Page 263 of 873
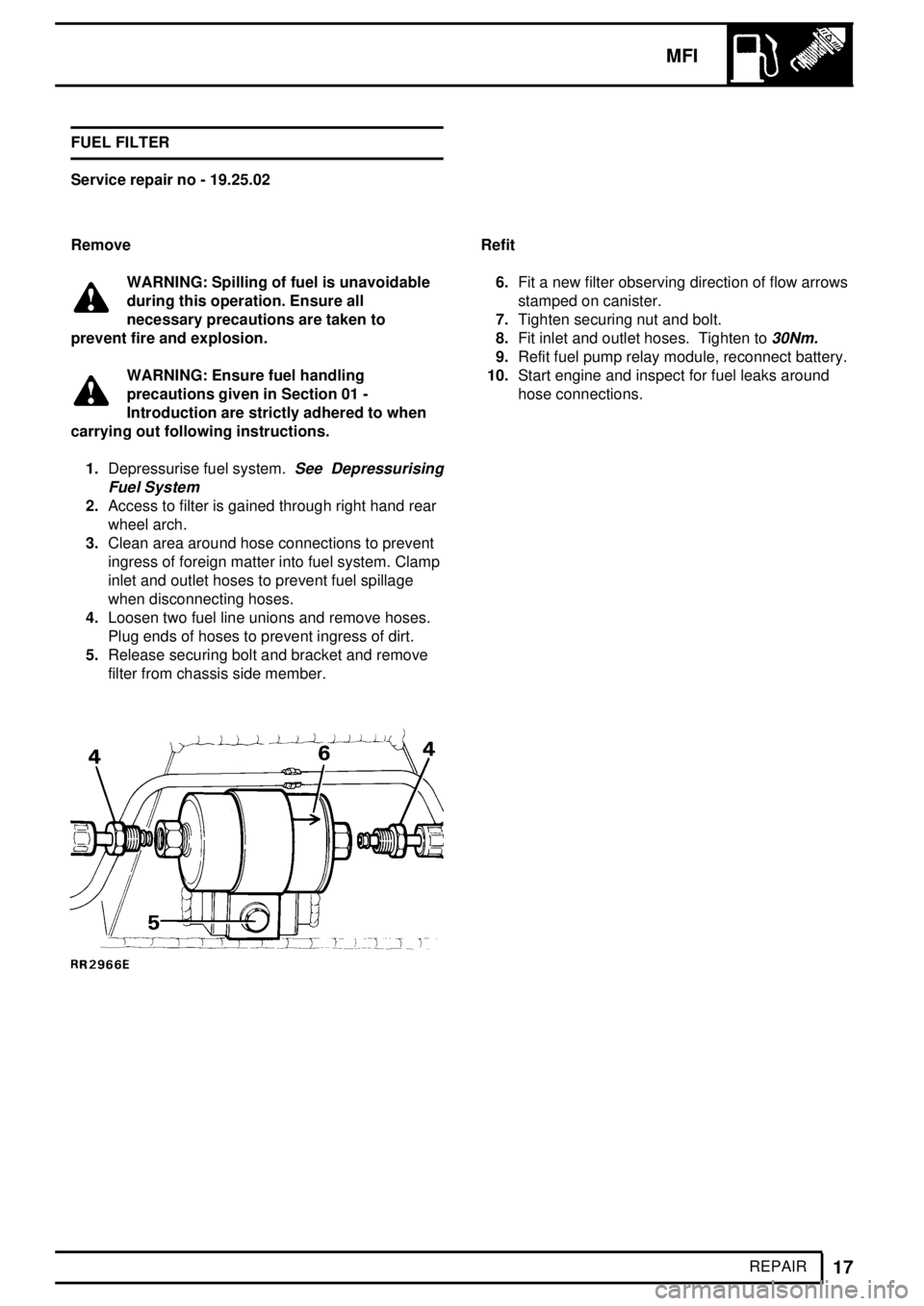
MFI
17
REPAIR FUEL FILTER
Service repair no - 19.25.02
Remove
WARNING: Spilling of fuel is unavoidable
during this operation. Ensure all
necessary precautions are taken to
prevent fire and explosion.
WARNING: Ensure fuel handling
precautions given in Section 01 -
Introduction are strictly adhered to when
carrying out following instructions.
1.Depressurise fuel system.
See Depressurising
Fuel System
2.Access to filter is gained through right hand rear
wheel arch.
3.Clean area around hose connections to prevent
ingress of foreign matter into fuel system. Clamp
inlet and outlet hoses to prevent fuel spillage
when disconnecting hoses.
4.Loosen two fuel line unions and remove hoses.
Plug ends of hoses to prevent ingress of dirt.
5.Release securing bolt and bracket and remove
filter from chassis side member.
Refit
6.Fit a new filter observing direction of flow arrows
stamped on canister.
7.Tighten securing nut and bolt.
8.Fit inlet and outlet hoses. Tighten to
30Nm.
9.Refit fuel pump relay module, reconnect battery.
10.Start engine and inspect for fuel leaks around
hose connections.
Page 265 of 873
MFI
19
REPAIR THROTTLE CABLE
Service repair no - 19.20.06
Remove
1.Remove clevis pin securing cable to lever.
2.Carefully pry throttle cable adjustment nut out of
mounting bracket.
3.Remove cable from mounting bracket.
4.Release outer cable from retaining clips in
engine compartment.
5.Remove lower dash panel.
6.Disconnect cable from accelerator pedal and
release cable locknut.
7.Feed cable through bulkhead grommet into
engine compartment.
Refit
8.Feed new cable from engine compartment
through bulkhead grommet.
9.Connect cable to accelerator pedal.
10.Connect cable to throttle linkage, using a new
cotter pin.
11.Clip outer cable adjustment nut into mounting
bracket.
12.Adjust outer cable to give 1.57 mm free play in
inner cable. Check throttle operation.
Page 267 of 873
MFI
21
REPAIR 6.Remove access panel from floor.
7.Disconnect multi-plug from fuel sender unit.
8.Disconnect two fuel line unions from fuel pump.
9.Using service tool no. LRT-19-001, remove
pump unit retaining ring. Withdraw unit from fuel
tank.
WARNING: A quantity of fuel will be
retained in body of unit, care must be
taken to prevent fuel spillage when unit is
removed.
Refit
10.Insert fuel pump into tank. Fit retaining ring.
Tighten to
48 Nm.
11.Connect fuel lines to pump.
12.Connect multi-plug to sender unit.
13.After assembly, check all fuel pipes, sealing
rings and hose connections are secure.
14.Run engine to check for fuel leaks.
15.Inspect access panel seal, fit a new seal if
necessary.
16.Fit access panel and tighten screws.
17.Reverse removal procedure. 4 - 5. Fit insulation
and carpet.
Page 269 of 873
MFI
23
REPAIR
13.Remove back two bolts and nut plates securing
fuel tank cradle.
14.Remove front nuts, bolts and washers. Remove
fuel tank cradle.
15.With assistance, tilt right hand side of tank
upwards and manoeuvre tank through chassis to
remove.
Refit
16.Reverse removal procedure. Ensuring sealing
ring, fuel pipe and hose connections are secure.
17.Run engine, check all connections for fuel leaks.
Page 272 of 873
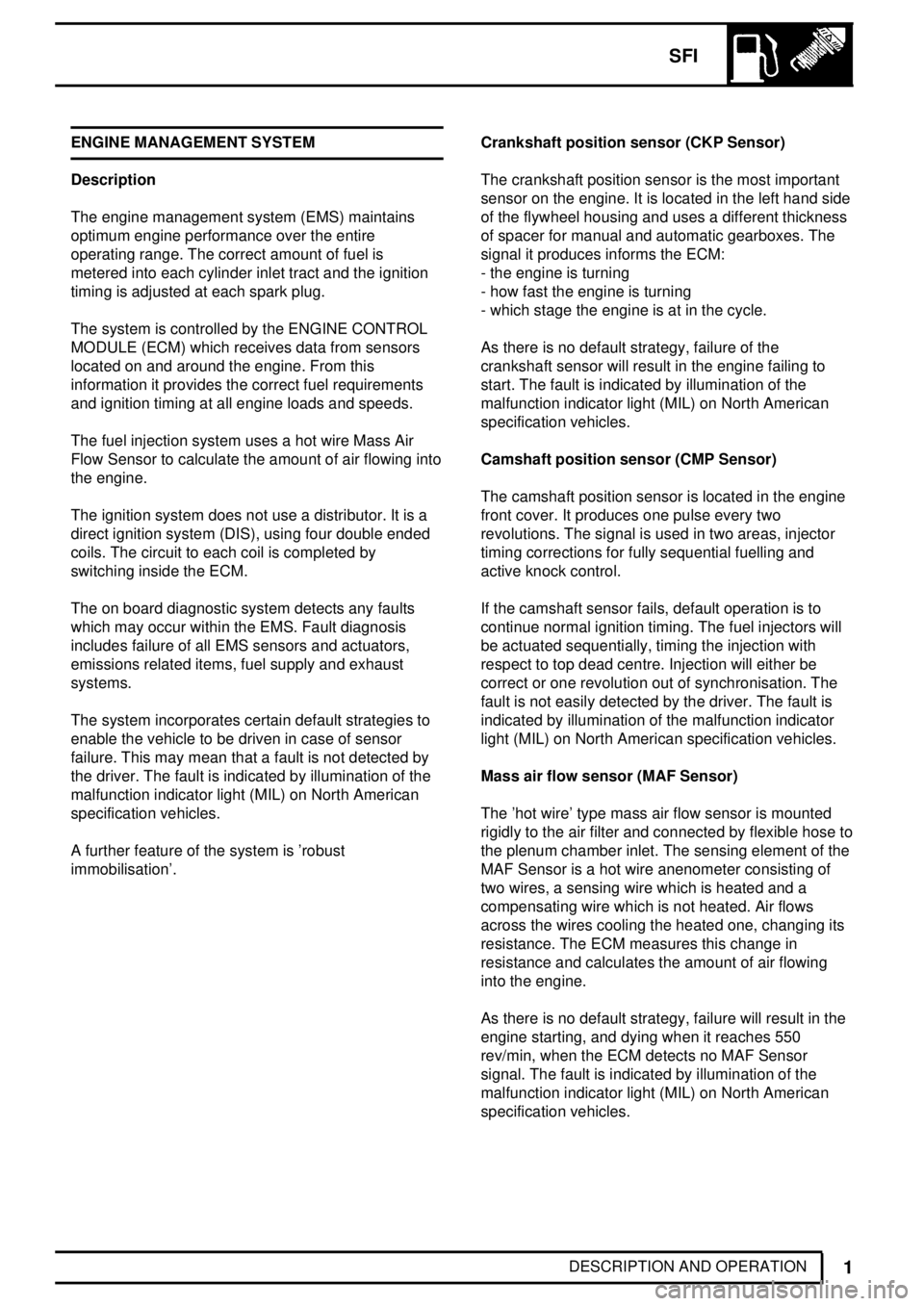
SFI
1
DESCRIPTION AND OPERATION ENGINE MANAGEMENT SYSTEM
Description
The engine management system (EMS) maintains
optimum engine performance over the entire
operating range. The correct amount of fuel is
metered into each cylinder inlet tract and the ignition
timing is adjusted at each spark plug.
The system is controlled by the ENGINE CONTROL
MODULE (ECM) which receives data from sensors
located on and around the engine. From this
information it provides the correct fuel requirements
and ignition timing at all engine loads and speeds.
The fuel injection system uses a hot wire Mass Air
Flow Sensor to calculate the amount of air flowing into
the engine.
The ignition system does not use a distributor. It is a
direct ignition system (DIS), using four double ended
coils. The circuit to each coil is completed by
switching inside the ECM.
The on board diagnostic system detects any faults
which may occur within the EMS. Fault diagnosis
includes failure of all EMS sensors and actuators,
emissions related items, fuel supply and exhaust
systems.
The system incorporates certain default strategies to
enable the vehicle to be driven in case of sensor
failure. This may mean that a fault is not detected by
the driver. The fault is indicated by illumination of the
malfunction indicator light (MIL) on North American
specification vehicles.
A further feature of the system is 'robust
immobilisation'.Crankshaft position sensor (CKP Sensor)
The crankshaft position sensor is the most important
sensor on the engine. It is located in the left hand side
of the flywheel housing and uses a different thickness
of spacer for manual and automatic gearboxes. The
signal it produces informs the ECM:
- the engine is turning
- how fast the engine is turning
- which stage the engine is at in the cycle.
As there is no default strategy, failure of the
crankshaft sensor will result in the engine failing to
start. The fault is indicated by illumination of the
malfunction indicator light (MIL) on North American
specification vehicles.
Camshaft position sensor (CMP Sensor)
The camshaft position sensor is located in the engine
front cover. It produces one pulse every two
revolutions. The signal is used in two areas, injector
timing corrections for fully sequential fuelling and
active knock control.
If the camshaft sensor fails, default operation is to
continue normal ignition timing. The fuel injectors will
be actuated sequentially, timing the injection with
respect to top dead centre. Injection will either be
correct or one revolution out of synchronisation. The
fault is not easily detected by the driver. The fault is
indicated by illumination of the malfunction indicator
light (MIL) on North American specification vehicles.
Mass air flow sensor (MAF Sensor)
The 'hot wire' type mass air flow sensor is mounted
rigidly to the air filter and connected by flexible hose to
the plenum chamber inlet. The sensing element of the
MAF Sensor is a hot wire anenometer consisting of
two wires, a sensing wire which is heated and a
compensating wire which is not heated. Air flows
across the wires cooling the heated one, changing its
resistance. The ECM measures this change in
resistance and calculates the amount of air flowing
into the engine.
As there is no default strategy, failure will result in the
engine starting, and dying when it reaches 550
rev/min, when the ECM detects no MAF Sensor
signal. The fault is indicated by illumination of the
malfunction indicator light (MIL) on North American
specification vehicles.
Page 273 of 873
19FUEL SYSTEM
2
DESCRIPTION AND OPERATION REV: 09/95 ENGINE MANAGEMENT SYSTEM COMPONENT
LOCATION - PRE ADVANCED EVAPS
1. Engine control module
2. Ignition coils
3. Fuel pressure regulator
4. Mass air flow sensor
5. Relay module
- Main relay
- Fuel pump relay
6. Engine coolant temperature sensor
7. Camshaft position sensor
8. Throttle position sensor
Page 274 of 873
SFI
3
DESCRIPTION AND OPERATION
1. EVAP purge valve
2. Inertia switch
3. Engine fuel temperature sensor
4. Crankshaft position sensor
5. Oxygen sensor (4 off)
6. Injectors
7. Idle air control
8. Knock sensors (2 off)
9. Intake air temperature sensor
Page 275 of 873
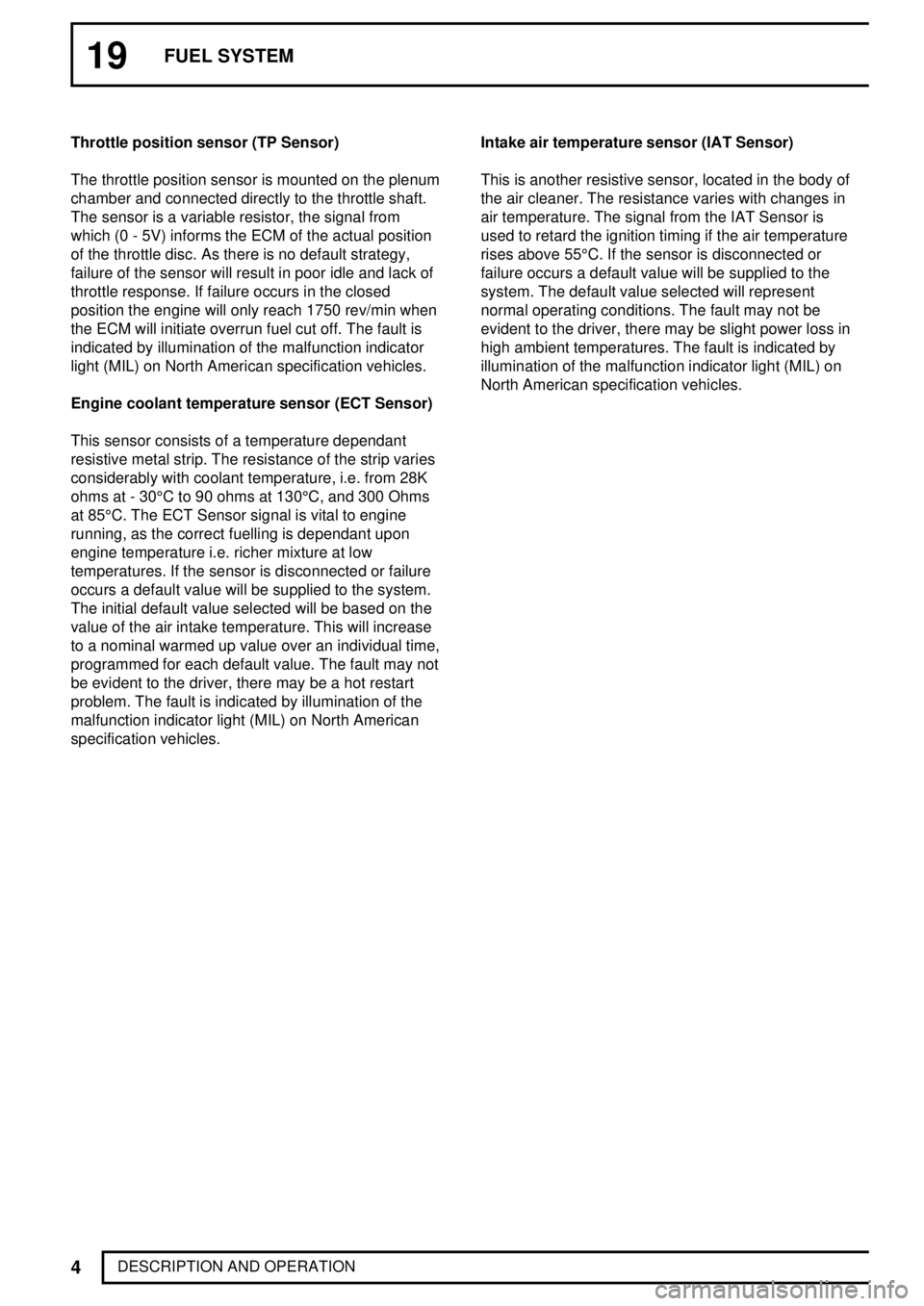
19FUEL SYSTEM
4
DESCRIPTION AND OPERATION Throttle position sensor (TP Sensor)
The throttle position sensor is mounted on the plenum
chamber and connected directly to the throttle shaft.
The sensor is a variable resistor, the signal from
which (0 - 5V) informs the ECM of the actual position
of the throttle disc. As there is no default strategy,
failure of the sensor will result in poor idle and lack of
throttle response. If failure occurs in the closed
position the engine will only reach 1750 rev/min when
the ECM will initiate overrun fuel cut off. The fault is
indicated by illumination of the malfunction indicator
light (MIL) on North American specification vehicles.
Engine coolant temperature sensor (ECT Sensor)
This sensor consists of a temperature dependant
resistive metal strip. The resistance of the strip varies
considerably with coolant temperature, i.e. from 28K
ohms at - 30°C to 90 ohms at 130°C, and 300 Ohms
at 85°C. The ECT Sensor signal is vital to engine
running, as the correct fuelling is dependant upon
engine temperature i.e. richer mixture at low
temperatures. If the sensor is disconnected or failure
occurs a default value will be supplied to the system.
The initial default value selected will be based on the
value of the air intake temperature. This will increase
to a nominal warmed up value over an individual time,
programmed for each default value. The fault may not
be evident to the driver, there may be a hot restart
problem. The fault is indicated by illumination of the
malfunction indicator light (MIL) on North American
specification vehicles.Intake air temperature sensor (IAT Sensor)
This is another resistive sensor, located in the body of
the air cleaner. The resistance varies with changes in
air temperature. The signal from the IAT Sensor is
used to retard the ignition timing if the air temperature
rises above 55°C. If the sensor is disconnected or
failure occurs a default value will be supplied to the
system. The default value selected will represent
normal operating conditions. The fault may not be
evident to the driver, there may be slight power loss in
high ambient temperatures. The fault is indicated by
illumination of the malfunction indicator light (MIL) on
North American specification vehicles.