Page 335 of 1672
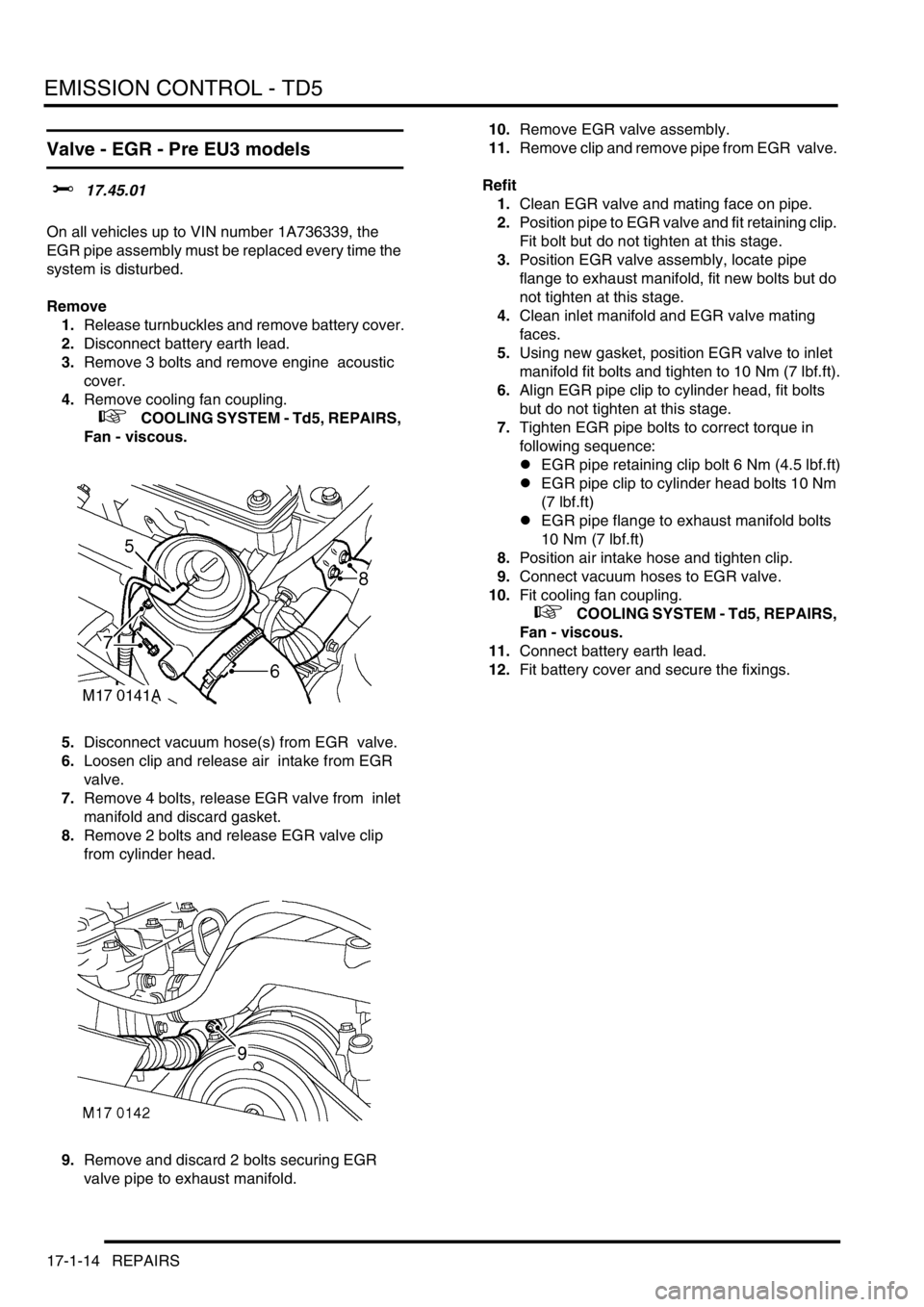
EMISSION CONTROL - TD5
17-1-14 REPAIRS
Valve - EGR - Pre EU3 models
$% 17.45.01
On all vehicles up to VIN number 1A736339, the
EGR pipe assembly must be replaced every time the
system is disturbed.
Remove
1.Release turnbuckles and remove battery cover.
2.Disconnect battery earth lead.
3.Remove 3 bolts and remove engine acoustic
cover.
4.Remove cooling fan coupling.
+ COOLING SYSTEM - Td5, REPAIRS,
Fan - viscous.
5.Disconnect vacuum hose(s) from EGR valve.
6.Loosen clip and release air intake from EGR
valve.
7.Remove 4 bolts, release EGR valve from inlet
manifold and discard gasket.
8.Remove 2 bolts and release EGR valve clip
from cylinder head.
9.Remove and discard 2 bolts securing EGR
valve pipe to exhaust manifold. 10.Remove EGR valve assembly.
11.Remove clip and remove pipe from EGR valve.
Refit
1.Clean EGR valve and mating face on pipe.
2.Position pipe to EGR valve and fit retaining clip.
Fit bolt but do not tighten at this stage.
3.Position EGR valve assembly, locate pipe
flange to exhaust manifold, fit new bolts but do
not tighten at this stage.
4.Clean inlet manifold and EGR valve mating
faces.
5.Using new gasket, position EGR valve to inlet
manifold fit bolts and tighten to 10 Nm (7 lbf.ft).
6.Align EGR pipe clip to cylinder head, fit bolts
but do not tighten at this stage.
7.Tighten EGR pipe bolts to correct torque in
following sequence:
lEGR pipe retaining clip bolt 6 Nm (4.5 lbf.ft)
lEGR pipe clip to cylinder head bolts 10 Nm
(7 lbf.ft)
lEGR pipe flange to exhaust manifold bolts
10 Nm (7 lbf.ft)
8.Position air intake hose and tighten clip.
9.Connect vacuum hoses to EGR valve.
10.Fit cooling fan coupling.
+ COOLING SYSTEM - Td5, REPAIRS,
Fan - viscous.
11.Connect battery earth lead.
12.Fit battery cover and secure the fixings.
Page 336 of 1672
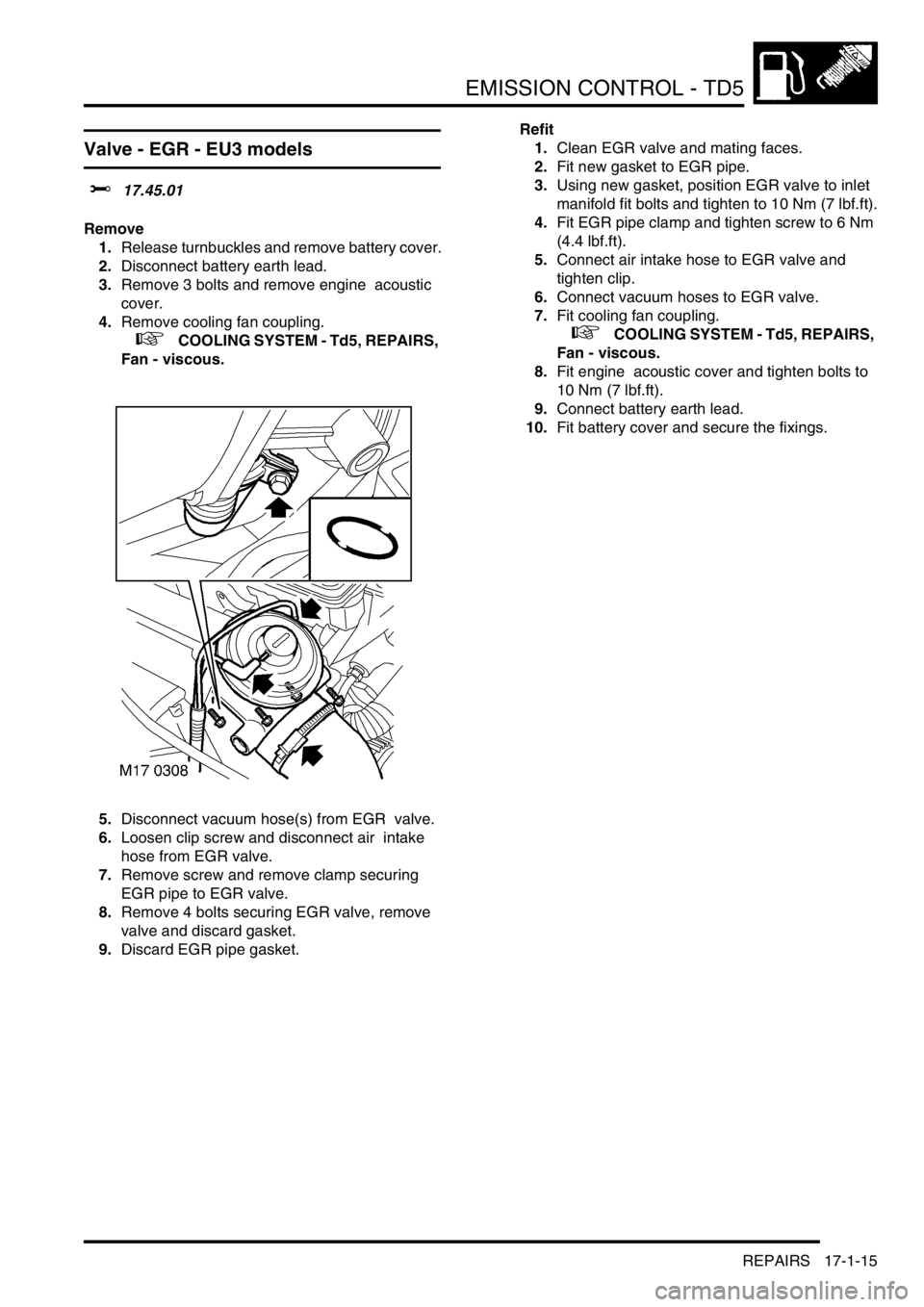
EMISSION CONTROL - TD5
REPAIRS 17-1-15
Valve - EGR - EU3 models
$% 17.45.01
Remove
1.Release turnbuckles and remove battery cover.
2.Disconnect battery earth lead.
3.Remove 3 bolts and remove engine acoustic
cover.
4.Remove cooling fan coupling.
+ COOLING SYSTEM - Td5, REPAIRS,
Fan - viscous.
5.Disconnect vacuum hose(s) from EGR valve.
6.Loosen clip screw and disconnect air intake
hose from EGR valve.
7.Remove screw and remove clamp securing
EGR pipe to EGR valve.
8.Remove 4 bolts securing EGR valve, remove
valve and discard gasket.
9.Discard EGR pipe gasket.Refit
1.Clean EGR valve and mating faces.
2.Fit new gasket to EGR pipe.
3.Using new gasket, position EGR valve to inlet
manifold fit bolts and tighten to 10 Nm (7 lbf.ft).
4.Fit EGR pipe clamp and tighten screw to 6 Nm
(4.4 lbf.ft).
5.Connect air intake hose to EGR valve and
tighten clip.
6.Connect vacuum hoses to EGR valve.
7.Fit cooling fan coupling.
+ COOLING SYSTEM - Td5, REPAIRS,
Fan - viscous.
8.Fit engine acoustic cover and tighten bolts to
10 Nm (7 lbf.ft).
9.Connect battery earth lead.
10.Fit battery cover and secure the fixings.
Page 340 of 1672
EMISSION CONTROL - V8
DESCRIPTION AND OPERATION 17-2-3
Evaporative emission system
component layout
1Purge valve
2Service port
3Snorkel tube (UK / ROW only)
4CVS unit (NAS vehicles with vacuum type leak
detection only)
5EVAP canister breather tube
6Vent pipe – fuel tank to EVAP canister
7Relief valve regulated flow
8Relief valve (UK / ROW only)
9Relief valve free flow
10Fuel filler cap
11Liquid vapour separator (UK / ROW type
shown)12Fuel filler hose (UK / ROW type shown)
13Tank breather hose (UK / ROW only)
14Vent hose
15Roll over valves (ROV's) – (4 off, UK / ROW
spec. shown)
16Fuel tank and breather assembly
17EVAP canister
18Purge line connection to engine manifold
19Tank EVAP system pressure sensor (NAS
vehicles with vacuum type leak detection only)
M17 0209
4
3
1
6
5
16
10
8
13
17
9
7
11
12
15
14
18
2
19
Page 341 of 1672
EMISSION CONTROL - V8
17-2-4 DESCRIPTION AND OPERATION
Evaporative emission system (with
positive pressure leak detection)
component layout (NAS only)
1Purge valve
2Service port
3Air filter canister
4EVAP canister breather tube
5Leak detection pump
6EVAP canister
7Vent pipe – fuel tank to EVAP canister
8Liquid vapour separator (metal)9Fuel filler cap
10Fuel filler
11Fuel tank breather assembly
12Vent hose
13Roll over valves (inside fuel tank)
14Fuel tank
15Purge line connection to engine manifold
M17 0208
3
1
7
4
14
11
6
8
10
13
12
15
2
5
9
Page 342 of 1672
EMISSION CONTROL - V8
DESCRIPTION AND OPERATION 17-2-5
Evaporative emission system control
diagram
1Battery
2Fuse 13 (engine compartment fusebox)
3Inertia switch
4Main relay (engine compartment fusebox)
5Engine Control Module (ECM)
6Purge Valve (black harness connector)
7Canister vent solenoid (CVS) valve – NAS
vehicles with vacuum type EVAP system leak
detection capability only8Leak detection pump – NAS vehicles with
positive pressure type EVAP system leak
detection capability only
9Fuel tank pressure sensor – NAS vehicles with
vacuum type EVAP system leak detection
capability only
10Instrument pack (MIL warning light)
M17 0210
12
3
4
5
6
7
9
8
10
Page 344 of 1672
EMISSION CONTROL - V8
DESCRIPTION AND OPERATION 17-2-7
1Engine Control Module (ECM)
2SAI vacuum solenoid valve
3Purge valve
4Vacuum reservoir
5SAI control valve (2 off)
6SAI pump
7SAI pump relay
8Main relay
Page 345 of 1672
EMISSION CONTROL - V8
17-2-8 DESCRIPTION AND OPERATION
Secondary air injection system control
diagram
1Fuselink 2 (engine compartment fusebox)
2SAI pump relay
3SAI pump
4SAI vacuum solenoid valve (grey harness
connector)
5Engine Control Module (ECM)6Battery
7Fuse 13 (engine compartment fusebox)
8Inertia switch
9Main relay
9
M17 0207
1
2
3
4
5
7
6
8
Page 346 of 1672
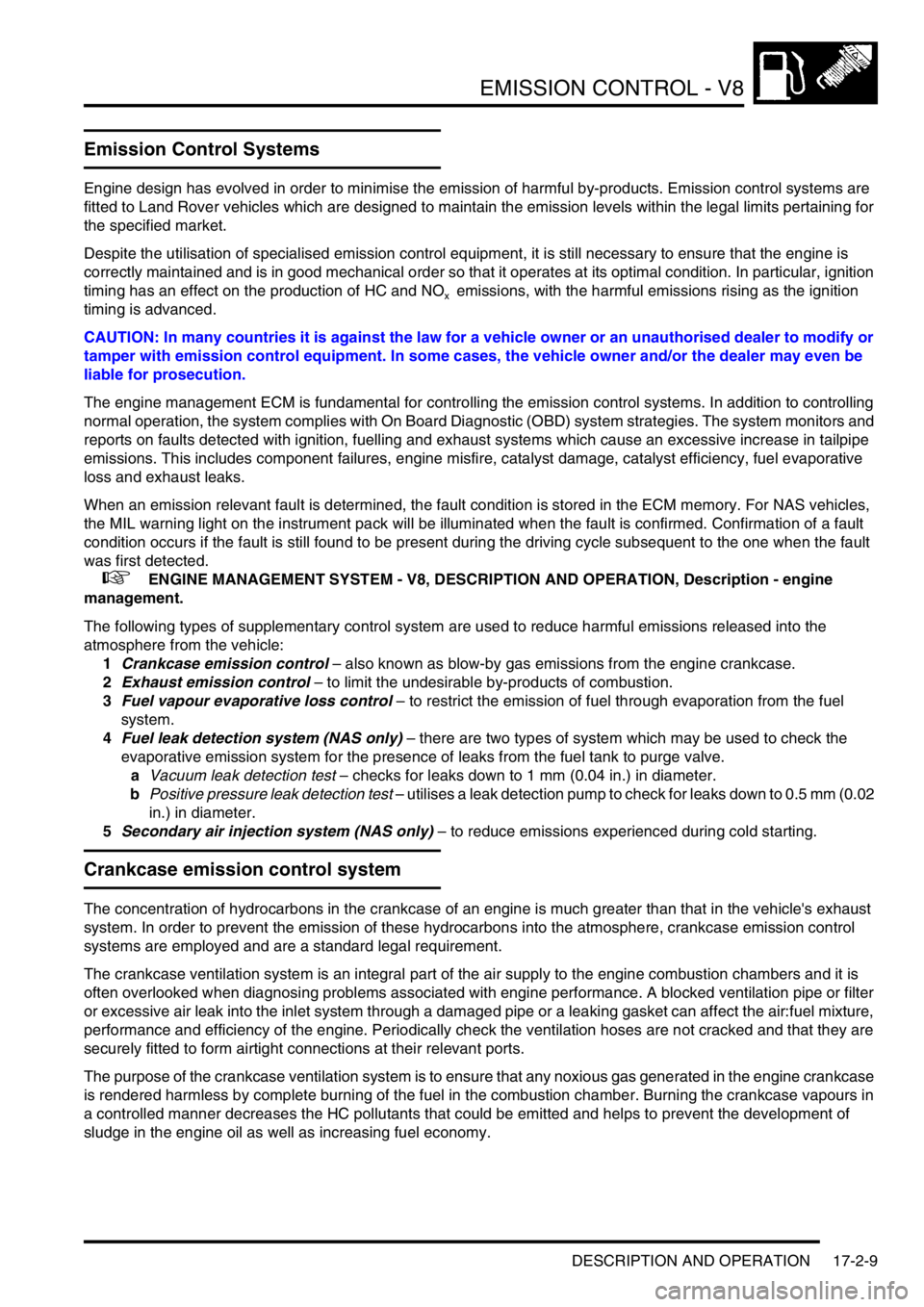
EMISSION CONTROL - V8
DESCRIPTION AND OPERATION 17-2-9
Emission Control Systems
Engine design has evolved in order to minimise the emission of harmful by-products. Emission control systems are
fitted to Land Rover vehicles which are designed to maintain the emission levels within the legal limits pertaining for
the specified market.
Despite the utilisation of specialised emission control equipment, it is still necessary to ensure that the engine is
correctly maintained and is in good mechanical order so that it operates at its optimal condition. In particular, ignition
timing has an effect on the production of HC and NO
x emissions, with the harmful emissions rising as the ignition
timing is advanced.
CAUTION: In many countries it is against the law for a vehicle owner or an unauthorised dealer to modify or
tamper with emission control equipment. In some cases, the vehicle owner and/or the dealer may even be
liable for prosecution.
The engine management ECM is fundamental for controlling the emission control systems. In addition to controlling
normal operation, the system complies with On Board Diagnostic (OBD) system strategies. The system monitors and
reports on faults detected with ignition, fuelling and exhaust systems which cause an excessive increase in tailpipe
emissions. This includes component failures, engine misfire, catalyst damage, catalyst efficiency, fuel evaporative
loss and exhaust leaks.
When an emission relevant fault is determined, the fault condition is stored in the ECM memory. For NAS vehicles,
the MIL warning light on the instrument pack will be illuminated when the fault is confirmed. Confirmation of a fault
condition occurs if the fault is still found to be present during the driving cycle subsequent to the one when the fault
was first detected.
+ ENGINE MANAGEMENT SYSTEM - V8, DESCRIPTION AND OPERATION, Description - engine
management.
The following types of supplementary control system are used to reduce harmful emissions released into the
atmosphere from the vehicle:
1Crankcase emission control – also known as blow-by gas emissions from the engine crankcase.
2Exhaust emission control – to limit the undesirable by-products of combustion.
3Fuel vapour evaporative loss control – to restrict the emission of fuel through evaporation from the fuel
system.
4Fuel leak detection system (NAS only) – there are two types of system which may be used to check the
evaporative emission system for the presence of leaks from the fuel tank to purge valve.
aVacuum leak detection test – checks for leaks down to 1 mm (0.04 in.) in diameter.
bPositive pressure leak detection test – utilises a leak detection pump to check for leaks down to 0.5 mm (0.02
in.) in diameter.
5Secondary air injection system (NAS only) – to reduce emissions experienced during cold starting.
Crankcase emission control system
The concentration of hydrocarbons in the crankcase of an engine is much greater than that in the vehicle's exhaust
system. In order to prevent the emission of these hydrocarbons into the atmosphere, crankcase emission control
systems are employed and are a standard legal requirement.
The crankcase ventilation system is an integral part of the air supply to the engine combustion chambers and it is
often overlooked when diagnosing problems associated with engine performance. A blocked ventilation pipe or filter
or excessive air leak into the inlet system through a damaged pipe or a leaking gasket can affect the air:fuel mixture,
performance and efficiency of the engine. Periodically check the ventilation hoses are not cracked and that they are
securely fitted to form airtight connections at their relevant ports.
The purpose of the crankcase ventilation system is to ensure that any noxious gas generated in the engine crankcase
is rendered harmless by complete burning of the fuel in the combustion chamber. Burning the crankcase vapours in
a controlled manner decreases the HC pollutants that could be emitted and helps to prevent the development of
sludge in the engine oil as well as increasing fuel economy.