Page 146 of 596
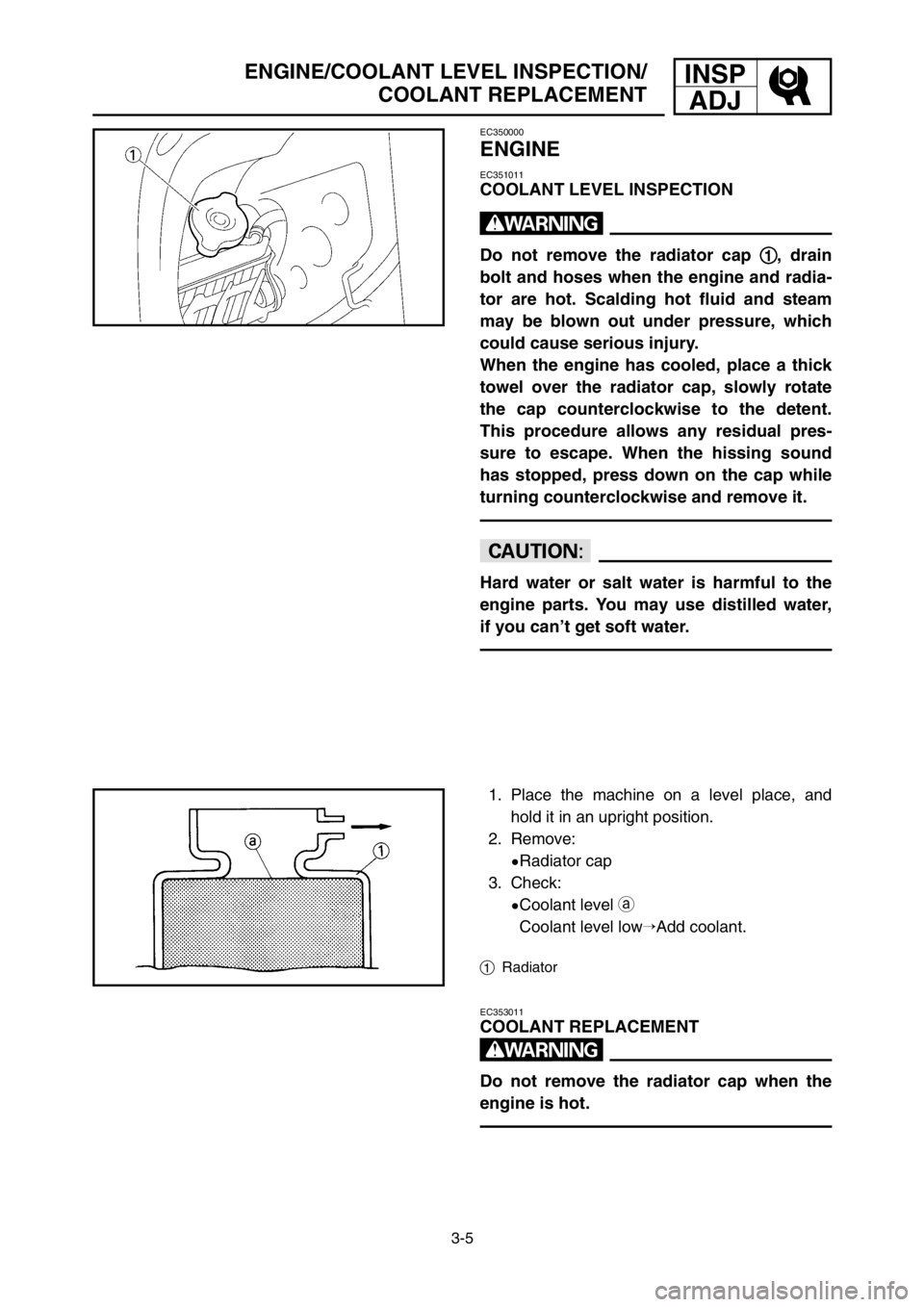
INSP
ADJ
3-5
ENGINE/COOLANT LEVEL INSPECTION/
COOLANT REPLACEMENT
EC350000
ENGINE
EC351011
COOLANT LEVEL INSPECTION
w
Do not remove the radiator cap 1 1
, drain
bolt and hoses when the engine and radia-
tor are hot. Scalding hot fluid and steam
may be blown out under pressure, which
could cause serious injury.
When the engine has cooled, place a thick
towel over the radiator cap, slowly rotate
the cap counterclockwise to the detent.
This procedure allows any residual pres-
sure to escape. When the hissing sound
has stopped, press down on the cap while
turning counterclockwise and remove it.
cC
Hard water or salt water is harmful to the
engine parts. You may use distilled water,
if you can’t get soft water.
1. Place the machine on a level place, and
hold it in an upright position.
2. Remove:
9Radiator cap
3. Check:
9Coolant level a
Coolant level lowAdd coolant.
1Radiator
EC353011
COOLANT REPLACEMENT
w
Do not remove the radiator cap when the
engine is hot.
1P8-9-30-3A 11/5/04 10:44 AM Page 18
Page 188 of 596
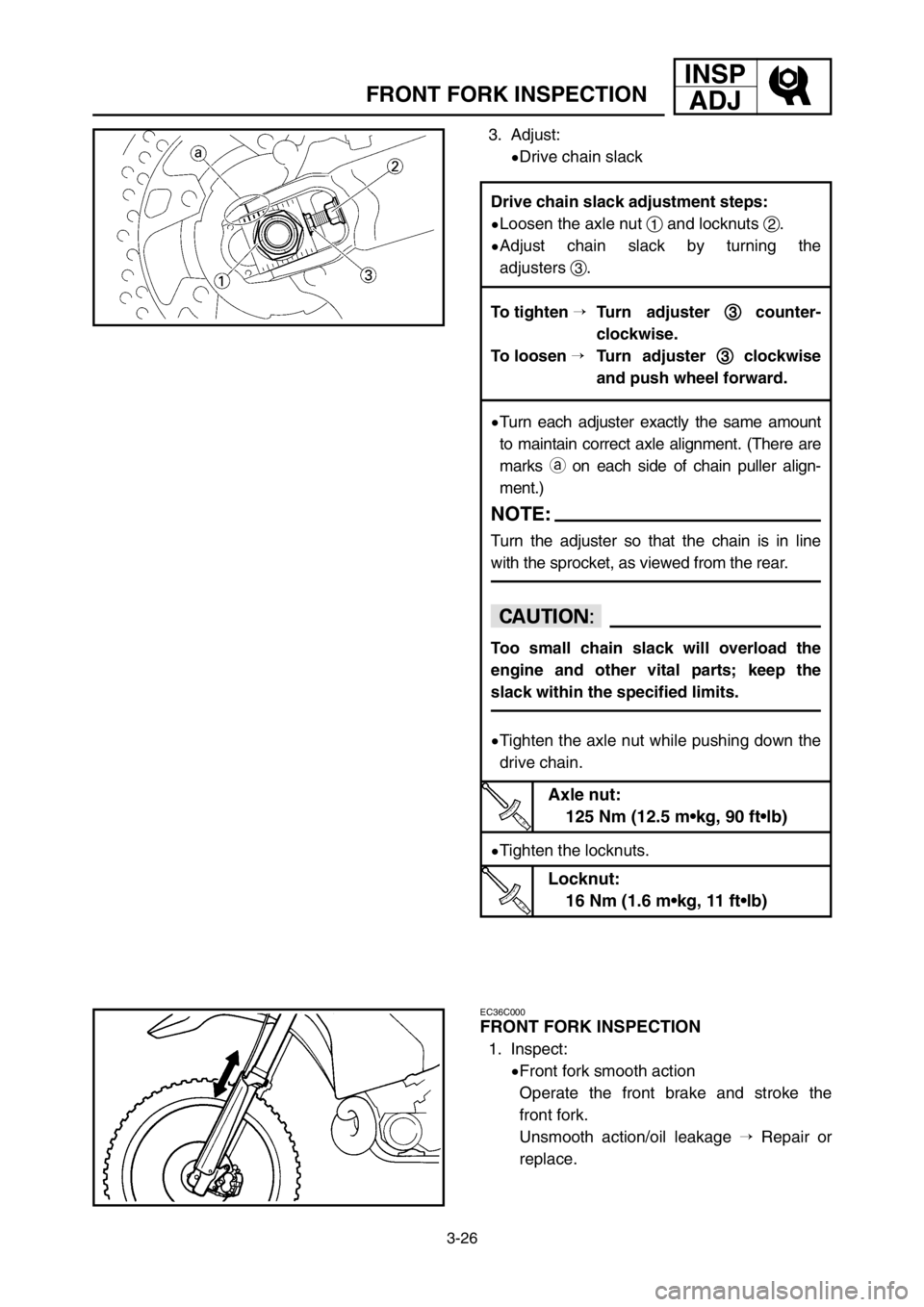
3-26
FRONT FORK INSPECTION
INSP
ADJ
3. Adjust:
9Drive chain slack
EC36C000
FRONT FORK INSPECTION
1. Inspect:
9Front fork smooth action
Operate the front brake and stroke the
front fork.
Unsmooth action/oil leakage Repair or
replace.
Drive chain slack adjustment steps:
9Loosen the axle nut 1and locknuts 2.
9Adjust chain slack by turning the
adjusters 3.
To tighten Turn adjuster 3 3
counter-
clockwise.
To loosen Turn adjuster 3 3
clockwise
and push wheel forward.
9Turn each adjuster exactly the same amount
to maintain correct axle alignment. (There are
marks aon each side of chain puller align-
ment.)
NOTE:
Turn the adjuster so that the chain is in line
with the sprocket, as viewed from the rear.
cC
Too small chain slack will overload the
engine and other vital parts; keep the
slack within the specified limits.
9Tighten the axle nut while pushing down the
drive chain.
9Tighten the locknuts.
Axle nut:
125 Nm (12.5 m•kg, 90 ft•lb)
Locknut:
16 Nm (1.6 m•kg, 11 ft•lb)
1P8-9-30-3B 19/5/04 9:11 AM Page 16
Page 214 of 596
3-39
IGNITION TIMING CHECK
INSP
ADJ
EC372012
IGNITION TIMING CHECK
1. Remove:
9Fuel tank
Refer to “SEAT, FUEL TANK AND SIDE
COVERS” section in the CHAPTER 4.
9Spark plug
9Crankcase cover (left)
2. Attach:
9Dial gauge 1
9Spark plug hole dial stand 2
3. Rotate the magneto rotor 1until the piston
reaches top dead center (TDC). When this
happens, the needle on the dial gauge will
stop and reverse directions even though the
rotor is being turned in the same direction.
4. Set the dial gauge to zero at TDC.
5. From TDC, rotate the rotor clockwise until
the dial gauge indicates that the piston is at
a specified distance from TDC.
6. Check:
9Ignition timing
Punch mark aon rotor should be aligned
with punch mark bon stator.
Not aligned Adjust.
Dial gauge:
YU-3097/90890-01252
Spark plug hole dial stand:
YU-1256
Ignition timing (B.T.D.C.):
0.18 mm (0.007 in)
1P8-9-30-3B 19/5/04 9:12 AM Page 42
Page 226 of 596
4-5
ENGRADIATOR
EC456000
HANDLING NOTE
w
Do not remove the radiator cap when the
engine and radiator are hot. Scalding hot
fluid and steam may be blown out under
pressure, which could cause serious
injury.
When the engine has cooled, open the
radiator cap by the following procedure:
Place a thick rag, like a towel, over the
radiator cap, slowly rotate the cap counter-
clockwise to the detent. This procedure
allows any residual pressure to escape.
When the hissing sound has stopped,
press down on the cap while turning coun-
terclockwise and remove it.
EC454000
INSPECTION
EC444100
Radiator
1. Inspect:
9Radiator core 1
Obstruction Blow out with compressed air
through rear of the radiator.
Bent fin Repair/replace.
1P8-9-30-4A 11/5/04 9:32 PM Page 10
Page 308 of 596
4-46
KICK AXLE, SHIFT SHAFT AND PRIMARY DRIVE GEARENG
EC4C5420
Kick idle gear
1. Install:
9Kick idle gear 1
9Plain washer 2
9Circlip 3
NOTE:
9Apply the transmission oil on the kick idle gear
inner circumference.
9Install the kick idle gear with its depressed side
atoward you.
3. Install:
9Spring guide 1
NOTE:
Slide the spring guide into the kick axle, make
sure the groove ain the spring guide fits on the
stopper of the torsion spring.
4. Install:
9Plain washer 1
9Kick axle assembly 2
NOTE:
9Apply the molybdenum disulfide grease on the
contacting surfaces of the kick axle stopper a
and stopper plate 3.
9Apply the transmission oil on the kick axle.
9Slide the kick axle assembly into the crankcase
and make sure the kick axle stopper fits into
the stopper plate.
5. Hook:
9Torsion spring 1
NOTE:
Turn the torsion spring clockwise and hook into
the proper hole ain the crankcase.
1P8-9-30-4B 11/5/04 10:59 AM Page 38
Page 330 of 596
4-57
CDI MAGNETOENG
EC4L5000
ASSEMBLY AND INSTALLATION
EC4L5172
CDI magneto
1. Install:
9Stator 1
9Screw (stator) 2
NOTE:
Temporarily tighten the screw (stator) at this
point.
2. Remove:
9Rotor 1
Use the flywheel puller 2.
NOTE:
When installing the flywheel puller, turn it coun-
terclockwise.
EC4L3000
REMOVAL POINTS
EC4L3102
Rotor
1. Remove:
9Nut (rotor) 1
9Plain washer 2
Use the rotor holding tool 3.
EC4L4000
INSPECTION
EC4L4101
CDI magneto
1. Inspect:
9Rotor inner surface a
9Stator outer surface b
Damage
Inspect the crankshaft runout
and crankshaft bearing.
If necessary, replace CDI magneto and/or
stator.
EC4L4200
Woodruff key
1. Inspect:
9Woodruff key 1
Damage
Replace.
Rotor holding tool:
YU-1235/90890-01235
Flywheel puller:
YM-1189/90890-01189
1P8-9-30-4C 21/5/04 12:59 PM Page 16
Page 358 of 596
4-71
CRANKCASE AND CRANKSHAFTENG
8. Tighten:
9Segment 1
9Bolt (segment) 2
NOTE:
9When installing the segment onto the shift cam
3, align the punch mark awith the dowel pin
b.
9Turn the segment clockwise until it stops and
tighten the bolt.
30 Nm (3.0 m•kg, 22 ft•lb)
7. Install:
9Tension spring 1
9Holder 2
9Bolt (holder) 3
NOTE:
Install the holder so that it contacts the projec-
tion aon the crankcase (right).
10 Nm (1.0 m•kg, 7.2 ft•lb)
9. Remove:
9Sealant
Forced out on the cylinder mating surface.
10. Apply:
9Engine oil
To the crank pin, bearing, oil delivery hole
and connecting rod big end washer.
11. Check:
9Crankshaft and transmission operation
Unsmooth operation
Repair.
14 Nm (1.4 m•kg, 10 ft•lb)
6. Install:
9Bolt (crankcase) 1
NOTE:
Tighten the crankcase tightening bolts in stage,
using a crisscross pattern.
1P8-9-30-4C 21/5/04 1:00 PM Page 44
Page 510 of 596
6-4
IGNITION SYSTEMELEC
EC626003
IGNITION COIL INSPECTION
1. Inspect:
9Primary coil resistance
Out of specification Replace.
2. Inspect:
9Secondary coil resistance
Out of specification Replace.
NOTE:
9Remove the spark plug cap by turning it coun-
terclockwise and inspect.
9Install the spark plug cap by turning it clock-
wise until it is tight.
Tester (+) leadYellow lead 1
Tester (–) lead
Black lead 2
Tester (+) leadSpark plug lead 1
Tester (–) lead
Yellow lead 2
Primary coil Tester selector
resistance position
0.20~0.30Ωat
Ω× 1
20°C (68°F)
Secondary coil Tester selector
resistance position
9.5~14.3kΩat
kΩ× 1
20°C (68°F)
1P8-9-30-6 21/5/04 11:42 AM Page 10