Page 185 of 1336
2. MAJOR COMPONENTS
Front View
Rear View
E-EGR valve
Fuel temperature sensor
Fuel HP pump assemblyE-VGT actuator
Coolant temperature sensor
IMV valve
Magnetic triggering
Crankshaft position sensor
Vacuum pump
Oil filter assembly
Camshaft position sensor
Power steering pump pulley
Water pump pulley
Alternator pulley
Idler pulley No. 1
A/C compressor pulley
Auto tensioner
Idler pulley No. 2
Isolation damper
Oil pressure switch
Page 246 of 1336
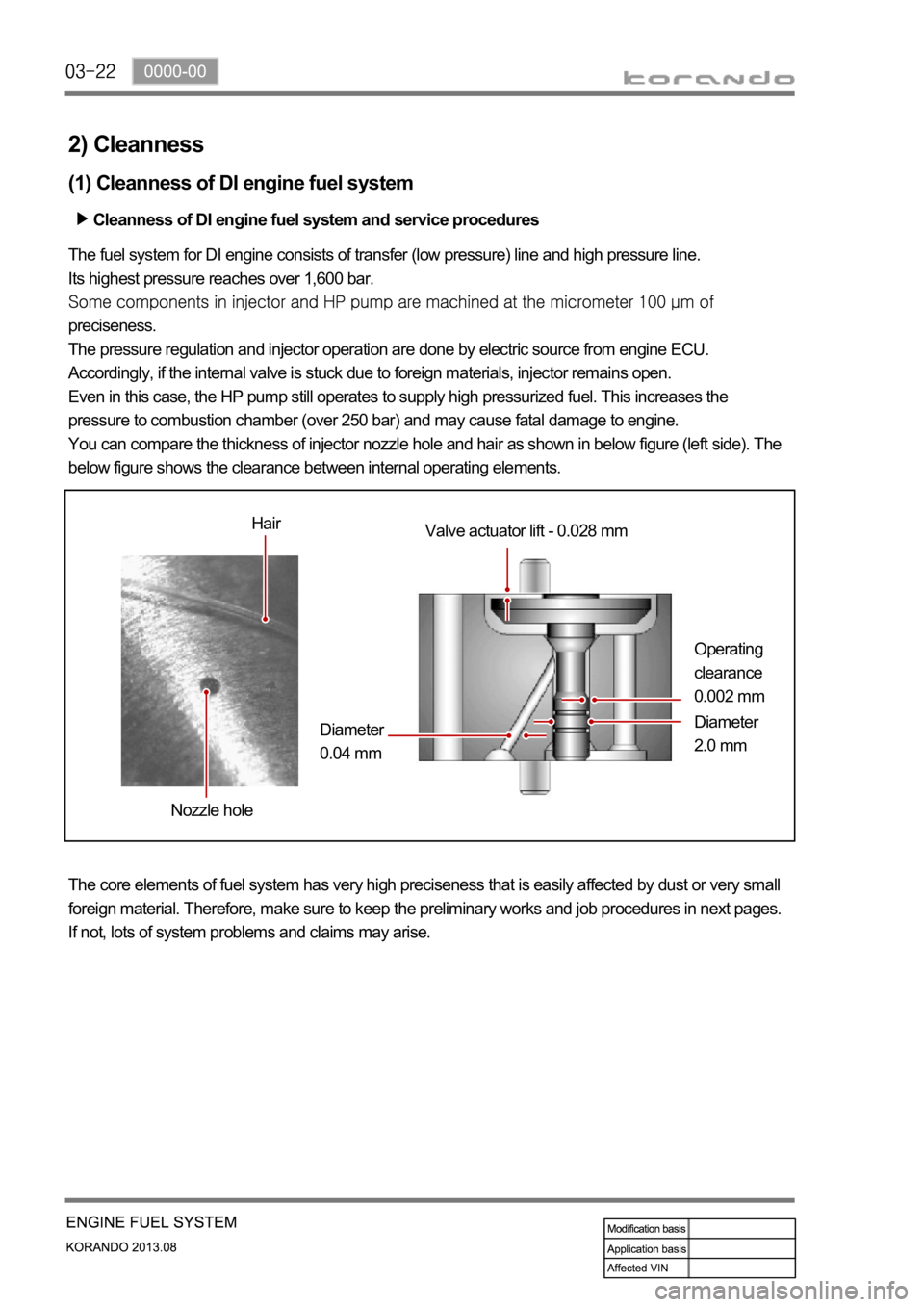
2) Cleanness
(1) Cleanness of DI engine fuel system
Cleanness of DI engine fuel system and service procedures
The fuel system for DI engine consists of transfer (low pressure) line and high pressure line.
Its highest pressure reaches over 1,600 bar.
preciseness.
The pressure regulation and injector operation are done by electric source from engine ECU.
Accordingly, if the internal valve is stuck due to foreign materials, injector remains open.
Even in this case, the HP pump still operates to supply high pressurized fuel. This increases the
pressure to combustion chamber (over 250 bar) and may cause fatal damage to engine.
You can compare the thickness of injector nozzle hole and hair as shown in below figure (left side). The
below figure shows the clearance between internal operating elements.
The core elements of fuel system has very high preciseness that is easily affected by dust or very small
foreign material. Therefore, make sure to keep the preliminary works and job procedures in next pages.
If not, lots of system problems and claims may arise.
Hair
Nozzle holeValve actuator lift - 0.028 mm
Diameter
0.04 mm
Operating
clearance
0.002 mm
Diameter
2.0 mm
Page 250 of 1336
Fuel rail assembly
Relieves the pulsation.
Measures the fuel pressure.
Distributes the fuel to injectors.Camshaft position sensor
Determines the injection order.
Injector (C3I)
Pre-injection, main injection, after-injection by
signals from ECU
Fuel tank
Fuel metering by dual sender. Supply the fuel in
main fuel tank and sub fuel tank through fuel
inlet tube
2. SYSTEM LAYOUT AND OPERATION
1) Layout
Fuel supply line
Fuel return line
For sensor and actuator control logic,
refer to Chapter "ENGINE CONTROL".
Page 265 of 1336
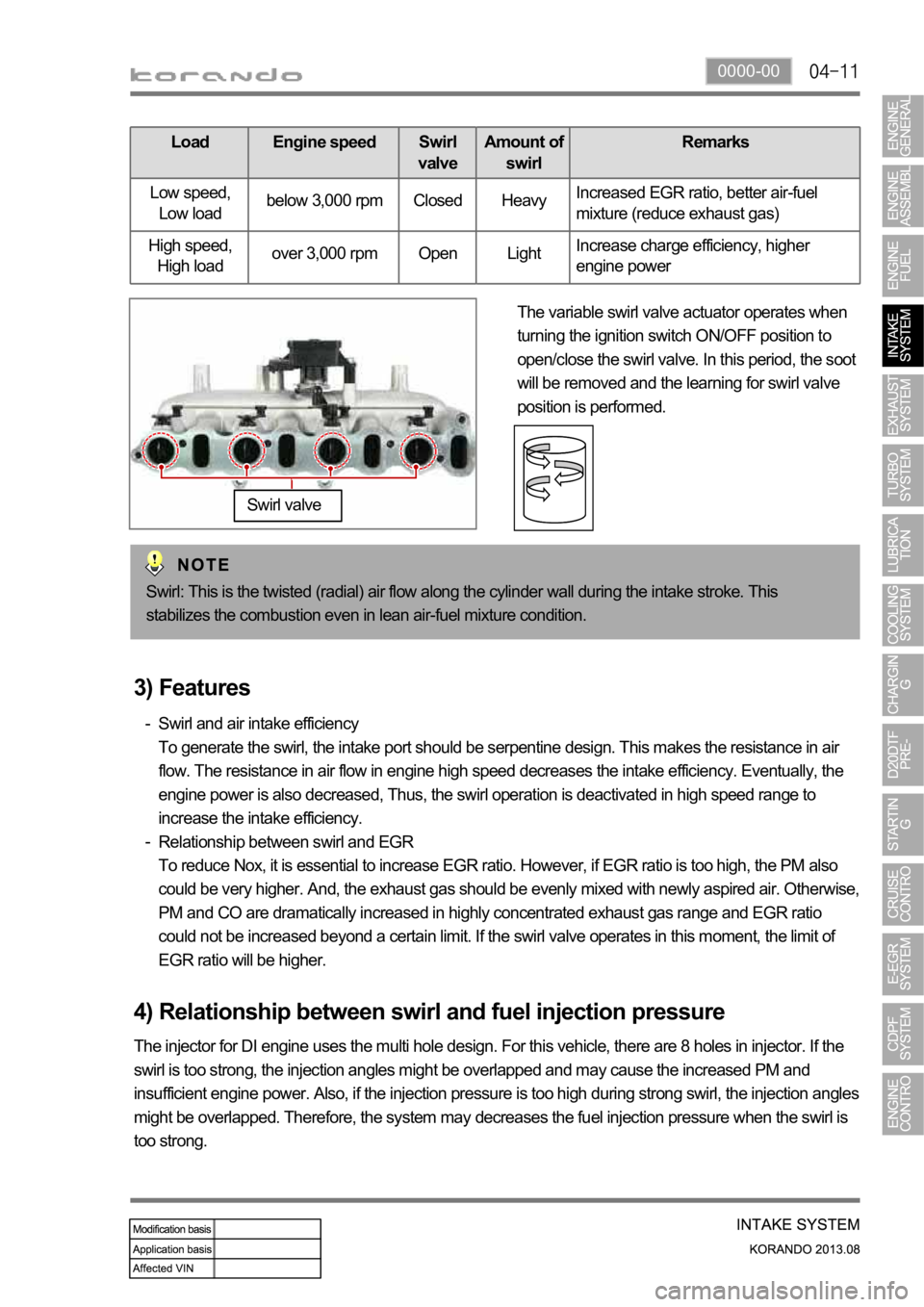
0000-00
Load Engine speed Swirl
valveAmount of
swirlRemarks
Low speed,
Low loadbelow 3,000 rpm Closed HeavyIncreased EGR ratio, better air-fuel
mixture (reduce exhaust gas)
High speed,
High loadover 3,000 rpm Open LightIncrease charge efficiency, higher
engine power
The variable swirl valve actuator operates when
turning the ignition switch ON/OFF position to
open/close the swirl valve. In this period, the soot
will be removed and the learning for swirl valve
position is performed.
Swirl valve
Swirl: This is the twisted (radial) air flow along the cylinder wall during the intake stroke. This
stabilizes the combustion even in lean air-fuel mixture condition.
3) Features
Swirl and air intake efficiency
To generate the swirl, the intake port should be serpentine design. This makes the resistance in air
flow. The resistance in air flow in engine high speed decreases the intake efficiency. Eventually, the
engine power is also decreased, Thus, the swirl operation is deactivated in high speed range to
increase the intake efficiency.
Relationship between swirl and EGR
To reduce Nox, it is essential to increase EGR ratio. However, if EGR ratio is too high, the PM also
could be very higher. And, the exhaust gas should be evenly mixed with newly aspired air. Otherwise,
PM and CO are dramatically increased in highly concentrated exhaust gas range and EGR ratio
could not be increased beyond a certain limit. If the swirl valve operates in this moment, the limit of
EGR ratio will be higher. -
-
4) Relationship between swirl and fuel injection pressure
The injector for DI engine uses the multi hole design. For this vehicle, there are 8 holes in injector. If the
swirl is too strong, the injection angles might be overlapped and may cause the increased PM and
insufficient engine power. Also, if the injection pressure is too high during strong swirl, the injection angles
might be overlapped. Therefore, the system may decreases the fuel injection pressure when the swirl is
too strong.
Page 271 of 1336
0000-00
1. SPECIFICATION
Component Item Specification
TurbochargerMax. expansion coefficient 5.0
Max. turbine speed 215,000 rpm
Max. temperature of turbine housing
Weight 7.2 kg
E-Actuator Operation duty cycle 300 Hz
Page 279 of 1336
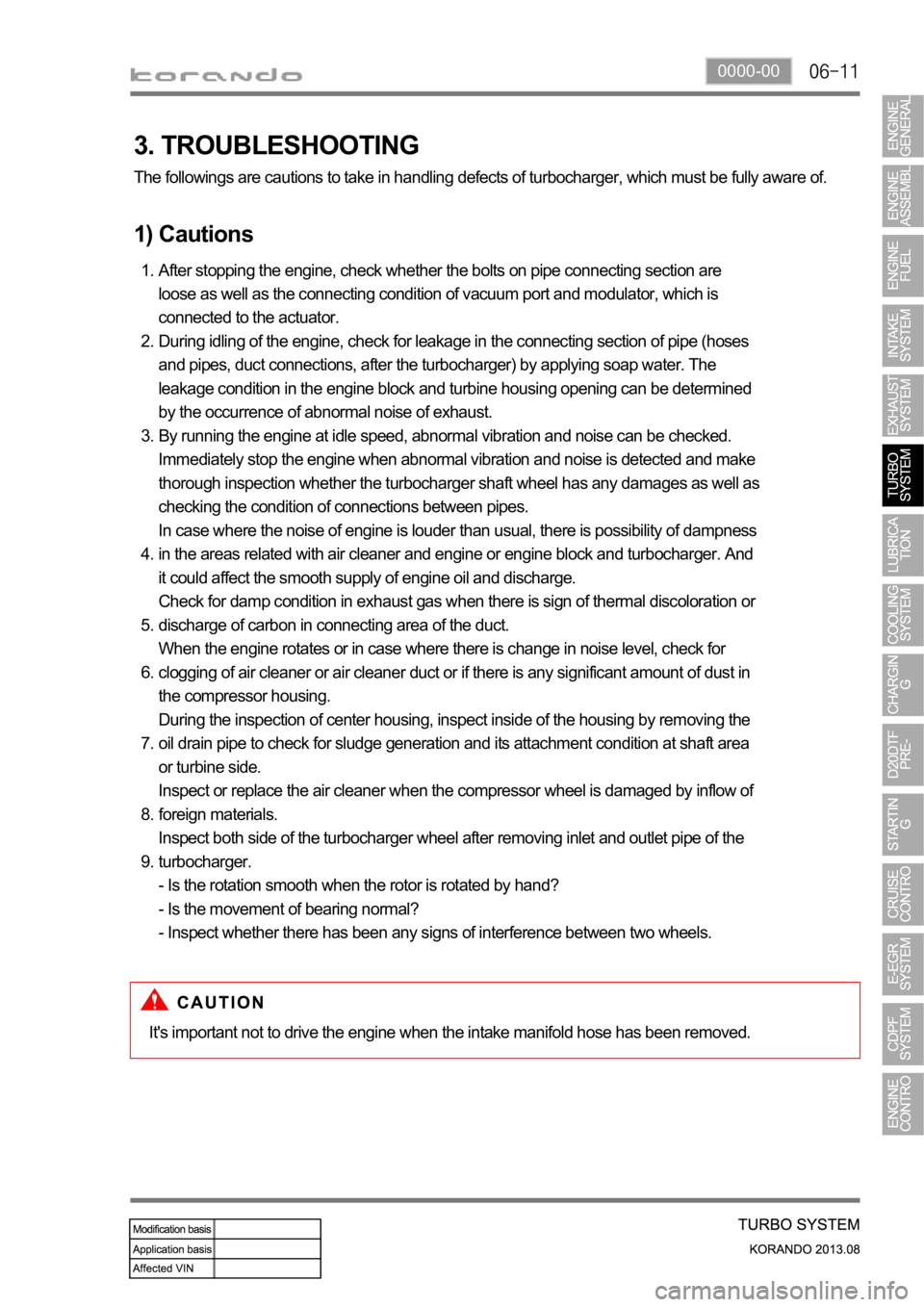
0000-00
3. TROUBLESHOOTING
The followings are cautions to take in handling defects of turbocharger, which must be fully aware of.
1) Cautions
After stopping the engine, check whether the bolts on pipe connecting section are
loose as well as the connecting condition of vacuum port and modulator, which is
connected to the actuator.
During idling of the engine, check for leakage in the connecting section of pipe (hoses
and pipes, duct connections, after the turbocharger) by applying soap water. The
leakage condition in the engine block and turbine housing opening can be determined
by the occurrence of abnormal noise of exhaust.
By running the engine at idle speed, abnormal vibration and noise can be checked.
Immediately stop the engine when abnormal vibration and noise is detected and make
thorough inspection whether the turbocharger shaft wheel has any damages as well as
checking the condition of connections between pipes.
In case where the noise of engine is louder than usual, there is possibility of dampness
in the areas related with air cleaner and engine or engine block and turbocharger. And
it could affect the smooth supply of engine oil and discharge.
Check for damp condition in exhaust gas when there is sign of thermal discoloration or
discharge of carbon in connecting area of the duct.
When the engine rotates or in case where there is change in noise level, check for
clogging of air cleaner or air cleaner duct or if there is any significant amount of dust in
the compressor housing.
During the inspection of center housing, inspect inside of the housing by removing the
oil drain pipe to check for sludge generation and its attachment condition at shaft area
or turbine side.
Inspect or replace the air cleaner when the compressor wheel is damaged by inflow of
foreign materials.
Inspect both side of the turbocharger wheel after removing inlet and outlet pipe of the
turbocharger.
- Is the rotation smooth when the rotor is rotated by hand?
- Is the movement of bearing normal?
- Inspect whether there has been any signs of interference between two wheels. 1.
2.
3.
4.
5.
6.
7.
8.
9.
It's important not to drive the engine when the intake manifold hose has been removed.
Page 285 of 1336
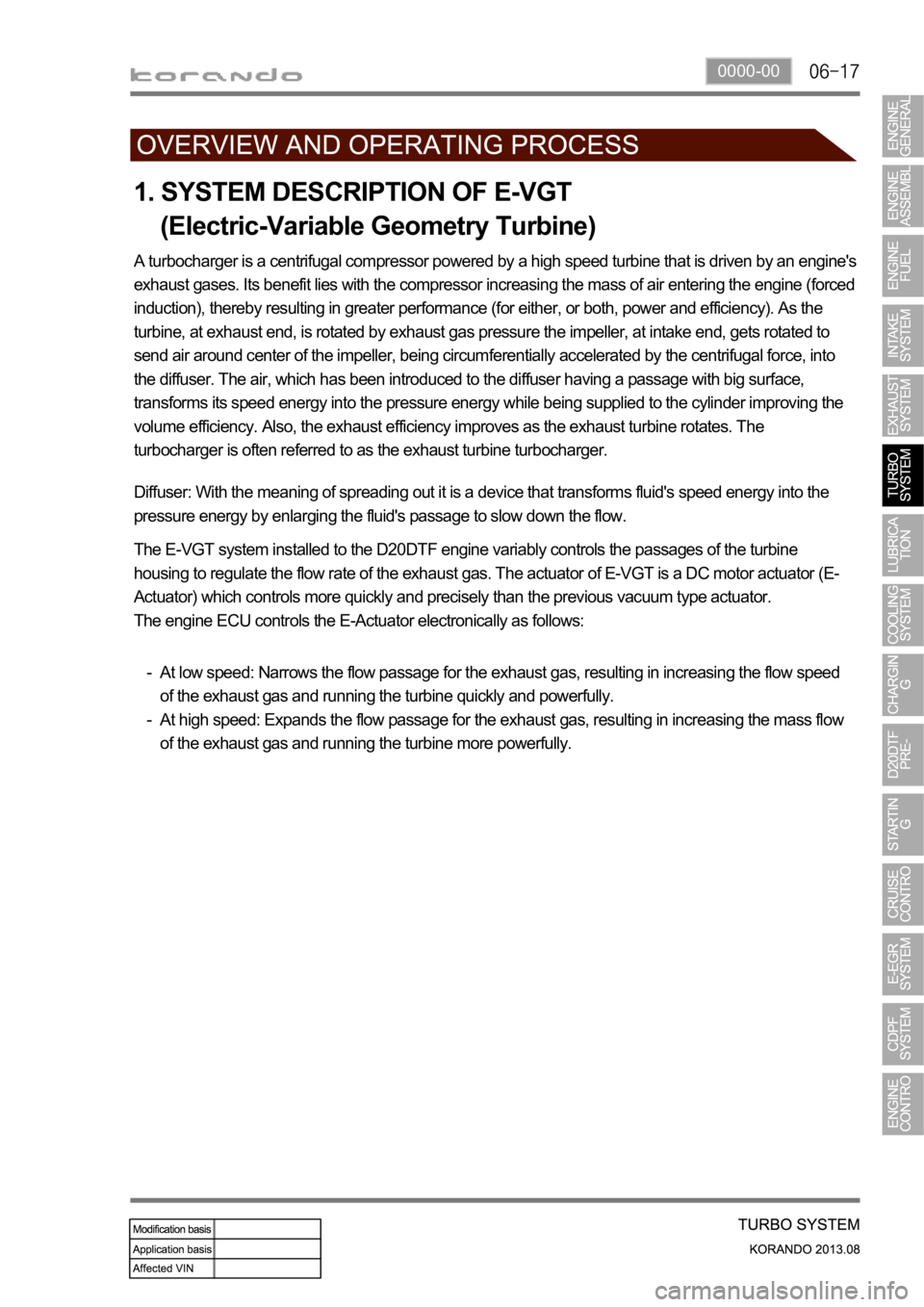
0000-00
1. SYSTEM DESCRIPTION OF E-VGT
(Electric-Variable Geometry Turbine)
A turbocharger is a centrifugal compressor powered by a high speed turbine that is driven by an engine's
exhaust gases. Its benefit lies with the compressor increasing the mass of air entering the engine (forced
induction), thereby resulting in greater performance (for either, or both, power and efficiency). As the
turbine, at exhaust end, is rotated by exhaust gas pressure the impeller, at intake end, gets rotated to
send air around center of the impeller, being circumferentially accelerated by the centrifugal force, into
the diffuser. The air, which has been introduced to the diffuser having a passage with big surface,
transforms its speed energy into the pressure energy while being supplied to the cylinder improving the
volume efficiency. Also, the exhaust efficiency improves as the exhaust turbine rotates. The
turbocharger is often referred to as the exhaust turbine turbocharger.
The E-VGT system installed to the D20DTF engine variably controls the passages of the turbine
housing to regulate the flow rate of the exhaust gas. The actuator of E-VGT is a DC motor actuator (E-
Actuator) which controls more quickly and precisely than the previous vacuum type actuator.
The engine ECU controls the E-Actuator electronically as follows:
Diffuser: With the meaning of spreading out it is a device that transforms fluid's speed energy into the
pressure energy by enlarging the fluid's passage to slow down the flow.
At low speed: Narrows the flow passage for the exhaust gas, resulting in increasing the flow speed
of the exhaust gas and running the turbine quickly and powerfully.
At high speed: Expands the flow passage for the exhaust gas, resulting in increasing the mass flow
of the exhaust gas and running the turbine more powerfully. -
-
Page 286 of 1336
Maximizes the intake air charging efficiency (Approx. 15%) -Optimizes the exhaust gas flow rate by controlling the vanes inside the turbine housing with the E-
Actuator. 1.
(2) E-Actuator (Electric-Actuator, Rotary type)
Target temperature and airflow control -Enhanced emission control: By temperature control with CDPF system 1.
(1) Performance (for EURO V)
Has a faster response time than the conventional vacuum actuator 2.
Improved low speed torque, high speed power and fuel economy.
Improved acceleration performance with rapid response time of vane -
-
1) Features
Features
BenefitsFolding and unfolding of the vane
is controlled electrically
Easy to get low speed air volume
Rapid response time
Electric control -
-
-
-
Improved low speed torque
Improved low speed torque and
power
Reduced exhaust gas
Improved fuel consumption
Improved acceleration
performance -
-
-
-