Page 3094 of 4647
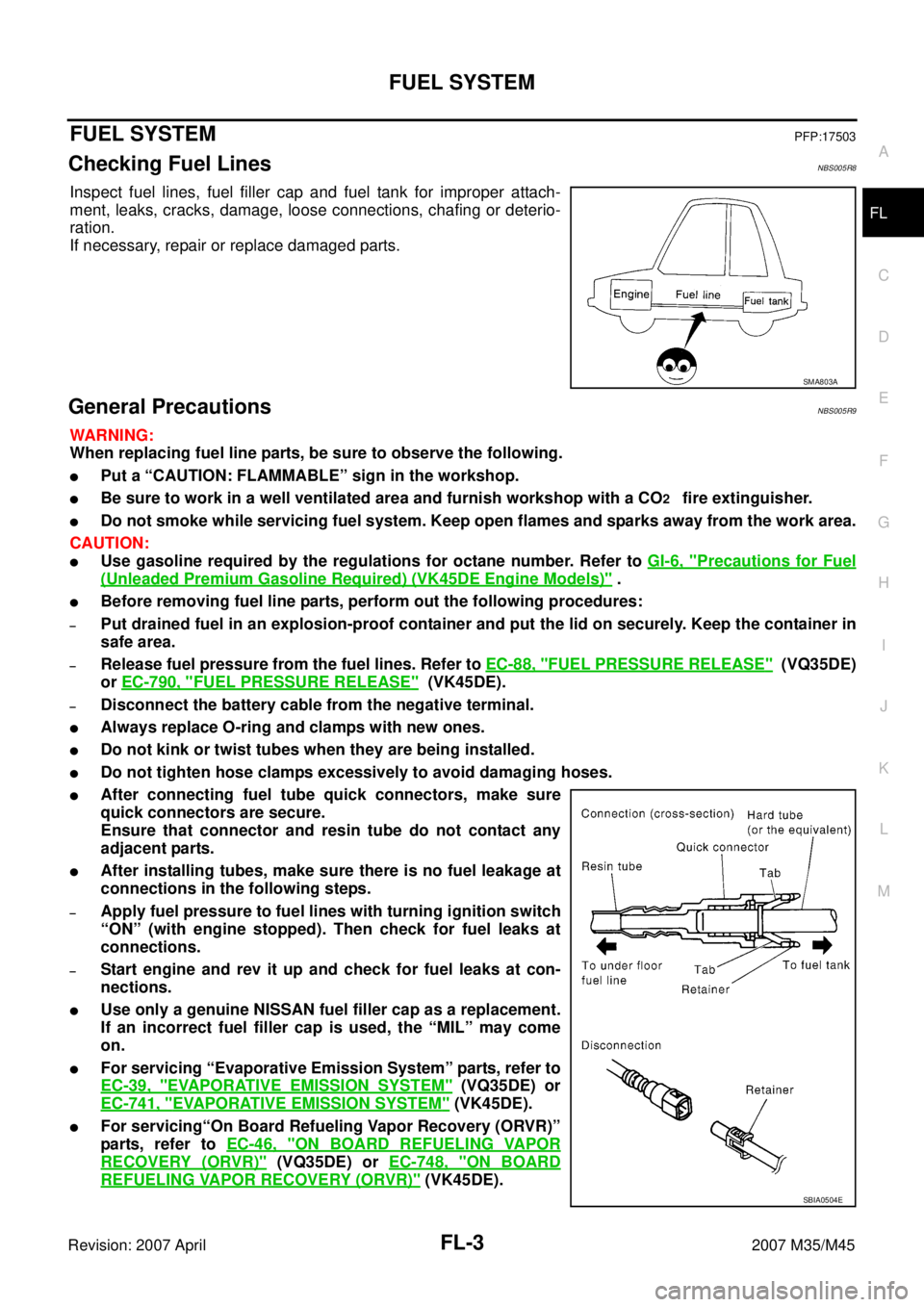
FUEL SYSTEM
FL-3
C
D
E
F
G
H
I
J
K
L
MA
FL
Revision: 2007 April2007 M35/M45
FUEL SYSTEMPFP:17503
Checking Fuel LinesNBS005R8
Inspect fuel lines, fuel filler cap and fuel tank for improper attach-
ment, leaks, cracks, damage, loose connections, chafing or deterio-
ration.
If necessary, repair or replace damaged parts.
General PrecautionsNBS005R9
WARNING:
When replacing fuel line parts, be sure to observe the following.
Put a “CAUTION: FLAMMABLE” sign in the workshop.
Be sure to work in a well ventilated area and furnish workshop with a CO2 fire extinguisher.
Do not smoke while servicing fuel system. Keep open flames and sparks away from the work area.
CAUTION:
Use gasoline required by the regulations for octane number. Refer to GI-6, "Precautions for Fuel
(Unleaded Premium Gasoline Required) (VK45DE Engine Models)" .
Before removing fuel line parts, perform out the following procedures:
–Put drained fuel in an explosion-proof container and put the lid on securely. Keep the container in
safe area.
–Release fuel pressure from the fuel lines. Refer to EC-88, "FUEL PRESSURE RELEASE" (VQ35DE)
or EC-790, "
FUEL PRESSURE RELEASE" (VK45DE).
–Disconnect the battery cable from the negative terminal.
Always replace O-ring and clamps with new ones.
Do not kink or twist tubes when they are being installed.
Do not tighten hose clamps excessively to avoid damaging hoses.
After connecting fuel tube quick connectors, make sure
quick connectors are secure.
Ensure that connector and resin tube do not contact any
adjacent parts.
After installing tubes, make sure there is no fuel leakage at
connections in the following steps.
–Apply fuel pressure to fuel lines with turning ignition switch
“ON” (with engine stopped). Then check for fuel leaks at
connections.
–Start engine and rev it up and check for fuel leaks at con-
nections.
Use only a genuine NISSAN fuel filler cap as a replacement.
If an incorrect fuel filler cap is used, the “MIL” may come
on.
For servicing “Evaporative Emission System” parts, refer to
EC-39, "
EVAPORATIVE EMISSION SYSTEM" (VQ35DE) or
EC-741, "
EVAPORATIVE EMISSION SYSTEM" (VK45DE).
For servicing“On Board Refueling Vapor Recovery (ORVR)”
parts, refer to EC-46, "
ON BOARD REFUELING VAPOR
RECOVERY (ORVR)" (VQ35DE) or EC-748, "ON BOARD
REFUELING VAPOR RECOVERY (ORVR)" (VK45DE).
SMA803A
SBIA0504E
Page 3099 of 4647
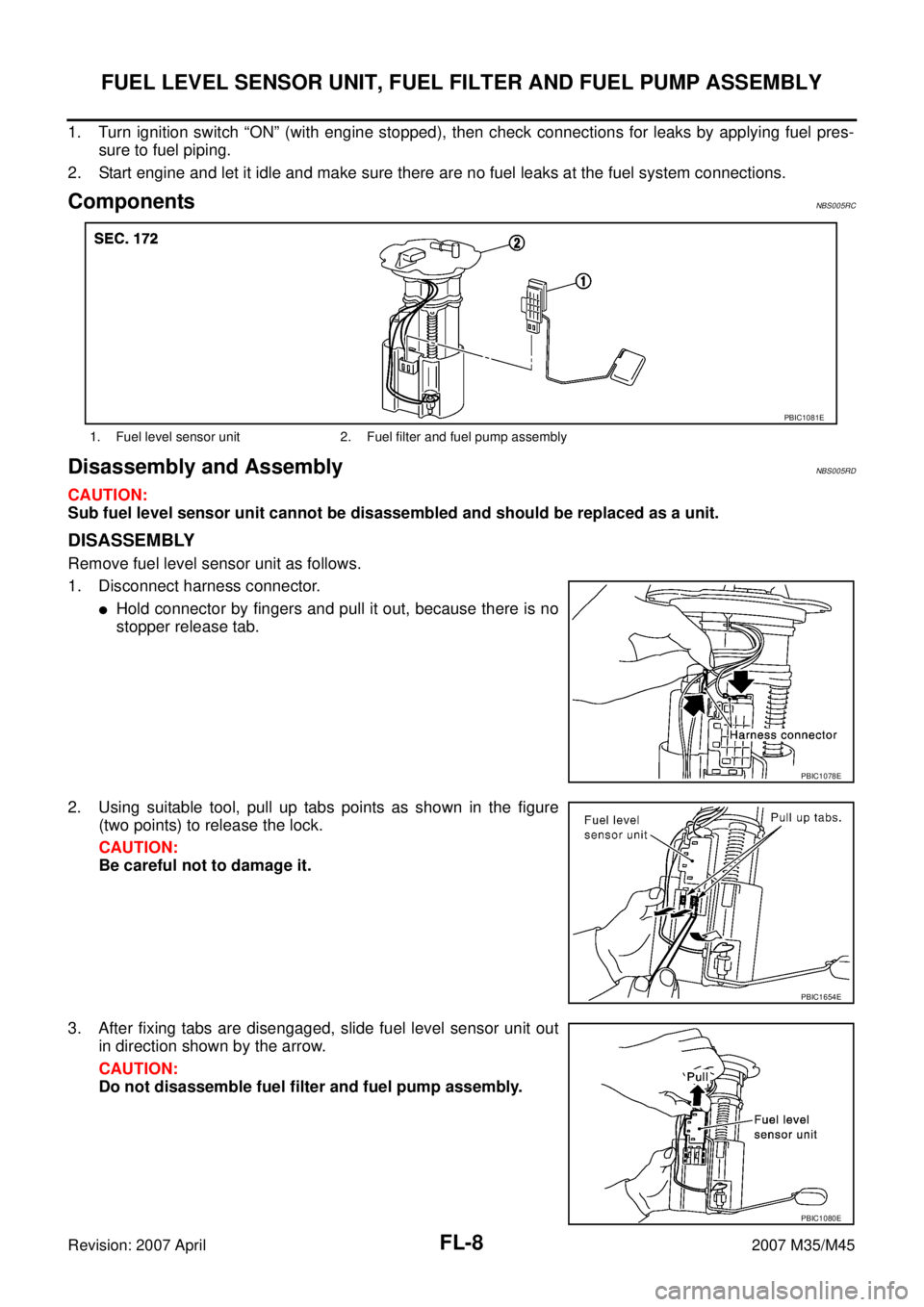
FL-8
FUEL LEVEL SENSOR UNIT, FUEL FILTER AND FUEL PUMP ASSEMBLY
Revision: 2007 April2007 M35/M45
1. Turn ignition switch “ON” (with engine stopped), then check connections for leaks by applying fuel pres-
sure to fuel piping.
2. Start engine and let it idle and make sure there are no fuel leaks at the fuel system connections.
ComponentsNBS005RC
Disassembly and AssemblyNBS005RD
CAUTION:
Sub fuel level sensor unit cannot be disassembled and should be replaced as a unit.
DISASSEMBLY
Remove fuel level sensor unit as follows.
1. Disconnect harness connector.
Hold connector by fingers and pull it out, because there is no
stopper release tab.
2. Using suitable tool, pull up tabs points as shown in the figure
(two points) to release the lock.
CAUTION:
Be careful not to damage it.
3. After fixing tabs are disengaged, slide fuel level sensor unit out
in direction shown by the arrow.
CAUTION:
Do not disassemble fuel filter and fuel pump assembly.
1. Fuel level sensor unit 2. Fuel filter and fuel pump assembly
PBIC1081E
PBIC1078E
PBIC1654E
PBIC1080E
Page 3102 of 4647
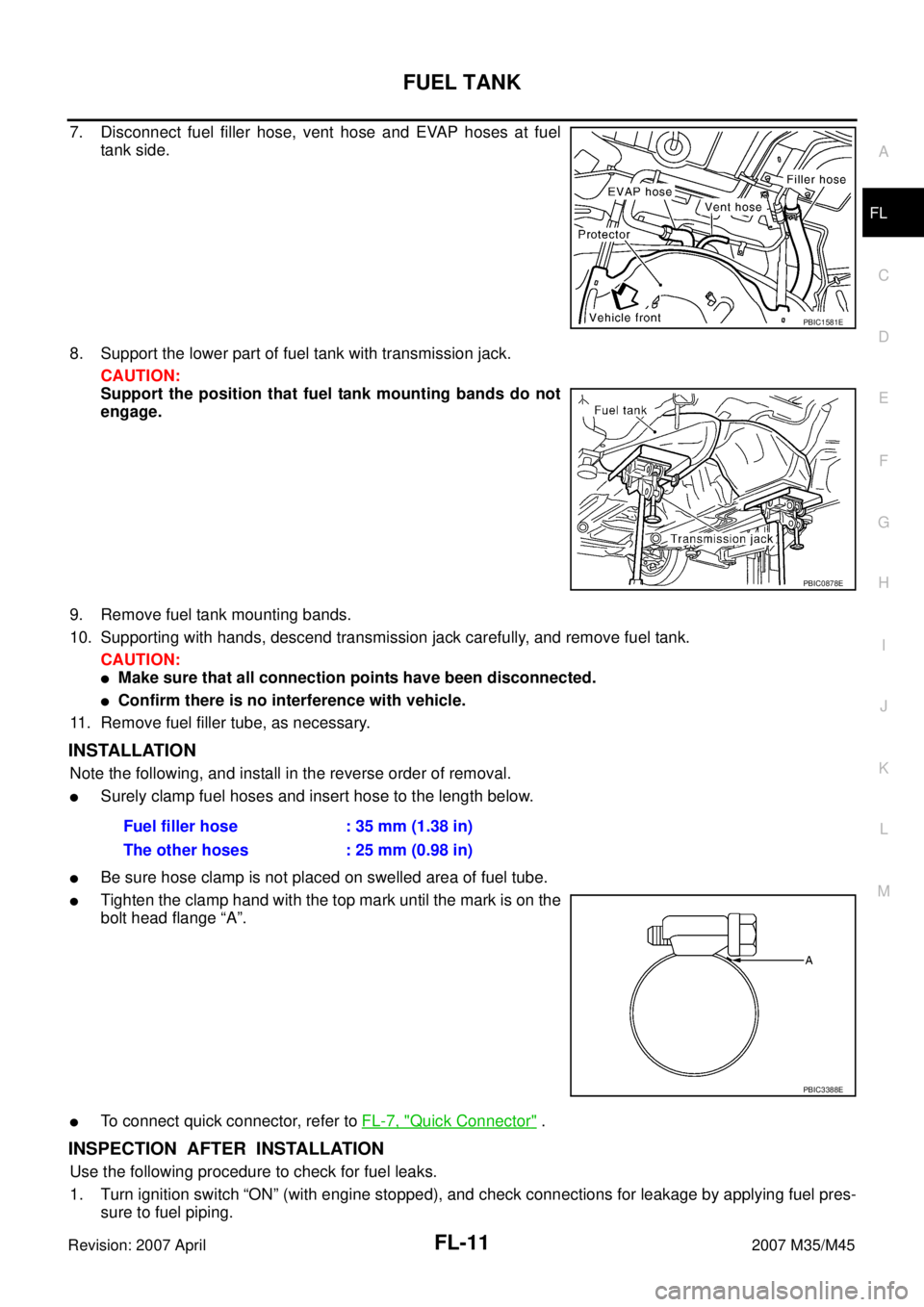
FUEL TANK
FL-11
C
D
E
F
G
H
I
J
K
L
MA
FL
Revision: 2007 April2007 M35/M45
7. Disconnect fuel filler hose, vent hose and EVAP hoses at fuel
tank side.
8. Support the lower part of fuel tank with transmission jack.
CAUTION:
Support the position that fuel tank mounting bands do not
engage.
9. Remove fuel tank mounting bands.
10. Supporting with hands, descend transmission jack carefully, and remove fuel tank.
CAUTION:
Make sure that all connection points have been disconnected.
Confirm there is no interference with vehicle.
11. Remove fuel filler tube, as necessary.
INSTALLATION
Note the following, and install in the reverse order of removal.
Surely clamp fuel hoses and insert hose to the length below.
Be sure hose clamp is not placed on swelled area of fuel tube.
Tighten the clamp hand with the top mark until the mark is on the
bolt head flange “A”.
To connect quick connector, refer to FL-7, "Quick Connector" .
INSPECTION AFTER INSTALLATION
Use the following procedure to check for fuel leaks.
1. Turn ignition switch “ON” (with engine stopped), and check connections for leakage by applying fuel pres-
sure to fuel piping.
PBIC1581E
PBIC0878E
Fuel filler hose : 35 mm (1.38 in)
The other hoses : 25 mm (0.98 in)
PBIC3388E
Page 3103 of 4647
FL-12
FUEL TANK
Revision: 2007 April2007 M35/M45
2. Start engine and rev it up and make sure there are no fuel leaks at the fuel system tube and hose connec-
tions.
After removing/installing rear suspension assembly, make sure to adjust wheel alignment and then, adjust
neutral position of steering angle sensor. Refer to RSU-5, "
Wheel Alignment Inspection" and BRC-6,
"Adjustment of Steering Angle Sensor Neutral Position" .
Page 3108 of 4647
PRECAUTIONS
FSU-3
[2WD]
C
D
F
G
H
I
J
K
L
MA
B
FSU
Revision: 2007 April2007 M35/M45
[2WD]PRECAUTIONSPFP:00001
CautionNES000I6
When installing rubber bushings, the final tightening must be carried out under unladen conditions with
tires on ground. Oil might shorten the life of rubber bushings. Be sure to wipe off any spilled oil.
–Unladen conditions mean that fuel, engine coolant and lubricant are full. Spare tire, jack, hand tools and
mats are in designated positions.
After servicing suspension parts, be sure to check wheel alignment.
Self-lock nuts are not reusable. Always use new ones when installing. Since new self-lock nuts are pre-
oiled, tighten as they are.
Page 3111 of 4647
![INFINITI M35 2007 Factory Service Manual FSU-6
[2WD]
FRONT SUSPENSION ASSEMBLY
Revision: 2007 April2007 M35/M45
FRONT SUSPENSION ASSEMBLYPFP:54010
On-Vehicle Inspection NES000IA
Make sure the mounting conditions (looseness, back lash) of eac INFINITI M35 2007 Factory Service Manual FSU-6
[2WD]
FRONT SUSPENSION ASSEMBLY
Revision: 2007 April2007 M35/M45
FRONT SUSPENSION ASSEMBLYPFP:54010
On-Vehicle Inspection NES000IA
Make sure the mounting conditions (looseness, back lash) of eac](/manual-img/42/57024/w960_57024-3110.png)
FSU-6
[2WD]
FRONT SUSPENSION ASSEMBLY
Revision: 2007 April2007 M35/M45
FRONT SUSPENSION ASSEMBLYPFP:54010
On-Vehicle Inspection NES000IA
Make sure the mounting conditions (looseness, back lash) of each component and component conditions
(wear, damage) are normal.
INSPECTION OF UPPER LINK BALL JOINT END PLAY
1. Set front wheels in a straight-ahead position. Do not depress brake pedal.
2. Place an iron bar or similar tool between transverse link and steering knuckle.
3. Measure axial end play by prying it up and down.
CAUTION:
Be careful not to damage ball joint boot. Do not damage the installation position by applying
excessive force.
SHOCK ABSORBER INSPECTION
Check for oil leakage, damage and breakage of installation positions.
Wheel Alignment InspectionNES000IB
DESCRIPTION
Measure wheel alignment under unladen conditions.
NOTE:
“Unladen conditions” means that fuel, engine coolant, and lubricant are full. Spare tire, jack, hand tools and
mats are in designated positions.
PRELIMINARY CHECK
Check tires for improper air pressure and wear.
Check road wheels for runout. Refer to WT-6, "ROAD WHEEL" .
Check wheel bearing axial end play. Refer to FAX-5, "WHEEL BEARING INSPECTION" .
Check transverse link ball joint axial end play. Refer to FSU-14, "INSPECTION AFTER REMOVAL" .
Check shock absorber operation.
Check each mounting part of axle and suspension for looseness and deformation.
Check each of suspension member, shock absorber, upper link and transverse link for cracks, deforma-
tion and other damage.
Check vehicle height (posture).
GENERAL INFORMATION AND RECOMMENDATIONS
A four-wheel thrust alignment should be performed.
–This type of alignment is recommended for any NISSAN/INFINITI vehicle.
–The four-wheel “thrust” process helps ensure that the vehicle is properly aligned and the steering wheel is
centered.
–The alignment rack itself should be capable of accepting any NISSAN/INFINITI vehicle.
–The rack should be checked to ensure that it is level.
Make sure the machine is properly calibrated.
–Your alignment equipment should be regularly calibrated in order to give correct information.
–Check with the manufacturer of your specific equipment for their recommended Service/Calibration
Schedule.Axial end play : 0 mm (0 in)
Page 3114 of 4647
![INFINITI M35 2007 Factory Service Manual FRONT SUSPENSION ASSEMBLY
FSU-9
[2WD]
C
D
F
G
H
I
J
K
L
MA
B
FSU
Revision: 2007 April2007 M35/M45
.
Removal and Installation NES000ID
REMOVAL
1. For VK45DE engine models, disconnect related electric w INFINITI M35 2007 Factory Service Manual FRONT SUSPENSION ASSEMBLY
FSU-9
[2WD]
C
D
F
G
H
I
J
K
L
MA
B
FSU
Revision: 2007 April2007 M35/M45
.
Removal and Installation NES000ID
REMOVAL
1. For VK45DE engine models, disconnect related electric w](/manual-img/42/57024/w960_57024-3113.png)
FRONT SUSPENSION ASSEMBLY
FSU-9
[2WD]
C
D
F
G
H
I
J
K
L
MA
B
FSU
Revision: 2007 April2007 M35/M45
.
Removal and Installation NES000ID
REMOVAL
1. For VK45DE engine models, disconnect related electric wires and hoses from engine assembly to remove
front suspension member with engine assembly. Refer to EM-247, "
ENGINE ASSEMBLY" .
2. Remove cowl top panel and hood. Refer to EI-18, "
COWL TOP" , EI-17, "HOOD" .
3. For VQ35DE engine models, install engine slinger, and then hoist engine. Refer to EM-114, "
Removal and
Installation (2WD Models)" .
4. Remove tires from vehicle with a power tool.
5. Remove wheel sensor from steering knuckle. Refer to BRC-54, "
WHEEL SENSOR" .
CAUTION:
Do not pull on wheel sensor harness.
6. Remove brake hose bracket. Refer to BR-11, "
BRAKE TUBE AND HOSE" .
7. Remove undercover with a power tool.
8. Remove cotter pin (1), and then loosen the nut.
9. Remove steering outer socket (2) from steering knuckle (3) so
as not to damage ball joint boot (4) using the ball joint remover
(suitable tool).
CAUTION:
Temporarily tighten the nut to prevent damage to threads
and to prevent the ball joint remover (suitable tool) from
suddenly coming off.
10. Remove the mounting nut on the upper side of stabilizer con-
necting rod with a power tool, and then remove stabilizer con-
necting rod from transverse link.
11. Separate steering gear assembly and lower joint. Refer to PS-13, "
STEERING COLUMN" .
12. Remove rack stay. Refer to FSU-8, "
Components" .
13. Remove steering hydraulic piping bracket from front suspension member. Refer to PS-39, "
HYDRAULIC
LINE" .
14. Remove the mounting nut and bolt on the lower side of shock absorber with a power tool, and then
remove shock absorber from transverse link.
15. Remove cotter pin of transverse link and steering knuckle, and then loosen nut.
16. Set jack under front suspension member.
17. Remove transverse link from steering knuckle so as not to damage ball joint boot using the ball joint
remover (suitable tool)
CAUTION:
Temporarily tighten the nut to prevent damage to threads and to prevent ball joint remover (suit-
able tool) from suddenly coming off.
18. Remove the mounting nuts of engine mounting insulator. Refer to EM-114, "
ENGINE ASSEMBLY" .
19. Remove the mounting bolts of member bracket, and then remove member bracket from front suspension
member with a power tool. Refer to FSU-8, "
Components" .
20. Remove the mounting nut and bolts of member stay, and then remove member stay from front suspension
member and vehicle with a power tool.
21. Remove the mounting nut of front suspension member with a power tool. Refer to FSU-8, "
Components" .
1. Shock absorber mounting bracket 2. Bound bumper 3. Rubber seat
4. Coil spring 5. Shock absorber 6. Upper link
7. Steering knuckle 8. Transverse link 9. Washer
10. Steering stopper bracket 11. Stabilizer connecting rod 12. Stabilizer bar
13. Stabilizer bushing 14. Stabilizer clamp 15. Front suspension member
16. Rack stay 17. Member stay 18. Member bracket
19. Clamp 20. Cotter pin 21. Stopper rubber
Refer to GI-11, "
Components" , for the symbols in the figure.
SGIA1183E
Page 3115 of 4647
FSU-10
[2WD]
FRONT SUSPENSION ASSEMBLY
Revision: 2007 April2007 M35/M45
22. For VQ35DE engine models, gradually lower a jack to remove front suspension assembly from vehicle.
For VK45DE engine models, gradually lower a jack to remove front suspension assembly with engine
assembly from vehicle.
INSTALLATION
Installation is the reverse order of removal. For tightening torque, refer to FSU-8, "Components" .
Perform final tightening of each of parts (rubber bushing), under unladen conditions, which were removed
when removing front suspension assembly. Check wheel alignment. Refer to FSU-6, "
Wheel Alignment
Inspection" .
Adjust neutral position of steering angle sensor after checking wheel alignment. Refer to BRC-6, "Adjust-
ment of Steering Angle Sensor Neutral Position" .
Check wheel sensor harness for proper connection. Refer to BRC-54, "WHEEL SENSOR" .