Page 2 of 54
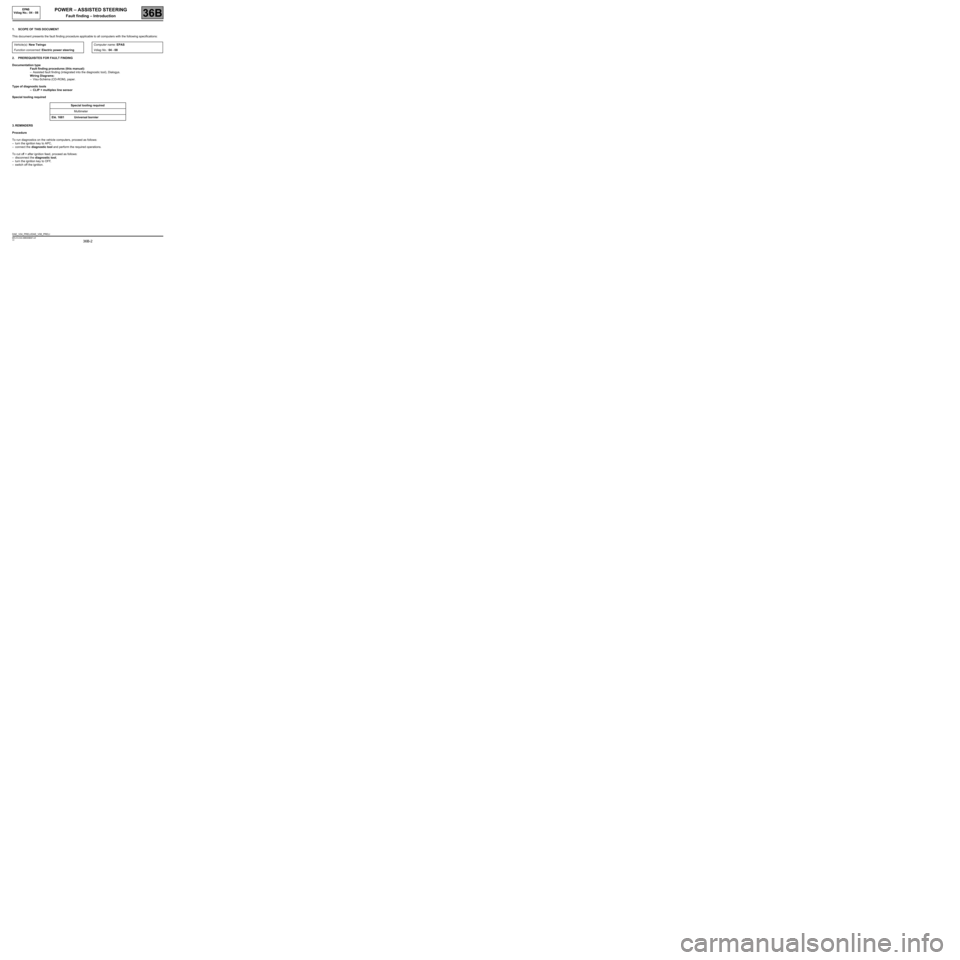
36B-2
MR-413-X44-36B000$067.mif
V2
36B
POWER – ASSISTED STEERING
Fault finding – Introduction
1. SCOPE OF THIS DOCUMENT
This document presents the fault finding procedure applicable to all computers with the following specifications:
2. PREREQUISITES FOR FAULT FINDING
Documentation type
Fault finding procedures (this manual):
–Assisted fault finding (integrated into the diagnostic tool), Dialogys.
Wiring Diagrams:
–Visu-Schéma (CD-ROM), paper.
Type of diagnostic tools
–CLIP + multiplex line sensor
Special tooling required
3. REMINDERS
Procedure
To run diagnostics on the vehicle computers, proceed as follows:
–turn the ignition key to APC,
–connect the diagnostic tool and perform the required operations.
To cut off + after ignition feed, proceed as follows:
–disconnect the diagnostic tool,
–turn the ignition key to OFF,
–switch off the ignition. Vehicle(s): New Twingo
Function concerned: Electric power steeringComputer name: EPAS
Vdiag No.: 04 - 08
Special tooling required
Multimeter
Elé. 1681 Universal bornier
DAE_V04_PRELI/DAE_V08_PRELI
EPAS
Vdiag No.: 04 - 08
MR-413-X44-36B000$067.mif
Page 7 of 54
36B-7
MR-413-X44-36B000$134.mif
V2
36B
POWER – ASSISTED STEERING
Fault finding – List and location of components
Figure 1: Computer and motor
1Engine
2Computer
Figure 2: Torque sensor and column adjustment handle
1Torque sensor
2Computer
3Column adjustment handle
1
2
3 1
2
EPAS
Vdiag No.: 04 - 08
MR-413-X44-36B000$134.mif
Page 8 of 54
36B-8
MR-413-X44-36B000$134.mif
V2
EPAS
Vdiag No.: 04 - 08POWER – ASSISTED STEERING
Fault finding – List and location of components36B
Figure 3: Computer, Angle sensor and Motor
1Computer
2Angle sensor (on for Vdiag 04)
3Engine
31
2
Page 9 of 54
36B-9
MR-413-X44-36B000$201.mif
V2
36B
POWER – ASSISTED STEERING
Fault finding – Role of components
Angle sensor:
This sensor indicates the position of the steering wheel in real time (only for Vdiag 04).
Torque sensor:
This sensor enables the assistance torque to be controlled according to the force applied to the steering wheel by
the driver.
Computer:
This computer calculates the level of steering assistance required according to various parameters, including the
vehicle speed and the steering wheel torque.
Motor:
The motor provides the necessary steering torque assistance according to driver requirements. EPAS
Vdiag No.: 04 - 08
MR-413-X44-36B000$201.mif
Page 10 of 54
36B-10
MR-413-X44-36B000$268.mif
V2
36B
POWER – ASSISTED STEERING
Fault finding – Function
Column steering system
1Computer
2Computer supply
3+ after ignition feed
4Vehicle speed
5Engine speed
6K line
7Fault warning light
8+ torque sensor
9Main signal
10 Secondary signal
11 0 V
12 + angle sensor (only in Vdiag 04)
13 Signal 1 (only in Vdiag 04)
14 Signal 2 (only in Vdiag 04)
15 0 V (only in Vdiag 04)
16 Brush motor supply
17 Power-assisted steering motor
18 Torque sensor
19 Angle sensor (only in Vdiag 04)
EPAS
Vdiag No.: 04 - 08
MR-413-X44-36B000$268.mif
Page 11 of 54
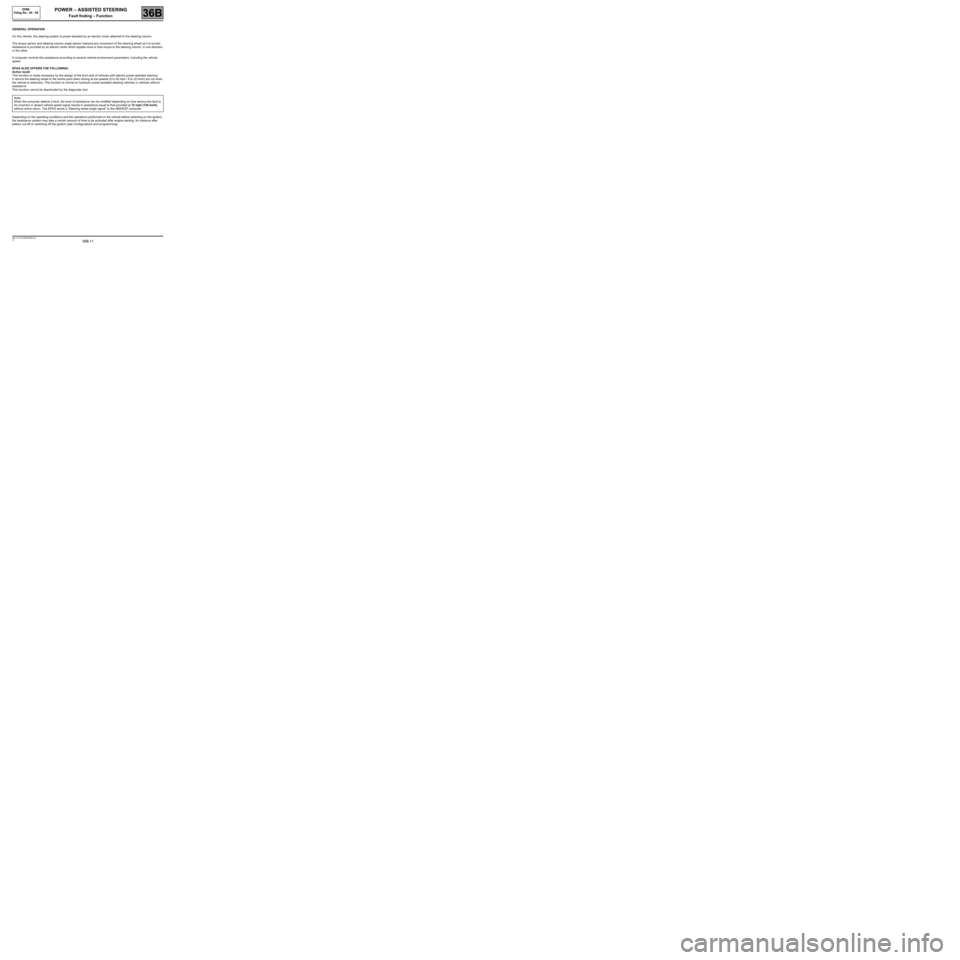
36B-11
MR-413-X44-36B000$268.mif
V2
POWER – ASSISTED STEERING
Fault finding – Function
EPAS
Vdiag No.: 04 - 08
36B
GENERAL OPERATION
On this vehicle, the steering system is power-assisted by an electric motor attached to the steering column.
The torque sensor and steering column angle sensor interpret any movement of the steering wheel as it is turned.
Assistance is provided by an electric motor which applies more or less torque to the steering column, in one direction
or the other.
A computer controls this assistance according to several vehicle environment parameters, including the vehicle
speed.
EPAS ALSO OFFERS THE FOLLOWING:
Active recall:
This function is made necessary by the design of the front axle of vehicles with electric power-assisted steering.
It returns the steering wheel to the centre point when driving at low speeds (5 to 20 mph / 8 to 32 km/h) but not when
the vehicle is stationary. This function is normal on hydraulic power-assisted steering vehicles or vehicles without
assistance.
This function cannot be deactivated by the diagnostic tool.
Depending on the operating conditions and the operations performed on the vehicle before switching on the ignition,
the assistance system may take a certain amount of time to be activated after engine starting, for instance after
battery cut-off or switching off the ignition (see Configurations and programming).Note:
When the computer detects a fault, the level of assistance can be modified depending on how serious the fault is.
An incorrect or absent vehicle speed signal results in assistance equal to that provided at 72 mph (120 km/h)
without active return. The EPAS sends a "Steering wheel angle signal" to the ABS/ESP computer.
Page 13 of 54
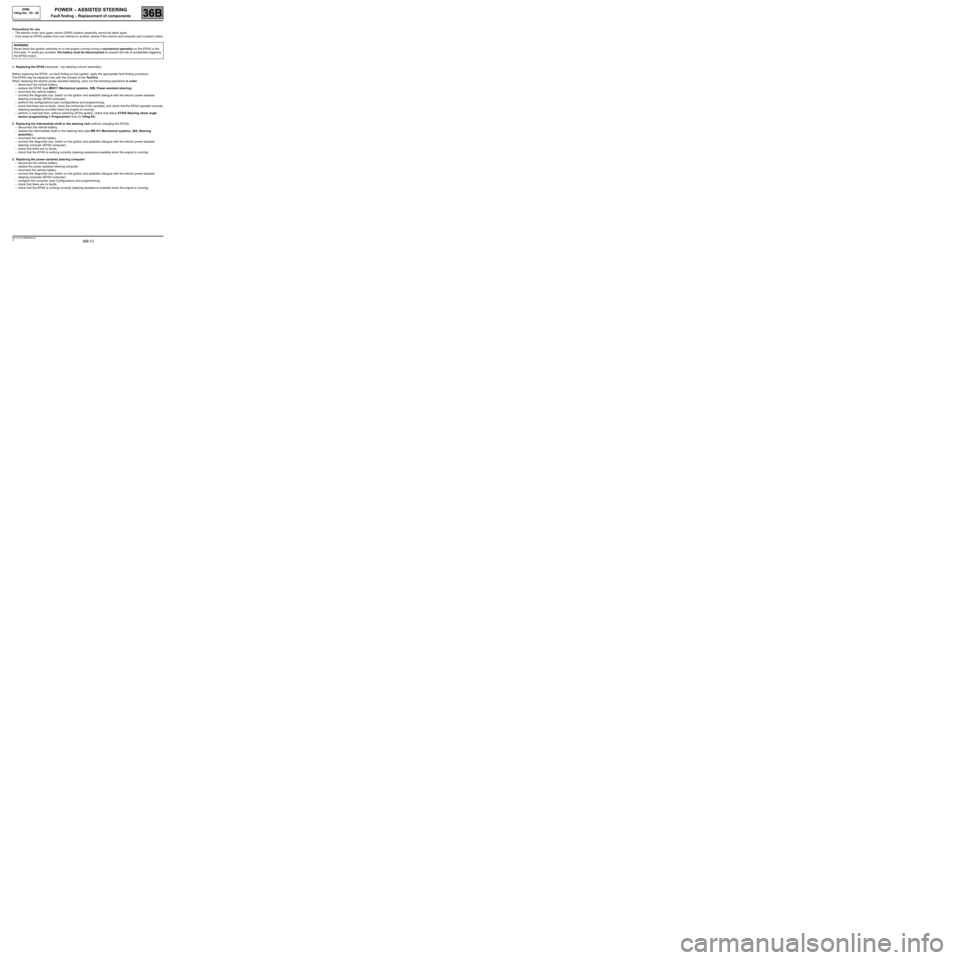
36B-13
MR-413-X44-36B000$335.mif
V2
36B
POWER – ASSISTED STEERING
Fault finding – Replacement of components
Precautions for use
–The electric motor and upper column (EPAS system) assembly cannot be taken apart.
–Only reuse an EPAS system from one vehicle on another vehicle if the column and computer part numbers match.
A. Replacing the EPAS (computer - top steering column assembly):
Before replacing the EPAS, run fault finding on the system: apply the appropriate fault finding procedure.
The EPAS may be replaced only with the consent of the Techline.
When replacing the electric power assisted steering, carry out the following operations in order:
–disconnect the vehicle battery,
–replace the EPAS (see MR411 Mechanical systems, 36B, Power-assisted steering),
–reconnect the vehicle battery,
–connect the diagnostic tool, switch on the ignition and establish dialogue with the electric power-assisted
steering computer (EPAS computer),
–perform the configurations (see Configurations and programming),
–check that there are no faults, check the conformity of the variables, and check that the EPAS operates correctly
(steering assistance provided when the engine is running),
–perform a road test then, without switching off the ignition, check that status ET020 Steering wheel angle
sensor programming is Programmed (only for Vdiag 04).
B. Replacing the intermediate shaft or the steering rack (without changing the EPAS):
–disconnect the vehicle battery,
–replace the intermediate shaft or the steering rack (see MR 411 Mechanical systems, 36A, Steering
assembly),
–reconnect the vehicle battery,
–connect the diagnostic tool, switch on the ignition and establish dialogue with the electric power-assisted
steering computer (EPAS computer),
–check that there are no faults,
–check that the EPAS is working correctly (steering assistance available when the engine is running).
C. Replacing the power-assisted steering computer:
–disconnect the vehicle battery,
–replace the power-assisted steering computer,
–reconnect the vehicle battery,
–connect the diagnostic tool, switch on the ignition and establish dialogue with the electric power-assisted
steering computer (EPAS computer),
–configure the computer (see Configurations and programming),
–check that there are no faults,
–check that the EPAS is working correctly (steering assistance available when the engine is running). WARNING
Never leave the ignition switched on or the engine running during a mechanical operation on the EPAS or the
front axle. To avoid any accident, the battery must be disconnected (to prevent the risk of accidentally triggering
the EPAS motor).
EPAS
Vdiag No.: 04 - 08
MR-413-X44-36B000$335.mif
Page 14 of 54
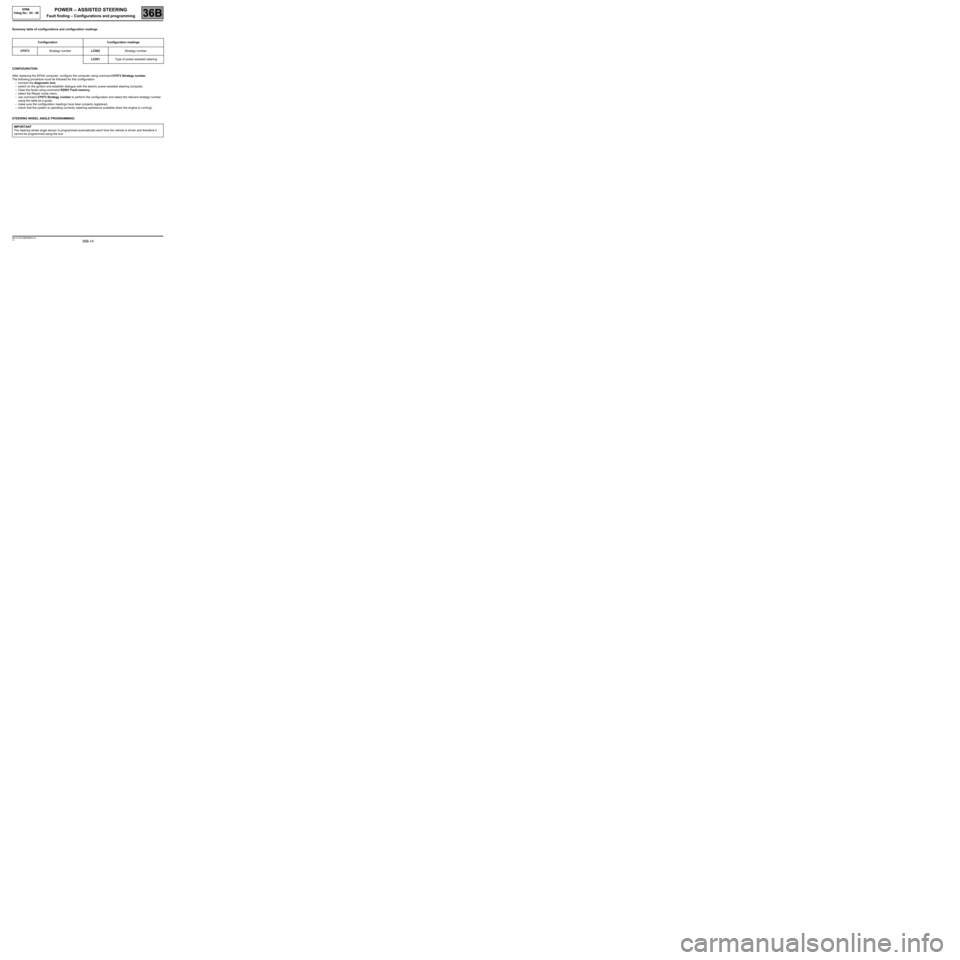
36B-14
MR-413-X44-36B000$402.mif
V2
36B
POWER – ASSISTED STEERING
Fault finding – Configurations and programming
Summary table of configurations and configuration readings
CONFIGURATION:
After replacing the EPAS computer, configure the computer using command CF073 Strategy number.
The following procedure must be followed for this configuration:
–connect the diagnostic tool,
–switch on the ignition and establish dialogue with the electric power-assisted steering computer,
–Clear the faults using command RZ001 Fault memory.
–select the Repair mode menu,
–use command CF073 Strategy number to perform the configuration and select the relevant strategy number
using the table as a guide,
–make sure the configuration readings have been properly registered,
–check that the system is operating correctly (steering assistance available when the engine is running).
STEERING WHEEL ANGLE PROGRAMMING:Configuration Configuration readings
CF073Strategy numberLC002Strategy number
LC001Type of power-assisted steering
IMPORTANT
The steering wheel angle sensor is programmed automatically each time the vehicle is driven and therefore it
cannot be programmed using the tool.
EPAS
Vdiag No.: 04 - 08
MR-413-X44-36B000$402.mif