Page 7 of 181
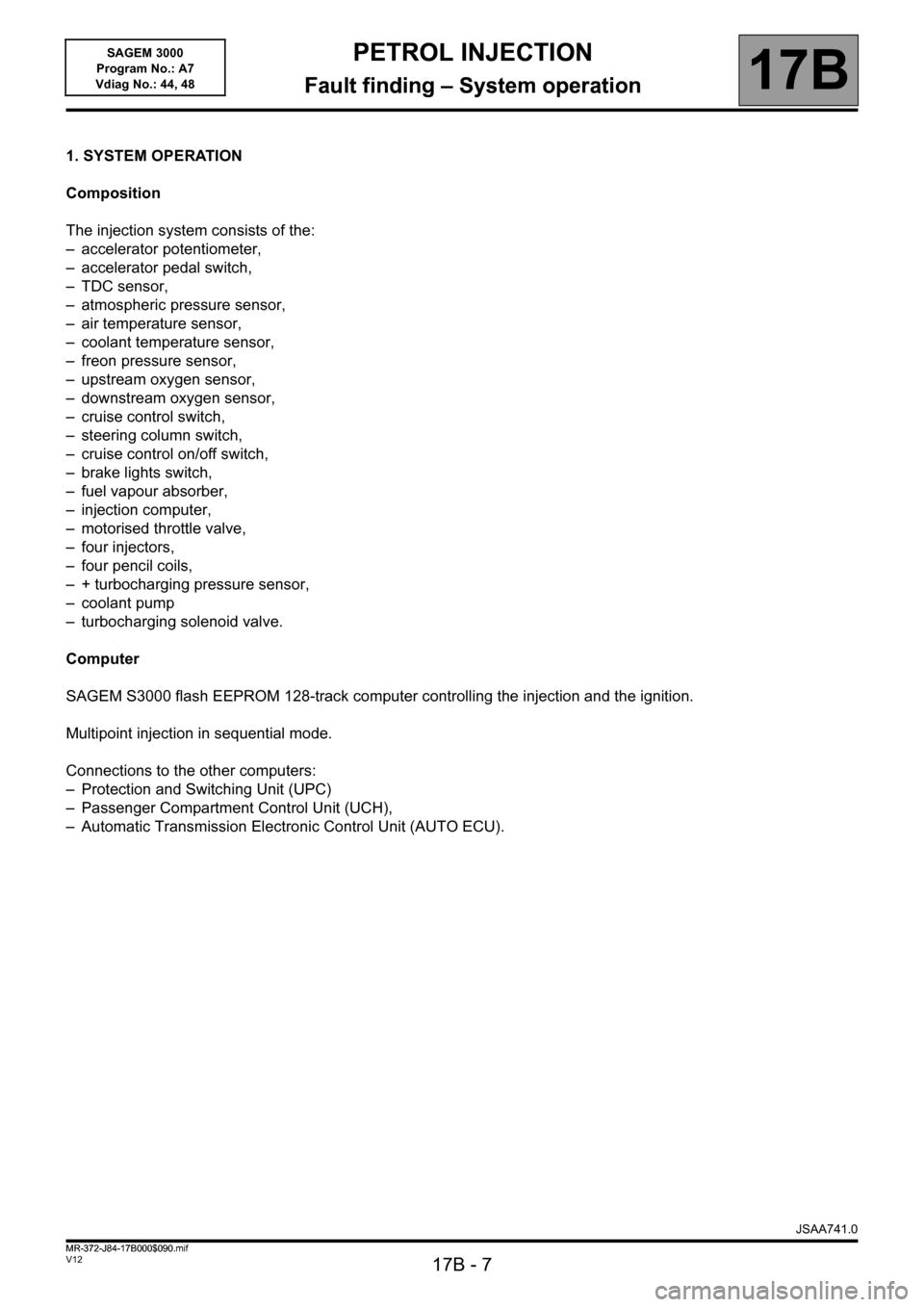
PETROL INJECTION
Fault finding – System operation17B
17B - 7V12 MR-372-J84-17B000$090.mif
SAGEM 3000
Program No.: A7
Vdiag No.: 44, 48PETROL INJECTION
Fault finding – System operation
1. SYSTEM OPERATION
Composition
The injection system consists of the:
– accelerator potentiometer,
– accelerator pedal switch,
– TDC sensor,
– atmospheric pressure sensor,
– air temperature sensor,
– coolant temperature sensor,
– freon pressure sensor,
– upstream oxygen sensor,
– downstream oxygen sensor,
– cruise control switch,
– steering column switch,
– cruise control on/off switch,
– brake lights switch,
– fuel vapour absorber,
– injection computer,
– motorised throttle valve,
– four injectors,
– four pencil coils,
– + turbocharging pressure sensor,
– coolant pump
– turbocharging solenoid valve.
Computer
SAGEM S3000 flash EEPROM 128-track computer controlling the injection and the ignition.
Multipoint injection in sequential mode.
Connections to the other computers:
– Protection and Switching Unit (UPC)
– Passenger Compartment Control Unit (UCH),
– Automatic Transmission Electronic Control Unit (AUTO ECU).
JSAA741.0
MR-372-J84-17B000$090.mif
Page 20 of 181
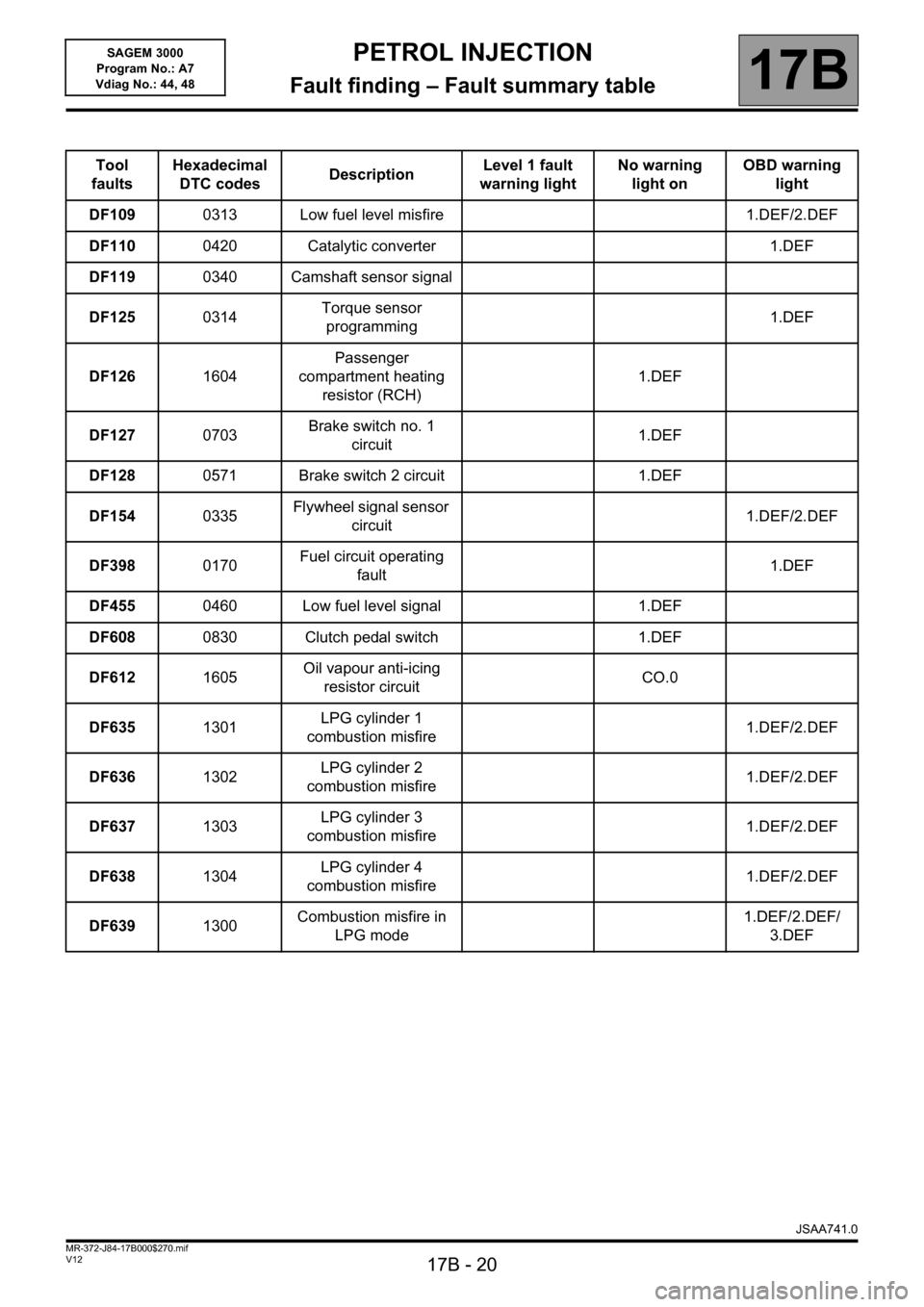
PETROL INJECTION
Fault finding – Fault summary table17B
17B - 20V12 MR-372-J84-17B000$270.mif
SAGEM 3000
Program No.: A7
Vdiag No.: 44, 48
Tool
faultsHexadecimal
DTC codesDescriptionLevel 1 fault
warning lightNo warning
light onOBD warning
light
DF1090313 Low fuel level misfire 1.DEF/2.DEF
DF1100420 Catalytic converter 1.DEF
DF1190340 Camshaft sensor signal
DF1250314Torque sensor
programming1.DEF
DF1261604Passenger
compartment heating
resistor (RCH)1.DEF
DF1270703Brake switch no. 1
circuit1.DEF
DF1280571 Brake switch 2 circuit 1.DEF
DF1540335Flywheel signal sensor
circuit1.DEF/2.DEF
DF3980170Fuel circuit operating
fault1.DEF
DF4550460 Low fuel level signal 1.DEF
DF6080830 Clutch pedal switch 1.DEF
DF6121605Oil vapour anti-icing
resistor circuitCO.0
DF6351301LPG cylinder 1
combustion misfire1.DEF/2.DEF
DF6361302LPG cylinder 2
combustion misfire1.DEF/2.DEF
DF6371303LPG cylinder 3
combustion misfire1.DEF/2.DEF
DF6381304LPG cylinder 4
combustion misfire1.DEF/2.DEF
DF6391300Combustion misfire in
LPG mode1.DEF/2.DEF/
3.DEF
JSAA741.0
Page 141 of 181
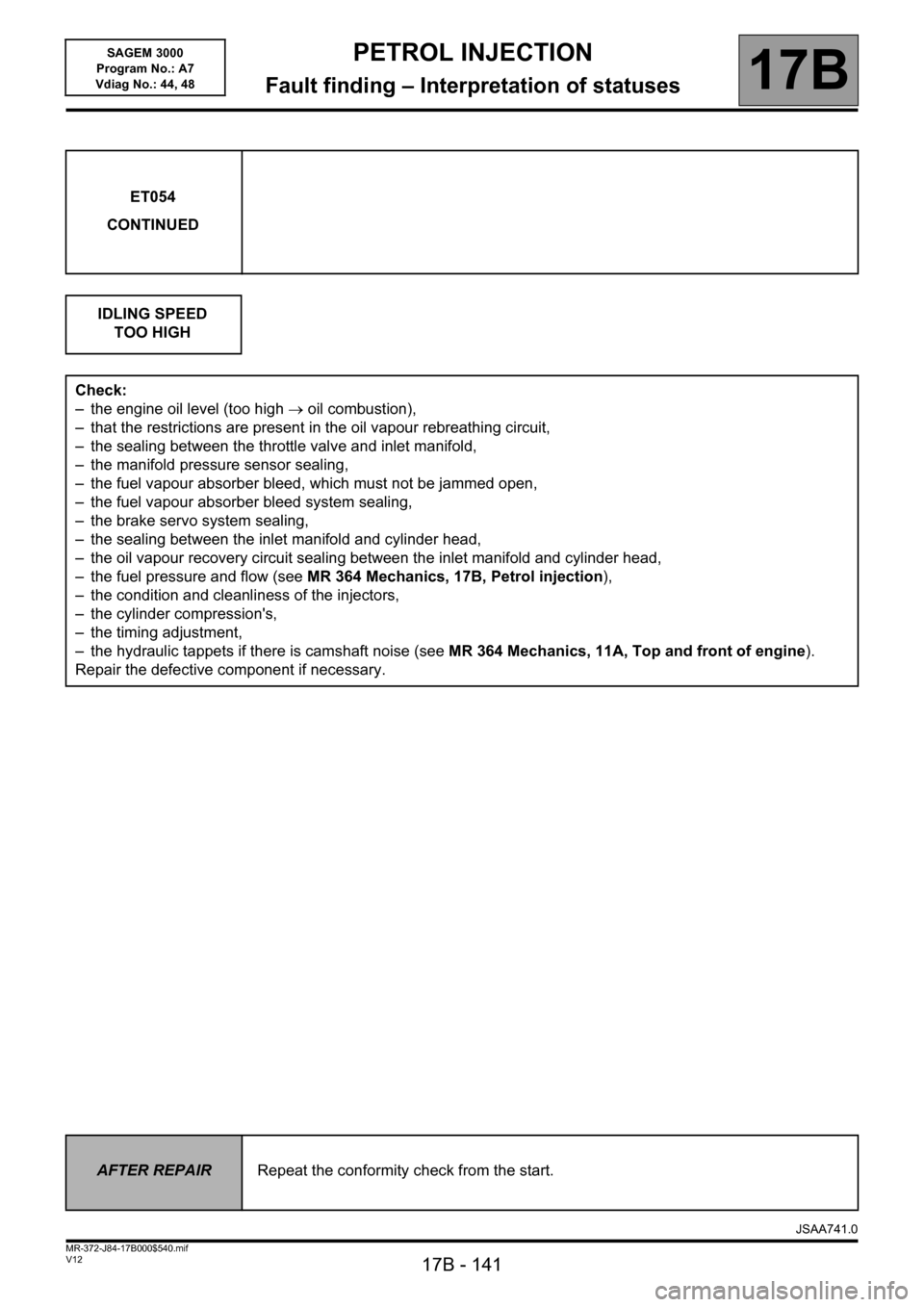
PETROL INJECTION
Fault finding – Interpretation of statuses17B
17B - 141V12 MR-372-J84-17B000$540.mif
SAGEM 3000
Program No.: A7
Vdiag No.: 44, 48
ET054
CONTINUED
IDLING SPEED
TOO HIGH
Check:
– the engine oil level (too high oil combustion),
– that the restrictions are present in the oil vapour rebreathing circuit,
– the sealing between the throttle valve and inlet manifold,
– the manifold pressure sensor sealing,
– the fuel vapour absorber bleed, which must not be jammed open,
– the fuel vapour absorber bleed system sealing,
– the brake servo system sealing,
– the sealing between the inlet manifold and cylinder head,
– the oil vapour recovery circuit sealing between the inlet manifold and cylinder head,
– the fuel pressure and flow (see MR 364 Mechanics, 17B, Petrol injection),
– the condition and cleanliness of the injectors,
– the cylinder compression's,
– the timing adjustment,
– the hydraulic tappets if there is camshaft noise (see MR 364 Mechanics, 11A, Top and front of engine).
Repair the defective component if necessary.
AFTER REPAIRRepeat the conformity check from the start.
JSAA741.0
Page 143 of 181
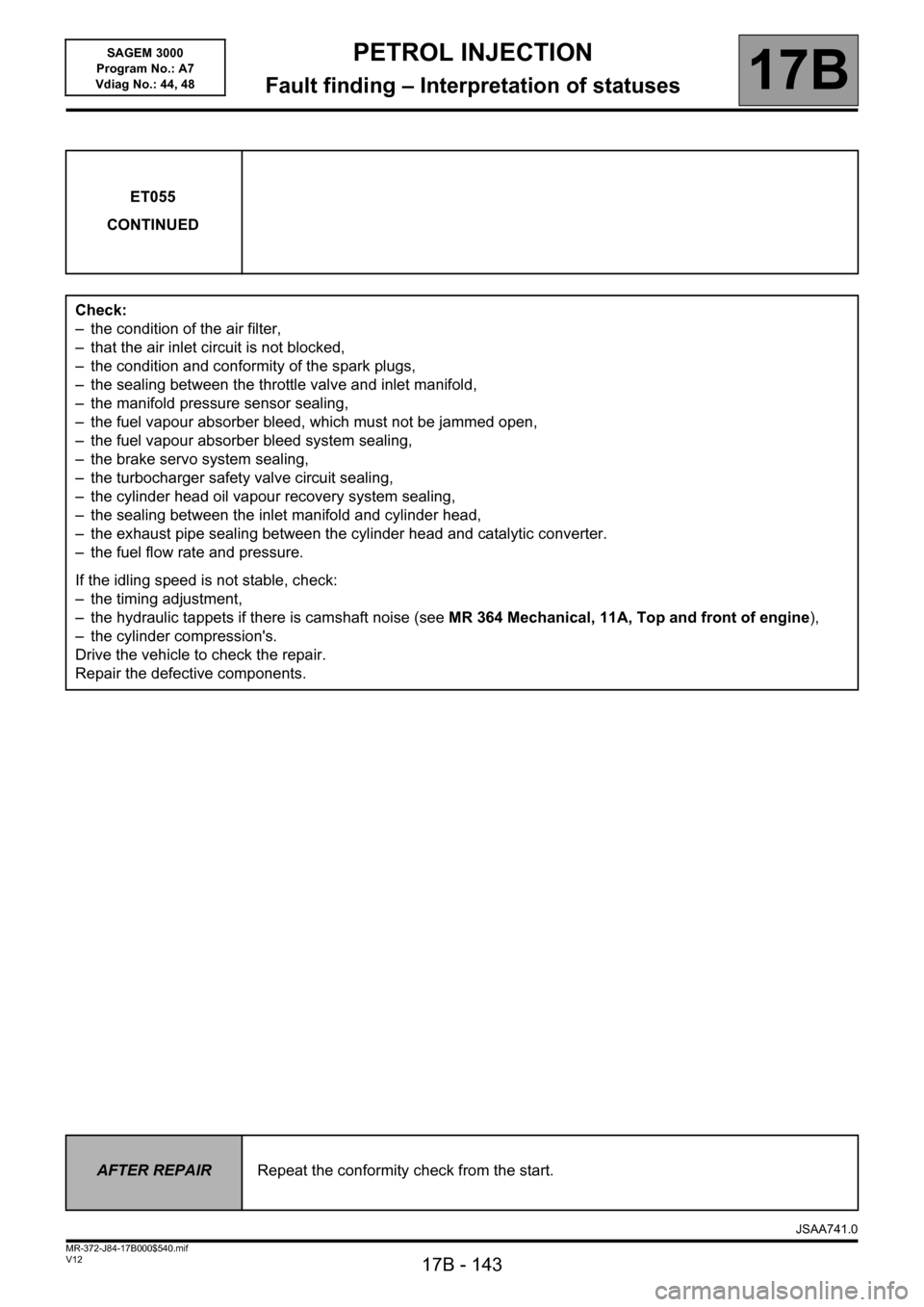
PETROL INJECTION
Fault finding – Interpretation of statuses17B
17B - 143V12 MR-372-J84-17B000$540.mif
SAGEM 3000
Program No.: A7
Vdiag No.: 44, 48
ET055
CONTINUED
Check:
– the condition of the air filter,
– that the air inlet circuit is not blocked,
– the condition and conformity of the spark plugs,
– the sealing between the throttle valve and inlet manifold,
– the manifold pressure sensor sealing,
– the fuel vapour absorber bleed, which must not be jammed open,
– the fuel vapour absorber bleed system sealing,
– the brake servo system sealing,
– the turbocharger safety valve circuit sealing,
– the cylinder head oil vapour recovery system sealing,
– the sealing between the inlet manifold and cylinder head,
– the exhaust pipe sealing between the cylinder head and catalytic converter.
– the fuel flow rate and pressure.
If the idling speed is not stable, check:
– the timing adjustment,
– the hydraulic tappets if there is camshaft noise (seeMR 364 Mechanical, 11A, Top and front of engine),
– the cylinder compression's.
Drive the vehicle to check the repair.
Repair the defective components.
AFTER REPAIRRepeat the conformity check from the start.
JSAA741.0
Page 159 of 181
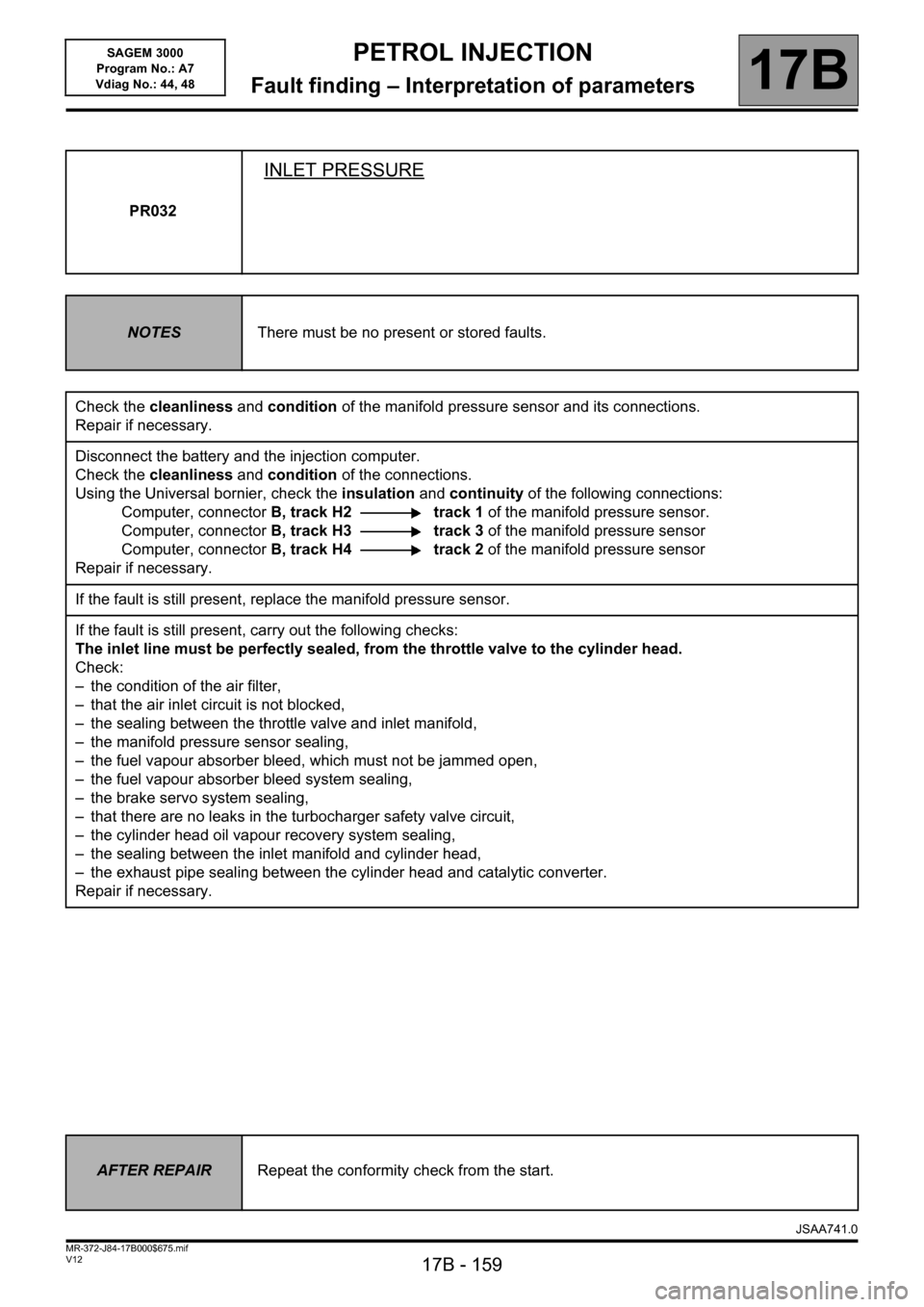
PETROL INJECTION
Fault finding – Interpretation of parameters17B
17B - 159V12 MR-372-J84-17B000$675.mif
SAGEM 3000
Program No.: A7
Vdiag No.: 44, 48
PR032
INLET PRESSURE
NOTESThere must be no present or stored faults.
Check the cleanliness and condition of the manifold pressure sensor and its connections.
Repair if necessary.
Disconnect the battery and the injection computer.
Check the cleanliness and condition of the connections.
Using the Universal bornier, check the insulation and continuity of the following connections:
Computer, connectorB, track H2 track 1 of the manifold pressure sensor.
Computer, connectorB, track H3 track 3 of the manifold pressure sensor
Computer, connectorB, track H4 track 2 of the manifold pressure sensor
Repair if necessary.
If the fault is still present, replace the manifold pressure sensor.
If the fault is still present, carry out the following checks:
The inlet line must be perfectly sealed, from the throttle valve to the cylinder head.
Check:
– the condition of the air filter,
– that the air inlet circuit is not blocked,
– the sealing between the throttle valve and inlet manifold,
– the manifold pressure sensor sealing,
– the fuel vapour absorber bleed, which must not be jammed open,
– the fuel vapour absorber bleed system sealing,
– the brake servo system sealing,
– that there are no leaks in the turbocharger safety valve circuit,
– the cylinder head oil vapour recovery system sealing,
– the sealing between the inlet manifold and cylinder head,
– the exhaust pipe sealing between the cylinder head and catalytic converter.
Repair if necessary.
AFTER REPAIRRepeat the conformity check from the start.
JSAA741.0
Page 163 of 181
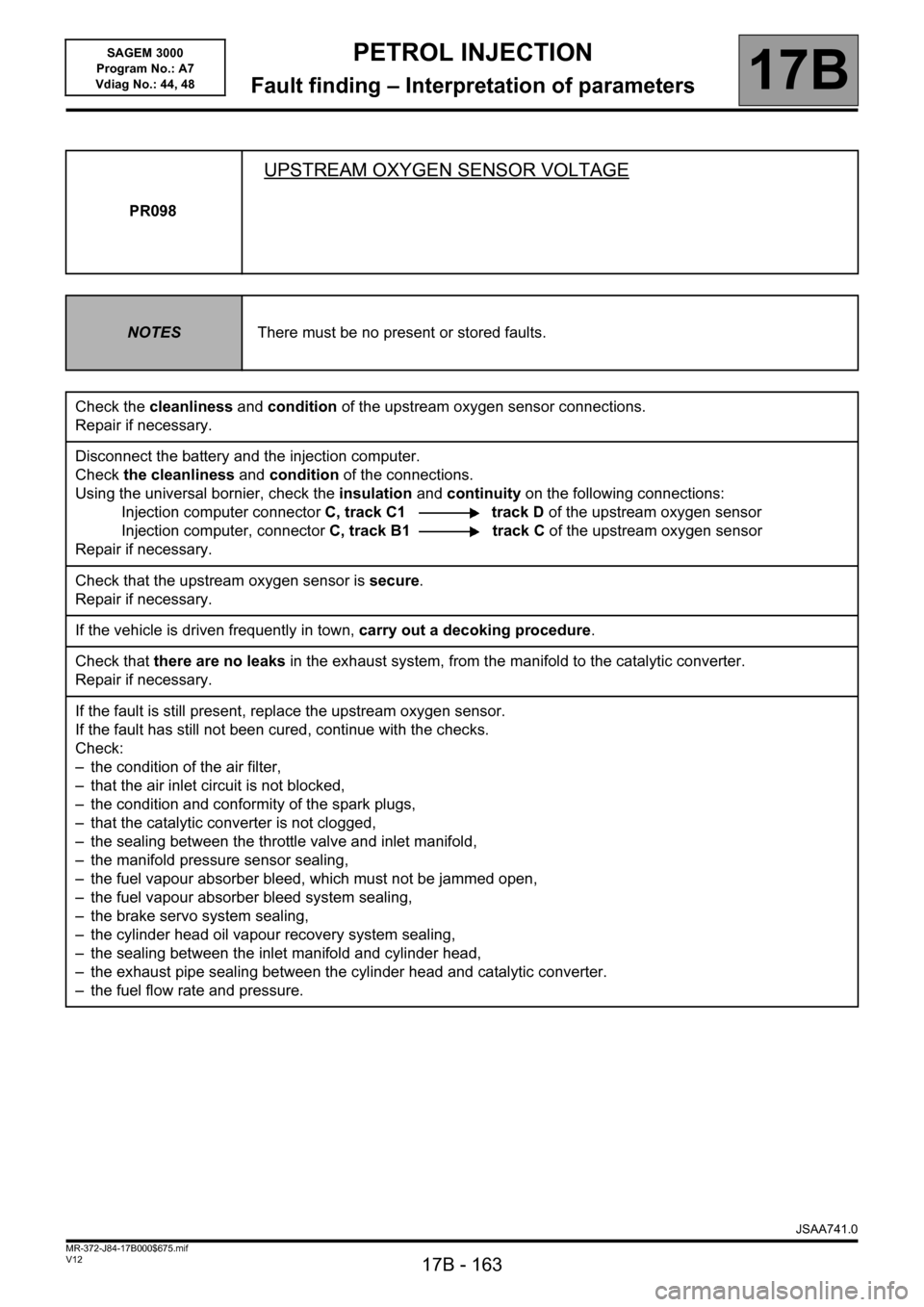
PETROL INJECTION
Fault finding – Interpretation of parameters17B
17B - 163V12 MR-372-J84-17B000$675.mif
SAGEM 3000
Program No.: A7
Vdiag No.: 44, 48
PR098
UPSTREAM OXYGEN SENSOR VOLTAGE
NOTESThere must be no present or stored faults.
Check the cleanliness and condition of the upstream oxygen sensor connections.
Repair if necessary.
Disconnect the battery and the injection computer.
Check the cleanliness and condition of the connections.
Using the universal bornier, check the insulation and continuity on the following connections:
Injection computer connectorC, track C1 track D of the upstream oxygen sensor
Injection computer, connectorC, track B1 track C of the upstream oxygen sensor
Repair if necessary.
Check that the upstream oxygen sensor is secure.
Repair if necessary.
If the vehicle is driven frequently in town, carry out a decoking procedure.
Check that there are no leaks in the exhaust system, from the manifold to the catalytic converter.
Repair if necessary.
If the fault is still present, replace the upstream oxygen sensor.
If the fault has still not been cured, continue with the checks.
Check:
– the condition of the air filter,
– that the air inlet circuit is not blocked,
– the condition and conformity of the spark plugs,
– that the catalytic converter is not clogged,
– the sealing between the throttle valve and inlet manifold,
– the manifold pressure sensor sealing,
– the fuel vapour absorber bleed, which must not be jammed open,
– the fuel vapour absorber bleed system sealing,
– the brake servo system sealing,
– the cylinder head oil vapour recovery system sealing,
– the sealing between the inlet manifold and cylinder head,
– the exhaust pipe sealing between the cylinder head and catalytic converter.
– the fuel flow rate and pressure.
JSAA741.0