Page 3723 of 4083
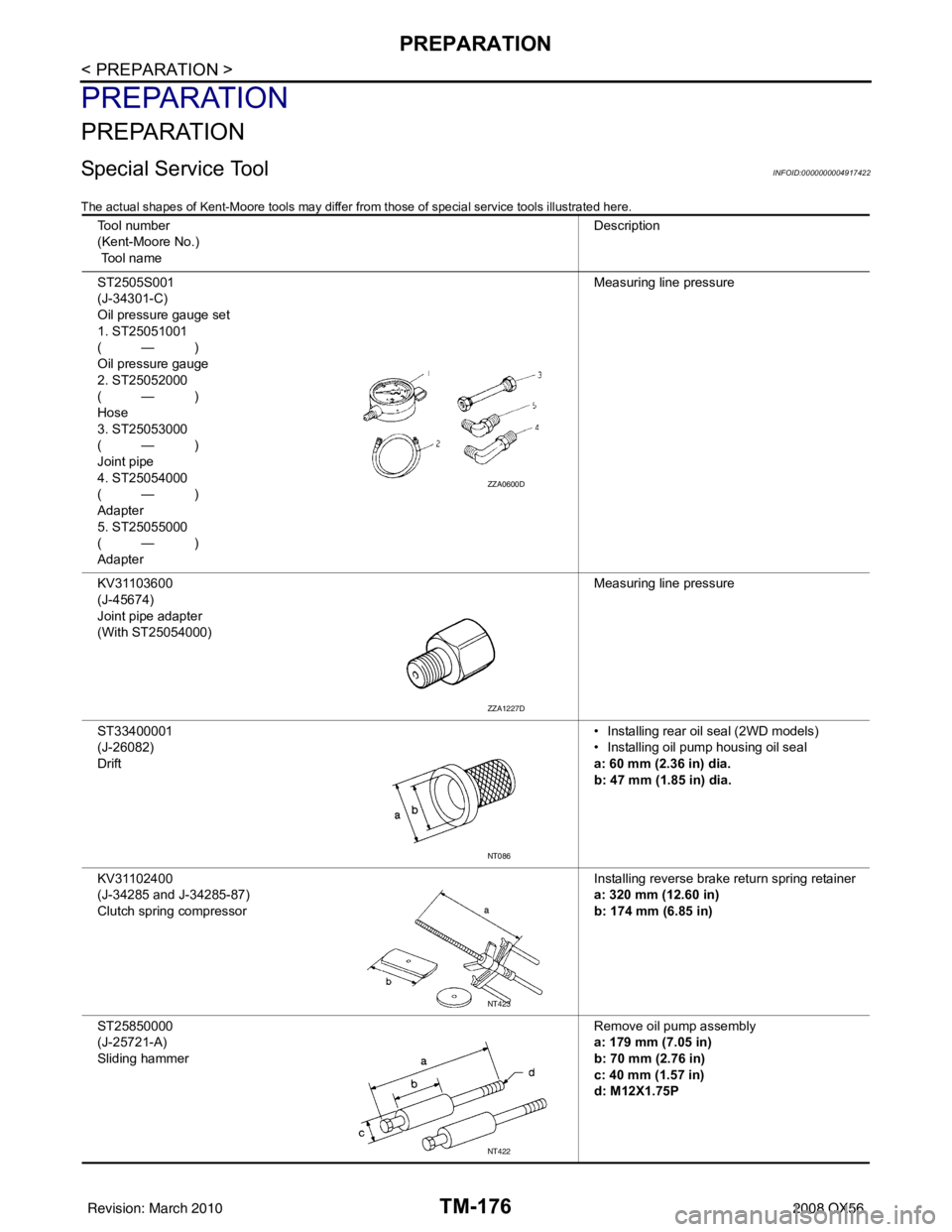
TM-176
< PREPARATION >
PREPARATION
PREPARATION
PREPARATION
Special Service ToolINFOID:0000000004917422
The actual shapes of Kent-Moore tools may differ from those of special service tools illustrated here.
Tool number
(Kent-Moore No.)
Tool name Description
ST2505S001
(J-34301-C)
Oil pressure gauge set
1. ST25051001
(—)
Oil pressure gauge
2. ST25052000
(—)
Hose
3. ST25053000
(—)
Joint pipe
4. ST25054000
(—)
Adapter
5. ST25055000
(—)
Adapter Measuring line pressure
KV31103600
(J-45674)
Joint pipe adapter
(With ST25054000) Measuring line pressure
ST33400001
(J-26082)
Drift • Installing rear oil seal (2WD models)
• Installing oil pump housing oil seal
a: 60 mm (2.36 in) dia.
b: 47 mm (1.85 in) dia.
KV31102400
(J-34285 and J-34285-87)
Clutch spring compressor Installing reverse brake return spring retainer
a: 320 mm (12.60 in)
b: 174 mm (6.85 in)
ST25850000
(J-25721-A)
Sliding hammer Remove oil pump assembly
a: 179 mm (7.05 in)
b: 70 mm (2.76 in)
c: 40 mm (1.57 in)
d: M12X1.75P
ZZA0600D
ZZA1227D
NT086
NT423
NT422
Revision: March 2010
2008 QX56
Page 3724 of 4083
PREPARATIONTM-177
< PREPARATION >
CEF
G H
I
J
K L
M A
B
TM
N
O P
Commercial Service ToolINFOID:0000000004917423
—
(J-47002)
Transmission jack adapter kit
1. —
(J-47002-2)
Center bracket
2. —
(J-47002-3)
Adapter plate
3. —
(J-47002-4)
Adapter block Assist in removal of transmission and transfer
case as one assembly using only one trans-
mission jack.
—
( J-46534 )
Trim tool set For removing trim
Tool number
(Kent-Moore No.)
Tool name
Description
WCIA0499E
AWJIA0483ZZ
Tool name
Description
Power tool Loosening bolts and nuts
Drift Installing manual shaft seals
a: 22 mm (0.87 in) dia.
Drift Installing rear oil seal (4WD models)
a: 64 mm (2.52 in) dia.
PBIC0190E
NT083
SCIA5338E
Revision: March 2010 2008 QX56
Page 3729 of 4083
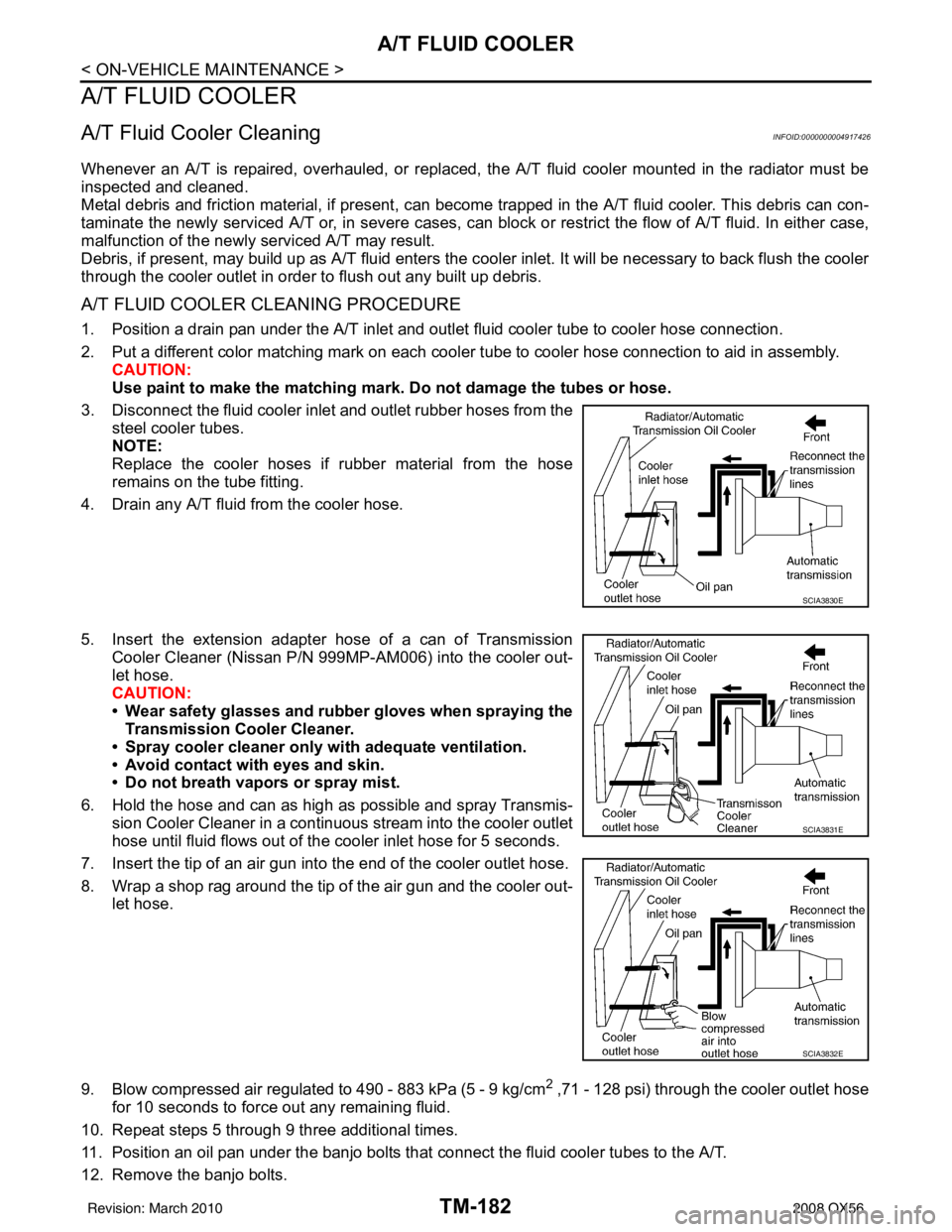
TM-182
< ON-VEHICLE MAINTENANCE >
A/T FLUID COOLER
A/T FLUID COOLER
A/T Fluid Cooler CleaningINFOID:0000000004917426
Whenever an A/T is repaired, overhauled, or replaced, the A/T fluid cooler mounted in the radiator must be
inspected and cleaned.
Metal debris and friction material, if present, can become trapped in the A/T fluid cooler. This debris can con-
taminate the newly serviced A/T or, in severe cases, can bloc k or restrict the flow of A/T fluid. In either case,
malfunction of the newly serviced A/T may result.
Debris, if present, may build up as A/T fluid enters the c ooler inlet. It will be necessary to back flush the cooler
through the cooler outlet in order to flush out any built up debris.
A/T FLUID COOLER CLEANING PROCEDURE
1. Position a drain pan under the A/T inlet and outlet fluid cooler tube to cooler hose connection.
2. Put a different color matching mark on each cooler tube to cooler hose connection to aid in assembly. CAUTION:
Use paint to make the matching mark. Do not damage the tubes or hose.
3. Disconnect the fluid cooler inlet and outlet rubber hoses from the steel cooler tubes.
NOTE:
Replace the cooler hoses if rubber material from the hose
remains on the tube fitting.
4. Drain any A/T fluid from the cooler hose.
5. Insert the extension adapter hose of a can of Transmission
Cooler Cleaner (Nissan P/N 999MP-AM006) into the cooler out-
let hose.
CAUTION:
• Wear safety glasses and rubber gloves when spraying the Transmission Cooler Cleaner.
• Spray cooler cleaner only wi th adequate ventilation.
• Avoid contact with eyes and skin.
• Do not breath vapors or spray mist.
6. Hold the hose and can as high as possible and spray Transmis- sion Cooler Cleaner in a continuous stream into the cooler outlet
hose until fluid flows out of the cooler inlet hose for 5 seconds.
7. Insert the tip of an air gun into the end of the cooler outlet hose.
8. Wrap a shop rag around the tip of the air gun and the cooler out- let hose.
9. Blow compressed air regulated to 490 - 883 kPa (5 - 9 kg/cm
2 ,71 - 128 psi) through the cooler outlet hose
for 10 seconds to force out any remaining fluid.
10. Repeat steps 5 through 9 three additional times.
11. Position an oil pan under the banjo bolts that connect the fluid cooler tubes to the A/T.
12. Remove the banjo bolts.
SCIA3830E
SCIA3831E
SCIA3832E
Revision: March 2010 2008 QX56
Page 3731 of 4083
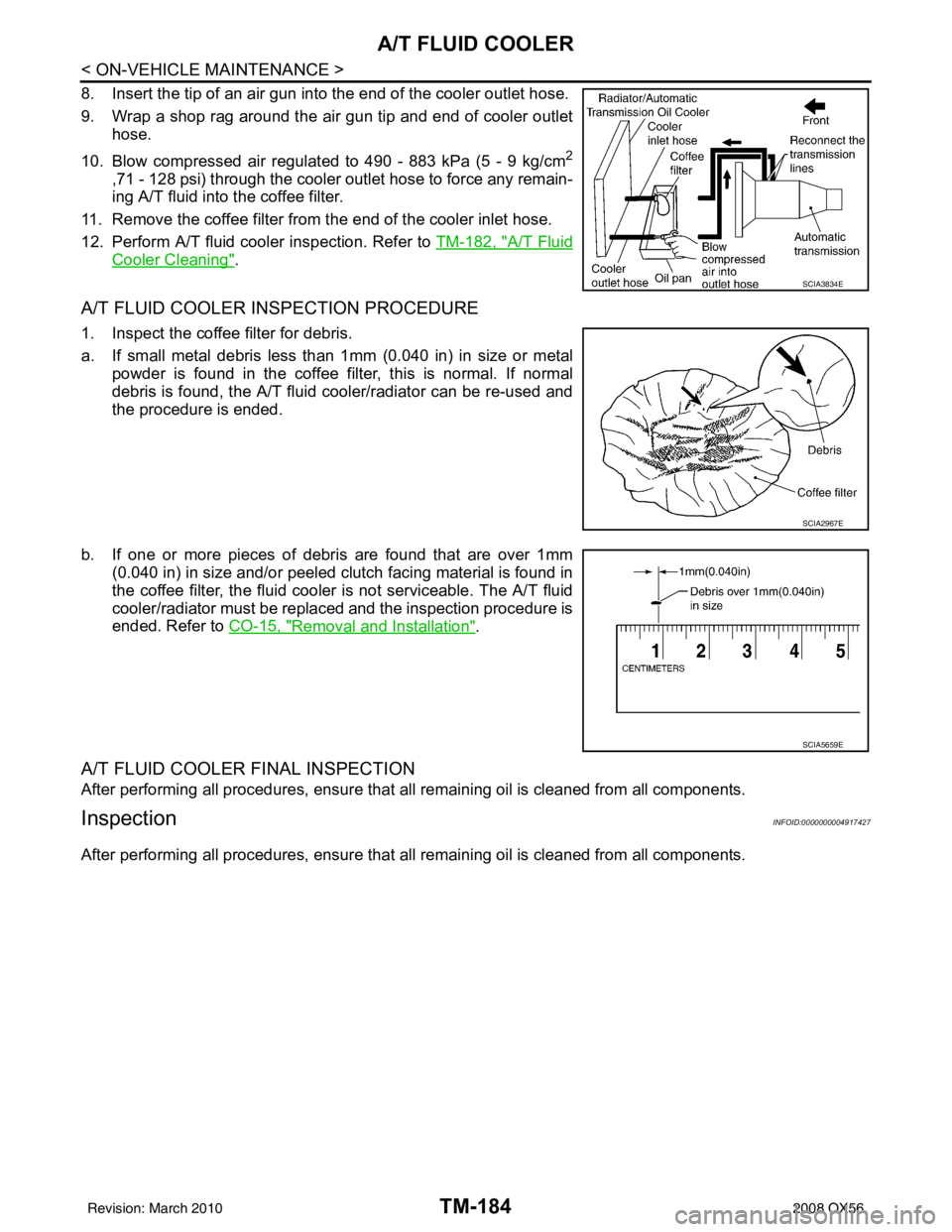
TM-184
< ON-VEHICLE MAINTENANCE >
A/T FLUID COOLER
8. Insert the tip of an air gun into the end of the cooler outlet hose.
9. Wrap a shop rag around the air gun tip and end of cooler outlethose.
10. Blow compressed air regulated to 490 - 883 kPa (5 - 9 kg/cm
2
,71 - 128 psi) through the cooler outlet hose to force any remain-
ing A/T fluid into the coffee filter.
11. Remove the coffee filter from the end of the cooler inlet hose.
12. Perform A/T fluid cooler inspection. Refer to TM-182, "
A/T Fluid
Cooler Cleaning".
A/T FLUID COOLER INSPECTION PROCEDURE
1. Inspect the coffee filter for debris.
a. If small metal debris less than 1mm (0.040 in) in size or metal
powder is found in the coffee filter, this is normal. If normal
debris is found, the A/T fluid cooler/radiator can be re-used and
the procedure is ended.
b. If one or more pieces of debris are found that are over 1mm (0.040 in) in size and/or peeled clutch facing material is found in
the coffee filter, the fluid cooler is not serviceable. The A/T fluid
cooler/radiator must be replaced and the inspection procedure is
ended. Refer to CO-15, "
Removal and Installation".
A/T FLUID COOLER FINAL INSPECTION
After performing all procedures, ensure that all remaining oil is cleaned from all components.
InspectionINFOID:0000000004917427
After performing all procedures, ensure that all remaining oil is cleaned from all components.
SCIA3834E
SCIA2967E
SCIA5659E
Revision: March 2010 2008 QX56
Page 3765 of 4083

TM-218
< REMOVAL AND INSTALLATION >
TRANSMISSION ASSEMBLY
8. Remove crankshaft position sensor (POS) from A/T assembly.CAUTION:
• Do not subject it to impact by dropping or hitting it.
• Do not disassemble.
• Do not allow metal filings or fo reign material to get on the
sensor's front edge magnetic area.
• Do not place in an area affected by magnetism.
9. Disconnect A/T fluid cooler tube from A/T assembly.
10. Remove dust cover from converter housing.
11. Turn crankshaft, and remove the four bolts for drive plate and torque converter.
CAUTION:
When turning crankshaft, turn it clockwise as viewed from
the front of the engine.
12. Support A/T assembly using transmission jack and Tool. CAUTION:
When setting the transmission j ack, be careful not to allow
it to collide agai nst the drain plug.
NOTE:
The actual special service tool may differ from tool shown.
13. Remove cross member using power tool.
14. Remove air breather hose. Refer to TM-197, "
Removal and
Installation".
15. Disconnect A/T assembly connector and transfer unit connector.
16. Remove A/T fluid indicator pipe.
17. Plug any openings such as the fluid charging pipe hole.
18. Remove A/T assembly to engine bolts using power tool.
19. Remove A/T assembly with transfer from vehicle. CAUTION:
• Secure torque converter to prevent it from dropping.
• Secure A/T assembly to transmission jack.
20. Remove transfer from A/T assembly. Refer to DLN-139, "
Removal and Installation".
INSPECTION
Installation and Inspection of Torque Converter
LCIA0334E
LCIA0335E
Tool number : — (J-47002)
SCIA2203E
Revision: March 2010 2008 QX56
Page 3838 of 4083
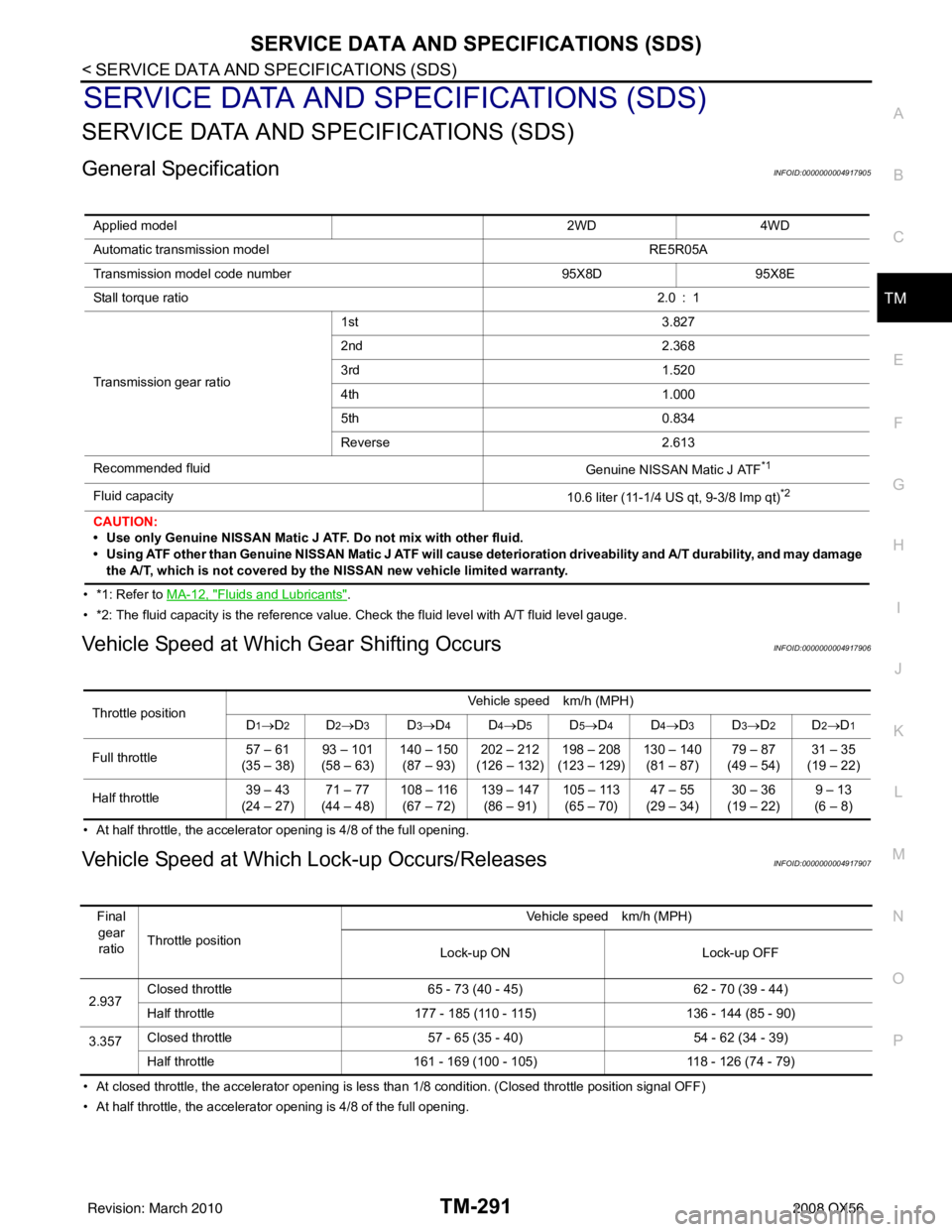
SERVICE DATA AND SPECIFICATIONS (SDS)TM-291
< SERVICE DATA AND SPECIFICATIONS (SDS)
CEF
G H
I
J
K L
M A
B
TM
N
O P
SERVICE DATA AND SPECIFICATIONS (SDS)
SERVICE DATA AND SPECIFICATIONS (SDS)
General SpecificationINFOID:0000000004917905
• *1: Refer to MA-12, "Fluids and Lubricants".
• *2: The fluid capacity is the reference value. Check the fluid level with A/T fluid level gauge.
Vehicle Speed at Which Gear Shifting OccursINFOID:0000000004917906
• At half throttle, the accelerator opening is 4/8 of the full opening.
Vehicle Speed at Which Lock-up Occurs/ReleasesINFOID:0000000004917907
• At closed throttle, the accelerator opening is less than 1/8 condition. (Closed throttle position signal OFF)
• At half throttle, the accelerator opening is 4/8 of the full opening. Applied model
2WD4WD
Automatic transmission model RE5R05A
Transmission model code number 95X8D95X8E
Stall torque ratio 2.0 : 1
Transmission gear ratio 1st
3.827
2nd 2.368
3rd 1.520
4th 1.000
5th 0.834
Reverse 2.613
Recommended fluid Genuine NISSAN Matic J ATF
*1
Fluid capacity10.6 liter (11-1/4 US qt, 9-3/8 Imp qt)*2
CAUTION:
• Use only Genuine NISSAN Matic J ATF. Do not mix with other fluid.
• Using ATF other than Genuine NISSAN Matic J ATF will cause deterioration driveability and A/ T durability, and may damage
the A/T, which is not covered by the NISSAN new vehicle limited warranty.
Throttle position Vehicle speed km/h (MPH)
D1→D2D2→ D3D3→D4D4→D5D5→D4D4→D3D3→D2D2→D1
Full throttle 57 – 61
(35 – 38) 93 – 101
(58 – 63) 140 – 150
(87 – 93) 202 – 212
(126 – 132) 198 – 208
(123 – 129) 130 – 140
(81 – 87) 79 – 87
(49 – 54) 31 – 35
(19 – 22)
Half throttle 39 – 43
(24 – 27) 71 – 77
(44 – 48) 108 – 116
(67 – 72) 139 – 147
(86 – 91) 105 – 113
(65 – 70) 47 – 55
(29 – 34) 30 – 36
(19 – 22) 9 – 13
(6 – 8)
Final gear ratio Throttle position Vehicle speed km/h (MPH)
Lock-up ON Lock-up OFF
2.937 Closed throttle
65 - 73 (40 - 45) 62 - 70 (39 - 44)
Half throttle 177 - 185 (110 - 115) 136 - 144 (85 - 90)
3.357 Closed throttle
57 - 65 (35 - 40) 54 - 62 (34 - 39)
Half throttle 161 - 169 (100 - 105) 118 - 126 (74 - 79)
Revision: March 2010 2008 QX56
Page 3839 of 4083

TM-292
< SERVICE DATA AND SPECIFICATIONS (SDS)
SERVICE DATA AND SPECIFICATIONS (SDS)
Stall Speed
INFOID:0000000004917908
Line PressureINFOID:0000000004917909
A/T Fluid Temperature SensorINFOID:0000000004917910
Input Speed SensorINFOID:0000000004917911
Output Speed SensorINFOID:0000000004917912
Reverse BrakeINFOID:0000000004917913
Total End PlayINFOID:0000000004917914
BEARING RACE FOR ADJUSTING TOTAL END PLAY
Stall speed 2,700 – 3,000 rpm
Engine speedLine pressure kPa (kg/cm2, psi)
“R” position “D” position
At idle speed 425 – 465 (4.3 – 4.7, 62 – 67) 379 – 428 (3.9 – 4.4, 55 – 62)
At stall speed 1,605 – 1,950 (16.4 – 19.9, 233 – 283) 1,310 – 1,500 (13.4 – 15.3, 190 – 218)
NameCondition CONSULT-I II “DATA MONITOR” (Approx.) (V) Resistance (Approx.) (k Ω)
ATF TEMP SE 1 0
°C (32 °F) 3.3 15
20 °C (68 °F) 2.7 6.5
80 °C (176 °F) 0.9 0.9
Name ConditionData (Approx.)
Input speed sensor 1 When running at 50 km/h (31 MPH) in 4th speed witch the closed throttle position
signal OFF.
1.3 kHz
Input speed sensor 2 When running at 20 km/h (12 MPH) in 1st speed witch the closed throttle position
signal OFF.
Name
ConditionData (Approx.)
Output speed sensor When running at 20 km/h (12 MPH). 185 Hz
Model code number 97X2E, 97X3A
Number of drive plates 6
Number of driven plates 6
Clearance mm (in) Standard 0.7 – 1.1 (0.028 – 0.043)
Thickness of retaining plates Thickness mm (in)
4.2 (0.165)
4.4 (0.173)
4.6 (0.181)
4.8 (0.189)
5.0 (0.197)
5.2 (0.205)
Total end play mm (in) 0.25 – 0.55 (0.0098 – 0.0217)
Revision: March 2010 2008 QX56
Page 3840 of 4083
SERVICE DATA AND SPECIFICATIONS (SDS)TM-293
< SERVICE DATA AND SPECIFICATIONS (SDS)
CEF
G H
I
J
K L
M A
B
TM
N
O P
Torque ConverterINFOID:0000000004917915
Thickness mm (in) 0.8 (0.031)
1.0 (0.039)
1.2 (0.047)
1.4 (0.055)
1.6 (0.063)
1.8 (0.071)
Distance between end of converter housing and torque
converter mm (in) 24.0 (0.94) or more
Revision: March 2010
2008 QX56