Page 91 of 754
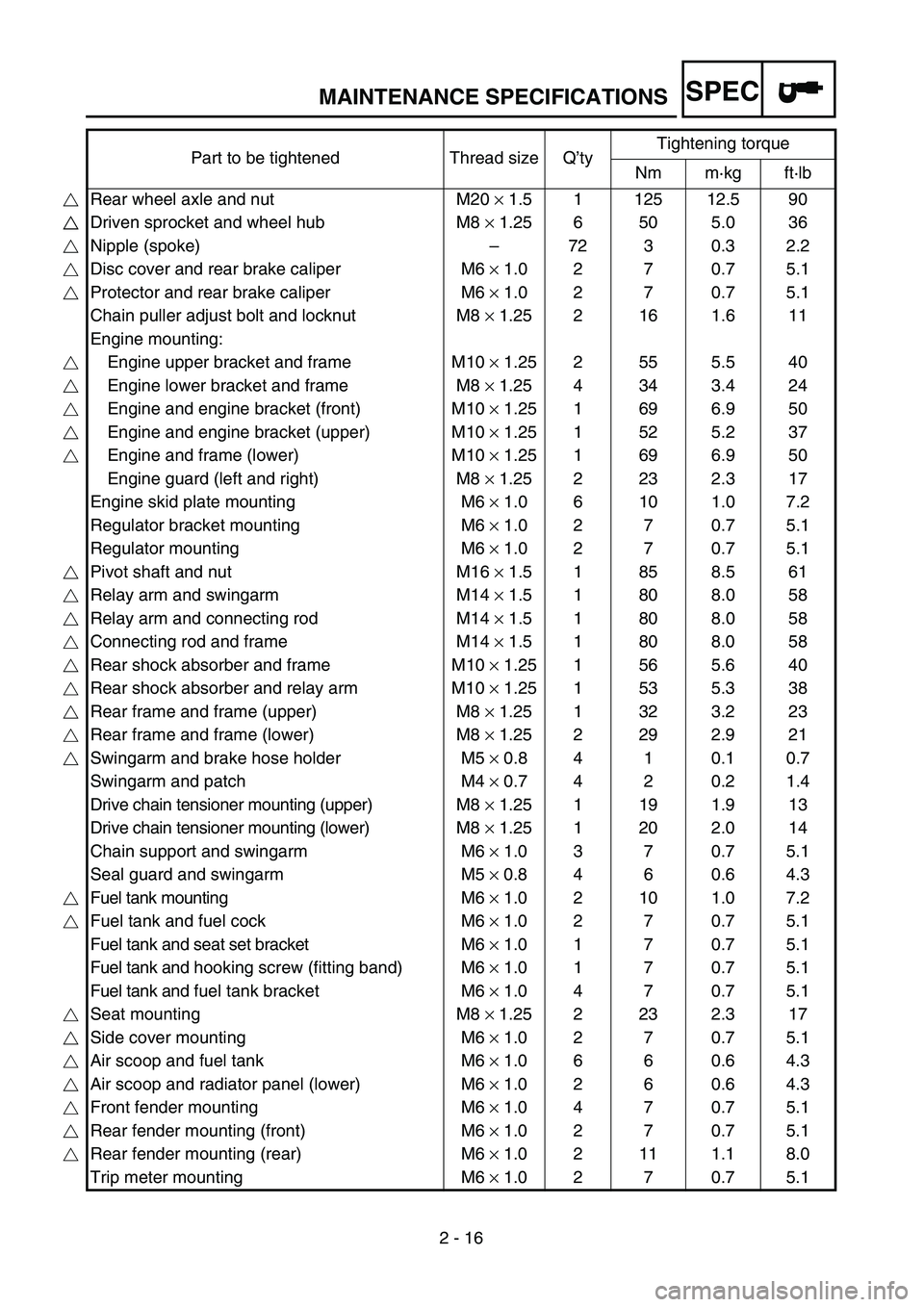
SPEC
2 - 16
MAINTENANCE SPECIFICATIONS
Part to be tightened Thread size Q’tyTightening torque
Nm m·kg ft·lb
Rear wheel axle and nut M20 × 1.5 1 125 12.5 90
Driven sprocket and wheel hub M8 × 1.25 6 50 5.0 36
Nipple (spoke)–72 3 0.3 2.2
Disc cover and rear brake caliper M6 × 1.0 2 7 0.7 5.1
Protector and rear brake caliper M6 × 1.0 2 7 0.7 5.1
Chain puller adjust bolt and locknut M8 × 1.25 2 16 1.6 11
Engine mounting:
Engine upper bracket and frame M10 × 1.25 2 55 5.5 40
Engine lower bracket and frame M8 × 1.25 4 34 3.4 24
Engine and engine bracket (front) M10 × 1.25 1 69 6.9 50
Engine and engine bracket (upper) M10 × 1.25 1 52 5.2 37
Engine and frame (lower) M10 × 1.25 1 69 6.9 50
Engine guard (left and right) M8 × 1.25 2 23 2.3 17
Engine skid plate mounting M6 × 1.0 6 10 1.0 7.2
Regulator bracket mounting M6 × 1.0 2 7 0.7 5.1
Regulator mounting M6 × 1.0 2 7 0.7 5.1
Pivot shaft and nut M16 × 1.5 1 85 8.5 61
Relay arm and swingarm M14 × 1.5 1 80 8.0 58
Relay arm and connecting rod M14 × 1.5 1 80 8.0 58
Connecting rod and frame M14 × 1.5 1 80 8.0 58
Rear shock absorber and frame M10 × 1.25 1 56 5.6 40
Rear shock absorber and relay arm M10 × 1.25 1 53 5.3 38
Rear frame and frame (upper) M8 × 1.25 1 32 3.2 23
Rear frame and frame (lower) M8 × 1.25 2 29 2.9 21
Swingarm and brake hose holder M5 × 0.8 4 1 0.1 0.7
Swingarm and patch M4 × 0.7 4 2 0.2 1.4
Drive chain tensioner mounting (upper) M8 × 1.25 1 19 1.9 13
Drive chain tensioner mounting (lower) M8 × 1.25 1 20 2.0 14
Chain support and swingarm M6 × 1.0 3 7 0.7 5.1
Seal guard and swingarm M5 × 0.8 4 6 0.6 4.3
Fuel tank mounting M6 × 1.0 2 10 1.0 7.2
Fuel tank and fuel cock M6 × 1.0 2 7 0.7 5.1
Fuel tank and seat set bracket M6 × 1.0 1 7 0.7 5.1
Fuel tank and hooking screw (fitting band) M6 × 1.0 1 7 0.7 5.1
Fuel tank and fuel tank bracket M6 × 1.0 4 7 0.7 5.1
Seat mounting M8 × 1.25 2 23 2.3 17
Side cover mounting M6 × 1.0 2 7 0.7 5.1
Air scoop and fuel tank M6 × 1.0 6 6 0.6 4.3
Air scoop and radiator panel (lower) M6 × 1.0 2 6 0.6 4.3
Front fender mounting M6 × 1.0 4 7 0.7 5.1
Rear fender mounting (front) M6 × 1.0 2 7 0.7 5.1
Rear fender mounting (rear) M6 × 1.0 2 11 1.1 8.0
Trip meter mounting M6 × 1.0 2 7 0.7 5.1
Page 94 of 754
SPEC
2 - 19
MAINTENANCE SPECIFICATIONS
NOTE:
Tighten the rotor nut to 65 Nm (6.5 m · kg, 47 ft · lb), loosen and retighten the rotor nut to 65 Nm
(6.5 m · kg, 47 ft · lb). Starter relay:
Model/manufacturer 2768090-A/JIDECO ----
Amperage rating 180 A ----
Coil winding resistance 4.2 ~ 4.6 Ω at 20 ˚C (68 ˚F) ----
Starting circuit cut-off relay:
Model/manufacturer ACM33221 M06/MATSUSHITA ----
Coil winding resistance 75.69 ~ 92.51 Ω at 20 ˚C (68 ˚F) ----
Fuse (amperage × quantity):
Main fuse 10 A × 1 ----
Reserve fuse 10 A × 1 ----
Part to be tightened Thread size Q’tyTightening torque
Nm m·kg ft·lb
Stator M5 × 0.8 2 7 0.7 5.1
Holder (AC magneto lead) M5 × 0.8 2 7 0.7 5.1
Rotor M12 × 1.25 1 Refer to NOTE.
Neutral switch M5 × 0.8 2 4 0.4 2.9
Starter motor M6 × 1.0 2 10 1.0 7.2
Starter relay terminal M6 × 1.0 2 4 0.4 2.9 Item Standard Limit
Page 168 of 754
2 - 27
SPECCABLE ROUTING DIAGRAM
1Starter motor lead
2Negative battery lead
3Wire harness
4Clamp
5Taillight lead
6Coolant reservoir tank
breather hose
7Coolant reservoir hose
8Positive battery lead
9Starting circuit cut-off
relay
0BatteryÅPosition the starter motor lead,
negative battery lead and wire
harness in the tank damper slit.
ıFasten the wire harness to the
frame with a plastic locking tie and
cut off the tie end.
ÇDo not allow the taillight lead to
slacken.
ÎPass the starter motor lead and
negative battery lead over the car-
buretor.
‰Fasten the coolant reservoir tank
breather hose and coolant reser-
voir hose to the frame with a plas-
tic band.ÏPass the coolant reservoir hose
on the outside of the coolant res-
ervoir tank breather hose.
Page 174 of 754
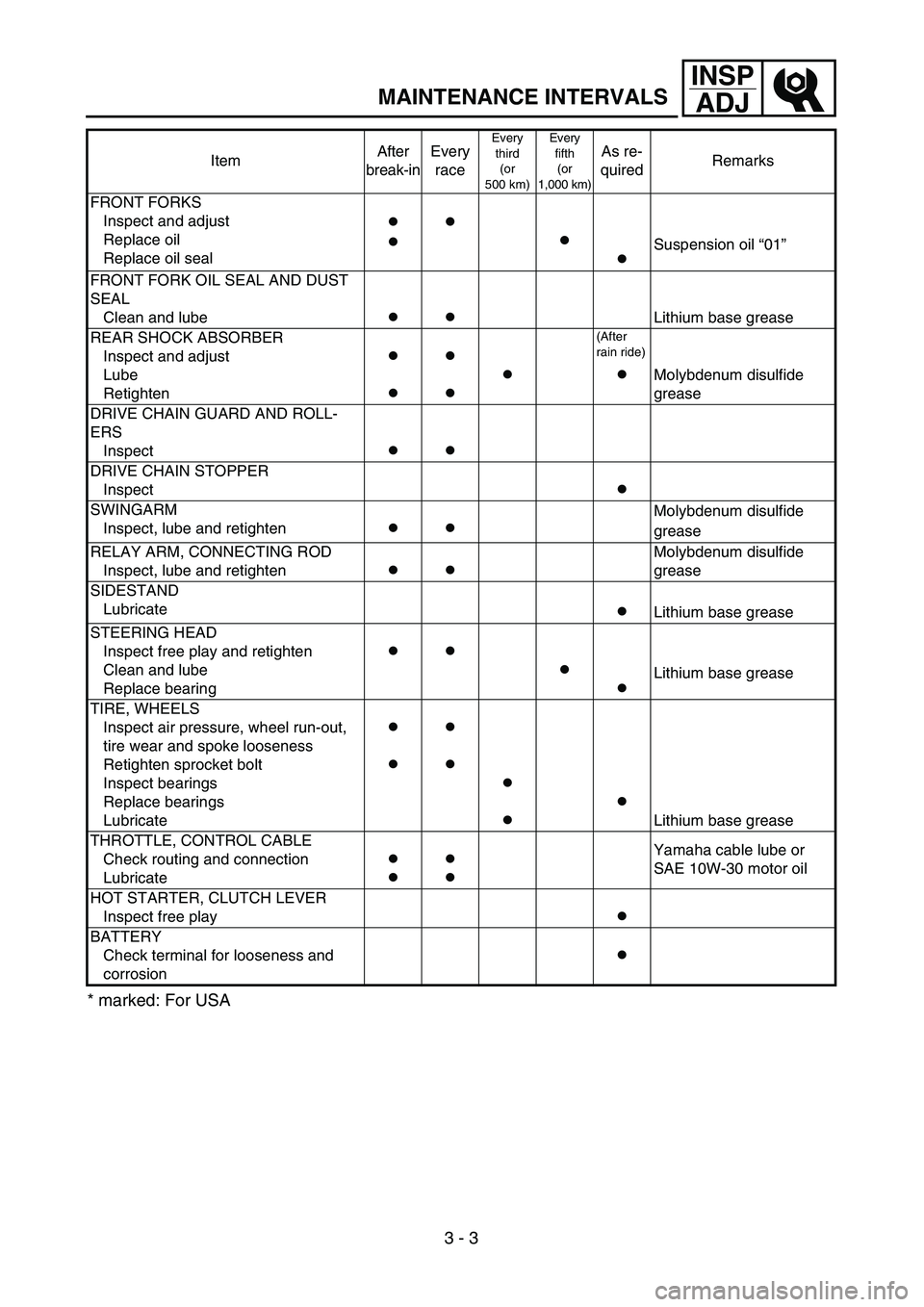
3 - 3
INSP
ADJ
MAINTENANCE INTERVALS
* marked: For USA
FRONT FORKS
Inspect and adjust
Replace oil
Replace oil seal
●
●
●
●
●
Suspension oil “01”
FRONT FORK OIL SEAL AND DUST
SEAL
Clean and lube
●
●
Lithium base grease
REAR SHOCK ABSORBER
Inspect and adjust
Lube
Retighten
●
●
●
●
●
(After
rain ride)
● Molybdenum disulfide
grease
DRIVE CHAIN GUARD AND ROLL-
ERS
Inspect
● ●
DRIVE CHAIN STOPPER
Inspect
●
SWINGARM
Inspect, lube and retighten
● ● Molybdenum disulfide
grease
RELAY ARM, CONNECTING ROD
Inspect, lube and retighten
● ● Molybdenum disulfide
grease
SIDESTAND
Lubricate
●Lithium base grease
STEERING HEAD
Inspect free play and retighten
Clean and lube
Replace bearing
● ●
●
● Lithium base grease
TIRE, WHEELS
Inspect air pressure, wheel run-out,
tire wear and spoke looseness
Retighten sprocket bolt
Inspect bearings
Replace bearings
Lubricate
●
●
●
●
●
●
●
Lithium base grease
THROTTLE, CONTROL CABLE
Check routing and connection
Lubricate
●
●
●
● Yamaha cable lube or
SAE 10W-30 motor oil
HOT STARTER, CLUTCH LEVER
Inspect free play
●
BATTERY
Check terminal for looseness and
corrosion
●
ItemAfter
break-inEvery
race
Every
third
(or
500 km)Every
fifth
(or
1,000 km)As re-
quiredRemarks
Page 608 of 754
5 - 52
CHASSWINGARM
EC570000
SWINGARM
Extent of removal:1 Swingarm removal
Extent of removal Order Part name Q’ty Remarks
SWINGARM REMOVAL
WARNINGSupport the machine securely so there is no
danger of it falling over.
Preparation for removal Hold the machine by placing the
suitable stand under the engine.
Brake hose holder
Rear caliper
Bolt (brake pedal)
Drive chainRefer to “FRONT BRAKE AND REAR
BRAKE” section.
Shift the brake pedal backward.
1 Chain support 1
2 Chain tensioner (lower) 1
3 Bolt (rear shock absorber-relay
arm)1 Hold the swingarm.
4 Bolt (connecting rod) 1
5 Pivot shaft 1
6 Swingarm 1
1
Page 610 of 754
5 - 53
CHASSWINGARM
EC578000
SWINGARM DISASSEMBLY
Extent of removal:1 Swingarm disassembly2 Connecting rod removal and disassembly
3 Relay arm removal and disassembly
Extent of removal Order Part name Q’ty Remarks
SWINGARM DISASSEMBLY
1 Cap 2
2 Relay arm 1
3 Connecting rod 1
4 Collar 2
5 Oil seal 2
6 Thrust bearing 2
7 Bush 2
8 Oil seal 8
9 Bearing 8 Refer to “REMOVAL POINTS”.
1
2
32
3
Page 612 of 754
5 - 54
CHASSWINGARM
EC573000
REMOVAL POINTS
EC573200
Bearing
1. Remove:
Bearing 1
NOTE:
Install the bearing by pressing its outer race.
EC574010
INSPECTION
Wash the bearings, bushes, collars, and cov-
ers in a solvent.
EC574111
Swingarm
1. Inspect:
Bearing 1
Bush 2
Free play exists/unsmooth revolution/
rust → Replace bearing and bush as a
set.
2. Inspect:
Oil seal 3
Damage → Replace.
EC574210
Relay arm
1. Inspect:
Bearing (polylube bearing) 1
Collar 2
Free play exists/unsmooth revolution/rust
→ Replace bearing and collar as a set.
2. Inspect:
Bearing (polylube bearing) 1
Loss of solid lubrication → Replace.
Oil seal 3
Damage → Replace.
NOTE:
Polylube bearings, with solid lubrication, have
been adopted with the intent to make the nee-
dle bearings, used in this model, maintenance
free. With polylube bearings, no grease nipple
and regular lubrication is necessary. However,
grease should be applied to all oil seals and
collars when removed or installed.
Page 616 of 754
5 - 56
CHASSWINGARM
2. Install:
Bearing 1
Oil seal 2
To relay arm.
NOTE:
Apply the molybdenum disulfide grease on
the bearing when installing.
Install the bearing by pressing it on the side
having the manufacture’s marks or numbers.
3. Install:
Bearing 1
Oil seal 2
To connecting rod.
NOTE:
Apply the molybdenum disulfide grease on
the bearing when installing.
Install the bearing by pressing it on the side
having the manufacture’s marks or numbers.
Installed depth of bearings a:
5 mm (0.20 in)
Installed depth of bearings a:
5 mm (0.20 in)
Swingarm
1. Install:
Bush 1
Thrust bearing 2
Oil seal 3
Collar 4
To swingarm 5.
NOTE:
Apply the molybdenum disulfide grease on the
bushes, thrust bearings and oil seal lips.
2. Install:
Collar 1
To relay arm 2.
NOTE:
Apply the molybdenum disulfide grease on the
collars and oil seal lips.