Page 43 of 1500
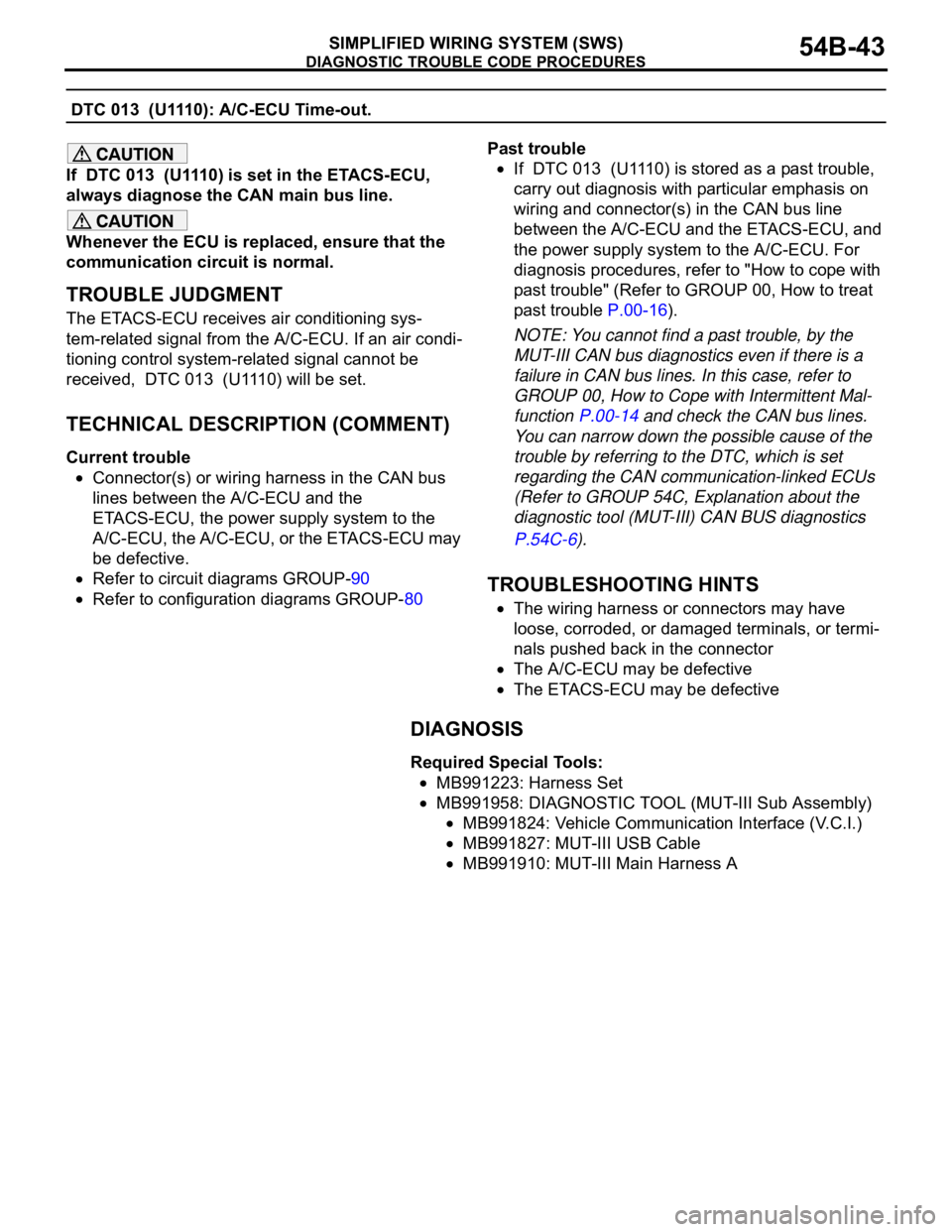
DIAGNOSTIC TROUBLE CODE PROCEDURES
SIMPLIFIED WIRING SYSTEM (SWS)54B-43
DTC 013 (U1110): A/C-ECU Time-out.
If DTC 013 (U1110) is set in the ETACS-ECU,
always diagnose the CAN main bus line.
Whenever the ECU is replaced, ensure that the
communication circuit is normal.
.
TROUBLE JUDGMENT
The ETACS-ECU receives air conditioning sys-
tem-related signal from the A/C-ECU. If an air condi-
tioning control system-related signal cannot be
received, DTC 013 (U1110) will be set.
.
TECHNICAL DESCRIPTION (COMMENT)
Current trouble
Connector(s) or wiring harness in the CAN bus
lines between the A/C-ECU and the
ETACS-ECU, the power supply system to the
A/C-ECU, the A/C-ECU, or the ETACS-ECU may
be defective.
Refer to circuit diagrams GROUP-90
Refer to configuration diagrams GROUP-80Past trouble
If DTC 013 (U1110) is stored as a past trouble,
carry out diagnosis with particular emphasis on
wiring and connector(s) in the CAN bus line
between the A/C-ECU and the ETACS-ECU, and
the power supply system to the A/C-ECU. For
diagnosis procedures, refer to "How to cope with
past trouble" (Refer to GROUP 00, How to treat
past trouble P.00-16).
NOTE: You cannot find a past trouble, by the
MUT-III CAN bus diagnostics even if there is a
failure in CAN bus lines. In this case, refer to
GROUP 00, How to Cope with Intermittent Mal-
function P.00-14 and check the CAN bus lines.
You can narrow down the possible cause of the
trouble by referring to the DTC, which is set
regarding the CAN communication-linked ECUs
(Refer to GROUP 54C, Explanation about the
diagnostic tool (MUT-III) CAN BUS diagnostics
P.54C-6).
.
TROUBLESHOOTING HINTS
The wiring harness or connectors may have
loose, corroded, or damaged terminals, or termi-
nals pushed back in the connector
The A/C-ECU may be defective
The ETACS-ECU may be defective
DIAGNOSIS
Required Special Tools:
MB991223: Harness Set
MB991958: DIAGNOSTIC TOOL (MUT-III Sub Assembly)
MB991824: Vehicle Communication Interface (V.C.I.)
MB991827: MUT-III USB Cable
MB991910: MUT-III Main Harness A
Page 44 of 1500
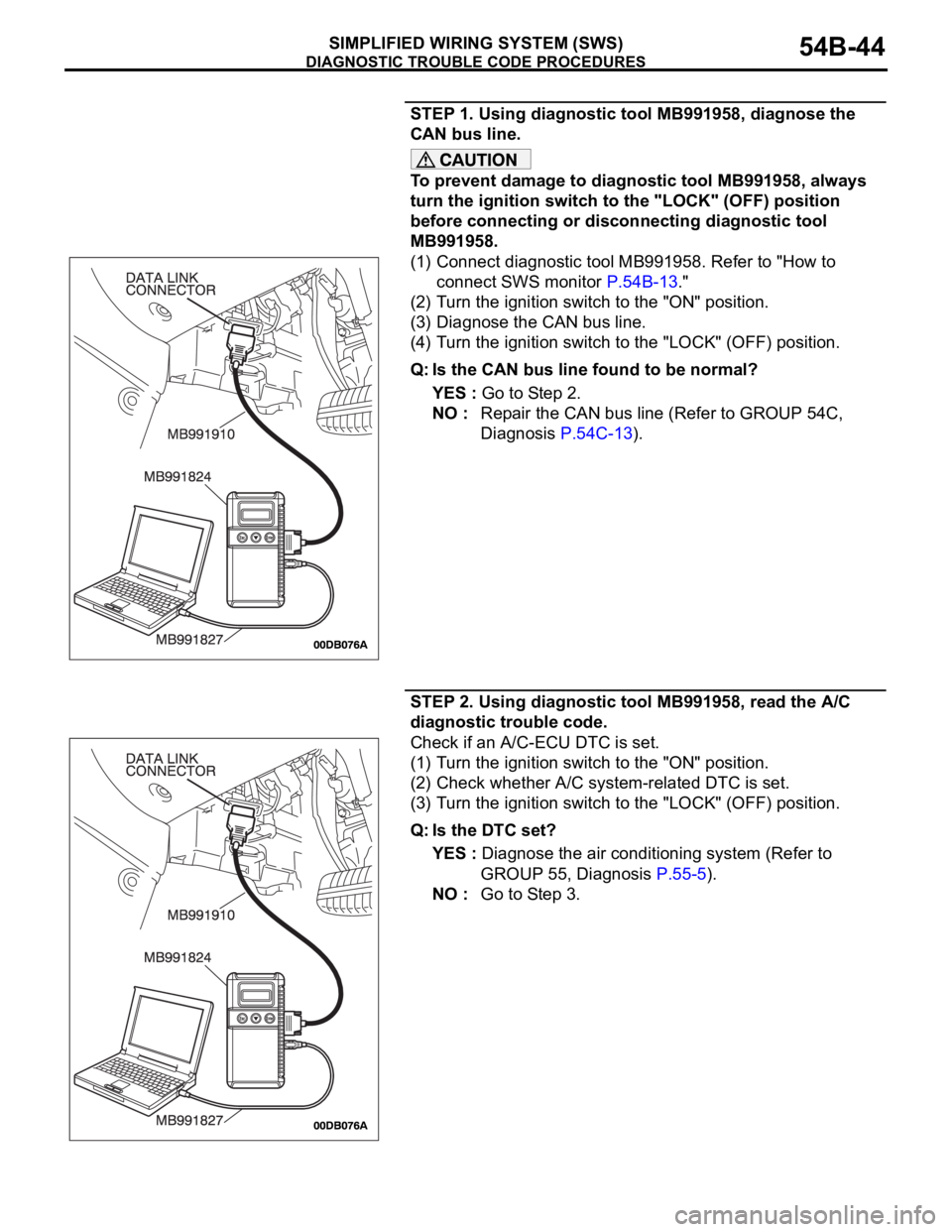
DIAGNOSTIC TROUBLE CODE PROCEDURES
SIMPLIFIED WIRING SYSTEM (SWS)54B-44
STEP 1. Using diagnostic tool MB991958, diagnose the
CAN bus line.
To prevent damage to diagnostic tool MB991958, always
turn the ignition switch to the "LOCK" (OFF) position
before connecting or disconnecting diagnostic tool
MB991958.
(1) Connect diagnostic tool MB991958. Refer to "How to
connect SWS monitor P.54B-13."
(2) Turn the ignition switch to the "ON" position.
(3) Diagnose the CAN bus line.
(4) Turn the ignition switch to the "LOCK" (OFF) position.
Q: Is the CAN bus line found to be normal?
YES : Go to Step 2.
NO : Repair the CAN bus line (Refer to GROUP 54C,
Diagnosis P.54C-13).
STEP 2. Using diagnostic tool MB991958, read the A/C
diagnostic trouble code.
Check if an A/C-ECU DTC is set.
(1) Turn the ignition switch to the "ON" position.
(2) Check whether A/C system-related DTC is set.
(3) Turn the ignition switch to the "LOCK" (OFF) position.
Q: Is the DTC set?
YES : Diagnose the air conditioning system (Refer to
GROUP 55, Diagnosis P.55-5).
NO : Go to Step 3.
Page 64 of 1500
SYMPTOM PROCEDURES
SIMPLIFIED WIRING SYSTEM (SWS)54B-64
STEP 1. Verify SWS monitor kit MB991813 for proper
connection.
Q: Is SWS monitor kit MB991813 connected with the
column switch properly?
YES : Go to Step 2.
NO : Connect SWS monitor kit MB991813 to the column
switch securely.
STEP 2. Verify the power supply circuit to the ETACS-ECU.
Q: Does the system communicate with diagnostic tool
MB991958 when the ignition switch is turned to the
"ON" position?
YES : Refer to Inspection Procedure A-3 "Communication
with the ETACS-ECU is not possible P.54B-74."
NO : Go to Step 3.
STEP 3. Check ETACS-ECU connectors C-218 and C-219
for loose, corroded or damaged terminals, or terminals
pushed back in the connector.
Q: Are ETACS-ECU connectors C-218 and C-219 in good
condition?
YES : Go to Step 4.
NO : Repair or replace the damaged component(s). Refer
to GROUP 00E, Harness Connector Inspection
P.00E-2. Verify that the system should communicate
with the SWS monitor normally.
Page 66 of 1500
SYMPTOM PROCEDURES
SIMPLIFIED WIRING SYSTEM (SWS)54B-66
STEP 5. Check the wiring harness between ETACS-ECU
connector C-218 (terminal 50) or ETACS-ECU connector
C-219 (terminal 3) and ground.
NOTE: Also check junction block connector C-211 for loose,
corroded, or damaged terminals, or terminals pushed back in
the connector. If junction block connector C-211 is damaged,
repair or replace the damaged component(s) as described in
GROUP 00E, Harness Connector Inspection P.00E-2.
Q: Is the wiring harness between ETACS-ECU connector
C-218 (terminal 50) or ETACS-ECU connector C-219
(terminal 3) and ground in good condition?
YES : No action is necessary and testing is complete.
NO : The wiring harness may be damaged or the
connector(s) may have loose, corroded or damaged
terminals, or terminals pushed back in the connector.
Repair the wiring harness as necessary. Verify that
the system should communicate with the SWS
monitor kit normally.
Page 67 of 1500
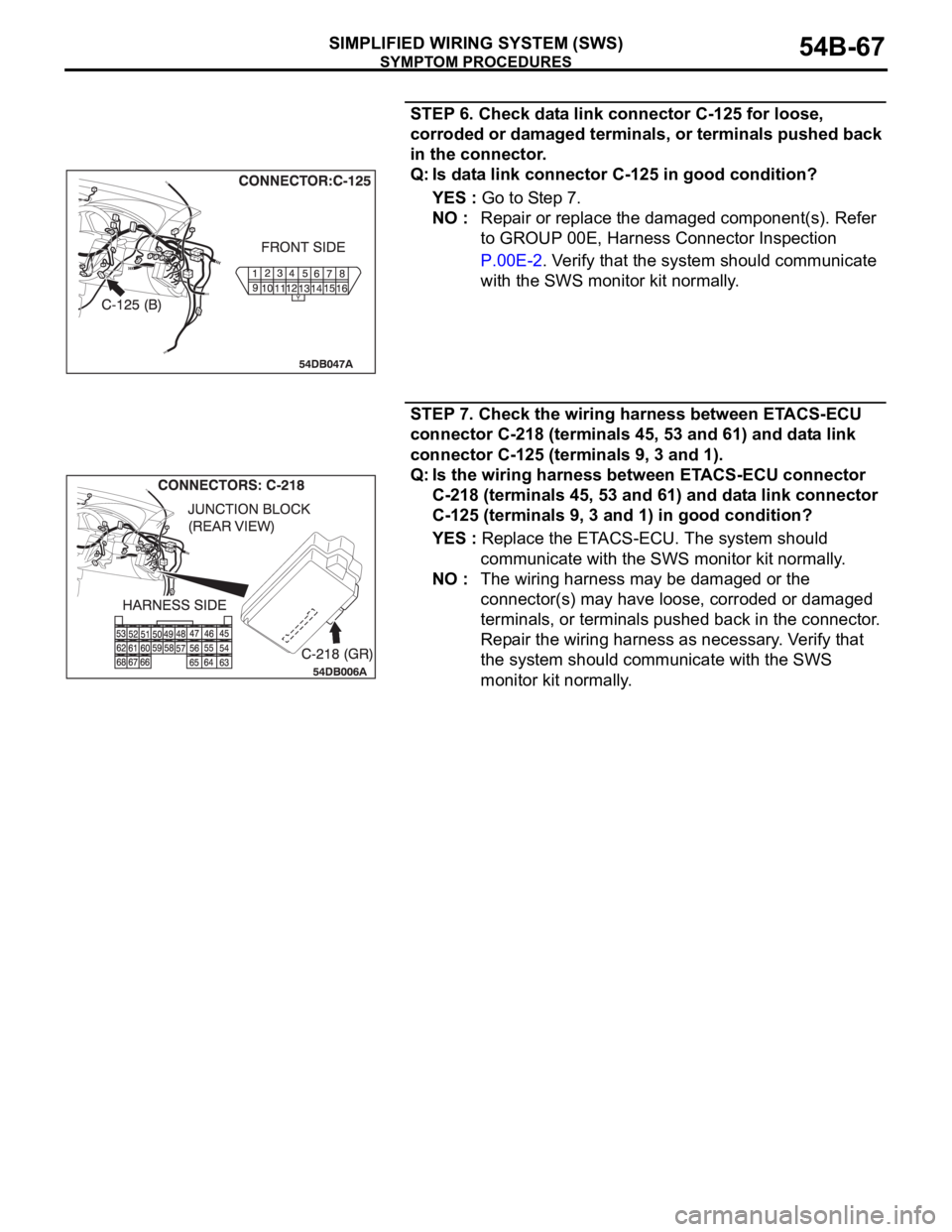
SYMPTOM PROCEDURES
SIMPLIFIED WIRING SYSTEM (SWS)54B-67
STEP 6. Check data link connector C-125 for loose,
corroded or damaged terminals, or terminals pushed back
in the connector.
Q: Is data link connector C-125 in good condition?
YES : Go to Step 7.
NO : Repair or replace the damaged component(s). Refer
to GROUP 00E, Harness Connector Inspection
P.00E-2. Verify that the system should communicate
with the SWS monitor kit normally.
STEP 7. Check the wiring harness between ETACS-ECU
connector C-218 (terminals 45, 53 and 61) and data link
connector C-125 (terminals 9, 3 and 1).
Q: Is the wiring harness between ETACS-ECU connector
C-218 (terminals 45, 53 and 61) and data link connector
C-125 (terminals 9, 3 and 1) in good condition?
YES : Replace the ETACS-ECU. The system should
communicate with the SWS monitor kit normally.
NO : The wiring harness may be damaged or the
connector(s) may have loose, corroded or damaged
terminals, or terminals pushed back in the connector.
Repair the wiring harness as necessary. Verify that
the system should communicate with the SWS
monitor kit normally.
Page 70 of 1500
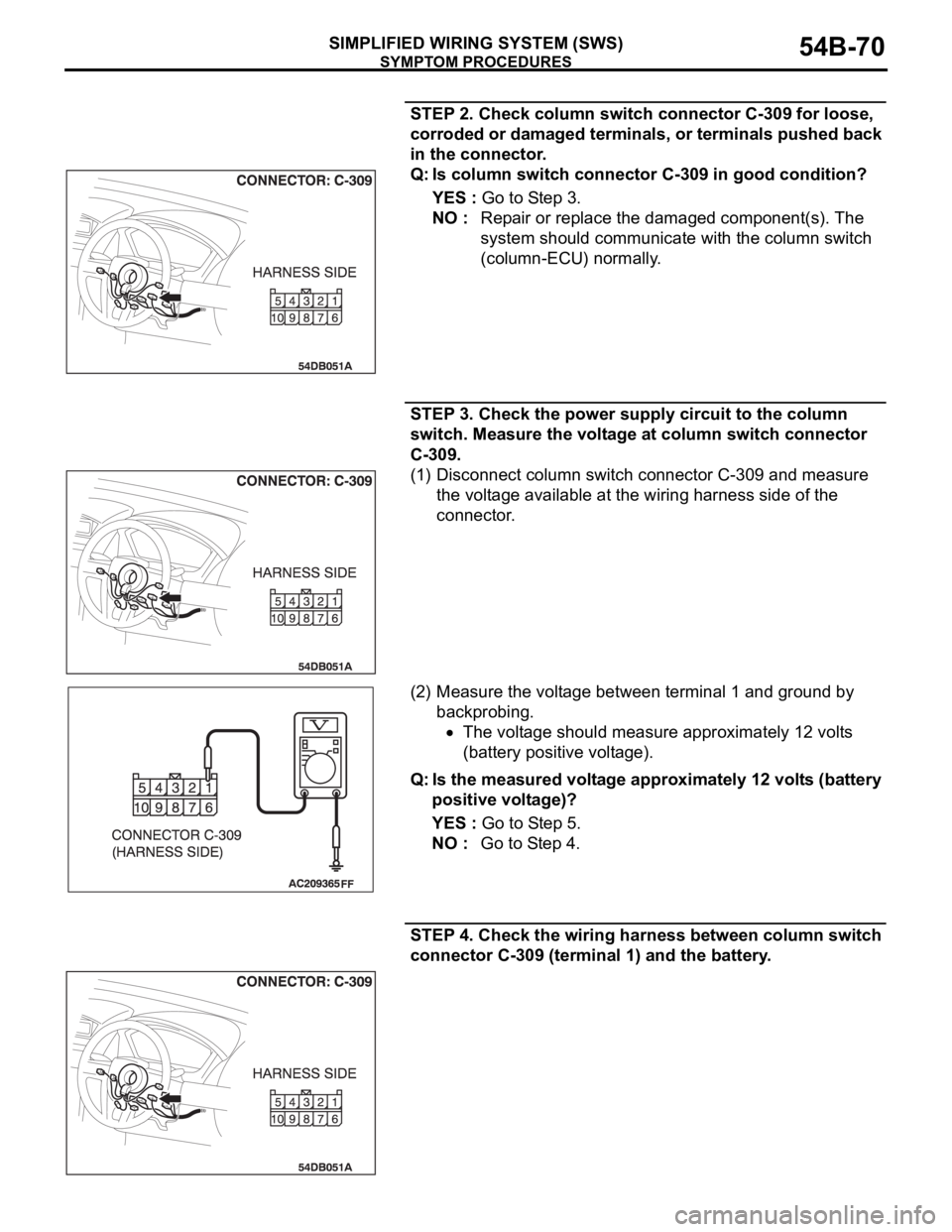
SYMPTOM PROCEDURES
SIMPLIFIED WIRING SYSTEM (SWS)54B-70
STEP 2. Check column switch connector C-309 for loose,
corroded or damaged terminals, or terminals pushed back
in the connector.
Q: Is column switch connector C-309 in good condition?
YES : Go to Step 3.
NO : Repair or replace the damaged component(s). The
system should communicate with the column switch
(column-ECU) normally.
STEP 3. Check the power supply circuit to the column
switch. Measure the voltage at column switch connector
C-309.
(1) Disconnect column switch connector C-309 and measure
the voltage available at the wiring harness side of the
connector.
(2) Measure the voltage between terminal 1 and ground by
backprobing.
The voltage should measure approximately 12 volts
(battery positive voltage).
Q: Is the measured voltage approximately 12 volts (battery
positive voltage)?
YES : Go to Step 5.
NO : Go to Step 4.
STEP 4. Check the wiring harness between column switch
connector C-309 (terminal 1) and the battery.
Page 71 of 1500
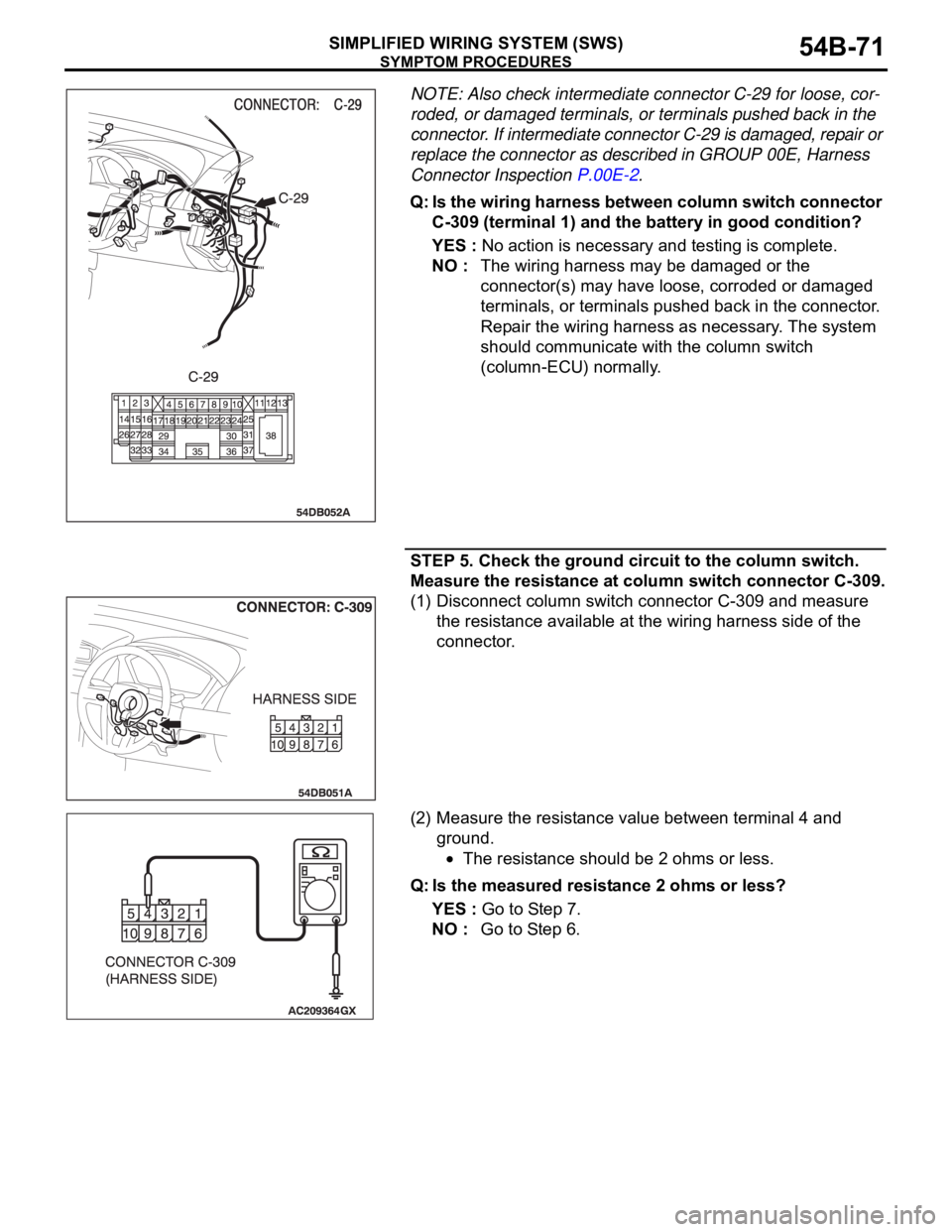
SYMPTOM PROCEDURES
SIMPLIFIED WIRING SYSTEM (SWS)54B-71
NOTE: Also check intermediate connector C-29 for loose, cor-
roded, or damaged terminals, or terminals pushed back in the
connector. If intermediate connector C-29 is damaged, repair or
replace the connector as described in GROUP 00E, Harness
Connector Inspection P.00E-2.
Q: Is the wiring harness between column switch connector
C-309 (terminal 1) and the battery in good condition?
YES : No action is necessary and testing is complete.
NO : The wiring harness may be damaged or the
connector(s) may have loose, corroded or damaged
terminals, or terminals pushed back in the connector.
Repair the wiring harness as necessary. The system
should communicate with the column switch
(column-ECU) normally.
STEP 5. Check the ground circuit to the column switch.
Measure the resistance at column switch connector C-309.
(1) Disconnect column switch connector C-309 and measure
the resistance available at the wiring harness side of the
connector.
(2) Measure the resistance value between terminal 4 and
ground.
The resistance should be 2 ohms or less.
Q: Is the measured resistance 2 ohms or less?
YES : Go to Step 7.
NO : Go to Step 6.
Page 72 of 1500
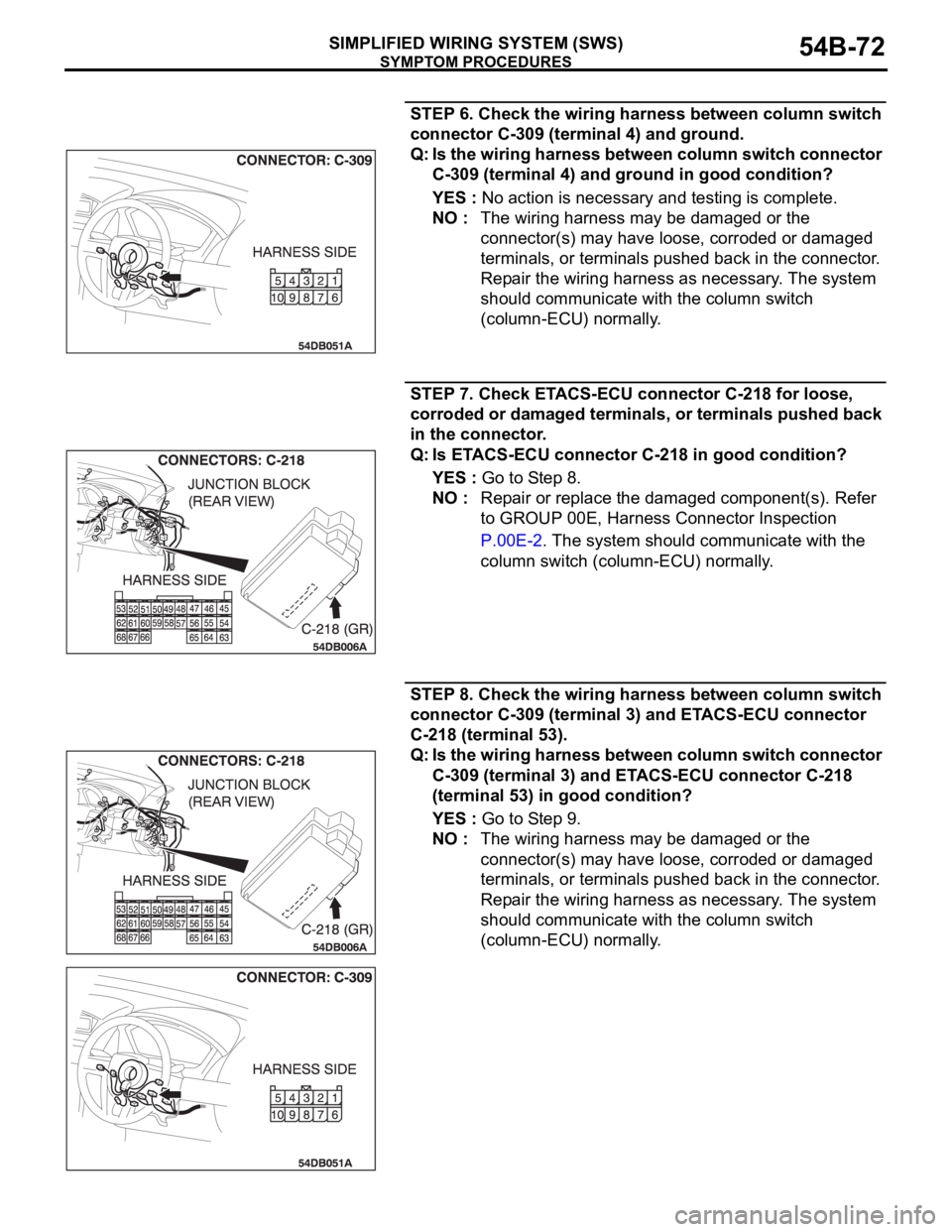
SYMPTOM PROCEDURES
SIMPLIFIED WIRING SYSTEM (SWS)54B-72
STEP 6. Check the wiring harness between column switch
connector C-309 (terminal 4) and ground.
Q: Is the wiring harness between column switch connector
C-309 (terminal 4) and ground in good condition?
YES : No action is necessary and testing is complete.
NO : The wiring harness may be damaged or the
connector(s) may have loose, corroded or damaged
terminals, or terminals pushed back in the connector.
Repair the wiring harness as necessary. The system
should communicate with the column switch
(column-ECU) normally.
STEP 7. Check ETACS-ECU connector C-218 for loose,
corroded or damaged terminals, or terminals pushed back
in the connector.
Q: Is ETACS-ECU connector C-218 in good condition?
YES : Go to Step 8.
NO : Repair or replace the damaged component(s). Refer
to GROUP 00E, Harness Connector Inspection
P.00E-2. The system should communicate with the
column switch (column-ECU) normally.
STEP 8. Check the wiring harness between column switch
connector C-309 (terminal 3) and ETACS-ECU connector
C-218 (terminal 53).
Q: Is the wiring harness between column switch connector
C-309 (terminal 3) and ETACS-ECU connector C-218
(terminal 53) in good condition?
YES : Go to Step 9.
NO : The wiring harness may be damaged or the
connector(s) may have loose, corroded or damaged
terminals, or terminals pushed back in the connector.
Repair the wiring harness as necessary. The system
should communicate with the column switch
(column-ECU) normally.