Page 915 of 1082
07-50000-00
2. SYSTEM LAYOUT
1) Components
(1) PTU (Power Transfer Unit)
<007b008f008c004700970096009e008c00990047009b009900880095009a008d008c00990047009c00950090009b0047009000950047009b008f008c0047008d009900960095009b0047009e008f008c008c00930047008b00990090009d008c0047009400
96008b008c00930047008a008f00880095008e008c009a0047>the angle of engine torque to 90°
and transfer it to E-coupling to distribute the torque to rear wheels.
(2) E-Coupling (Electronic Coupling)
E-Coupling transfer the engine torque from PTU to rear axle and controls to distribute it between front
wheels and rear wheels.
(3) E-Coupling Control Unit (ECU)
E-Coupling controls the current (clutch engagement force) of EMCD in E-Coupling according to CAN
signals (wheel speed, engine torque, pedal position, ABS/ESP signals).
* EMCD: Electro-Magnetic Control Device PTU assemblyE-coupling control unit
(located on the floor under driver seat)E-coupling
Page 921 of 1082
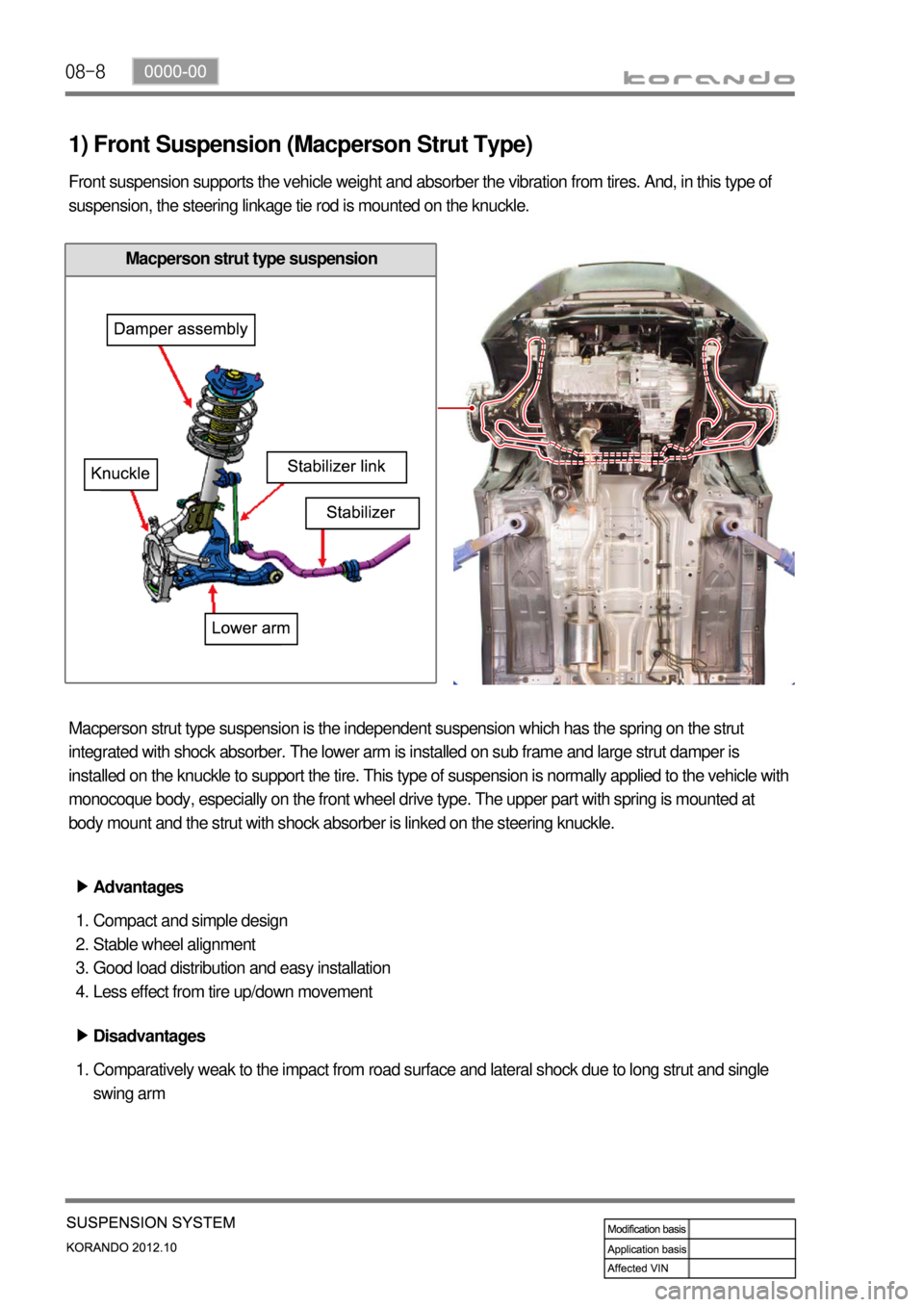
08-8
1) Front Suspension (Macperson Strut Type)
Front suspension supports the vehicle weight and absorber the vibration from tires. And, in this type of
suspension, the steering linkage tie rod is mounted on the knuckle.
Macperson strut type suspension is the independent suspension which has the spring on the strut
integrated with shock absorber. The lower arm is installed on sub frame and large strut damper is
installed on the knuckle to support the tire. This type of suspension is normally applied to the vehicle with
monocoque body, especially on the front wheel drive type. The upper part with spring is mounted at
body mount and the strut with shock absorber is linked on the steering knuckle.
Advantages ▶
Compact and simple design
Stable wheel alignment
Good load distribution and easy installation
Less effect from tire up/down movement 1.
2.
3.
4.
Disadvantages ▶
Comparatively weak to the impact from road surface and lateral shock due to long strut and single
swing arm 1.
Macperson strut type suspension
Page 923 of 1082
09-34850-00
1. SYSTEM OVERVIEW
1) Terms and Definition
CBS: Conventional Brake System
ABS: Anti-Lock Brake System
EBD: Electronic brake-Force Distribution
ESP: Electronic Stability Program
ABD: Automatic Braking Differential
ASR: Acceleration Slip Regulation
AYC: Active Yaw Control (Understeer and Oversteer Control)
HBA: Hydraulic Brake Assistant
ARP: Active Rollover Protection
HSA: Hill Start Assistant -
-
-
-
-
-
-
-
-
-
2) Functions
FunctionVehicle with CBS
Vehicle with ABS/EBD Vehicle with ESP
ABS
Not appliedApplied
Applied EBD Applied
ABD
Not applied ASR
AYC
HBA
ARP
HSA
Page 924 of 1082
09-4
3) Parts Arrangement
Part nameVehicle with
CBSVehicle with ABS/EBDVehicle with
ESP
HECU
Not appliedAppliedApplied Front wheel speed sensor
Rear wheel speed sensor
ABS warning lamp
EBD indicator
Longitudinal G sensor 2WD: N/A, 4WD: Applied Not applied
Sensor cluster
(Yaw rate sensor,
lateral/longitudinal G sensor)
Not applied Applied
ESP indicator
ESP OFF switch and warning
lamp
Steering wheel angle sensor
Page 925 of 1082
09-54850-00
F. Front/rear wheel speed sensor
Front/rear-4WD Rear-2WDH. Parking brake
A. Meter cluster-ABS, EBD, ESP
indicator/warning lampB. Master cylinder and
boosterC. HECU
G. Brake pedal
4) Component
ABS warning lamp
ESP indicator
D. Front brake
assembly
E. Rear brake
assembly
Disc
Disc
Parking brake
warning lamp
Caliper
Caliper
Page 934 of 1082
10-34890-00
1. SPECIFICATION
Unit DescriptionSpecification
ABS ESP
HECUClock frequency 32 MHz 50 MHz
Memory 128 KB 512 KB
Switch Orifice Orifice
Wheel speed
sensorABS / ESP CBS
Operating temperature- 40°C to 150°C - 40°C to 150°C
- 40°C to 115°C - 40°C to 115°C
Operating frequency 1 to 2,500 Hz 1 to 8,000 Hz
Operating voltage 4.5 to 16 V 3.3 to 18 V
G-sensor ABS CBS / ESP
Operating voltage 4.75 to 5.25 V N/A
Operating temperature- 30°C to 85°C
Operating range -1.5 to 1.5 g
Output voltage 0.5 to 4.5 V
Page 935 of 1082
10-4
ABS / ESP CBS
Circuit diagram of wheel speed sensor ▶
Page 949 of 1082
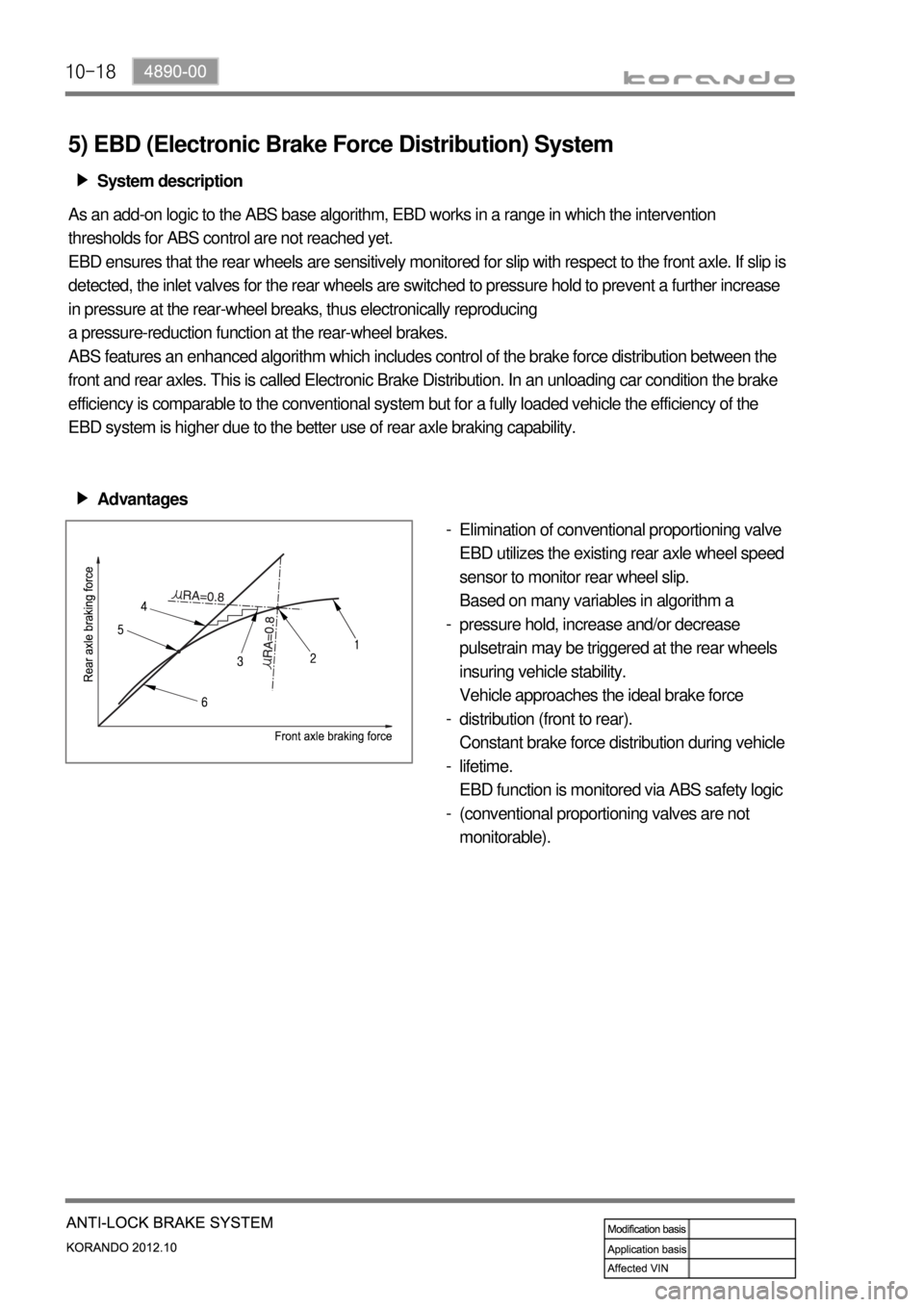
10-18
5) EBD (Electronic Brake Force Distribution) System
System description ▶
As an add-on logic to the ABS base algorithm, EBD works in a range in which the intervention
thresholds for ABS control are not reached yet.
EBD ensures that the rear wheels are sensitively monitored for slip with respect to the front axle. If slip is
detected, the inlet valves for the rear wheels are switched to pressure hold to prevent a further increase
in pressure at the rear-wheel breaks, thus electronically reproducing
a pressure-reduction function at the rear-wheel brakes.
ABS features an enhanced algorithm which includes control of the brake force distribution between the
front and rear axles. This is called Electronic Brake Distribution. In an unloading car condition the brake
efficiency is comparable to the conventional system but for a fully loaded vehicle the efficiency of the
EBD system is higher due to the better use of rear axle braking capability.
Advantages ▶
Elimination of conventional proportioning valve
EBD utilizes the existing rear axle wheel speed
sensor to monitor rear wheel slip.
Based on many variables in algorithm a
pressure hold, increase and/or decrease
pulsetrain may be triggered at the rear wheels
insuring vehicle stability.
Vehicle approaches the ideal brake force
distribution (front to rear).
Constant brake force distribution during vehicle
lifetime.
EBD function is monitored via ABS safety logic
(conventional proportioning valves are not
monitorable). -
-
-
-
-