Page 137 of 230
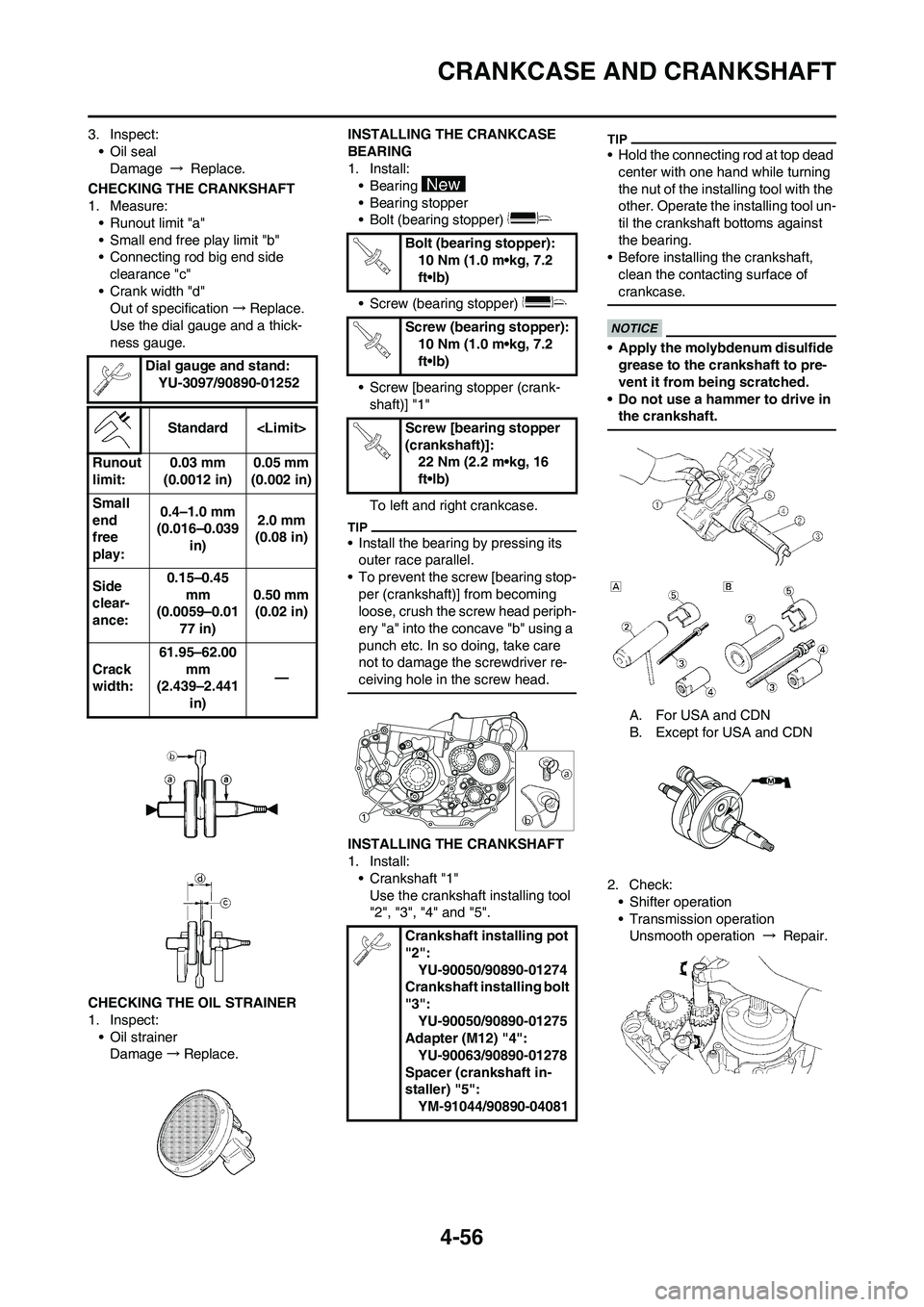
4-56
CRANKCASE AND CRANKSHAFT
3. Inspect:
• Oil seal
Damage → Replace.
CHECKING THE CRANKSHAFT
1. Measure:
• Runout limit "a"
• Small end free play limit "b"
• Connecting rod big end side
clearance "c"
• Crank width "d"
Out of specification→Replace.
Use the dial gauge and a thick-
ness gauge.
CHECKING THE OIL STRAINER
1. Inspect:
• Oil strainer
Damage→Replace.INSTALLING THE CRANKCASE
BEARING
1. Install:
•Bearing
• Bearing stopper
• Bolt (bearing stopper)
• Screw (bearing stopper)
• Screw [bearing stopper (crank-
shaft)] "1"
To left and right crankcase.
• Install the bearing by pressing its
outer race parallel.
• To prevent the screw [bearing stop-
per (crankshaft)] from becoming
loose, crush the screw head periph-
ery "a" into the concave "b" using a
punch etc. In so doing, take care
not to damage the screwdriver re-
ceiving hole in the screw head.
INSTALLING THE CRANKSHAFT
1. Install:
• Crankshaft "1"
Use the crankshaft installing tool
"2", "3", "4" and "5".
• Hold the connecting rod at top dead
center with one hand while turning
the nut of the installing tool with the
other. Operate the installing tool un-
til the crankshaft bottoms against
the bearing.
• Before installing the crankshaft,
clean the contacting surface of
crankcase.
• Apply the molybdenum disulfide
grease to the crankshaft to pre-
vent it from being scratched.
• Do not use a hammer to drive in
the crankshaft.
A. For USA and CDN
B. Except for USA and CDN
2. Check:
• Shifter operation
• Transmission operation
Unsmooth operation → Repair. Dial gauge and stand:
YU-3097/90890-01252
Standard
Runout
limit:0.03 mm
(0.0012 in)0.05 mm
(0.002 in)
Small
end
free
play:0.4–1.0 mm
(0.016–0.039
in)2.0 mm
(0.08 in)
Side
clear-
ance:0.15–0.45
mm
(0.0059–0.01
77 in)0.50 mm
(0.02 in)
Crack
width:61.95–62.00
mm
(2.439–2.441
in)—
Bolt (bearing stopper):
10 Nm (1.0 m•kg, 7.2
ft•lb)
Screw (bearing stopper):
10 Nm (1.0 m•kg, 7.2
ft•lb)
Screw [bearing stopper
(crankshaft)]:
22 Nm (2.2 m•kg, 16
ft•lb)
Crankshaft installing pot
"2":
YU-90050/90890-01274
Crankshaft installing bolt
"3":
YU-90050/90890-01275
Adapter (M12) "4":
YU-90063/90890-01278
Spacer (crankshaft in-
staller) "5":
YM-91044/90890-04081
Page 138 of 230
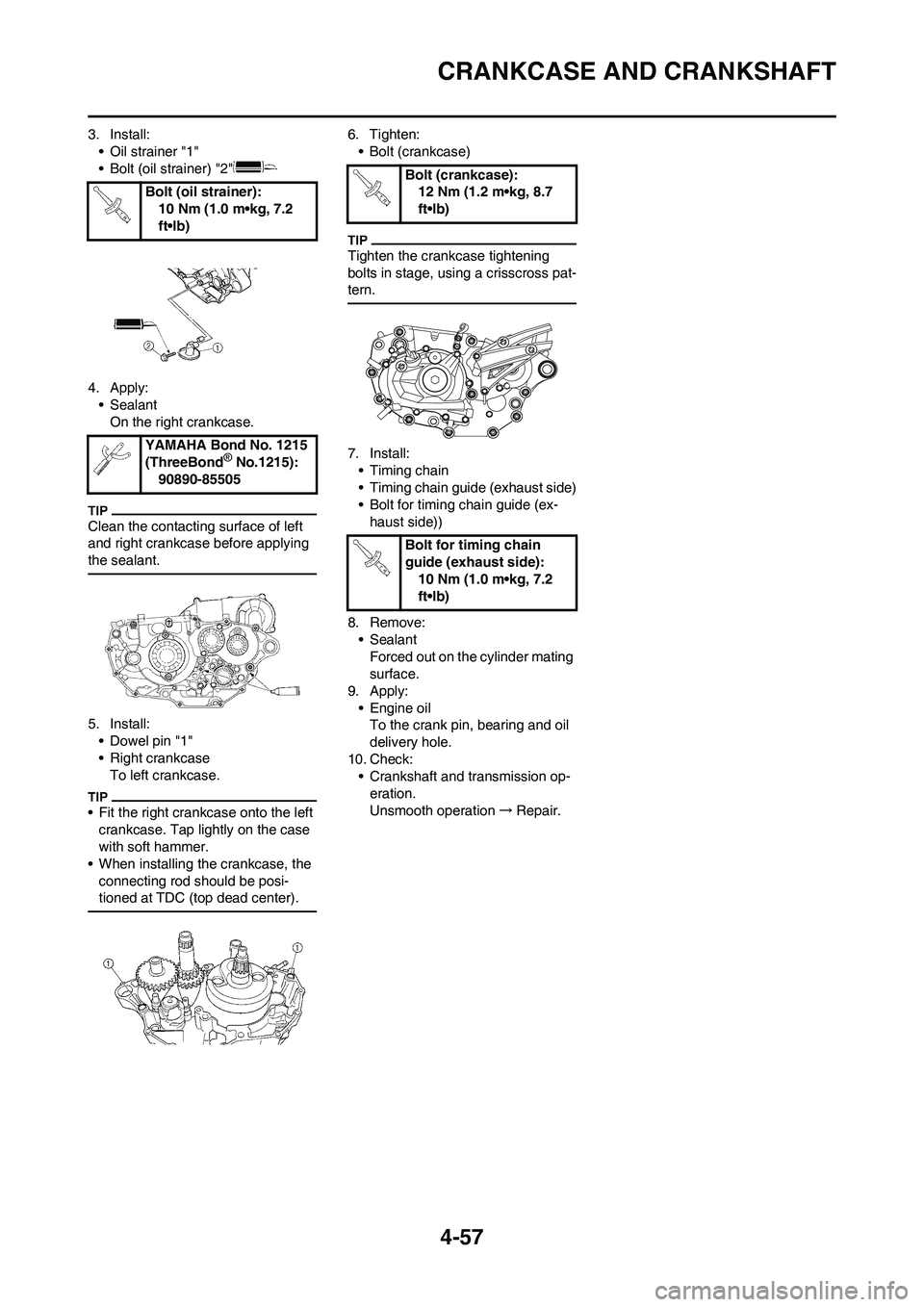
4-57
CRANKCASE AND CRANKSHAFT
3. Install:
• Oil strainer "1"
• Bolt (oil strainer) "2"
4. Apply:
• Sealant
On the right crankcase.
Clean the contacting surface of left
and right crankcase before applying
the sealant.
5. Install:
• Dowel pin "1"
• Right crankcase
To left crankcase.
• Fit the right crankcase onto the left
crankcase. Tap lightly on the case
with soft hammer.
• When installing the crankcase, the
connecting rod should be posi-
tioned at TDC (top dead center).
6. Tighten:
• Bolt (crankcase)
Tighten the crankcase tightening
bolts in stage, using a crisscross pat-
tern.
7. Install:
• Timing chain
• Timing chain guide (exhaust side)
• Bolt for timing chain guide (ex-
haust side))
8. Remove:
• Sealant
Forced out on the cylinder mating
surface.
9. Apply:
• Engine oil
To the crank pin, bearing and oil
delivery hole.
10. Check:
• Crankshaft and transmission op-
eration.
Unsmooth operation→Repair. Bolt (oil strainer):
10 Nm (1.0 m•kg, 7.2
ft•lb)
YAMAHA Bond No. 1215
(ThreeBond® No.1215):
90890-85505
Bolt (crankcase):
12 Nm (1.2 m•kg, 8.7
ft•lb)
Bolt for timing chain
guide (exhaust side):
10 Nm (1.0 m•kg, 7.2
ft•lb)
Page 139 of 230
4-58
TRANSMISSION, SHIFT CAM AND SHIFT FORK
TRANSMISSION, SHIFT CAM AND SHIFT FORK
REMOVING THE TRANSMISSION, SHIFT CAM AND SHIFT FORK
Order Part name Q'ty Remarks
Engine Refer to "ENGINE REMOVAL" section.
Separate the crankcase.Refer to "CRANKCASE AND CRANK-
SHAFT" section.
1 Main axle 1 Refer to removal section.
2 Drive axle 1 Refer to removal section.
3 Shift cam 1 Refer to removal section.
4 Shift fork 3 1 Refer to removal section.
5 Shift fork 2 1 Refer to removal section.
6 Shift fork 1 1 Refer to removal section.
7 Collar 1
Page 140 of 230
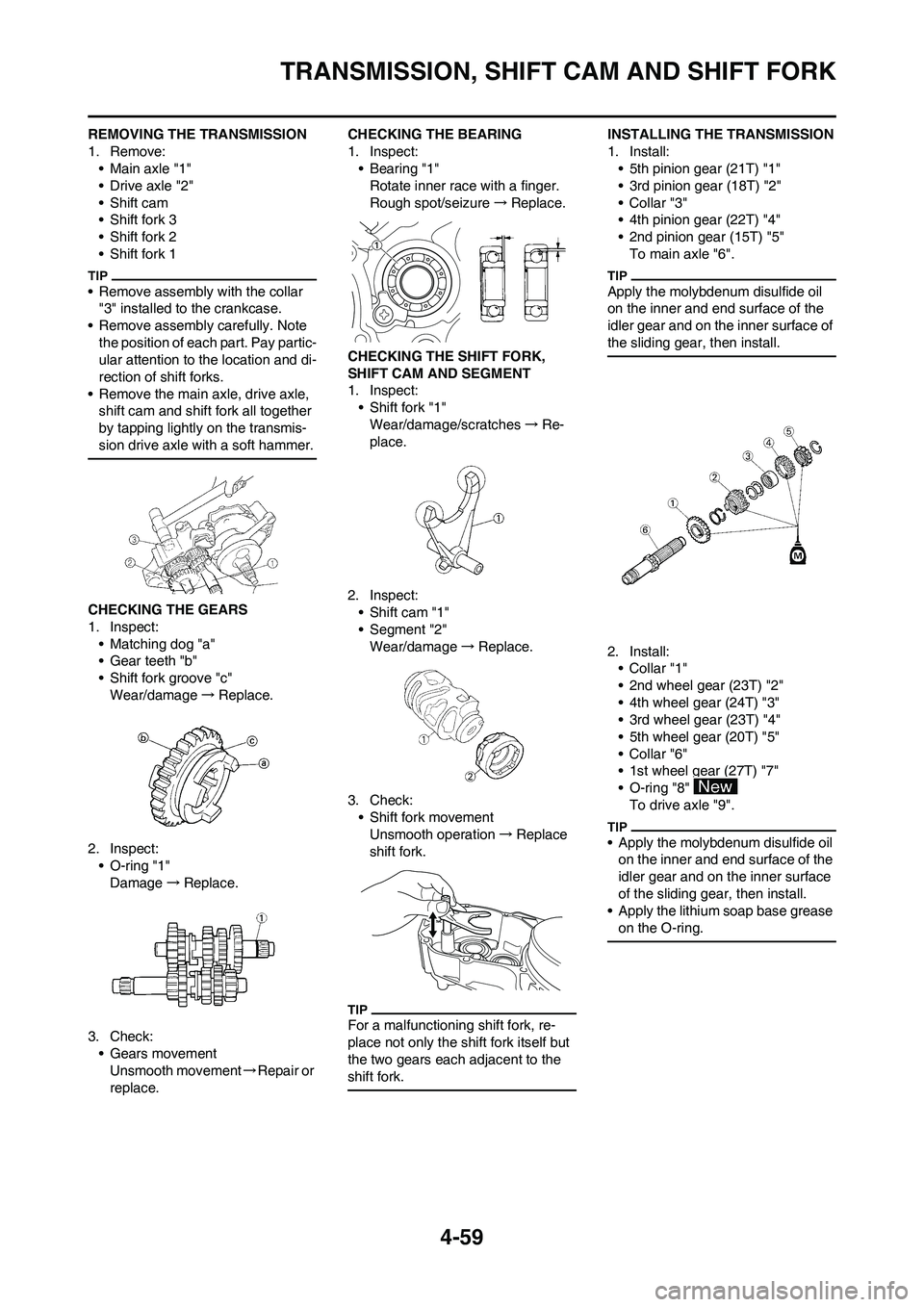
4-59
TRANSMISSION, SHIFT CAM AND SHIFT FORK
REMOVING THE TRANSMISSION
1. Remove:
• Main axle "1"
• Drive axle "2"
• Shift cam
• Shift fork 3
• Shift fork 2
• Shift fork 1
• Remove assembly with the collar
"3" installed to the crankcase.
• Remove assembly carefully. Note
the position of each part. Pay partic-
ular attention to the location and di-
rection of shift forks.
• Remove the main axle, drive axle,
shift cam and shift fork all together
by tapping lightly on the transmis-
sion drive axle with a soft hammer.
CHECKING THE GEARS
1. Inspect:
• Matching dog "a"
• Gear teeth "b"
• Shift fork groove "c"
Wear/damage→Replace.
2. Inspect:
• O-ring "1"
Damage→Replace.
3. Check:
• Gears movement
Unsmooth movement→Repair or
replace.CHECKING THE BEARING
1. Inspect:
•Bearing "1"
Rotate inner race with a finger.
Rough spot/seizure→Replace.
CHECKING THE SHIFT FORK,
SHIFT CAM AND SEGMENT
1. Inspect:
• Shift fork "1"
Wear/damage/scratches→Re-
place.
2. Inspect:
• Shift cam "1"
• Segment "2"
Wear/damage→Replace.
3. Check:
• Shift fork movement
Unsmooth operation→Replace
shift fork.
For a malfunctioning shift fork, re-
place not only the shift fork itself but
the two gears each adjacent to the
shift fork.
INSTALLING THE TRANSMISSION
1. Install:
• 5th pinion gear (21T) "1"
• 3rd pinion gear (18T) "2"
•Collar "3"
• 4th pinion gear (22T) "4"
• 2nd pinion gear (15T) "5"
To main axle "6".
Apply the molybdenum disulfide oil
on the inner and end surface of the
idler gear and on the inner surface of
the sliding gear, then install.
2. Install:
•Collar "1"
• 2nd wheel gear (23T) "2"
• 4th wheel gear (24T) "3"
• 3rd wheel gear (23T) "4"
• 5th wheel gear (20T) "5"
•Collar "6"
• 1st wheel gear (27T) "7"
• O-ring "8"
To drive axle "9".
• Apply the molybdenum disulfide oil
on the inner and end surface of the
idler gear and on the inner surface
of the sliding gear, then install.
• Apply the lithium soap base grease
on the O-ring.
Page 141 of 230
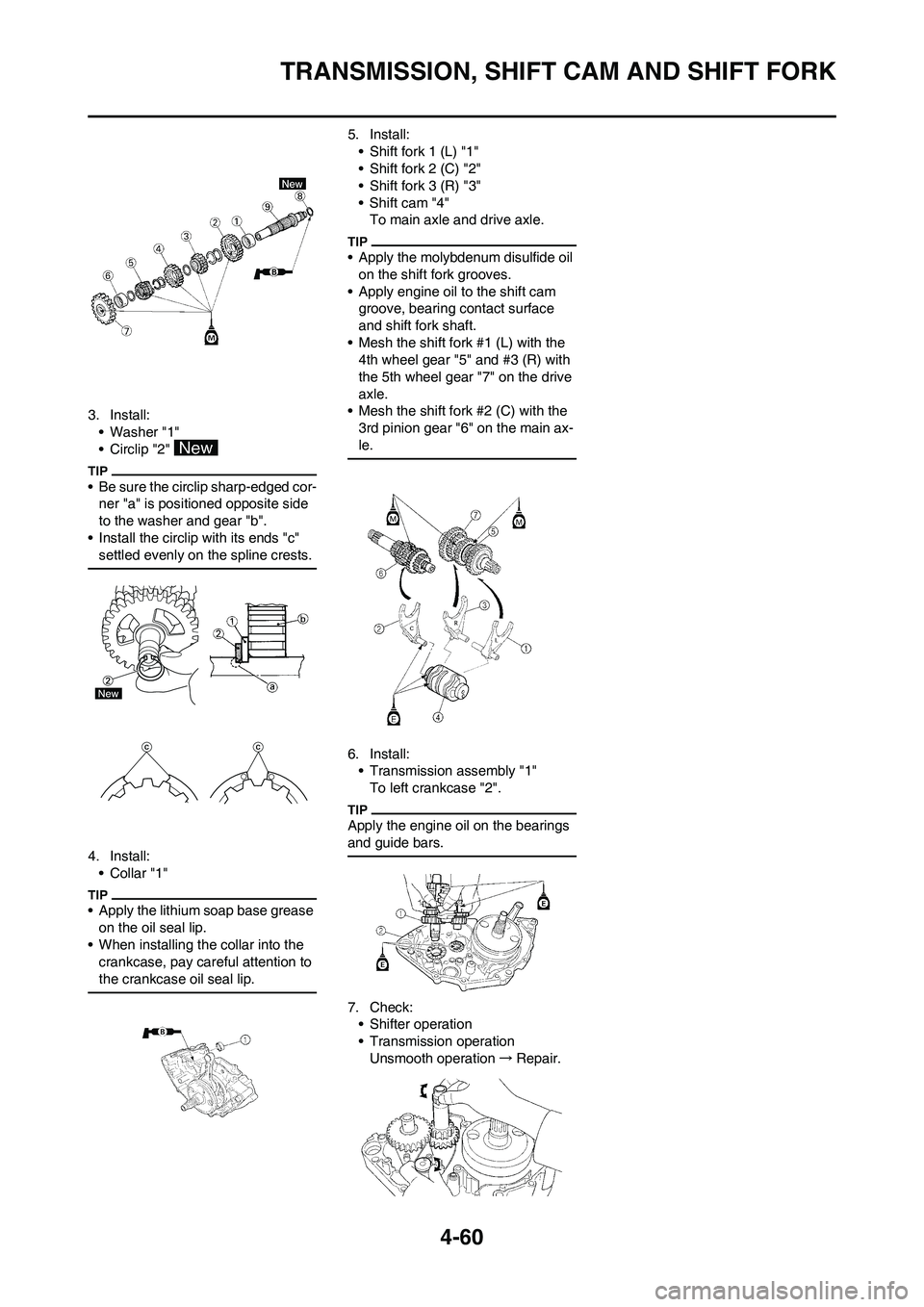
4-60
TRANSMISSION, SHIFT CAM AND SHIFT FORK
3. Install:
• Washer "1"
• Circlip "2"
• Be sure the circlip sharp-edged cor-
ner "a" is positioned opposite side
to the washer and gear "b".
• Install the circlip with its ends "c"
settled evenly on the spline crests.
4. Install:
•Collar "1"
• Apply the lithium soap base grease
on the oil seal lip.
• When installing the collar into the
crankcase, pay careful attention to
the crankcase oil seal lip.
5. Install:
• Shift fork 1 (L) "1"
• Shift fork 2 (C) "2"
• Shift fork 3 (R) "3"
• Shift cam "4"
To main axle and drive axle.
• Apply the molybdenum disulfide oil
on the shift fork grooves.
• Apply engine oil to the shift cam
groove, bearing contact surface
and shift fork shaft.
• Mesh the shift fork #1 (L) with the
4th wheel gear "5" and #3 (R) with
the 5th wheel gear "7" on the drive
axle.
• Mesh the shift fork #2 (C) with the
3rd pinion gear "6" on the main ax-
le.
6. Install:
• Transmission assembly "1"
To left crankcase "2".
Apply the engine oil on the bearings
and guide bars.
7. Check:
• Shifter operation
• Transmission operation
Unsmooth operation→Repair.
Page 142 of 230
5-1
FRONT WHEEL AND REAR WHEEL
CHASSIS
This section is intended for those who have basic knowledge and skill concerning the servicing of Yamaha motorcycles
(e.g., Yamaha dealers, service engineers, etc.) Those who have little knowledge and skill concerning servicing are request-
ed not to undertake inspection, adjustment, disassembly, or reassembly only by reference to this manual. It may lead to
servicing trouble and mechanical damage.
FRONT WHEEL AND REAR WHEEL
REMOVING THE FRONT WHEEL
Order Part name Q'ty Remarks Hold the machine by placing the suitable stand
under the engine. Refer to "HANDLING NOTE".
1 Bolt (axle holder) 4 Only loosening.
2 Nut (front wheel axle) 1
3 Front wheel axle 1
4 Front wheel 1
5 Collar 2
6 Oil seal 2
7 Bearing 2 Refer to removal section.
8 Brake disc 1
Page 143 of 230
5-2
FRONT WHEEL AND REAR WHEEL
REMOVING THE REAR WHEEL
Order Part name Q'ty Remarks
Hold the machine by placing the suitable stand
under the engine.Refer to "HANDLING NOTE".
1 Nut (rear wheel axle) 1
2 Rear wheel axle 1
3 Drive chain puller 2
4 Rear wheel 1 Refer to removal section.
5 Collar 2
6 Rear wheel sprocket 1
7 Oil seal 2
8 Circlip 1
9 Bearing 3 Refer to removal section.
10 Brake disc 1
5
Page 144 of 230
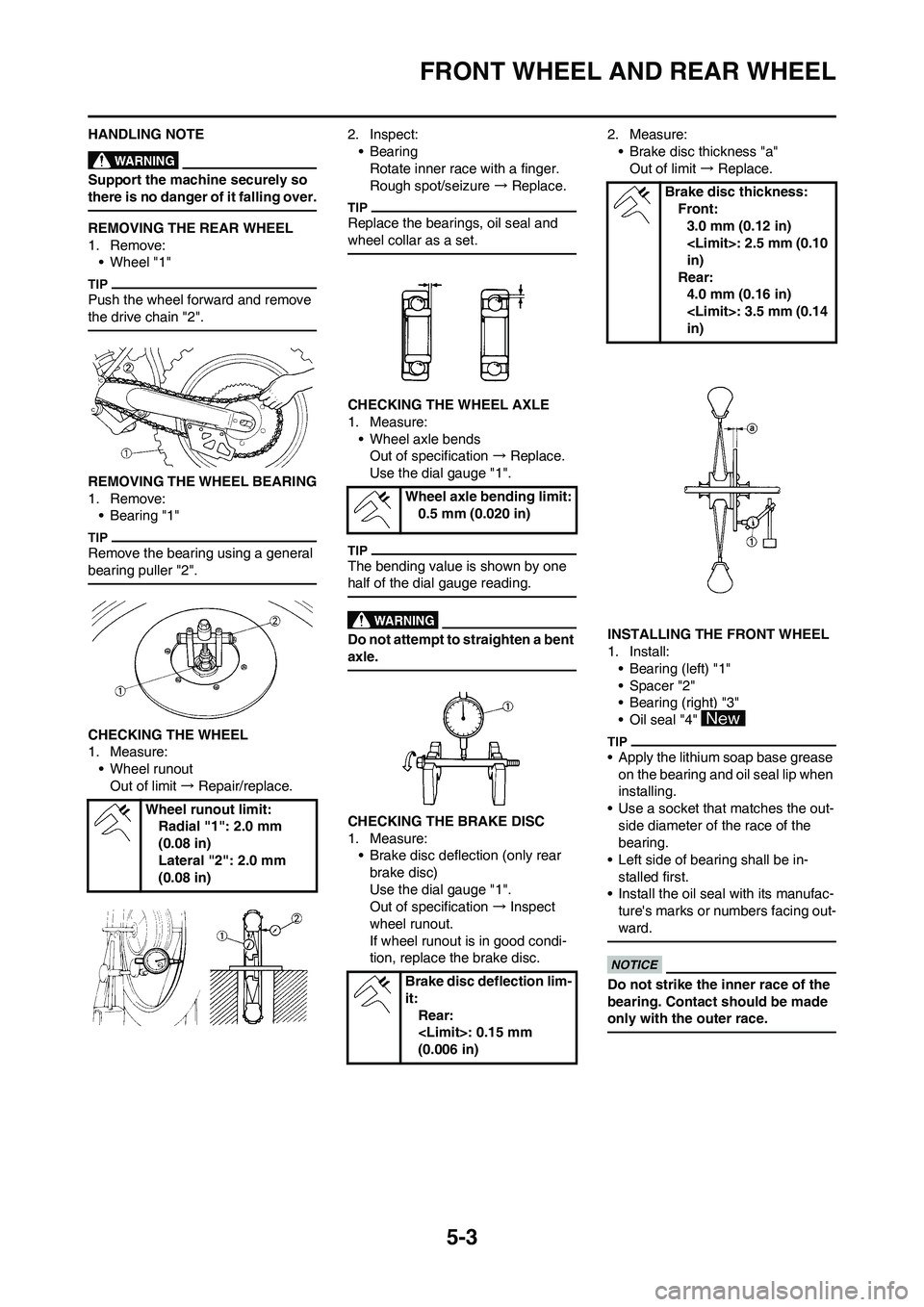
5-3
FRONT WHEEL AND REAR WHEEL
HANDLING NOTE
Support the machine securely so
there is no danger of it falling over.
REMOVING THE REAR WHEEL
1. Remove:
• Wheel "1"
Push the wheel forward and remove
the drive chain "2".
REMOVING THE WHEEL BEARING
1. Remove:
• Bearing "1"
Remove the bearing using a general
bearing puller "2".
CHECKING THE WHEEL
1. Measure:
• Wheel runout
Out of limit → Repair/replace.2. Inspect:
•Bearing
Rotate inner race with a finger.
Rough spot/seizure → Replace.
Replace the bearings, oil seal and
wheel collar as a set.
CHECKING THE WHEEL AXLE
1. Measure:
• Wheel axle bends
Out of specification → Replace.
Use the dial gauge "1".
The bending value is shown by one
half of the dial gauge reading.
Do not attempt to straighten a bent
axle.
CHECKING THE BRAKE DISC
1. Measure:
• Brake disc deflection (only rear
brake disc)
Use the dial gauge "1".
Out of specification → Inspect
wheel runout.
If wheel runout is in good condi-
tion, replace the brake disc.2. Measure:
• Brake disc thickness "a"
Out of limit → Replace.
INSTALLING THE FRONT WHEEL
1. Install:
• Bearing (left) "1"
• Spacer "2"
• Bearing (right) "3"
• Oil seal "4"
• Apply the lithium soap base grease
on the bearing and oil seal lip when
installing.
• Use a socket that matches the out-
side diameter of the race of the
bearing.
• Left side of bearing shall be in-
stalled first.
• Install the oil seal with its manufac-
ture's marks or numbers facing out-
ward.
Do not strike the inner race of the
bearing. Contact should be made
only with the outer race.
Wheel runout limit:
Radial "1": 2.0 mm
(0.08 in)
Lateral "2": 2.0 mm
(0.08 in)
Wheel axle bending limit:
0.5 mm (0.020 in)
Brake disc deflection lim-
it:
Rear:
: 0.15 mm
(0.006 in)
Brake disc thickness:
Front:
3.0 mm (0.12 in)
: 2.5 mm (0.10
in)
Rear:
4.0 mm (0.16 in)
: 3.5 mm (0.14
in)