Page 304 of 873
SFI
21
REPAIR ADD: 09/95
5.Fold back loadspace carpet and sound
insulation to reveal access panel.
6.Remove 6 screws securing fuel pump access
panel.
7.Remove access panel.8.Disconnect multiplugs from fuel pump and
pressure sensor
9.Noting their fitted positions, disconnect both fuel
connections by pressing the black release
latches on each connector and pushing the
connector back down the line.
10.Care must be taken to catch any excess fuel
which may spill from the fuel lines once
removed.
11.Raise rear of vehicle.
WARNING: Support on safety stands.
Page 305 of 873
19FUEL SYSTEM
22
REPAIRADD: 09/95
12.Mark location of anti-roll [sway] bar straps.
13.Remove nuts and bolts securing anti-roll [sway]
bar straps, and allow bar to swing down clear of
tank.14.Disconnect pressure sensor breather pipe
connection.
15.Disconnect vent line quickfit connector from
liquid/vapour separator.
16.Remove torque screw cap from hose to tank
filler neck clip.
17.Loosen clip screw securing hose to tank filler
neck.
18.Release hose from filler neck and internal filler
neck breather hose from fuel tank.
19.Remove and discard fuel filler neck clip.
Page 306 of 873
SFI
23
REPAIR ADD: 09/95
20.Remove nut and bolt securing RH side of upper
fuel tank strap to chassis.
21.Remove 4 nuts and bolts securing fuel tank
cradle.
22.Remove fuel tank cradle.
23.With assistance, tilt right hand side of tank
upwards and manoeuvre through chassis to
remove.
Do not carry out further dismantling if
component is removed for access only.
24.Release vent hose from tank pressure sensor.
25.Remove vent hose from 3 fuel tank clips.
26.Using service tool LRT-19-009 loosen and
remove the metal locking ring.
27.Prise the pump from the tank opening using a
blunt instrument under the edge of the lip of the
pump flange.
CAUTION: Do not lift the pump from the
tank using the feed and return stubs.
28.Remove and discard seal.
Page 307 of 873

19FUEL SYSTEM
24
REPAIRADD: 09/95 Refit
29.Fit NEW pump seal to tank opening.
30.Carefully lower pump into tank opening, pressing
firmly on the pump top flange to allow correct
positioning.
NOTE: Ensure location tag on pump top
flange is engaged correctly to tank
opening lip.
31.Fit locking ring and tighten to
35 Nmusing
service tool LRT-19-009.
32.Fit vent hose to fuel tank clips and connect to
pressure sensor.
33.With assistance, fit fuel tank into position.
34.Fit fuel tank cradle and secure with nuts and
bolts.
35.Align upper fuel tank strap and secure with nut
and bolt.
36.Fit NEW clip to fuel filler neck hose.
37.Connect fuel filler neck internal breather to tank.
38.Connect fuel filler neck hose to tank.
39.Position fuel filler neck hose clip and tighten until
head shears.
40.Connect vent line quickfit connector to
liquid/vapour separator.
41.Connect vent line hose connection.
42.Position anti-roll [sway] bar straps and secure
with nuts and bolts.
43.Remove stand(s) and lower vehicle.
44.Connect both fuel lines to the pump by pushing
the connectors down each line square to the
pump connection until the connectors positively
latches.
45.Connect multiplugs to fuel pump and pressure
sensor.
46.Reconnect battery negative lead.
47.Refill tank with drained fuel.
48.Run the engine to check for any fuel leaks.
49.Fit access panel and secure with screws.
50.Reposition loadspace sound insulation and
carpet.
51.Fit RH luggage compartment side panel.
See
CHASSIS AND BODY, Repair, rear
compartment trim panels
52.Fit tail door tread strip and secure with screws.FUEL TANK - DRAINING - ADVANCED EVAPS
Service repair no - 19.55.02
WARNING: Before removing the fuel tank
it must be drained.
WARNING: Petrol/gasoline vapour is
highly flammable and in confined spaces
is also explosive and toxic. Always have a
fire extinguisher containing FOAM, CO2, GAS or
POWDER close at hand when handling or draining
fuel. See Introduction
CAUTION: Before disconnecting any part
of fuel system, it is imperative that all dust,
dirt and debris is removed from around
components to prevent ingress of foreign matter
into fuel system.
NOTE: Assuming the fuel tank is FULL
drain the following quantities:
Renew Fuel pump = 9 Litres (2.4 US Gallons)
Renew Fuel filler neck = 22 Litres (6 US Gallons)
Renew Fuel tank = COMPLETE DRAIN
1.Depressurise fuel system.
See fuel system -
depressurise - advanced evaps
2.Disconnect battery negative lead.
3.Remove 6 screws securing tail door tread strip
and remove tread strip.
4.Remove RH luggage compartment side panel.
See CHASSIS AND BODY, Repair,
Page 310 of 873
SFI
27
REPAIR ADD: 09/95
11.Disconnect vent line quickfit connector from
liquid/vapour separator.
12.Remove torque screw cap from hose to tank
filler neck clip.
13.Loosen clip screw securing hose to tank filler
neck.
14.Release hose from filler neck and internal filler
neck breather hose from fuel tank.
15.Remove and discard fuel filler neck clip.
16.Disconnect the pressure sensor breather pipe
connection.
17.Disconnect the vent line hose connection.
18.Fit ignition key to fuel filler flap lock and open
flap.
19.Release fuel filler cap from filler neck.
20.Remove filler neck assembly from vehicle.
Do not carry out further dismantling if
component is removed for access only.
21.Remove torque screw cap from hose to filler
neck clip.
22.Loosen clip screw securing hose to filler neck.
23.Remove hose from filler neck.
24.Remove and discard fuel filler hose clip.
25.Remove vent line from filler neck.
Page 311 of 873
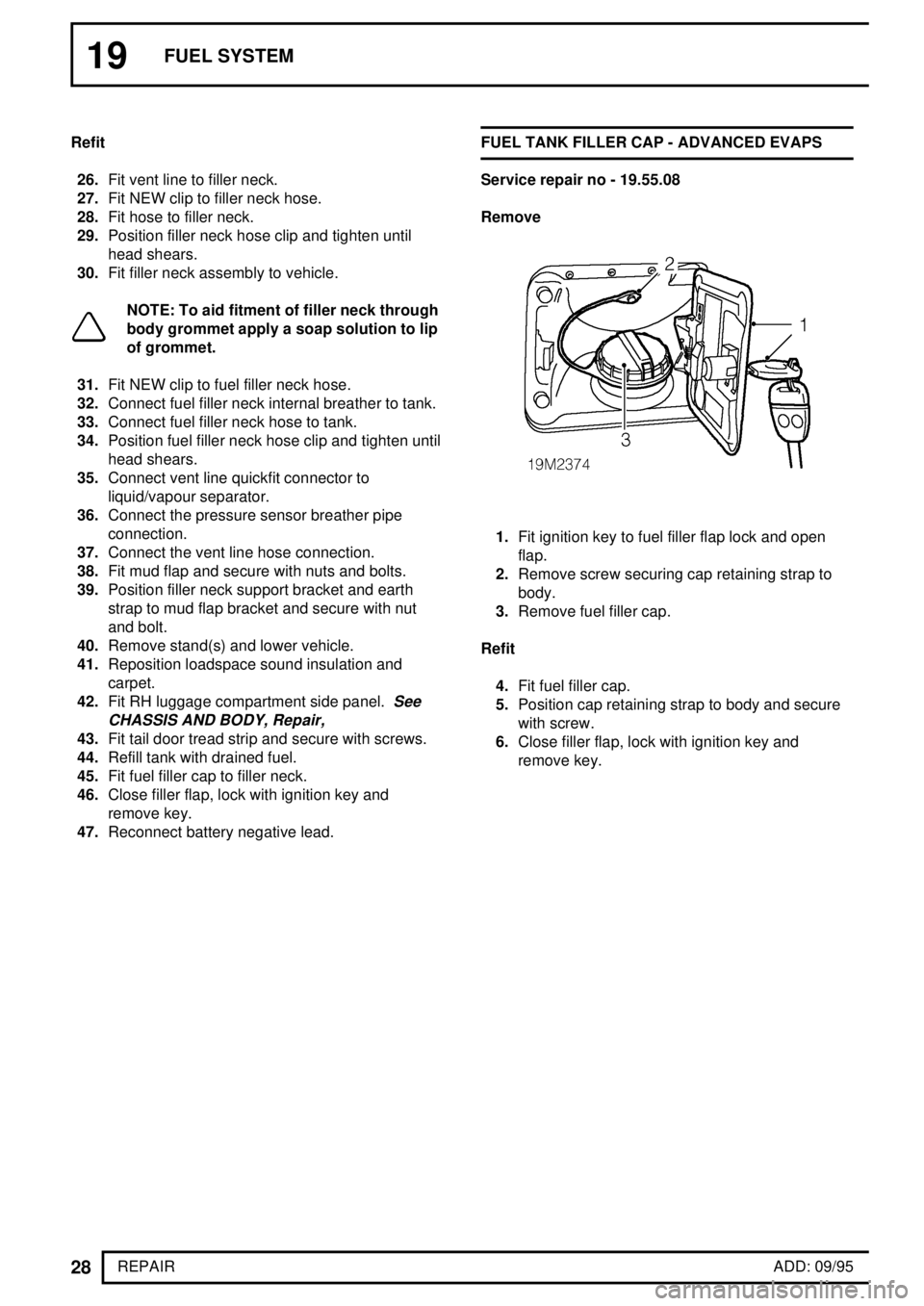
19FUEL SYSTEM
28
REPAIRADD: 09/95 Refit
26.Fit vent line to filler neck.
27.Fit NEW clip to filler neck hose.
28.Fit hose to filler neck.
29.Position filler neck hose clip and tighten until
head shears.
30.Fit filler neck assembly to vehicle.
NOTE: To aid fitment of filler neck through
body grommet apply a soap solution to lip
of grommet.
31.Fit NEW clip to fuel filler neck hose.
32.Connect fuel filler neck internal breather to tank.
33.Connect fuel filler neck hose to tank.
34.Position fuel filler neck hose clip and tighten until
head shears.
35.Connect vent line quickfit connector to
liquid/vapour separator.
36.Connect the pressure sensor breather pipe
connection.
37.Connect the vent line hose connection.
38.Fit mud flap and secure with nuts and bolts.
39.Position filler neck support bracket and earth
strap to mud flap bracket and secure with nut
and bolt.
40.Remove stand(s) and lower vehicle.
41.Reposition loadspace sound insulation and
carpet.
42.Fit RH luggage compartment side panel.
See
CHASSIS AND BODY, Repair,
43.Fit tail door tread strip and secure with screws.
44.Refill tank with drained fuel.
45.Fit fuel filler cap to filler neck.
46.Close filler flap, lock with ignition key and
remove key.
47.Reconnect battery negative lead.FUEL TANK FILLER CAP - ADVANCED EVAPS
Service repair no - 19.55.08
Remove
1.Fit ignition key to fuel filler flap lock and open
flap.
2.Remove screw securing cap retaining strap to
body.
3.Remove fuel filler cap.
Refit
4.Fit fuel filler cap.
5.Position cap retaining strap to body and secure
with screw.
6.Close filler flap, lock with ignition key and
remove key.
Page 313 of 873

Mpi
1
DESCRIPTION AND OPERATION DESCRIPTION
The Mpi Modular Engine Management System
(MEMS) controls the fuel injection and programmed
ignition systems.
The main features are as follows:
·The Engine Control Module (ECM) controls
programmed ignition and fuel injection. The ECM
incorporates short circuit protection and can
store intermittent faults on certain inputs.
Testbook can interrogate the ECM for these
stored faults.
·The ECM uses the speed/density method of air
flow measurement to calculate fuel delivery. This
method measures the inlet air temperature and
inlet manifold pressure and assumes that the
engine is a calibrated vacuum pump with its
characteristics stored in the ECM
·If certain system inputs fail, the ECM implements
a back-up facility to enable the system to
continue functioning, although at a reduced level
of performance.
·A separate diagnostic connector allows engine
tuning or fault diagnosis to be carried out using
Testbook without disconnecting the ECM
harness connector.
·The ECM harness multiplug incorporates
specially plated pins to minimise oxidation and
give improved reliability.
·The throttle potentiometer requires no
adjustment in service. The following components
supply data for both fuelling and ignition:Ignition system
The ECM determines the optimum ignition timing
based on the signals it receives from the following
sensors:
1.Crankshaft sensor - Engine speed and
crankshaft position.
2.Manifold absolute pressure sensor - Engine load
3.Coolant temperature sensor - Engine
temperature.
4.Manifold absolute pressure sensor - Throttle
closed.
5.Knock sensor - Engine noise and vibration.
MEMS uses no centrifugal or vacuum advance, timing
being controlled by the ECM which is energised by the
main relay, within the relay module. Spark distribution
is achieved by 2 coils mounted at the rear of the
engine and controlled by the ECM.
Page 314 of 873

19FUEL SYSTEM
2
DESCRIPTION AND OPERATION Basic ignition timing
MEMS provides the optimum ignition timing for the
relevant engine speed and load. The speed and
position of the engine is detected by the crankshaft
sensor which is bolted to, and projects through the
engine adapter plate.
The sensor incorporates an armature which runs
adjacent to a reluctor insert in the flywheel, the insert
consisting of 34 poles spaced at 10°intervals, with
two missing poles 180°apart to identify the T.D.C.
positions.
The sensor 'reads' these poles to provide a constant
up-date of engine speed and crankshaft position to
the ECM
The load signal is provided by the manifold absolute
pressure sensor mounted inside the ECM casing
which detects manifold pressure via a hose connected
to the manifold chamber. The sensor converts
pressure variations into graduated electrical signals
which can be read by the ECMIgnition timing compensation
Coolant temperature sensor
When the ECM receives a low engine temperature
signal from the coolant sensor, it provides optimum
driveability and emissions by advancing or retarding
the ignition timing.
Knock sensor
The knock sensor is a capacitive device mounted in
the cylinder block between nos. 2 and 3 cylinders
below the inlet manifold. The sensor monitors noise
and vibration in the engine and passes this
information to the ECM which is able to identify the
characteristics of the knocking and make the
necessary corrections to the ignition timing of
individual cylinders.
Idle speed control
When the throttle pedal is released and the engine is
at idle, the ECM uses the fast response of ignition
timing to assist idle speed control.
When loads are placed on, or removed from the
engine the ECM senses the change in engine speed
and in conjuction with the opening of the throttle disc
by the stepper motor, advances or retards the ignition
timing to maintain the specified idle speed. When load
is removed from the engine and the stepper motor
returns to it's original position, the ignition timing
returns to the idle setting.
NOTE: Due to the sensitivity of this system
the ignition timing will be constantly
changing at idle speed.