Page 180 of 230
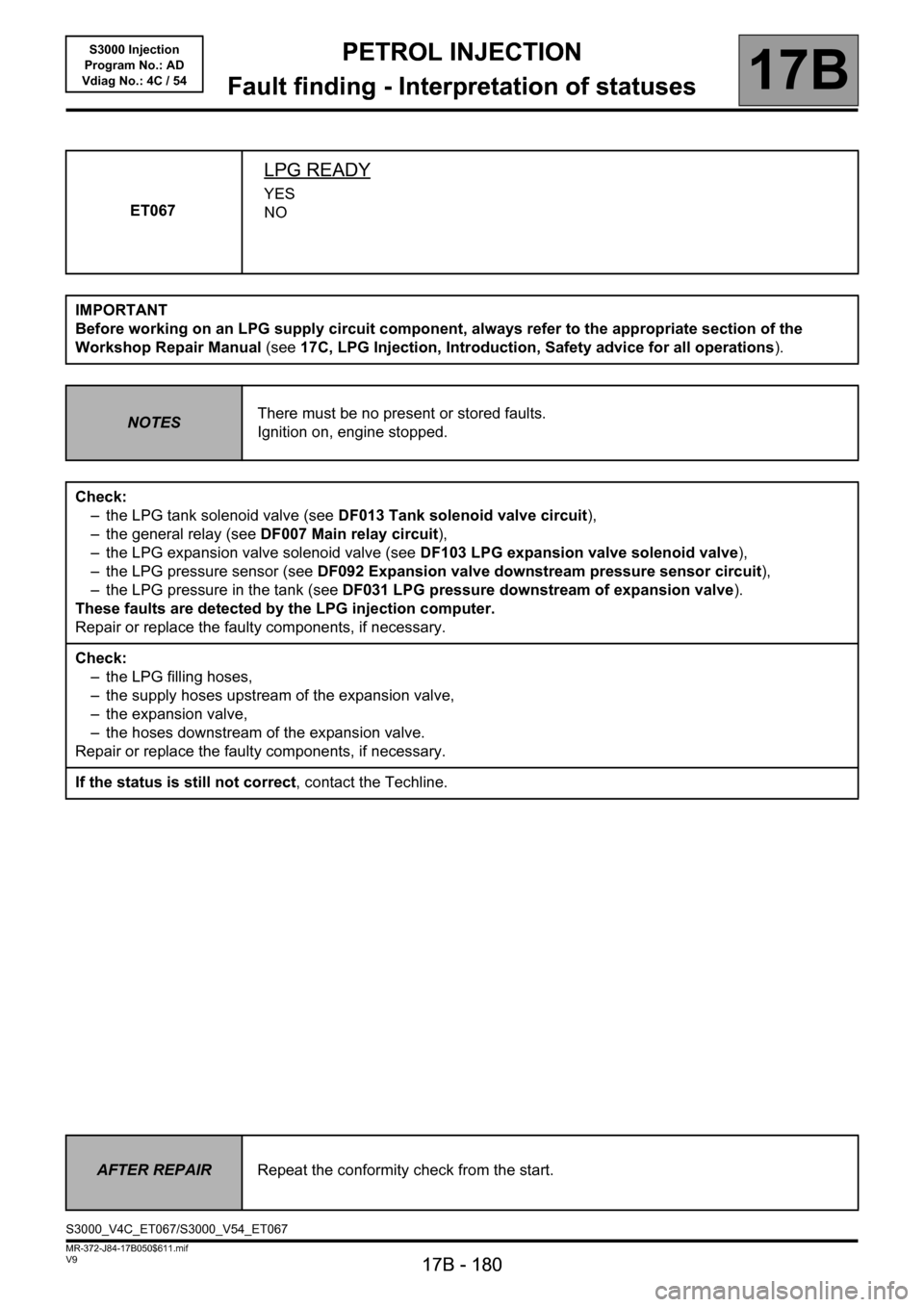
PETROL INJECTION
Fault finding - Interpretation of statuses
17B
17B - 180
PETROL INJECTION
Fault finding - Interpretation of statuses
17B
17B - 180V9 MR-372-J84-17B050$611.mif
S3000 Injection
Program No.: AD
Vdiag No.: 4C / 54
ET067
LPG READY
YES
NO
IMPORTANT
Before working on an LPG supply circuit component, always refer to the appropriate section of the
Workshop Repair Manual (see17C, LPG Injection, Introduction, Safety advice for all operations).
NOTESThere must be no present or stored faults.
Ignition on, engine stopped.
Check:
– the LPG tank solenoid valve (see DF013 Tank solenoid valve circuit),
– the general relay (see DF007 Main relay circuit),
– the LPG expansion valve solenoid valve (see DF103 LPG expansion valve solenoid valve),
– the LPG pressure sensor (see DF092 Expansion valve downstream pressure sensor circuit),
– the LPG pressure in the tank (see DF031 LPG pressure downstream of expansion valve).
These faults are detected by the LPG injection computer.
Repair or replace the faulty components, if necessary.
Check:
– the LPG filling hoses,
– the supply hoses upstream of the expansion valve,
– the expansion valve,
– the hoses downstream of the expansion valve.
Repair or replace the faulty components, if necessary.
If the status is still not correct, contact the Techline.
AFTER REPAIRRepeat the conformity check from the start.
S3000_V4C_ET067/S3000_V54_ET067
Page 191 of 230
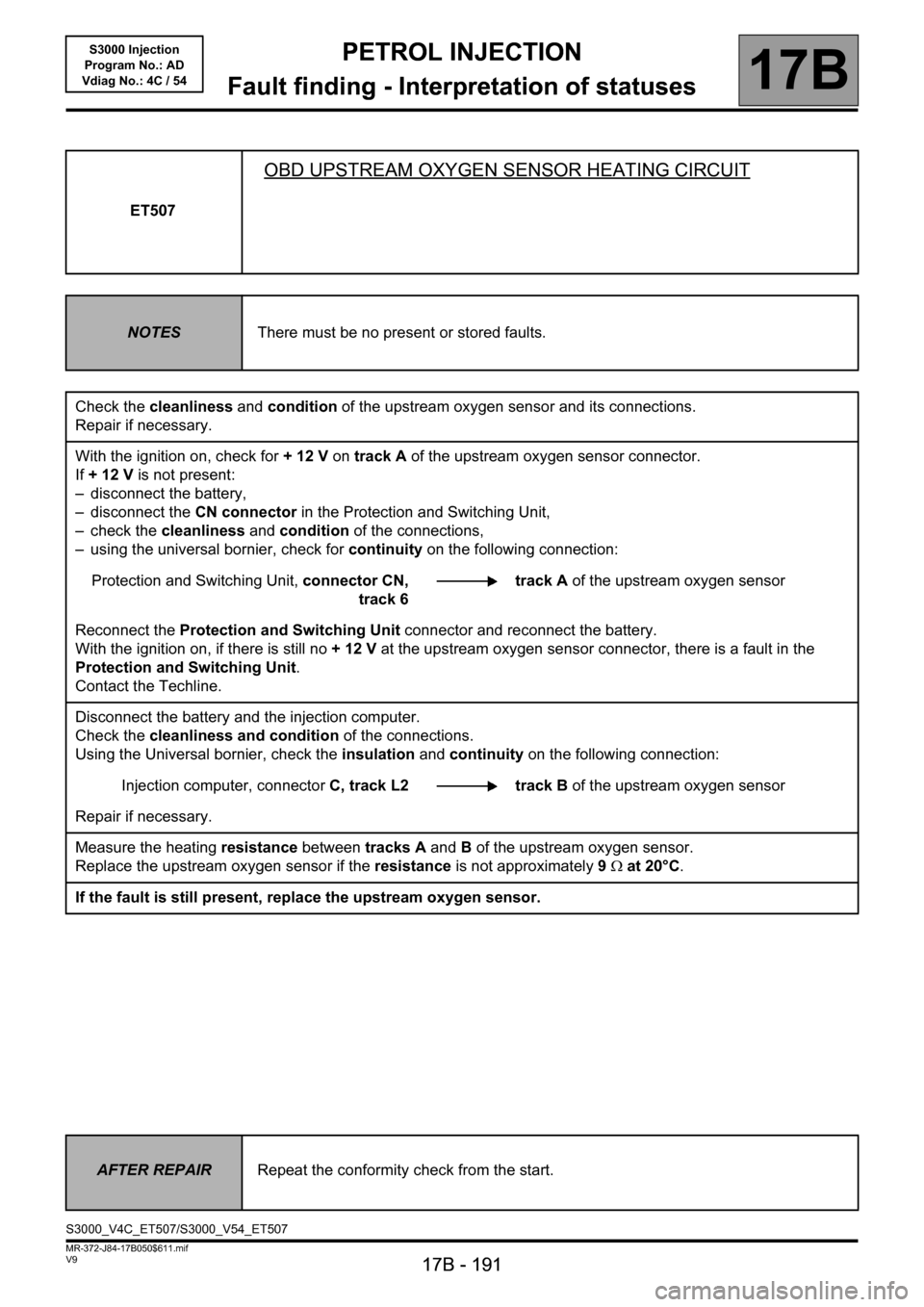
PETROL INJECTION
Fault finding - Interpretation of statuses
17B
17B - 191
PETROL INJECTION
Fault finding - Interpretation of statuses
17B
17B - 191V9 MR-372-J84-17B050$611.mif
S3000 Injection
Program No.: AD
Vdiag No.: 4C / 54
ET507
OBD UPSTREAM OXYGEN SENSOR HEATING CIRCUIT
NOTESThere must be no present or stored faults.
Check the cleanliness and condition of the upstream oxygen sensor and its connections.
Repair if necessary.
With the ignition on, check for + 12 V on track A of the upstream oxygen sensor connector.
If +12V is not present:
– disconnect the battery,
– disconnect the CN connector in the Protection and Switching Unit,
– check the cleanliness and condition of the connections,
– using the universal bornier, check for continuity on the following connection:
Protection and Switching Unit, connector CN,
track 6track A of the upstream oxygen sensor
Reconnect the Protection and Switching Unit connector and reconnect the battery.
With the ignition on, if there is still no +12V at the upstream oxygen sensor connector, there is a fault in the
Protection and Switching Unit.
Contact the Techline.
Disconnect the battery and the injection computer.
Check the cleanliness and condition of the connections.
Using the Universal bornier, check the insulation and continuity on the following connection:
Injection computer, connectorC, track L2 track B of the upstream oxygen sensor
Repair if necessary.
Measure the heating resistance between tracks A and B of the upstream oxygen sensor.
Replace the upstream oxygen sensor if the resistance is not approximately 9Ω at 20°C.
If the fault is still present, replace the upstream oxygen sensor.
AFTER REPAIRRepeat the conformity check from the start.
S3000_V4C_ET507/S3000_V54_ET507
Page 192 of 230
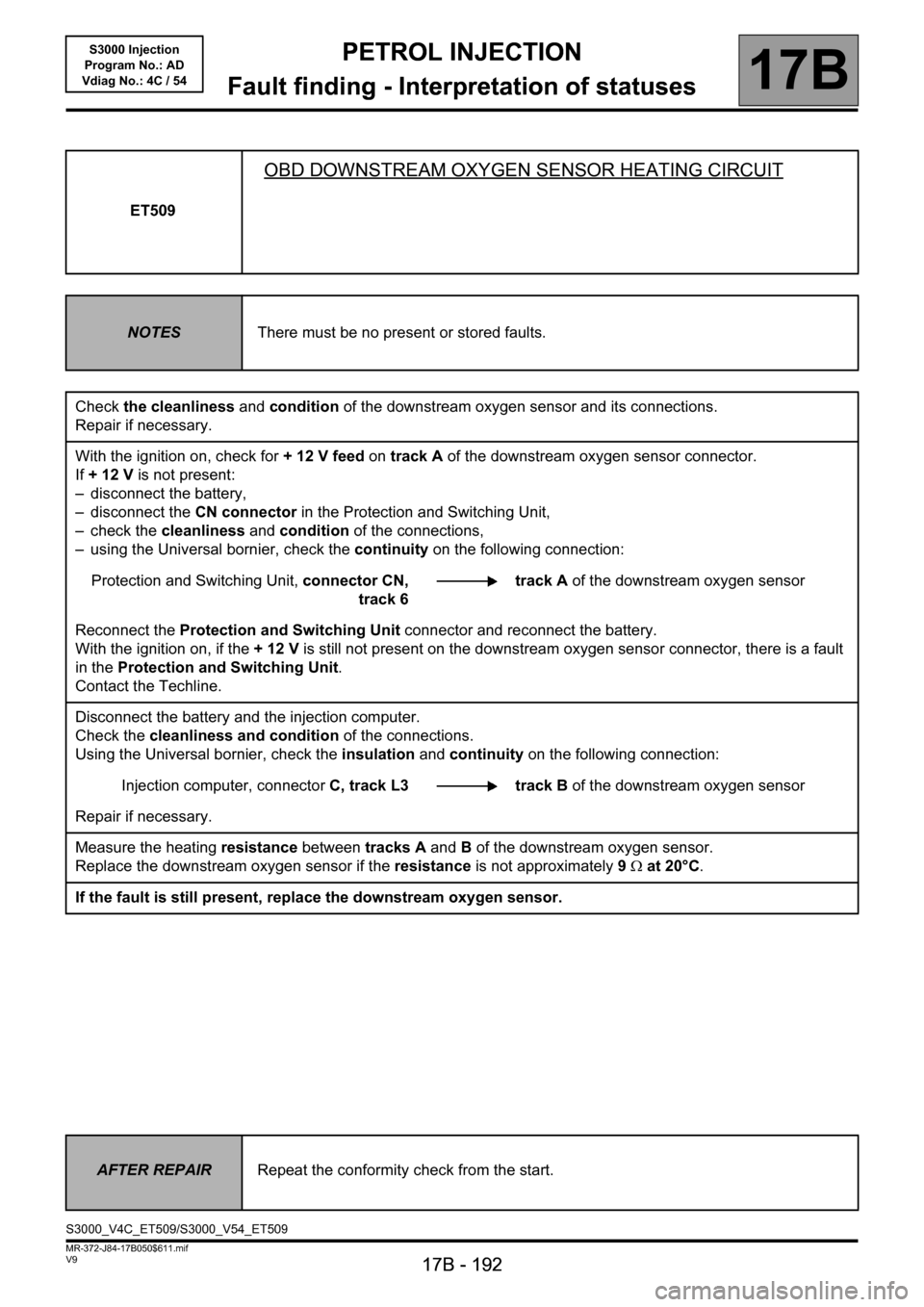
PETROL INJECTION
Fault finding - Interpretation of statuses
17B
17B - 192
PETROL INJECTION
Fault finding - Interpretation of statuses
17B
17B - 192V9 MR-372-J84-17B050$611.mif
S3000 Injection
Program No.: AD
Vdiag No.: 4C / 54
ET509
OBD DOWNSTREAM OXYGEN SENSOR HEATING CIRCUIT
NOTESThere must be no present or stored faults.
Check the cleanliness and condition of the downstream oxygen sensor and its connections.
Repair if necessary.
With the ignition on, check for + 12 V feed on track A of the downstream oxygen sensor connector.
If +12V is not present:
– disconnect the battery,
– disconnect the CN connector in the Protection and Switching Unit,
– check the cleanliness and condition of the connections,
– using the Universal bornier, check the continuity on the following connection:
Protection and Switching Unit, connector CN,
track 6track A of the downstream oxygen sensor
Reconnect the Protection and Switching Unit connector and reconnect the battery.
With the ignition on, if the +12V is still not present on the downstream oxygen sensor connector, there is a fault
in the Protection and Switching Unit.
Contact the Techline.
Disconnect the battery and the injection computer.
Check the cleanliness and condition of the connections.
Using the Universal bornier, check the insulation and continuity on the following connection:
Injection computer, connectorC, track L3 track B of the downstream oxygen sensor
Repair if necessary.
Measure the heating resistance between tracks A and B of the downstream oxygen sensor.
Replace the downstream oxygen sensor if the resistance is not approximately 9Ω at 20°C.
If the fault is still present, replace the downstream oxygen sensor.
AFTER REPAIRRepeat the conformity check from the start.
S3000_V4C_ET509/S3000_V54_ET509
Page 202 of 230
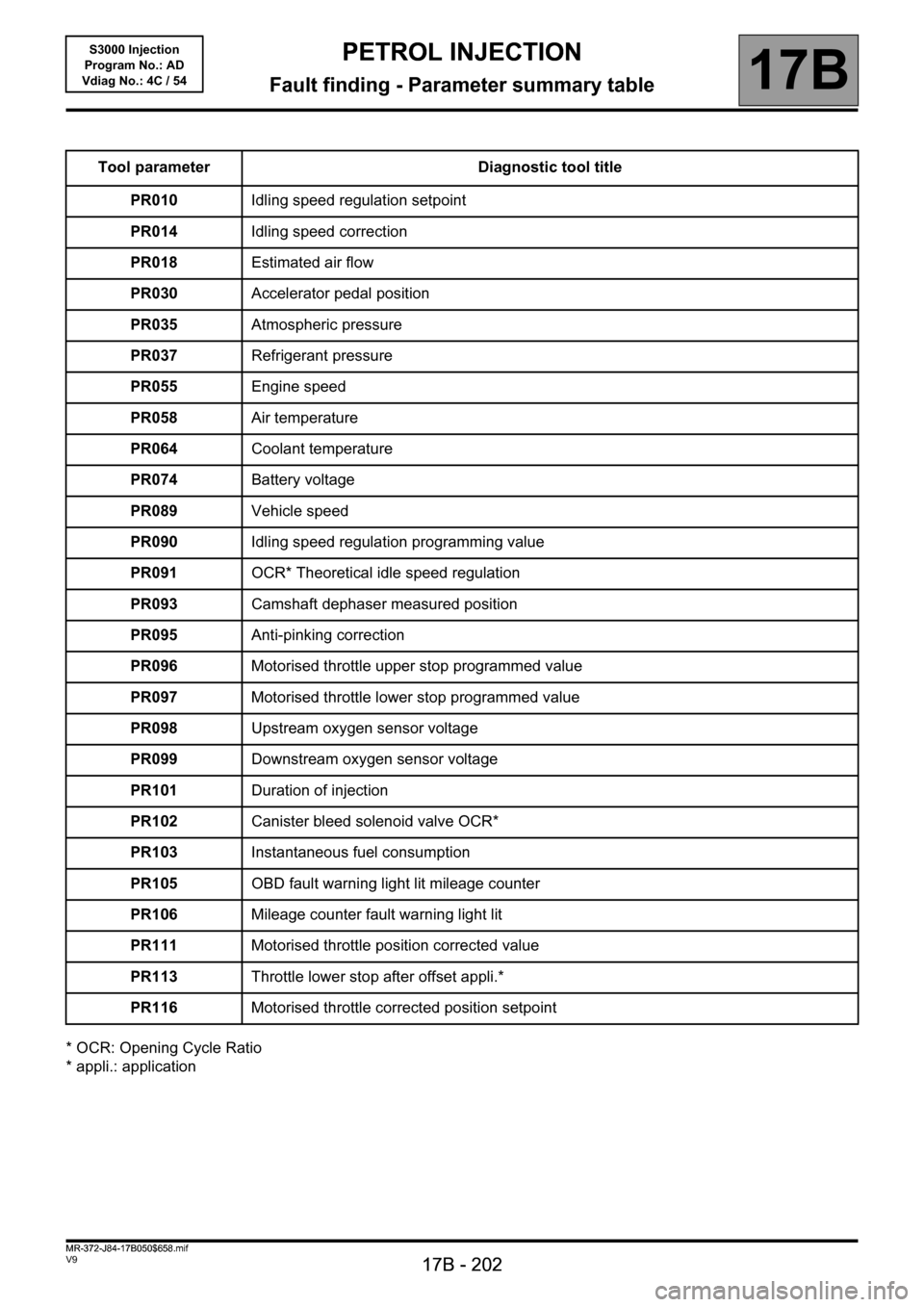
PETROL INJECTION
17B
17B - 202
17B
17B - 202V9 MR-372-J84-17B050$658.mif
S3000 Injection
Program No.: AD
Vdiag No.: 4C / 54PETROL INJECTION
Fault finding - Parameter summary table
* OCR: Opening Cycle Ratio
* appli.: applicationTool parameter Diagnostic tool title
PR010Idling speed regulation setpoint
PR014Idling speed correction
PR018Estimated air flow
PR030Accelerator pedal position
PR035Atmospheric pressure
PR037Refrigerant pressure
PR055Engine speed
PR058Air temperature
PR064Coolant temperature
PR074Battery voltage
PR089Vehicle speed
PR090Idling speed regulation programming value
PR091OCR* Theoretical idle speed regulation
PR093Camshaft dephaser measured position
PR095Anti-pinking correction
PR096Motorised throttle upper stop programmed value
PR097Motorised throttle lower stop programmed value
PR098Upstream oxygen sensor voltage
PR099Downstream oxygen sensor voltage
PR101Duration of injection
PR102Canister bleed solenoid valve OCR*
PR103Instantaneous fuel consumption
PR105OBD fault warning light lit mileage counter
PR106Mileage counter fault warning light lit
PR111Motorised throttle position corrected value
PR113Throttle lower stop after offset appli.*
PR116Motorised throttle corrected position setpoint
MR-372-J84-17B050$658.mif
Page 205 of 230
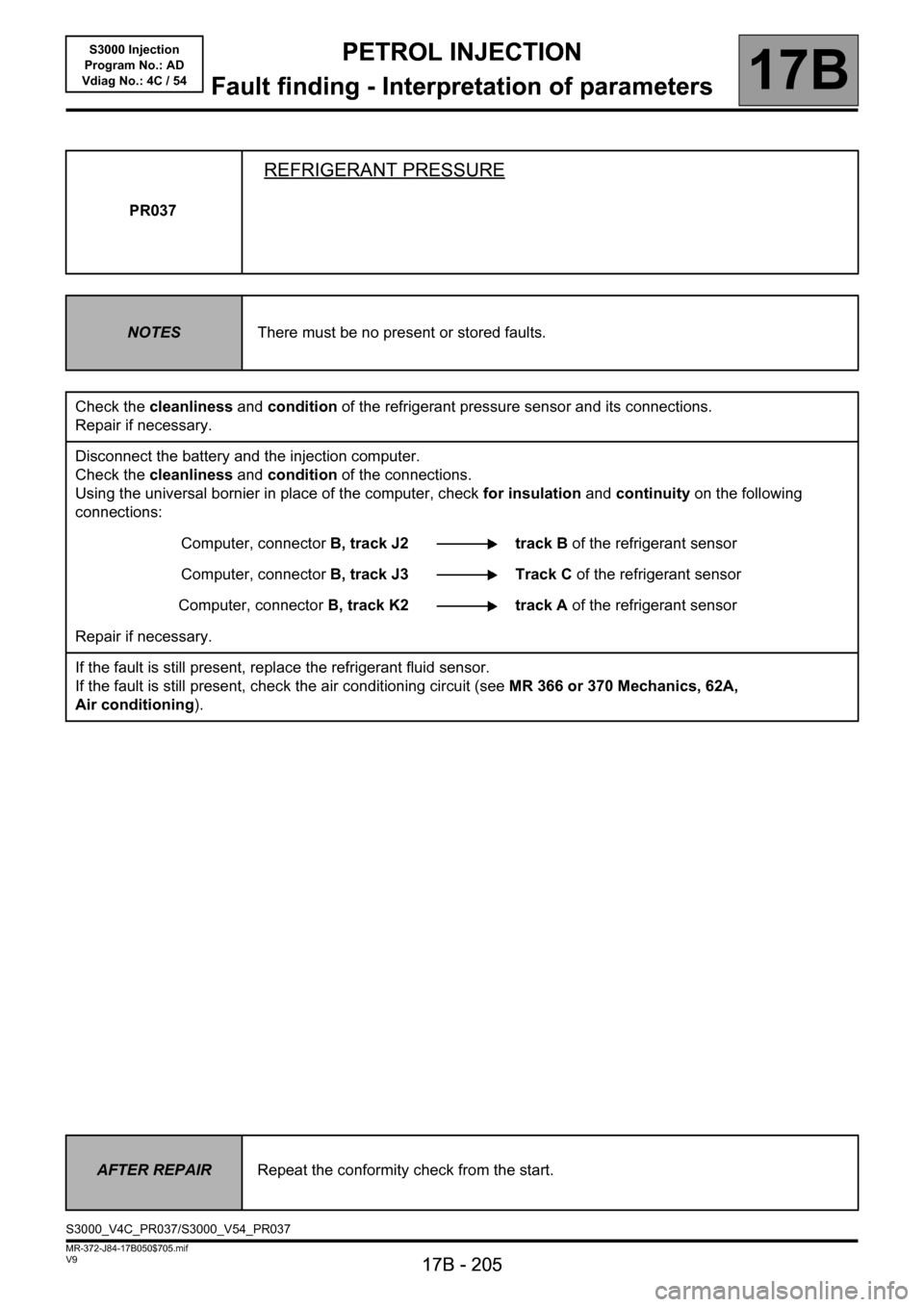
PETROL INJECTION
Fault finding - Interpretation of parameters
17B
17B - 205
PETROL INJECTION
Fault finding - Interpretation of parameters
17B
17B - 205V9 MR-372-J84-17B050$705.mif
S3000 Injection
Program No.: AD
Vdiag No.: 4C / 54
PR037
REFRIGERANT PRESSURE
NOTESThere must be no present or stored faults.
Check the cleanliness and condition of the refrigerant pressure sensor and its connections.
Repair if necessary.
Disconnect the battery and the injection computer.
Check the cleanliness and condition of the connections.
Using the universal bornier in place of the computer, check for insulation and continuity on the following
connections:
Computer, connectorB, track J2 track B of the refrigerant sensor
Computer, connectorB, track J3 Track C of the refrigerant sensor
Computer, connectorB, track K2 track A of the refrigerant sensor
Repair if necessary.
If the fault is still present, replace the refrigerant fluid sensor.
If the fault is still present, check the air conditioning circuit (see MR 366 or 370 Mechanics, 62A,
Air conditioning).
AFTER REPAIRRepeat the conformity check from the start.
S3000_V4C_PR037/S3000_V54_PR037
Page 207 of 230
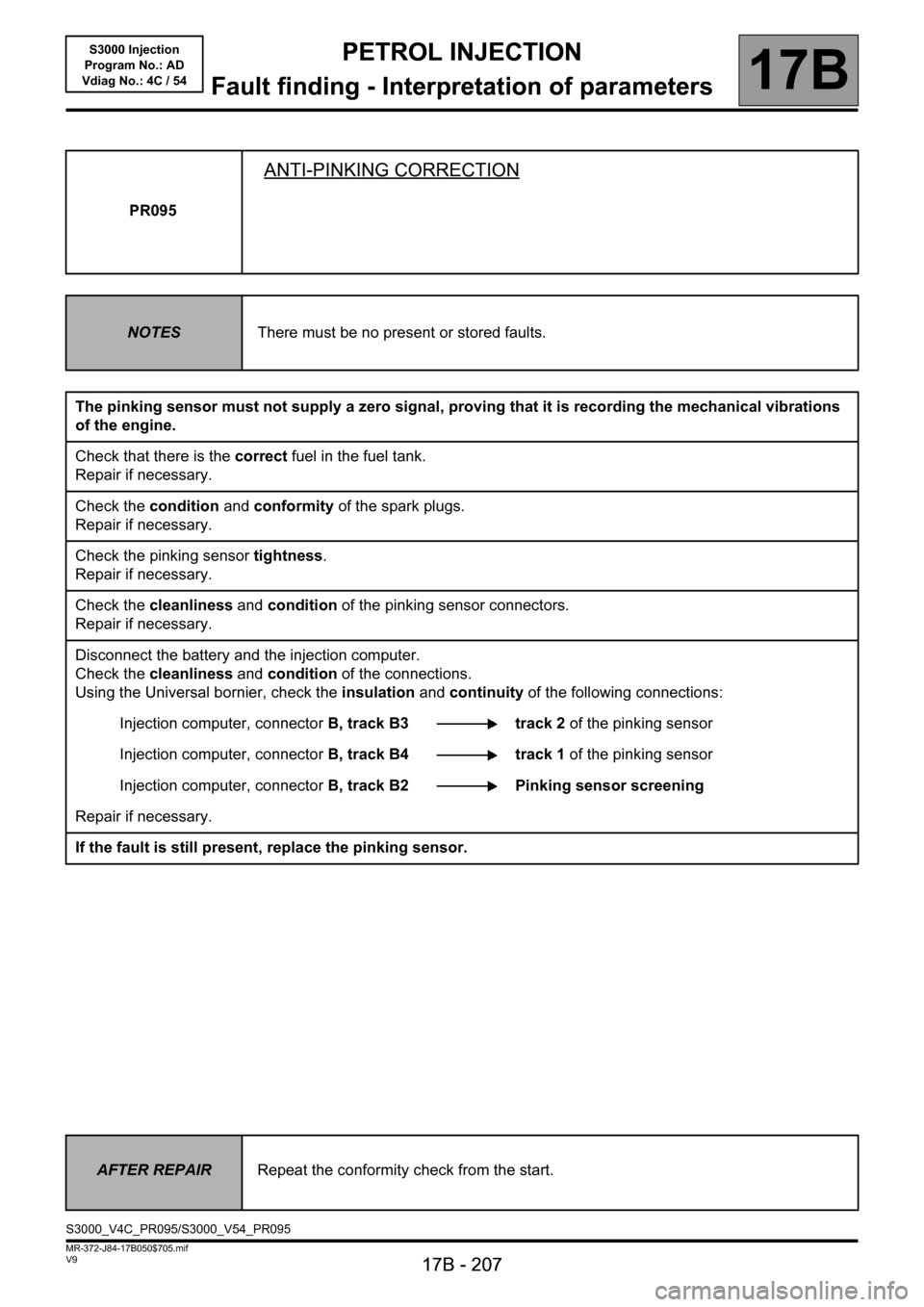
PETROL INJECTION
Fault finding - Interpretation of parameters
17B
17B - 207
PETROL INJECTION
Fault finding - Interpretation of parameters
17B
17B - 207V9 MR-372-J84-17B050$705.mif
S3000 Injection
Program No.: AD
Vdiag No.: 4C / 54
PR095
ANTI-PINKING CORRECTION
NOTESThere must be no present or stored faults.
The pinking sensor must not supply a zero signal, proving that it is recording the mechanical vibrations
of the engine.
Check that there is the correct fuel in the fuel tank.
Repair if necessary.
Check the condition and conformity of the spark plugs.
Repair if necessary.
Check the pinking sensor tightness.
Repair if necessary.
Check the cleanliness and condition of the pinking sensor connectors.
Repair if necessary.
Disconnect the battery and the injection computer.
Check the cleanliness and condition of the connections.
Using the Universal bornier, check the insulation and continuity of the following connections:
Injection computer, connectorB, track B3 track 2 of the pinking sensor
Injection computer, connectorB, track B4 track 1 of the pinking sensor
Injection computer, connectorB, track B2 Pinking sensor screening
Repair if necessary.
If the fault is still present, replace the pinking sensor.
AFTER REPAIRRepeat the conformity check from the start.
S3000_V4C_PR095/S3000_V54_PR095
Page 208 of 230
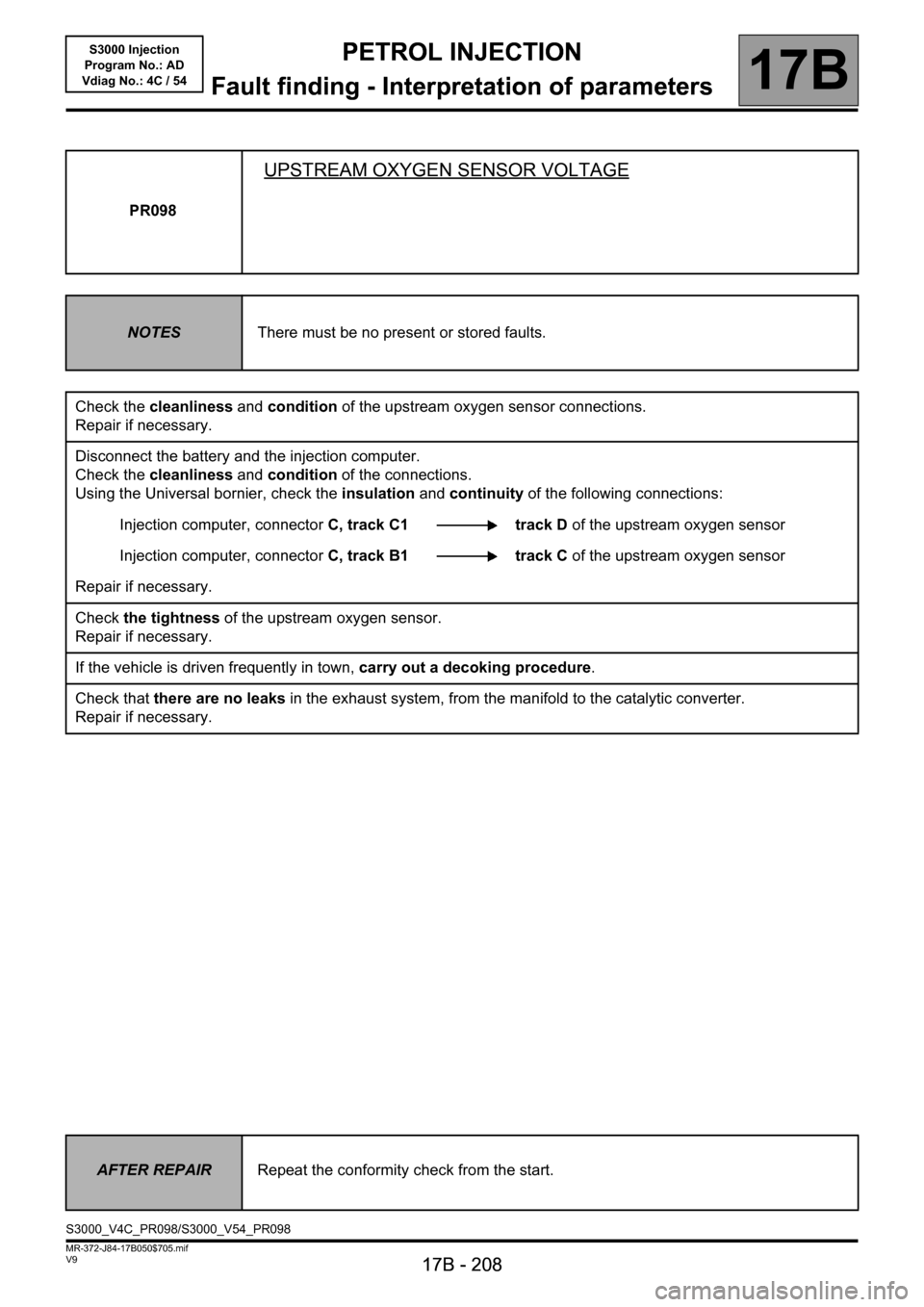
PETROL INJECTION
Fault finding - Interpretation of parameters
17B
17B - 208
PETROL INJECTION
Fault finding - Interpretation of parameters
17B
17B - 208V9 MR-372-J84-17B050$705.mif
S3000 Injection
Program No.: AD
Vdiag No.: 4C / 54
PR098
UPSTREAM OXYGEN SENSOR VOLTAGE
NOTESThere must be no present or stored faults.
Check the cleanliness and condition of the upstream oxygen sensor connections.
Repair if necessary.
Disconnect the battery and the injection computer.
Check the cleanliness and condition of the connections.
Using the Universal bornier, check the insulation and continuity of the following connections:
Injection computer, connectorC, track C1 track D of the upstream oxygen sensor
Injection computer, connectorC, track B1 track C of the upstream oxygen sensor
Repair if necessary.
Check the tightness of the upstream oxygen sensor.
Repair if necessary.
If the vehicle is driven frequently in town, carry out a decoking procedure.
Check that there are no leaks in the exhaust system, from the manifold to the catalytic converter.
Repair if necessary.
AFTER REPAIRRepeat the conformity check from the start.
S3000_V4C_PR098/S3000_V54_PR098
Page 209 of 230

PETROL INJECTION
Fault finding - Interpretation of parameters
17B
17B - 209
PETROL INJECTION
Fault finding - Interpretation of parameters
17B
17B - 209V9 MR-372-J84-17B050$705.mif
S3000 Injection
Program No.: AD
Vdiag No.: 4C / 54
PR098
CONTINUED
If the fault is still present, replace the upstream oxygen sensor.
If the fault has still not been cured, continue with the checks.
Check:
– the condition of the air filter,
– that the air inlet circuit is not blocked,
– the condition and conformity of the spark plugs,
– that the catalytic converter is not clogged,
– the sealing between the throttle valve and inlet manifold,
– the manifold pressure sensor sealing,
– the fuel vapour absorber bleed, which must not be jammed open,'
– the fuel vapour absorber bleed system sealing,
– the brake servo system sealing,
– the cylinder head oil vapour recovery system sealing,
– the sealing between the inlet manifold and cylinder head,
– the exhaust pipe sealing between the cylinder head and catalytic converter.
– the fuel flow rate and pressure.
If the idle speed is not stable, check:
– the timing adjustment,
– the hydraulic tappets if there is camshaft noise (see MR 364 or 370 Mechanics, 11A, Top and front of engine),
– the cylinder compressions.
Drive the vehicle to check the repair.
AFTER REPAIRRepeat the conformity check from the start.