Page 2201 of 4264
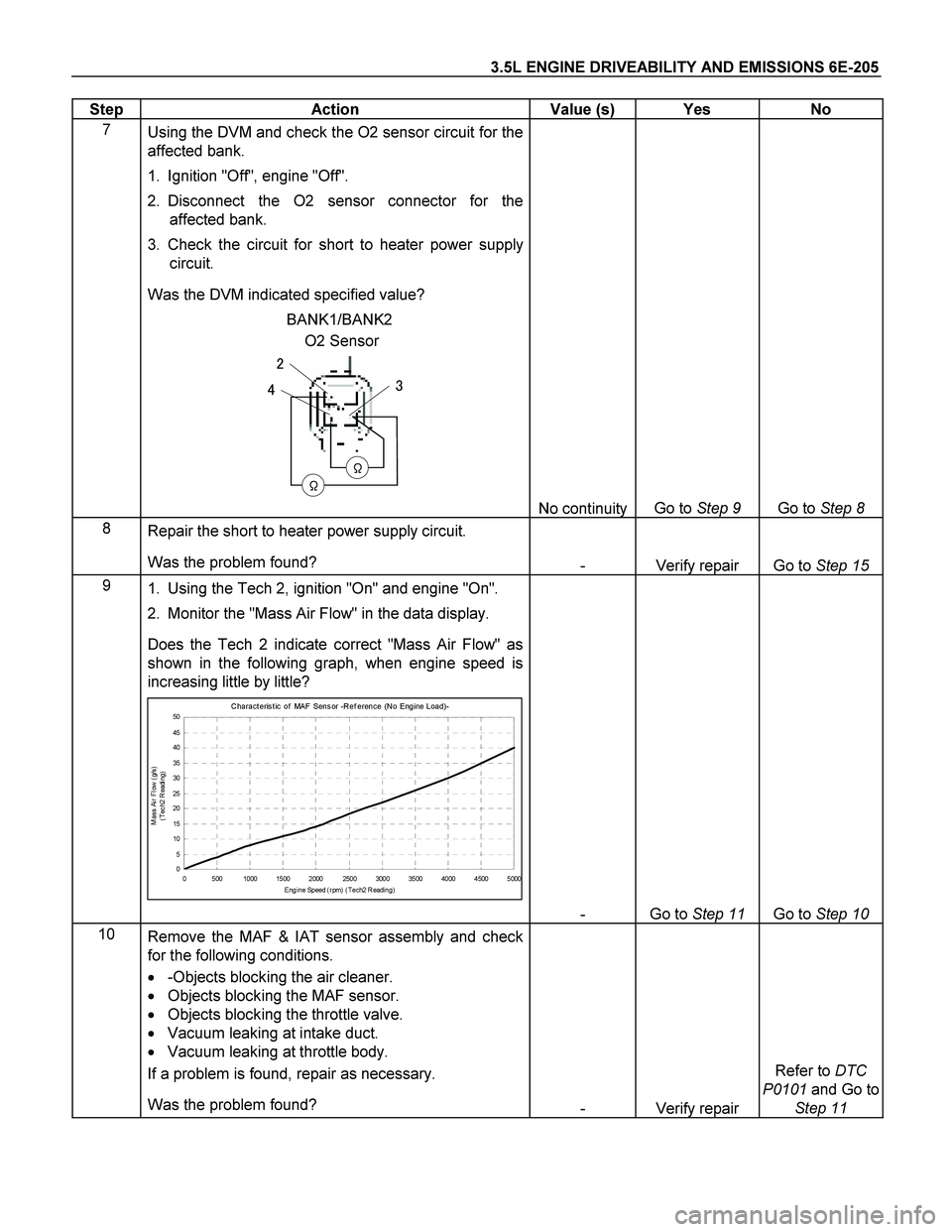
3.5L ENGINE DRIVEABILITY AND EMISSIONS 6E-205
Step Action Value (s) Yes No
7
Using the DVM and check the O2 sensor circuit for the
affected bank.
1. Ignition "Off", engine "Off".
2. Disconnect the O2 sensor connector for the
affected bank.
3. Check the circuit for short to heater power supply
circuit.
Was the DVM indicated specified value?
O2 Sensor BANK1/BANK2
No continuity
Go to Step 9
Go to Step 8
8
Repair the short to heater power supply circuit.
Was the problem found?
- Verify repair Go to Step 15
9
1. Using the Tech 2, ignition "On" and engine "On".
2. Monitor the "Mass Air Flow" in the data display.
Does the Tech 2 indicate correct "Mass Air Flow" as
shown in the following graph, when engine speed is
increasing little by little?
Characteris tic of MAF Sens or -Ref erence (No Engine Load)-
0 5 10 15 20 25 30 35 40 45 50
0 500 1000 1500 2000 2500 3000 3500 4000 4500 5000
Eng i ne Speed ( r pm) ( T ech2 R eadi ng )
Mass Air Flow (g/s)
( T ec h2 R eadi ng)
- Go to Step 11 Go to Step 10
10
Remove the MAF & IAT sensor assembly and check
for the following conditions.
-Objects blocking the air cleaner.
Objects blocking the MAF sensor.
Objects blocking the throttle valve.
Vacuum leaking at intake duct.
Vacuum leaking at throttle body.
If a problem is found, repair as necessary.
Was the problem found?
- Verify repair Refer to DTC
P0101 and Go to
Step 11
Page 2204 of 4264
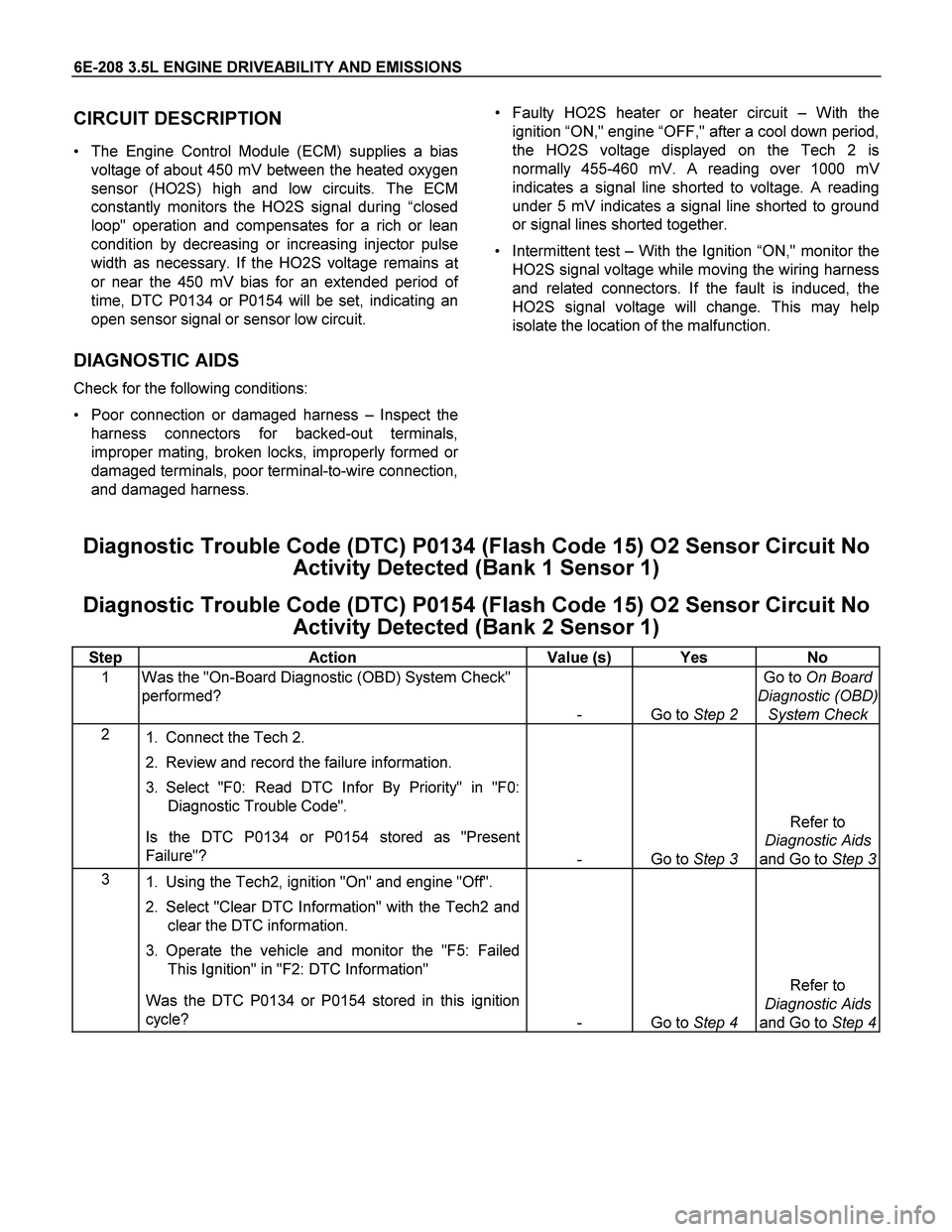
6E-208 3.5L ENGINE DRIVEABILITY AND EMISSIONS
CIRCUIT DESCRIPTION
The Engine Control Module (ECM) supplies a bias
voltage of about 450 mV between the heated oxygen
sensor (HO2S) high and low circuits. The ECM
constantly monitors the HO2S signal during “closed
loop" operation and compensates for a rich or lean
condition by decreasing or increasing injector pulse
width as necessary. If the HO2S voltage remains a
t
or near the 450 mV bias for an extended period of
time, DTC P0134 or P0154 will be set, indicating an
open sensor signal or sensor low circuit.
DIAGNOSTIC AIDS
Check for the following conditions:
Poor connection or damaged harness – Inspect the
harness connectors for backed-out terminals,
improper mating, broken locks, improperly formed o
r
damaged terminals, poor terminal-to-wire connection,
and damaged harness.
Faulty HO2S heater or heater circuit –With the
ignition “ON," engine “OFF," after a cool down period,
the HO2S voltage displayed on the Tech 2 is
normally 455-460 mV. A reading over 1000 m
V
indicates a signal line shorted to voltage. A reading
under 5 mV indicates a signal line shorted to ground
or signal lines shorted together.
Intermittent test –With the Ignition “ON," monitor the
HO2S signal voltage while moving the wiring harness
and related connectors. If the fault is induced, the
HO2S signal voltage will change. This may help
isolate the location of the malfunction.
Diagnostic Trouble Code (DTC) P0134 (Flash Code 15) O2 Sensor Circuit No
Activity Detected (Bank 1 Sensor 1)
Diagnostic Trouble Code (DTC) P0154 (Flash Code 15) O2 Sensor Circuit No
Activity Detected (Bank 2 Sensor 1)
Step Action Value (s) Yes No
1 Was the "On-Board Diagnostic (OBD) System Check"
performed?
- Go to Step 2 Go to On Board
Diagnostic (OBD)
System Check
2
1. Connect the Tech 2.
2. Review and record the failure information.
3. Select "F0: Read DTC Infor By Priority" in "F0:
Diagnostic Trouble Code".
Is the DTC P0134 or P0154 stored as "Present
Failure"?
- Go to Step 3 Refer to
Diagnostic Aids
and Go to Step 3
3
1. Using the Tech2, ignition "On" and engine "Off".
2. Select "Clear DTC Information" with the Tech2 and
clear the DTC information.
3. Operate the vehicle and monitor the "F5: Failed
This Ignition" in "F2: DTC Information"
Was the DTC P0134 or P0154 stored in this ignition
cycle?
- Go to Step 4 Refer to
Diagnostic Aids
and Go to Step 4
Page 2205 of 4264
3.5L ENGINE DRIVEABILITY AND EMISSIONS 6E-209
Step Action Value (s) Yes No
4
Check for poor/faulty connection at the O2 sensor or
ECM connector. If a poor/faulty connection is found,
repair as necessary.
Was the problem found?
E-77/E-78
E-61(B)
- Verify repair Go to Step 5
5
Using the DVM and check the O2 sensor circuit for the
affected bank.
1. Ignition "On", engine "Off".
2. Disconnect the O2 sensor connector for the
affected bank.
3. Check the circuit for open, short to heater ground
or ground circuit.
Was the DVM indicated specified value?
E-77/E-78 BANK1/BANK2
V
Approximatly
450mV
Go to Step 6
Go to Step 12
6
Using the DVM and check the O2 sensor heater
power supply circuit for the affected bank.
1. Ignition "On", engine "Off".
2. Disconnect the O2 sensor connector for the
affected cylinder.
3. Check the circuit for open circuit.
Was the DVM indicated specified value?
E-77/E-78 BANK1/BANK2
V
10-14.5 V
Go to Step 9
Go to Step 7
Page 2206 of 4264
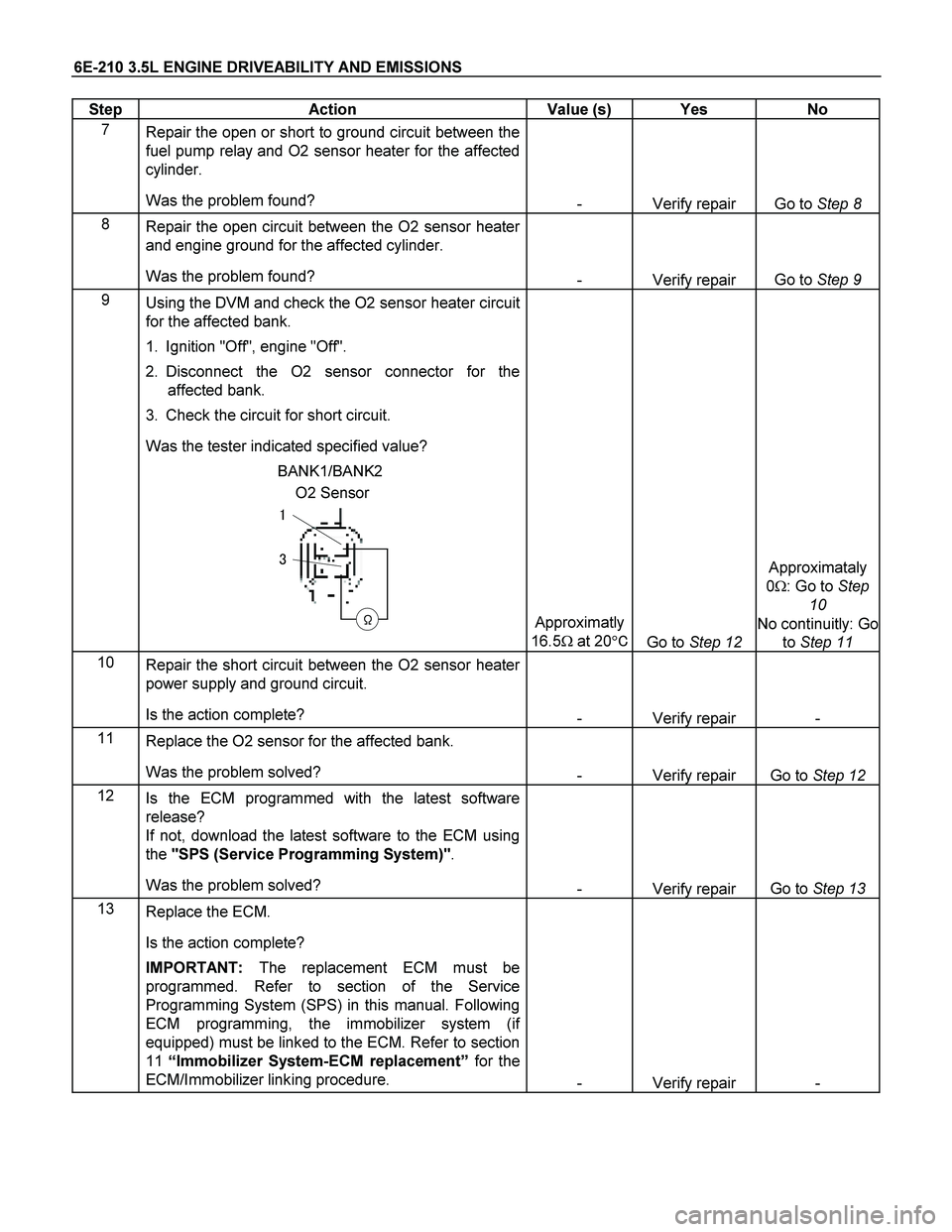
6E-210 3.5L ENGINE DRIVEABILITY AND EMISSIONS
Step Action Value (s) Yes No
7
Repair the open or short to ground circuit between the
fuel pump relay and O2 sensor heater for the affected
cylinder.
Was the problem found?
- Verify repair Go to Step 8
8
Repair the open circuit between the O2 sensor heater
and engine ground for the affected cylinder.
Was the problem found?
- Verify repair Go to Step 9
9
Using the DVM and check the O2 sensor heater circuit
for the affected bank.
1. Ignition "Off", engine "Off".
2. Disconnect the O2 sensor connector for the
affected bank.
3. Check the circuit for short circuit.
Was the tester indicated specified value?
O2 Sensor BANK1/BANK2
Approximatly
16.5 at 20
Go to Step 12
Approximataly
0: Go to Step
10
No continuitly: Go
to Step 11
10
Repair the short circuit between the O2 sensor heater
power supply and ground circuit.
Is the action complete?
- Verify repair -
11
Replace the O2 sensor for the affected bank.
Was the problem solved?
- Verify repair Go to Step 12
12
Is the ECM programmed with the latest software
release?
If not, download the latest software to the ECM using
the "SPS (Service Programming System)".
Was the problem solved?
- Verify repair Go to Step 13
13
Replace the ECM.
Is the action complete?
IMPORTANT: The replacement ECM must be
programmed. Refer to section of the Service
Programming System (SPS) in this manual. Following
ECM programming, the immobilizer system (if
equipped) must be linked to the ECM. Refer to section
11 “Immobilizer System-ECM replacement” for the
ECM/Immobilizer linking procedure.
- Verify repair -
Page 2483 of 4264
ENGINE MECHANICAL (C24SE) 6A-63
OPERATIONS ON COOLING SYSTEM
Caution!
Before working with the cooling system, be sure to confirm that
the temperature of the engine is cooled down.
Failure to observe this may cause burn.
Cooling System, Check for Leaks
Installation
1. Install commercially available coolant checking
instrument onto compensation tank (Refer to section 6B;
Engine cooling).
2. Check coolant level.
Inspection
Use 5-8840-0277-0 tester & 5-8840-2603-0 adaptor.
Cooling System, Fill Up and Bleed
Important!
Radiator and heater core are made from alminium.
To avoid corrosion, use only anti-freeze with corrosion
protection.
Replace Coolant
1. Confirm the engine is cold enough.
2. Open the radiator cap, pour coolant to the filler neck level
and close the cap.
3. Pour coolant into the reservoir until MAX line is reached.
4. Start the engine, run 2
3 minutes at idling speed and
switch off the engine.
5. Refill coolant if the coolant level is lowered.
Page 2484 of 4264
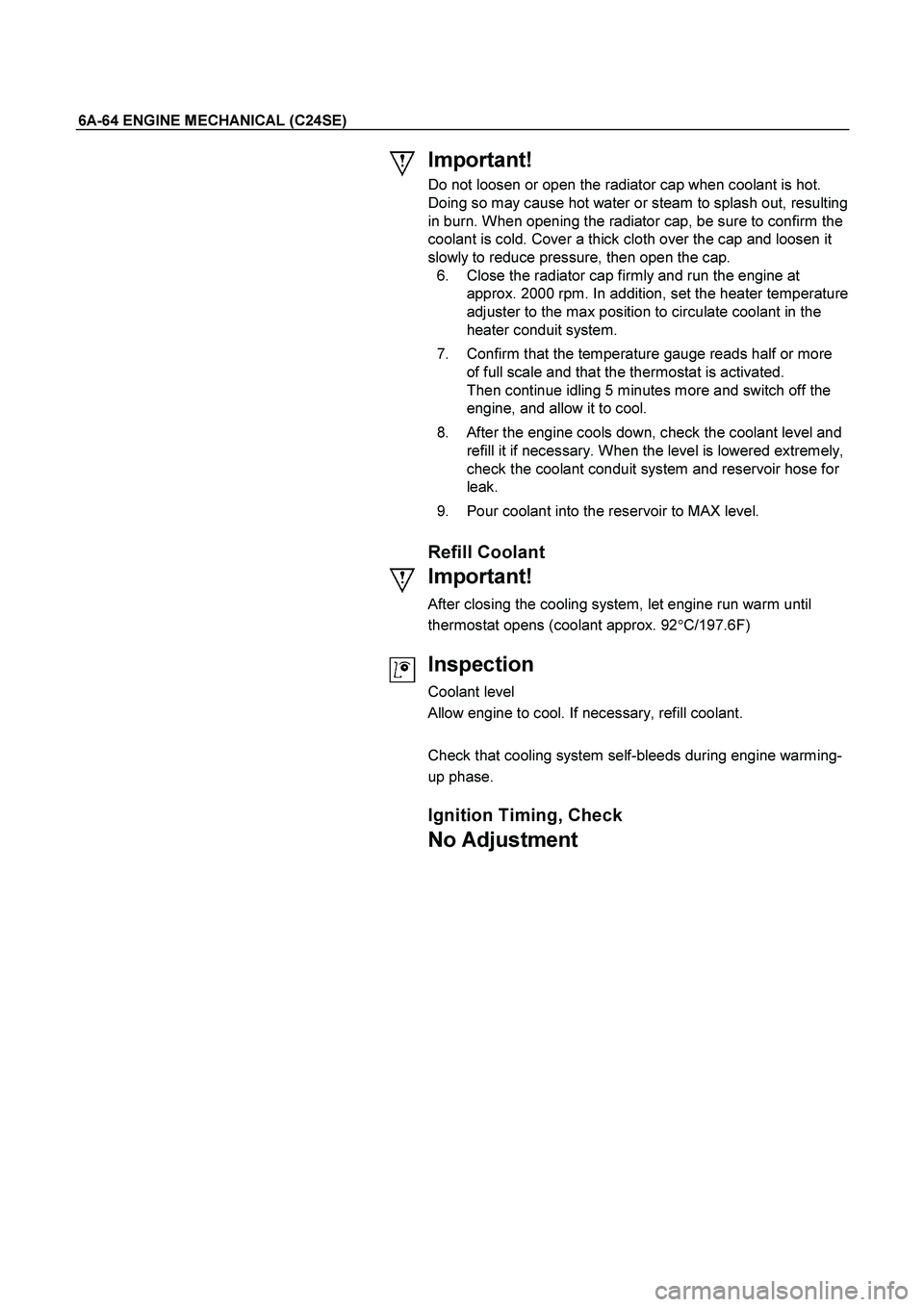
6A-64 ENGINE MECHANICAL (C24SE)
Important!
Do not loosen or open the radiator cap when coolant is hot.
Doing so may cause hot water or steam to splash out, resulting
in burn. When opening the radiator cap, be sure to confirm the
coolant is cold. Cover a thick cloth over the cap and loosen it
slowly to reduce pressure, then open the cap.
6. Close the radiator cap firmly and run the engine at
approx. 2000 rpm. In addition, set the heater temperature
adjuster to the max position to circulate coolant in the
heater conduit system.
7. Confirm that the temperature gauge reads half or more
of full scale and that the thermostat is activated.
Then continue idling 5 minutes more and switch off the
engine, and allow it to cool.
8. After the engine cools down, check the coolant level and
refill it if necessary. When the level is lowered extremely,
check the coolant conduit system and reservoir hose for
leak.
9. Pour coolant into the reservoir to MAX level.
Refill Coolant
Important!
After closing the cooling system, let engine run warm until
thermostat opens (coolant approx. 92C/197.6F)
Inspection
Coolant level
Allow engine to cool. If necessary, refill coolant.
Check that cooling system self-bleeds during engine warming-
up phase.
Ignition Timing, Check
No Adjustment
Page 2512 of 4264
6B-2 ENGINE COOLING
General Description
Legend
1 Water Pump
2 Thermostat
3 Radiator
4 Reserve Tank5 Coolant Distributor
6 Cylinder Block and Head
7 Throttle Body
8 Heater
The Cooling System is a pressurized type, where the water
pump, which is cambelt driven, forces the circulation of
the coolant through the cylinder block and head. The
thermostat regulates the flow of coolant between the
radiator and the bypass circuit. The heater is part of the
bypass circuit. The throttle body pre-heat is a separate
circuit which is not regulated by the thermostat. An oil
cooler may be fitted as part of this circuit.
Page 2523 of 4264
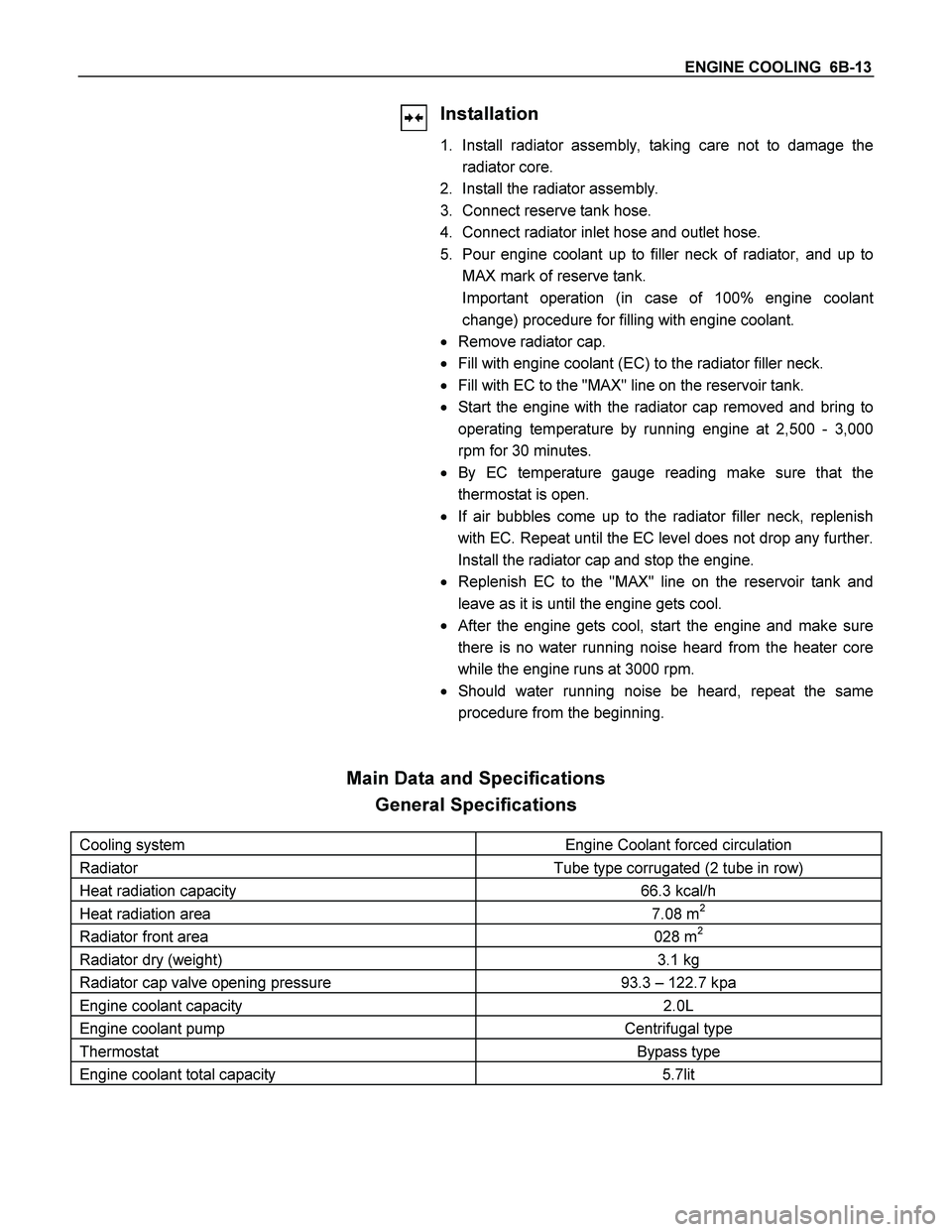
ENGINE COOLING 6B-13
Installation
1. Install radiator assembly, taking care not to damage the
radiator core.
2. Install the radiator assembly.
3. Connect reserve tank hose.
4. Connect radiator inlet hose and outlet hose.
5. Pour engine coolant up to filler neck of radiator, and up to
MAX mark of reserve tank.
Important operation (in case of 100% engine coolan
t
change) procedure for filling with engine coolant.
Remove radiator cap.
Fill with engine coolant (EC) to the radiator filler neck.
Fill with EC to the "MAX" line on the reservoir tank.
Start the engine with the radiator cap removed and bring to
operating temperature by running engine at 2,500 - 3,000
rpm for 30 minutes.
By EC temperature gauge reading make sure that the
thermostat is open.
If air bubbles come up to the radiator filler neck, replenish
with EC. Repeat until the EC level does not drop any further.
Install the radiator cap and stop the engine.
Replenish EC to the "MAX" line on the reservoir tank and
leave as it is until the engine gets cool.
After the engine gets cool, start the engine and make sure
there is no water running noise heard from the heater core
while the engine runs at 3000 rpm.
Should water running noise be heard, repeat the same
procedure from the beginning.
Main Data and Specifications
General Specifications
Cooling system Engine Coolant forced circulation
Radiator Tube type corrugated (2 tube in row)
Heat radiation capacity 66.3 kcal/h
Heat radiation area 7.08 m2
Radiator front area 028 m2
Radiator dry (weight) 3.1 kg
Radiator cap valve opening pressure 93.3 – 122.7 kpa
Engine coolant capacity 2.0L
Engine coolant pump Centrifugal type
Thermostat Bypass type
Engine coolant total capacity 5.7lit