Page 312 of 715
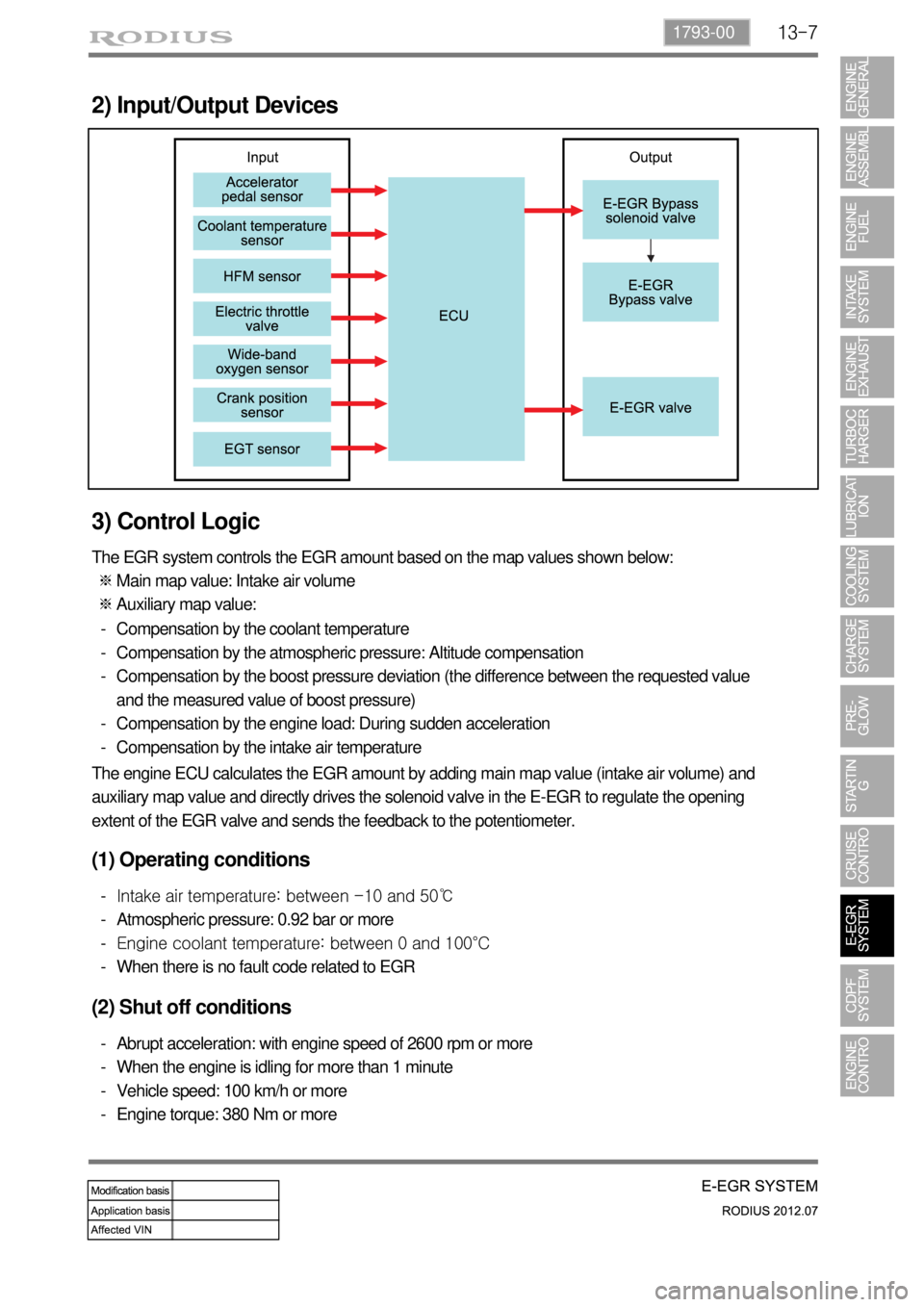
13-71793-00
2) Input/Output Devices
3) Control Logic
The EGR system controls the EGR amount based on the map values shown below:
Main map value: Intake air volume
Auxiliary map value: ※
※
Compensation by the coolant temperature
Compensation by the atmospheric pressure: Altitude compensation
Compensation by the boost pressure deviation (the difference between the requested value
and the measured value of boost pressure)
Compensation by the engine load: During sudden acceleration
Compensation by the intake air temperature -
-
-
-
-
The engine ECU calculates the EGR amount by adding main map value (intake air volume) and
auxiliary map value and directly drives the solenoid valve in the E-EGR to regulate the opening
extent of the EGR valve and sends the feedback to the potentiometer.
(1) Operating conditions
Intake air temperature: between -10 and 50℃
Atmospheric pressure: 0.92 bar or more
Engine coolant temperature: between 0 and 100°C
When there is no fault code related to EGR -
-
-
-
(2) Shut off conditions
Abrupt acceleration: with engine speed of 2600 rpm or more
When the engine is idling for more than 1 minute
Vehicle speed: 100 km/h or more
Engine torque: 380 Nm or more -
-
-
-
Page 328 of 715
15-30000-00
1. ENGINE DATA LIST
Data Unit Value
Coolant temperature℃ 130℃~-40℃
Intake air temperature℃ -40 to 130℃ (varies by ambient air
temperature or engine mode)
Idle speed rpm 700 ± 50 (P/N), 600 ± (D)
Engine load % 18~25%
Mass air flow kg/h 16 to 25 kg/h
Throttle position angle°TA 0° (Full Open) to 78° (Close)
Engine torque Nm varies by engine conditions
Injection time ms 3 to 5ms
Battery voltage V 13.5 V to 14.1 V
Accelerator pedal position 1 V 0.4. to 4.8V
Accelerator pedal position 2 V 0.2 to 2.4 V
Throttle position 1 V 0.3 to 4.6 V
Throttle position 2 V 0.3 to 4.6 V
Oxygen sensor V 0 to 5 V
A/C compressor switch
1=ON / 0=OFF -
Full load 1=ON / 0=OFF -
Gear selection (A/T) 1=ON / 0=OFF -
Knocking control 1=ON / 0=OFF -
Brake switch 1=ON / 0=OFF -
Cruise control 1=ON / 0=OFF -
Page 332 of 715
15-70000-00
Fuel Temperature
SensorCoolant Temperature Sensor
Knock Sensor (2)T-MAP SensorD20DTR ECU
Page 334 of 715
15-90000-00
Fuel rail pressure Water sensor
(2) Components for ECU Input
CAN
- ABS & ESP
- GCU
- Indicator/
Warning Lamp,
Meter Cluster
- TCUSwirl valve
position
sensor
Differential
pressure sensorE-EGR valve
position
sensorCamshaft position
sensorCoolant
temperature
sensor
EGT sensorHFM sensorOxygen sensorT-MAP sensor
Crankshaft
position
sensorAccelerator pedal
sensorThrottle
position
sensorKnock sensor
- Auto cruise switch
- Refrigerant pressure
sensor
- Blower switch signal
- Brake pedal signal
Page 338 of 715
15-130000-00
b. Pilot Injection
Injection before main injection. Consists of 1st and 2nd pilot injection, and Pre-injection
Inject a small amount of fuel before main injection to make the combustion smooth. Also, called as
preliminary injection or ignition injection. This helps to reduce Nox, engine noise and vibration, and to
stabilize the idling.
The injected fuel volume is changed and stopped according to the coolant temperature and intake air
volume.
Pilot injection is much earlier than main injection due to higher engine rpm
Too small injection volume (insufficient injection pressure, insufficient fuel injection volume in main
injection, engine braking)
System failure (fuel system, engine control system) -
-
-
Pilot injection
Main injection
Combustion pressure with pilot injection
Combustion pressure without pilot injection 1.
2.
1a.
2b. Stop conditions
Combustion pressure characteristic curve for pilot injection ▶
Page 339 of 715
15-14
c. Main Injection
The power of the vehicle is determined by the main fuel injection volume.
Main injection calculates the fuel volume based on pilot injection. The calculation uses the value for
accelerator pedal position, engine rpm, coolant temperature, intake air temperature, boost pressure,
boost temperature and atmospheric pressure etc.
d. Post Injection
Injection after main injection. Consists of After injection, Post 1, Post 2 injection.
Post injection reduces PM and smoke from exhaust gas. No actual output is generated during these
injections, instead, fuel is injected to the unburned gas after main injection to enable fuel activation.
Page 340 of 715
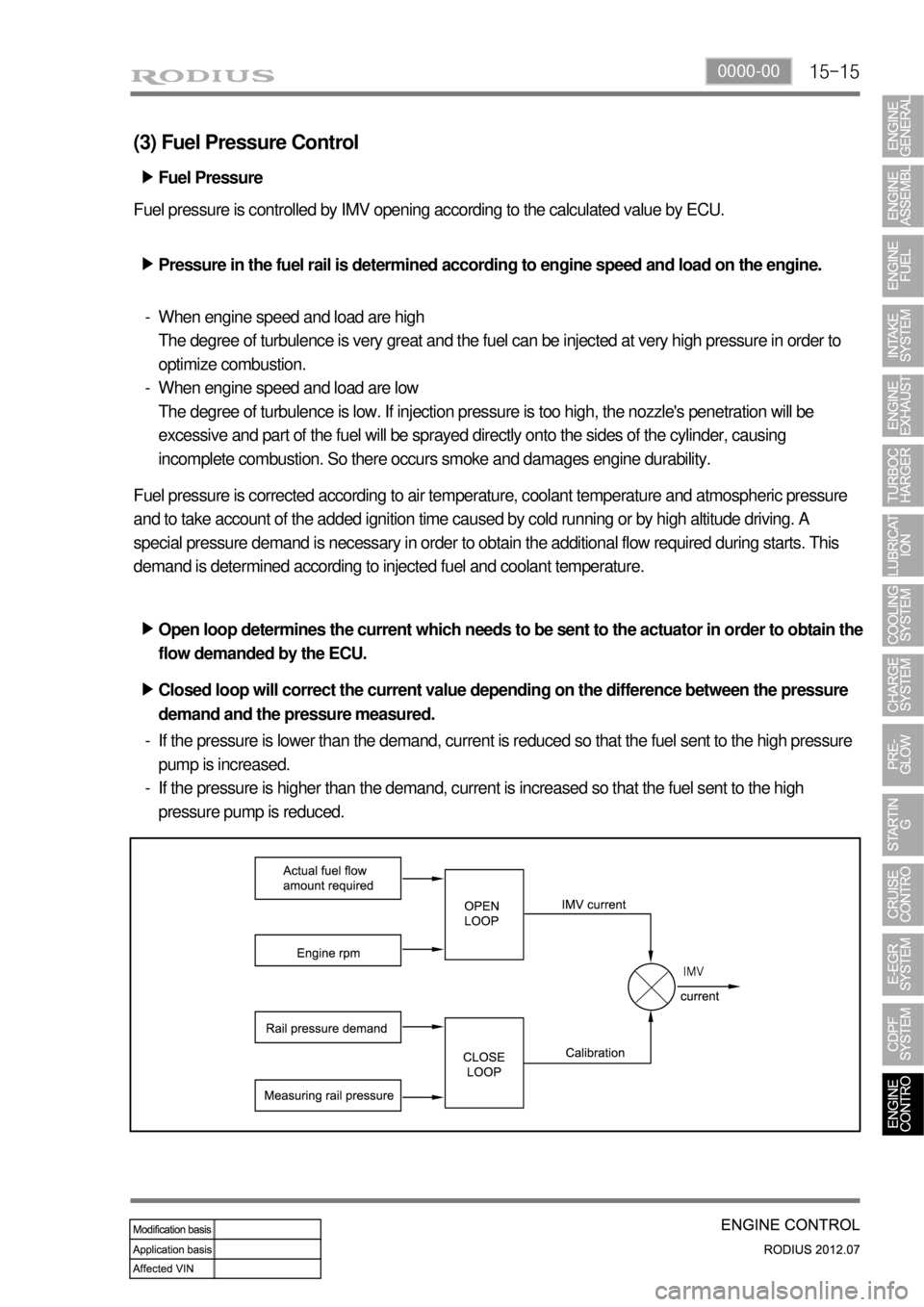
15-150000-00
(3) Fuel Pressure Control
Fuel pressure is controlled by IMV opening according to the calculated value by ECU.
Pressure in the fuel rail is determined according to engine speed and load on the engine. ▶
When engine speed and load are high
The degree of turbulence is very great and the fuel can be injected at very high pressure in order to
optimize combustion.
When engine speed and load are low
The degree of turbulence is low. If injection pressure is too high, the nozzle's penetration will be
excessive and part of the fuel will be sprayed directly onto the sides of the cylinder, causing
incomplete combustion. So there occurs smoke and damages engine durability. -
-
Fuel pressure is corrected according to air temperature, coolant temperature and atmospheric pressure
and to take account of the added ignition time caused by cold running or by high altitude driving. A
special pressure demand is necessary in order to obtain the additional flow required during starts. This
demand is determined according to injected fuel and coolant temperature.
Open loop determines the current which needs to be sent to the actuator in order to obtain the
flow demanded by the ECU. ▶
Closed loop will correct the current value depending on the difference between the pressure
demand and the pressure measured. ▶
If the pressure is lower than the demand, current is reduced so that the fuel sent to the high pressure
pump is increased.
If the pressure is higher than the demand, current is increased so that the fuel sent to the high
pressure pump is reduced. -
-Fuel Pressure ▶
Page 341 of 715
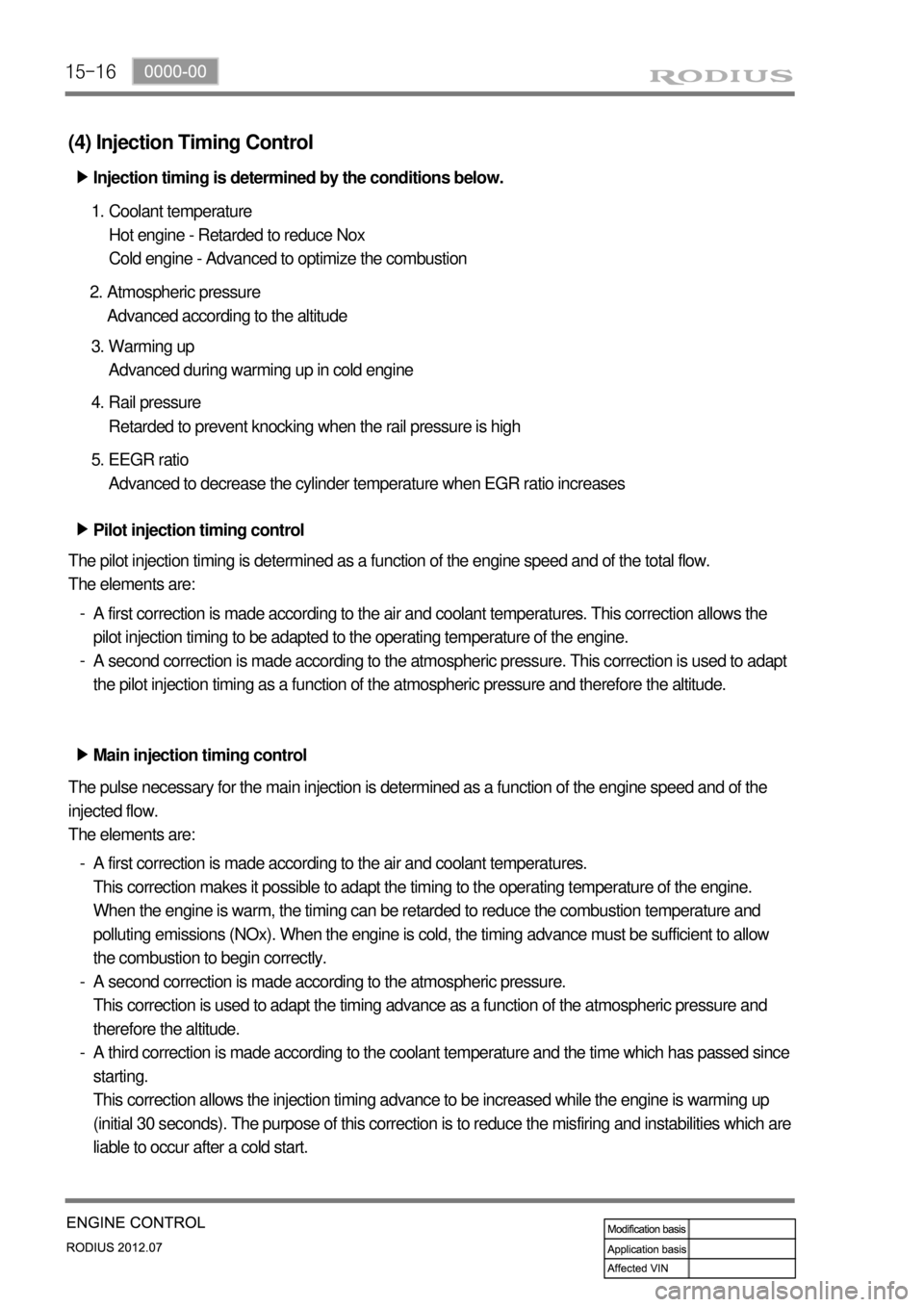
15-16
Pilot injection timing control ▶
The pilot injection timing is determined as a function of the engine speed and of the total flow.
The elements are:
A first correction is made according to the air and coolant temperatures. This correction allows the
pilot injection timing to be adapted to the operating temperature of the engine.
A second correction is made according to the atmospheric pressure. This correction is used to adapt
the pilot injection timing as a function of the atmospheric pressure and therefore the altitude. -
-
(4) Injection Timing Control
Injection timing is determined by the conditions below. ▶
Coolant temperature
Hot engine - Retarded to reduce Nox
Cold engine - Advanced to optimize the combustion 1.
Atmospheric pressure
Advanced according to the altitude 2.
Warming up
Advanced during warming up in cold engine 3.
Rail pressure
Retarded to prevent knocking when the rail pressure is high 4.
EEGR ratio
Advanced to decrease the cylinder temperature when EGR ratio increases 5.
Main injection timing control ▶
The pulse necessary for the main injection is determined as a function of the engine speed and of the
injected flow.
The elements are:
A first correction is made according to the air and coolant temperatures.
This correction makes it possible to adapt the timing to the operating temperature of the engine.
When the engine is warm, the timing can be retarded to reduce the combustion temperature and
polluting emissions (NOx). When the engine is cold, the timing advance must be sufficient to allow
the combustion to begin correctly.
A second correction is made according to the atmospheric pressure.
This correction is used to adapt the timing advance as a function of the atmospheric pressure and
therefore the altitude.
A third correction is made according to the coolant temperature and the time which has passed since
starting.
This correction allows the injection timing advance to be increased while the engine is warming up
(initial 30 seconds). The purpose of this correction is to reduce the misfiring and instabilities which are
liable to occur after a cold start. -
-
-