Page 447 of 873
![LAND ROVER DISCOVERY 1995 Workshop Manual 44AUTOMATIC GEARBOX
10
REPAIR OIL SCREEN
Service repair no - 44.24.07
Renew
1.Site vehicle on a four post ramp [hoist].
2.Disconnect battery negative lead.
3.Raise vehicle.
4.Drain oil and refit plug LAND ROVER DISCOVERY 1995 Workshop Manual 44AUTOMATIC GEARBOX
10
REPAIR OIL SCREEN
Service repair no - 44.24.07
Renew
1.Site vehicle on a four post ramp [hoist].
2.Disconnect battery negative lead.
3.Raise vehicle.
4.Drain oil and refit plug](/manual-img/64/57248/w960_57248-446.png)
44AUTOMATIC GEARBOX
10
REPAIR OIL SCREEN
Service repair no - 44.24.07
Renew
1.Site vehicle on a four post ramp [hoist].
2.Disconnect battery negative lead.
3.Raise vehicle.
4.Drain oil and refit plug with new seal.
5.Detach heat shield at front exhaust pipe to
manifold.
6.Disconnect electrics from Lambda sensors.
7.Remove catalytic converter assembly.
8.Remove chassis cross-member from under
gearbox.
9.Disconnect dipstick tube at oil sump. Loosen
securing bolt at bell housing and move dipstick
aside.
10.Remove clamps securing oil sump. Note their
locations for refit and withdraw sump.
11.Remove gasket and clean gasket mating faces.
12.Remove securing screws and detach oil screen
and suction pipe, taking care to retain suction
pipe spacer, discard 'O' ring seal.13.Detach suction pipe from oil screen, discard 'O'
ring seal.
14.Clean oil screen and blow out with airline.
15.Clean suction pipe.
16.Fit new 'O' ring seals to oil screen using light
grease to aid assembly.
17.Fit oil screen and suction pipe with spacer and
secure with three bolts.
18.Refit oil sump using a new gasket.
19.Connect dipstick tube to oil sump and tighten
bolt at bell housing.
20.Refit chassis cross-member.
21.Refit catalytic converter assembly
22.Connect electrics to Lambda sensors.
23.Connect heat shield front pipe to manifold.
24.Connect battery.
25.Refill gearbox oil system using correct grade of
oil.
See LUBRICANTS, FLUIDS AND
CAPACITIES, Information, Recommended
Lubricants and Fluids
Page 448 of 873
ZF
11
REPAIR CONTROL UNIT
Remove
1.Site vehicle on a four post ramp [hoist].
2.Disconnect battery negative lead.
3.Raise vehicle.
4.Drain oil and refit plug with new seal.
5.Detach heat shield at front exhaust pipe to
manifold.
6.Disconnect electrics from Lambda sensors.
7.Remove catalytic converter assembly.
8.Remove chassis cross-member from under
gearbox.
9.Disconnect dipstick tube at oil sump. Loosen
securing bolt at bell housing and move dipstick
aside.
10.Remove clamps securing oil sump. Note their
locations for refit and withdraw sump.
11.Remove gasket and clean gasket mating faces.
12.Remove securing screws and detach oil screen
and suction pipe, taking care to retain suction
pipe spacer, discard 'O' ring seal.
13.Remove securing screws and detach control unit
from casing.
Page 449 of 873
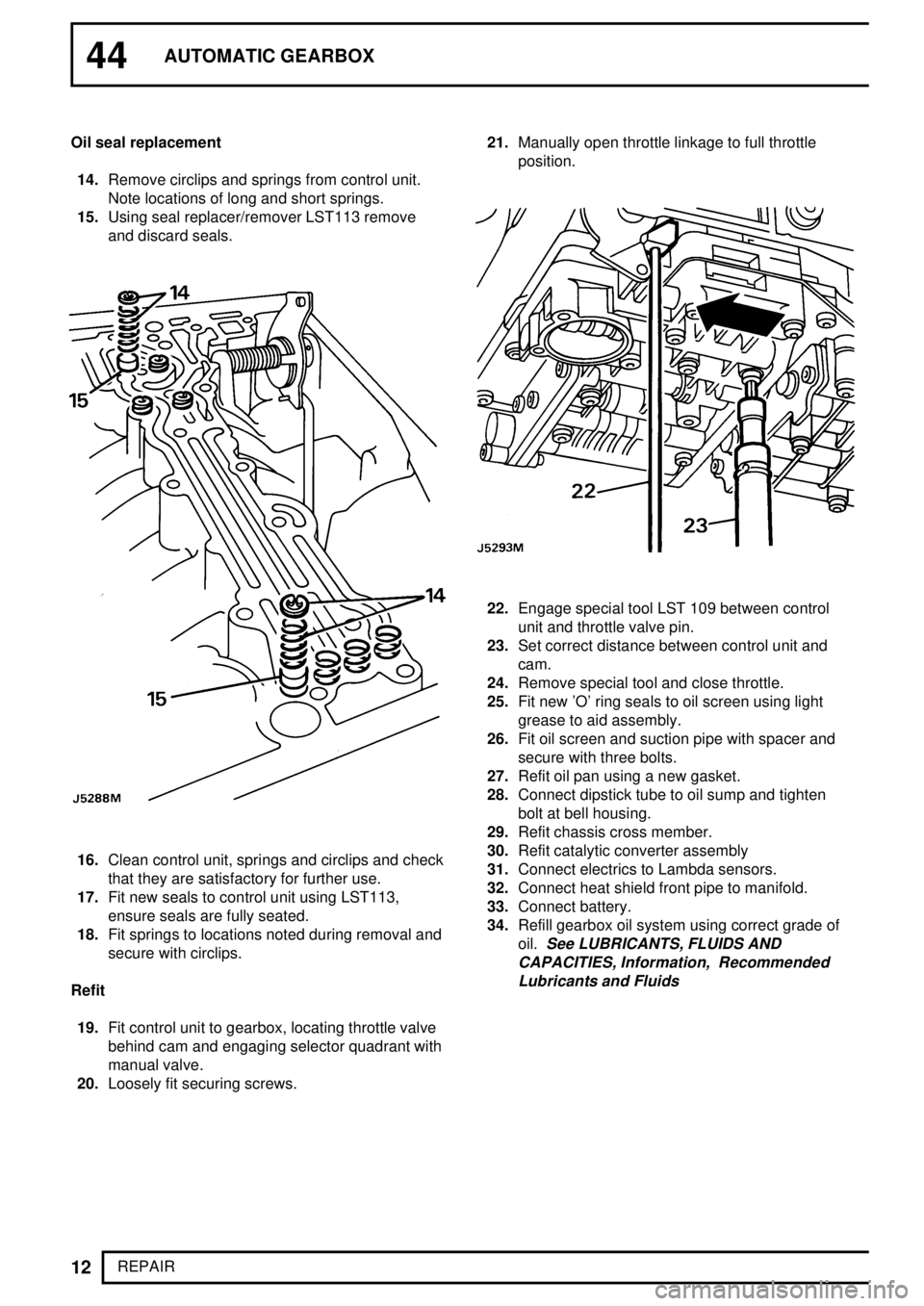
44AUTOMATIC GEARBOX
12
REPAIR Oil seal replacement
14.Remove circlips and springs from control unit.
Note locations of long and short springs.
15.Using seal replacer/remover LST113 remove
and discard seals.
16.Clean control unit, springs and circlips and check
that they are satisfactory for further use.
17.Fit new seals to control unit using LST113,
ensure seals are fully seated.
18.Fit springs to locations noted during removal and
secure with circlips.
Refit
19.Fit control unit to gearbox, locating throttle valve
behind cam and engaging selector quadrant with
manual valve.
20.Loosely fit securing screws.21.Manually open throttle linkage to full throttle
position.
22.Engage special tool LST 109 between control
unit and throttle valve pin.
23.Set correct distance between control unit and
cam.
24.Remove special tool and close throttle.
25.Fit new 'O' ring seals to oil screen using light
grease to aid assembly.
26.Fit oil screen and suction pipe with spacer and
secure with three bolts.
27.Refit oil pan using a new gasket.
28.Connect dipstick tube to oil sump and tighten
bolt at bell housing.
29.Refit chassis cross member.
30.Refit catalytic converter assembly
31.Connect electrics to Lambda sensors.
32.Connect heat shield front pipe to manifold.
33.Connect battery.
34.Refill gearbox oil system using correct grade of
oil.
See LUBRICANTS, FLUIDS AND
CAPACITIES, Information, Recommended
Lubricants and Fluids
Page 450 of 873
![LAND ROVER DISCOVERY 1995 Workshop Manual ZF
13
REPAIR KICKDOWN CABLE
Service repair no - 44.15.01
Remove
1.Site vehicle on a four post ramp [hoist].
2.Select neutral N gear lever.
3.Disconnect battery negative lead.
4.Disconnect kickdown c LAND ROVER DISCOVERY 1995 Workshop Manual ZF
13
REPAIR KICKDOWN CABLE
Service repair no - 44.15.01
Remove
1.Site vehicle on a four post ramp [hoist].
2.Select neutral N gear lever.
3.Disconnect battery negative lead.
4.Disconnect kickdown c](/manual-img/64/57248/w960_57248-449.png)
ZF
13
REPAIR KICKDOWN CABLE
Service repair no - 44.15.01
Remove
1.Site vehicle on a four post ramp [hoist].
2.Select neutral 'N' gear lever.
3.Disconnect battery negative lead.
4.Disconnect kickdown cable at throttle linkage.
5.Release outer cable locknut.
6.Disconnect cable from mounting bracket.
7.Release cable from bracket attached to cylinder
head.
8.Feed cable through to underside of vehicle.
9.Raise vehicle on ramp [hoist].
10.Drain oil and refit plug with new seal.
11.Detach heat shield at front exhaust pipe to
manifold.
12.Disconnect electrics from Lambda sensors.
13.Remove catalytic converter assembly.
14.Remove chassis cross-member from under
gearbox.
15.Disconnect dipstick tube at oil sump. Loosen
securing bolt at bell housing and move dipstick
aside.
16.Remove clamps securing oil sump. Note their
locations for refit, and withdraw sump.
17.Pull kickdown inner cable to fully open valve
cam. Wedge cam in this position.
18.Release cable from cam by pushing inner cable
into outer casing and detaching cable nipple
from cam.
19.Using special tool LST112 compress cable tangs
and remove cable from gearbox.
20.If cable is to be refitted remove 'O' ring seal and
clean cable assembly.
Refit
21.Fit new 'O' ring seal to cable and lubricate seal.
22.Fit cable to gearbox casing ensuring it is
correctly seated.
23.Fit inner cable nipple to its location on cam.
NOTE: When a new cable is fitted, to help
locate nipple to cam, introduce a curve
into the cable. Do not bend or kink cable.24.Remove wedge from cam and ensure nipple
remains engaged.
25.Feed free end of cable assembly into engine
compartment.
26.Refit oil pan using a new gasket.
27.Connect dipstick tube to oil sump and tighten
bolt at bell housing.
28.Refit chassis cross-member
29.Refit catalytic converter assembly
30.Connect electrics to Lambda sensors.
31.Connect heat shield front pipe to manifold.
32.Lower vehicle on ramp [hoist].
33.Fit cable to bracket at cylinder head.
34.Locate cable in mounting bracket, do not tighten
locknut.
35.Fit cable to throttle linkage.
36.Ensure throttle linkage is fully closed.
37.Adjust outer cable to achieve a gap of 0,25 to
1,25mm (dimension 'A') between end of outer
cable and crimped collar on inner cable.
38.Tighten locknuts and recheck gap.
NOTE: If fitting a new cable, and collar on
inner cable is loose, measure distance 'B'
on old cable. Crimp collar on new cable to
this dimension.
39.Reconnect battery negative lead.
40.Refill gearbox oil using correct grade of oil.
See
LUBRICANTS, FLUIDS AND CAPACITIES,
Information, Recommended Lubricants and
Fluids
Page 473 of 873
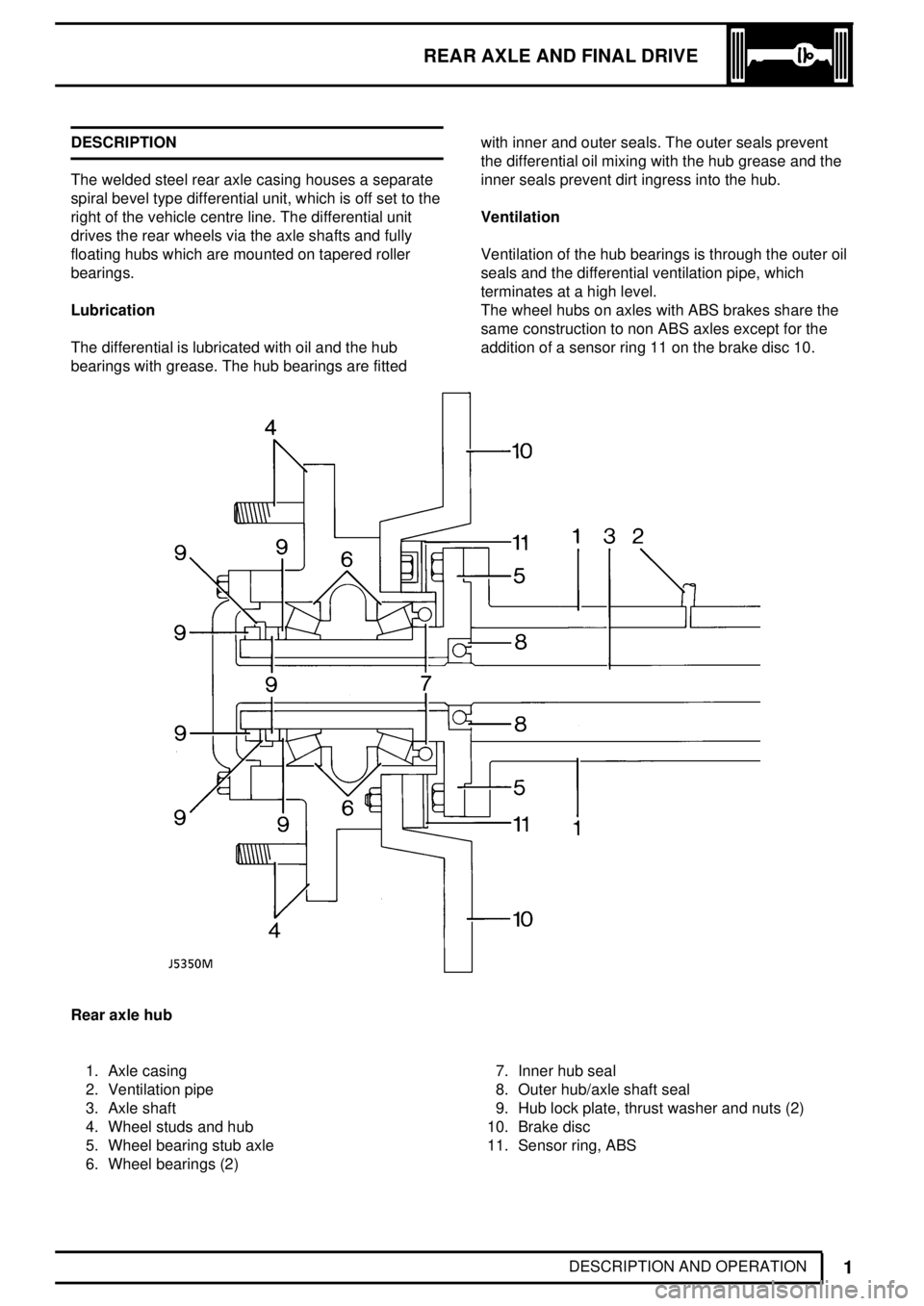
REAR AXLE AND FINAL DRIVE
1
DESCRIPTION AND OPERATION DESCRIPTION
The welded steel rear axle casing houses a separate
spiral bevel type differential unit, which is off set to the
right of the vehicle centre line. The differential unit
drives the rear wheels via the axle shafts and fully
floating hubs which are mounted on tapered roller
bearings.
Lubrication
The differential is lubricated with oil and the hub
bearings with grease. The hub bearings are fittedwith inner and outer seals. The outer seals prevent
the differential oil mixing with the hub grease and the
inner seals prevent dirt ingress into the hub.
Ventilation
Ventilation of the hub bearings is through the outer oil
seals and the differential ventilation pipe, which
terminates at a high level.
The wheel hubs on axles with ABS brakes share the
same construction to non ABS axles except for the
addition of a sensor ring 11 on the brake disc 10.
Rear axle hub
1. Axle casing
2. Ventilation pipe
3. Axle shaft
4. Wheel studs and hub
5. Wheel bearing stub axle
6. Wheel bearings (2)7. Inner hub seal
8. Outer hub/axle shaft seal
9. Hub lock plate, thrust washer and nuts (2)
10. Brake disc
11. Sensor ring, ABS
Page 476 of 873
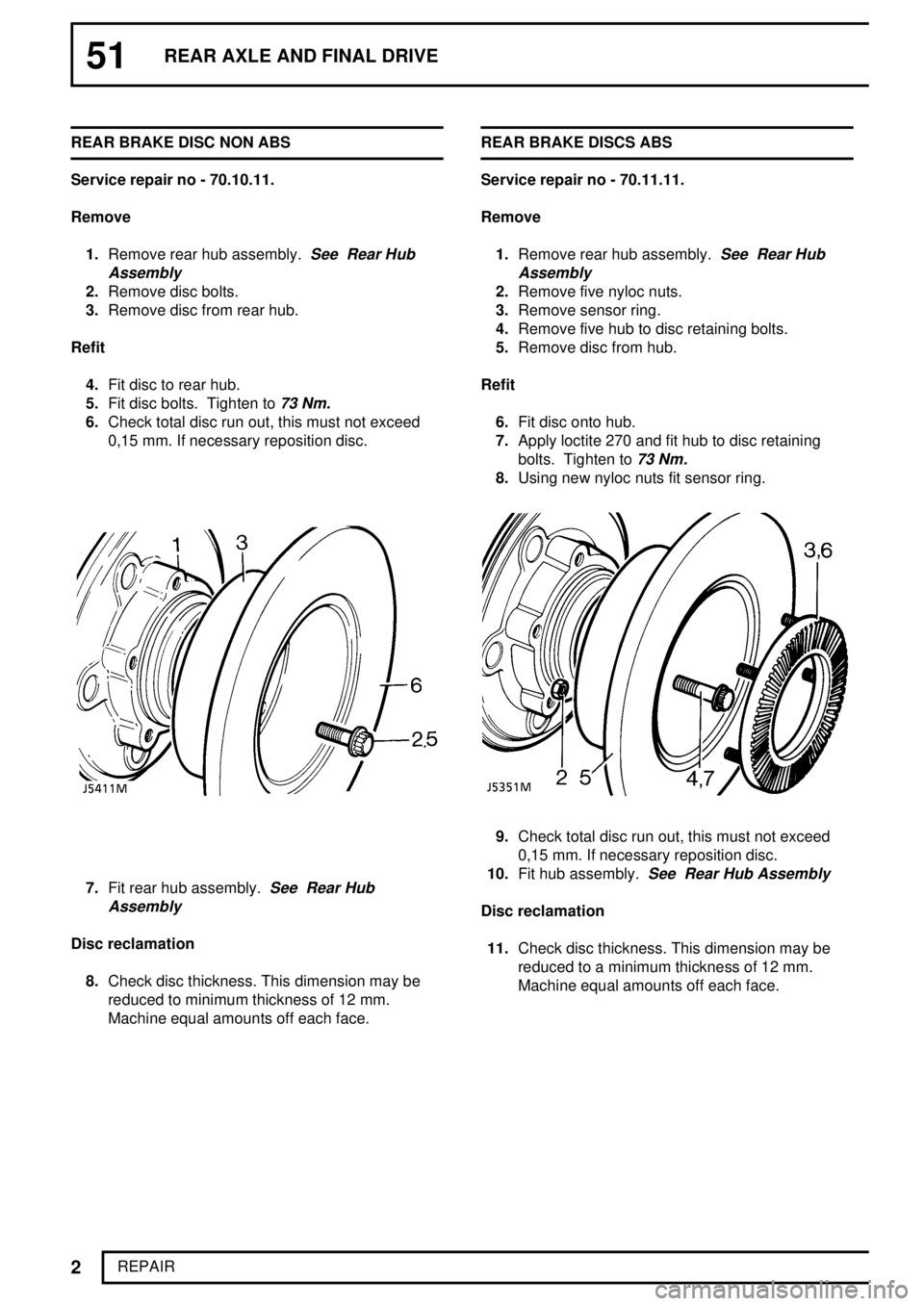
51REAR AXLE AND FINAL DRIVE
2
REPAIR REAR BRAKE DISC NON ABS
Service repair no - 70.10.11.
Remove
1.Remove rear hub assembly.
See Rear Hub
Assembly
2.Remove disc bolts.
3.Remove disc from rear hub.
Refit
4.Fit disc to rear hub.
5.Fit disc bolts. Tighten to
73 Nm.
6.Check total disc run out, this must not exceed
0,15 mm. If necessary reposition disc.
7.Fit rear hub assembly.See Rear Hub
Assembly
Disc reclamation
8.Check disc thickness. This dimension may be
reduced to minimum thickness of 12 mm.
Machine equal amounts off each face.REAR BRAKE DISCS ABS
Service repair no - 70.11.11.
Remove
1.Remove rear hub assembly.
See Rear Hub
Assembly
2.Remove five nyloc nuts.
3.Remove sensor ring.
4.Remove five hub to disc retaining bolts.
5.Remove disc from hub.
Refit
6.Fit disc onto hub.
7.Apply loctite 270 and fit hub to disc retaining
bolts. Tighten to
73 Nm.
8.Using new nyloc nuts fit sensor ring.
9.Check total disc run out, this must not exceed
0,15 mm. If necessary reposition disc.
10.Fit hub assembly.
See Rear Hub Assembly
Disc reclamation
11.Check disc thickness. This dimension may be
reduced to a minimum thickness of 12 mm.
Machine equal amounts off each face.
Page 477 of 873
REAR AXLE AND FINAL DRIVE
3
REPAIR REAR HUB ASSEMBLY
Service repair no - 64.15.01
Remove
1.Place rear axle onto axle stands and remove
road wheel.
2.Release brake hose clips and remove brake
caliper bolts. Secure to one side.
WARNING: Take care not to kink brake
hose.
3.Remove five bolts and withdraw axle shaft.
4.Remove joint washer.
5.Bend back lock washer tabs.
6.Remove locknut and lock washer.
7.Remove hub adjusting nut.
8.Remove spacing washer.
9.Remove hub and brake disc assembly complete
with bearings.REAR HUB COMPONENTS
1. Sensor ring retaining nut ABS.
2. Axle shaft.
3. Axle shaft joint washer.
4. Axle shaft retaining bolt (five off).
5. Lock nut.
6. Lock washer.
7. Hub adjusting nut.
8. Spacing washer.
9. Outer bearing.
10. Hub.
11. Inner bearing.
12. Grease seal.
13. Brake disc.
14. Disc retaining bolt (five off).
15. Sensor ring ABS.
Page 478 of 873
51REAR AXLE AND FINAL DRIVE
4
REPAIR Refit
10.Clean stub axle. Retract ABS sensor slightly
from sensor sleeve, if applicable
11.Fit hub assembly to stub axle.
12.Fit spacing washer.
13.Fit hub adjusting nut. Tighten to
61 Nm.
Back off adjusting nut 90°. Tighten to4 Nm.
This will give the required hub end float of
0,010mm
14.Fit a new lock washer.
15.Fit locknut. Tighten to61 Nm.
16.Tab over lock washer to secure adjusting nut
and locknut.
17.Using a new joint washer fit axle shaft to hub,
secure with five bolts. Tighten to
65 Nm.
18.Fit brake caliper. Tighten to82 Nm.
Secure brake pipes to axle casing.
19.If applicable, set ABS brakes sensor.
Push sensor in until it touches sensor ring then
rotate hub to set sensor.
20.Fit road wheel, remove axle stands and final
tighten road wheel nuts to
126 Nm.
21.Operate footbrake to locate brake pads before
driving vehicle.