Page 590 of 4171
PREPARATIONBRC-113
< PREPARATION > [VDC/TCS/ABS]
C
D
E
G H
I
J
K L
M A
B
BRC
N
O P
PREPARATION
PREPARATION
Special Service ToolINFOID:0000000003772635
The actual shapes of Kent-Moore tools may differ from those of special service tools illustrated here.
Commercial Service ToolINFOID:0000000003772636
Tool number
(Kent-Moore No.)
Tool name Description
KV991J0080
(J-45741)
ABS active wheel sensor tester Checking operation of ABS active wheel sen-
sors
WFIA0101E
Tool name
Description
1. Flare nut crowfoot
2. Torque wrench Removing and installing brake piping
a: 10 mm (0.39 in)/12 mm (0.47 in)
S-NT360
Revision: December 20092009 QX56
Page 591 of 4171
![INFINITI QX56 2009 Factory Service Manual BRC-114
< REMOVAL AND INSTALLATION >[VDC/TCS/ABS]
WHEEL SENSORS
REMOVAL AND INSTALLATION
WHEEL SENSORS
Removal and InstallationINFOID:0000000003772637
REMOVAL
1. Remove wheel sensor bolt.
• When rem INFINITI QX56 2009 Factory Service Manual BRC-114
< REMOVAL AND INSTALLATION >[VDC/TCS/ABS]
WHEEL SENSORS
REMOVAL AND INSTALLATION
WHEEL SENSORS
Removal and InstallationINFOID:0000000003772637
REMOVAL
1. Remove wheel sensor bolt.
• When rem](/manual-img/42/57031/w960_57031-590.png)
BRC-114
< REMOVAL AND INSTALLATION >[VDC/TCS/ABS]
WHEEL SENSORS
REMOVAL AND INSTALLATION
WHEEL SENSORS
Removal and InstallationINFOID:0000000003772637
REMOVAL
1. Remove wheel sensor bolt.
• When removing the front wheel sensor, first remove t he disc rotor to gain access to the front wheel sen-
sor bolt. Refer to BR-31, "
Removal and Installation of Brake Caliper and Rotor".
• When removing the rear wheel sensor, first remove the rear hub and bearing assembly to gain access to
the rear wheel sensor bolt. Refer to RAX-7, "
Removal and Installation".
2. Pull out the sensor, being careful to turn it as little as possible. CAUTION:
• Do not pull on the sensor harness.
3. Disconnect wheel sensor harness electrical connec tor, then remove harness from attaching points.
INSTALLATION
Installation is in the reverse order of removal. Tighten wheel sensor bolt to specification.
CAUTION:
• Inspect wheel sensor O-ring, replace sensor assembly if damaged.
• Before installing wheel sensor, make sure no foreign materials (such as iron fragments) are adhered
to the pick-up part of the sensor, to the inside of the sensor hole or on the rotor mating surface.
• Apply a coat of suitable grease to the wheel sensor O-ring and hole. Refer to MA-12, "
Fluids and
Lubricants".
WFIA0376E
Revision: December 20092009 QX56
Page 592 of 4171
SENSOR ROTORBRC-115
< REMOVAL AND INSTALLATION > [VDC/TCS/ABS]
C
D
E
G H
I
J
K L
M A
B
BRC
N
O P
SENSOR ROTOR
Removal and InstallationINFOID:0000000003772638
NOTE:
The wheel sensor rotors are built into the wheel hubs and are not removable. If damaged, replace wheel hub
and bearing assembly. Refer to FA X - 7 , "
Removal and Installation" (front), RAX-7, "Removal and Installation"
(rear).
Revision: December 20092009 QX56
Page 594 of 4171
ACTUATOR AND ELECTRIC UNIT (ASSEMBLY)BRC-117
< REMOVAL AND INSTALLATION > [VDC/TCS/ABS]
C
D
E
G H
I
J
K L
M A
B
BRC
N
O P
• Always tighten brake tubes to sp ecification when installing.
• Never reuse drained brake fluid.
• After installation of the ABS actuator and elect ric unit (control unit), perform the following.
- Refill brake system with new br ake fluid. Then bleed the air from the system. Refer to BR-17, "
Bleed-
ing Brake System".
- Adjust the steering angle sensor. Refer to BRC-8, "
ADJUSTMENT OF STEERING ANGLE SENSOR
NEUTRAL POSITION : Speci al Repair Requirement".
- Calibrate the decel G sensor. Refer to BRC-9, "
CALIBRATION OF DECEL G SENSOR : Special Repair
Requirement".
Revision: December 20092009 QX56
Page 595 of 4171
BRC-118
< REMOVAL AND INSTALLATION >[VDC/TCS/ABS]
STEERING ANGLE SENSOR
STEERING ANGLE SENSOR
Removal and InstallationINFOID:0000000003772640
REMOVAL
1. Remove spiral cable. Refer to
SR-7, "Removal and Installation".
2. Remove the screws and remove the steering angle sensor.
INSTALLATION
Installation is in the reverse order of removal.
CAUTION:
After installation of spiral cable, ad just steering angle sensor. Refer to BRC-8, "
ADJUSTMENT OF
STEERING ANGLE SENSOR NEUTRAL POSIT ION : Special Repair Requirement".
Revision: December 20092009 QX56
Page 596 of 4171
G SENSORBRC-119
< REMOVAL AND INSTALLATION > [VDC/TCS/ABS]
C
D
E
G H
I
J
K L
M A
B
BRC
N
O P
G SENSOR
Removal and InstallationINFOID:0000000003772641
REMOVAL
1. Remove center console. Refer to IP-20, "Removal and Installa-
tion".
2. Remove yaw rate/side/decel G sensor attaching nuts. CAUTION:
• Do not use power tools to re move or install yaw rate/side/
decel G sensor.
• Do not drop or strike the yaw rate/side/decel G sensor.
3. Disconnect harness connector and remove the yaw rate/side/ decel G sensor.
INSTALLATION
Installation is in the reverse order of removal.
CAUTION:
• Do not drop or strike the yaw rate/side/decel G sensor.
• After installation, calibrate the yaw rate/side/decel G sensor. Refer to BRC-9, "
CALIBRATION OF
DECEL G SENSOR : Special Repair Requirement".
WFIA0202E
Revision: December 20092009 QX56
Page 598 of 4171
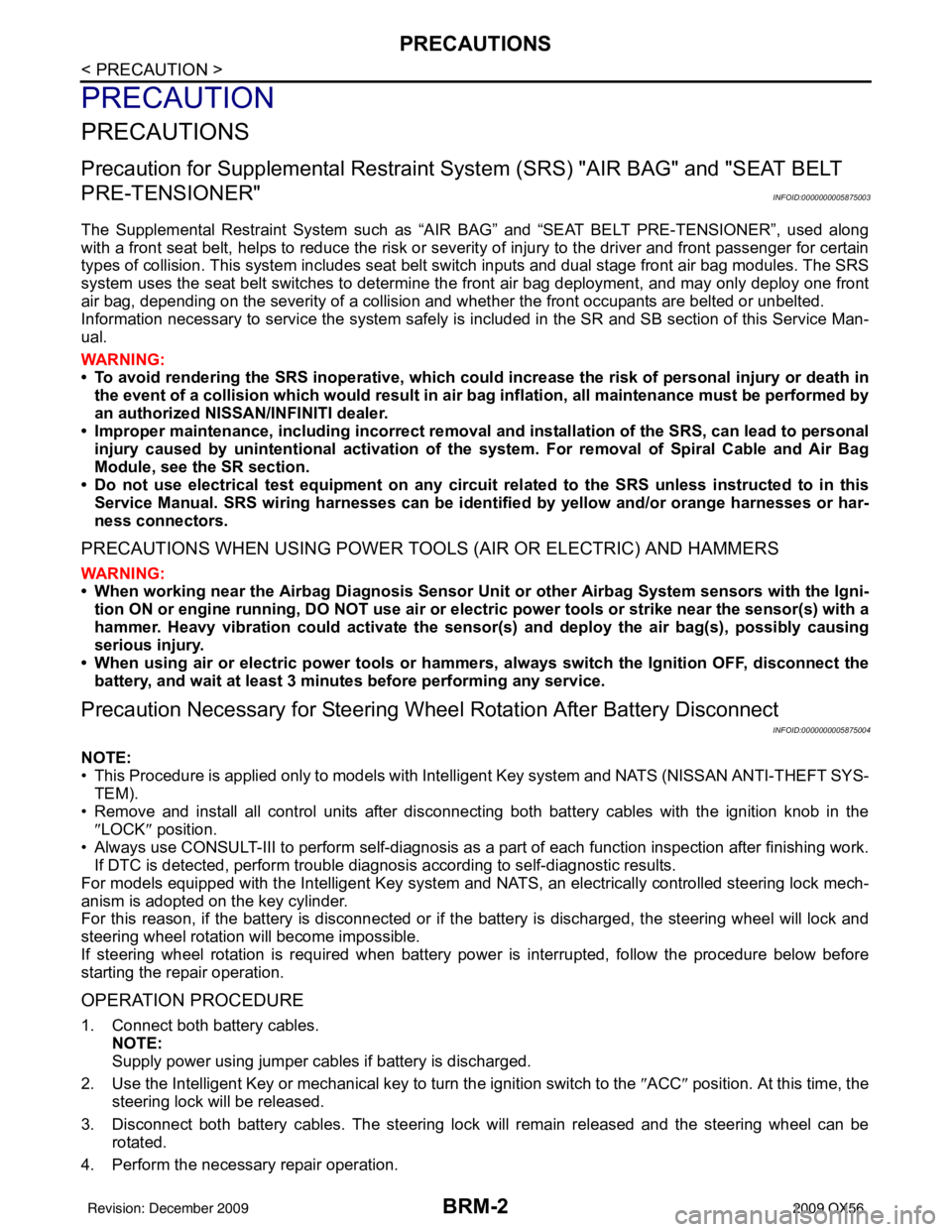
BRM-2
< PRECAUTION >
PRECAUTIONS
PRECAUTION
PRECAUTIONS
Precaution for Supplemental Restraint System (SRS) "AIR BAG" and "SEAT BELT
PRE-TENSIONER"
INFOID:0000000005875003
The Supplemental Restraint System such as “A IR BAG” and “SEAT BELT PRE-TENSIONER”, used along
with a front seat belt, helps to reduce the risk or severity of injury to the driver and front passenger for certain
types of collision. This system includes seat belt switch inputs and dual stage front air bag modules. The SRS
system uses the seat belt switches to determine the front air bag deployment, and may only deploy one front
air bag, depending on the severity of a collision and w hether the front occupants are belted or unbelted.
Information necessary to service the system safely is included in the SR and SB section of this Service Man-
ual.
WARNING:
• To avoid rendering the SRS inopera tive, which could increase the risk of personal injury or death in
the event of a collision which would result in air bag inflation, all maintenance must be performed by
an authorized NISSAN/INFINITI dealer.
• Improper maintenance, including in correct removal and installation of the SRS, can lead to personal
injury caused by unintent ional activation of the system. For re moval of Spiral Cable and Air Bag
Module, see the SR section.
• Do not use electrical test equipmen t on any circuit related to the SRS unless instructed to in this
Service Manual. SRS wiring harn esses can be identified by yellow and/or orange harnesses or har-
ness connectors.
PRECAUTIONS WHEN USING POWER TOOLS (AIR OR ELECTRIC) AND HAMMERS
WARNING:
• When working near the Airbag Diagnosis Sensor Unit or other Airbag System sensors with the Igni-
tion ON or engine running, DO NOT use air or electri c power tools or strike near the sensor(s) with a
hammer. Heavy vibration could activate the sensor( s) and deploy the air bag(s), possibly causing
serious injury.
• When using air or electric power tools or hammers , always switch the Ignition OFF, disconnect the
battery, and wait at least 3 minu tes before performing any service.
Precaution Necessary for Steering W heel Rotation After Battery Disconnect
INFOID:0000000005875004
NOTE:
• This Procedure is applied only to models with Intelligent Key system and NATS (NISSAN ANTI-THEFT SYS-
TEM).
• Remove and install all control units after disconnecting both battery cables with the ignition knob in the
″LOCK ″ position.
• Always use CONSULT-III to perform self-diagnosis as a part of each function inspection after finishing work.
If DTC is detected, perform trouble diagnosis according to self-diagnostic results.
For models equipped with the Intelligent Key system and NATS, an electrically controlled steering lock mech-
anism is adopted on the key cylinder.
For this reason, if the battery is disconnected or if the battery is discharged, the steering wheel will lock and
steering wheel rotation will become impossible.
If steering wheel rotation is required when battery pow er is interrupted, follow the procedure below before
starting the repair operation.
OPERATION PROCEDURE
1. Connect both battery cables. NOTE:
Supply power using jumper cables if battery is discharged.
2. Use the Intelligent Key or mechanical key to turn the ignition switch to the ″ACC ″ position. At this time, the
steering lock will be released.
3. Disconnect both battery cables. The steering lock will remain released and the steering wheel can be rotated.
4. Perform the necessary repair operation.
Revision: December 20092009 QX56
Page 652 of 4171
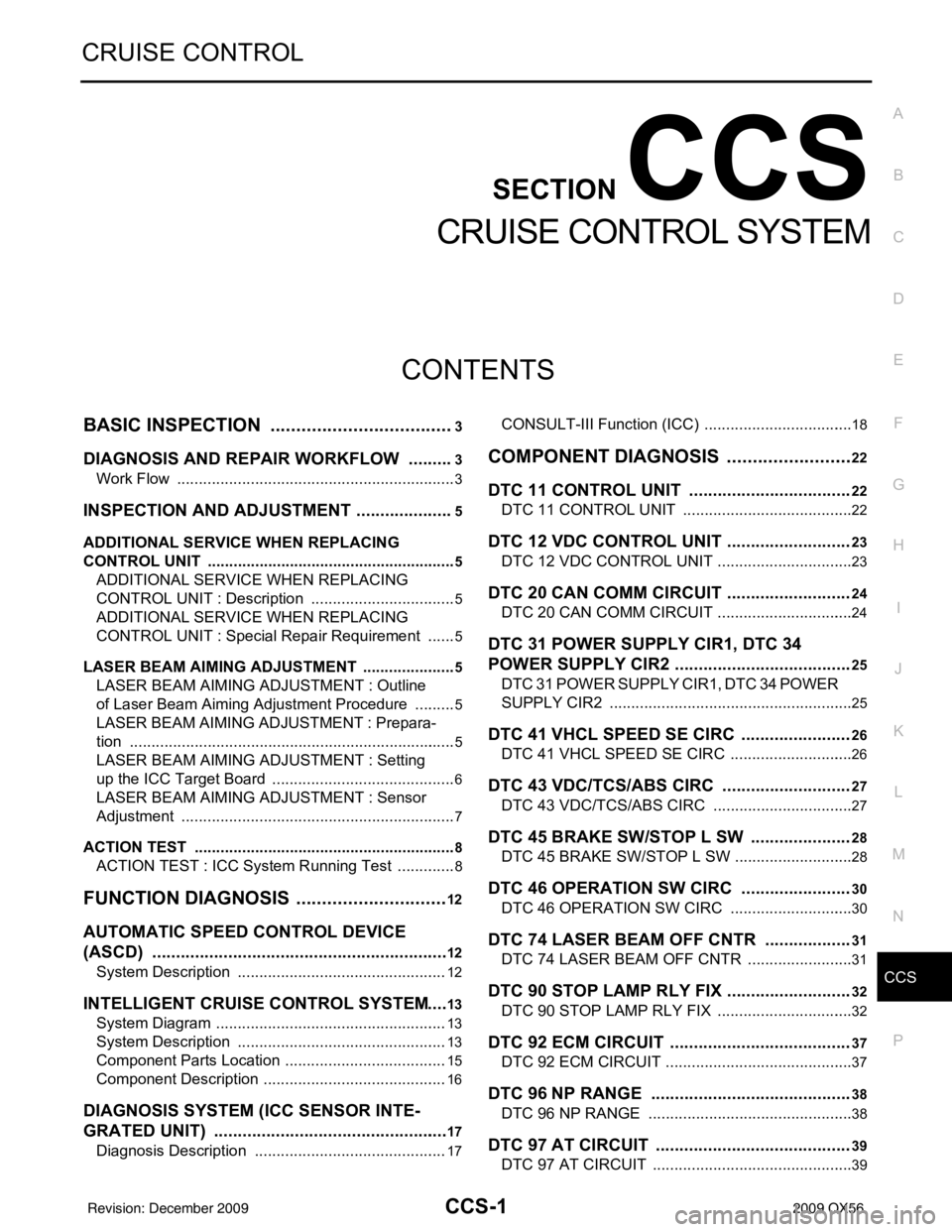
CCS-1
CRUISE CONTROL
C
DE
F
G H
I
J
K L
M B
CCS
SECTION CCS
N
P A
CONTENTS
CRUISE CONTROL SYSTEM
BASIC INSPECTION ....... .............................3
DIAGNOSIS AND REPAIR WORKFLOW ..... .....3
Work Flow ........................................................... ......3
INSPECTION AND ADJUSTMENT .....................5
ADDITIONAL SERVICE WHEN REPLACING
CONTROL UNIT .................................................... ......
5
ADDITIONAL SERVICE WHEN REPLACING
CONTROL UNIT : Description ..................................
5
ADDITIONAL SERVICE WHEN REPLACING
CONTROL UNIT : Special Repair Requirement .......
5
LASER BEAM AIMING ADJUSTMENT ................ ......5
LASER BEAM AIMING ADJUSTMENT : Outline
of Laser Beam Aiming Adjustment Procedure ..........
5
LASER BEAM AIMING ADJUSTMENT : Prepara-
tion ...................................................................... ......
5
LASER BEAM AIMING ADJUSTMENT : Setting
up the ICC Target Board ...........................................
6
LASER BEAM AIMING ADJUSTMENT : Sensor
Adjustment ................................................................
7
ACTION TEST ....................................................... ......8
ACTION TEST : ICC System Running Test ..............8
FUNCTION DIAGNOSIS ..............................12
AUTOMATIC SPEED CONTROL DEVICE
(ASCD) ........................................................... ....
12
System Description ............................................. ....12
INTELLIGENT CRUISE CONTROL SYSTEM ....13
System Diagram .................................................. ....13
System Description .................................................13
Component Parts Location ......................................15
Component Description ...........................................16
DIAGNOSIS SYSTEM (ICC SENSOR INTE-
GRATED UNIT) ..................................................
17
Diagnosis Description ......................................... ....17
CONSULT-III Function (ICC) ............................... ....18
COMPONENT DIAGNOSIS .........................22
DTC 11 CONTROL UNIT ..................................22
DTC 11 CONTROL UNIT .................................... ....22
DTC 12 VDC CONTROL UNIT ..........................23
DTC 12 VDC CONTROL UNIT ................................23
DTC 20 CAN COMM CIRCUIT ..........................24
DTC 20 CAN COMM CIRCUIT ................................24
DTC 31 POWER SUPPLY CIR1, DTC 34
POWER SUPPLY CIR2 .....................................
25
DTC 31 POWER SUPPLY CIR1, DTC 34 POWER
SUPPLY CIR2 .........................................................
25
DTC 41 VHCL SPEED SE CIRC .......................26
DTC 41 VHCL SPEED SE CIRC .............................26
DTC 43 VDC/TCS/ABS CIRC ...........................27
DTC 43 VDC/TCS/ABS CIRC .................................27
DTC 45 BRAKE SW/STOP L SW .....................28
DTC 45 BRAKE SW/STOP L SW ............................28
DTC 46 OPERATION SW CIRC .......................30
DTC 46 OPERATION SW CIRC ......................... ....30
DTC 74 LASER BEAM OFF CNTR ..................31
DTC 74 LASER BEAM OFF CNTR .........................31
DTC 90 STOP LAMP RLY FIX ..........................32
DTC 90 STOP LAMP RLY FIX ................................32
DTC 92 ECM CIRCUIT ......................................37
DTC 92 ECM CIRCUIT ............................................37
DTC 96 NP RANGE ..........................................38
DTC 96 NP RANGE ............................................ ....38
DTC 97 AT CIRCUIT .........................................39
DTC 97 AT CIRCUIT ...............................................39
Revision: December 20092009 QX56