Page 152 of 392
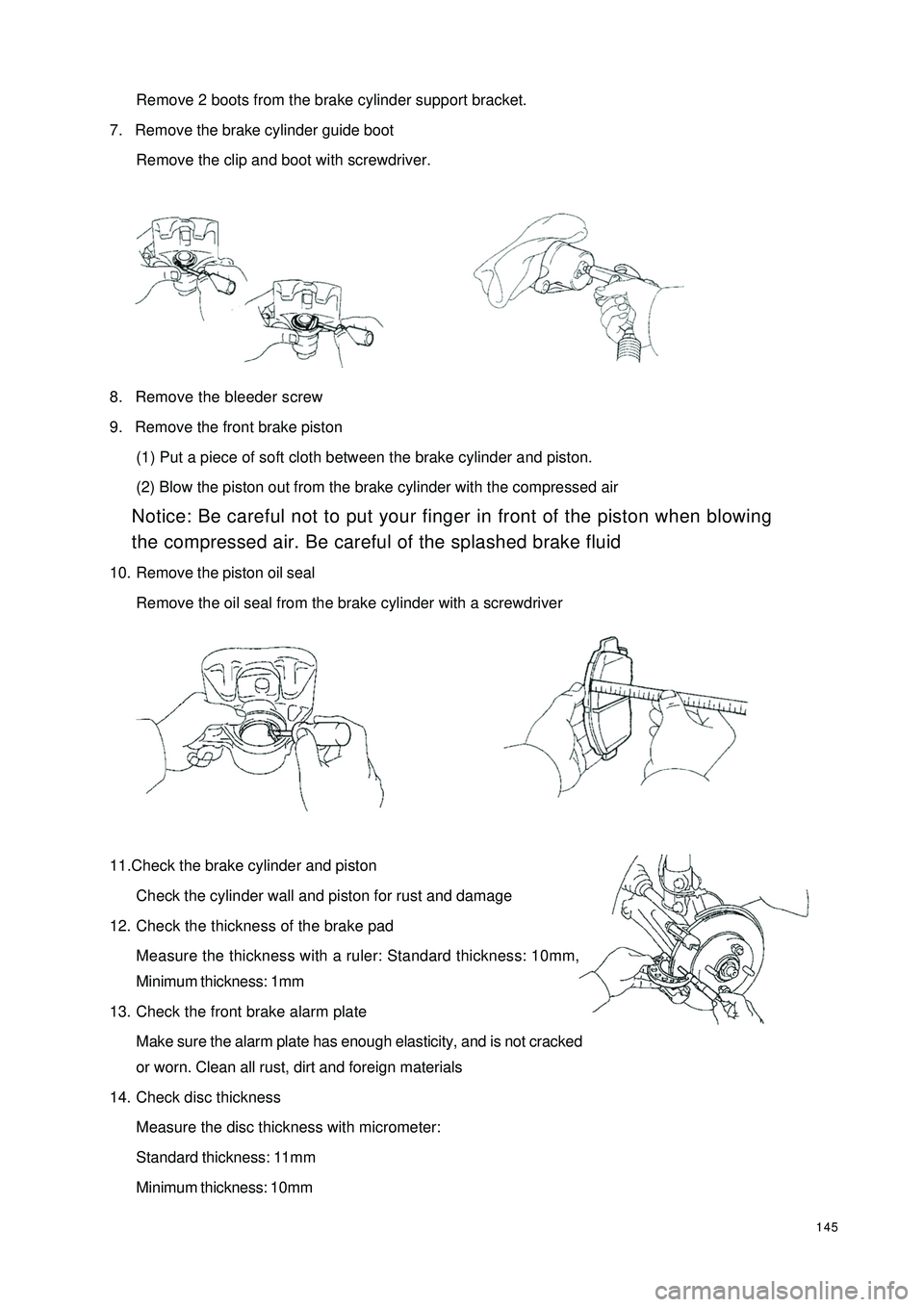
145Remove 2 boots from the brake cylinder support bracket.
7. Remove the brake cylinder guide boot
Remove the clip and boot with screwdriver.
8. Remove the bleeder screw
9. Remove the front brake piston
(1) Put a piece of soft cloth between the brake cylinder and piston.
(2) Blow the piston out from the brake cylinder with the compressed air
Notice: Be careful not to put your finger in front of the piston when blowing
the compressed air. Be careful of the splashed brake fluid
10. Remove the piston oil seal
Remove the oil seal from the brake cylinder with a screwdriver
11.Check the brake cylinder and piston
Check the cylinder wall and piston for rust and damage
12. Check the thickness of the brake pad
Measure the thickness with a ruler: Standard thickness: 10mm,
Minimum thickness: 1mm
13. Check the front brake alarm plate
Make sure the alarm plate has enough elasticity, and is not cracked
or worn. Clean all rust, dirt and foreign materials
14. Check disc thickness
Measure the disc thickness with micrometer:
Standard thickness: 11mm
Minimum thickness: 10mm
Page 153 of 392
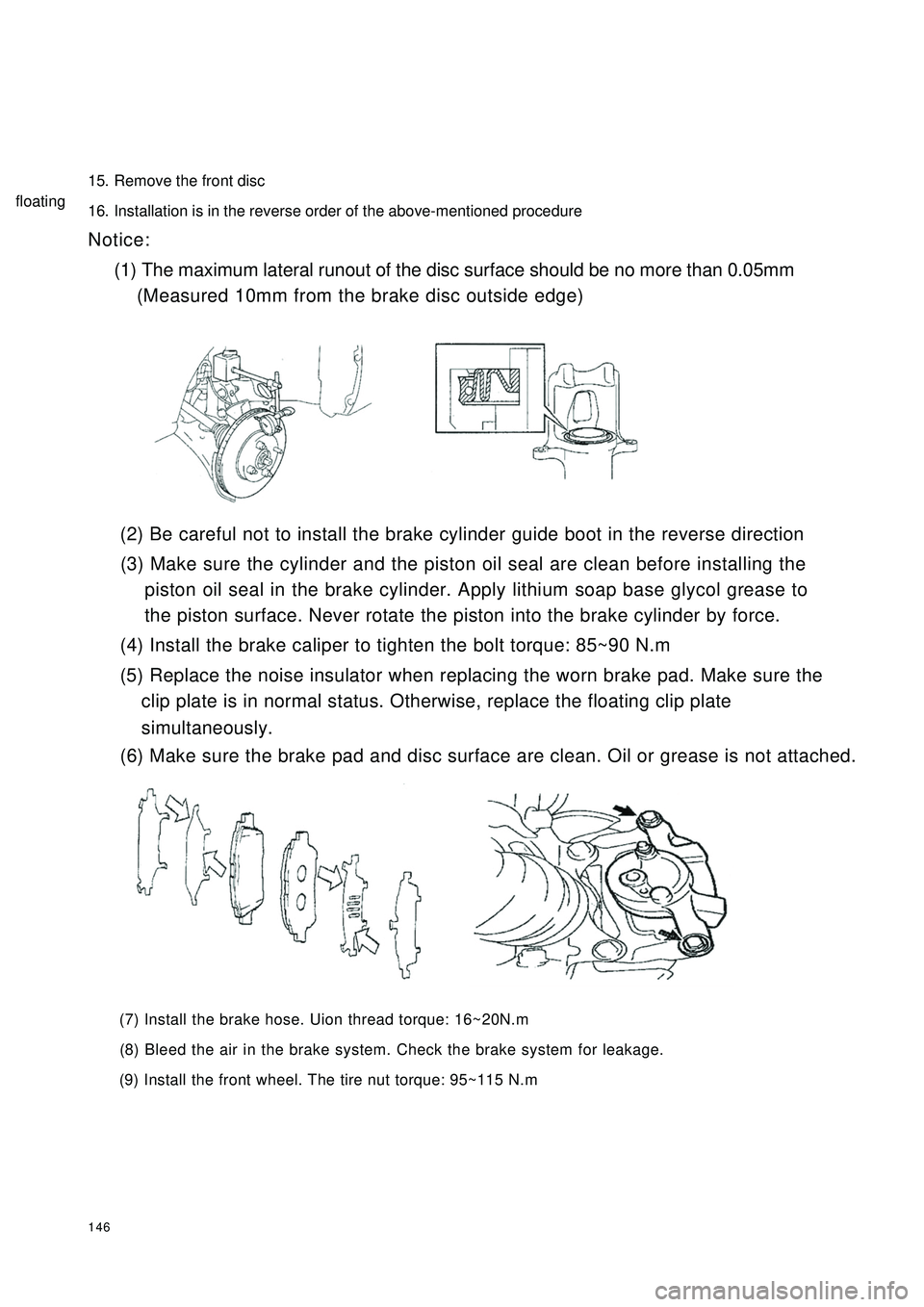
14615. Remove the front disc
16. Installation is in the reverse order of the above-mentioned procedure
Notice:
(1) The maximum lateral runout of the disc surface should be no more than 0.05mm
(Measured 10mm from the brake disc outside edge)
(2) Be careful not to install the brake cylinder guide boot in the reverse direction
(3) Make sure the cylinder and the piston oil seal are clean before installing the
piston oil seal in the brake cylinder. Apply lithium soap base glycol grease to
the piston surface. Never rotate the piston into the brake cylinder by force.
(4) Install the brake caliper to tighten the bolt torque: 85~90 N.m
(5) Replace the noise insulator when replacing the worn brake pad. Make sure the
clip plate is in normal status. Otherwise, replace the floating clip plate
(6) Make sure the brake pad and disc surface are clean. Oil or grease is not attached.
(7) Install the brake hose. Uion thread torque: 16~20N.m
(8) Bleed the air in the brake system. Check the brake system for leakage.
(9) Install the front wheel. The tire nut torque: 95~115 N.msimultaneously.floating
Page 168 of 392
161Chapter 2 Starting and Charging SystemSection 1 Starting System
(MR479Q MR479QA MR481QA)I. STARTER INSPECTIONNOTICE:
These tests must be done within 5 seconds to avoid burning out the coil.
1. INSPECT MAGNETIC SWITCH
(a) Use wire to connect the starter as shown.
(b) Connect the magnetic switch and the battery as
shown.
(c) Disconnect the magnet exciting coil from the
terminal A.
(d) Check if the clutch pinion gear is moving out.
If the clutch pinion gear is not moving out, replace
the magnetic switch.
(e) Connect the battery as shown above. Disconnect
the battery positive (+) from the terminal, to make the clutch pinion gear disengaged.
(f) Check if the clutch pinion gear has returned.
If the clutch pinion gear has not returned, replace
the magnetic switch.Terminal ABatteryBatteryDisconnect
Page 169 of 392
1622. INSPECT STARTER NO-LOAD
(a) Connect the magnet exciting coil and the terminal.
(b) Connect the ammeter and the battery to the starter
as shown.
(c) Check that the starter rotates smoothly and steadily
with the clutch pinion gear moving out.
(d) Check that the ammeter shows the specified
current.
Specified current: 90 A or less at 11.5 V
if the current is not normal, replace the starter.
3. WIRING
(a) Check that the connecting wire between
the positive (+) and the starter is stable
and reliable, and the insulating bush is in
good condition, in order to avoid a fire
caused by electric spark.
(b) Check that there is continuity in the wire
and if the insulating bush is not damaged.
If the harness is damaged, replace it.AmmeterIgnition SwitchBattery Main Fuse BoxStarter
Page 203 of 392
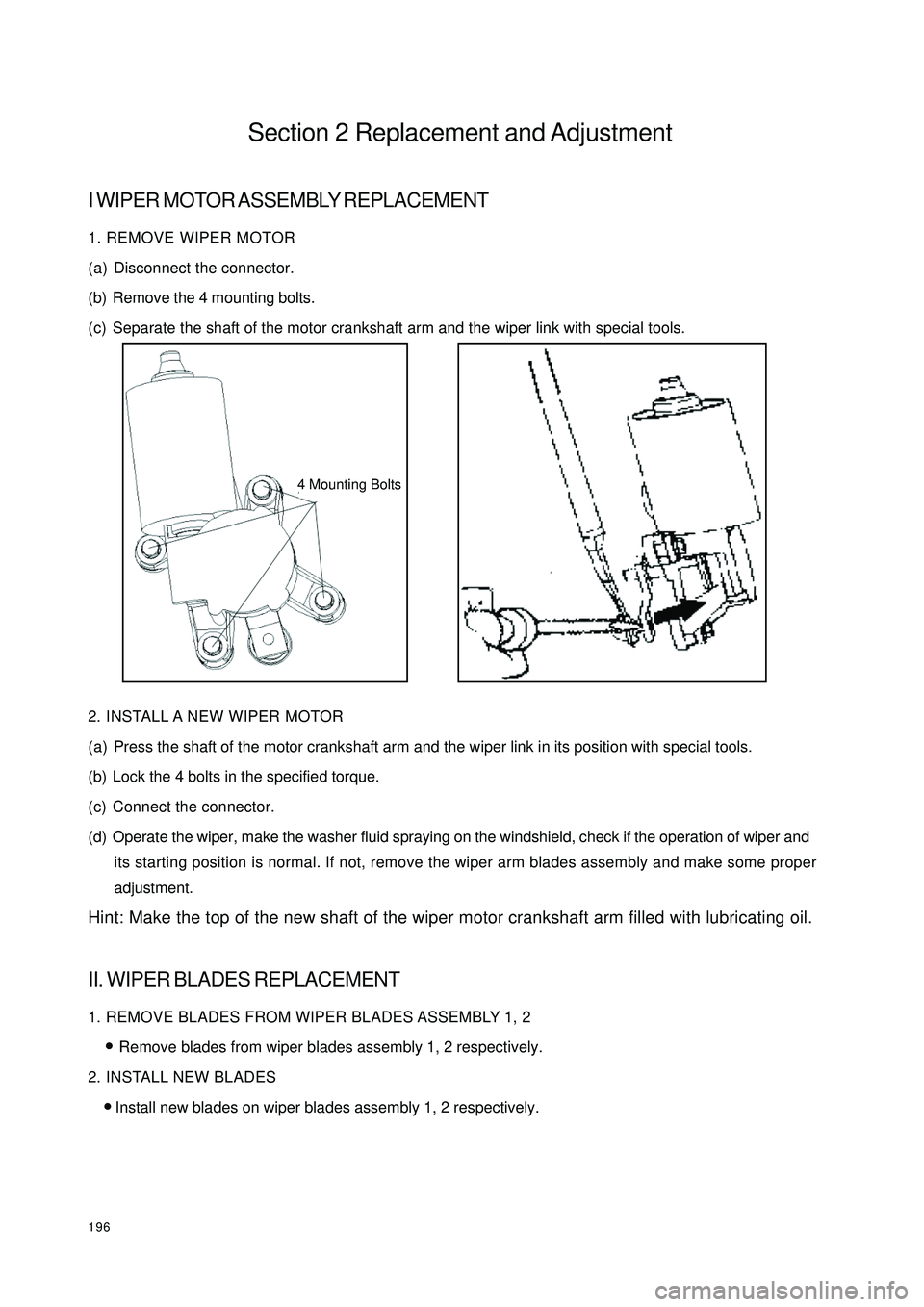
196Section 2 Replacement and AdjustmentI WIPER MOTOR ASSEMBLY REPLACEMENT1. REMOVE WIPER MOTOR
(a) Disconnect the connector.
(b) Remove the 4 mounting bolts.
(c) Separate the shaft of the motor crankshaft arm and the wiper link with special tools.
2. INSTALL A NEW WIPER MOTOR
(a) Press the shaft of the motor crankshaft arm and the wiper link in its position with special tools.
(b) Lock the 4 bolts in the specified torque.
(c) Connect the connector.
(d) Operate the wiper, make the washer fluid spraying on the windshield, check if the operation of wiper and
its starting position is normal. If not, remove the wiper arm blades assembly and make some proper
adjustment.
Hint: Make the top of the new shaft of the wiper motor crankshaft arm filled with lubricating oil.II. WIPER BLADES REPLACEMENT1. REMOVE BLADES FROM WIPER BLADES ASSEMBLY 1, 2
yRemove blades from wiper blades assembly 1, 2 respectively.
2. INSTALL NEW BLADES
yInstall new blades on wiper blades assembly 1, 2 respectively.4 Mounting Bolts
Page 267 of 392
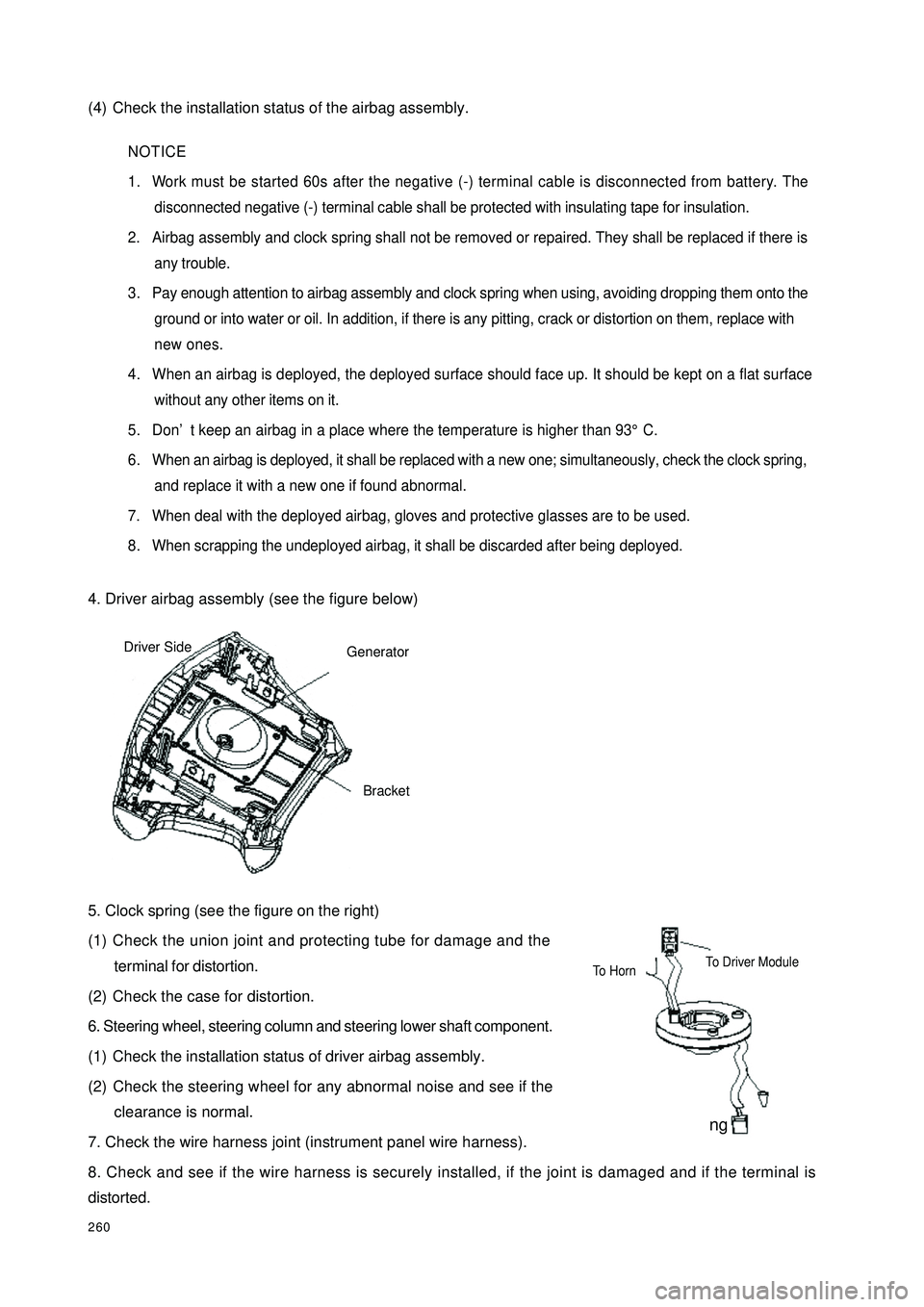
260(4) Check the installation status of the airbag assembly.
4. Driver airbag assembly (see the figure below)
5. Clock spring (see the figure on the right)
(1) Check the union joint and protecting tube for damage and the
terminal for distortion.
(2) Check the case for distortion.
6. Steering wheel, steering column and steering lower shaft component.
(1) Check the installation status of driver airbag assembly.
(2) Check the steering wheel for any abnormal noise and see if the
clearance is normal.
7. Check the wire harness joint (instrument panel wire harness).
8. Check and see if the wire harness is securely installed, if the joint is damaged and if the terminal is
distorted.NOTICE
1. Work must be started 60s after the negative (-) terminal cable is disconnected from battery. The
disconnected negative (-) terminal cable shall be protected with insulating tape for insulation.
2. Airbag assembly and clock spring shall not be removed or repaired. They shall be replaced if there is
any trouble.
3. Pay enough attention to airbag assembly and clock spring when using, avoiding dropping them onto the
ground or into water or oil. In addition, if there is any pitting, crack or distortion on them, replace with
new ones.
4. When an airbag is deployed, the deployed surface should face up. It should be kept on a flat surface
without any other items on it.
5. Don’t keep an airbag in a place where the temperature is higher than 93°C.
6. When an airbag is deployed, it shall be replaced with a new one; simultaneously, check the clock spring,
and replace it with a new one if found abnormal.
7. When deal with the deployed airbag, gloves and protective glasses are to be used.
8. When scrapping the undeployed airbag, it shall be discarded after being deployed.GeneratorBracketDriver Side Clock SpringTo HornTo Driver Module
Page 284 of 392

277Whether the sensor is installed
correctlyCheck the sensor Output Volt-
age at the ABS ECU25 pin
connector Check each sensorCheck each sensor ringgearCheck the wheel bearing
clearance Check the wire harness be-
tween the sensor and the
ABS ECUNo
Install it correctly
Replace the ABS ECUAbn.
Abn.
Abn.
Abn. Ye s
Normal Normal
Normal
NormalReplace
Replace
Replace or Repair 2 DTC 00283,00285,00283,00285,
00287,00290Like ly Caus e s
[De s cription]
When no open in the circuit can
be detected and there is no signal output when
the vehicle speed exceeds 20km/h, this DTC is
set.
[H int]
The likely c ause ma y be the se nsor
ina dvertently not insta lle d, short c ircuit in the
sensor coil or wire harness, excessive
clearance between the sensor and the ring gear
or dama ged ring ge a r. z
T h e s e n s o r is n o t in s t a lle d in a d v e r t e n t ly
z
Short c irc uit in the se nsor c oil or w ire ha rne ss
z
Excessive big clearance between the sensor and
the ring gea r
z
The ring gea r is not insta lle d ina dverte ntly
z
ABS ECU failure
Page 285 of 392
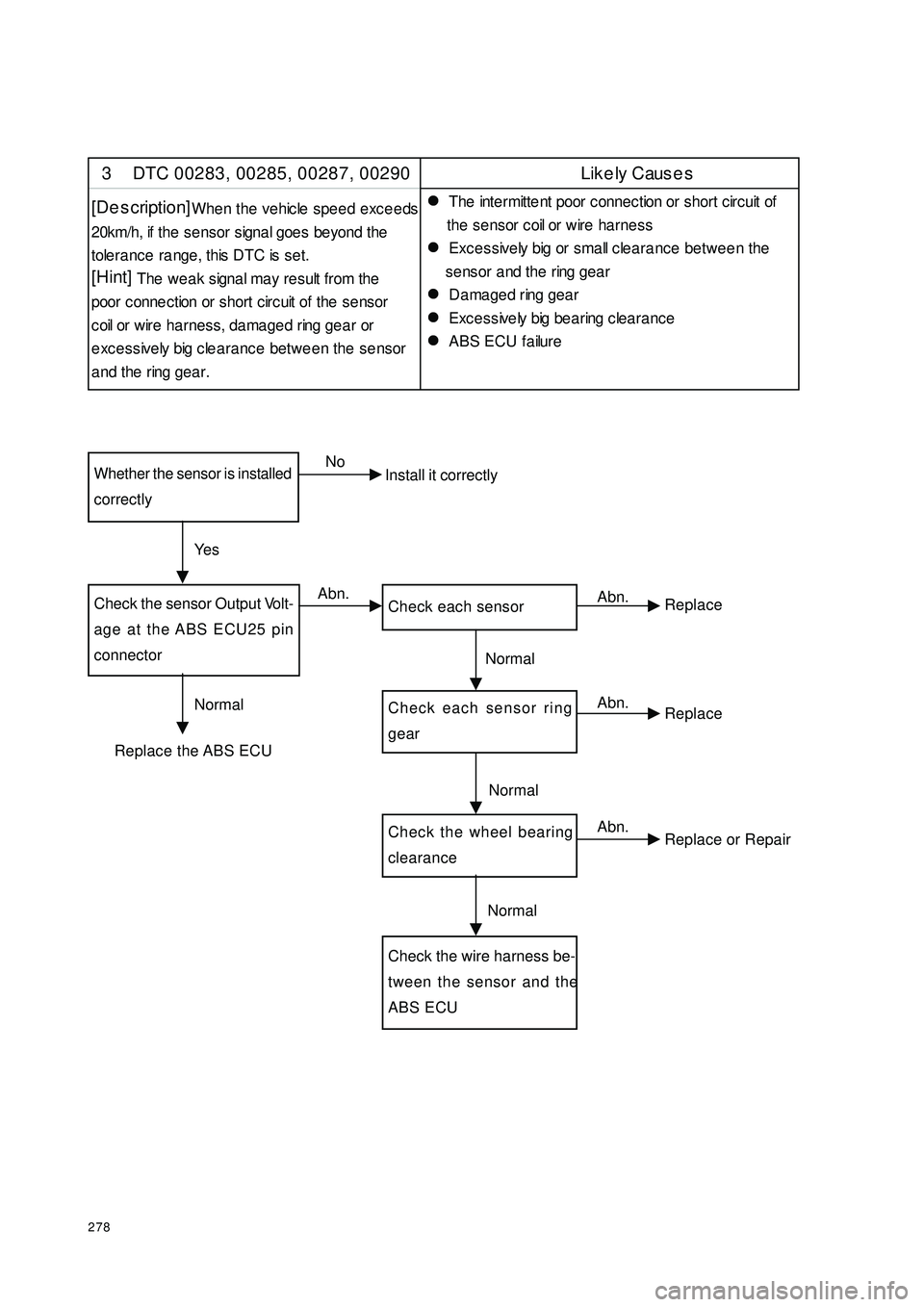
278Whether the sensor is installedcorrectlyCheck the sensor Output Volt-
age at the ABS ECU25 pin
connector Check each sensorCheck each sensor ringgearCheck the wheel bearing
clearance Check the wire harness be-
tween the sensor and the
ABS ECUNo
Install it correctly
Replace the ABS ECUAbn.
Abn.
Abn.
Abn. Ye s
Normal Normal
Normal
NormalReplace
Replace
Replace or Repair 3 DTC 00283, 00285, 00287, 00290 Likely Cause s
[De s cription]
When the vehicle speed exceeds
20km/h, if the se nsor signa l goe s be yond the
tolerance range, this DTC is set.
[Hint]
The we ak signa l ma y re sult from the
poor c onne c tion or short c irc uit of the se nsor
c oil or wire ha rness, da ma ge d ring gea r or
excessively big clearance between the sensor
a nd the ring gea r. z The inte rmitte nt poor connec tion or short circ uit of
the se nsor c oil or wire ha rne ss
z Excessively big or small clearance between the
se nsor a nd the ring gea r
z Da ma ge d ring gea r
z Exc e ssive ly big be a ring c lea ra nc e
z ABS ECU failure