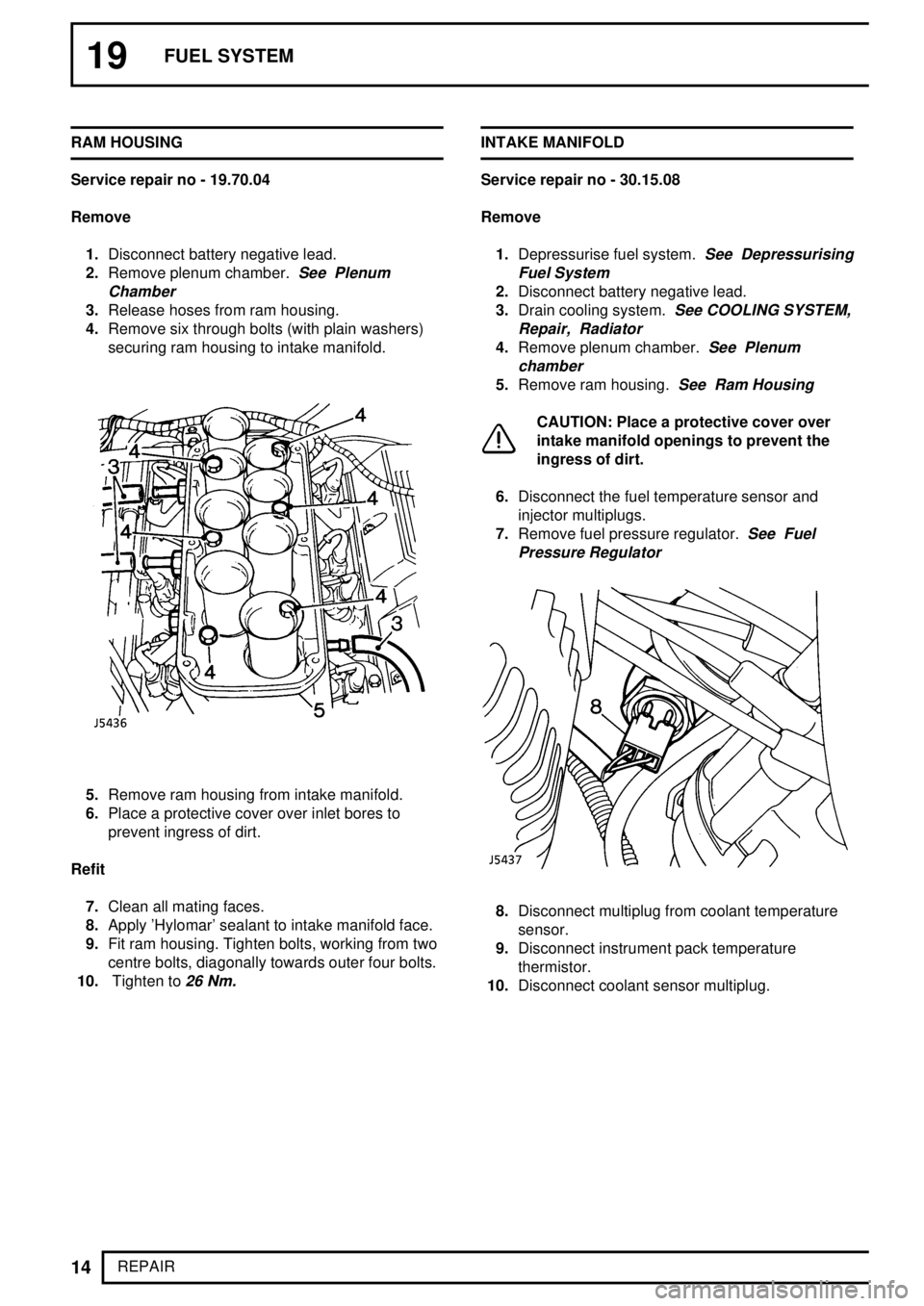
19FUEL SYSTEM
14
REPAIR RAM HOUSING
Service repair no - 19.70.04
Remove
1.Disconnect battery negative lead.
2.Remove plenum chamber.
See Plenum
Chamber
3.Release hoses from ram housing.
4.Remove six through bolts (with plain washers)
securing ram housing to intake manifold.
5.Remove ram housing from intake manifold.
6.Place a protective cover over inlet bores to
prevent ingress of dirt.
Refit
7.Clean all mating faces.
8.Apply 'Hylomar' sealant to intake manifold face.
9.Fit ram housing. Tighten bolts, working from two
centre bolts, diagonally towards outer four bolts.
10.Tighten to
26 Nm.
INTAKE MANIFOLD
Service repair no - 30.15.08
Remove
1.Depressurise fuel system.
See Depressurising
Fuel System
2.Disconnect battery negative lead.
3.Drain cooling system.
See COOLING SYSTEM,
Repair, Radiator
4.Remove plenum chamber.See Plenum
chamber
5.Remove ram housing.See Ram Housing
CAUTION: Place a protective cover over
intake manifold openings to prevent the
ingress of dirt.
6.Disconnect the fuel temperature sensor and
injector multiplugs.
7.Remove fuel pressure regulator.
See Fuel
Pressure Regulator
8.Disconnect multiplug from coolant temperature
sensor.
9.Disconnect instrument pack temperature
thermistor.
10.Disconnect coolant sensor multiplug.