Page 466 of 751
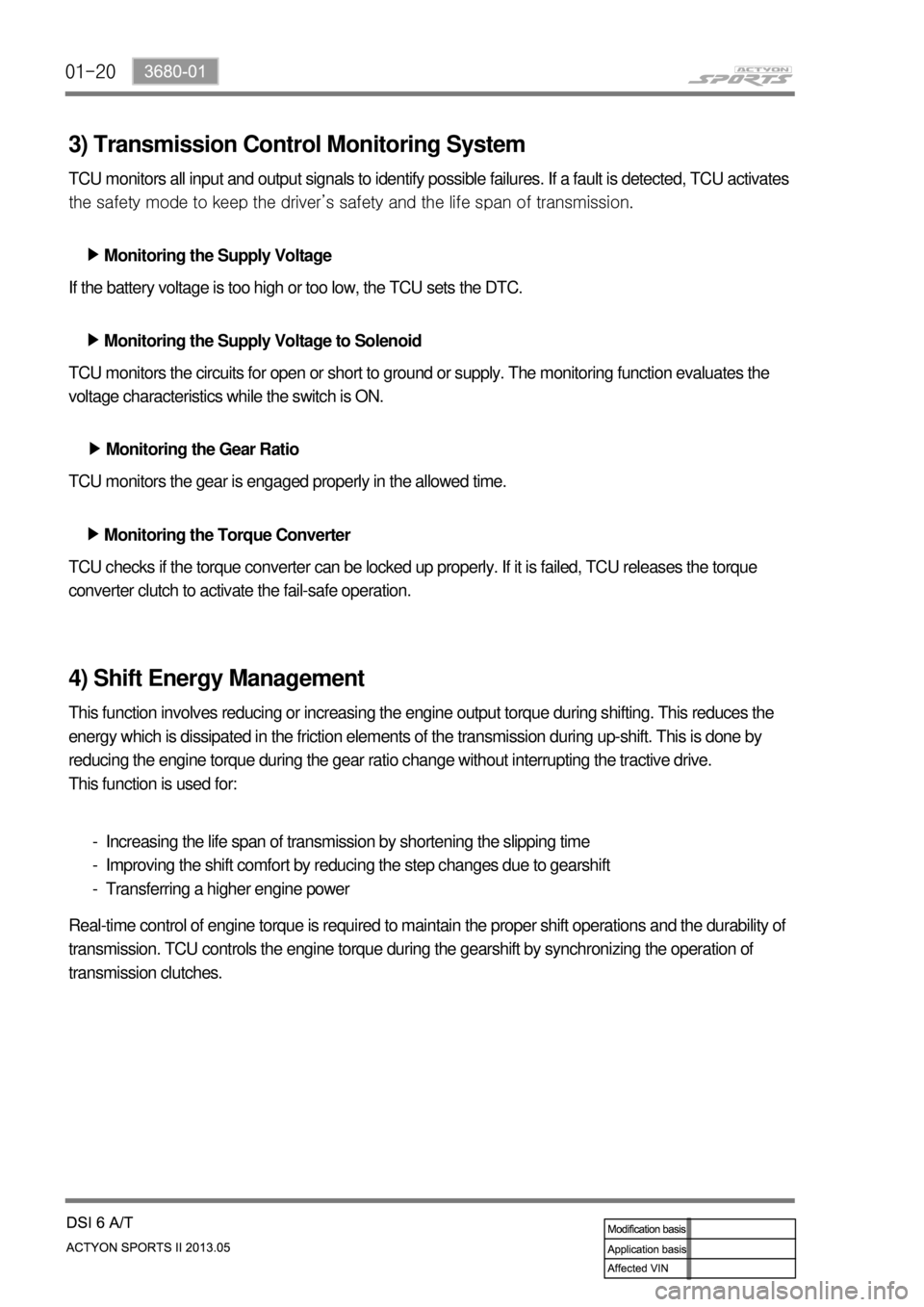
01-20
3) Transmission Control Monitoring System
TCU monitors all input and output signals to identify possible failures. If a fault is detected, TCU activates
<009b008f008c0047009a0088008d008c009b00a0004700940096008b008c0047009b009600470092008c008c00970047009b008f008c0047008b00990090009d008c009902c5009a0047009a0088008d008c009b00a0004700880095008b0047009b008f00
8c004700930090008d008c0047009a00970088009500470096>f transmission.
Monitoring the Supply Voltage ▶
Monitoring the Supply Voltage to Solenoid ▶
Monitoring the Gear Ratio ▶
Monitoring the Torque Converter ▶ If the battery voltage is too high or too low, the TCU sets the DTC.
TCU monitors the circuits for open or short to ground or supply. The monitoring function evaluates the
voltage characteristics while the switch is ON.
TCU monitors the gear is engaged properly in the allowed time.
TCU checks if the torque converter can be locked up properly. If it is failed, TCU releases the torque
converter clutch to activate the fail-safe operation.
4) Shift Energy Management
This function involves reducing or increasing the engine output torque during shifting. This reduces the
energy which is dissipated in the friction elements of the transmission during up-shift. This is done by
reducing the engine torque during the gear ratio change without interrupting the tractive drive.
This function is used for:
Increasing the life span of transmission by shortening the slipping time
Improving the shift comfort by reducing the step changes due to gearshift
Transferring a higher engine power -
-
-
Real-time control of engine torque is required to maintain the proper shift operations and the durability of
transmission. TCU controls the engine torque during the gearshift by synchronizing the operation of
transmission clutches.
Page 501 of 751
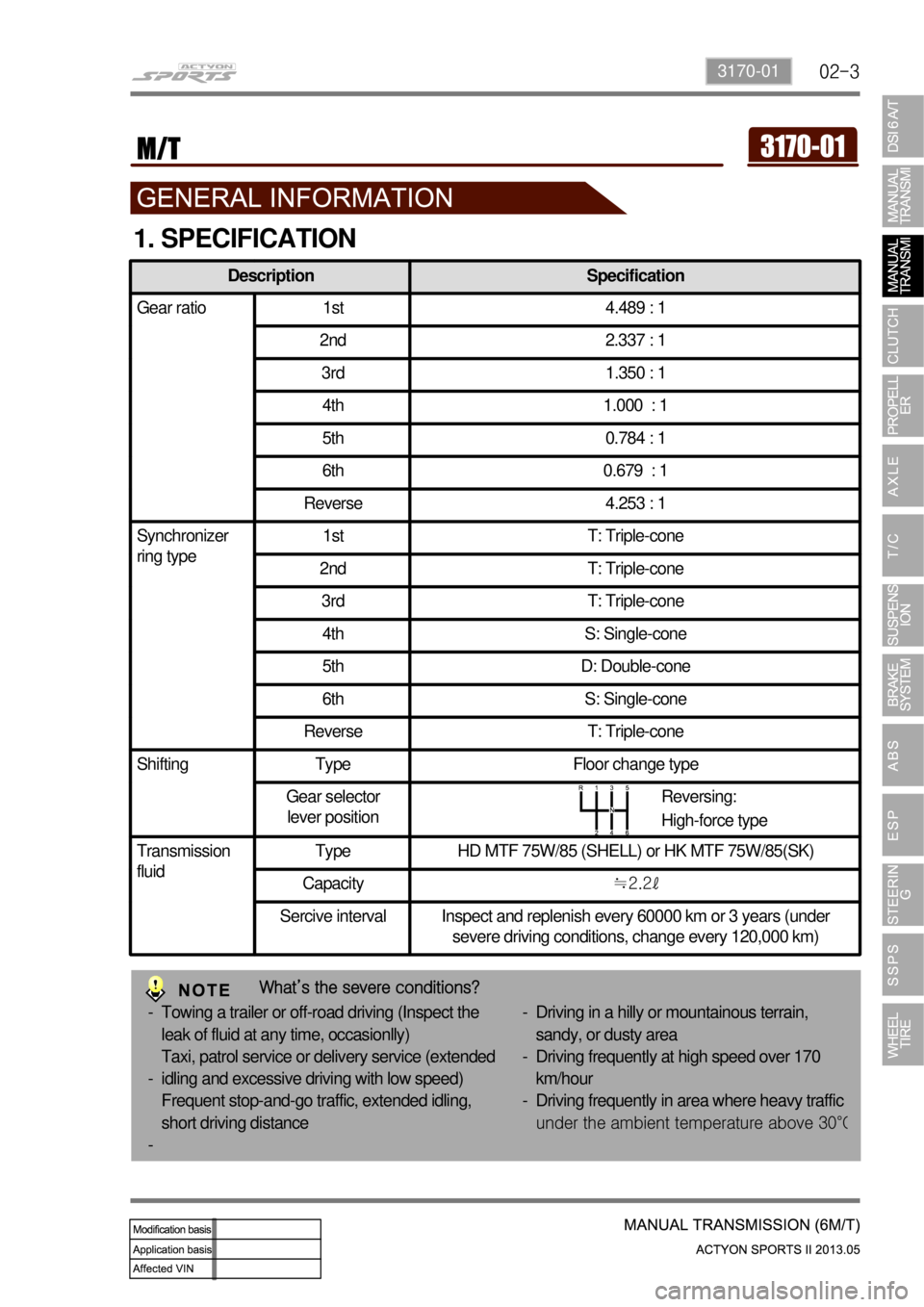
02-33170-01
Description Specification
Gear ratio 1st 4.489 : 1
2nd 2.337 : 1
3rd 1.350 : 1
4th 1.000 : 1
5th 0.784 : 1
6th 0.679 : 1
Reverse 4.253 : 1
Synchronizer
ring type1st T: Triple-cone
2nd T: Triple-cone
3rd T: Triple-cone
4th S: Single-cone
5th D: Double-cone
6th S: Single-cone
Reverse T: Triple-cone
Shifting Type Floor change type
Gear selector
lever position
Transmission
fluidType HD MTF 75W/85 (SHELL) or HK MTF 75W/85(SK)
Capacity≒2.2ℓ
Sercive interval Inspect and replenish every 60000 km or 3 years (under
severe driving conditions, change every 120,000 km)
1. SPECIFICATION
Reversing:
High-force type
What’s the severe conditions?
Towing a trailer or off-road driving (Inspect the
leak of fluid at any time, occasionlly)
Taxi, patrol service or delivery service (extended
idling and excessive driving with low speed)
Frequent stop-and-go traffic, extended idling,
short driving distance -
-
-Driving in a hilly or mountainous terrain,
sandy, or dusty area
Driving frequently at high speed over 170
km/hour
Driving frequently in area where heavy traffic
under the ambient tem
perature above 30°C
-
-
-
Page 520 of 751
04-4
1. OVERVIEW
The hydraulic clutch transmits the force required to operate the clutch pedal to the concentric slave
cylinder fitted to the clutch housing as a hydraulic pressure.
(The hydraulic pressure is transmitted in the following order: Clutch pedal - Clutch master cylinder -
Clutch pipe - Clutch damper - Clutch pipe and hose - Concentric slave cylinder - Pressure plate -
Flywheel.)
If a driver depress the clutch pedal, the hydraulic pressure is generated in the master cylinder. It is
transmitted to the concentric slave cylinder through the pipe, resulting in the cylinder being forced out. At
this time, the clutch disc is forced against the cylinder by pushing the cover. This, in turn, remove the
flywheel from the pressure plate. As a consequence, the power from the engine will be cut off and the
gear change can be carried out.
Page 565 of 751
09-16
Let the engine run for 1 to 2 minutes and
stop it. If the brake pedal stroke is shortened
as pumping the brake pedal, the system is
normal. If not, the system is defective.
Depress the brake pedal several times with
engine off. If the brake goes down when
starting engine with pedal depressed, the
system is normal. If not, the system is
defective.
Depress the brake pedal when the engine is
running. If the pedal height is not changed for
30 seconds after stopping the engine, the
system is normal. If not, the system is
defective. 1.
2.
3.
If the above three checks are OK, the system is
normal. If any condition is not met, check the
valve, vacuum hose and brake booster. Brake Booster ▶
Page 614 of 751
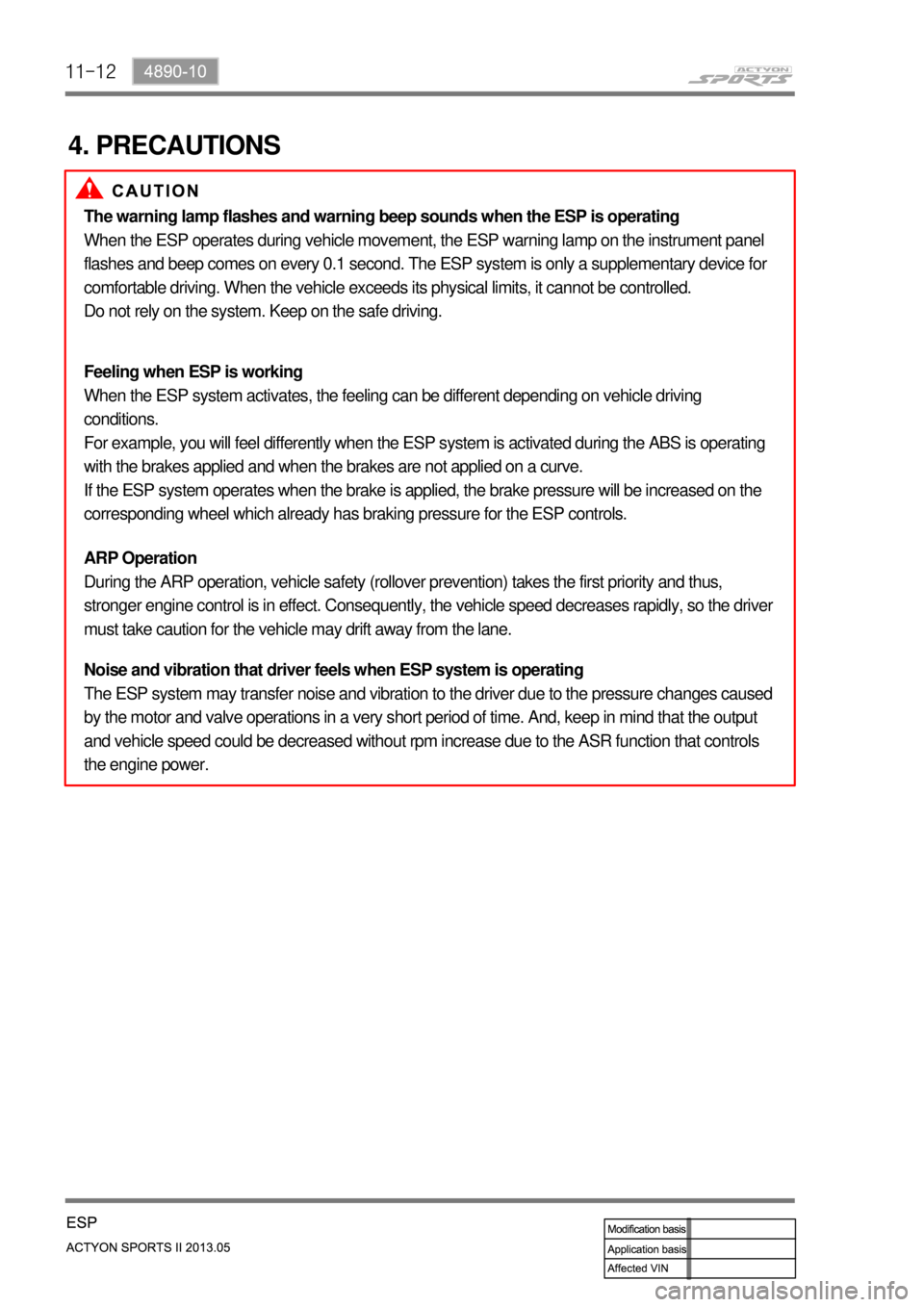
11-12
4. PRECAUTIONS
The warning lamp flashes and warning beep sounds when the ESP is operating
When the ESP operates during vehicle movement, the ESP warning lamp on the instrument panel
flashes and beep comes on every 0.1 second. The ESP system is only a supplementary device for
comfortable driving. When the vehicle exceeds its physical limits, it cannot be controlled.
Do not rely on the system. Keep on the safe driving.
Feeling when ESP is working
When the ESP system activates, the feeling can be different depending on vehicle driving
conditions.
For example, you will feel differently when the ESP system is activated during the ABS is operating
with the brakes applied and when the brakes are not applied on a curve.
If the ESP system operates when the brake is applied, the brake pressure will be increased on the
corresponding wheel which already has braking pressure for the ESP controls.
ARP Operation
During the ARP operation, vehicle safety (rollover prevention) takes the first priority and thus,
stronger engine control is in effect. Consequently, the vehicle speed decreases rapidly, so the driver
must take caution for the vehicle may drift away from the lane.
Noise and vibration that driver feels when ESP system is operating
The ESP system may transfer noise and vibration to the driver due to the pressure changes caused
by the motor and valve operations in a very short period of time. And, keep in mind that the output
and vehicle speed could be decreased without rpm increase due to the ASR function that controls
the engine power.
Page 624 of 751
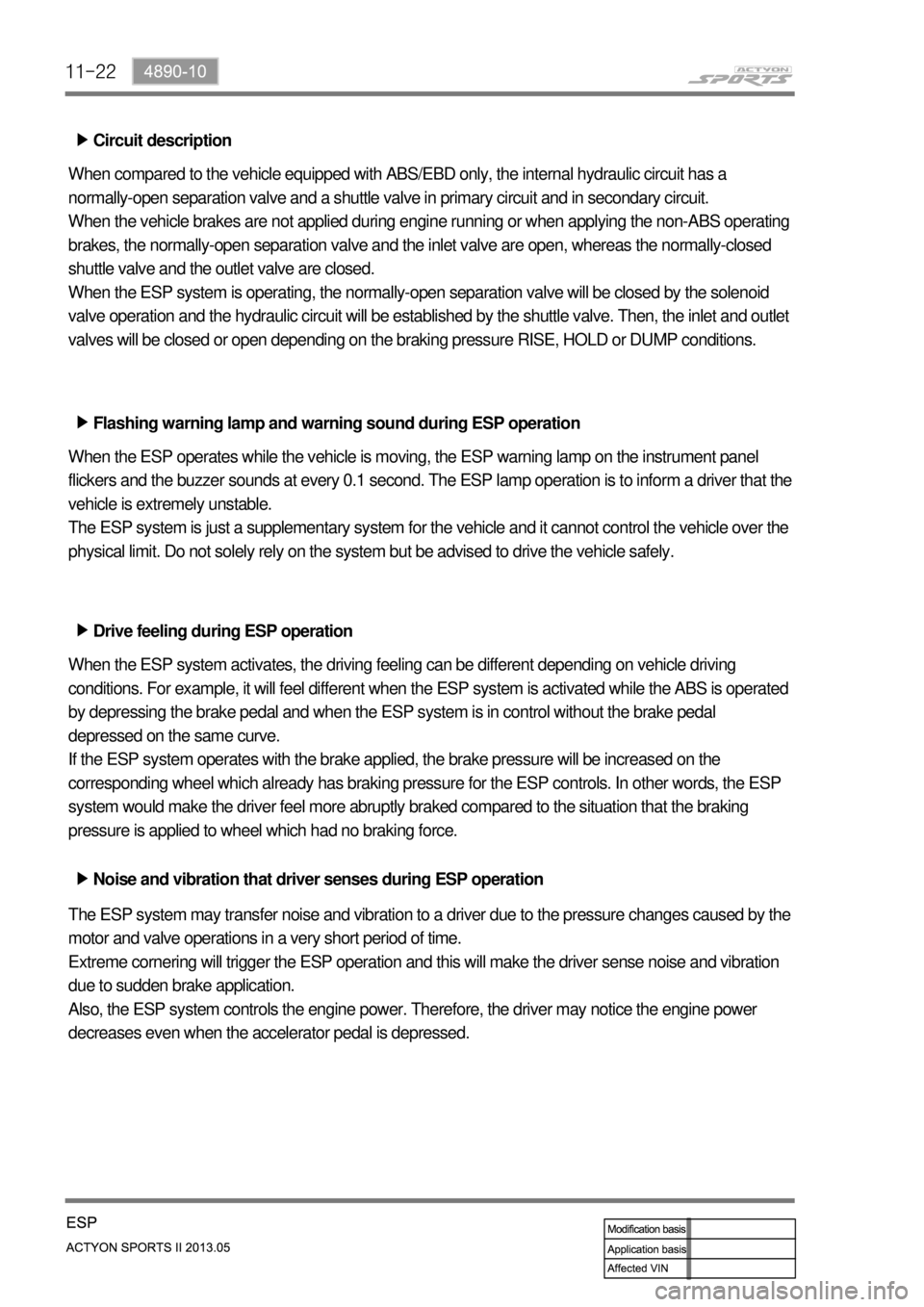
11-22
Circuit description ▶
When compared to the vehicle equipped with ABS/EBD only, the internal hydraulic circuit has a
normally-open separation valve and a shuttle valve in primary circuit and in secondary circuit.
When the vehicle brakes are not applied during engine running or when applying the non-ABS operating
brakes, the normally-open separation valve and the inlet valve are open, whereas the normally-closed
shuttle valve and the outlet valve are closed.
When the ESP system is operating, the normally-open separation valve will be closed by the solenoid
valve operation and the hydraulic circuit will be established by the shuttle valve. Then, the inlet and outlet
valves will be closed or open depending on the braking pressure RISE, HOLD or DUMP conditions.
Flashing warning lamp and warning sound during ESP operation ▶
When the ESP operates while the vehicle is moving, the ESP warning lamp on the instrument panel
flickers and the buzzer sounds at every 0.1 second. The ESP lamp operation is to inform a driver that the
vehicle is extremely unstable.
The ESP system is just a supplementary system for the vehicle and it cannot control the vehicle over the
physical limit. Do not solely rely on the system but be advised to drive the vehicle safely.
Drive feeling during ESP operation ▶
When the ESP system activates, the driving feeling can be different depending on vehicle driving
conditions. For example, it will feel different when the ESP system is activated while the ABS is operated
by depressing the brake pedal and when the ESP system is in control without the brake pedal
depressed on the same curve.
If the ESP system operates with the brake applied, the brake pressure will be increased on the
corresponding wheel which already has braking pressure for the ESP controls. In other words, the ESP
system would make the driver feel more abruptly braked compared to the situation that the braking
pressure is applied to wheel which had no braking force.
Noise and vibration that driver senses during ESP operation ▶
The ESP system may transfer noise and vibration to a driver due to the pressure changes caused by the
motor and valve operations in a very short period of time.
Extreme cornering will trigger the ESP operation and this will make the driver sense noise and vibration
due to sudden brake application.
Also, the ESP system controls the engine power. Therefore, the driver may notice the engine power
decreases even when the accelerator pedal is depressed.
Page 646 of 751
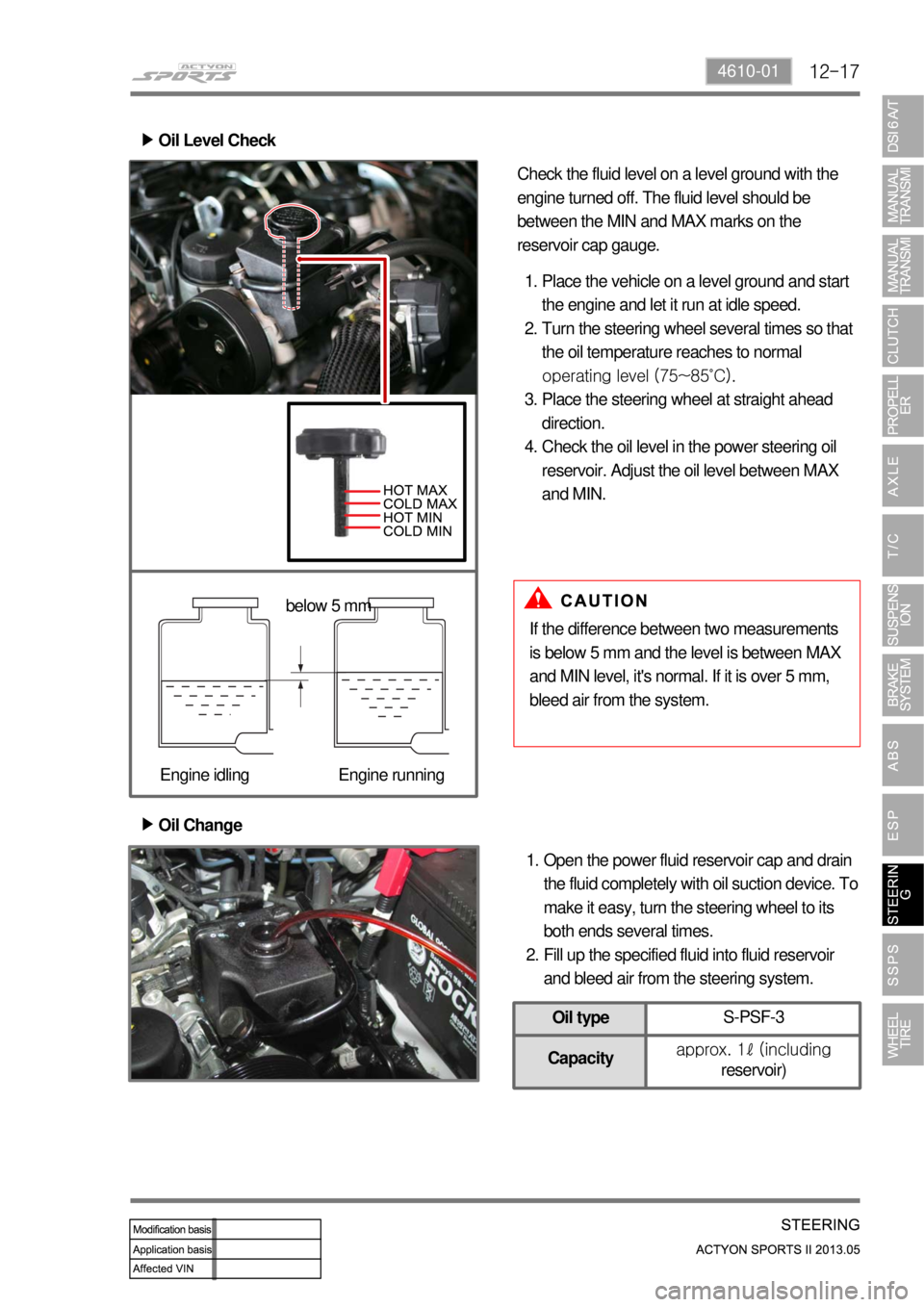
12-174610-01
Oil Change ▶
Open the power fluid reservoir cap and drain
the fluid completely with oil suction device. To
make it easy, turn the steering wheel to its
both ends several times.
Fill up the specified fluid into fluid reservoir
and bleed air from the steering system. 1.
2. Oil Level Check ▶
Place the vehicle on a level ground and start
the engine and let it run at idle speed.
Turn the steering wheel several times so that
the oil temperature reaches to normal
operating level (75~85˚C).
Place the steering wheel at straight ahead
direction.
Check the oil level in the power steering oil
reservoir. Adjust the oil level between MAX
and MIN. 1.
2.
3.
4.
If the difference between two measurements
is below 5 mm and the level is between MAX
and MIN level, it's normal. If it is over 5 mm,
bleed air from the system. Check the fluid level on a level ground with the
engine turned off. The fluid level should be
between the MIN and MAX marks on the
reservoir cap gauge.
below 5 mm
Engine idling Engine running
Oil typeS-PSF-3
Capacityapprox. 1ℓ (including
reservoir)
Page 672 of 751
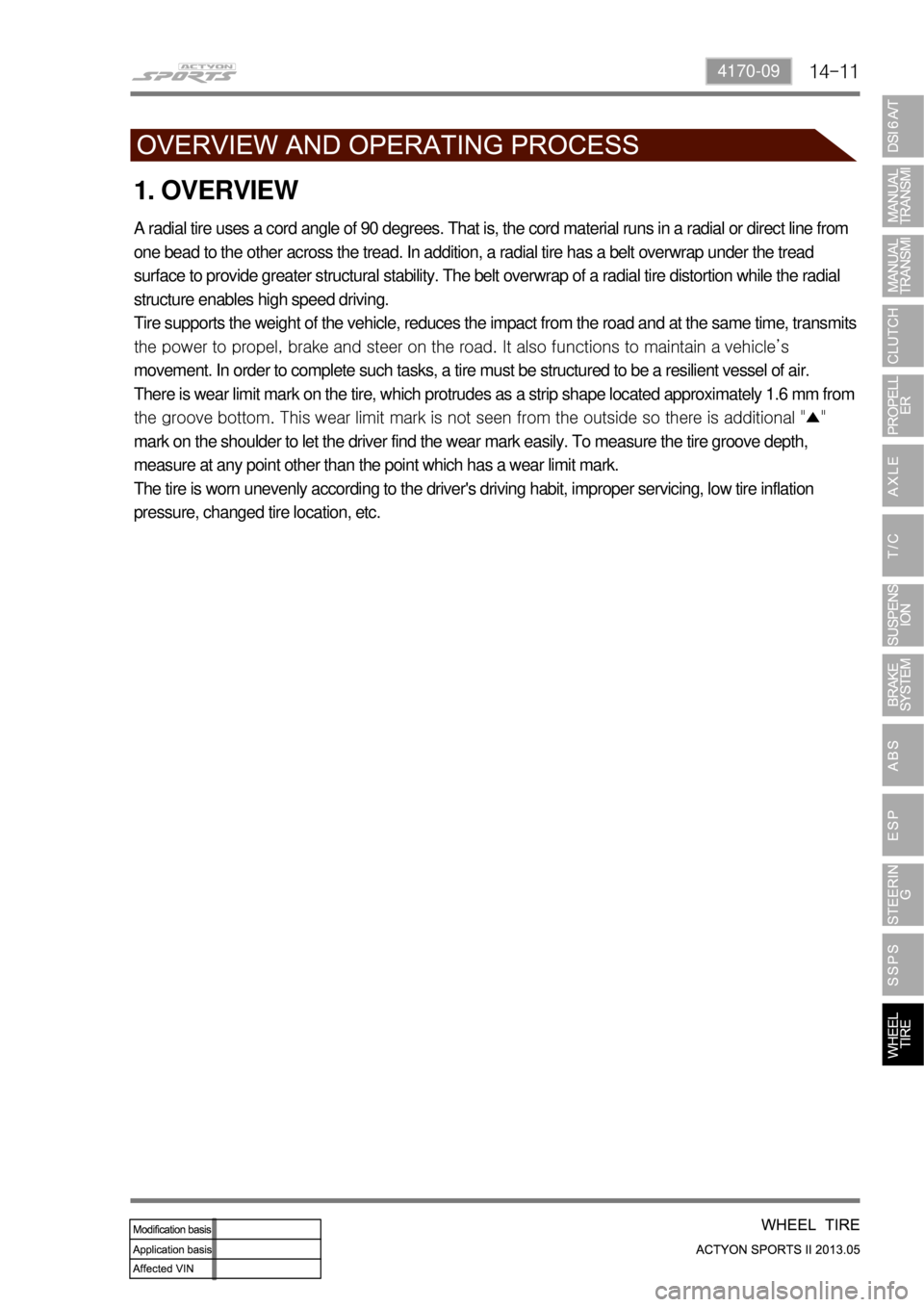
14-114170-09
1. OVERVIEW
A radial tire uses a cord angle of 90 degrees. That is, the cord material runs in a radial or direct line from
one bead to the other across the tread. In addition, a radial tire has a belt overwrap under the tread
surface to provide greater structural stability. The belt overwrap of a radial tire distortion while the radial
structure enables high speed driving.
Tire supports the weight of the vehicle, reduces the impact from the road and at the same time, transmits
<009b008f008c004700970096009e008c00990047009b009600470097009900960097008c0093005300470089009900880092008c004700880095008b0047009a009b008c008c00990047009600950047009b008f008c0047009900960088008b0055004700
70009b004700880093009a00960047008d009c0095008a009b>ions to maintain a vehicle’s
movement. In order to complete such tasks, a tire must be structured to be a resilient vessel of air.
There is wear limit mark on the tire, which protrudes as a strip shape located approximately 1.6 mm from
the groove bottom. This wear limit mark is not seen from the outside so there is additional "▲"
mark on the shoulder to let the driver find the wear mark easily. To measure the tire groove depth,
measure at any point other than the point which has a wear limit mark.
The tire is worn unevenly according to the driver's driving habit, improper servicing, low tire inflation
pressure, changed tire location, etc.