Page 355 of 365

13B-355
MR-372-J84-13B200$936.mif
V13
EDC16
Program No: C1
Vdiag No: 18, 1C, 20,
50, 58, 5CDIESEL INJECTION
Fault finding – Tests13B
2 – Injector return flow balance check:
3 – Removing the tool:
Disconnect the pipe from an injector:
– press on the injector clip,
– pull vertically on the end piece of the pipe of tool Mot.1760, placing a wipe on the end piece to prevent run-off.
Lift the end piece vertically so that the fuel contained in the pipes flows into the measuring cylinders of tool
Mot.1760.
Remove the other 3 pipes using the same procedure.
TEST 9
CONTINUED 5
Does the engine start?
YES
– The injector return pipes must be fitted to the injectors.
– Start the engine.
– Display the Fuel circuit sub-function in the CLIP diagnostic tool.
– Raise the temperature of the engine.
– Read the diesel fuel temperature with PR063 Fuel temperature until a diesel fuel temperature greater than
50°C is reached
– Switch off the engine.
–Fit Mot. 1760 as shown in the installation procedure (see step 1).
– Check the value of the PR038 Rail pressure.
– Ask another Cotech to monitor the rise in fuel in the cans during engine turnover, as one of the cans will fill up
quickly if one of the injectors is leaking.
– Start the engine.
– Accelerate the engine until the pressure in the rail is 550 bar:
* if the engine speed is less than 3000 rpm, maintain this pressure.
* if the engine speed is greater than 3000 rpm, reduce the engine speed until the rail pressure is 500 bar and
maintain this pressure.
– Maintain these conditions for one minute.
– Release the accelerator pedal and maintain the idle speed for 10 seconds.
– Switch off the engine.
– Measure the quantity of fuel contained in each measuring cylinder.
– Replace the injector if the quantity of fuel is more than 50 ml.
– Remove Mot. 1760 as shown in the tool removal procedure (see step 3).
IMPORTANT
Use a cleaning cloth (part number 77 11 211 707) to absorb fuel run-off.NO
Fit Mot. 1760 as shown in the tool fitting procedure.
- Start the vehicle or perform a 15 second starting sequence
(with ignition key).
- Measure the length travelled by the diesel fuel in the pipes of
Mot. 1760.
Replace the injector if the length travelled by the fuel is more than
10 cm compared with the average of the other three injectors.
Page 357 of 365
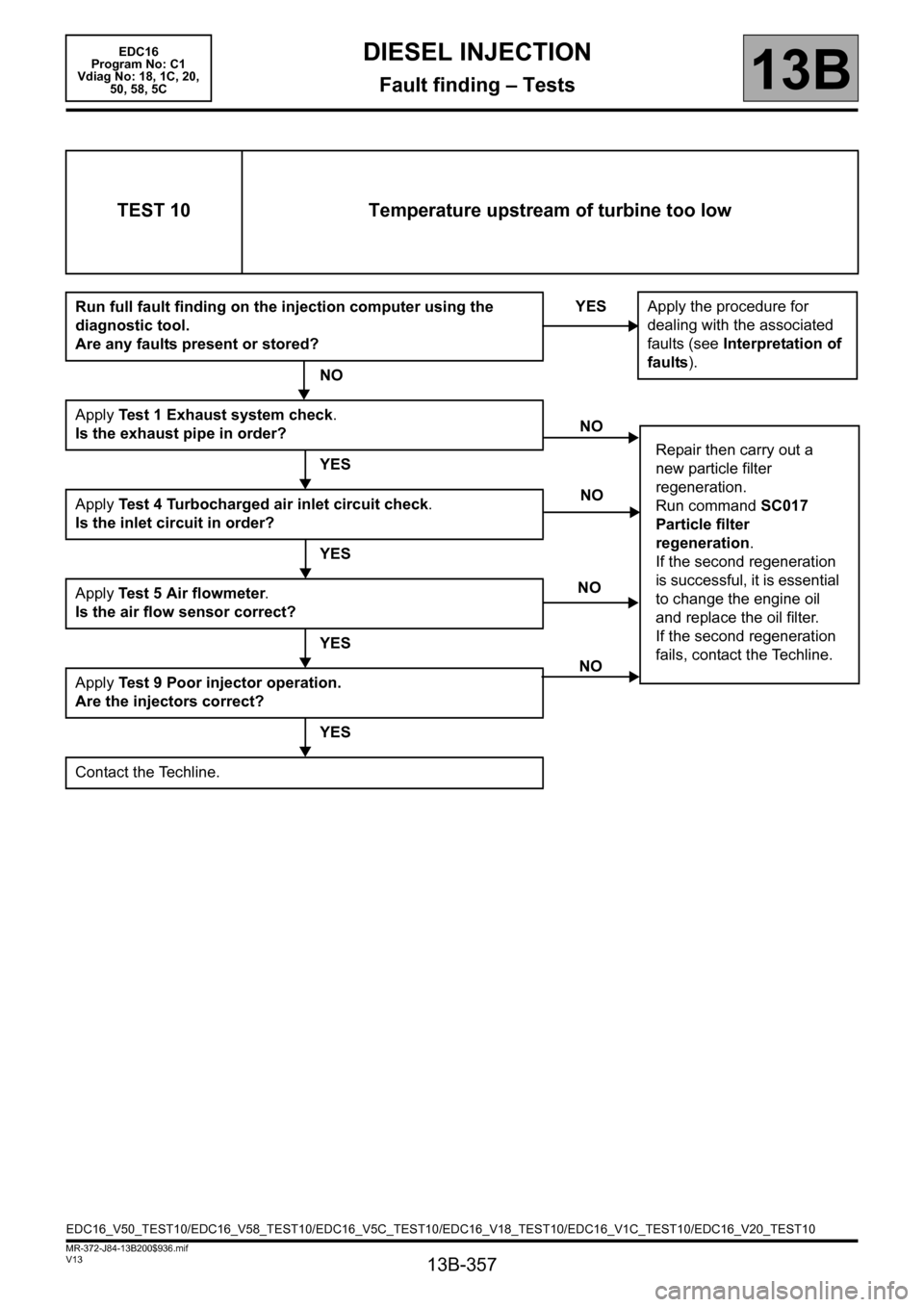
13B-357
MR-372-J84-13B200$936.mif
V13
EDC16
Program No: C1
Vdiag No: 18, 1C, 20,
50, 58, 5CDIESEL INJECTION
Fault finding – Tests13B
TEST 10 Temperature upstream of turbine too low
Run full fault finding on the injection computer using the
diagnostic tool.
Are any faults present or stored?
NO
Apply Test 1 Exhaust system check.
Is the exhaust pipe in order?
YES
Apply Test 4 Turbocharged air inlet circuit check.
Is the inlet circuit in order?
YES
Apply Test 5 Air flowmeter.
Is the air flow sensor correct?
YES
Apply Test 9 Poor injector operation.
Are the injectors correct?
YES
Contact the Techline.YES
Apply the procedure for
dealing with the associated
faults (see Interpretation of
faults).
NO
Repair then carry out a
new particle filter
regeneration.
Run command SC017
Particle filter
regeneration.
If the second regeneration
is successful, it is essential
to change the engine oil
and replace the oil filter.
If the second regeneration
fails, contact the Techline.
NO
NO
NO
EDC16_V50_TEST10/EDC16_V58_TEST10/EDC16_V5C_TEST10/EDC16_V18_TEST10/EDC16_V1C_TEST10/EDC16_V20_TEST10
Page 360 of 365
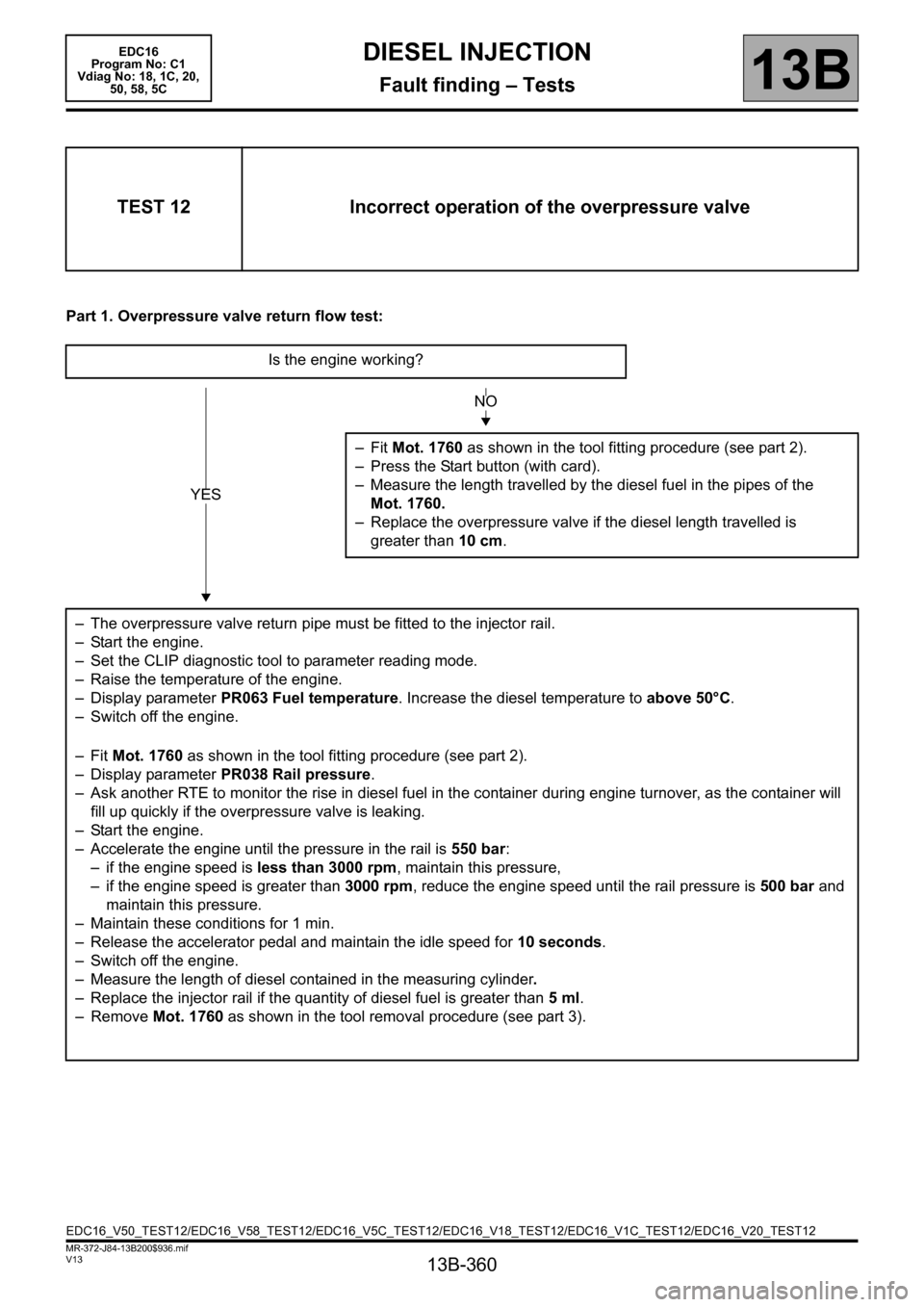
13B-360
MR-372-J84-13B200$936.mif
V13
DIESEL INJECTION
Fault finding – Tests
EDC16
Program No: C1
Vdiag No: 18, 1C, 20,
50, 58, 5C
13B
Part 1. Overpressure valve return flow test:
TEST 12 Incorrect operation of the overpressure valve
Is the engine working?
–Fit Mot. 1760 as shown in the tool fitting procedure (see part 2).
– Press the Start button (with card).
– Measure the length travelled by the diesel fuel in the pipes of the
Mot. 1760.
– Replace the overpressure valve if the diesel length travelled is
greater than 10 cm.
– The overpressure valve return pipe must be fitted to the injector rail.
– Start the engine.
– Set the CLIP diagnostic tool to parameter reading mode.
– Raise the temperature of the engine.
– Display parameter PR063 Fuel temperature. Increase the diesel temperature to above 50°C.
– Switch off the engine.
–Fit Mot. 1760 as shown in the tool fitting procedure (see part 2).
– Display parameter PR038 Rail pressure.
– Ask another RTE to monitor the rise in diesel fuel in the container during engine turnover, as the container will
fill up quickly if the overpressure valve is leaking.
– Start the engine.
– Accelerate the engine until the pressure in the rail is 550 bar:
– if the engine speed is less than 3000 rpm, maintain this pressure,
– if the engine speed is greater than 3000 rpm, reduce the engine speed until the rail pressure is 500 bar and
maintain this pressure.
– Maintain these conditions for 1 min.
– Release the accelerator pedal and maintain the idle speed for 10 seconds.
– Switch off the engine.
– Measure the length of diesel contained in the measuring cylinder.
– Replace the injector rail if the quantity of diesel fuel is greater than 5ml.
– Remove Mot. 1760 as shown in the tool removal procedure (see part 3).
YES
NO
EDC16_V50_TEST12/EDC16_V58_TEST12/EDC16_V5C_TEST12/EDC16_V18_TEST12/EDC16_V1C_TEST12/EDC16_V20_TEST12
Page 361 of 365
13B-361
MR-372-J84-13B200$936.mif
V13
DIESEL INJECTION
Fault finding – Tests
EDC16
Program No: C1
Vdiag No: 18, 1C, 20,
50, 58, 5C
13B
Part 2: Fitting the tool:
Remove the engine undertray.
Disconnect the overpressure valve return pipe according to the following procedure (do not remove the clips):
– press the clip,
– pull vertically on the end piece (1) of the fuel return pipe.
TEST 12
CONTINUED 1
IMPORTANT
The end piece is fragile. Be careful not to break it by pulling it too hard. Replace all removed clips.
Page 365 of 365
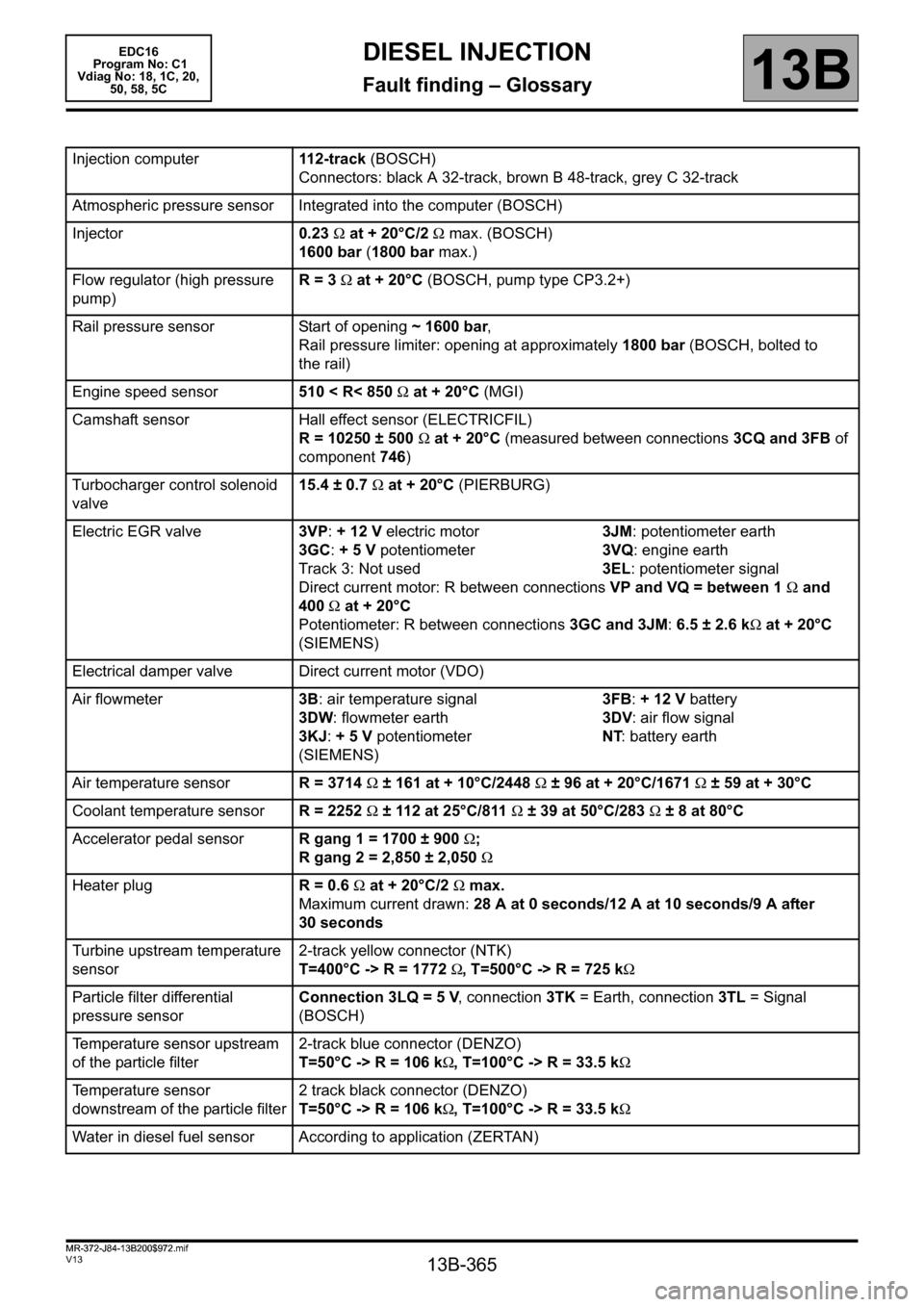
13B-365
MR-372-J84-13B200$972.mif
V13
13B
DIESEL INJECTION
Fault finding – Glossary
Injection computer112-track (BOSCH)
Connectors: black A 32-track, brown B 48-track, grey C 32-track
Atmospheric pressure sensor Integrated into the computer (BOSCH)
Injector0.23 Ω at + 20°C/2 Ω max. (BOSCH)
1600 bar (1800 bar max.)
Flow regulator (high pressure
pump)R = 3 Ω at + 20°C (BOSCH, pump type CP3.2+)
Rail pressure sensor Start of opening ~ 1600 bar,
Rail pressure limiter: opening at approximately 1800 bar (BOSCH, bolted to
the rail)
Engine speed sensor510 < R< 850 Ω at + 20°C (MGI)
Camshaft sensor Hall effect sensor (ELECTRICFIL)
R = 10250 ± 500 Ω at + 20°C (measured between connections 3CQ and 3FB of
component 746)
Turbocharger control solenoid
valve15.4 ± 0.7 Ω at + 20°C (PIERBURG)
Electric EGR valve3VP: + 12 V electric motor 3JM: potentiometer earth
3GC: + 5 V potentiometer 3VQ: engine earth
Track 3: Not used 3EL: potentiometer signal
Direct current motor: R between connections VP and VQ = between 1 Ω and
400 Ω at + 20°C
Potentiometer: R between connections 3GC and 3JM: 6.5 ± 2.6 kΩ at + 20°C
(SIEMENS)
Electrical damper valve Direct current motor (VDO)
Air flowmeter3B: air temperature signal 3FB: + 12 V battery
3DW: flowmeter earth 3DV: air flow signal
3KJ: + 5 V potentiometer NT: battery earth
(SIEMENS)
Air temperature sensorR = 3714
Ω ± 161 at + 10°C/2448 Ω ± 96 at + 20°C/1671 Ω ± 59 at + 30°C
Coolant temperature sensorR = 2252 Ω ± 112 at 25°C/811 Ω ± 39 at 50°C/283 Ω ± 8 at 80°C
Accelerator pedal sensorR gang 1 = 1700 ± 900 Ω;
R gang 2 = 2,850 ± 2,050Ω
Heater plugR = 0.6 Ω at + 20°C/2 Ω max.
Maximum current drawn: 28 A at 0 seconds/12 A at 10 seconds/9 A after
30 seconds
Turbine upstream temperature
sensor2-track yellow connector (NTK)
T=400°C -> R = 1772 Ω, T=500°C -> R = 725 kΩ
Particle filter differential
pressure sensorConnection 3LQ = 5 V, connection 3TK = Earth, connection 3TL = Signal
(BOSCH)
Temperature sensor upstream
of the particle filter2-track blue connector (DENZO)
T=50°C -> R = 106 kΩ, T=100°C -> R = 33.5 kΩ
Temperature sensor
downstream of the particle filter2 track black connector (DENZO)
T=50°C -> R = 106 kΩ, T=100°C -> R = 33.5 kΩ
Water in diesel fuel sensor According to application (ZERTAN)
MR-372-J84-13B200$972.mif
EDC16
Program No: C1
Vdiag No: 18, 1C, 20,
50, 58, 5C