Page 211 of 873
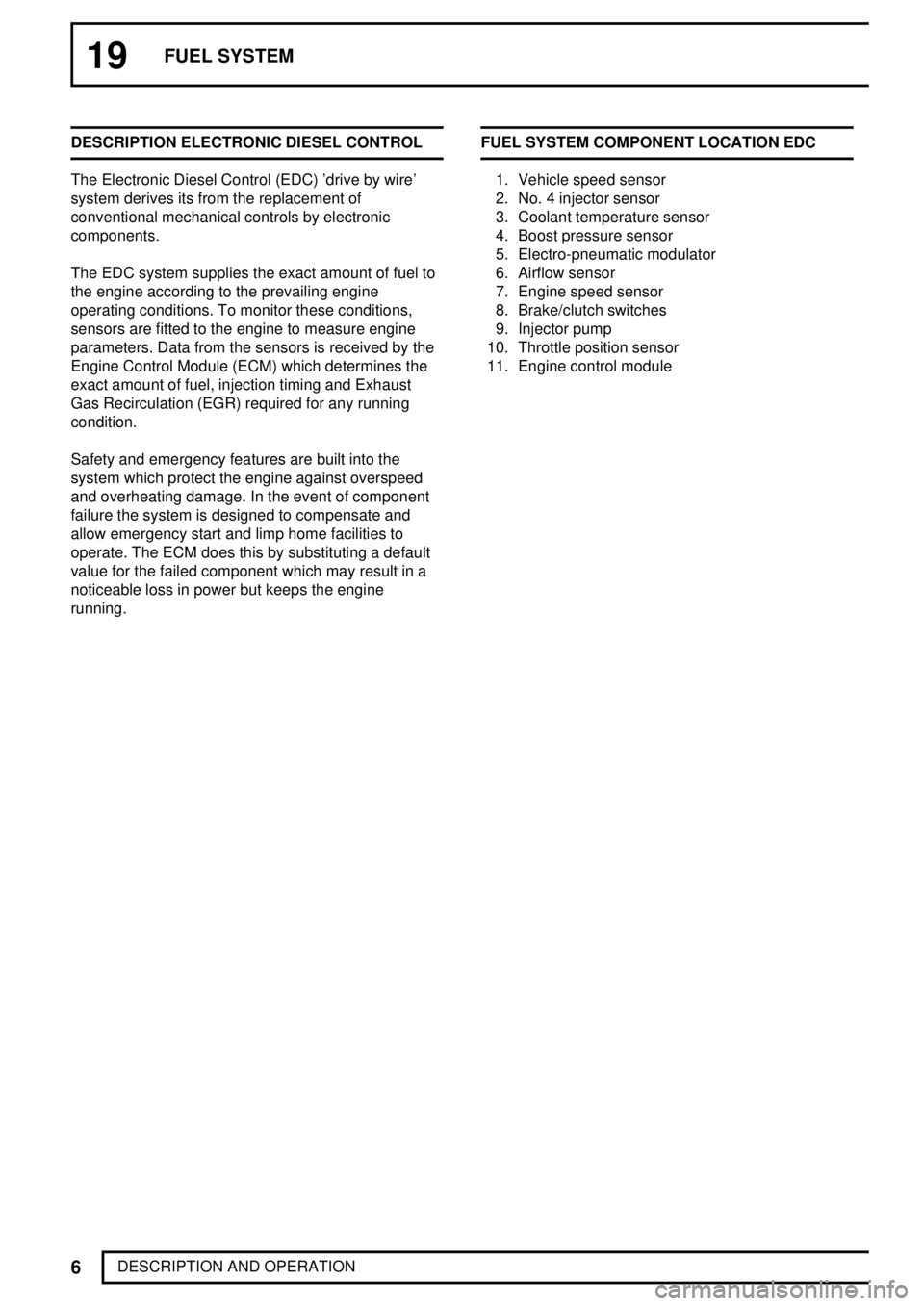
19FUEL SYSTEM
6
DESCRIPTION AND OPERATION DESCRIPTION ELECTRONIC DIESEL CONTROL
The Electronic Diesel Control (EDC) 'drive by wire'
system derives its from the replacement of
conventional mechanical controls by electronic
components.
The EDC system supplies the exact amount of fuel to
the engine according to the prevailing engine
operating conditions. To monitor these conditions,
sensors are fitted to the engine to measure engine
parameters. Data from the sensors is received by the
Engine Control Module (ECM) which determines the
exact amount of fuel, injection timing and Exhaust
Gas Recirculation (EGR) required for any running
condition.
Safety and emergency features are built into the
system which protect the engine against overspeed
and overheating damage. In the event of component
failure the system is designed to compensate and
allow emergency start and limp home facilities to
operate. The ECM does this by substituting a default
value for the failed component which may result in a
noticeable loss in power but keeps the engine
running.FUEL SYSTEM COMPONENT LOCATION EDC
1. Vehicle speed sensor
2. No. 4 injector sensor
3. Coolant temperature sensor
4. Boost pressure sensor
5. Electro-pneumatic modulator
6. Airflow sensor
7. Engine speed sensor
8. Brake/clutch switches
9. Injector pump
10. Throttle position sensor
11. Engine control module
Page 213 of 873
19FUEL SYSTEM
8
DESCRIPTION AND OPERATION FUEL SYSTEM LAYOUT EDC
1. Fuel injection pump
2. Fuel temperature sensor
3. Air temperature sensor
4. Water temperature sensor
5. No. 4 injector sensor
6. Air flow sensor
7. Engine speed sensor
8. Boost pressure sensor
9. Vehicle speed sensor
10. Clutch switch
11. Brake switch
12. Throttle position sensor
13. Electro-pneumatic modulator
14. Exhaust gas recirculation (EGR) valve
15. Engine control module (ECM)
16. Diagnostic indicator
A. To turbo
B. To air box.
C. To 'T' piece on brake servo hose position
D. Solenoid operated valve energization timing device.
E. Fuel cut off
F. Actuator current
G. Control collar
Page 214 of 873
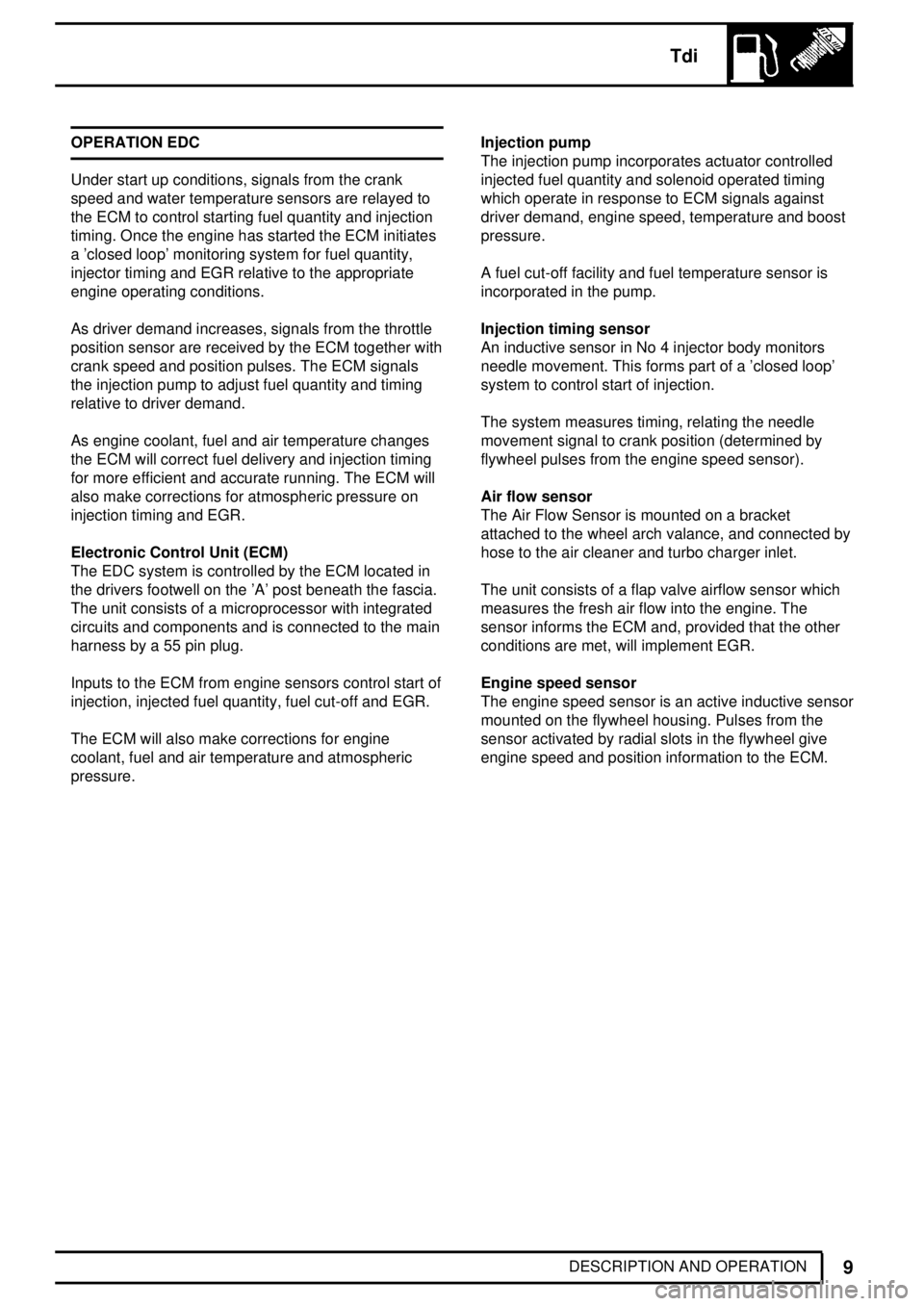
Tdi
9
DESCRIPTION AND OPERATION OPERATION EDC
Under start up conditions, signals from the crank
speed and water temperature sensors are relayed to
the ECM to control starting fuel quantity and injection
timing. Once the engine has started the ECM initiates
a 'closed loop' monitoring system for fuel quantity,
injector timing and EGR relative to the appropriate
engine operating conditions.
As driver demand increases, signals from the throttle
position sensor are received by the ECM together with
crank speed and position pulses. The ECM signals
the injection pump to adjust fuel quantity and timing
relative to driver demand.
As engine coolant, fuel and air temperature changes
the ECM will correct fuel delivery and injection timing
for more efficient and accurate running. The ECM will
also make corrections for atmospheric pressure on
injection timing and EGR.
Electronic Control Unit (ECM)
The EDC system is controlled by the ECM located in
the drivers footwell on the 'A' post beneath the fascia.
The unit consists of a microprocessor with integrated
circuits and components and is connected to the main
harness by a 55 pin plug.
Inputs to the ECM from engine sensors control start of
injection, injected fuel quantity, fuel cut-off and EGR.
The ECM will also make corrections for engine
coolant, fuel and air temperature and atmospheric
pressure.Injection pump
The injection pump incorporates actuator controlled
injected fuel quantity and solenoid operated timing
which operate in response to ECM signals against
driver demand, engine speed, temperature and boost
pressure.
A fuel cut-off facility and fuel temperature sensor is
incorporated in the pump.
Injection timing sensor
An inductive sensor in No 4 injector body monitors
needle movement. This forms part of a 'closed loop'
system to control start of injection.
The system measures timing, relating the needle
movement signal to crank position (determined by
flywheel pulses from the engine speed sensor).
Air flow sensor
The Air Flow Sensor is mounted on a bracket
attached to the wheel arch valance, and connected by
hose to the air cleaner and turbo charger inlet.
The unit consists of a flap valve airflow sensor which
measures the fresh air flow into the engine. The
sensor informs the ECM and, provided that the other
conditions are met, will implement EGR.
Engine speed sensor
The engine speed sensor is an active inductive sensor
mounted on the flywheel housing. Pulses from the
sensor activated by radial slots in the flywheel give
engine speed and position information to the ECM.
Page 215 of 873
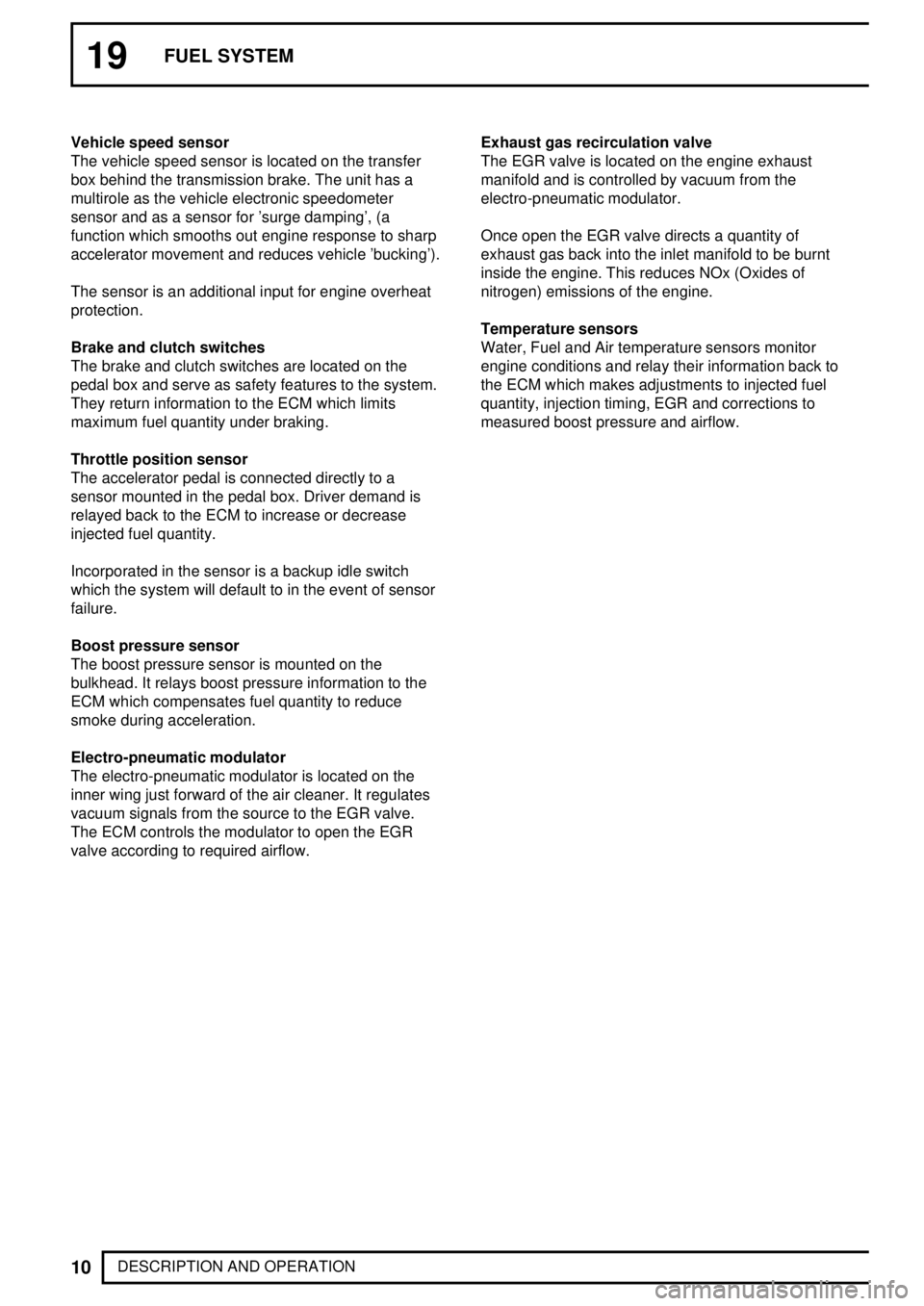
19FUEL SYSTEM
10
DESCRIPTION AND OPERATION Vehicle speed sensor
The vehicle speed sensor is located on the transfer
box behind the transmission brake. The unit has a
multirole as the vehicle electronic speedometer
sensor and as a sensor for 'surge damping', (a
function which smooths out engine response to sharp
accelerator movement and reduces vehicle 'bucking').
The sensor is an additional input for engine overheat
protection.
Brake and clutch switches
The brake and clutch switches are located on the
pedal box and serve as safety features to the system.
They return information to the ECM which limits
maximum fuel quantity under braking.
Throttle position sensor
The accelerator pedal is connected directly to a
sensor mounted in the pedal box. Driver demand is
relayed back to the ECM to increase or decrease
injected fuel quantity.
Incorporated in the sensor is a backup idle switch
which the system will default to in the event of sensor
failure.
Boost pressure sensor
The boost pressure sensor is mounted on the
bulkhead. It relays boost pressure information to the
ECM which compensates fuel quantity to reduce
smoke during acceleration.
Electro-pneumatic modulator
The electro-pneumatic modulator is located on the
inner wing just forward of the air cleaner. It regulates
vacuum signals from the source to the EGR valve.
The ECM controls the modulator to open the EGR
valve according to required airflow.Exhaust gas recirculation valve
The EGR valve is located on the engine exhaust
manifold and is controlled by vacuum from the
electro-pneumatic modulator.
Once open the EGR valve directs a quantity of
exhaust gas back into the inlet manifold to be burnt
inside the engine. This reduces NOx (Oxides of
nitrogen) emissions of the engine.
Temperature sensors
Water, Fuel and Air temperature sensors monitor
engine conditions and relay their information back to
the ECM which makes adjustments to injected fuel
quantity, injection timing, EGR and corrections to
measured boost pressure and airflow.
Page 216 of 873
Tdi
1
ADJUSTMENT THROTTLE CABLE
Adjust
1.Loosen throttle cable adjustment ferrule.
2.Hold throttle lever in fully closed position.
3.Adjust outer cable, by rotating ferrule, to give
1.57 mm (0.062 in) of free play in the inner
cable.
4.Check that throttle opens fully when the throttle
is depressed.EGR THROTTLE POSITION SENSOR
Check
1.Run engine until normal operating temperature is
reached.
2.Switch off engine and disconnect sensor
multiplug.
3.Connect an Ohmmeter across pins 1 and 3 of
multiplug. Ohmmeter should read between 1K
and 1.05K ohms.
4.Connect an Ohmmeter across pins 1 and 2 of
multiplug. Ohmmeter should read between 850
and 900 ohms.
5.If the readings are correct, EGR throttle position
sensor is Ok - reconnect multiplug.
6.Loosen 2 Torx screws securing sensor.
7.Rotate sensor to achieve correct Ohmmeter
readings, then tighten Torx screws.
8.Re-check Ohmmeter readings, then reconnect
multiplug.
Page 217 of 873
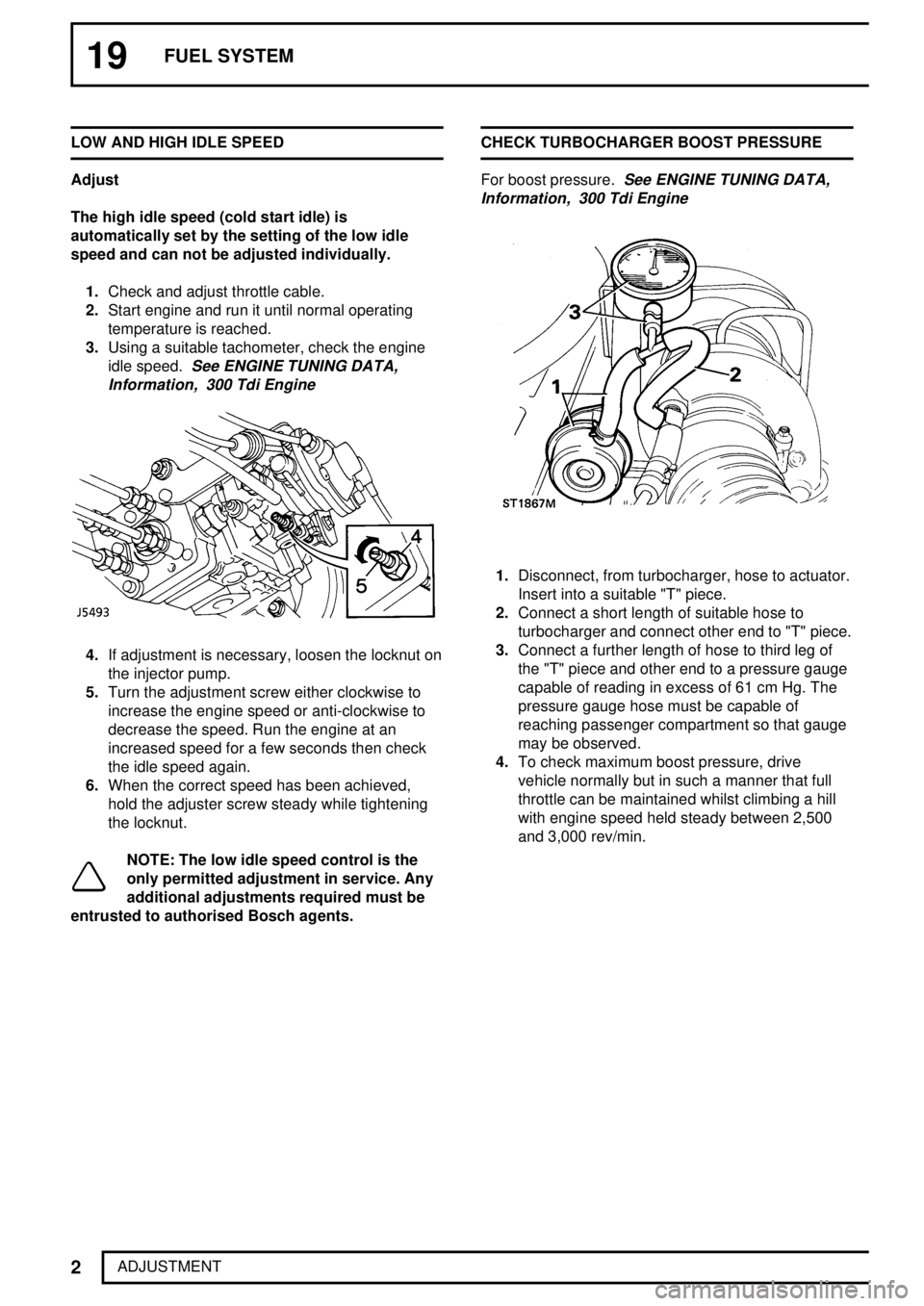
19FUEL SYSTEM
2
ADJUSTMENT LOW AND HIGH IDLE SPEED
Adjust
The high idle speed (cold start idle) is
automatically set by the setting of the low idle
speed and can not be adjusted individually.
1.Check and adjust throttle cable.
2.Start engine and run it until normal operating
temperature is reached.
3.Using a suitable tachometer, check the engine
idle speed.
See ENGINE TUNING DATA,
Information, 300 Tdi Engine
4.If adjustment is necessary, loosen the locknut on
the injector pump.
5.Turn the adjustment screw either clockwise to
increase the engine speed or anti-clockwise to
decrease the speed. Run the engine at an
increased speed for a few seconds then check
the idle speed again.
6.When the correct speed has been achieved,
hold the adjuster screw steady while tightening
the locknut.
NOTE: The low idle speed control is the
only permitted adjustment in service. Any
additional adjustments required must be
entrusted to authorised Bosch agents.CHECK TURBOCHARGER BOOST PRESSURE
For boost pressure.
See ENGINE TUNING DATA,
Information, 300 Tdi Engine
1.Disconnect, from turbocharger, hose to actuator.
Insert into a suitable "T" piece.
2.Connect a short length of suitable hose to
turbocharger and connect other end to "T" piece.
3.Connect a further length of hose to third leg of
the "T" piece and other end to a pressure gauge
capable of reading in excess of 61 cm Hg. The
pressure gauge hose must be capable of
reaching passenger compartment so that gauge
may be observed.
4.To check maximum boost pressure, drive
vehicle normally but in such a manner that full
throttle can be maintained whilst climbing a hill
with engine speed held steady between 2,500
and 3,000 rev/min.
Page 219 of 873
19FUEL SYSTEM
2
REPAIR THROTTLE CABLE
Service repair no - 19.20.06
Remove
1.Disconnect battery negative lead.
2.Remove pin and clevis pin securing throttle
cable to throttle lever.
3.Pull ferrule from abutment bracket and withdraw
throttle cable.
4.Release throttle cable from clip on bulkhead.
5.Remove pin and clevis pin securing throttle
cable to throttle lever.
6.Release grommet from bulkhead.
7.Withdraw throttle cable from engine
compartment.
Refit
8.Reverse removal procedure. Use new pins to
secure clevis pins.
9.Adjust throttle cable.
See Adjustment,
Throttle Cable
INTAKE HOSE TURBOCHARGER
Service repair no - 19.42.11
Remove
1.Disconnect battery negative lead.
2.Loosen clip and disconnect intake hose from
turbocharger.
3.Loosen clip and disconnect breather hose from
intake hose.
4.Remove clip and disconnect hose from air
cleaner, discard clip.
5.Remove intake hose
Refit
6.Reverse removal procedure. Use a new clip to
secure intake hose to air cleaner.
Page 220 of 873
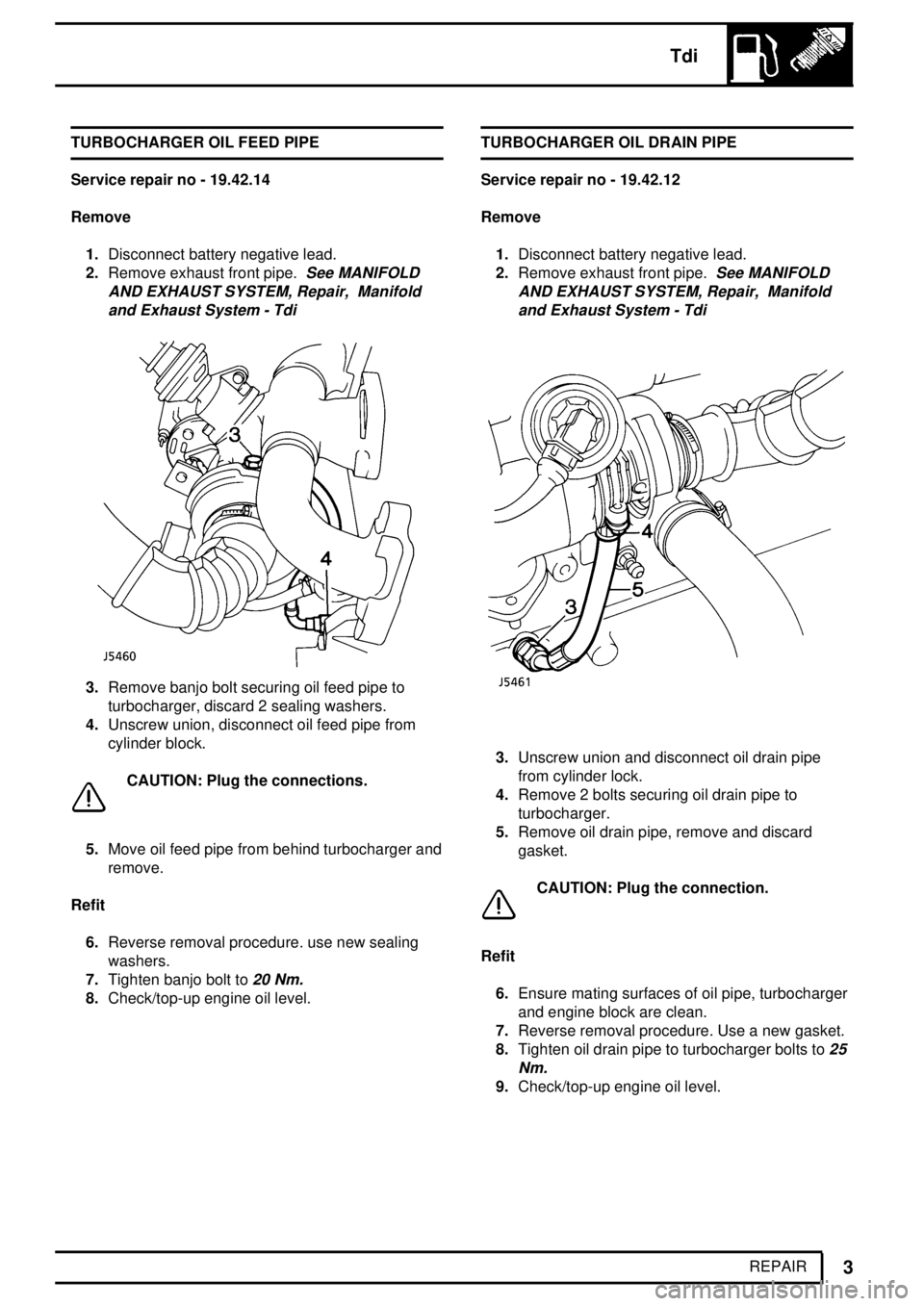
Tdi
3
REPAIR TURBOCHARGER OIL FEED PIPE
Service repair no - 19.42.14
Remove
1.Disconnect battery negative lead.
2.Remove exhaust front pipe.
See MANIFOLD
AND EXHAUST SYSTEM, Repair, Manifold
and Exhaust System - Tdi
3.Remove banjo bolt securing oil feed pipe to
turbocharger, discard 2 sealing washers.
4.Unscrew union, disconnect oil feed pipe from
cylinder block.
CAUTION: Plug the connections.
5.Move oil feed pipe from behind turbocharger and
remove.
Refit
6.Reverse removal procedure. use new sealing
washers.
7.Tighten banjo bolt to
20 Nm.
8.Check/top-up engine oil level.TURBOCHARGER OIL DRAIN PIPE
Service repair no - 19.42.12
Remove
1.Disconnect battery negative lead.
2.Remove exhaust front pipe.
See MANIFOLD
AND EXHAUST SYSTEM, Repair, Manifold
and Exhaust System - Tdi
3.Unscrew union and disconnect oil drain pipe
from cylinder lock.
4.Remove 2 bolts securing oil drain pipe to
turbocharger.
5.Remove oil drain pipe, remove and discard
gasket.
CAUTION: Plug the connection.
Refit
6.Ensure mating surfaces of oil pipe, turbocharger
and engine block are clean.
7.Reverse removal procedure. Use a new gasket.
8.Tighten oil drain pipe to turbocharger bolts to
25
Nm.
9.Check/top-up engine oil level.