Page 194 of 676
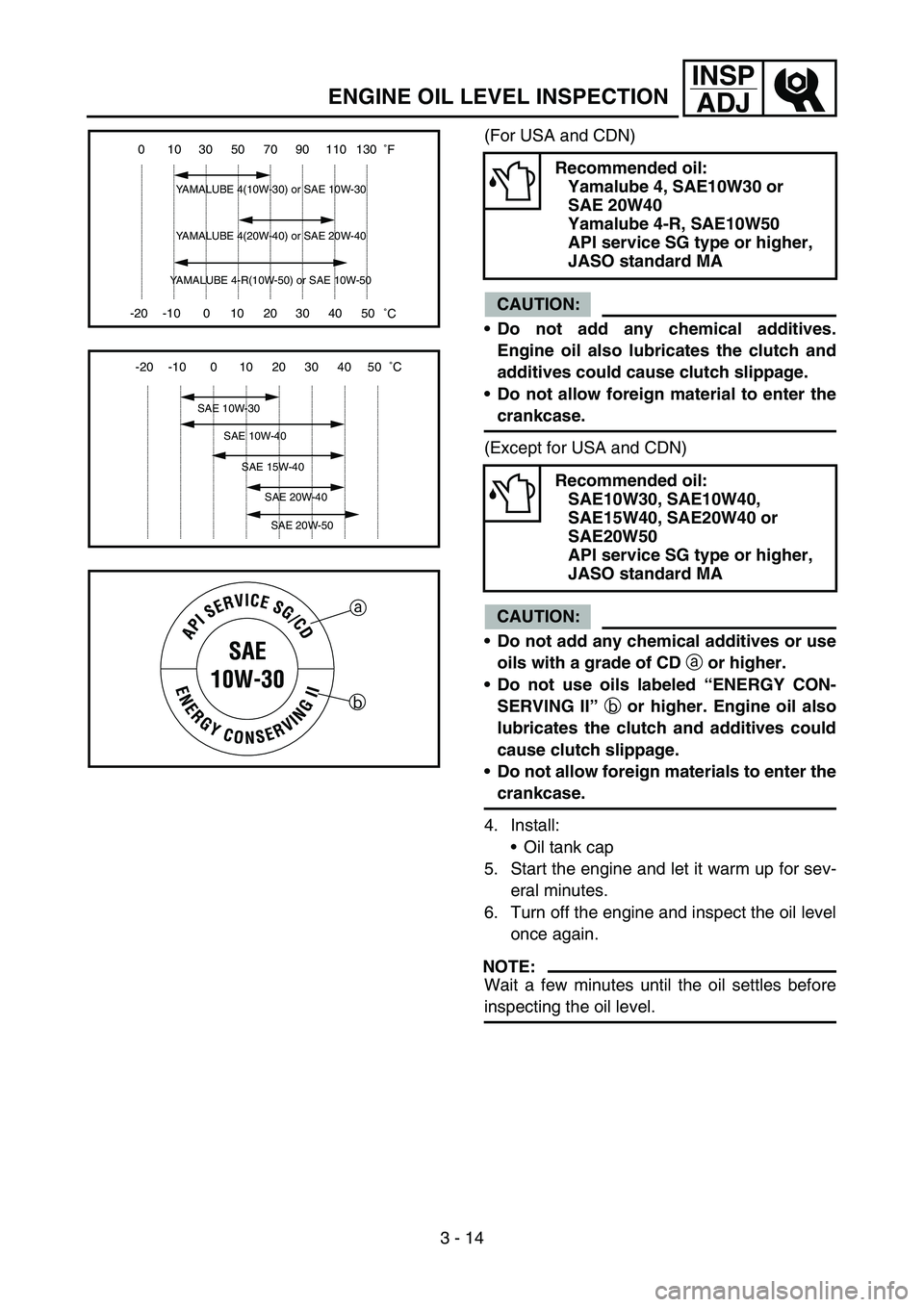
3 - 14
INSP
ADJ
ENGINE OIL LEVEL INSPECTION
(For USA and CDN)
CAUTION:
Do not add any chemical additives.
Engine oil also lubricates the clutch and
additives could cause clutch slippage.
Do not allow foreign material to enter the
crankcase.
(Except for USA and CDN)
CAUTION:
Do not add any chemical additives or use
oils with a grade of CD
a or higher.
Do not use oils labeled “ENERGY CON-
SERVING II”
b or higher. Engine oil also
lubricates the clutch and additives could
cause clutch slippage.
Do not allow foreign materials to enter the
crankcase.
4. Install:
Oil tank cap
5. Start the engine and let it warm up for sev-
eral minutes.
6. Turn off the engine and inspect the oil level
once again.
NOTE:
Wait a few minutes until the oil settles before
inspecting the oil level.
Recommended oil:
Yamalube 4, SAE10W30 or
SAE 20W40
Yamalube 4-R, SAE10W50
API service SG type or higher,
JASO standard MA
Recommended oil:
SAE10W30, SAE10W40,
SAE15W40, SAE20W40 or
SAE20W50
API service SG type or higher,
JASO standard MA
-20 -10 0 10 20 30 40 50
˚C 0 10 30 50 70 90 110 130
˚F
YAMALUBE 4(10W-30) or SAE 10W-30
YAMALUBE 4(20W-40) or SAE 20W-40
YAMALUBE 4-R(10W-50) or SAE 10W-50
-20 -10 0 10 20 30 40 50
˚C
SAE 10W-30
SAE 10W-40
SAE 15W-40
SAE 20W-40
SAE 20W-50
a
b
Page 196 of 676
3 - 15
INSP
ADJ
ENGINE OIL REPLACEMENT
ENGINE OIL REPLACEMENT
1. Start the engine and warm it up for several
minutes, and then turn off the engine and
wait for five minute.
2. Place the machine on a level place and
hold it on upright position by placing the
suitable stand under the engine.
3. Place a suitable container under the
engine.
4. Remove:
Lower engine guard 1
Bolt (oil tank) 2
Washer 3
Oil filler cap 4
Oil tank drain bolt 5
Crankcase oil drain bolt 6
Oil filter element drain bolt 7
Drain the crankcase and oil tank of its oil.
6
5
5. Remove:
Oil hose clamp 1
Bolt (oil hose)
Oil hose 2
Oil strainer 3
6. Inspect:
Oil strainer
Clogged → Blow.
3 1 2
Page 198 of 676
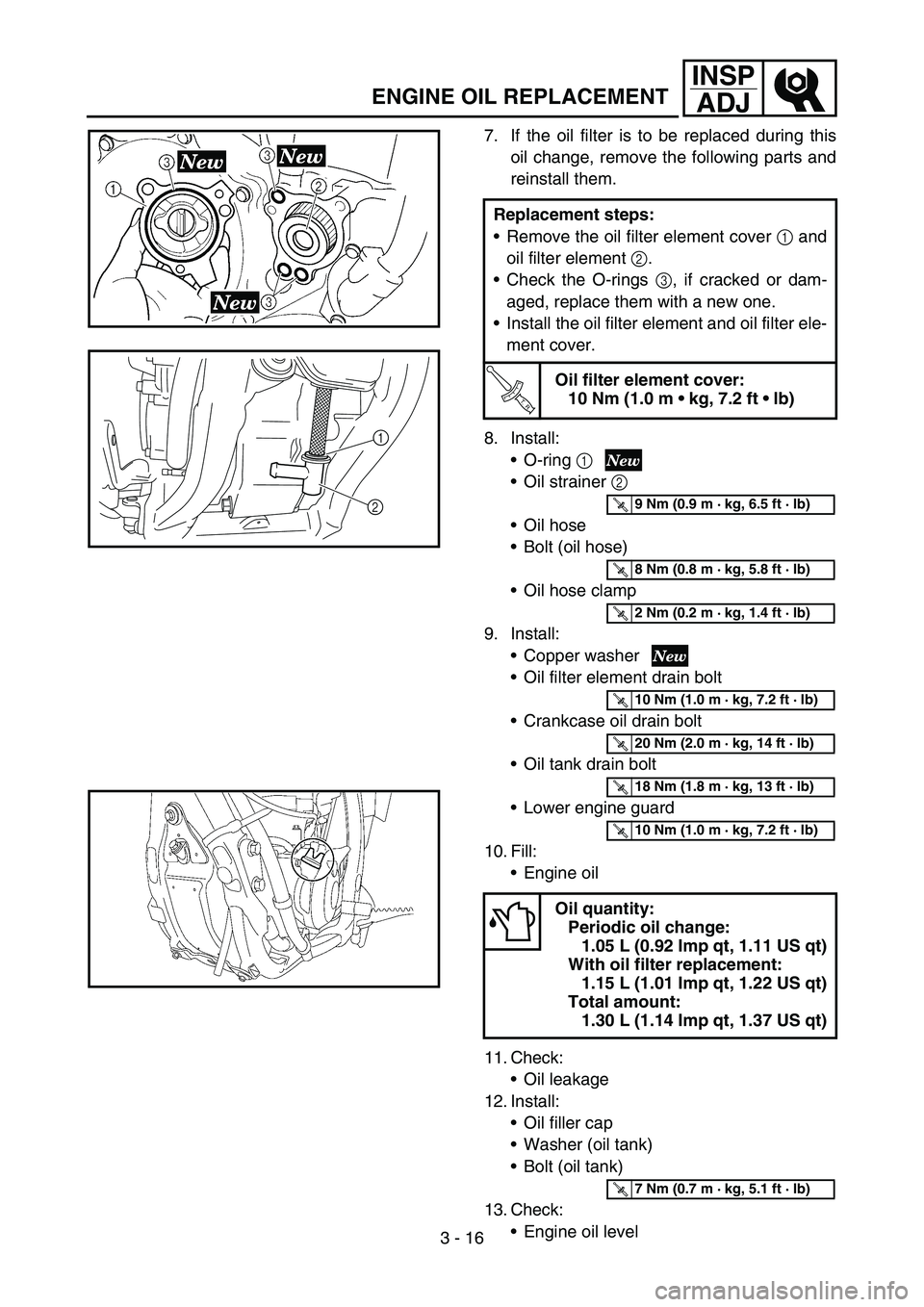
3 - 16
INSP
ADJ
ENGINE OIL REPLACEMENT
7. If the oil filter is to be replaced during this
oil change, remove the following parts and
reinstall them.
8. Install:
O-ring 1
Oil strainer 2
Oil hose
Bolt (oil hose)
Oil hose clamp
9. Install:
Copper washer
Oil filter element drain bolt
Crankcase oil drain bolt
Oil tank drain bolt
Lower engine guard
10. Fill:
Engine oil
11. Check:
Oil leakage
12. Install:
Oil filler cap
Washer (oil tank)
Bolt (oil tank)
13. Check:
Engine oil level Replacement steps:
Remove the oil filter element cover 1 and
oil filter element 2.
Check the O-rings 3, if cracked or dam-
aged, replace them with a new one.
Install the oil filter element and oil filter ele-
ment cover.
T R..
Oil filter element cover:
10 Nm (1.0 m kg, 7.2 ft lb)
Oil quantity:
Periodic oil change:
1.05 L (0.92 Imp qt, 1.11 US qt)
With oil filter replacement:
1.15 L (1.01 Imp qt, 1.22 US qt)
Total amount:
1.30 L (1.14 Imp qt, 1.37 US qt)
1
2
T R..9 Nm (0.9 m · kg, 6.5 ft · lb)
T R..8 Nm (0.8 m · kg, 5.8 ft · lb)
T R..2 Nm (0.2 m · kg, 1.4 ft · lb)
T R..10 Nm (1.0 m · kg, 7.2 ft · lb)
T R..20 Nm (2.0 m · kg, 14 ft · lb)
T R..18 Nm (1.8 m · kg, 13 ft · lb)
T R..10 Nm (1.0 m · kg, 7.2 ft · lb)
T R..7 Nm (0.7 m · kg, 5.1 ft · lb)
Page 200 of 676
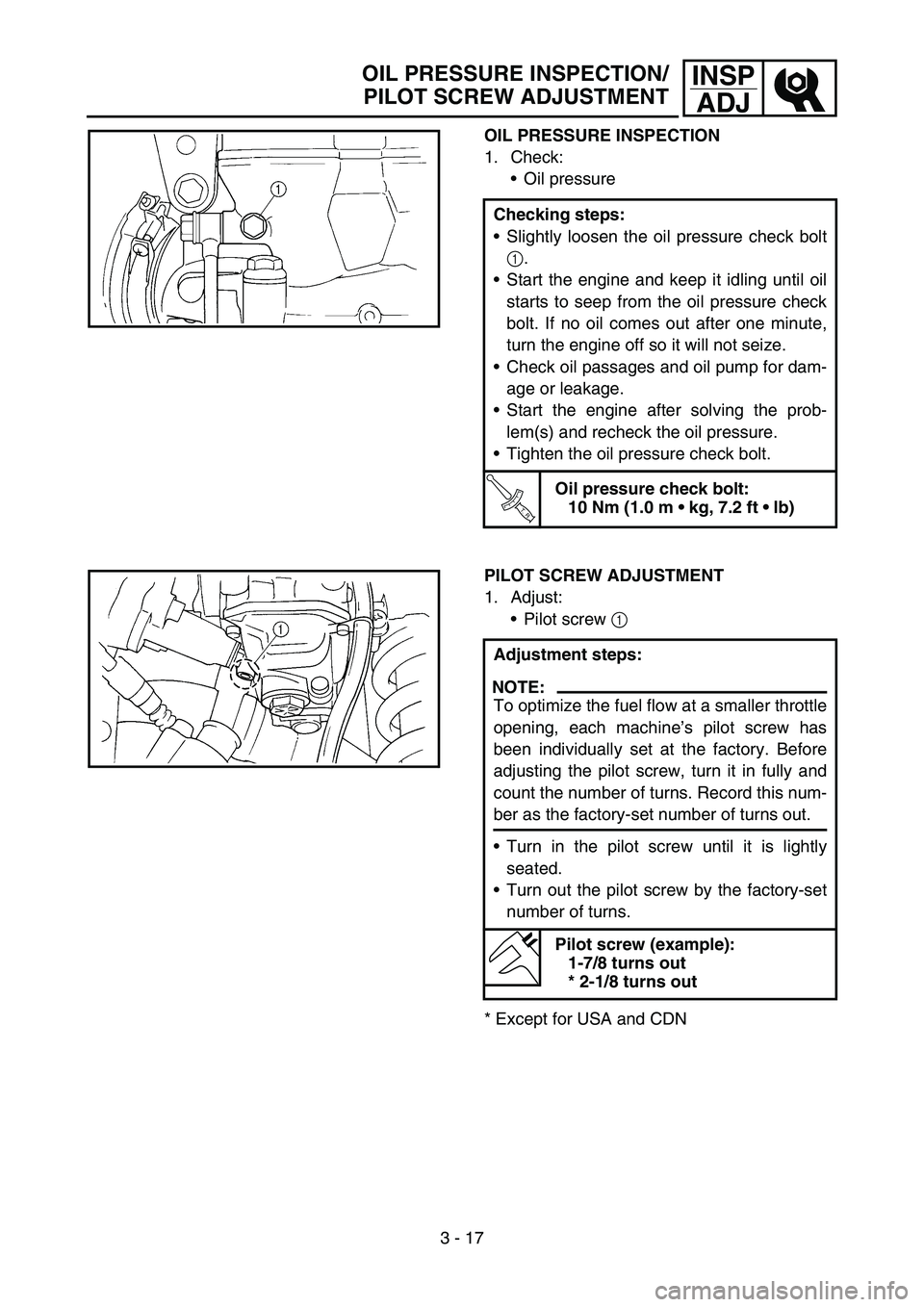
3 - 17
INSP
ADJ
OIL PRESSURE INSPECTION
1. Check:
Oil pressure
Checking steps:
Slightly loosen the oil pressure check bolt
1.
Start the engine and keep it idling until oil
starts to seep from the oil pressure check
bolt. If no oil comes out after one minute,
turn the engine off so it will not seize.
Check oil passages and oil pump for dam-
age or leakage.
Start the engine after solving the prob-
lem(s) and recheck the oil pressure.
Tighten the oil pressure check bolt.
T R..
Oil pressure check bolt:
10 Nm (1.0 m kg, 7.2 ft lb)
PILOT SCREW ADJUSTMENT
1. Adjust:
Pilot screw 1
* Except for USA and CDNAdjustment steps:
NOTE:
To optimize the fuel flow at a smaller throttle
opening, each machine’s pilot screw has
been individually set at the factory. Before
adjusting the pilot screw, turn it in fully and
count the number of turns. Record this num-
ber as the factory-set number of turns out.
Turn in the pilot screw until it is lightly
seated.
Turn out the pilot screw by the factory-set
number of turns.
Pilot screw (example):
1-7/8 turns out
* 2-1/8 turns out
OIL PRESSURE INSPECTION/
PILOT SCREW ADJUSTMENT
Page 202 of 676
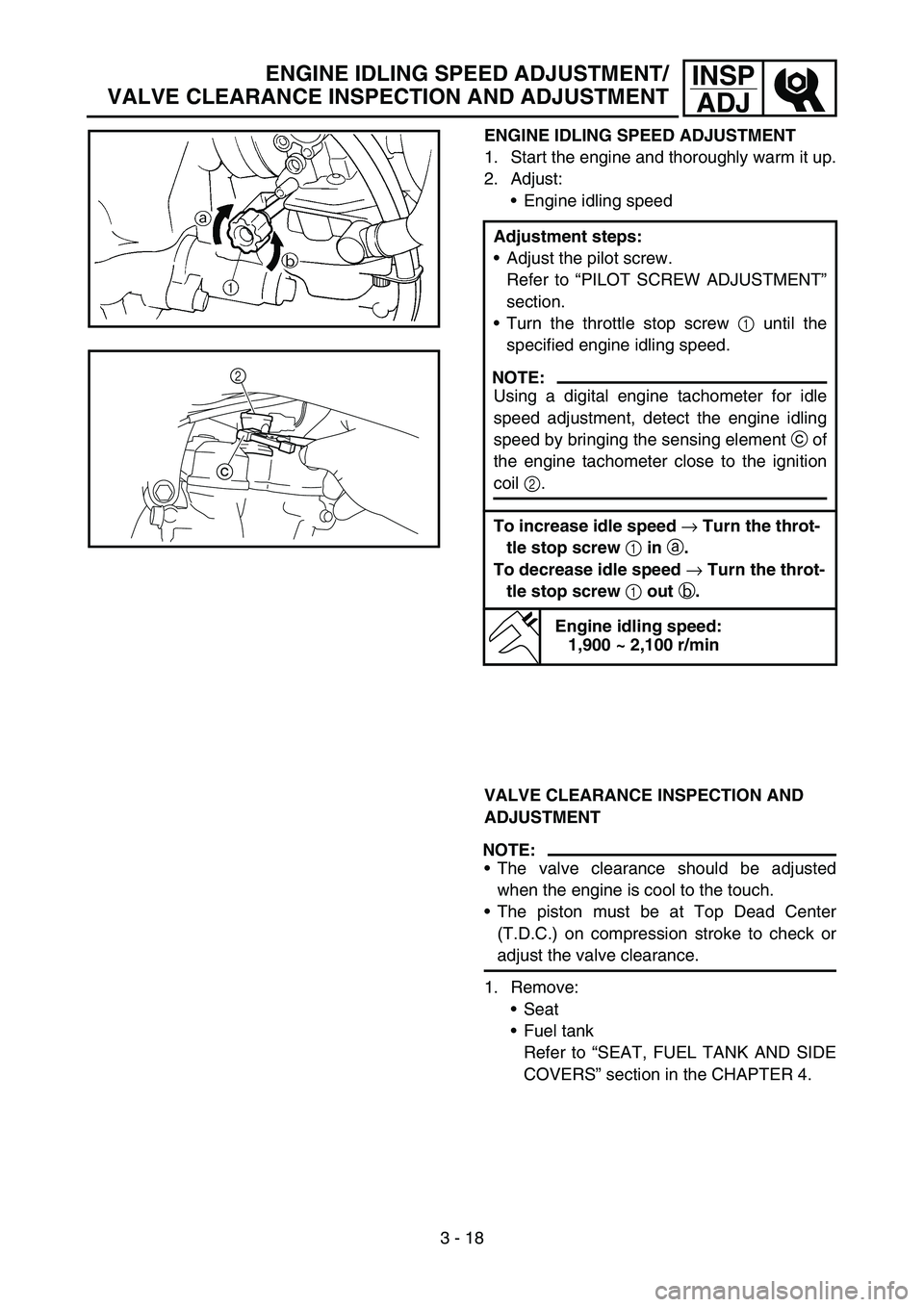
3 - 18
INSP
ADJ
ENGINE IDLING SPEED ADJUSTMENT
1. Start the engine and thoroughly warm it up.
2. Adjust:
Engine idling speed
Adjustment steps:
Adjust the pilot screw.
Refer to “PILOT SCREW ADJUSTMENT”
section.
Turn the throttle stop screw 1 until the
specified engine idling speed.
NOTE:
Using a digital engine tachometer for idle
speed adjustment, detect the engine idling
speed by bringing the sensing element c of
the engine tachometer close to the ignition
coil 2.
To increase idle speed → Turn the throt-
tle stop screw 1 in a.
To decrease idle speed → Turn the throt-
tle stop screw 1 out b.
Engine idling speed:
1,900 ~ 2,100 r/min
c2
VALVE CLEARANCE INSPECTION AND
ADJUSTMENT
NOTE:
The valve clearance should be adjusted
when the engine is cool to the touch.
The piston must be at Top Dead Center
(T.D.C.) on compression stroke to check or
adjust the valve clearance.
1. Remove:
Seat
Fuel tank
Refer to “SEAT, FUEL TANK AND SIDE
COVERS” section in the CHAPTER 4.
ENGINE IDLING SPEED ADJUSTMENT/
VALVE CLEARANCE INSPECTION AND ADJUSTMENT
Page 208 of 676
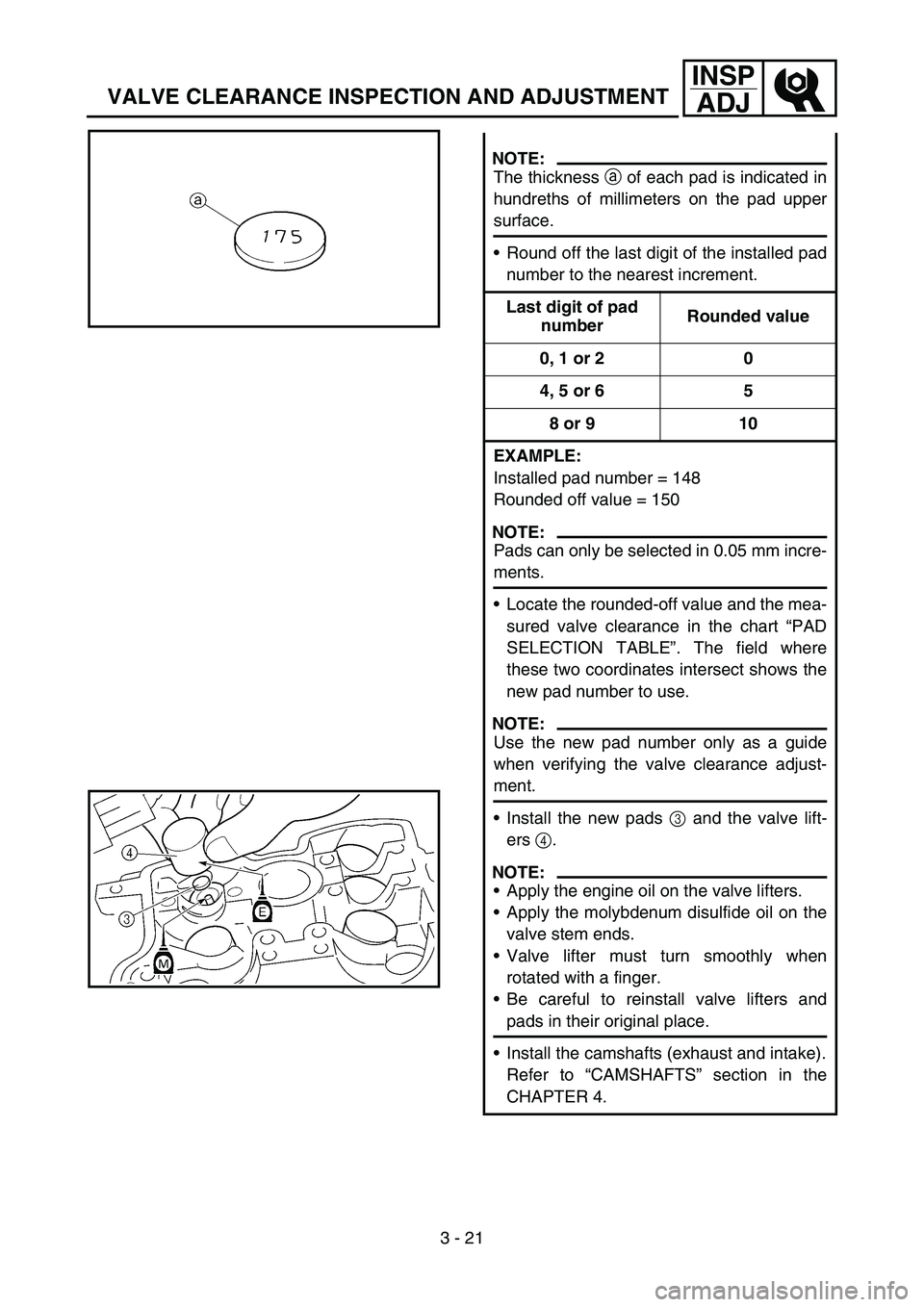
3 - 21
INSP
ADJ
VALVE CLEARANCE INSPECTION AND ADJUSTMENT
NOTE:
The thickness a of each pad is indicated in
hundreths of millimeters on the pad upper
surface.
Round off the last digit of the installed pad
number to the nearest increment.
Last digit of pad
numberRounded value
0, 1 or 2 0
4, 5 or 6 5
8 or 9 10
EXAMPLE:
Installed pad number = 148
Rounded off value = 150
NOTE:
Pads can only be selected in 0.05 mm incre-
ments.
Locate the rounded-off value and the mea-
sured valve clearance in the chart “PAD
SELECTION TABLE”. The field where
these two coordinates intersect shows the
new pad number to use.
NOTE:
Use the new pad number only as a guide
when verifying the valve clearance adjust-
ment.
Install the new pads 3 and the valve lift-
ers 4.
NOTE:
Apply the engine oil on the valve lifters.
Apply the molybdenum disulfide oil on the
valve stem ends.
Valve lifter must turn smoothly when
rotated with a finger.
Be careful to reinstall valve lifters and
pads in their original place.
Install the camshafts (exhaust and intake).
Refer to “CAMSHAFTS” section in the
CHAPTER 4.
Page 230 of 676
3 - 31
INSP
ADJ
DRIVE CHAIN SLACK ADJUSTMENT
4. Check:
Drive chain stiffness a
Clean and oil the drive chain and hold as
illustrated.
Stiff → Replace drive chain.
5. Install:
Drive chain 1
Joint 2
Master link clip 3
CAUTION:
Be sure to install the master link clip to the
direction as shown.
aTurning direction
6. Lubricate:
Drive chain
Drive chain lubricant:
SAE 10W-30 motor oil or
suitable chain lubricants
DRIVE CHAIN SLACK ADJUSTMENT
1. Elevate the rear wheel by placing the suit-
able stand under the engine.
2. Check:
Drive chain slack a
Above the seal guard installation bolt.
Out of specification → Adjust.
NOTE:
Before checking and/or adjusting, rotate the
rear wheel through several revolutions and
check the slack several times to find the tight-
est point. Check and/or adjust the drive chain
slack with the rear wheel in this “tight chain”
position.
Drive chain slack:
48 ~ 58 mm (1.9 ~ 2.3 in)
Page 232 of 676
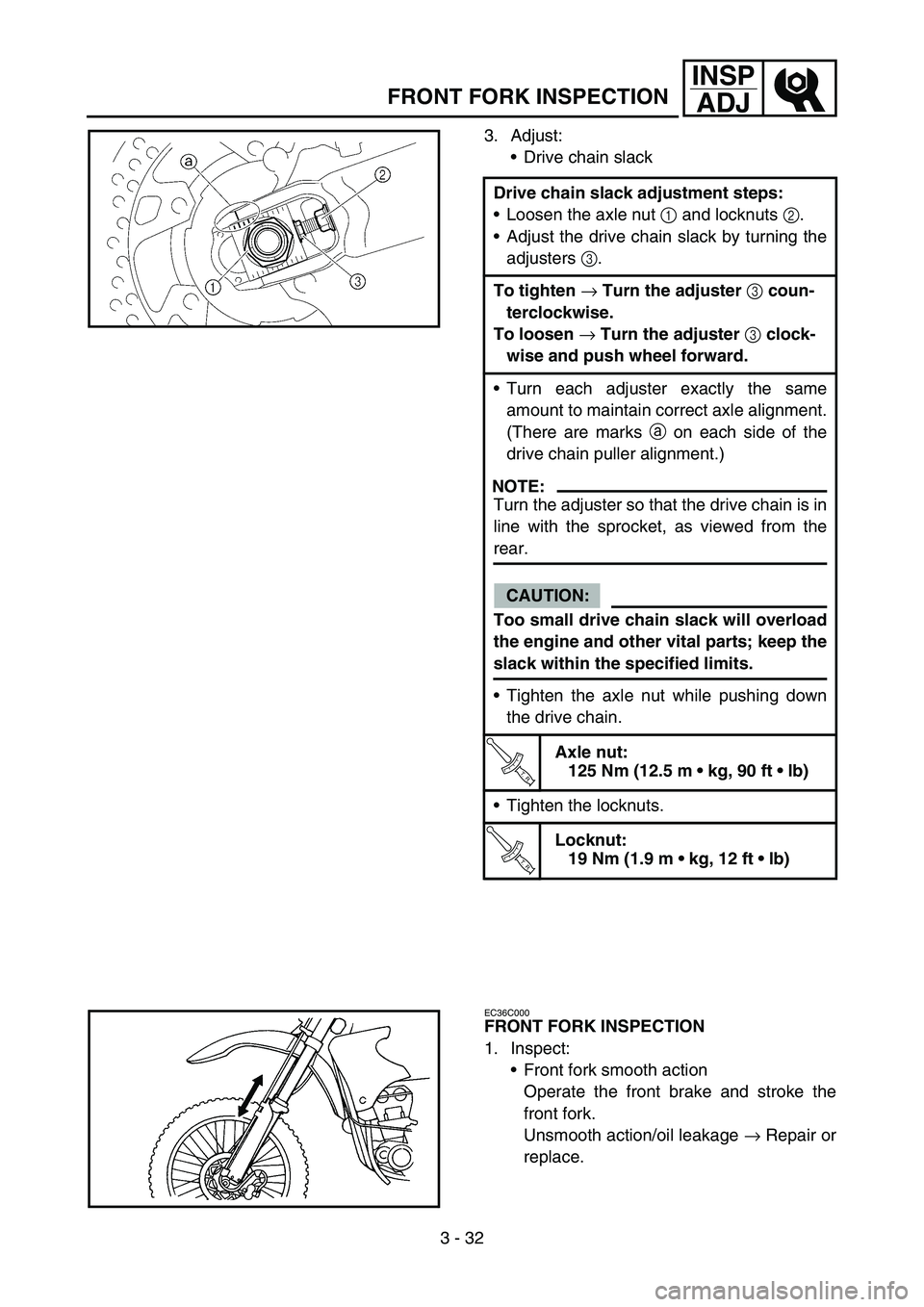
3 - 32
INSP
ADJ
FRONT FORK INSPECTION
3. Adjust:
Drive chain slack
Drive chain slack adjustment steps:
Loosen the axle nut 1 and locknuts 2.
Adjust the drive chain slack by turning the
adjusters 3.
To tighten
→ Turn the adjuster
3 coun-
terclockwise.
To loosen
→ Turn the adjuster
3 clock-
wise and push wheel forward.
Turn each adjuster exactly the same
amount to maintain correct axle alignment.
(There are marks a on each side of the
drive chain puller alignment.)
NOTE:
Turn the adjuster so that the drive chain is in
line with the sprocket, as viewed from the
rear.
CAUTION:
Too small drive chain slack will overload
the engine and other vital parts; keep the
slack within the specified limits.
Tighten the axle nut while pushing down
the drive chain.
T R..
Axle nut:
125 Nm (12.5 m kg, 90 ft lb)
Tighten the locknuts.
T R..
Locknut:
19 Nm (1.9 m kg, 12 ft lb)
EC36C000
FRONT FORK INSPECTION
1. Inspect:
Front fork smooth action
Operate the front brake and stroke the
front fork.
Unsmooth action/oil leakage → Repair or
replace.