Page 217 of 1672
ENGINE - TD5
12-1-78 OVERHAUL
14.Check end-float of camshaft using a DTI:
l Camshaft end-float = 0.06 to 0.16 mm
(0.002 to 0.006 in)
15.Renew components as necessary to achieve
correct end-float.
16.Check camshaft bearing clearances using the
following procedures.
17.Position camshaft in cylinder head.
18.Place a piece of Plastigage along centre line of
each camshaft bearing journal.
19.Carefully fit the camshaft carrier ensuring it is
located on dowels. Do not rotate camshaft.20.Fit original camshaft carrier bolts and tighten in
sequence shown to 25 Nm (18 lbf.ft).
21.Using sequence shown, loosen then remove
camshaft carrier retaining bolts. Do not
discard bolts at this stage.
22.Carefully remove camshaft carrier.
23.Measure and record widest portion of
Plastigage on each camshaft bearing journal.
Page 218 of 1672
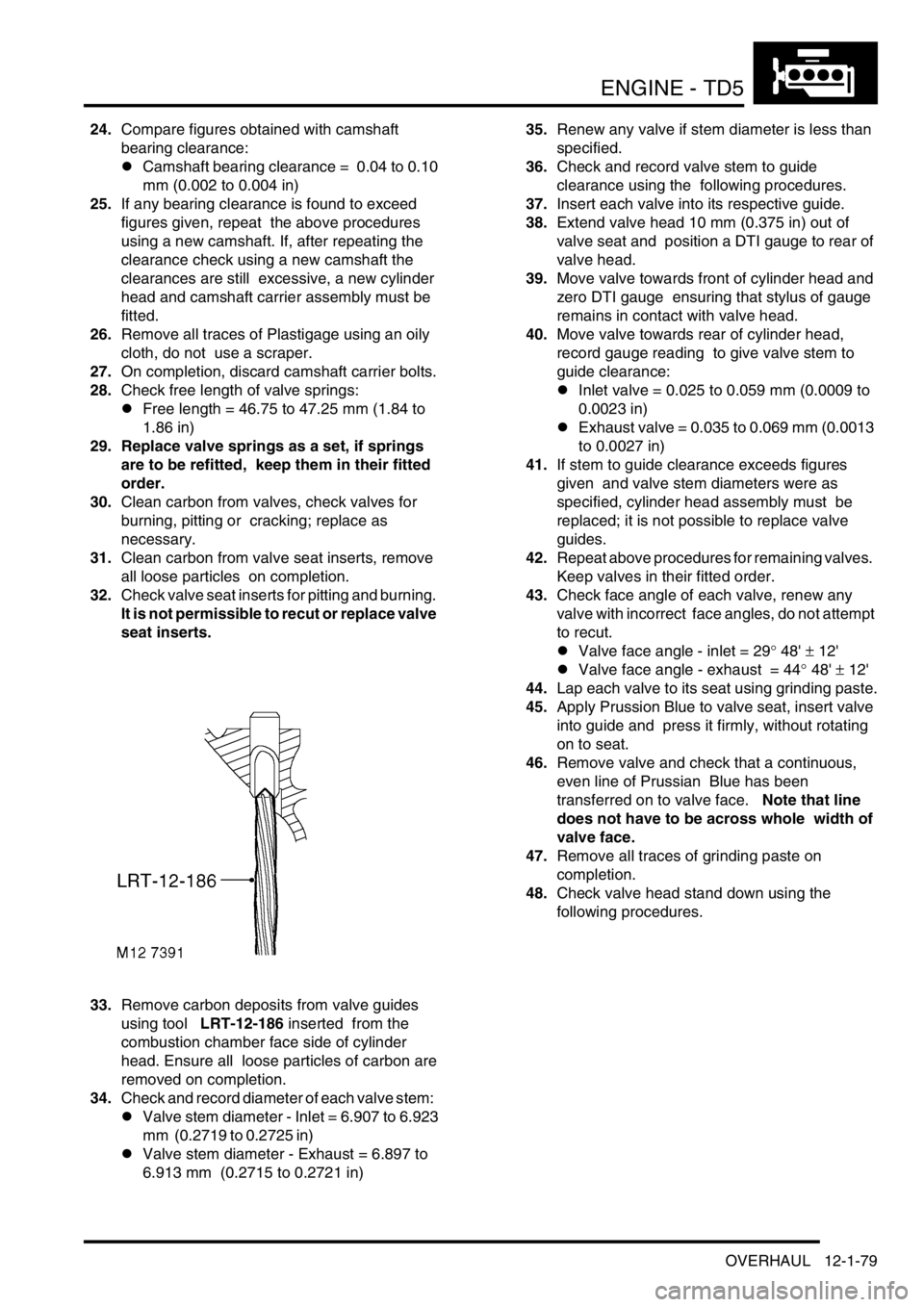
ENGINE - TD5
OVERHAUL 12-1-79
24.Compare figures obtained with camshaft
bearing clearance:
lCamshaft bearing clearance = 0.04 to 0.10
mm (0.002 to 0.004 in)
25.If any bearing clearance is found to exceed
figures given, repeat the above procedures
using a new camshaft. If, after repeating the
clearance check using a new camshaft the
clearances are still excessive, a new cylinder
head and camshaft carrier assembly must be
fitted.
26.Remove all traces of Plastigage using an oily
cloth, do not use a scraper.
27.On completion, discard camshaft carrier bolts.
28.Check free length of valve springs:
lFree length = 46.75 to 47.25 mm (1.84 to
1.86 in)
29. Replace valve springs as a set, if springs
are to be refitted, keep them in their fitted
order.
30.Clean carbon from valves, check valves for
burning, pitting or cracking; replace as
necessary.
31.Clean carbon from valve seat inserts, remove
all loose particles on completion.
32.Check valve seat inserts for pitting and burning.
It is not permissible to recut or replace valve
seat inserts.
33.Remove carbon deposits from valve guides
using tool LRT-12-186 inserted from the
combustion chamber face side of cylinder
head. Ensure all loose particles of carbon are
removed on completion.
34.Check and record diameter of each valve stem:
lValve stem diameter - Inlet = 6.907 to 6.923
mm (0.2719 to 0.2725 in)
lValve stem diameter - Exhaust = 6.897 to
6.913 mm (0.2715 to 0.2721 in)35.Renew any valve if stem diameter is less than
specified.
36.Check and record valve stem to guide
clearance using the following procedures.
37.Insert each valve into its respective guide.
38.Extend valve head 10 mm (0.375 in) out of
valve seat and position a DTI gauge to rear of
valve head.
39.Move valve towards front of cylinder head and
zero DTI gauge ensuring that stylus of gauge
remains in contact with valve head.
40.Move valve towards rear of cylinder head,
record gauge reading to give valve stem to
guide clearance:
lInlet valve = 0.025 to 0.059 mm (0.0009 to
0.0023 in)
lExhaust valve = 0.035 to 0.069 mm (0.0013
to 0.0027 in)
41.If stem to guide clearance exceeds figures
given and valve stem diameters were as
specified, cylinder head assembly must be
replaced; it is not possible to replace valve
guides.
42.Repeat above procedures for remaining valves.
Keep valves in their fitted order.
43.Check face angle of each valve, renew any
valve with incorrect face angles, do not attempt
to recut.
lValve face angle - inlet = 29
° 48' ± 12'
lValve face angle - exhaust = 44
° 48' ± 12'
44.Lap each valve to its seat using grinding paste.
45.Apply Prussion Blue to valve seat, insert valve
into guide and press it firmly, without rotating
on to seat.
46.Remove valve and check that a continuous,
even line of Prussian Blue has been
transferred on to valve face. Note that line
does not have to be across whole width of
valve face.
47.Remove all traces of grinding paste on
completion.
48.Check valve head stand down using the
following procedures.
Page 219 of 1672
ENGINE - TD5
12-1-80 OVERHAUL
49.Insert each valve into its respective guide.
50.Using a straight edge and feeler gauges, check
and record stand down of each valve head.
51.Compare figures obtained with those given
below:
lValve head stand down - Inlet valve A =
0.555 to 0.825 mm (0.022 to 0.032 in)
lValve head stand down - Exhaust valve B =
0.545 to 1.35 mm (0.021 to 0.053 in)
52. If any valve has a stand down greater than
specified, repeat check using a new valve.
If, after checking with a new valve, stand
down is still excessive, cylinder head
assembly must be replaced. It is not
possible to replace valve seat inserts.53.Suitably identify each rocker arm to its fitted
position and type of rocker arm fitted.
NOTE:
lEngine Serial No. Prefixes 10P to 14P -
Type A rocker arms
lEngine Serial No. Prefixes 15P to 19P -
Type B rocker arms.
Type B rocker arms and shafts may be fitted to
Engine Serial No. Prefixes 10P to 14P as an
assembly.
Page 220 of 1672
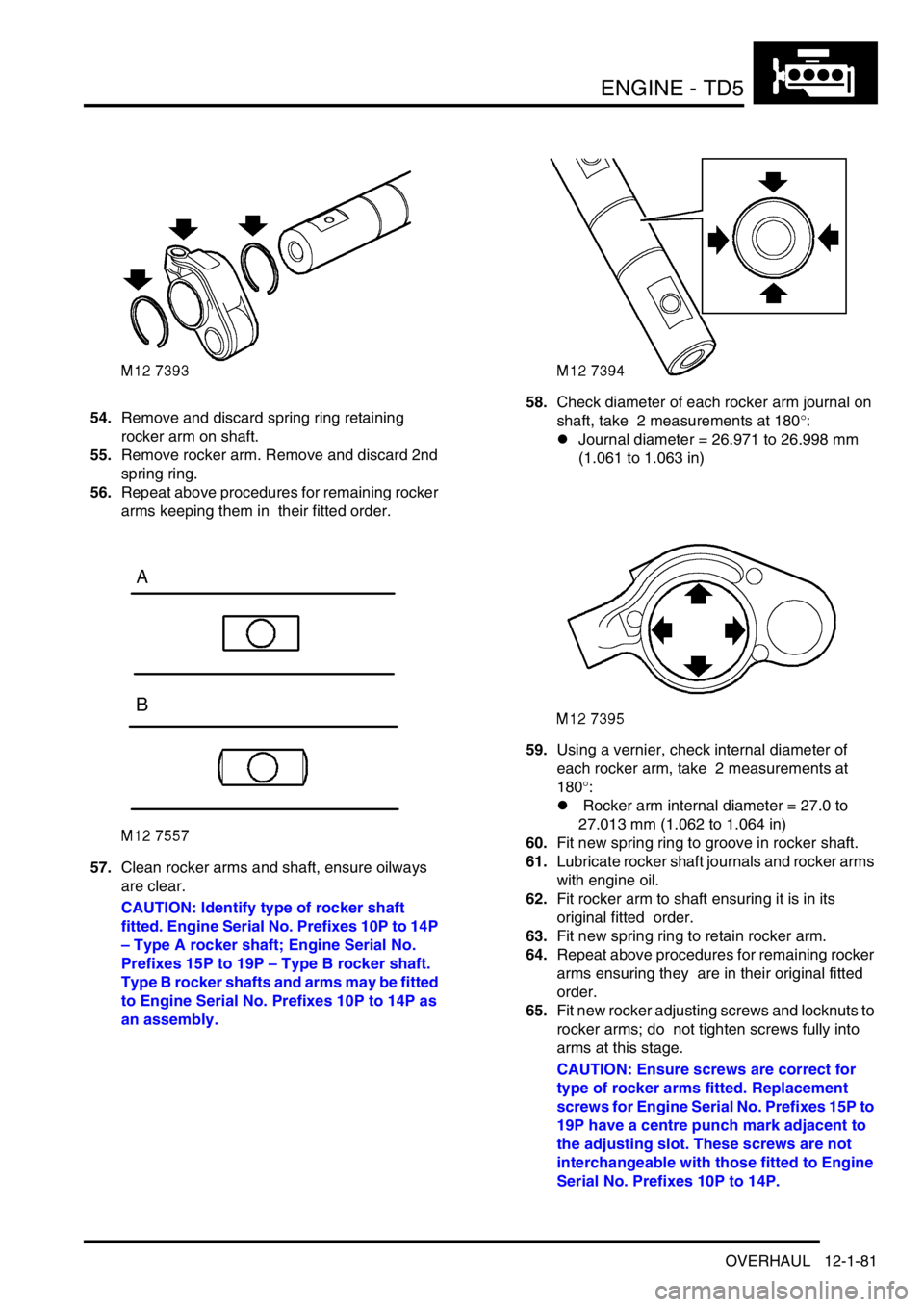
ENGINE - TD5
OVERHAUL 12-1-81
54.Remove and discard spring ring retaining
rocker arm on shaft.
55.Remove rocker arm. Remove and discard 2nd
spring ring.
56.Repeat above procedures for remaining rocker
arms keeping them in their fitted order.
57.Clean rocker arms and shaft, ensure oilways
are clear.
CAUTION: Identify type of rocker shaft
fitted. Engine Serial No. Prefixes 10P to 14P
– Type A rocker shaft; Engine Serial No.
Prefixes 15P to 19P – Type B rocker shaft.
Type B rocker shafts and arms may be fitted
to Engine Serial No. Prefixes 10P to 14P as
an assembly.58.Check diameter of each rocker arm journal on
shaft, take 2 measurements at 180°:
lJournal diameter = 26.971 to 26.998 mm
(1.061 to 1.063 in)
59.Using a vernier, check internal diameter of
each rocker arm, take 2 measurements at
180
°:
l Rocker arm internal diameter = 27.0 to
27.013 mm (1.062 to 1.064 in)
60.Fit new spring ring to groove in rocker shaft.
61.Lubricate rocker shaft journals and rocker arms
with engine oil.
62.Fit rocker arm to shaft ensuring it is in its
original fitted order.
63.Fit new spring ring to retain rocker arm.
64.Repeat above procedures for remaining rocker
arms ensuring they are in their original fitted
order.
65.Fit new rocker adjusting screws and locknuts to
rocker arms; do not tighten screws fully into
arms at this stage.
CAUTION: Ensure screws are correct for
type of rocker arms fitted. Replacement
screws for Engine Serial No. Prefixes 15P to
19P have a centre punch mark adjacent to
the adjusting slot. These screws are not
interchangeable with those fitted to Engine
Serial No. Prefixes 10P to 14P.
Page 221 of 1672
ENGINE - TD5
12-1-82 OVERHAUL
Reassembly
1.Lubricate new valve stem oil seals with engine
oil.
2.Using tool LRT-12-071 fit valve stem oil seals.
3.Lubricate valve guides, valve stems, valve
spring caps and springs with engine oil. 4.Assemble valves, springs and spring caps
ensuring they are in their original fitted order.
5.Compress valve springs using tool LRT-12-
034 , fit collets.
6.Using a wooden dowel and mallet, tap each
spring cap lightly to seat collets.
7.Lubricate new injector 'O' rings with engine oil.
8.Using tool LRT-12-154/2, fit new 'O' ring to
each injector.
Page 222 of 1672
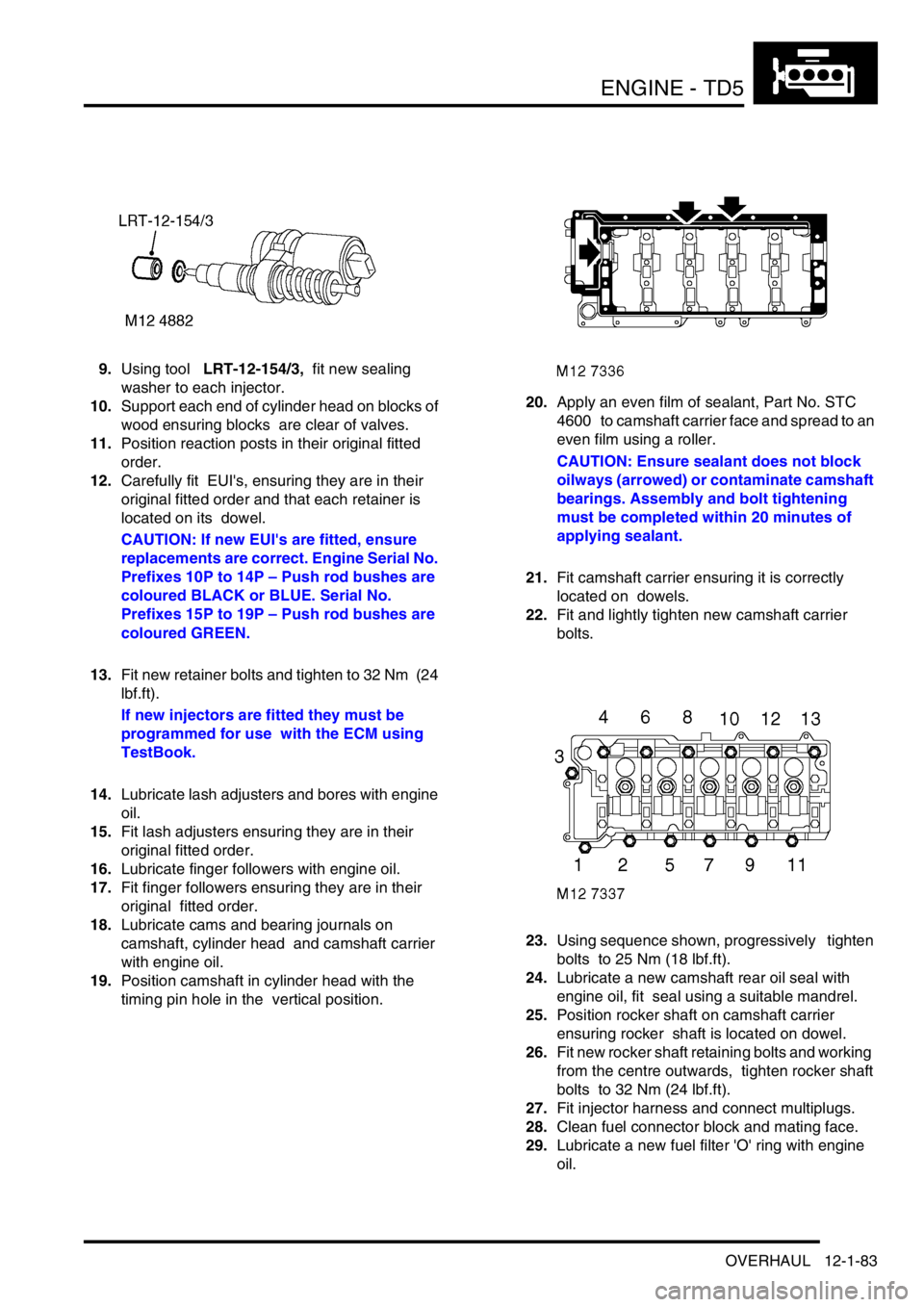
ENGINE - TD5
OVERHAUL 12-1-83
9.Using tool LRT-12-154/3, fit new sealing
washer to each injector.
10.Support each end of cylinder head on blocks of
wood ensuring blocks are clear of valves.
11.Position reaction posts in their original fitted
order.
12.Carefully fit EUI's, ensuring they are in their
original fitted order and that each retainer is
located on its dowel.
CAUTION: If new EUI's are fitted, ensure
replacements are correct. Engine Serial No.
Prefixes 10P to 14P – Push rod bushes are
coloured BLACK or BLUE. Serial No.
Prefixes 15P to 19P – Push rod bushes are
coloured GREEN.
13.Fit new retainer bolts and tighten to 32 Nm (24
lbf.ft).
If new injectors are fitted they must be
programmed for use with the ECM using
TestBook.
14.Lubricate lash adjusters and bores with engine
oil.
15.Fit lash adjusters ensuring they are in their
original fitted order.
16.Lubricate finger followers with engine oil.
17.Fit finger followers ensuring they are in their
original fitted order.
18.Lubricate cams and bearing journals on
camshaft, cylinder head and camshaft carrier
with engine oil.
19.Position camshaft in cylinder head with the
timing pin hole in the vertical position.20.Apply an even film of sealant, Part No. STC
4600 to camshaft carrier face and spread to an
even film using a roller.
CAUTION: Ensure sealant does not block
oilways (arrowed) or contaminate camshaft
bearings. Assembly and bolt tightening
must be completed within 20 minutes of
applying sealant.
21.Fit camshaft carrier ensuring it is correctly
located on dowels.
22.Fit and lightly tighten new camshaft carrier
bolts.
23.Using sequence shown, progressively tighten
bolts to 25 Nm (18 lbf.ft).
24.Lubricate a new camshaft rear oil seal with
engine oil, fit seal using a suitable mandrel.
25.Position rocker shaft on camshaft carrier
ensuring rocker shaft is located on dowel.
26.Fit new rocker shaft retaining bolts and working
from the centre outwards, tighten rocker shaft
bolts to 32 Nm (24 lbf.ft).
27.Fit injector harness and connect multiplugs.
28.Clean fuel connector block and mating face.
29.Lubricate a new fuel filter 'O' ring with engine
oil.
Page 223 of 1672
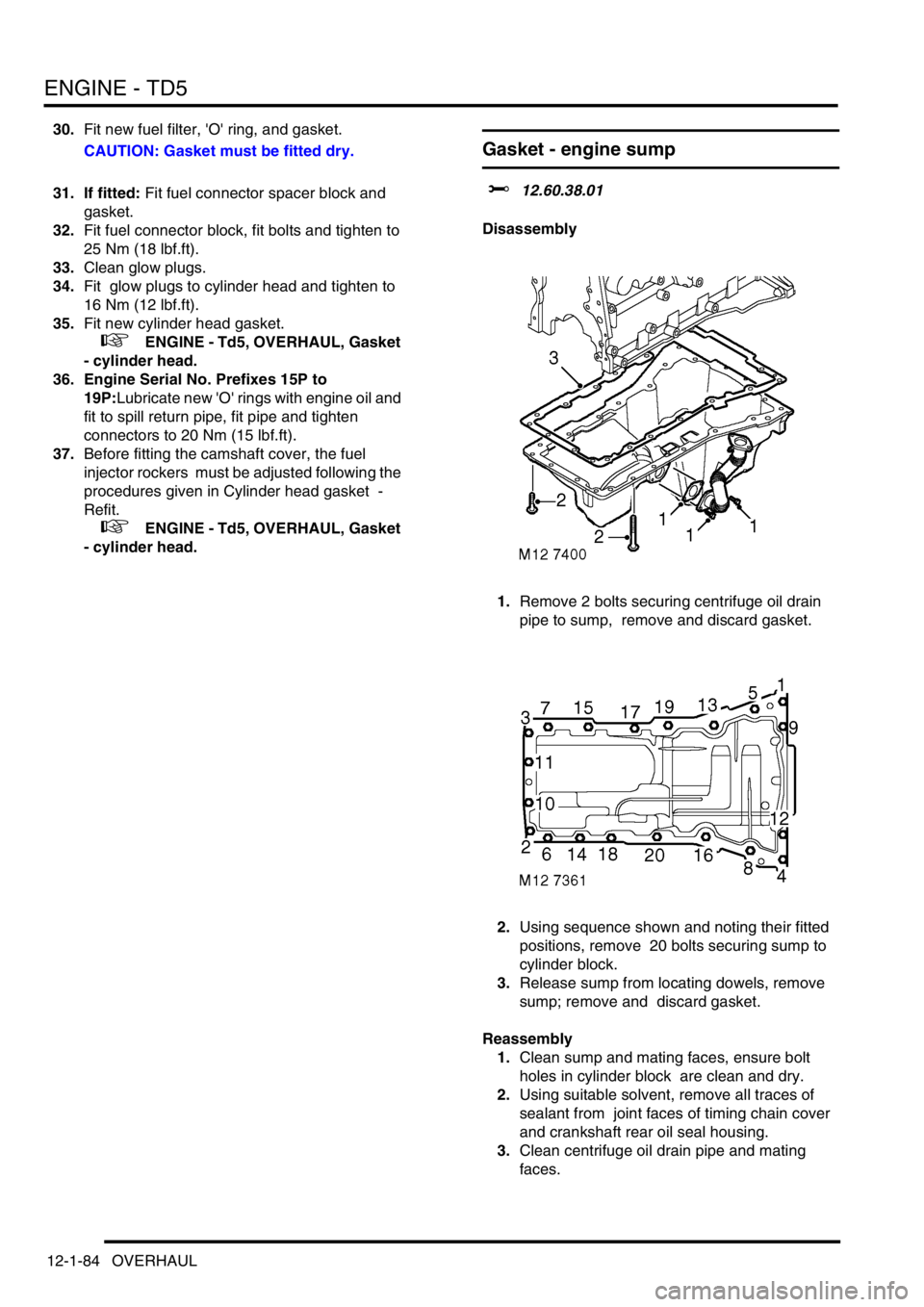
ENGINE - TD5
12-1-84 OVERHAUL
30.Fit new fuel filter, 'O' ring, and gasket.
CAUTION: Gasket must be fitted dry.
31. If fitted: Fit fuel connector spacer block and
gasket.
32.Fit fuel connector block, fit bolts and tighten to
25 Nm (18 lbf.ft).
33.Clean glow plugs.
34.Fit glow plugs to cylinder head and tighten to
16 Nm (12 lbf.ft).
35.Fit new cylinder head gasket.
+ ENGINE - Td5, OVERHAUL, Gasket
- cylinder head.
36. Engine Serial No. Prefixes 15P to
19P:Lubricate new 'O' rings with engine oil and
fit to spill return pipe, fit pipe and tighten
connectors to 20 Nm (15 lbf.ft).
37.Before fitting the camshaft cover, the fuel
injector rockers must be adjusted following the
procedures given in Cylinder head gasket -
Refit.
+ ENGINE - Td5, OVERHAUL, Gasket
- cylinder head.
Gasket - engine sump
$% 12.60.38.01
Disassembly
1.Remove 2 bolts securing centrifuge oil drain
pipe to sump, remove and discard gasket.
2.Using sequence shown and noting their fitted
positions, remove 20 bolts securing sump to
cylinder block.
3.Release sump from locating dowels, remove
sump; remove and discard gasket.
Reassembly
1.Clean sump and mating faces, ensure bolt
holes in cylinder block are clean and dry.
2.Using suitable solvent, remove all traces of
sealant from joint faces of timing chain cover
and crankshaft rear oil seal housing.
3.Clean centrifuge oil drain pipe and mating
faces.
Page 224 of 1672
ENGINE - TD5
OVERHAUL 12-1-85
4.Apply a bead of sealant, Part No. STC 3254 to
joint faces of timing chain cover and crankshaft
rear oil seal housing.
CAUTION: Assembly and bolt tightening
must be completed within 20 minutes of
applying sealant.
5.Position new sump gasket.
CAUTION: Gasket must be fitted dry.
6.Position sump, fit and lightly tighten bolts
ensuring they are in their original fitted
positions.
7.Using sequence shown, tighten sump bolts to
25 Nm (18 lbf.ft).8.Fit new centrifuge oil drain pipe gasket.
CAUTION: Gasket must be fitted dry.
9.Fit centrifuge oil drain pipe, fit bolts and tighten
to 10 Nm (7 lbf.ft).