Page 119 of 751
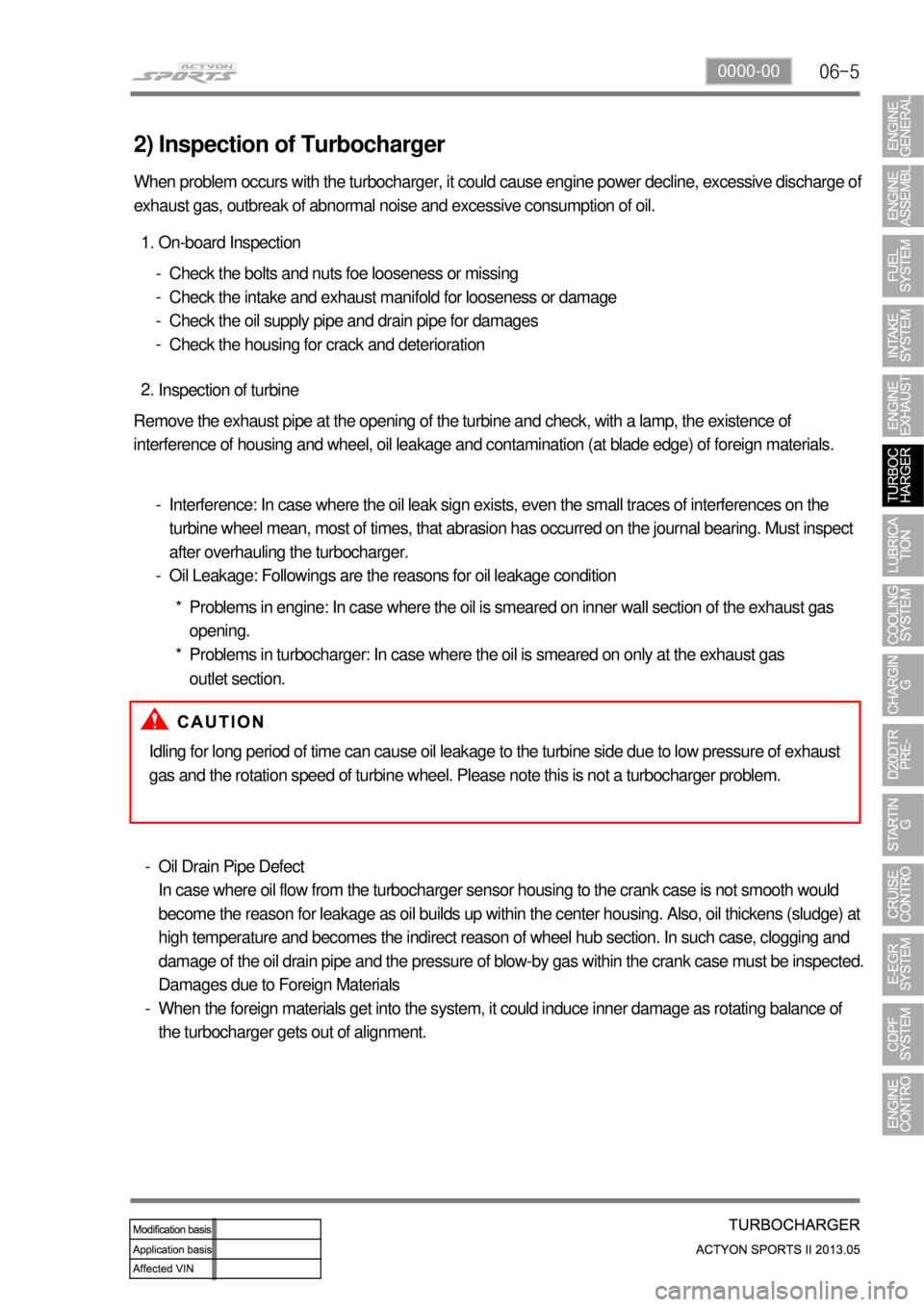
06-50000-00
2) Inspection of Turbocharger
When problem occurs with the turbocharger, it could cause engine power decline, excessive discharge of
exhaust gas, outbreak of abnormal noise and excessive consumption of oil.
On-board Inspection 1.
Check the bolts and nuts foe looseness or missing
Check the intake and exhaust manifold for looseness or damage
Check the oil supply pipe and drain pipe for damages
Check the housing for crack and deterioration -
-
-
-
Inspection of turbine 2.
Remove the exhaust pipe at the opening of the turbine and check, with a lamp, the existence of
interference of housing and wheel, oil leakage and contamination (at blade edge) of foreign materials.
Interference: In case where the oil leak sign exists, even the small traces of interferences on the
turbine wheel mean, most of times, that abrasion has occurred on the journal bearing. Must inspect
after overhauling the turbocharger.
Oil Leakage: Followings are the reasons for oil leakage condition -
-
Idling for long period of time can cause oil leakage to the turbine side due to low pressure of exhaust
gas and the rotation speed of turbine wheel. Please note this is not a turbocharger problem.
Oil Drain Pipe Defect
In case where oil flow from the turbocharger sensor housing to the crank case is not smooth would
become the reason for leakage as oil builds up within the center housing. Also, oil thickens (sludge) at
high temperature and becomes the indirect reason of wheel hub section. In such case, clogging and
damage of the oil drain pipe and the pressure of blow-by gas within the crank case must be inspected.
Damages due to Foreign Materials
When the foreign materials get into the system, it could induce inner damage as rotating balance of
the turbocharger gets out of alignment. -
-Problems in engine: In case where the oil is smeared on inner wall section of the exhaust gas
opening.
Problems in turbocharger: In case where the oil is smeared on only at the exhaust gas
outlet section. *
*
Page 125 of 751
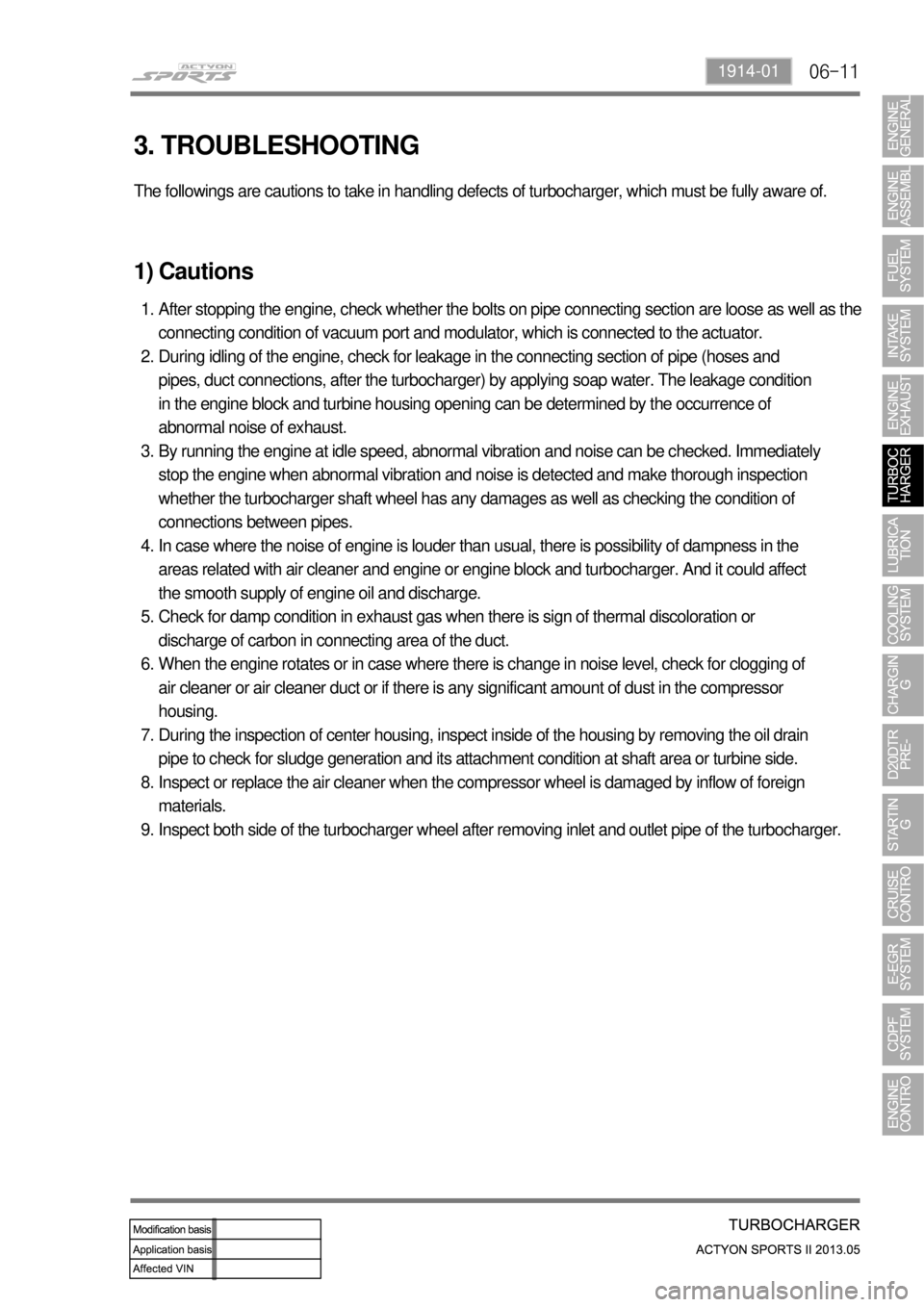
06-111914-01
3. TROUBLESHOOTING
The followings are cautions to take in handling defects of turbocharger, which must be fully aware of.
1) Cautions
After stopping the engine, check whether the bolts on pipe connecting section are loose as well as the
connecting condition of vacuum port and modulator, which is connected to the actuator.
During idling of the engine, check for leakage in the connecting section of pipe (hoses and
pipes, duct connections, after the turbocharger) by applying soap water. The leakage condition
in the engine block and turbine housing opening can be determined by the occurrence of
abnormal noise of exhaust.
By running the engine at idle speed, abnormal vibration and noise can be checked. Immediately
stop the engine when abnormal vibration and noise is detected and make thorough inspection
whether the turbocharger shaft wheel has any damages as well as checking the condition of
connections between pipes.
In case where the noise of engine is louder than usual, there is possibility of dampness in the
areas related with air cleaner and engine or engine block and turbocharger. And it could affect
the smooth supply of engine oil and discharge.
Check for damp condition in exhaust gas when there is sign of thermal discoloration or
discharge of carbon in connecting area of the duct.
When the engine rotates or in case where there is change in noise level, check for clogging of
air cleaner or air cleaner duct or if there is any significant amount of dust in the compressor
housing.
During the inspection of center housing, inspect inside of the housing by removing the oil drain
pipe to check for sludge generation and its attachment condition at shaft area or turbine side.
Inspect or replace the air cleaner when the compressor wheel is damaged by inflow of foreign
materials.
Inspect both side of the turbocharger wheel after removing inlet and outlet pipe of the turbocharger. 1.
2.
3.
4.
5.
6.
7.
8.
9.
Page 504 of 751
02-6
3. TIGHTENING TORQUE
Part nameTightening torque
(Nm)Numbers Adhesive
1. Seal bolt (rolling plunger and guide spring) 53.9~67.6 1EA Loctite
2. Guide bolt 14.7~21.5 1EA Loctite
3. Pocket ball bearing bolt 29.4~41.1 1EA Loctite
4. Reverse shift fork retainer bolt 53.9~67.6 2EA Loctite
5. Backup lamp switch 29.4~34.3 1EA Loctite
6. Oil drain plug 58.8~78.4 1EA Loctite
7. Interlock bolt 14.7~21.5 1EA -
8. Neutral switch 29.4~34.3 1EA Loctite
9. Oil filler plug 58.8~78.4 1EA Loctite
10. Extension housing bolt 42.1~53.9 12EA -
11. Concentric slave cylinder bolt 9.8~15.6 3EA -
12. Front bearing retainer bolt 19.6~24.5 8EA Loctite