Page 304 of 1708
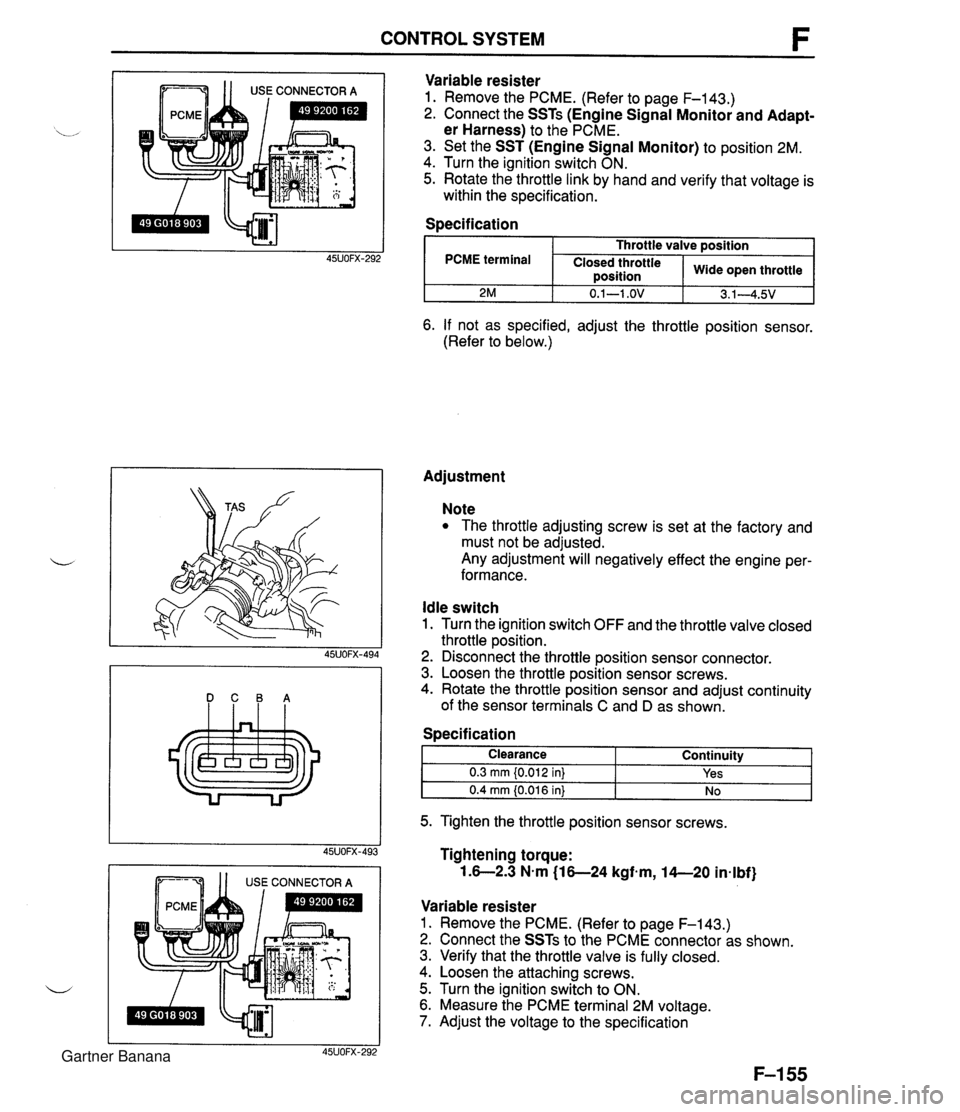
CONTROL SYSTEM DCB IIIf I 1 USECONNECTORA I Variable resister 1. Remove the PCME. (Refer to page F-143.) 2. Connect the SSTs (Engine Signal Monitor and Adapt- er Harness) to the PCME. 3. Set the SST (Engine Signal Monitor) to position 2M. 4. Turn the ignition switch ON. 5. Rotate the throttle link by hand and verify that voltage is within the specification. Specification 6. If not as specified, adjust the throttle position sensor. (Refer to below.) - PCME terminal Adjustment Throttle valve position I Wide open throttle ~osition Note The throttle adjusting screw is set at the factory and must not be adjusted. Any adjustment will negatively effect the engine per- formance. Idle switch 1. Turn the ignition switch OFF and the throttle valve closed throttle position. 2. Disconnect the throttle position sensor connector. 3. Loosen the throttle position sensor screws. 4. Rotate the throttle position sensor and adjust continuity of the sensor terminals C and D as shown. Specification I Clearance Continuity I 5. Tighten the throttle position sensor screws. 0.3 mm (0.012 in} Tightening torque: 1.6-2.3 N.m (16-24 kgf-m, 14--20 in-lbf) Yes Variable resister 1. Remove the PCME. (Refer to page F-143.) 2. Connect the SSTs to the PCME connector as shown. 3. Verify that the throttle valve is fully closed. 4. Loosen the attaching screws. 5. Turn the ignition switch to ON. 6. Measure the PCME terminal 2M voltage. 7. Adjust the voltage to the specification 0.4 mm (0.01 6 in) I No Gartner Banana
Page 305 of 1708
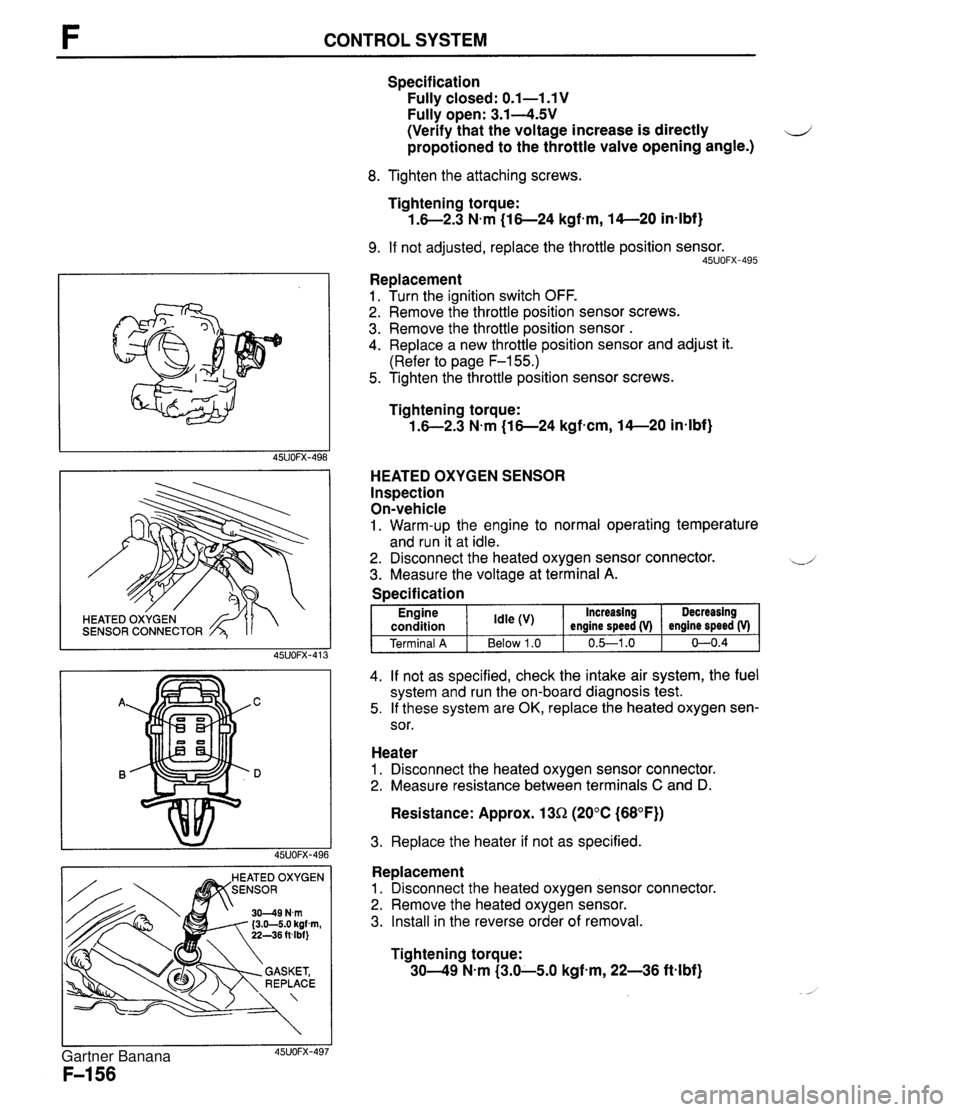
CONTROL SYSTEM SENSOR CONNECTOR EATED OXYGEN Specification Fully closed: 0.1-1.1 V Fully open: 3.14.5V (Verify that the voltage increase is directly d propotioned to the throttle valve opening angle.) 8. Tighten the attaching screws. Tightening torque: 1.6-2.3 N.m (16-24 kgfmm, 14-20 in-lbf} 9. If not adjusted, replace the throttle position sensor. 45UOFX-495 Replacement 1. Turn the ignition switch OFF. 2. Remove the throttle position sensor screws. 3. Remove the throttle position sensor . 4. Replace a new throttle position sensor and adjust it. (Refer to page F-155.) 5. Tighten the throttle position sensor screws. Tightening torque: 1.6-2.3 N.m (16-24 kgf-cm, 14-20 in-lbf} HEATED OXYGEN SENSOR Inspection On-vehicle 1. Warm-up the engine to normal operating temperature and run it at idle. 2. Disconnect the heated oxygen sensor connector. -.-' 3. Measure the voltage at terminal A. 4. If not as specified, check the intake air system, the fuel system and run the on-board diagnosis test. 5. If these system are OK, replace the heated oxygen sen- sor. Specification Heater 1. Disconnect the heated oxygen sensor connector. 2. Measure resistance between terminals C and D. Resistance: Approx. 13R (20°C (68°F)) Engine condition Terminal A 3. Replace the heater if not as specified. Increasing engine speed (V) 0.&1 .O Idle Below 1.0 Replacement 1. Disconnect the heated oxygen sensor connector. 2. Remove the heated oxygen sensor. 3. Install in the reverse order of removal. Decreasing engine speed (V) 0-0.4 Tightening torque: 3049 N-m (3.0-5.0 kgf-m, 22-36 ftlbf) Gartner Banana
Page 317 of 1708
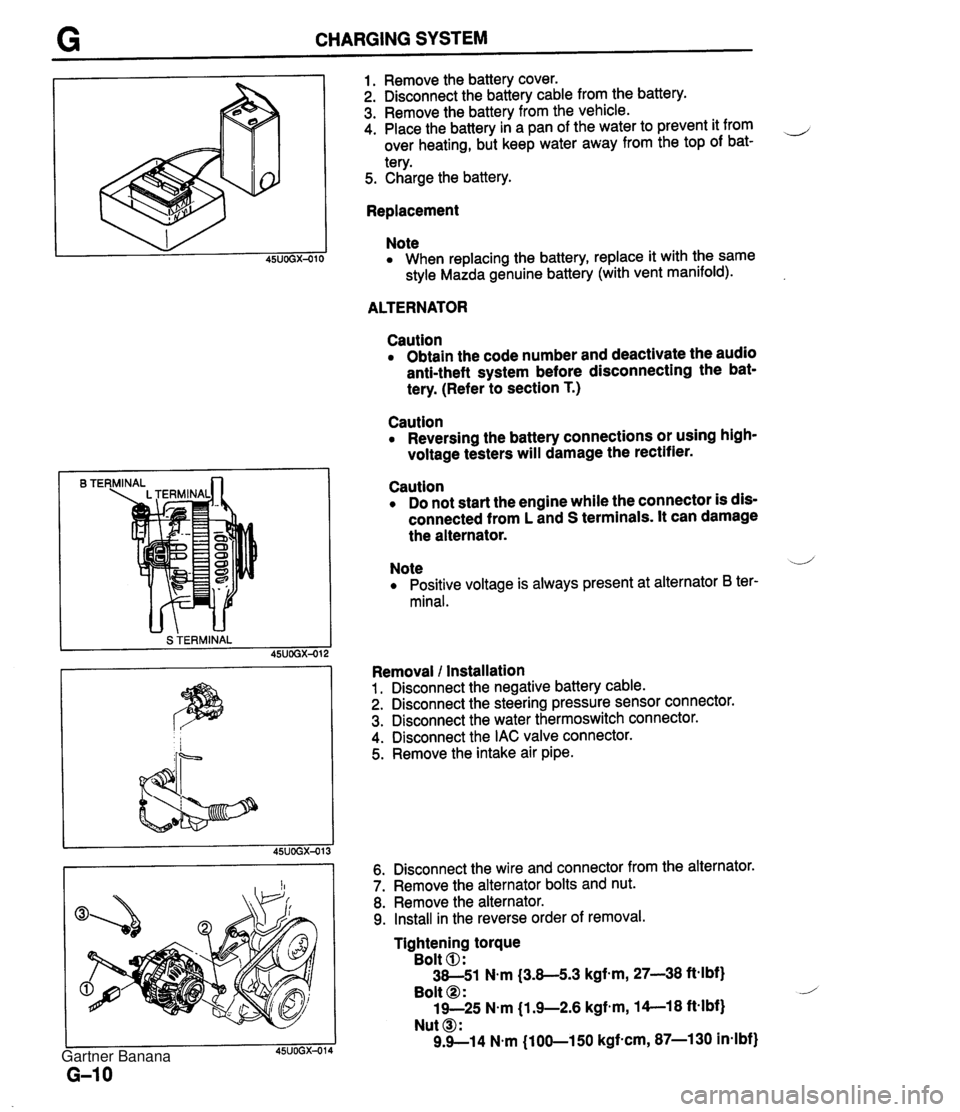
CHARGING SYSTEM B TE S TERMINAL 1. Remove the battery cover. 2. Disconnect the battery cable from the battery. 3. Remove the battery from the vehicle. 4. Place the battery in a pan of the water to prevent it from ,-, over heating, but keep water away from the top of bat- tery. 5. Charge the battery. Replacement Note When replacing the battery, replace it with the same style Mazda genuine battery (with vent manifold). ALTERNATOR Caution Obtain the code number and deactivate the audio anti-theft system before disconnecting the bat- tery. (Refer to section T.) Caution Reversing the battery connections or using high- voltage testers will damage the rectifier. Caution Do not start the engine while the connector is dis- connected from L and S terminals. It can damage the alternator. Note .--,' Positive voltage is always present at alternator B ter- minal. Removal l Installation 1. Disconnect the negative battery cable. 2. Disconnect the steering pressure sensor connector. 3. Disconnect the water thermoswitch connector. 4. Disconnect the IAC valve connector. 5. Remove the intake air pipe. 6. Disconnect the wire and connector from the alternator. 7. Remove the alternator bolts and nut. 8. Remove the alternator. 9. Install in the reverse order of removal. Tightening torque Bolt 0: 38-51 N.m (3.8-5.3 kgf-m, 27-38 ftelbf) Bolt @ : 19-25 N.m j1.9-2.6 kgfem, 14--18 ft-lbf) Nut @I: 9.9--14 N.m (100-150 kgf-cm, 87-1 30 in-lbf) Gartner Banana
Page 321 of 1708
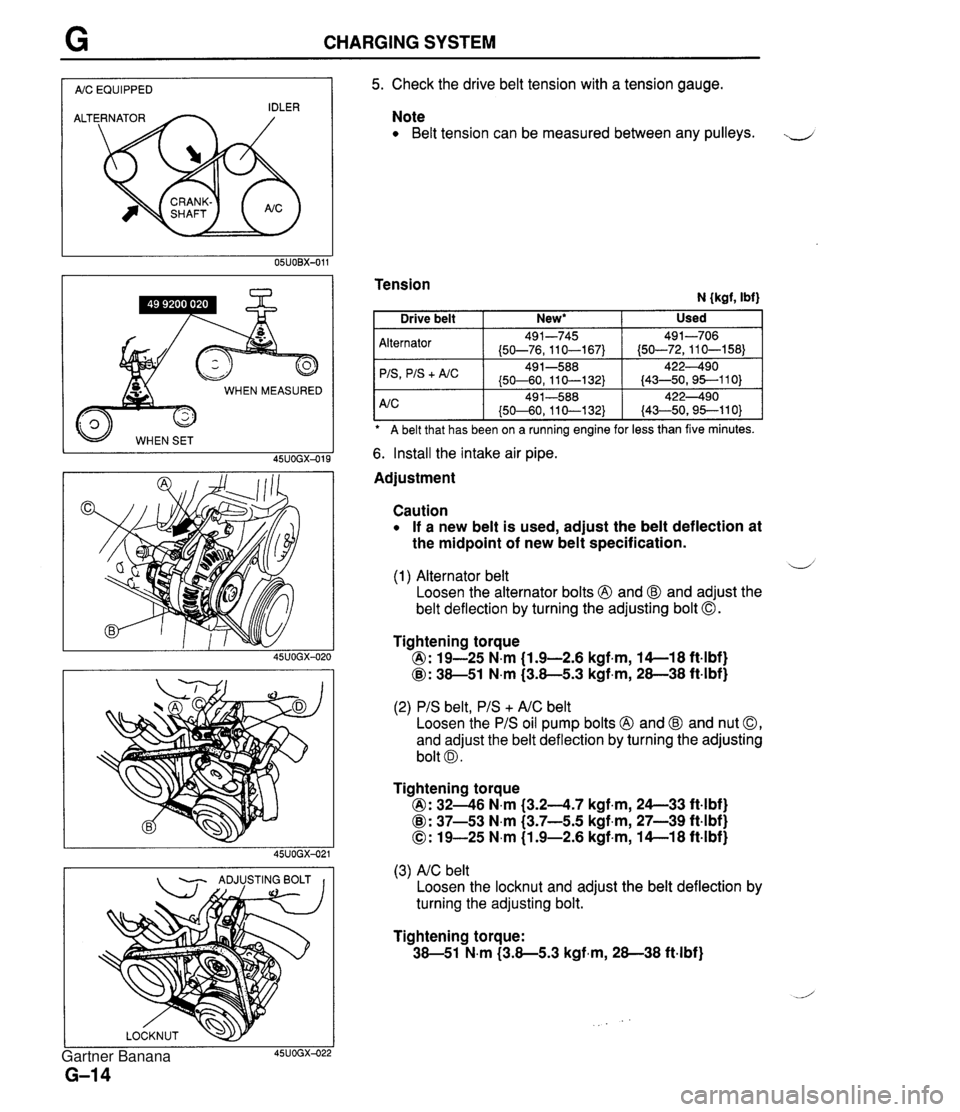
CHARGING SYSTEM I AIC EQUIPPED I WHEN MEASURED 45UOGX-015 - ADJUSTING BOLT I I 5. Check the drive belt tension with a tension gauge. Note Belt tension can be measured between any pulleys. J Tension N {kgf, Ibf) A belt that has been on a ruining engine for less than five minutes. Alternator 'IS
+ A/C 6. Install the intake air pipe. Used Drive belt Adjustment New* I Caution If a new belt is used, adjust the belt deflection at the midpoint of new belt specification. 491-745 (50-76,110-167) 49 1-588 (50-60, 11 0-1 32) d (1) Alternator belt Loosen the alternator bolts @ and @ and adjust the belt deflection by turning the adjusting bolt 0. 491-706 (50-72,110-158) 422490 (43-50,95--110) Tightening torque @: 19-25 N.m (1.9-2.6 kgf.m, 14-1 8 ft4bf) @: 38-51 N.m (3.8-5.3 kgf,m, 28-38 ft-lbf) (2) PIS belt, PIS + AIC belt Loosen the PIS oil pump bolts @ and @ and nut 0, and adjust the belt deflection by turning the adjusting bolt 0. Tightening torque @: 3246 N.m (3.24.7 kgf.m, 24--33 ft4bf) @: 37-53 N.m (3.7-5.5 kgf,m, 27-39 ft-lbf) 0: 19-25 N.m (1.9-2.6 kgf-m, 14-1 8 ft-lbf) (3) AIC belt Loosen the locknut and adjust the belt deflection by turning the adjusting bolt. Tightening torque: 38-51 N.m (3.8-5.3 kgf-m, 28-38 ft-lbf) Gartner Banana
Page 324 of 1708
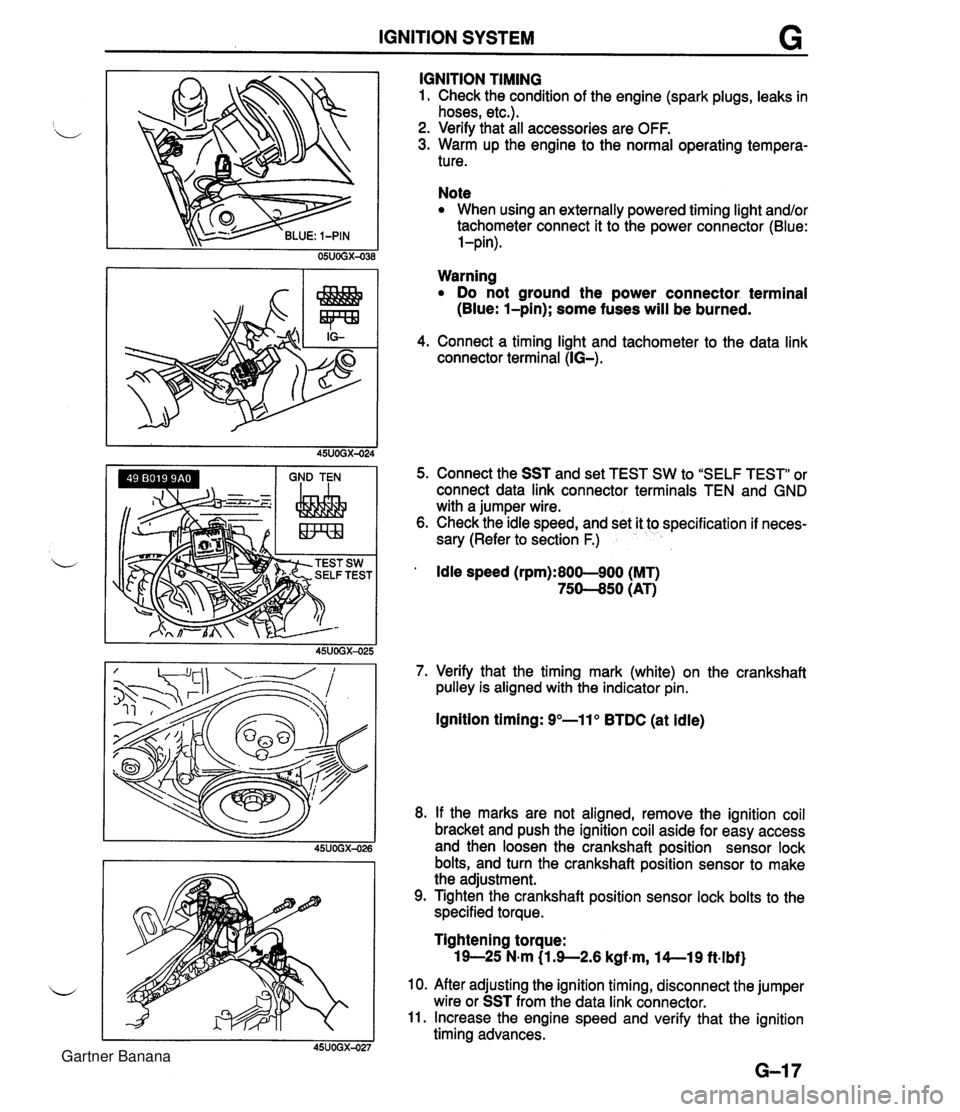
IGNITION SYSTEM G GND TEN I I I IGNITION TIMING 1. Check the condition of the engine (spark plugs, leaks in hoses, etc.). 2. Verify that all accessories are OFF. 3. Warm up the engine to the normal operating tempera- ture. Note When using an externally powered timing light and/or tachometer connect it to the power connector (Blue: l-pin). Warning Do not ground the power connector. terminal (Blue: l-pin); some fuses will be burned. 4. Connect a timing light and tachometer to the data link connector terminal (IG-). 5. Connect the SST and set TEST SW to "SELF TEST" or connect data link connector terminals TEN and GND with a jumper wire. 6. Check the idle speed, and set it to specification if neces- sary (Refer to section F.) ' Idle speed (rpm):800-900 (MT) 75-50 (AT) 7. Verify that the timing mark (white) on the crankshaft pulley is aligned with the indicator pin. Ignition timing: 9"-11" BTDC (at idle) 8. If the marks are not aligned, remove the ignition coil bracket and push the ignition coil aside for easy access and then loosen the crankshaft position sensor lock bolts, and turn the crankshaft position sensor to make the adjustment. 9. Tighten the crankshaft position sensor lock bolts to the specified torque. Tightening torque: 19-25 N-m (1 3-2.6 kgf~m, l4--19 ft.lbf) 10. After adjusting the ignition timing, disconnect the jumper wire or SST from the data link connector. 11. Increase the engine speed and verify that the ignition timing advances. Gartner Banana
Page 325 of 1708
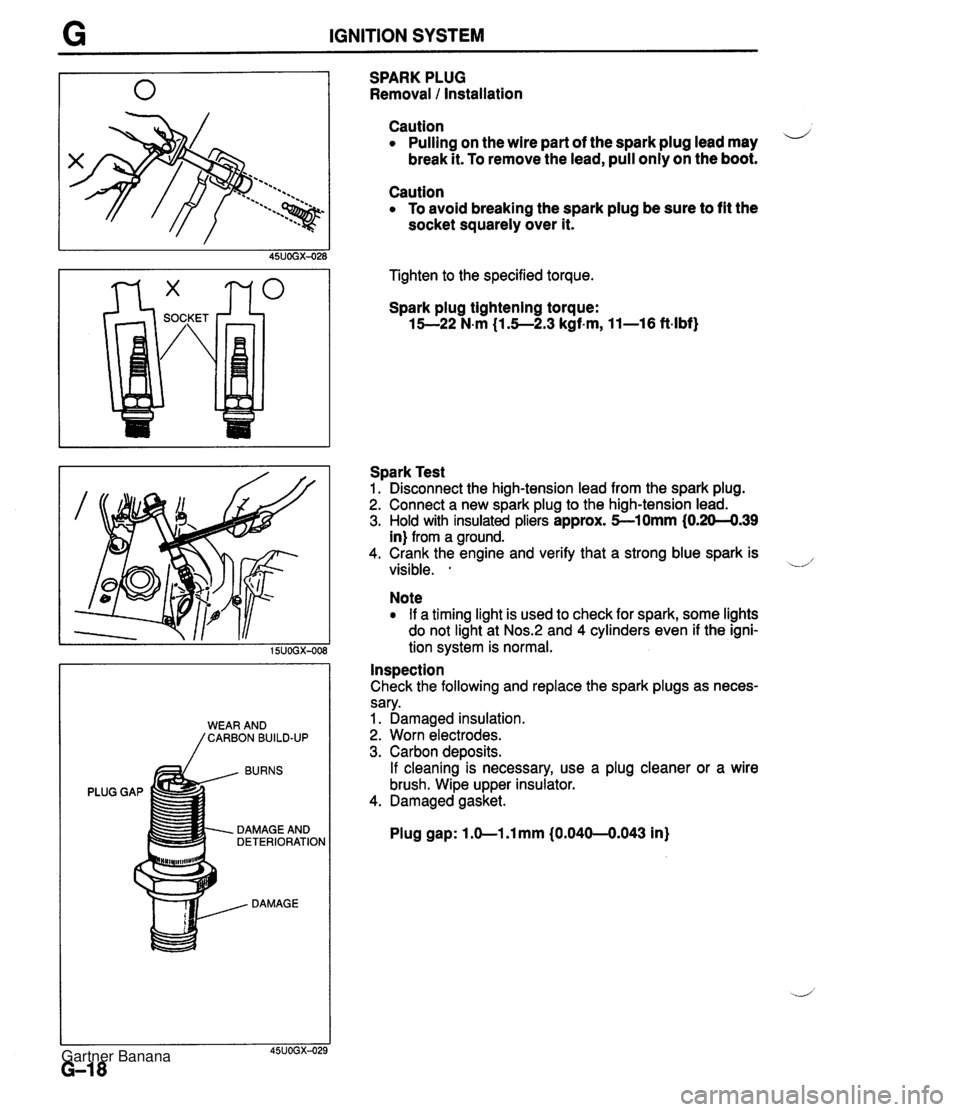
G IGNITION SYSTEM BURNS PLUG GAP DAMAGE AND DETERIORATION DAMAGE SPARK PLUG Removal 1 Installation Caution Pulling on the wire part of the spark plug lead may i/ break it. To remove the lead, pull only on the boot. Caution To avoid breaking the spark plug be sure to fit the socket squarely over it. Tighten to the specified torque. Spark plug tightening torque: 15--22 N-m (1.5--2.3 kgf-m, 11-16 ft-lbf) Spark Test 1. Disconnect the high-tension lead from the spark plug. 2. Connect a new spark plug to the high-tension lead. 3. Hold with insulated pliers approx. 5-10mm (0.20-4.39 in) from a ground. 4. Crank the engine and verify that a strong blue spark is visible. . -.d' Note If a timing light is used to check for spark, some lights do not light at Nos.:! and 4 cylinders even if the igni- tion system is normal. Inspection Check the following and replace the spark plugs as neces- sary. 1. Damaged insulation. 2. Worn electrodes. 3. Carbon deposits. If cleaning is necessary, use a plug cleaner or a wire brush. Wipe upper insulator. 4. Damaged gasket. Plug gap: 1 .O-1 .l mm (0.040-0.043 in) Gartner Banana
Page 326 of 1708
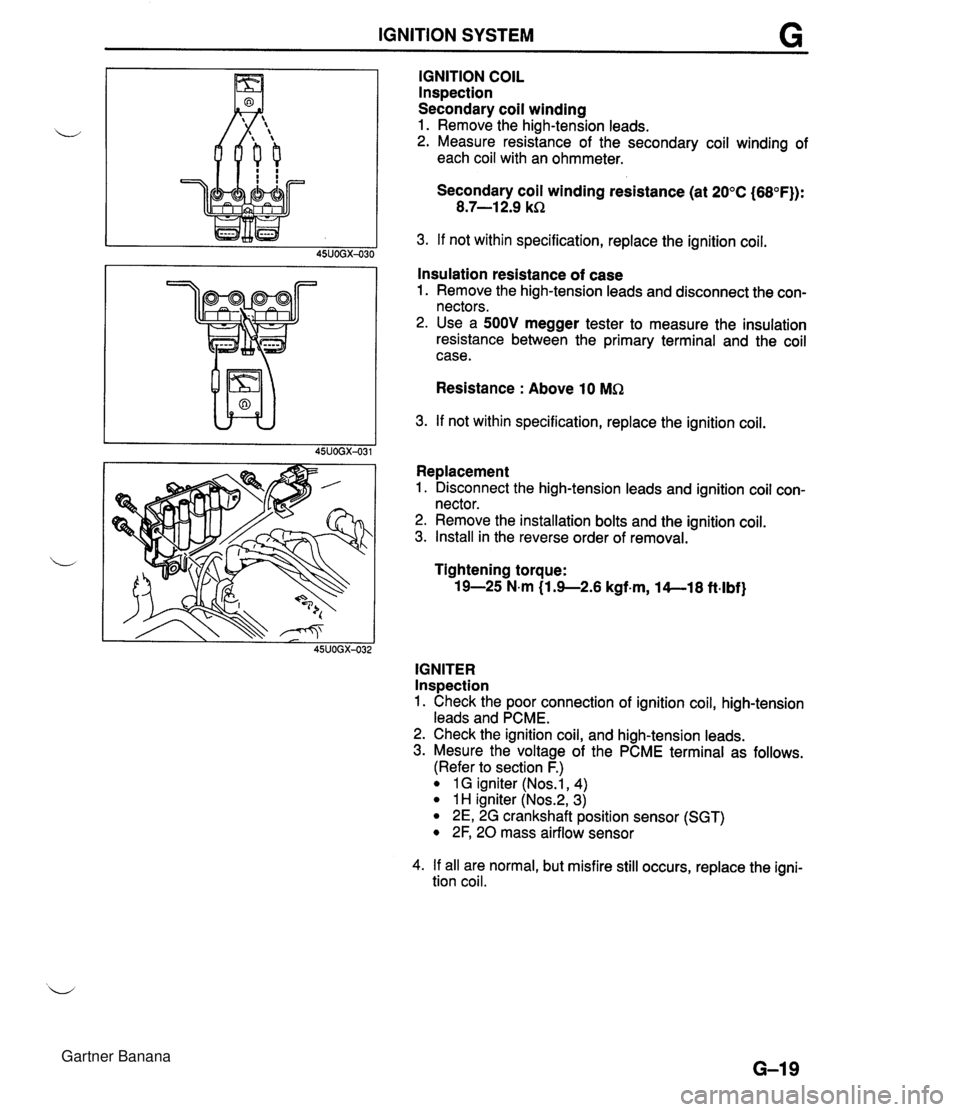
IGNITION SYSTEM IGNITION COIL lnspection Secondary coil winding 1. Remove the high-tension leads. u 2. Measure resistance of the secondary coil winding of each coil with an ohmmeter. Secondary coil winding resistance (at 20°C (68°F)): 8.7-1 2.9 kR 3. If not within specification, replace the ignition coil. 45UOGX-030 I I Insulation resistance of case 1. Remove the high-tension leads and disconnect the con- nectors. 2. Use a 500V megger tester to measure the insulation resistance between the primary terminal and the coil case. Resistance : Above 10 MR 3. If not within specification, replace the ignition coil. L I 45UOGX-031 Replacement 1. Disconnect the high-tension leads and ignition coil con- nector. 2. Remove the installation bolts and the ignition coil. 3. Install in the reverse order of removal. L Tightening torque: 19-25 N.m (1.9--2.6 kgf-m, 14--18 ft-lbf) 45UOGX-032 IGNITER Inspection 1. Check the poor connection of ignition coil, high-tension leads and PCME. 2. Check the ignition coil, and high-tension leads. 3. Mesure the voltage of the PCME terminal as follows. (Refer to section F.) 1 G igniter (Nos.1, 4) 1 H igniter (Nos.2, 3) 2E, 2G crankshaft position sensor (SGT) 2F, 20 mass airflow sensor 4. If all are normal, but misfire still occurs, replace the igni- tion coil. Gartner Banana
Page 329 of 1708
G STARTING SYSTEM Check 1 Check 3 Check 2 STARTER Caution Obtain the code number and deactivate the audio anti-theft system before disconnecting the bat- tery. (Refer to section T.) Removal / Installation 1. Disconnect the negative battery cable. 2. Disconnect the wiring from the starter. 3. Remove the starter bracket. (MT only) 4. Raise the front of the vehicle and support it with safety stands. 5. Remove the bolts and the starter. 6. Install in the reverse order of removal. Tightening torque Nut O: 10-11 N.m (100-120 kgfam, 87-100 in4bf) Bolt, Nut O: 38-51 N.m (3.8-53 kgf-m, 28-38 ft4bf) Bolt 0: 16-22 N.m (1.6-2.3 kgf.m, 12-16 ft-lbf) Bolt 0: 38-51 N.m (3.8-5.3 kgf-m, 28-38 ft-lbf) Gartner Banana