Page 495 of 1082
01-70000-00
Brake Master cylinder type Tandem type
Booster type Vacuum assisted booster type
Brake type Front wheel Disc
Rear wheel Disc
Parking brake Mechanical type
Suspension Front suspension MacPherson + Coil spring
Rear suspension Multi-link + Coil spring
Air
ConditionerRefrigerant (capacity)
R-134a(430 ± 30g)
Electrical Battery type / Capacity (V-AH) MF / 12 - 90
Starter capacity (V-KW) 12 - 2.3
Alternator capacity (V-A) 14V-140A (EPS), 14V-120A (NPS)
* ( ) option
DescriptionDiesel 2.0 Engine
(D20DTF(Low CO2))
Manual
TransaxleOperating type Floor change type
Gear ratio 1st 3.385
2nd 1.708
3rd 1.033
4th 0.786
5th 0.730
6th 0.595
Reverse 3.747
Transfer Case Model 4WD
Type Electronic control type
Clutch Operating type Hydraulic type
Disc type Dry single diaphragm type
Power
SteeringType Rack and pinion
Steering angle Inner39.0°
Outer31.24°
Rear Axle Drive shaft type Independent
suspensionBall joint type (4WD)
Axle housing type Build-up type (4WD)
Page 899 of 1082
04-30000-00
1. SPECIFICATION
Description Specification
Operating type Hydraulic type
Clutch cover Type Diaphragm spring strap
Adjusting type SATIC (Self Adjusting Technology with
Integrated Cassette) type
Clutch pedal Type Suspended type
Max. operating travel135 ± 3 mm
Pedal free play (Longitudinal)7.1 ± 3 mm
Pedal free play (Transverse) 3 mm
Clutch disc Type Dry type single diaphragm (Rigid type)
Diameter of facingOuter: 250 ± 1 mm
Inner:160 ± 0.8 mm
Thickness of discFree: 8.7 ± 0.3 mm
When loaded: 8.0 ± 0.2 (at 7,800 N)
Numbers of disc 2
Weight 1.18 kg
Flywheel type DMF (Dual Mass Flywheel)
Setting load of clutch cover assembly At least 7,800 N
Clutch master cylinder Operating travel 30 mm
Inner diameter 17.46 mm
Concentric slave
cylinderMaximum operating travel 12.55 mm
Operating pressure Maximum 50 bar
Standard DOT 3 or DOT 4
Capacity As required
Clutch oil
Page 900 of 1082
04-4
2. TIGHTENING TORQUE
DescriptionTightening torque
Amount
Clutch housing boltUpper (17 mm) 85.0 to 100 Nm 2
Front (14 mm)54.0 Nm + 20°1
Rear (14 mm) 51.3 to 56.7 Nm 2
Lower (14 mm) 56.0 to 62.0 Nm 4
Pressure plate assembly bolt (Hexagon 6 mm) 21.0 to 27.0 Nm 6
Concentric slave cylinder bolt (Hexagon 5 mm) 10 to 16 Nm 3
Concentric slave cylinder oil pipe nut 24.5 to 28.4 Nm Remove the nut if it is
necessary. (Once
removed, apply the
Loctite on the thread
before installation.)
Master cylinder nut (12 mm) 7.8 to 17.6 Nm
Master cylinder oil pipe nut (10 mm) 14.7 to 17.6 Nm
Master cylinder push rod lock nut 8.8 to 13.7 Nm
Clutch oil chamber screw and bolt (10 mm) 3.9 to 7.8 Nm
Oil pipe nut (10 mm) 14.7 to 17.6 Nm
Clutch pedal mounting nut (12 mm) 7.8 to 17.6 Nm
Stopper bolt 16 to 22 Nm
Page 901 of 1082
04-50000-00
1. OVERVIEW
The hydraulic clutch transmits the force required to operate the clutch pedal to the concentric slave
cylinder fitted to the clutch housing as a hydraulic pressure.
(The hydraulic pressure is transmitted in the following order: Clutch pedal - Clutch master cylinder -
Clutch pipe - Clutch damper - Clutch pipe and hose - Concentric slave cylinder - Pressure plate -
Flywheel.)
If a driver depress the clutch pedal, the hydraulic pressure is generated in the master cylinder. It is
transmitted to the concentric slave cylinder through the pipe, resulting in the cylinder being forced out. At
this time, the clutch disc is forced against the cylinder by pushing the cover. This, in turn, remove the
flywheel from the pressure plate. As a consequence, the power from the engine will be cut off and the
gear change can be carried out.
Page 903 of 1082
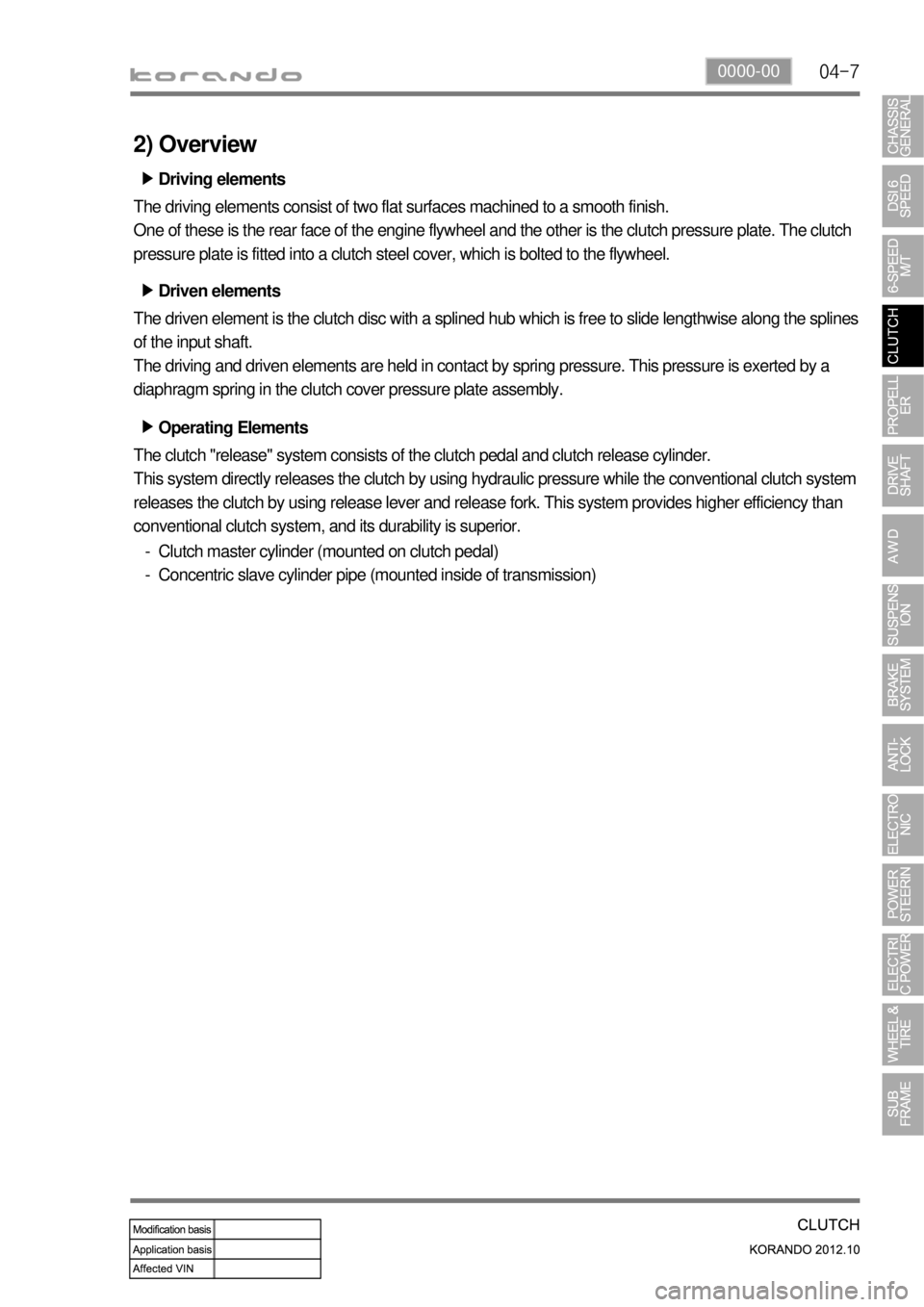
04-70000-00
Operating Elements ▶
The clutch "release" system consists of the clutch pedal and clutch release cylinder.
This system directly releases the clutch by using hydraulic pressure while the conventional clutch system
releases the clutch by using release lever and release fork. This system provides higher efficiency than
conventional clutch system, and its durability is superior.
Clutch master cylinder (mounted on clutch pedal)
Concentric slave cylinder pipe (mounted inside of transmission) -
-Driving elements ▶
The driving elements consist of two flat surfaces machined to a smooth finish.
One of these is the rear face of the engine flywheel and the other is the clutch pressure plate. The clutch
pressure plate is fitted into a clutch steel cover, which is bolted to the flywheel.
Driven elements ▶
The driven element is the clutch disc with a splined hub which is free to slide lengthwise along the splines
of the input shaft.
The driving and driven elements are held in contact by spring pressure. This pressure is exerted by a
diaphragm spring in the clutch cover pressure plate assembly.
2) Overview