Page 91 of 801
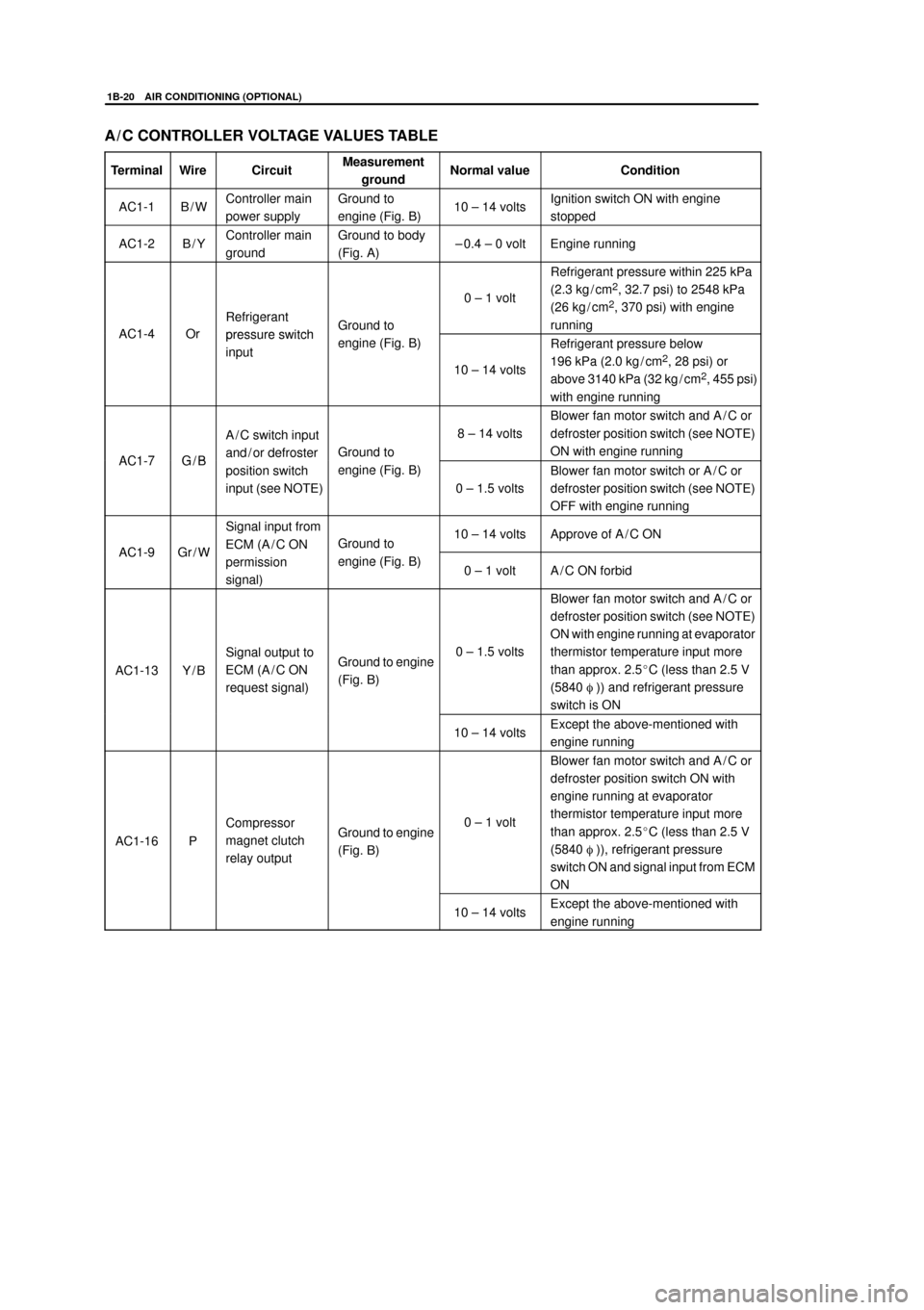
YH4
GRAND
VITARA
1B-20 AIR CONDITIONING (OPTIONAL)
A / C CONTROLLER VOLTAGE VALUES TABLE
TerminalWireCircuitMeasurement
groundNormal valueCondition
AC1-1B/WController main
power supplyGround to
engine (Fig. B)10 ± 14 voltsIgnition switch ON with engine
stopped
AC1-2B/YController main
groundGround to body
(Fig. A)± 0.4 ± 0 voltEngine running
AC1 4Or
Refrigerant
p
ressure switchGround to
0 ± 1 volt
Refrigerant pressure within 225 kPa
(2.3 kg / cm
2, 32.7 psi) to 2548 kPa
(26 kg / cm
2, 370 psi) with engine
running
AC1-4Orpressure switch
inputengine (Fig. B)
10 ± 14 volts
Refrigerant pressure below
196 kPa (2.0 kg / cm
2, 28 psi) or
above 3140 kPa (32 kg / cm
2, 455 psi)
with engine running
AC1 7G/B
A / C switch input
and / or defroster
Ground to
8 ± 14 volts
Blower fan motor switch and A / C or
defroster position switch (see NOTE)
ON with engine running
AC1-7G/Bposition switch
input (see NOTE)engine (Fig. B)
0 ± 1.5 volts
Blower fan motor switch or A / C or
defroster position switch (see NOTE)
OFF with engine running
AC1 9Gr/W
Signal input from
ECM (A / C ON
Ground to10 ± 14 voltsApprove of A / C ON
AC1-9Gr/W(
permission
signal)engine (Fig. B)0 ± 1 voltA / C ON forbid
AC1-13Y/B
Signal output to
ECM (A / C ON
request signal)Ground to engine
(Fig. B)0 ± 1.5 volts
Blower fan motor switch and A / C or
defroster position switch (see NOTE)
ON with engine running at evaporator
thermistor temperature input more
than approx. 2.5C (less than 2.5 V
(5840 )) and refrigerant pressure
switch is ON
10 ± 14 voltsExcept the above-mentioned with
engine running
AC1-16P
Compressor
magnet clutch
relay outputGround to engine
(Fig. B)0 ± 1 volt
Blower fan motor switch and A / C or
defroster position switch ON with
engine running at evaporator
thermistor temperature input more
than approx. 2.5C (less than 2.5 V
(5840 )), refrigerant pressure
switch ON and signal input from ECM
ON
10 ± 14 voltsExcept the above-mentioned with
engine running
Page 92 of 801
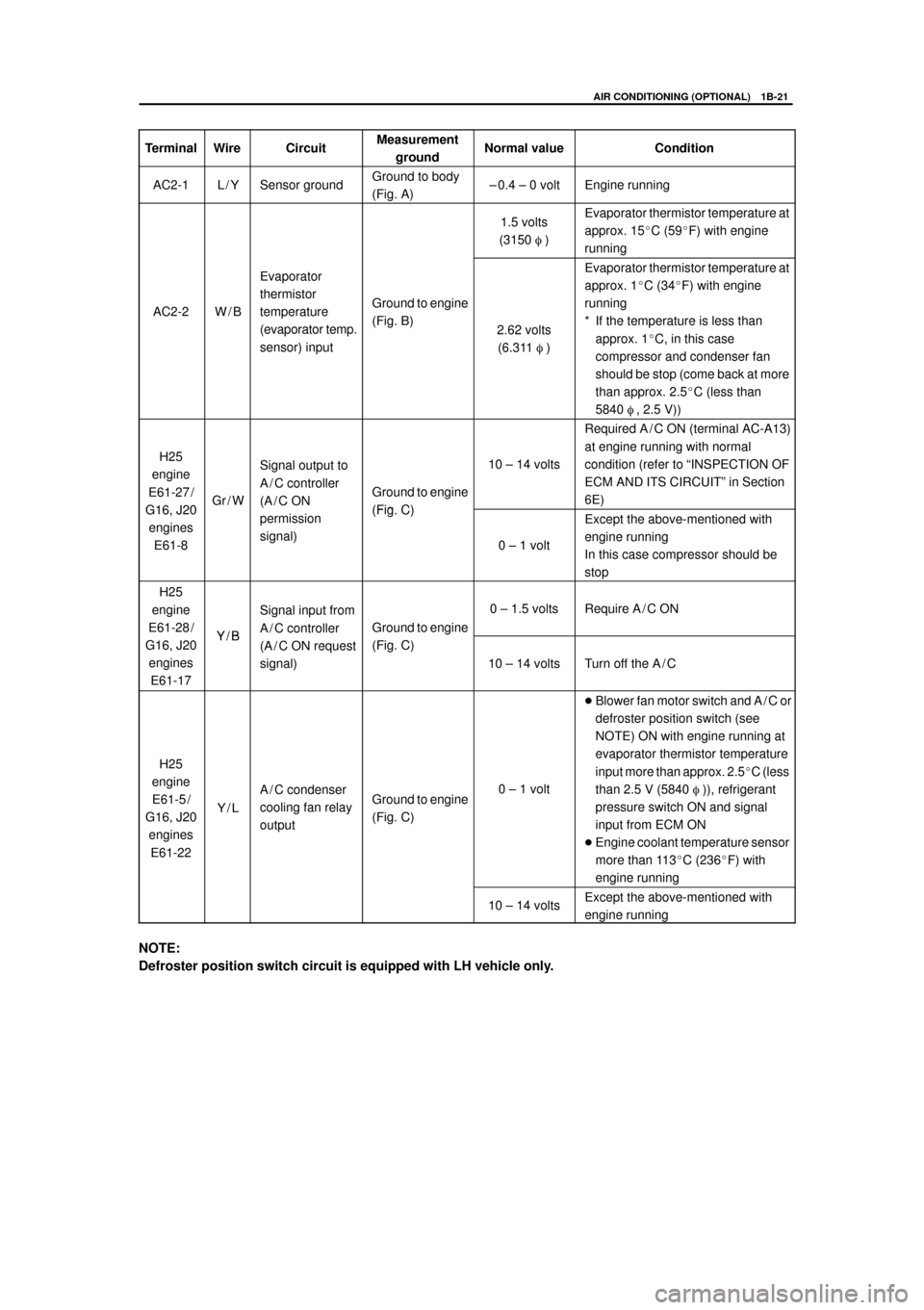
YH4
GRAND
VITARA
AIR CONDITIONING (OPTIONAL) 1B-21
TerminalWireCircuitMeasurement
groundNormal valueCondition
AC2-1L/YSensor groundGround to body
(Fig. A)± 0.4 ± 0 voltEngine running
1.5 volts
(3150 )Evaporator thermistor temperature at
approx. 15C (59F) with engine
running
AC2-2W/B
Evaporator
thermistor
temperature
(evaporator temp.
sensor) input
Ground to engine
(Fig. B)
2.62 volts
(6.311 )
Evaporator thermistor temperature at
approx. 1C (34F) with engine
running
* If the temperature is less than
approx. 1C, in this case
compressor and condenser fan
should be stop (come back at more
than approx. 2.5C (less than
5840 , 2.5 V))
H25
engine
E61-27 /
G16 J20Gr/W
Signal output to
A / C controller
(A / C ON
Ground to engine
(Fig C)
10 ± 14 volts
Required A / C ON (terminal AC-A13)
at engine running with normal
condition (refer to ªINSPECTION OF
ECM AND ITS CIRCUITº in Section
6E)
G16, J20
engines
E61-8
(
permission
signal)(Fig. C)
0 ± 1 volt
Except the above-mentioned with
engine running
In this case compressor should be
stop
H25
engine
E61-28 /
Y/B
Signal input from
A / C controller
Ground to engine
0 ± 1.5 voltsRequire A / C ON
G16, J20
engines
E61-17Y/B(A / C ON request
signal)
g
(Fig. C)
10 ± 14 voltsTurn off the A / C
H25
engine
E61-5 /
G16, J20
engines
E61-22
Y/L
A / C condenser
cooling fan relay
outputGround to engine
(Fig. C)0 ± 1 volt
Blower fan motor switch and A / C or
defroster position switch (see
NOTE) ON with engine running at
evaporator thermistor temperature
input more than approx. 2.5C (less
than 2.5 V (5840 )), refrigerant
pressure switch ON and signal
input from ECM ON
Engine coolant temperature sensor
more than 113C (236F) with
engine running
10 ± 14 voltsExcept the above-mentioned with
engine running
NOTE:
Defroster position switch circuit is equipped with LH vehicle only.
Page 93 of 801
YH4
GRAND
VITARA
J20 engine
H25 engine G16 engine
1. Generator belt
2. Compressor drive belt3. Compressor pulley
4. Crankshaft pulley
1B-22 AIR CONDITIONING (OPTIONAL)
DRIVE BELT
INSPECTION
For G16 and H25 engines
Refer to Section 3B1 for details.
For J20 engine
Refer to Section 6H for details.
Page 97 of 801
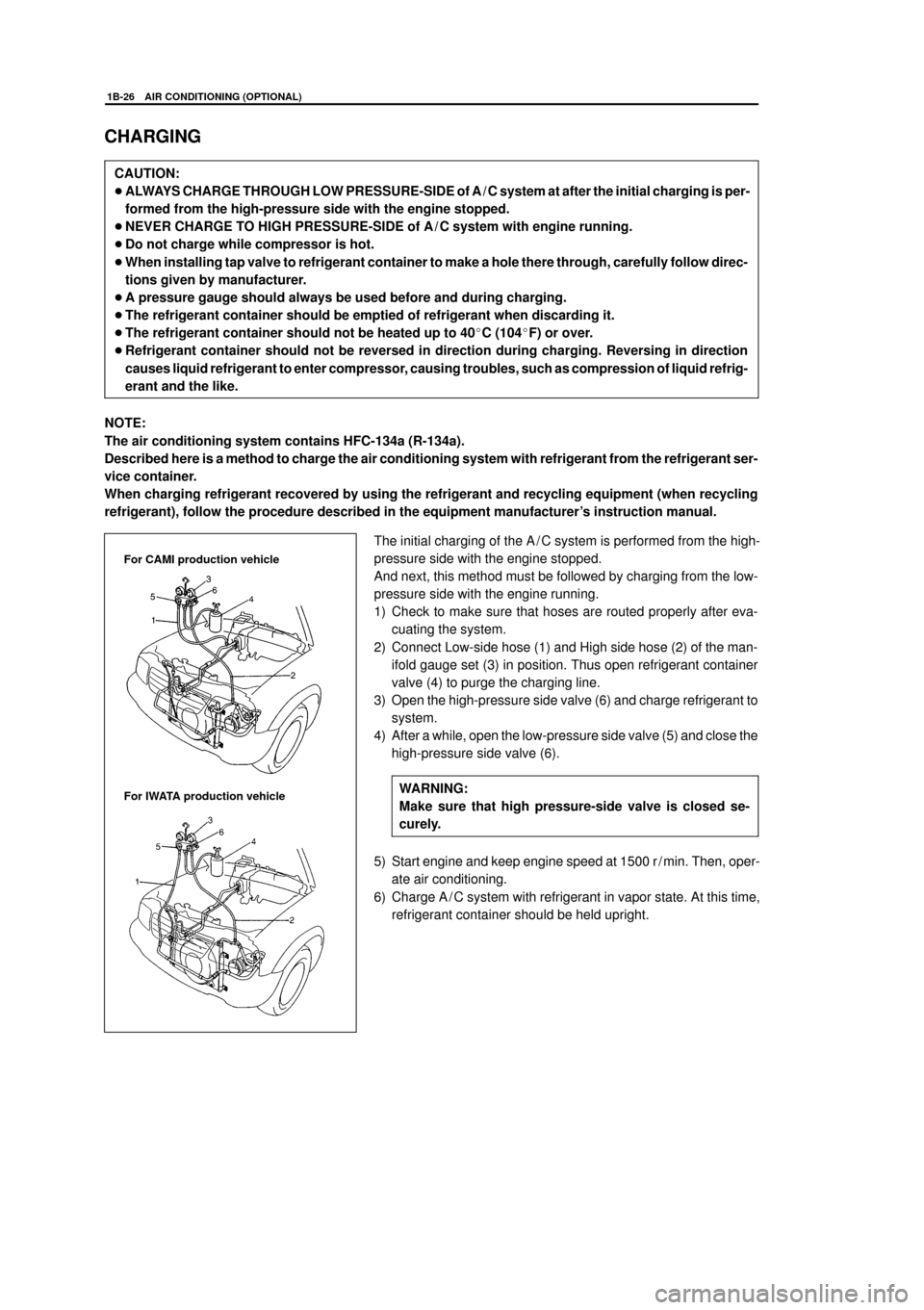
YH4
GRAND
VITARA
For CAMI production vehicle
For IWATA production vehicle
1B-26 AIR CONDITIONING (OPTIONAL)
CHARGING
CAUTION:
ALWAYS CHARGE THROUGH LOW PRESSURE-SIDE of A / C system at after the initial charging is per-
formed from the high-pressure side with the engine stopped.
NEVER CHARGE TO HIGH PRESSURE-SIDE of A / C system with engine running.
Do not charge while compressor is hot.
When installing tap valve to refrigerant container to make a hole there through, carefully follow direc-
tions given by manufacturer.
A pressure gauge should always be used before and during charging.
The refrigerant container should be emptied of refrigerant when discarding it.
The refrigerant container should not be heated up to 40C (104F) or over.
Refrigerant container should not be reversed in direction during charging. Reversing in direction
causes liquid refrigerant to enter compressor, causing troubles, such as compression of liquid refrig-
erant and the like.
NOTE:
The air conditioning system contains HFC-134a (R-134a).
Described here is a method to charge the air conditioning system with refrigerant from the refrigerant ser-
vice container.
When charging refrigerant recovered by using the refrigerant and recycling equipment (when recycling
refrigerant), follow the procedure described in the equipment manufacturer's instruction manual.
The initial charging of the A / C system is performed from the high-
pressure side with the engine stopped.
And next, this method must be followed by charging from the low-
pressure side with the engine running.
1) Check to make sure that hoses are routed properly after eva-
cuating the system.
2) Connect Low-side hose (1) and High side hose (2) of the man-
ifold gauge set (3) in position. Thus open refrigerant container
valve (4) to purge the charging line.
3) Open the high-pressure side valve (6) and charge refrigerant to
system.
4) After a while, open the low-pressure side valve (5) and close the
high-pressure side valve (6).
WARNING:
Make sure that high pressure-side valve is closed se-
curely.
5) Start engine and keep engine speed at 1500 r / min. Then, oper-
ate air conditioning.
6) Charge A / C system with refrigerant in vapor state. At this time,
refrigerant container should be held upright.
Page 100 of 801
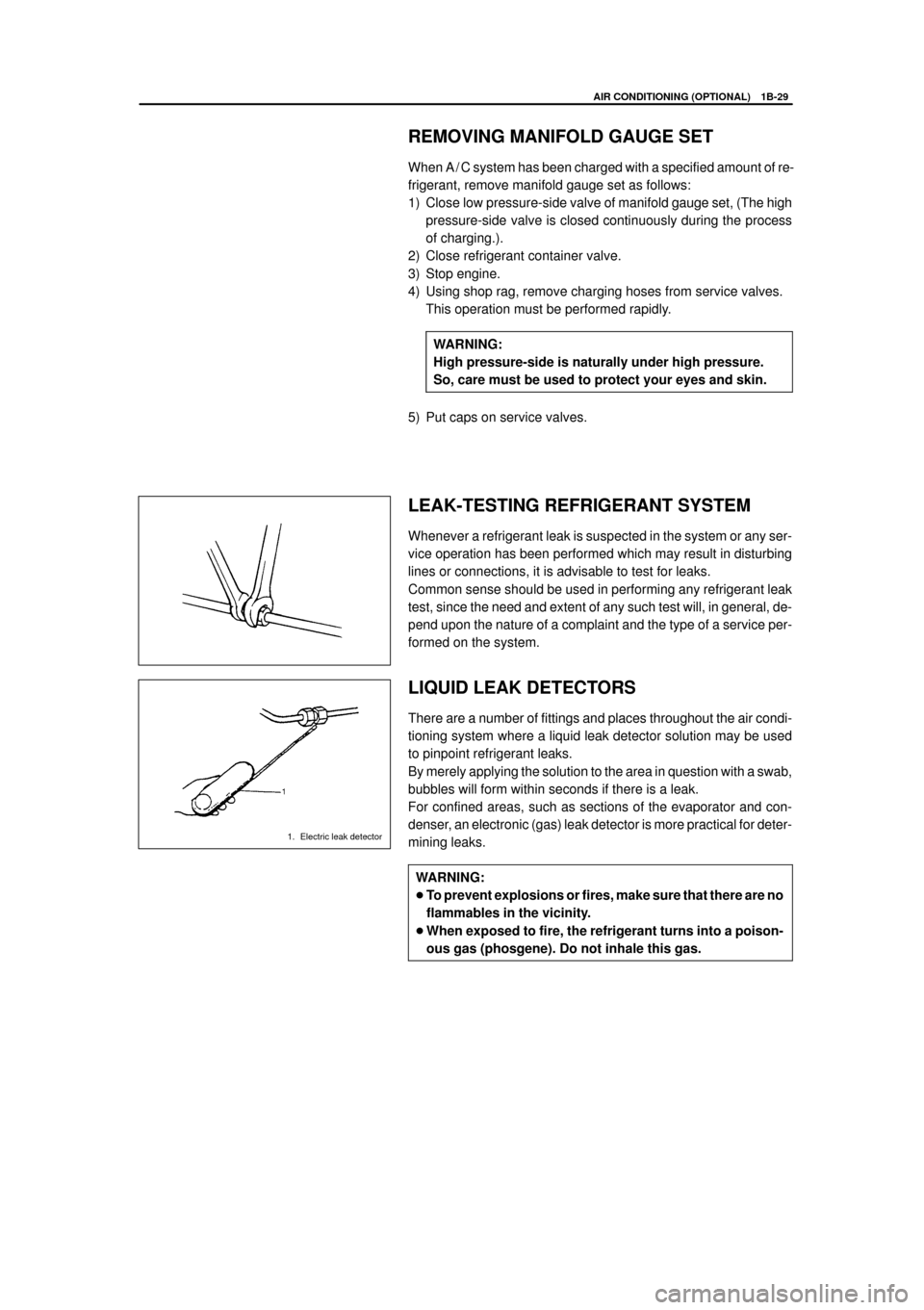
YH4
GRAND
VITARA
1. Electric leak detector
AIR CONDITIONING (OPTIONAL) 1B-29
REMOVING MANIFOLD GAUGE SET
When A / C system has been charged with a specified amount of re-
frigerant, remove manifold gauge set as follows:
1) Close low pressure-side valve of manifold gauge set, (The high
pressure-side valve is closed continuously during the process
of charging.).
2) Close refrigerant container valve.
3) Stop engine.
4) Using shop rag, remove charging hoses from service valves.
This operation must be performed rapidly.
WARNING:
High pressure-side is naturally under high pressure.
So, care must be used to protect your eyes and skin.
5) Put caps on service valves.
LEAK-TESTING REFRIGERANT SYSTEM
Whenever a refrigerant leak is suspected in the system or any ser-
vice operation has been performed which may result in disturbing
lines or connections, it is advisable to test for leaks.
Common sense should be used in performing any refrigerant leak
test, since the need and extent of any such test will, in general, de-
pend upon the nature of a complaint and the type of a service per-
formed on the system.
LIQUID LEAK DETECTORS
There are a number of fittings and places throughout the air condi-
tioning system where a liquid leak detector solution may be used
to pinpoint refrigerant leaks.
By merely applying the solution to the area in question with a swab,
bubbles will form within seconds if there is a leak.
For confined areas, such as sections of the evaporator and con-
denser, an electronic (gas) leak detector is more practical for deter-
mining leaks.
WARNING:
To prevent explosions or fires, make sure that there are no
flammables in the vicinity.
When exposed to fire, the refrigerant turns into a poison-
ous gas (phosgene). Do not inhale this gas.
Page 103 of 801
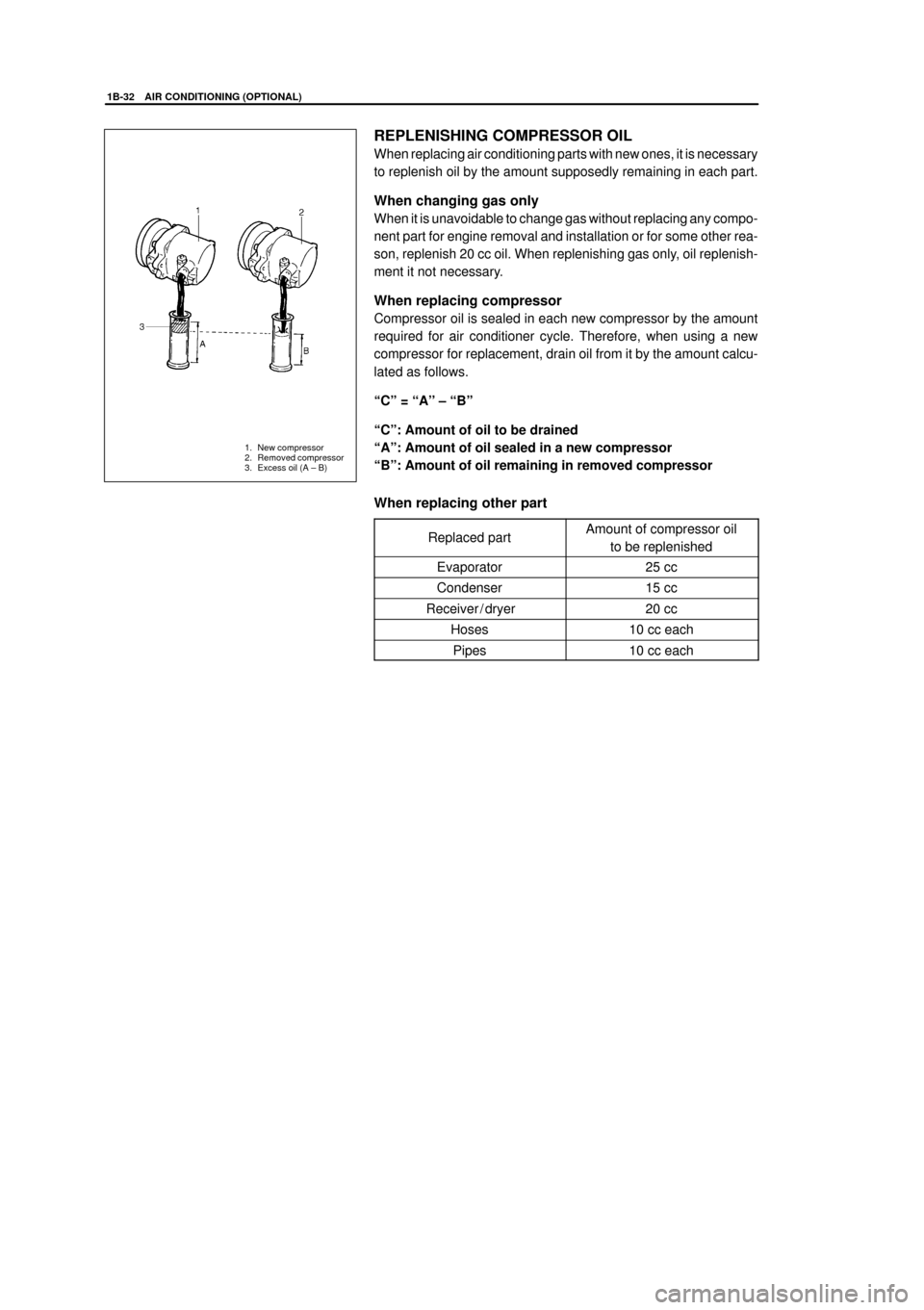
YH4
GRAND
VITARA
1. New compressor
2. Removed compressor
3. Excess oil (A ± B)
1B-32 AIR CONDITIONING (OPTIONAL)
REPLENISHING COMPRESSOR OIL
When replacing air conditioning parts with new ones, it is necessary
to replenish oil by the amount supposedly remaining in each part.
When changing gas only
When it is unavoidable to change gas without replacing any compo-
nent part for engine removal and installation or for some other rea-
son, replenish 20 cc oil. When replenishing gas only, oil replenish-
ment it not necessary.
When replacing compressor
Compressor oil is sealed in each new compressor by the amount
required for air conditioner cycle. Therefore, when using a new
compressor for replacement, drain oil from it by the amount calcu-
lated as follows.
ªCº = ªAº ± ªBº
ªCº: Amount of oil to be drained
ªAº: Amount of oil sealed in a new compressor
ªBº: Amount of oil remaining in removed compressor
When replacing other part
Replaced partAmount of compressor oil
to be replenished
Evaporator25 cc
Condenser15 cc
Receiver / dryer20 cc
Hoses10 cc each
Pipes10 cc each
Page 110 of 801
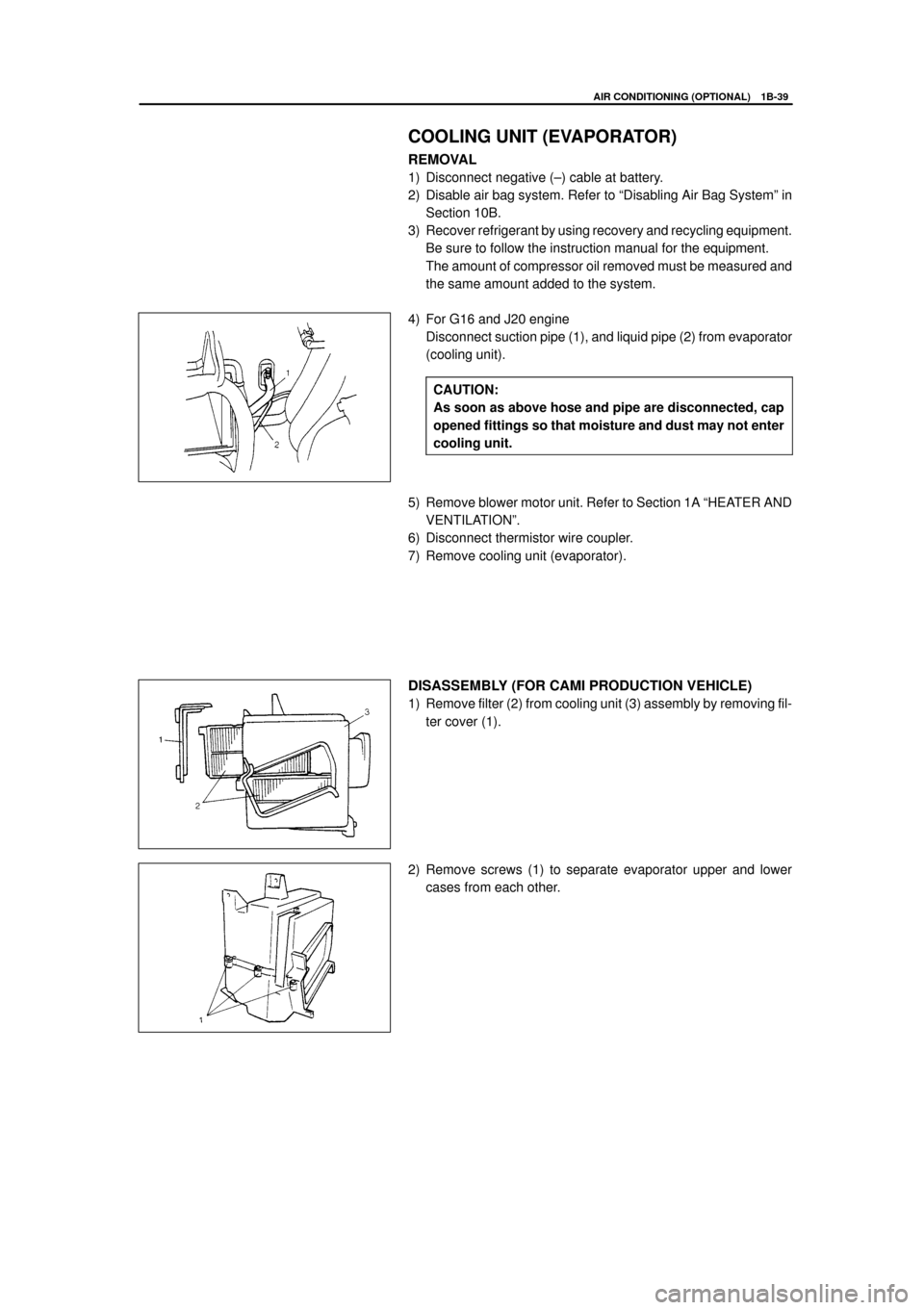
YH4
GRAND
VITARA
AIR CONDITIONING (OPTIONAL) 1B-39
COOLING UNIT (EVAPORATOR)
REMOVAL
1) Disconnect negative (±) cable at battery.
2) Disable air bag system. Refer to ªDisabling Air Bag Systemº in
Section 10B.
3) Recover refrigerant by using recovery and recycling equipment.
Be sure to follow the instruction manual for the equipment.
The amount of compressor oil removed must be measured and
the same amount added to the system.
4) For G16 and J20 engine
Disconnect suction pipe (1), and liquid pipe (2) from evaporator
(cooling unit).
CAUTION:
As soon as above hose and pipe are disconnected, cap
opened fittings so that moisture and dust may not enter
cooling unit.
5) Remove blower motor unit. Refer to Section 1A ªHEATER AND
VENTILATIONº.
6) Disconnect thermistor wire coupler.
7) Remove cooling unit (evaporator).
DISASSEMBLY (FOR CAMI PRODUCTION VEHICLE)
1) Remove filter (2) from cooling unit (3) assembly by removing fil-
ter cover (1).
2) Remove screws (1) to separate evaporator upper and lower
cases from each other.
Page 115 of 801
YH4
GRAND
VITARA
1B-44 AIR CONDITIONING (OPTIONAL)
REFRIGERANT PIPES AND HOSES
INSPECTION
1) Use a leak tester to check hoses and pipes for any gas leakage.
2) Check each hose or pipe clamp for tightness.
Retighten or replace loose clamp as required, if any.
REMOVAL
1) Recover refrigerant by using recovery and recycling equipment.
Be sure to follow the instruction manual for the equipment.
The amount of compressor oil removed must be measured and
the same amount must be added to the system when reinstal-
ling.
2) Replace defective hose or pipe.
CAUTION:
As soon as the above hose or pipe is disconnected, cap
its opened fitting to prevent moisture and dust from en-
tering.
INSTALLATION
1) Reverse removal procedure to install refrigerant line.
2) Evacuate and charge system. Refer to ªEVACUATINGº and
ªCHARGINGº in this section.
INSPECTION OF IDLE SPEED WITH A / C ON
For G16 and J20 engines model, refer to Section 6E1.
For H25 engine model, refer to Section 6E2.