Page 1542 of 3419
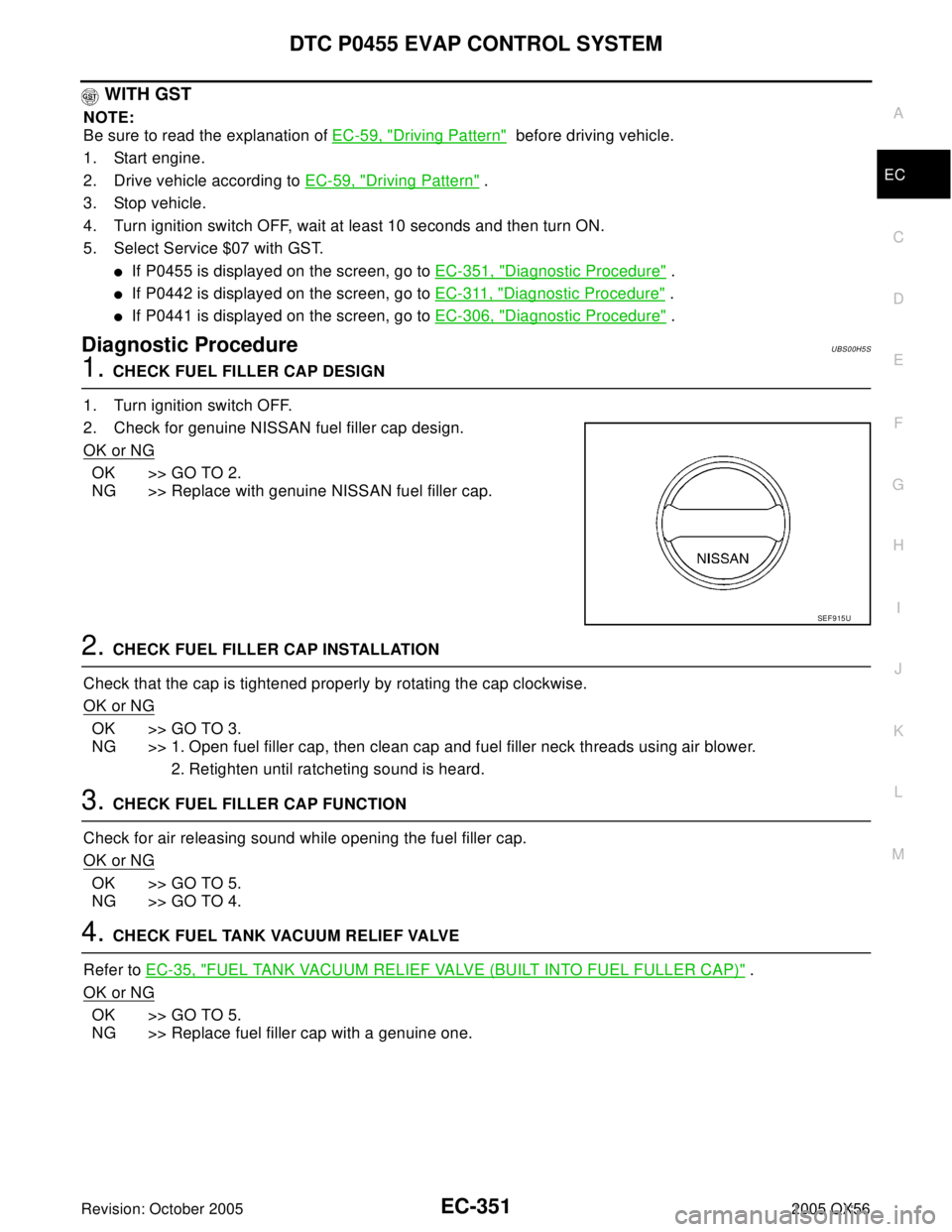
DTC P0455 EVAP CONTROL SYSTEM
EC-351
C
D
E
F
G
H
I
J
K
L
MA
EC
Revision: October 20052005 QX56
WITH GST
NOTE:
Be sure to read the explanation of EC-59, "
Driving Pattern" before driving vehicle.
1. Start engine.
2. Drive vehicle according to EC-59, "
Driving Pattern" .
3. Stop vehicle.
4. Turn ignition switch OFF, wait at least 10 seconds and then turn ON.
5. Select Service $07 with GST.
If P0455 is displayed on the screen, go to EC-351, "Diagnostic Procedure" .
If P0442 is displayed on the screen, go to EC-311, "Diagnostic Procedure" .
If P0441 is displayed on the screen, go to EC-306, "Diagnostic Procedure" .
Diagnostic ProcedureUBS00H5S
1. CHECK FUEL FILLER CAP DESIGN
1. Turn ignition switch OFF.
2. Check for genuine NISSAN fuel filler cap design.
OK or NG
OK >> GO TO 2.
NG >> Replace with genuine NISSAN fuel filler cap.
2. CHECK FUEL FILLER CAP INSTALLATION
Check that the cap is tightened properly by rotating the cap clockwise.
OK or NG
OK >> GO TO 3.
NG >> 1. Open fuel filler cap, then clean cap and fuel filler neck threads using air blower.
2. Retighten until ratcheting sound is heard.
3. CHECK FUEL FILLER CAP FUNCTION
Check for air releasing sound while opening the fuel filler cap.
OK or NG
OK >> GO TO 5.
NG >> GO TO 4.
4. CHECK FUEL TANK VACUUM RELIEF VALVE
Refer to EC-35, "
FUEL TANK VACUUM RELIEF VALVE (BUILT INTO FUEL FULLER CAP)" .
OK or NG
OK >> GO TO 5.
NG >> Replace fuel filler cap with a genuine one.
SEF 9 15 U
Page 1551 of 3419
EC-360Revision: October 2005
DTC P0456 EVAP CONTROL SYSTEM
2005 QX56
Diagnostic ProcedureUBS00H5W
1. CHECK FUEL FILLER CAP DESIGN
1. Turn ignition switch OFF.
2. Check for genuine NISSAN fuel filler cap design.
OK or NG
OK >> GO TO 2.
NG >> Replace with genuine NISSAN fuel filler cap.
2. CHECK FUEL FILLER CAP INSTALLATION
Check that the cap is tightened properly by rotating the cap clockwise.
OK or NG
OK >> GO TO 3.
NG >> 1. Open fuel filler cap, then clean cap and fuel filler neck threads using air blower.
2. Retighten until ratcheting sound is heard.
3. CHECK FUEL FILLER CAP FUNCTION
Check for air releasing sound while opening the fuel filler cap.
OK or NG
OK >> GO TO 5.
NG >> GO TO 4.
4. CHECK FUEL TANK VACUUM RELIEF VALVE
Refer to EC-35, "
FUEL TANK VACUUM RELIEF VALVE (BUILT INTO FUEL FULLER CAP)" .
OK or NG
OK >> GO TO 5.
NG >> Replace fuel filler cap with a genuine one.
SEF 9 15 U
Page 1866 of 3419
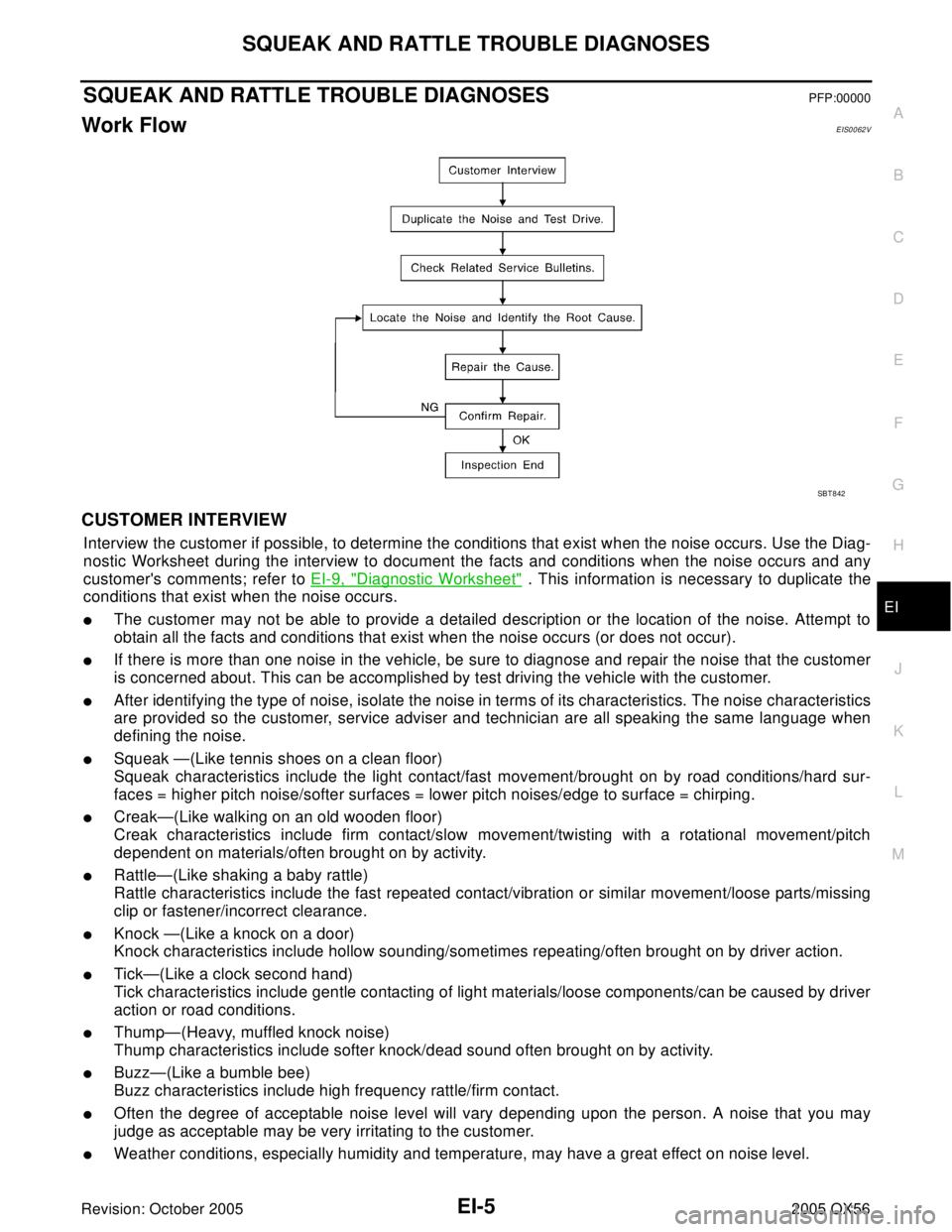
SQUEAK AND RATTLE TROUBLE DIAGNOSES
EI-5
C
D
E
F
G
H
J
K
L
MA
B
EI
Revision: October 20052005 QX56
SQUEAK AND RATTLE TROUBLE DIAGNOSESPFP:00000
Work FlowEIS0062V
CUSTOMER INTERVIEW
Interview the customer if possible, to determine the conditions that exist when the noise occurs. Use the Diag-
nostic Worksheet during the interview to document the facts and conditions when the noise occurs and any
customer's comments; refer to EI-9, "
Diagnostic Worksheet" . This information is necessary to duplicate the
conditions that exist when the noise occurs.
The customer may not be able to provide a detailed description or the location of the noise. Attempt to
obtain all the facts and conditions that exist when the noise occurs (or does not occur).
If there is more than one noise in the vehicle, be sure to diagnose and repair the noise that the customer
is concerned about. This can be accomplished by test driving the vehicle with the customer.
After identifying the type of noise, isolate the noise in terms of its characteristics. The noise characteristics
are provided so the customer, service adviser and technician are all speaking the same language when
defining the noise.
Squeak —(Like tennis shoes on a clean floor)
Squeak characteristics include the light contact/fast movement/brought on by road conditions/hard sur-
faces = higher pitch noise/softer surfaces = lower pitch noises/edge to surface = chirping.
Creak—(Like walking on an old wooden floor)
Creak characteristics include firm contact/slow movement/twisting with a rotational movement/pitch
dependent on materials/often brought on by activity.
Rattle—(Like shaking a baby rattle)
Rattle characteristics include the fast repeated contact/vibration or similar movement/loose parts/missing
clip or fastener/incorrect clearance.
Knock —(Like a knock on a door)
Knock characteristics include hollow sounding/sometimes repeating/often brought on by driver action.
Tick—(Like a clock second hand)
Tick characteristics include gentle contacting of light materials/loose components/can be caused by driver
action or road conditions.
Thump—(Heavy, muffled knock noise)
Thump characteristics include softer knock/dead sound often brought on by activity.
Buzz—(Like a bumble bee)
Buzz characteristics include high frequency rattle/firm contact.
Often the degree of acceptable noise level will vary depending upon the person. A noise that you may
judge as acceptable may be very irritating to the customer.
Weather conditions, especially humidity and temperature, may have a great effect on noise level.
SBT 8 42
Page 1916 of 3419
DRIVE BELTS
EM-13
C
D
E
F
G
H
I
J
K
L
MA
EM
Revision: October 20052005 QX56
INSTALLATION
Installation is in the reverse order of removal.
CAUTION:
Make sure belt is securely installed around all pulleys.
Rotate the crankshaft pulley several turns clockwise to equalize belt tension between pulleys.
Make sure belt tension is within the allowable working range, using indicator notch on the auto tensioner.
Refer to EM-12, "
Checking Drive Belts" .
Drive Belt Auto Tensioner and Idler PulleyEBS00LLZ
REMOVAL
1. Remove the air duct and resonator assembly. Refer to EM-14 .
2. Remove the drive belt. Refer to EM-12, "
Checking Drive Belts" .
3. Remove the auto tensioner and idler pulley using power tool.
INSTALLATION
Installation is in the reverse order of removal.
WBIA0607E
1. Auto tensioner 2. Idler pulley
Page 1939 of 3419
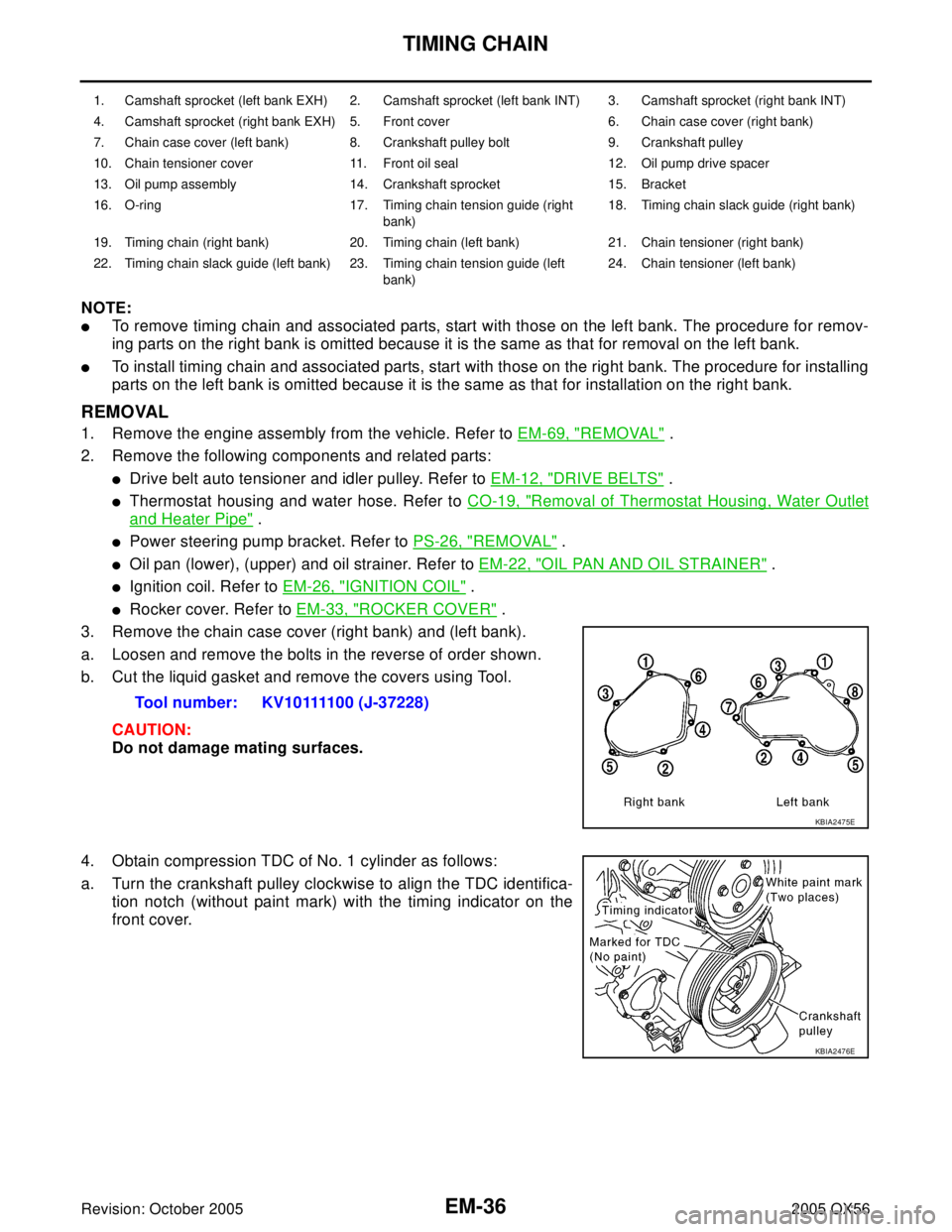
EM-36Revision: October 2005
TIMING CHAIN
2005 QX56
NOTE:
To remove timing chain and associated parts, start with those on the left bank. The procedure for remov-
ing parts on the right bank is omitted because it is the same as that for removal on the left bank.
To install timing chain and associated parts, start with those on the right bank. The procedure for installing
parts on the left bank is omitted because it is the same as that for installation on the right bank.
REMOVAL
1. Remove the engine assembly from the vehicle. Refer to EM-69, "REMOVAL" .
2. Remove the following components and related parts:
Drive belt auto tensioner and idler pulley. Refer to EM-12, "DRIVE BELTS" .
Thermostat housing and water hose. Refer to CO-19, "Removal of Thermostat Housing, Water Outlet
and Heater Pipe" .
Power steering pump bracket. Refer to PS-26, "REMOVAL" .
Oil pan (lower), (upper) and oil strainer. Refer to EM-22, "OIL PAN AND OIL STRAINER" .
Ignition coil. Refer to EM-26, "IGNITION COIL" .
Rocker cover. Refer to EM-33, "ROCKER COVER" .
3. Remove the chain case cover (right bank) and (left bank).
a. Loosen and remove the bolts in the reverse of order shown.
b. Cut the liquid gasket and remove the covers using Tool.
CAUTION:
Do not damage mating surfaces.
4. Obtain compression TDC of No. 1 cylinder as follows:
a. Turn the crankshaft pulley clockwise to align the TDC identifica-
tion notch (without paint mark) with the timing indicator on the
front cover.
1. Camshaft sprocket (left bank EXH) 2. Camshaft sprocket (left bank INT) 3. Camshaft sprocket (right bank INT)
4. Camshaft sprocket (right bank EXH) 5. Front cover 6. Chain case cover (right bank)
7. Chain case cover (left bank) 8. Crankshaft pulley bolt 9. Crankshaft pulley
10. Chain tensioner cover 11. Front oil seal 12. Oil pump drive spacer
13. Oil pump assembly 14. Crankshaft sprocket 15. Bracket
16. O-ring 17. Timing chain tension guide (right
bank)18. Timing chain slack guide (right bank)
19. Timing chain (right bank) 20. Timing chain (left bank) 21. Chain tensioner (right bank)
22. Timing chain slack guide (left bank) 23. Timing chain tension guide (left
bank)24. Chain tensioner (left bank)
Tool number: KV10111100 (J-37228)
KBIA2475E
KBIA2476E
Page 1945 of 3419
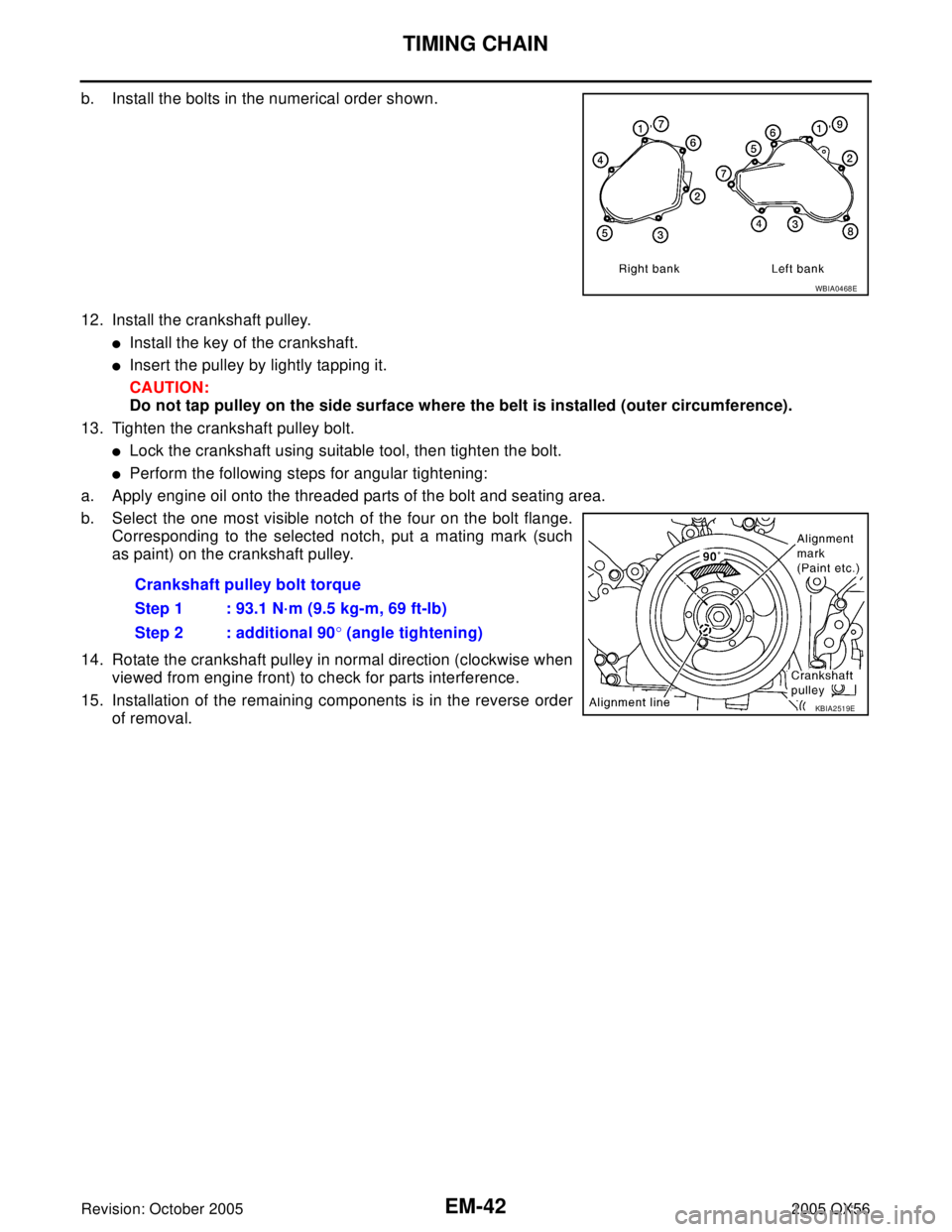
EM-42Revision: October 2005
TIMING CHAIN
2005 QX56
b. Install the bolts in the numerical order shown.
12. Install the crankshaft pulley.
Install the key of the crankshaft.
Insert the pulley by lightly tapping it.
CAUTION:
Do not tap pulley on the side surface where the belt is installed (outer circumference).
13. Tighten the crankshaft pulley bolt.
Lock the crankshaft using suitable tool, then tighten the bolt.
Perform the following steps for angular tightening:
a. Apply engine oil onto the threaded parts of the bolt and seating area.
b. Select the one most visible notch of the four on the bolt flange.
Corresponding to the selected notch, put a mating mark (such
as paint) on the crankshaft pulley.
14. Rotate the crankshaft pulley in normal direction (clockwise when
viewed from engine front) to check for parts interference.
15. Installation of the remaining components is in the reverse order
of removal.
WBIA0468E
Crankshaft pulley bolt torque
Step 1 : 93.1 N·m (9.5 kg-m, 69 ft-lb)
Step 2 : additional 90° (angle tightening)
KBIA2519E
Page 1955 of 3419
EM-52Revision: October 2005
CAMSHAFT
2005 QX56
3. Remove the right bank and left bank rocker covers using power tool. Refer to EM-33, "Removal and
Installation" .
4. Turn the crankshaft pulley in the normal direction (clockwise
when viewed from engine front) to align TDC identification notch
(without paint mark) with timing indicator.
5. At this time, make sure both the intake and exhaust cam noses
of No. 1 cylinder (top front on left bank) face outside.
If they do not face outside, turn crankshaft pulley once more.
6. Measure valve clearances at the locations marked “×” as shown
in the table below (locations indicated with black arrow).
NOTE:
Firing order 1-8-7-3-6-5-4-2
No. 1 cylinder compression TDC
KBIA2476E
KBIA0400J
Measuring position (RH bank) No. 2 CYL No. 4 CYL No. 6 CYL No. 8 CYL
No. 1 cylinder at TDC EXH ×
INT××
Measuring position (LH bank) No. 1 CYL No. 3 CYL No. 5 CYL No. 7 CYL
No. 1 cylinder at TDCINT××
EXH××
KBIA2526E
Page 1956 of 3419
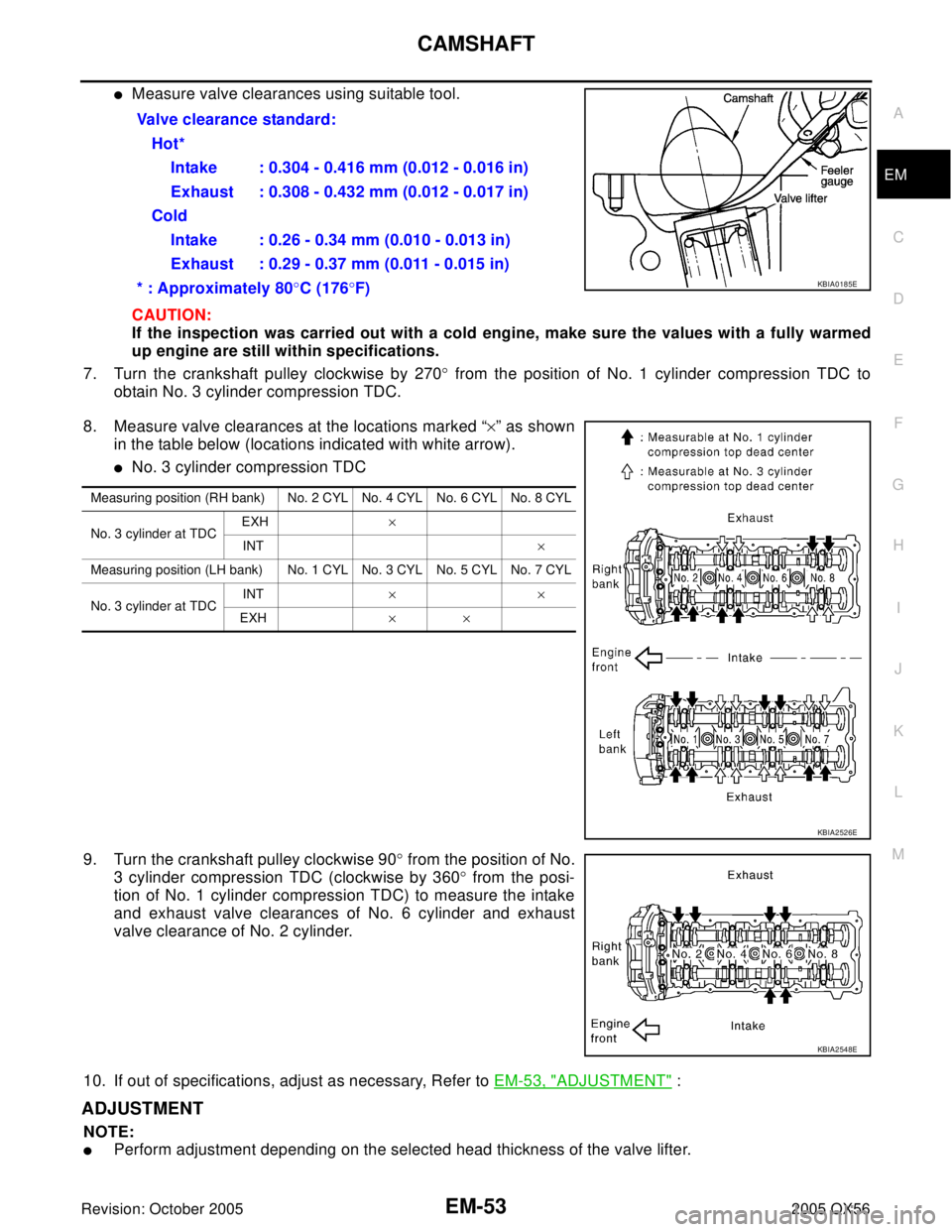
CAMSHAFT
EM-53
C
D
E
F
G
H
I
J
K
L
MA
EM
Revision: October 20052005 QX56
Measure valve clearances using suitable tool.
CAUTION:
If the inspection was carried out with a cold engine, make sure the values with a fully warmed
up engine are still within specifications.
7. Turn the crankshaft pulley clockwise by 270° from the position of No. 1 cylinder compression TDC to
obtain No. 3 cylinder compression TDC.
8. Measure valve clearances at the locations marked “×” as shown
in the table below (locations indicated with white arrow).
No. 3 cylinder compression TDC
9. Turn the crankshaft pulley clockwise 90° from the position of No.
3 cylinder compression TDC (clockwise by 360° from the posi-
tion of No. 1 cylinder compression TDC) to measure the intake
and exhaust valve clearances of No. 6 cylinder and exhaust
valve clearance of No. 2 cylinder.
10. If out of specifications, adjust as necessary, Refer to EM-53, "
ADJUSTMENT" :
ADJUSTMENT
NOTE:
Perform adjustment depending on the selected head thickness of the valve lifter.Valve clearance standard:
Hot*
Intake : 0.304 - 0.416 mm (0.012 - 0.016 in)
Exhaust : 0.308 - 0.432 mm (0.012 - 0.017 in)
Cold
Intake : 0.26 - 0.34 mm (0.010 - 0.013 in)
Exhaust : 0.29 - 0.37 mm (0.011 - 0.015 in)
* : Approximately 80°C (176°F)
KBIA0185E
Measuring position (RH bank) No. 2 CYL No. 4 CYL No. 6 CYL No. 8 CYL
No. 3 cylinder at TDC EXH ×
INT ×
Measuring position (LH bank) No. 1 CYL No. 3 CYL No. 5 CYL No. 7 CYL
No. 3 cylinder at TDCINT××
EXH××
KBIA2526E
KBIA2548E