Page 1 of 230
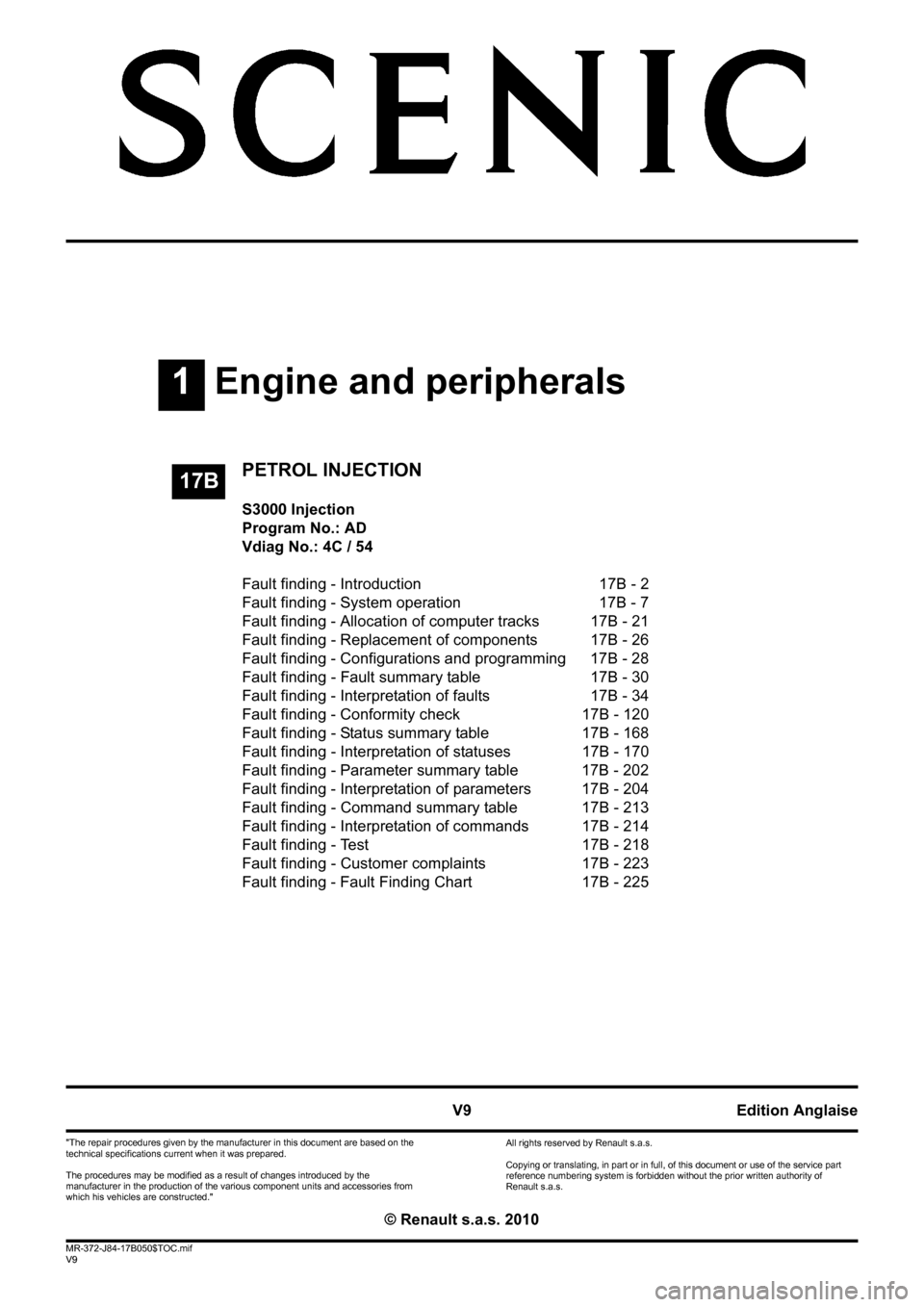
1Engine and peripherals
V9 MR-372-J84-17B050$TOC.mif
V9
17B
"The repair procedures given by the manufacturer in this document are based on the
technical specifications current when it was prepared.
The procedures may be modified as a result of changes introduced by the
manufacturer in the production of the various component units and accessories from
which his vehicles are constructed."
V9
All rights reserved by Renault s.a.s.
Edition Anglaise
Copying or translating, in part or in full, of this document or use of the service part
reference numbering system is forbidden without the prior written authority of
Renault s.a.s.
© Renault s.a.s. 2010
PETROL INJECTION
S3000 Injection
Program No.: AD
Vdiag No.: 4C / 54
Fault finding - Introduction 17B - 2
Fault finding - System operation 17B - 7
Fault finding - Allocation of computer tracks 17B - 21
Fault finding - Replacement of components 17B - 26
Fault finding - Configurations and programming 17B - 28
Fault finding - Fault summary table 17B - 30
Fault finding - Interpretation of faults 17B - 34
Fault finding - Conformity check 17B - 120
Fault finding - Status summary table 17B - 168
Fault finding - Interpretation of statuses 17B - 170
Fault finding - Parameter summary table 17B - 202
Fault finding - Interpretation of parameters 17B - 204
Fault finding - Command summary table 17B - 213
Fault finding - Interpretation of commands 17B - 214
Fault finding - Test 17B - 218
Fault finding - Customer complaints 17B - 223
Fault finding - Fault Finding Chart 17B - 225
Page 19 of 230
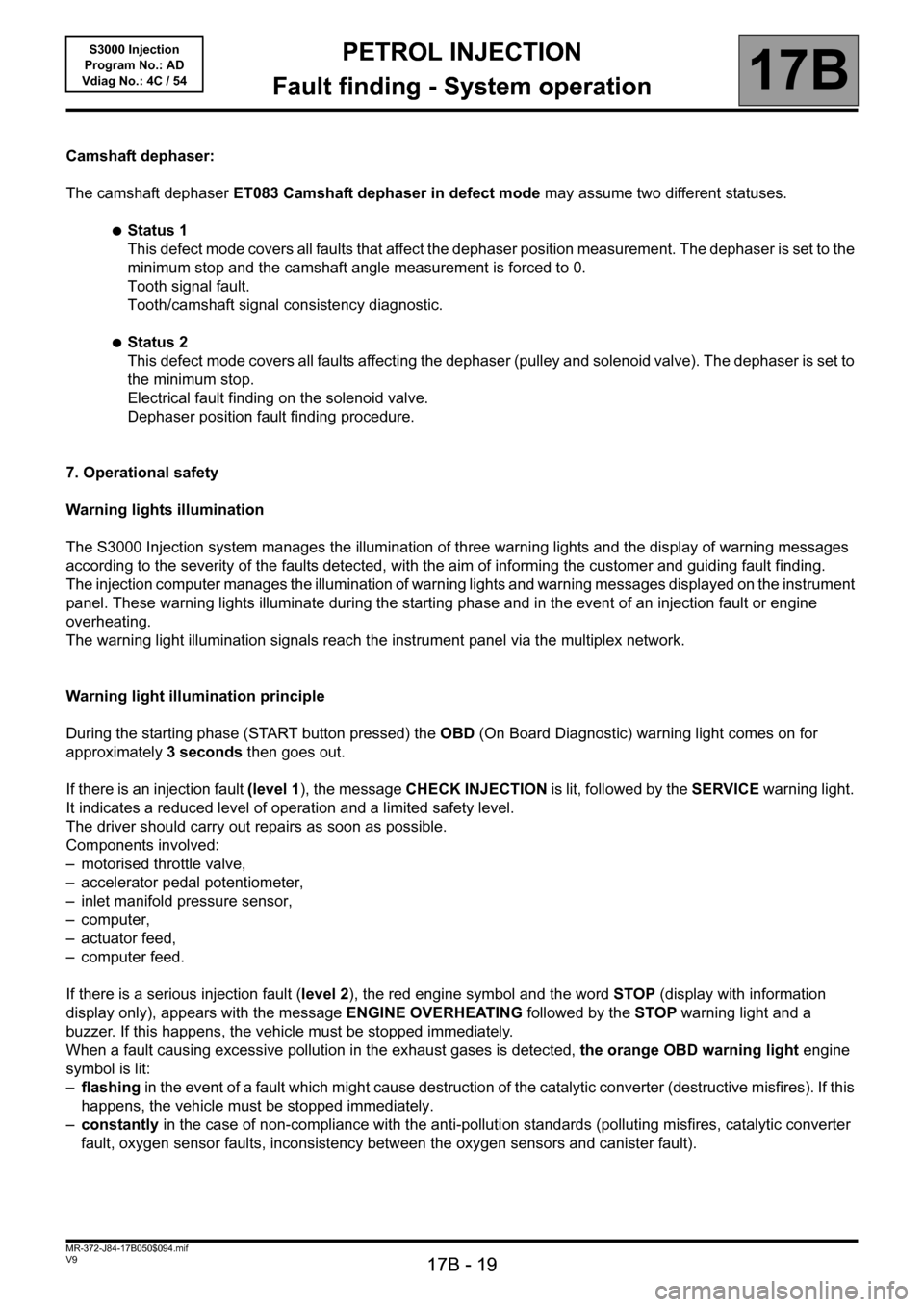
PETROL INJECTION
Fault finding - System operation
17B
17B - 19
PETROL INJECTION
Fault finding - System operation
17B
17B - 19V9 MR-372-J84-17B050$094.mif
S3000 Injection
Program No.: AD
Vdiag No.: 4C / 54
Camshaft dephaser:
The camshaft dephaser ET083 Camshaft dephaser in defect mode may assume two different statuses.
●Status 1
This defect mode covers all faults that affect the dephaser position measurement. The dephaser is set to the
minimum stop and the camshaft angle measurement is forced to 0.
Tooth signal fault.
Tooth/camshaft signal consistency diagnostic.
●Status 2
This defect mode covers all faults affecting the dephaser (pulley and solenoid valve). The dephaser is set to
the minimum stop.
Electrical fault finding on the solenoid valve.
Dephaser position fault finding procedure.
7. Operational safety
Warning lights illumination
The S3000 Injection system manages the illumination of three warning lights and the display of warning messages
according to the severity of the faults detected, with the aim of informing the customer and guiding fault finding.
The injection computer manages the illumination of warning lights and warning messages displayed on the instrument
panel. These warning lights illuminate during the starting phase and in the event of an injection fault or engine
overheating.
The warning light illumination signals reach the instrument panel via the multiplex network.
Warning light illumination principle
During the starting phase (START button pressed) the OBD (On Board Diagnostic) warning light comes on for
approximately 3 seconds then goes out.
If there is an injection fault (level 1), the message CHECK INJECTION is lit, followed by the SERVICE warning light.
It indicates a reduced level of operation and a limited safety level.
The driver should carry out repairs as soon as possible.
Components involved:
– motorised throttle valve,
– accelerator pedal potentiometer,
– inlet manifold pressure sensor,
– computer,
– actuator feed,
– computer feed.
If there is a serious injection fault (level 2), the red engine symbol and the word STOP (display with information
display only), appears with the message ENGINE OVERHEATING followed by the STOP warning light and a
buzzer. If this happens, the vehicle must be stopped immediately.
When a fault causing excessive pollution in the exhaust gases is detected, the orange OBD warning light engine
symbol is lit:
–flashing in the event of a fault which might cause destruction of the catalytic converter (destructive misfires). If this
happens, the vehicle must be stopped immediately.
–constantly in the case of non-compliance with the anti-pollution standards (polluting misfires, catalytic converter
fault, oxygen sensor faults, inconsistency between the oxygen sensors and canister fault).
Page 211 of 230
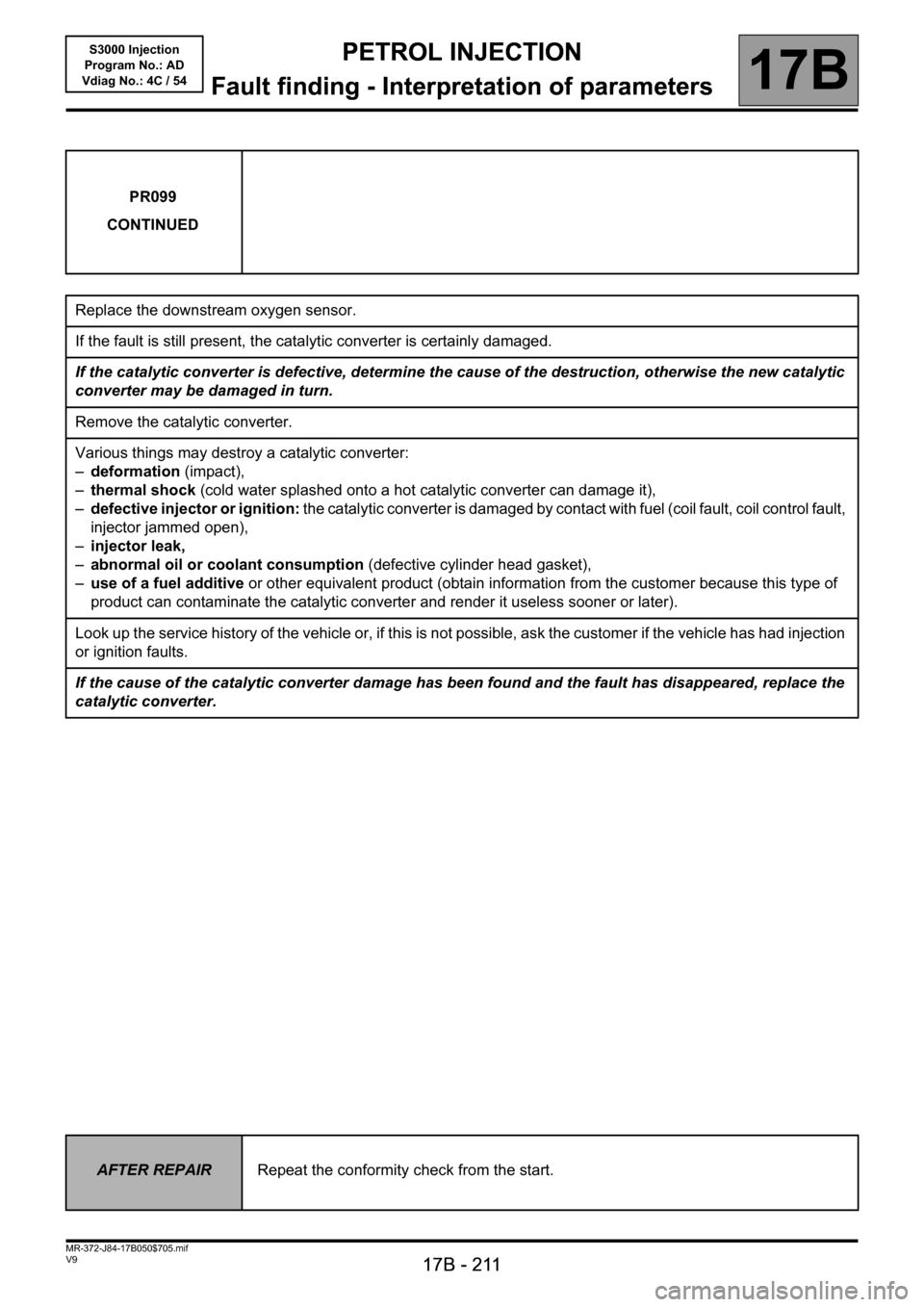
PETROL INJECTION
Fault finding - Interpretation of parameters
17B
17B - 211
PETROL INJECTION
Fault finding - Interpretation of parameters
17B
17B - 211V9 MR-372-J84-17B050$705.mif
S3000 Injection
Program No.: AD
Vdiag No.: 4C / 54
PR099
CONTINUED
Replace the downstream oxygen sensor.
If the fault is still present, the catalytic converter is certainly damaged.
If the catalytic converter is defective, determine the cause of the destruction, otherwise the new catalytic
converter may be damaged in turn.
Remove the catalytic converter.
Various things may destroy a catalytic converter:
–deformation (impact),
–thermal shock (cold water splashed onto a hot catalytic converter can damage it),
–defective injector or ignition: the catalytic converter is damaged by contact with fuel (coil fault, coil control fault,
injector jammed open),
–injector leak,
–abnormal oil or coolant consumption (defective cylinder head gasket),
–use of a fuel additive or other equivalent product (obtain information from the customer because this type of
product can contaminate the catalytic converter and render it useless sooner or later).
Look up the service history of the vehicle or, if this is not possible, ask the customer if the vehicle has had injection
or ignition faults.
If the cause of the catalytic converter damage has been found and the fault has disappeared, replace the
catalytic converter.
AFTER REPAIRRepeat the conformity check from the start.