Page 234 of 676
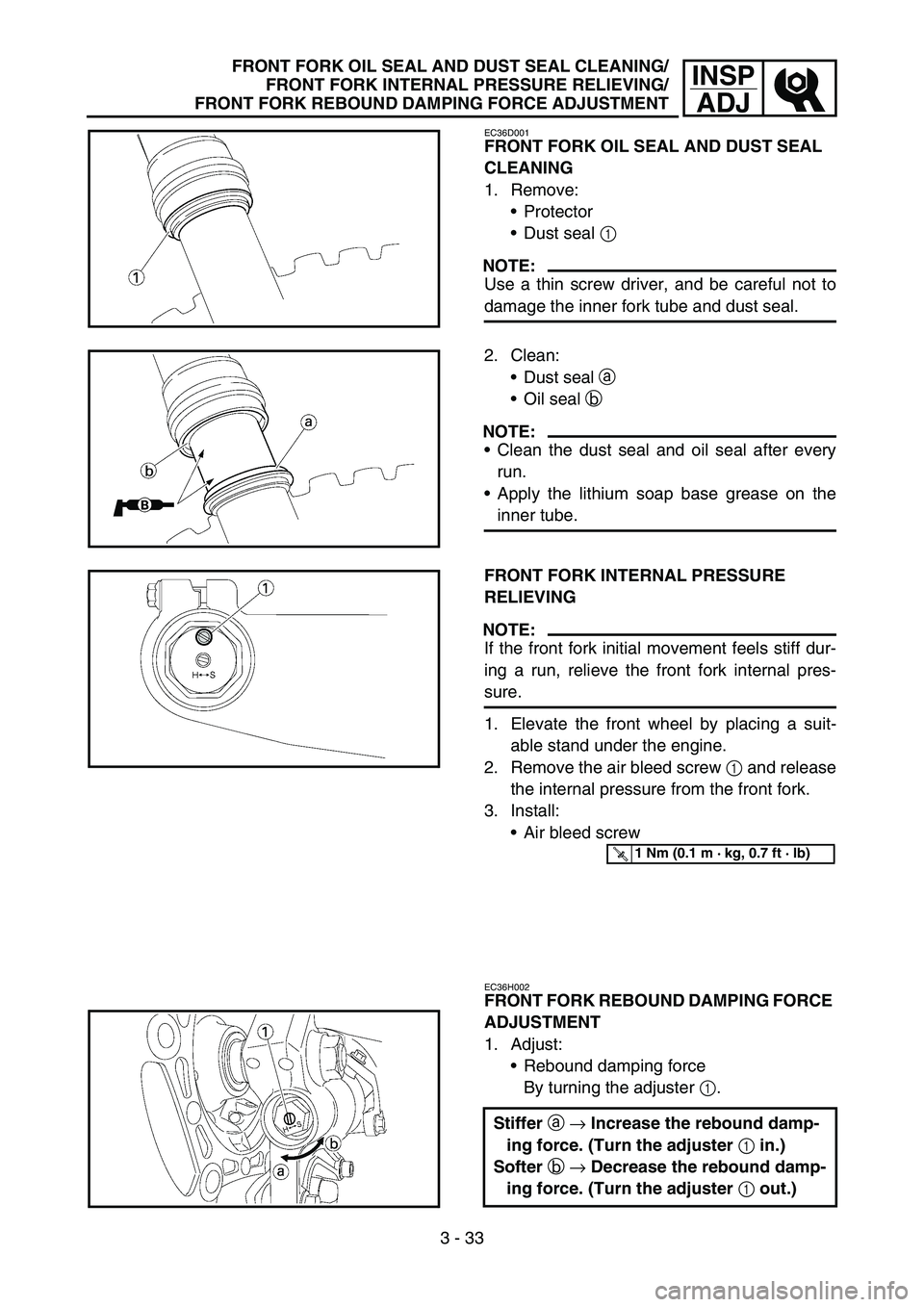
3 - 33
INSP
ADJFRONT FORK OIL SEAL AND DUST SEAL CLEANING/
FRONT FORK INTERNAL PRESSURE RELIEVING/
FRONT FORK REBOUND DAMPING FORCE ADJUSTMENT
EC36D001
FRONT FORK OIL SEAL AND DUST SEAL
CLEANING
1. Remove:
Protector
Dust seal 1
NOTE:
Use a thin screw driver, and be careful not to
damage the inner fork tube and dust seal.
2. Clean:
Dust seal a
Oil seal b
NOTE:
Clean the dust seal and oil seal after every
run.
Apply the lithium soap base grease on the
inner tube.
FRONT FORK INTERNAL PRESSURE
RELIEVING
NOTE:
If the front fork initial movement feels stiff dur-
ing a run, relieve the front fork internal pres-
sure.
1. Elevate the front wheel by placing a suit-
able stand under the engine.
2. Remove the air bleed screw 1 and release
the internal pressure from the front fork.
3. Install:
Air bleed screw
EC36H002
FRONT FORK REBOUND DAMPING FORCE
ADJUSTMENT
1. Adjust:
Rebound damping force
By turning the adjuster 1.
Stiffer a → Increase the rebound damp-
ing force. (Turn the adjuster 1 in.)
Softer b → Decrease the rebound damp-
ing force. (Turn the adjuster 1 out.)
T R..1 Nm (0.1 m · kg, 0.7 ft · lb)
Page 240 of 676
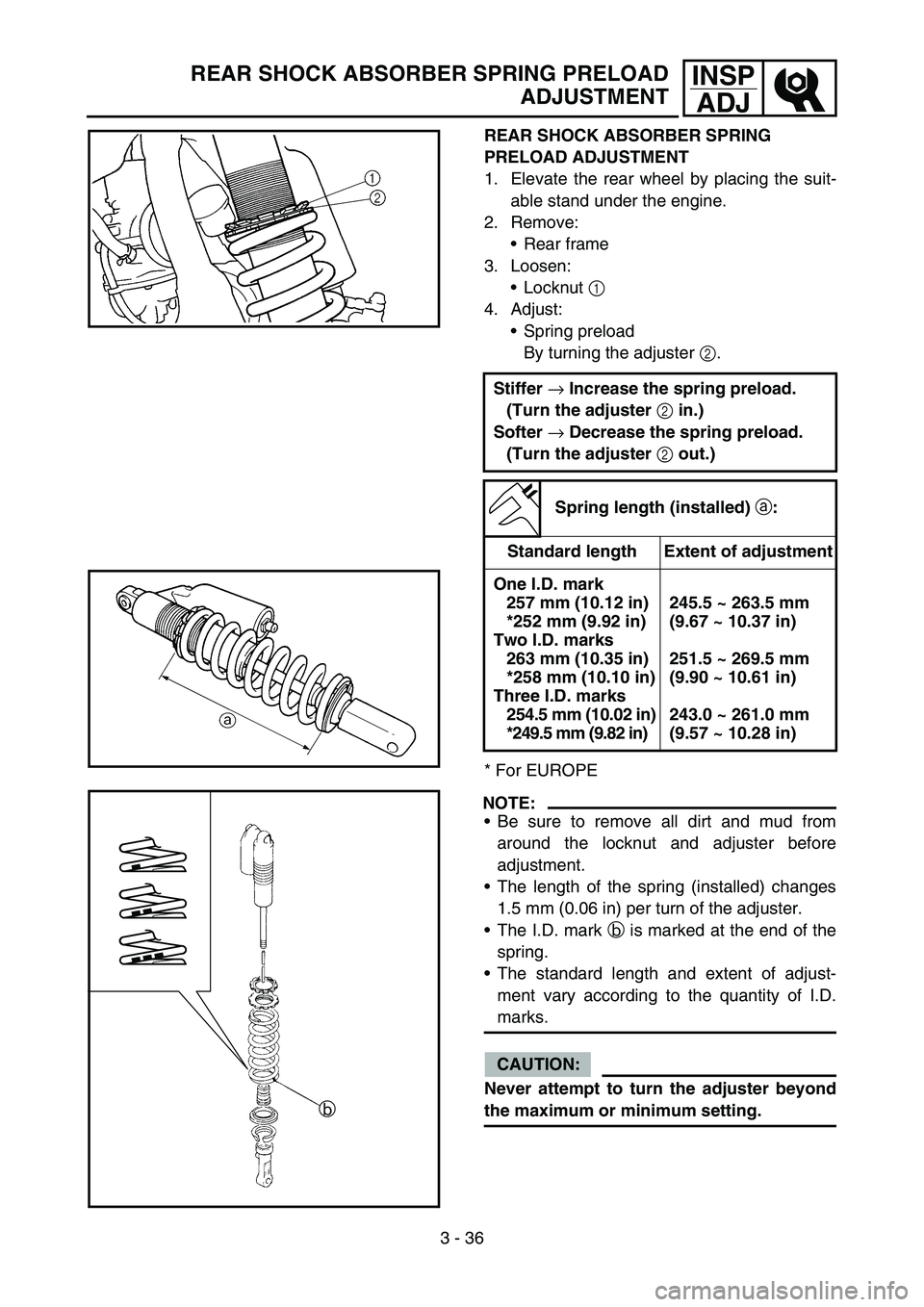
3 - 36
INSP
ADJREAR SHOCK ABSORBER SPRING PRELOAD
ADJUSTMENT
REAR SHOCK ABSORBER SPRING
PRELOAD ADJUSTMENT
1. Elevate the rear wheel by placing the suit-
able stand under the engine.
2. Remove:
Rear frame
3. Loosen:
Locknut 1
4. Adjust:
Spring preload
By turning the adjuster 2.
* For EUROPE
NOTE:
Be sure to remove all dirt and mud from
around the locknut and adjuster before
adjustment.
The length of the spring (installed) changes
1.5 mm (0.06 in) per turn of the adjuster.
The I.D. mark b is marked at the end of the
spring.
The standard length and extent of adjust-
ment vary according to the quantity of I.D.
marks.
CAUTION:
Never attempt to turn the adjuster beyond
the maximum or minimum setting.Stiffer
→ Increase the spring preload.
(Turn the adjuster
2 in.)
Softer
→ Decrease the spring preload.
(Turn the adjuster
2 out.)
Spring length (installed)
a:
Standard length Extent of adjustment
One I.D. mark
257 mm (10.12 in)
*252 mm (9.92 in)
Two I.D. marks
263 mm (10.35 in)
*258 mm (10.10 in)
Three I.D. marks
254.5 mm (10.02 in)
*249.5 mm (9.82 in)245.5 ~ 263.5 mm
(9.67 ~ 10.37 in)
251.5 ~ 269.5 mm
(9.90 ~ 10.61 in)
243.0 ~ 261.0 mm
(9.57 ~ 10.28 in)
b
Page 250 of 676
3 - 41
INSP
ADJ
STEERING HEAD INSPECTION AND ADJUSTMENT
2. Inspect:
Bearing free play
Exist play → Replace.
EC36U013
STEERING HEAD INSPECTION AND
ADJUSTMENT
1. Elevate the front wheel by placing a suit-
able stand under the engine.
2. Check:
Steering stem
Grasp the bottom of the forks and gently
rock the fork assembly back and forth.
Free play → Adjust steering head.
3. Check:
Steering smooth action
Turn the handlebar lock to lock.
Unsmooth action → Adjust steering ring
nut.
4. Adjust:
Steering ring nut
Steering ring nut adjustment steps:
Remove the number plate.
Remove the handlebar and upper bracket.
Loosen the steering ring nut 1 using the
steering nut wrench 2.
Steering nut wrench:
YU-33975/90890-01403
Page 258 of 676
3 - 45
INSP
ADJ
ELECTRICAL/SPARK PLUG INSPECTION
EC370000
ELECTRICAL
EC371001
SPARK PLUG INSPECTION
1. Remove:
Spark plug
2. Inspect:
Electrode 1
Wear/damage → Replace.
Insulator color 2
Normal condition is a medium to light tan
color.
Distinctly different color → Check the
engine condition.
NOTE:
When the engine runs for many hours at low
speeds, the spark plug insulator will become
sooty, even if the engine and carburetor are in
good operating condition.
3. Measure:
Plug gap a
Use a wire gauge or thickness gauge.
Out of specification → Regap.
4. Clean the plug with a spark plug cleaner if
necessary.
Spark plug gap:
0.7 ~ 0.8 mm (0.028 ~ 0.031 in)
5. Tighten:
Spark plug
NOTE:
Before installing a spark plug, clean the gas-
ket surface and plug surface.
Finger-tighten a the spark plug before torqu-
ing to specification b.
T R..13 Nm (1.3 m · kg, 9.4 ft · lb)
Page 260 of 676
3 - 46
INSP
ADJ
IGNITION TIMING CHECK
IGNITION TIMING CHECK
1. Remove:
Timing mark accessing screw 1
2. Attach:
Timing light
Inductive tachometer
To the ignition coil lead (orange lead 1).
Timing light:
YM-33277-A/90890-03141
1
3. Adjust:
Engine idling speed
Refer to “ENGINE IDLING SPEED
ADJUSTMENT” section.
4. Check:
Ignition timing
Visually check the stationary pointer a is
within the firing range b on the rotor.
Incorrect firing range → Check rotor and
pickup assembly.
5. Install:
Timing mark accessing screw
Page 262 of 676
4 - 1
ENG
EC400000
ENGINE
SEAT, FUEL TANK AND SIDE COVERS
Extent of removal:
1 Seat removal
2 Fuel tank removal
3 Side covers removal
4 Number plate removal
Extent of removal Order Part name Q’ty Remarks
SEAT, FUEL TANK AND SIDE
COVERS REMOVAL
Preparation for removal Turn the fuel cock to “OFF”.
Disconnect the fuel hose.
1Seat 1
2 Air scoop (left and right) 2
3 Bolt (fuel tank) 2
4 Fuel tank 1
5 Left side cover 1
Refer to “REMOVAL POINTS”. 6 Right side cover 1
7 Number plate 1
4
2
1
3
3
SEAT, FUEL TANK AND SIDE COVERS
4
Page 274 of 676
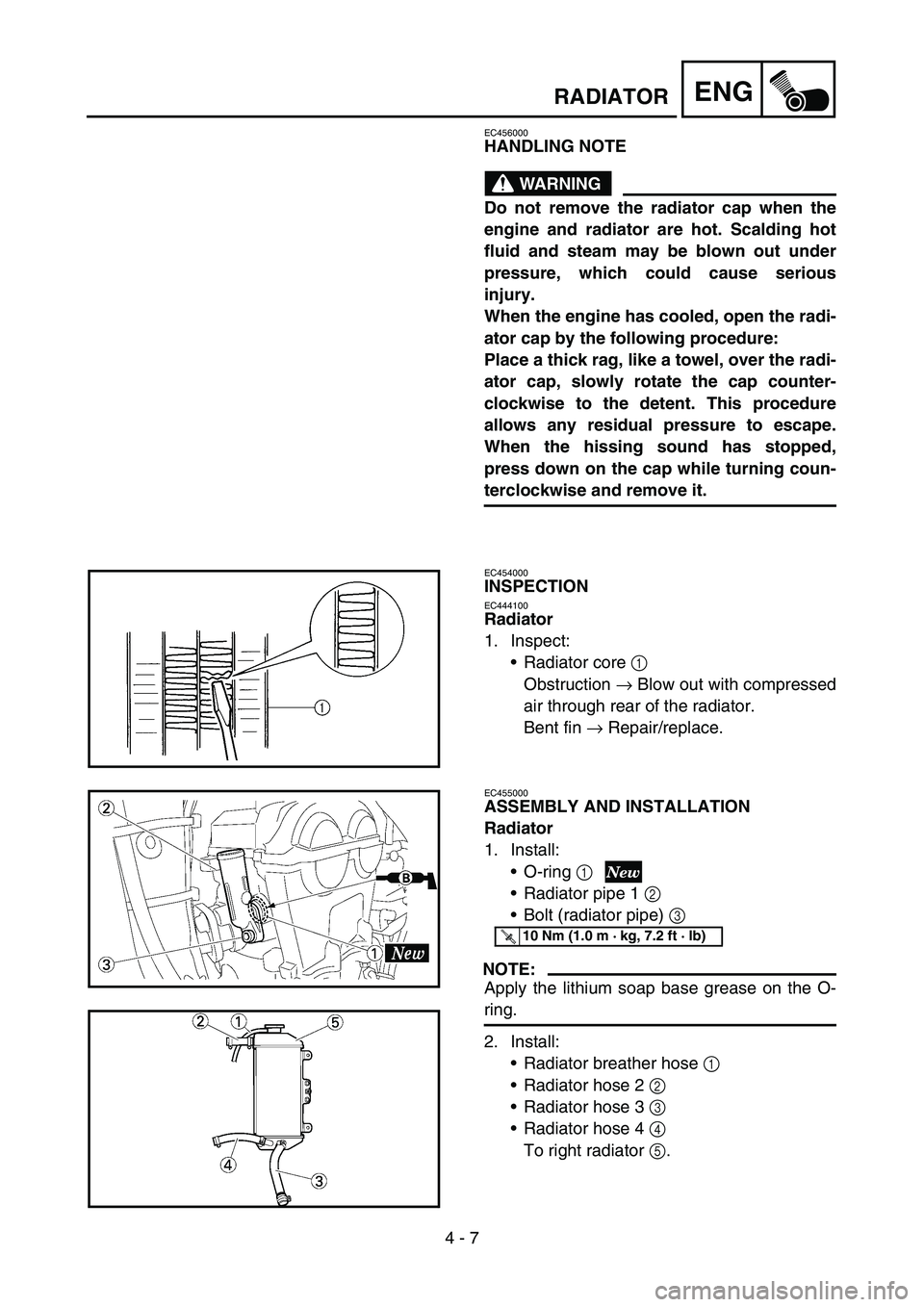
4 - 7
ENGRADIATOR
EC456000
HANDLING NOTE
WARNING
Do not remove the radiator cap when the
engine and radiator are hot. Scalding hot
fluid and steam may be blown out under
pressure, which could cause serious
injury.
When the engine has cooled, open the radi-
ator cap by the following procedure:
Place a thick rag, like a towel, over the radi-
ator cap, slowly rotate the cap counter-
clockwise to the detent. This procedure
allows any residual pressure to escape.
When the hissing sound has stopped,
press down on the cap while turning coun-
terclockwise and remove it.
EC454000
INSPECTION
EC444100
Radiator
1. Inspect:
Radiator core 1
Obstruction → Blow out with compressed
air through rear of the radiator.
Bent fin → Repair/replace.
EC455000
ASSEMBLY AND INSTALLATION
Radiator
1. Install:
O-ring 1
Radiator pipe 1 2
Bolt (radiator pipe) 3
NOTE:
Apply the lithium soap base grease on the O-
ring.
2. Install:
Radiator breather hose 1
Radiator hose 2 2
Radiator hose 3 3
Radiator hose 4 4
To right radiator 5.
T R..10 Nm (1.0 m · kg, 7.2 ft · lb)
Page 284 of 676
4 - 12
ENGCARBURETOR
HANDLING NOTE
CAUTION:
Do not loosen the screws (throttle position
sensor)
1 except when changing the throt-
tle position sensor due to failure because it
will cause a drop in engine performance.
1
REMOVAL POINTS
Pilot screw
1. Remove:
Pilot screw 1
NOTE:
To optimize the fuel flow at a small throttle
opening, each machine’s pilot screw has been
individually set at the factory. Before removing
the pilot screw, turn it in fully and count the
number of turns. Record this number as the
factory-set number of turns out.
INSPECTION
Carburetor
1. Inspect:
Carburetor body
Contamination → Clean.
NOTE:
Use a petroleum based solvent for cleaning.
Blow out all passages and jets with com-
pressed air.
Never use a wire.