Page 9 of 48
9
M54engMS43/ST036/6/20000
SYSTEM OVERVIEW I-P-O
Service
Engine
Soon
ART-IPO46X.EPS
Page 10 of 48
10
M54engMS43/ST036/6/2000
MS 43 NEW FUNCTIONS
ELECTRONIC THROTTLE SYSTEM - EML
The M54 engine with MS 43 engine control uses an electronic throttle control system
adopted from the ME 7.2 system on the M62 engine. The system incorporates an electric
throttle valve (EDK) and pedal position sensor (PWG) for engine power control.
The MS 43 control module monitors the PWG input and activates the EDK motor based on
the programmed maps for throttle control. The MS 43 module self checks the activation of
the EDK via feedback potentiometers motor on the EDK motor.
Additional functions of the EML system include:
• Cruise control function
• DSC throttle interventions
• Maximum engine and road speed control
ART-SCANDIAGRAM
Page 12 of 48
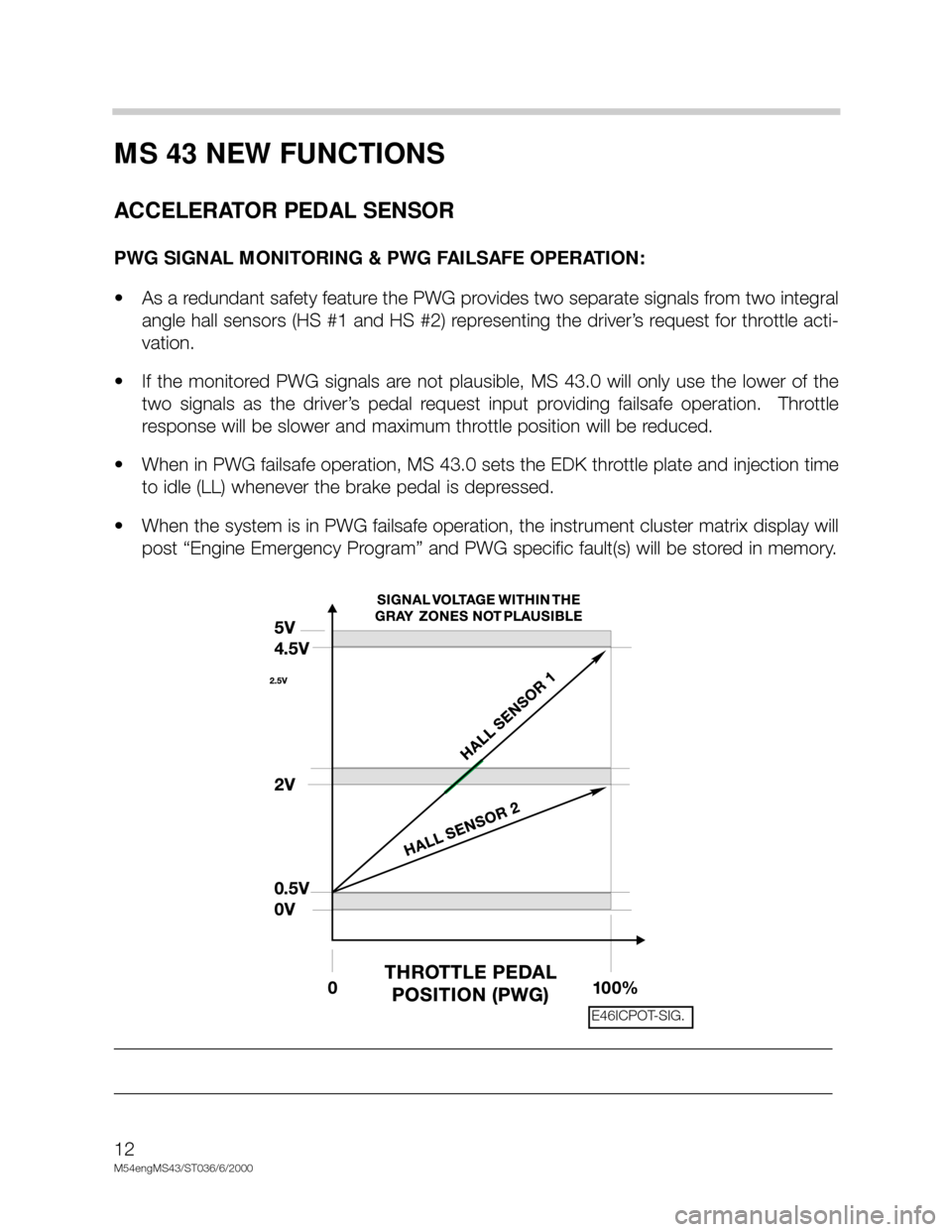
12
M54engMS43/ST036/6/2000
MS 43 NEW FUNCTIONS
ACCELERATOR PEDAL SENSOR
PWG SIGNAL MONITORING & PWG FAILSAFE OPERATION:
• As a redundant safety feature the PWG provides two separate signals from two integral
angle hall sensors (HS #1 and HS #2) representing the driver’s request for throttle acti-
vation.
• If the monitored PWG signals are not plausible, MS 43.0 will only use the lower of the
two signals as the driver’s pedal request input providing failsafe operation. Throttle
response will be slower and maximum throttle position will be reduced.
• When in PWG failsafe operation, MS 43.0 sets the EDK throttle plate and injection time
to idle (LL) whenever the brake pedal is depressed.
• When the system is in PWG failsafe operation, the instrument cluster matrix display will
post “Engine Emergency Program” and PWG specific fault(s) will be stored in memory.
_____________________________________________________________________________
_____________________________________________________________________________
E46ICPOT-SIG.
Page 14 of 48
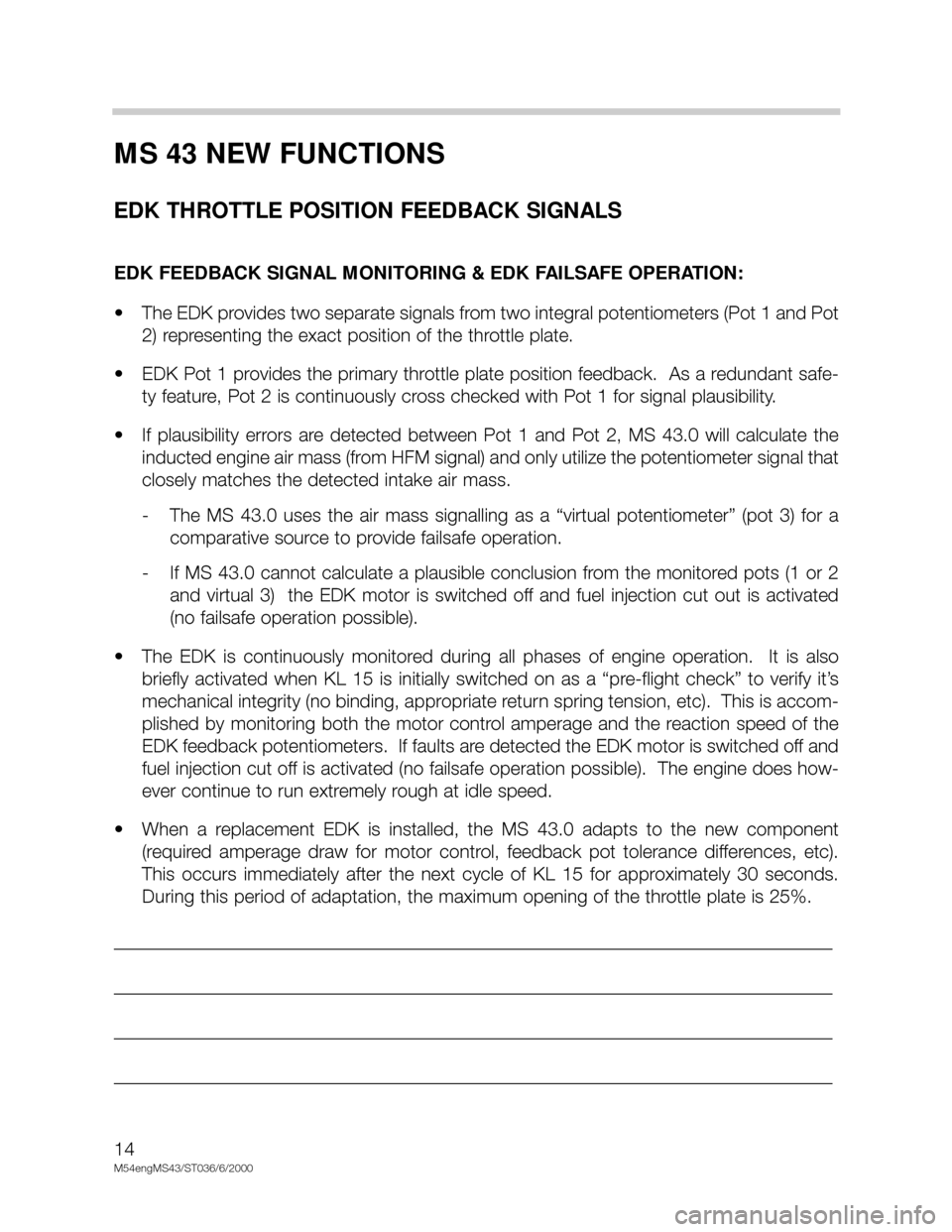
14
M54engMS43/ST036/6/2000
MS 43 NEW FUNCTIONS
EDK THROTTLE POSITION FEEDBACK SIGNALS
EDK FEEDBACK SIGNAL MONITORING & EDK FAILSAFE OPERATION:
• The EDK provides two separate signals from two integral potentiometers (Pot 1 and Pot
2) representing the exact position of the throttle plate.
• EDK Pot 1 provides the primary throttle plate position feedback. As a redundant safe-
ty feature, Pot 2 is continuously cross checked with Pot 1 for signal plausibility.
• If plausibility errors are detected between Pot 1 and Pot 2, MS 43.0 will calculate the
inducted engine air mass (from HFM signal) and only utilize the potentiometer signal that
closely matches the detected intake air mass.
- The MS 43.0 uses the air mass signalling as a “virtual potentiometer” (pot 3) for a
comparative source to provide failsafe operation.
- If MS 43.0 cannot calculate a plausible conclusion from the monitored pots (1 or 2
and virtual 3) the EDK motor is switched off and fuel injection cut out is activated
(no failsafe operation possible).
• The EDK is continuously monitored during all phases of engine operation. It is also
briefly activated when KL 15 is initially switched on as a “pre-flight check” to verify it’s
mechanical integrity (no binding, appropriate return spring tension, etc). This is accom-
plished by monitoring both the motor control amperage and the reaction speed of the
EDK feedback potentiometers. If faults are detected the EDK motor is switched off and
fuel injection cut off is activated (no failsafe operation possible). The engine does how-
ever continue to run extremely rough at idle speed.
• When a replacement EDK is installed, the MS 43.0 adapts to the new component
(required amperage draw for motor control, feedback pot tolerance differences, etc).
This occurs immediately after the next cycle of KL 15 for approximately 30 seconds.
During this period of adaptation, the maximum opening of the throttle plate is 25%.
_____________________________________________________________________________
_____________________________________________________________________________
_____________________________________________________________________________
_____________________________________________________________________________
Page 16 of 48
16
M54engMS43/ST036/6/2000
MS 43 NEW FUNCTIONS
EMISSION OPTIMIZED - IGNITION KEY OFF
“Emission Optimized Ignition Key Off” is a programmed feature of the MS 43 control mod-
ule.
After the ECM detects KL 15 being switched OFF, the ignition stays active for two more
individual coil firings. This means that just two cylinders are fired - not two revolutions.
This feature allows residual fuel injected into the cylinders, as the ignition key is switched
off, to be burned as the engine runs down.
__________________________________________________________________
__________________________________________________________________
__________________________________________________________________
__________________________________________________________________
ART-E46ICEMIOPT
Page 17 of 48
17
M54engms43/STO36/6/2000
MS 43 NEW FUNCTIONS
DM-TL (DIAGNOSIS MODULE - TANK LEAKAGE)
The M54 engine with the Siemens MS43.0 engine control system uses the DMTL system
for fuel system leakage monitoring. The pump is manufactured by Bosch for use with the
Siemen’s control system.
Page 19 of 48
19
M54engMS43/ST039/3/17/00
DM-TL (DIAGNOSIS MODULE - TANK LEAKAGE)
FUNCTION
The DC Motor LDP ensures accurate fuel system leak detection for leaks as small as
0.5mm (.020”). The pump contains an integral DC motor which is activated directly by the
engine control module. The ECM monitors the pump motor operating current as the mea-
surement for detecting leaks.
The pump also contains an ECM controlled change over valve that is energized closed dur-
ing a Leak Diagnosis test. The change over valve is open during all other periods of oper-
ation allowing the fuel system to “breath” through the inlet filter (similar to the full down
stroke of the current vacuum operated LDP).
Page 20 of 48
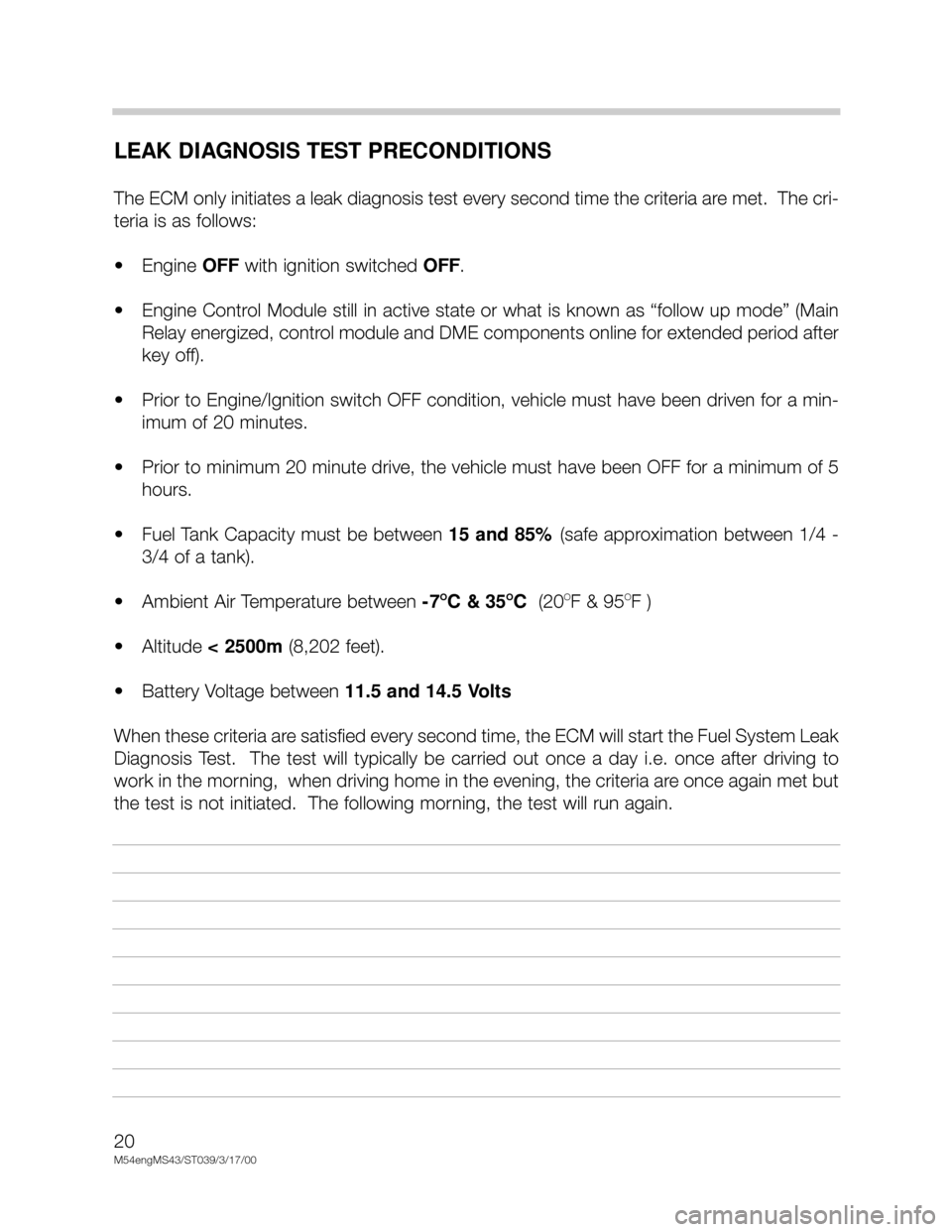
20
M54engMS43/ST039/3/17/00
LEAK DIAGNOSIS TEST PRECONDITIONS
The ECM only initiates a leak diagnosis test every second time the criteria are met. The cri-
teria is as follows:
• Engine OFF with ignition switched OFF.
• Engine Control Module still in active state or what is known as “follow up mode” (Main
Relay energized, control module and DME components online for extended period after
key off).
• Prior to Engine/Ignition switch OFF condition, vehicle must have been driven for a min-
imum of 20 minutes.
• Prior to minimum 20 minute drive, the vehicle must have been OFF for a minimum of 5
hours.
• Fuel Tank Capacity must be between 15 and 85%(safe approximation between 1/4 -
3/4 of a tank).
• Ambient Air Temperature between -7
OC & 35OC(20OF & 95OF )
• Altitude < 2500m(8,202 feet).
• Battery Voltage between 11.5 and 14.5 Volts
When these criteria are satisfied every second time, the ECM will start the Fuel System Leak
Diagnosis Test. The test will typically be carried out once a day i.e. once after driving to
work in the morning, when driving home in the evening, the criteria are once again met but
the test is not initiated. The following morning, the test will run again.