Page 361 of 873
26COOLING SYSTEM
2
FAULT DIAGNOSIS ENGINE RUNS COLD
Before conducting any cooling system diagnosis:
See
Description and operation, Engine cooling
1.Check operation of viscous unit.See
Description and operation, Viscous Fan
Is viscous unit operating correctly?
NO -
See Repair, Viscous coupling, fan
blades, pulley and fan cowl
YES - Continue.
2.Is thermostat correct type and operating?
See
Repair, Thermostat
If problem is not diagnosed: Continue.
3.Are the air conditioning fans operating
continuously?
YES -
See Electrical Trouble Shooting
Manual.
NO - Continue.
4.Is temperature sender and gauge giving
accurate readings? Substitute parts and
compare readings. If problem is not diagnosed
repeat tests, starting at 1.
Page 362 of 873
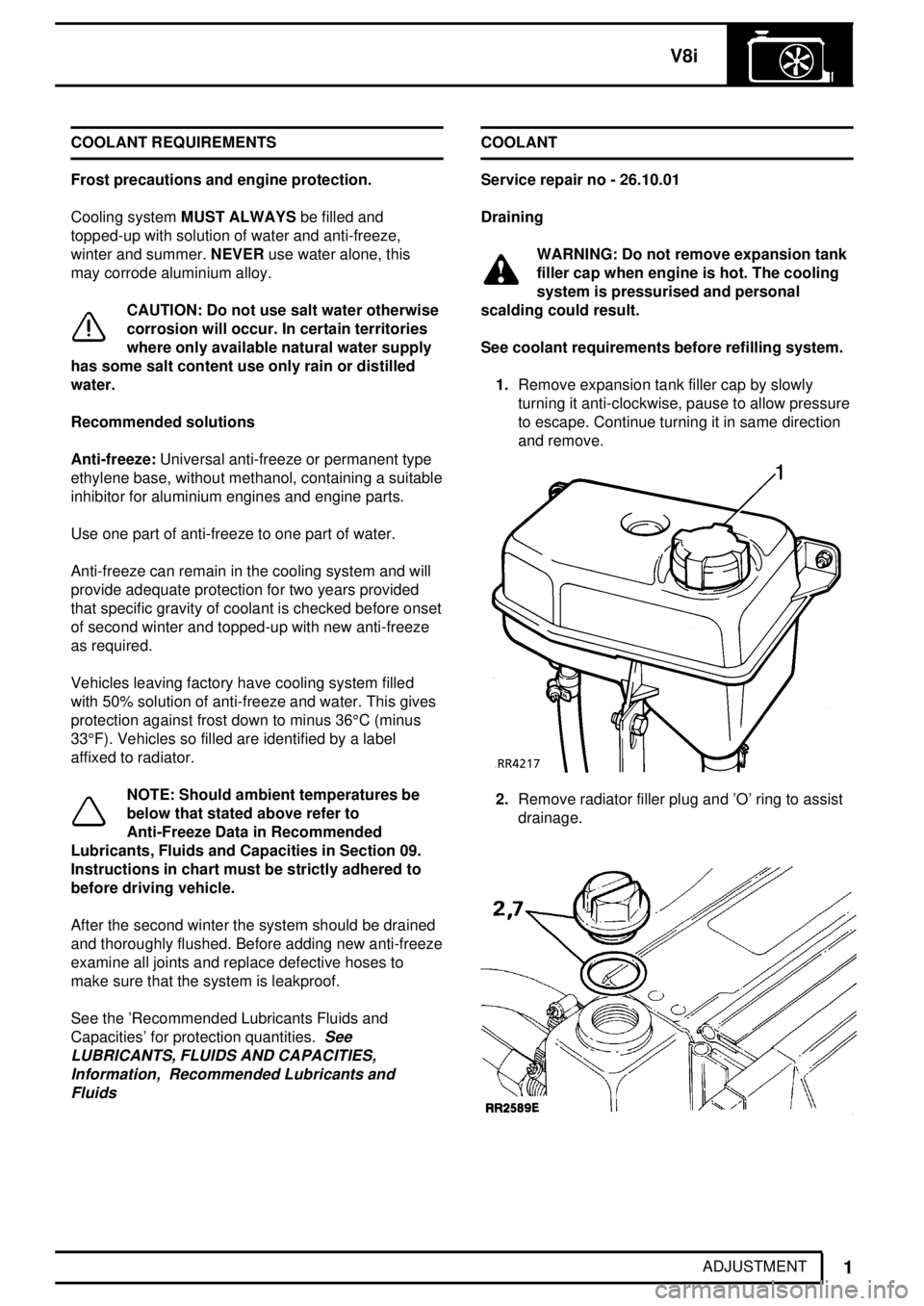
V8i
1
ADJUSTMENT COOLANT REQUIREMENTS
Frost precautions and engine protection.
Cooling systemMUST ALWAYSbe filled and
topped-up with solution of water and anti-freeze,
winter and summer.NEVERuse water alone, this
may corrode aluminium alloy.
CAUTION: Do not use salt water otherwise
corrosion will occur. In certain territories
where only available natural water supply
has some salt content use only rain or distilled
water.
Recommended solutions
Anti-freeze:Universal anti-freeze or permanent type
ethylene base, without methanol, containing a suitable
inhibitor for aluminium engines and engine parts.
Use one part of anti-freeze to one part of water.
Anti-freeze can remain in the cooling system and will
provide adequate protection for two years provided
that specific gravity of coolant is checked before onset
of second winter and topped-up with new anti-freeze
as required.
Vehicles leaving factory have cooling system filled
with 50% solution of anti-freeze and water. This gives
protection against frost down to minus 36°C (minus
33°F). Vehicles so filled are identified by a label
affixed to radiator.
NOTE: Should ambient temperatures be
below that stated above refer to
Anti-Freeze Data in Recommended
Lubricants, Fluids and Capacities in Section 09.
Instructions in chart must be strictly adhered to
before driving vehicle.
After the second winter the system should be drained
and thoroughly flushed. Before adding new anti-freeze
examine all joints and replace defective hoses to
make sure that the system is leakproof.
See the 'Recommended Lubricants Fluids and
Capacities' for protection quantities.
See
LUBRICANTS, FLUIDS AND CAPACITIES,
Information, Recommended Lubricants and
Fluids
COOLANT
Service repair no - 26.10.01
Draining
WARNING: Do not remove expansion tank
filler cap when engine is hot. The cooling
system is pressurised and personal
scalding could result.
See coolant requirements before refilling system.
1.Remove expansion tank filler cap by slowly
turning it anti-clockwise, pause to allow pressure
to escape. Continue turning it in same direction
and remove.
2.Remove radiator filler plug and 'O' ring to assist
drainage.
Page 363 of 873
26COOLING SYSTEM
2
ADJUSTMENT 3.Disconnect bottom hose from radiator. Drain
coolant into a clean container. Reconnect bottom
hose, re-tighten hose clamp.
NOTE: It is not possible to drain all coolant
retained in heater system. It is not
desirable to flush through system, after
draining.
4.Remove engine drain plugs, one each side of
cylinder block, beneath exhaust manifolds. Drain
coolant, refit and tighten plugs.
5.Pour correct solution of water and anti-freeze
into expansion tank until radiator is full.
6.Start engine, run it until normal operating
temperature is attained, topping up as
necessary.
7.Refit radiator filler plug and 'O' ring, with new 'O'
ring if required. Tighten to
6 Nm.
8.Fit expansion tank filler cap.
9.Allow engine to cool, check coolant level. Finally
top up expansion tank until level reaches seam
of expansion tank.
Page 364 of 873
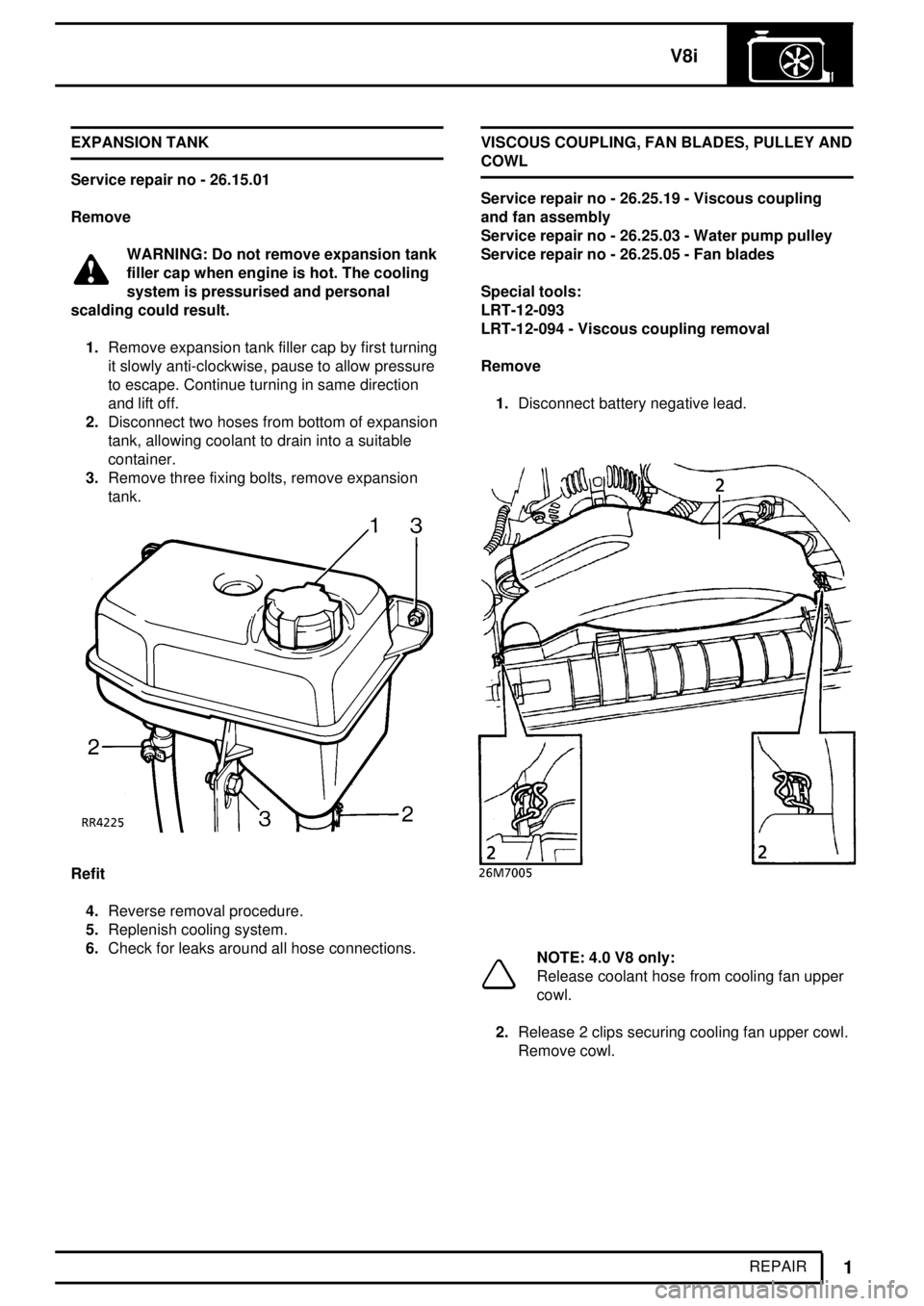
V8i
1
REPAIR EXPANSION TANK
Service repair no - 26.15.01
Remove
WARNING: Do not remove expansion tank
filler cap when engine is hot. The cooling
system is pressurised and personal
scalding could result.
1.Remove expansion tank filler cap by first turning
it slowly anti-clockwise, pause to allow pressure
to escape. Continue turning in same direction
and lift off.
2.Disconnect two hoses from bottom of expansion
tank, allowing coolant to drain into a suitable
container.
3.Remove three fixing bolts, remove expansion
tank.
Refit
4.Reverse removal procedure.
5.Replenish cooling system.
6.Check for leaks around all hose connections.VISCOUS COUPLING, FAN BLADES, PULLEY AND
COWL
Service repair no - 26.25.19 - Viscous coupling
and fan assembly
Service repair no - 26.25.03 - Water pump pulley
Service repair no - 26.25.05 - Fan blades
Special tools:
LRT-12-093
LRT-12-094 - Viscous coupling removal
Remove
1.Disconnect battery negative lead.
NOTE: 4.0 V8 only:
Release coolant hose from cooling fan upper
cowl.
2.Release 2 clips securing cooling fan upper cowl.
Remove cowl.
Page 367 of 873
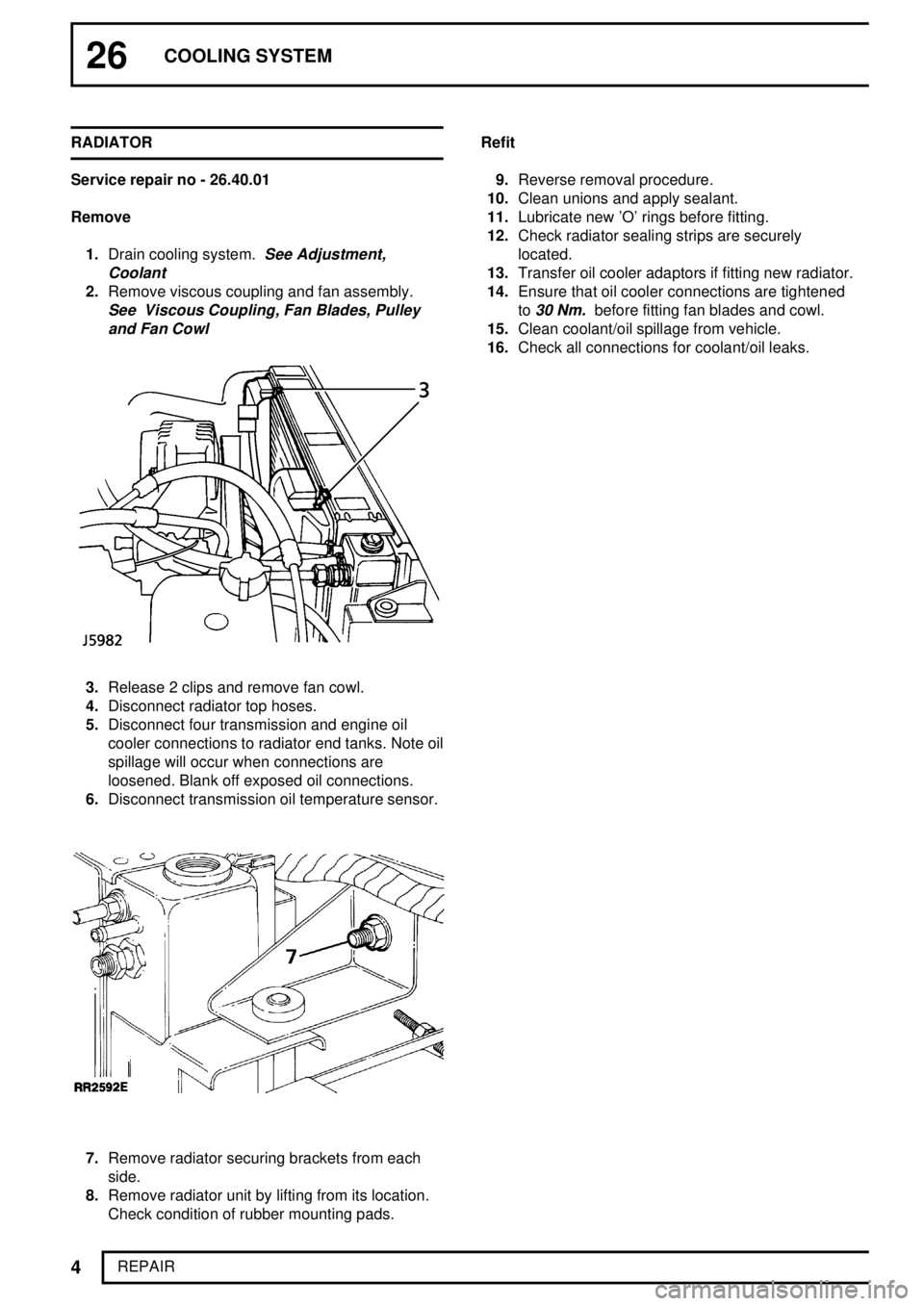
26COOLING SYSTEM
4
REPAIR RADIATOR
Service repair no - 26.40.01
Remove
1.Drain cooling system.
See Adjustment,
Coolant
2.Remove viscous coupling and fan assembly.
See Viscous Coupling, Fan Blades, Pulley
and Fan Cowl
3.Release 2 clips and remove fan cowl.
4.Disconnect radiator top hoses.
5.Disconnect four transmission and engine oil
cooler connections to radiator end tanks. Note oil
spillage will occur when connections are
loosened. Blank off exposed oil connections.
6.Disconnect transmission oil temperature sensor.
7.Remove radiator securing brackets from each
side.
8.Remove radiator unit by lifting from its location.
Check condition of rubber mounting pads.Refit
9.Reverse removal procedure.
10.Clean unions and apply sealant.
11.Lubricate new 'O' rings before fitting.
12.Check radiator sealing strips are securely
located.
13.Transfer oil cooler adaptors if fitting new radiator.
14.Ensure that oil cooler connections are tightened
to
30 Nm.before fitting fan blades and cowl.
15.Clean coolant/oil spillage from vehicle.
16.Check all connections for coolant/oil leaks.
Page 369 of 873
26COOLING SYSTEM
6
REPAIR WATER PUMP
Service repair no - 26.50.01
Remove
WARNING: Disconnect battery negative
terminal to prevent engine being started
before removing or adjusting drive belts.
1.Drain engine cooling system.
See Adjustment,
Coolant
2.Remove fan blades and pulley.See Viscous
Coupling, Fan Blades, Pulley and Fan Cowl
3.Disconnect inlet hose from water pump.
4.Remove water pump bolts.
5.Remove water pump and joint washer.
Refit
6.Lightly grease new joint washer, position on
timing cover.
7.Clean threads of all long bolts and coat with
Loctite 572 thread lubricant-sealant.
8.Locate water pump in position. Tighten
remaining water pump housing bolts evenly to
28 Nm.
9.Reverse removal procedure. 1 to 3.
10.Check for coolant leaks around all hose
connections and joint faces.
Page 380 of 873
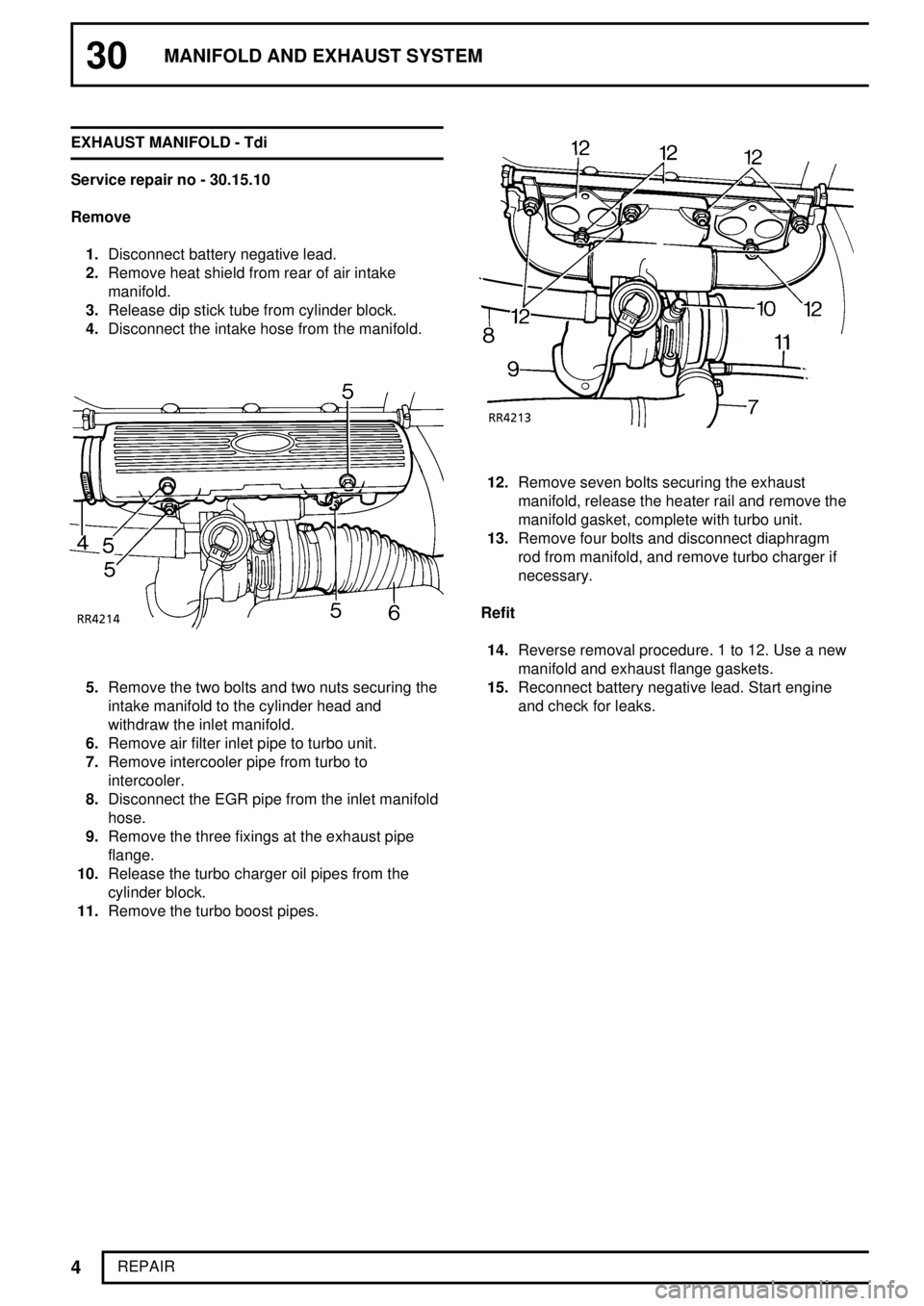
30MANIFOLD AND EXHAUST SYSTEM
4
REPAIR EXHAUST MANIFOLD - Tdi
Service repair no - 30.15.10
Remove
1.Disconnect battery negative lead.
2.Remove heat shield from rear of air intake
manifold.
3.Release dip stick tube from cylinder block.
4.Disconnect the intake hose from the manifold.
5.Remove the two bolts and two nuts securing the
intake manifold to the cylinder head and
withdraw the inlet manifold.
6.Remove air filter inlet pipe to turbo unit.
7.Remove intercooler pipe from turbo to
intercooler.
8.Disconnect the EGR pipe from the inlet manifold
hose.
9.Remove the three fixings at the exhaust pipe
flange.
10.Release the turbo charger oil pipes from the
cylinder block.
11.Remove the turbo boost pipes.
12.Remove seven bolts securing the exhaust
manifold, release the heater rail and remove the
manifold gasket, complete with turbo unit.
13.Remove four bolts and disconnect diaphragm
rod from manifold, and remove turbo charger if
necessary.
Refit
14.Reverse removal procedure. 1 to 12. Use a new
manifold and exhaust flange gaskets.
15.Reconnect battery negative lead. Start engine
and check for leaks.
Page 391 of 873

33CLUTCH
2
FAULT DIAGNOSIS FAULT/SYMPTOM CHART
Symptoms
Slip Spin/Drag Judder/Fierce Fault Item
* * * Worn or oil on clutch linings 2
* * * Mechanical damage45678
* * Distorted clutch plate 2
* Failed or air in hydraulic system 12 13
* * Primary shaft tight fit in crankshaft bush 15 17
* Clutch splines sticking 2 15
* Weak clutch plate springs or insecure/worn
engine/gearbox mountings6
* Insecure/worn propeller shafts
* Insecure/worn suspension components/rubber
bushes
For items refered to in this chart.See Description and operation, Description
CLUTCH NOISE - MECHANICAL FAULTS
Noise from clutch or gearbox in neutral, which
disappears when clutch is depressed.
Suspect gearbox input/primary shaft bearings.
See MANUAL GEARBOX, Fault diagnosis,
Manual Gearbox
- Noise from gearbox in neutral, which
disappears when clutch is depressed
Noise from clutch or gearbox in neutral, which
changes tone or becomes worse when the clutch
is depressed.
Suspect worn release bearing.
Knocking/rattling from clutch or gearbox in
neutral, which is reduced or disappears when the
clutch is depressed.
Suspect worn/weak release lever retainer or
clutch unit.
Noise from clutch or gearbox in neutral, which
disappears when clutch is depressed.
Suspect gearbox fault.
See MANUAL GEARBOX, Fault diagnosis,
Manual Gearbox
- Noise from gearbox in neutral, which
disappears when clutch is depressed.HYDRAULIC FAULTS
Unable to dis-engage clutch, little or no pedal
resistance.
1.Check condition, specification and level of fluid.
2.Check pipes and cylinders for leaks.
3.Check that air vent in reservoir lid is clear.
Suspect faulty master cylinder if no fluid leaks
present.
See Repair, Master Cylinder
Spongy pedal operation
1.Check condition, specification and level of fluid.
2.Check that air vent in reservoir lid is clear.
Suspect air in fluid.
See Repair, Bleed Hydraulic System
Clutch is difficult to dis-engage and/or does not
immediately re-engage when pedal is released.
1.Check condition, specification and level of fluid.
2.Check that air vent in reservoir lid is clear.
Suspect pedal pivot, master cylinder or slave
cylinder seizure.
See Repair, Master Cylinder