Page 522 of 1184
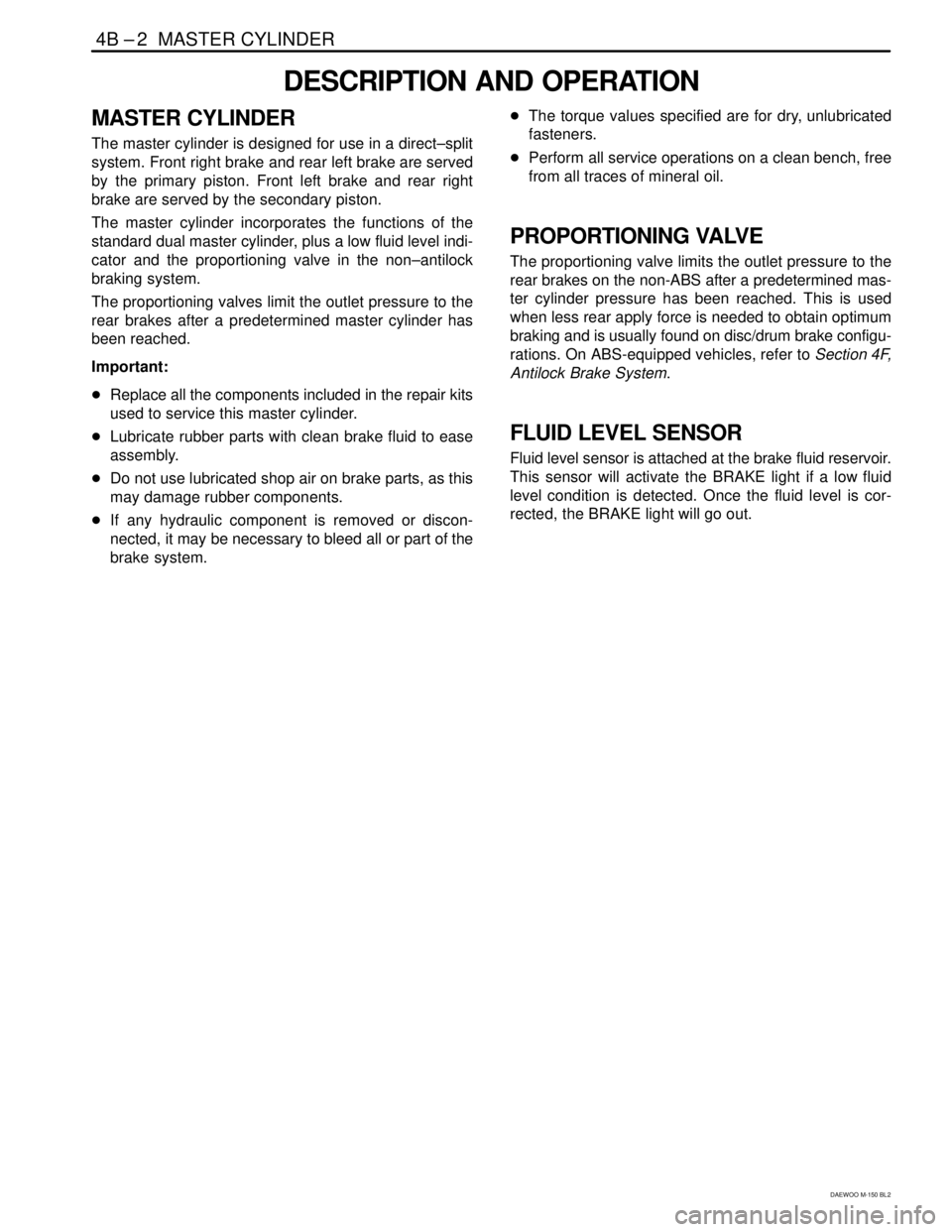
4B –2 MASTER CYLINDER
DAEWOO M-150 BL2
DESCRIPTION AND OPERATION
MASTER CYLINDER
The master cylinder is designed for use in a direct–split
system. Front right brake and rear left brake are served
by the primary piston. Front left brake and rear right
brake are served by the secondary piston.
The master cylinder incorporates the functions of the
standard dual master cylinder, plus a low fluid level indi-
cator and the proportioning valve in the non–antilock
braking system.
The proportioning valves limit the outlet pressure to the
rear brakes after a predetermined master cylinder has
been reached.
Important:
Replace all the components included in the repair kits
used to service this master cylinder.
Lubricate rubber parts with clean brake fluid to ease
assembly.
Do not use lubricated shop air on brake parts, as this
may damage rubber components.
If any hydraulic component is removed or discon-
nected, it may be necessary to bleed all or part of the
brake system.The torque values specified are for dry, unlubricated
fasteners.
Perform all service operations on a clean bench, free
from all traces of mineral oil.
PROPORTIONING VALVE
The proportioning valve limits the outlet pressure to the
rear brakes on the non-ABS after a predetermined mas-
ter cylinder pressure has been reached. This is used
when less rear apply force is needed to obtain optimum
braking and is usually found on disc/drum brake configu-
rations. On ABS-equipped vehicles, refer to Section 4F,
Antilock Brake System.
FLUID LEVEL SENSOR
Fluid level sensor is attached at the brake fluid reservoir.
This sensor will activate the BRAKE light if a low fluid
level condition is detected. Once the fluid level is cor-
rected, the BRAKE light will go out.
Page 789 of 1184
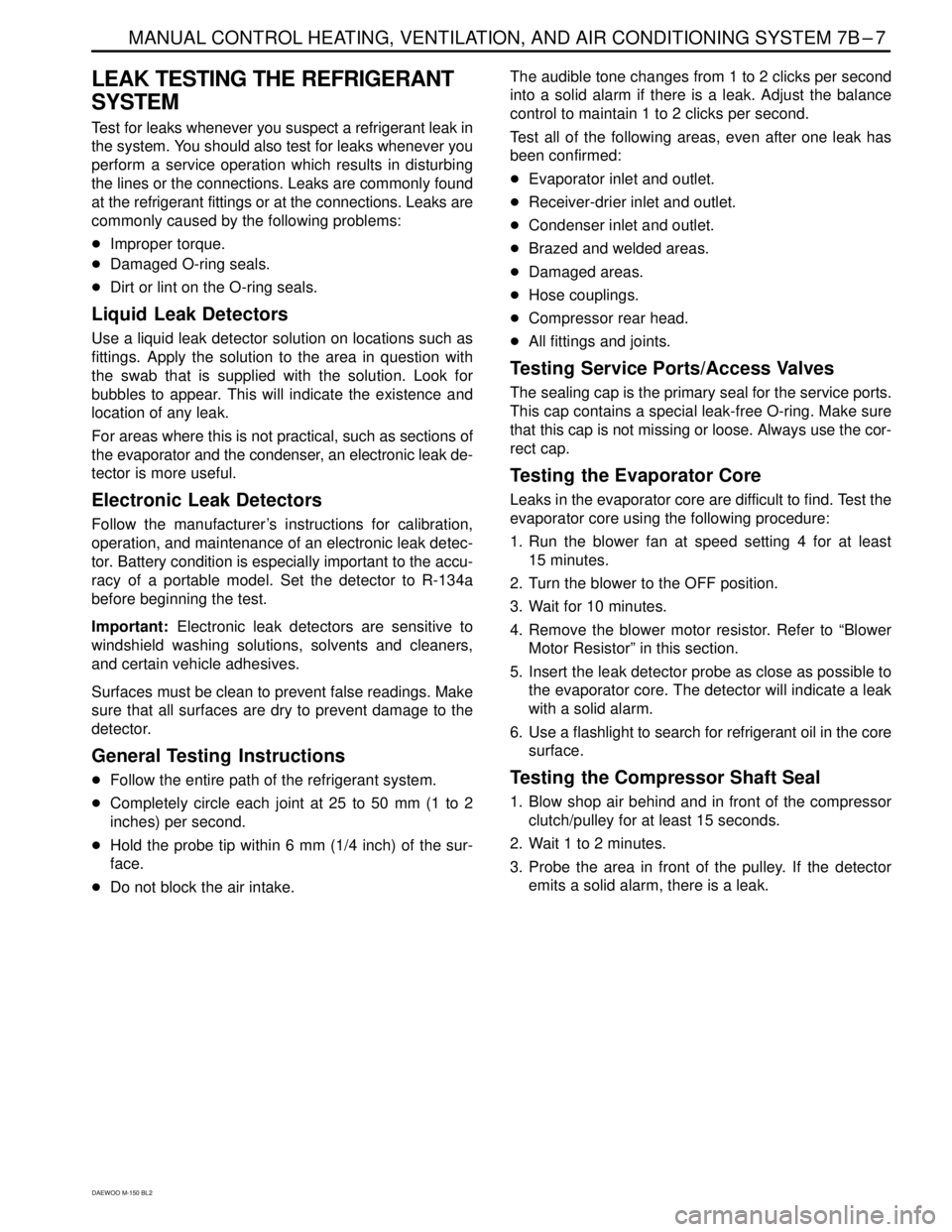
MANUAL CONTROL HEATING, VENTILATION, AND AIR CONDITIONING SYSTEM 7B–7
DAEWOO M-150 BL2
LEAK TESTING THE REFRIGERANT
SYSTEM
Test for leaks whenever you suspect a refrigerant leak in
the system. You should also test for leaks whenever you
perform a service operation which results in disturbing
the lines or the connections. Leaks are commonly found
at the refrigerant fittings or at the connections. Leaks are
commonly caused by the following problems:
Improper torque.
Damaged O-ring seals.
Dirt or lint on the O-ring seals.
Liquid Leak Detectors
Use a liquid leak detector solution on locations such as
fittings. Apply the solution to the area in question with
the swab that is supplied with the solution. Look for
bubbles to appear. This will indicate the existence and
location of any leak.
For areas where this is not practical, such as sections of
the evaporator and the condenser, an electronic leak de-
tector is more useful.
Electronic Leak Detectors
Follow the manufacturer’s instructions for calibration,
operation, and maintenance of an electronic leak detec-
tor. Battery condition is especially important to the accu-
racy of a portable model. Set the detector to R-134a
before beginning the test.
Important: Electronic leak detectors are sensitive to
windshield washing solutions, solvents and cleaners,
and certain vehicle adhesives.
Surfaces must be clean to prevent false readings. Make
sure that all surfaces are dry to prevent damage to the
detector.
General Testing Instructions
Follow the entire path of the refrigerant system.
Completely circle each joint at 25 to 50 mm (1 to 2
inches) per second.
Hold the probe tip within 6 mm (1/4 inch) of the sur-
face.
Do not block the air intake.The audible tone changes from 1 to 2 clicks per second
into a solid alarm if there is a leak. Adjust the balance
control to maintain 1 to 2 clicks per second.
Test all of the following areas, even after one leak has
been confirmed:
Evaporator inlet and outlet.
Receiver-drier inlet and outlet.
Condenser inlet and outlet.
Brazed and welded areas.
Damaged areas.
Hose couplings.
Compressor rear head.
All fittings and joints.
Testing Service Ports/Access Valves
The sealing cap is the primary seal for the service ports.
This cap contains a special leak-free O-ring. Make sure
that this cap is not missing or loose. Always use the cor-
rect cap.
Testing the Evaporator Core
Leaks in the evaporator core are difficult to find. Test the
evaporator core using the following procedure:
1. Run the blower fan at speed setting 4 for at least
15 minutes.
2. Turn the blower to the OFF position.
3. Wait for 10 minutes.
4. Remove the blower motor resistor. Refer to “Blower
Motor Resistor” in this section.
5. Insert the leak detector probe as close as possible to
the evaporator core. The detector will indicate a leak
with a solid alarm.
6. Use a flashlight to search for refrigerant oil in the core
surface.
Testing the Compressor Shaft Seal
1. Blow shop air behind and in front of the compressor
clutch/pulley for at least 15 seconds.
2. Wait 1 to 2 minutes.
3. Probe the area in front of the pulley. If the detector
emits a solid alarm, there is a leak.
Page 1051 of 1184
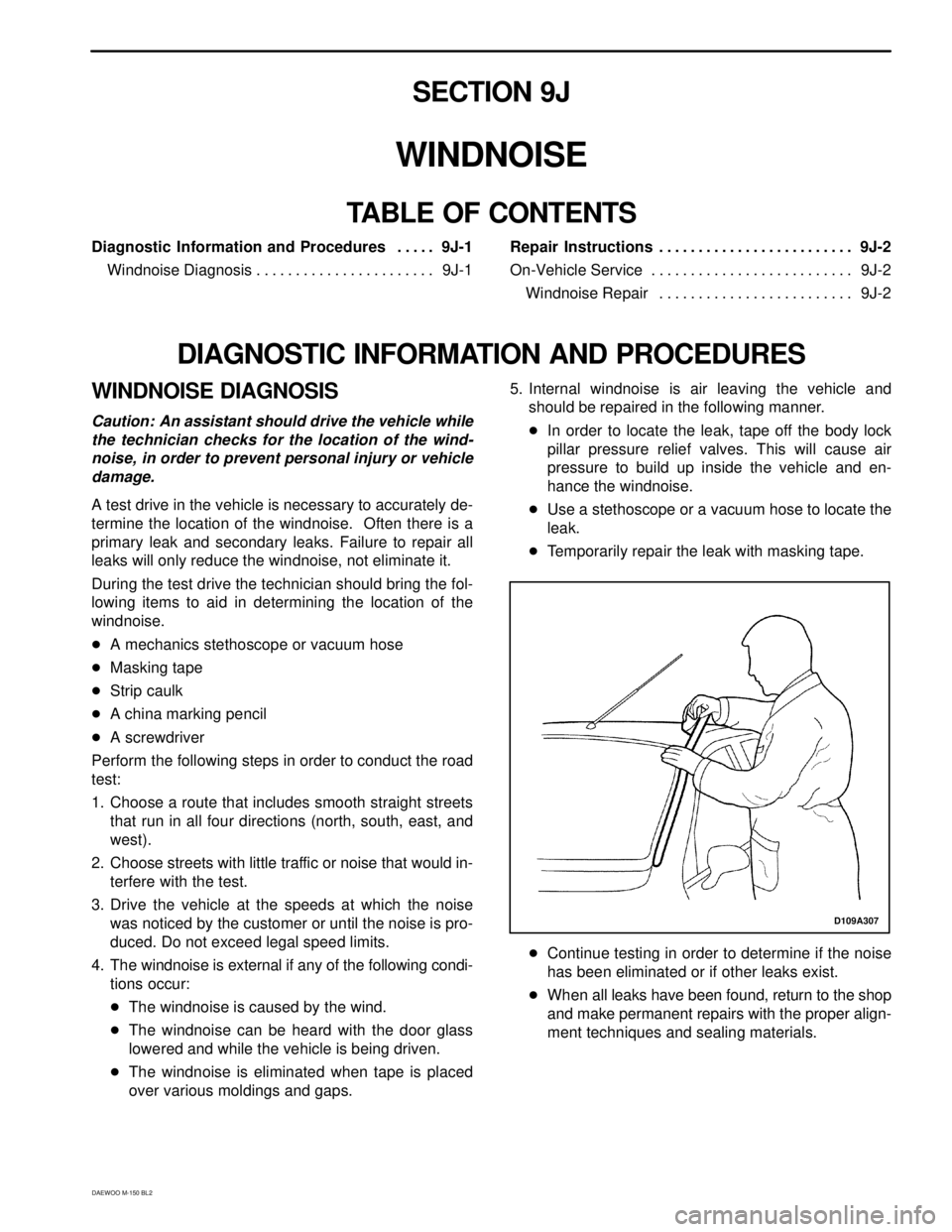
DAEWOO M-150 BL2
SECTION 9J
WINDNOISE
TABLE OF CONTENTS
Diagnostic Information and Procedures 9J-1. . . . .
Windnoise Diagnosis 9J-1. . . . . . . . . . . . . . . . . . . . . . . Repair Instructions 9J-2. . . . . . . . . . . . . . . . . . . . . . . . .
On-Vehicle Service 9J-2. . . . . . . . . . . . . . . . . . . . . . . . . .
Windnoise Repair 9J-2. . . . . . . . . . . . . . . . . . . . . . . . .
DIAGNOSTIC INFORMATION AND PROCEDURES
WINDNOISE DIAGNOSIS
Caution: An assistant should drive the vehicle while
the technician checks for the location of the wind-
noise, in order to prevent personal injury or vehicle
damage.
A test drive in the vehicle is necessary to accurately de-
termine the location of the windnoise. Often there is a
primary leak and secondary leaks. Failure to repair all
leaks will only reduce the windnoise, not eliminate it.
During the test drive the technician should bring the fol-
lowing items to aid in determining the location of the
windnoise.
A mechanics stethoscope or vacuum hose
Masking tape
Strip caulk
A china marking pencil
A screwdriver
Perform the following steps in order to conduct the road
test:
1. Choose a route that includes smooth straight streets
that run in all four directions (north, south, east, and
west).
2. Choose streets with little traffic or noise that would in-
terfere with the test.
3. Drive the vehicle at the speeds at which the noise
was noticed by the customer or until the noise is pro-
duced. Do not exceed legal speed limits.
4. The windnoise is external if any of the following condi-
tions occur:
The windnoise is caused by the wind.
The windnoise can be heard with the door glass
lowered and while the vehicle is being driven.
The windnoise is eliminated when tape is placed
over various moldings and gaps.5. Internal windnoise is air leaving the vehicle and
should be repaired in the following manner.
In order to locate the leak, tape off the body lock
pillar pressure relief valves. This will cause air
pressure to build up inside the vehicle and en-
hance the windnoise.
Use a stethoscope or a vacuum hose to locate the
leak.
Temporarily repair the leak with masking tape.
D109A307
Continue testing in order to determine if the noise
has been eliminated or if other leaks exist.
When all leaks have been found, return to the shop
and make permanent repairs with the proper align-
ment techniques and sealing materials.