Page 880 of 2395
Diagnostic ProcedureNBEC0202
1 CHECK STARTING SYSTEM
Turn ignition switch to ªSTARTº position.
Does the engine turn over?
Does the starter motor operate?
YesorNo
Ye s©GO TO 2.
No©Check starting system. (Refer to SC-10, ªSTARTING SYSTEMº.)
2 RETIGHTEN GROUND SCREWS
1. Turn ignition switch ªOFFº.
2. Loosen and retighten engine ground screws.
SEF959Y
©GO TO 3.
3 CHECK CMPS (PHASE) INPUT SIGNAL CIRCUIT FOR OPEN AND SHORT
1. Turn ignition switch ªOFFº.
2. Disconnect ECM harness connector and CMPS (PHASE) harness connector.
SEF982Y
3. Check harness continuity between CMPS (PHASE) terminal 2 and ECM terminals 66, 76. Refer to Wiring Diagram.
Continuity should exist.
4. Also check harness for short to ground and short to power.
OK or NG
OK©GO TO 4.
NG©Repair open circuit or short to ground or short to power in harness or connectors.
GI
MA
EM
LC
FE
AT
TF
PD
AX
SU
BR
ST
RS
BT
HA
SC
EL
IDX
DTC P0340 CAMSHAFT POSITION SENSOR (CMPS) (PHASE)
Diagnostic Procedure
EC-345
Page 881 of 2395
4 CHECK CMPS (PHASE) GROUND CIRCUIT FOR OPEN AND SHORT
1. Check harness continuity between CMPS (PHASE) terminal 1 and engine ground.
Continuity should exist.
2. Also check harness for short to power.
OK or NG
OK©GO TO 5.
NG©Repair open circuit or short to power in harness or connector.
5 CHECK CAMSHAFT POSITION SENSOR (PHASE)-I
1. Loosen the fixing bolt of the camshaft position sensor (PHASE).
2. Remove the CMPS (PHASE).
3. Visually check the CMPS (PHASE) for chipping.
SEF583P
OK or NG
OK©GO TO 6.
NG©Replace camshaft position sensor (PHASE).
6 CHECK CAMSHAFT POSITION SENSOR (PHASE)-II
Check resistance between CMPS (PHASE) terminals 1 and 2 as shown below.
SEF325X
OK or NG
OK©GO TO 7.
NG©Replace camshaft position sensor (PHASE).
7 CHECK INTERMITTENT INCIDENT
Refer to ªTROUBLE DIAGNOSIS FOR INTERMITTENT INCIDENTº, EC-140.
©INSPECTION END
DTC P0340 CAMSHAFT POSITION SENSOR (CMPS) (PHASE)
Diagnostic Procedure (Cont'd)
EC-346
Page 882 of 2395
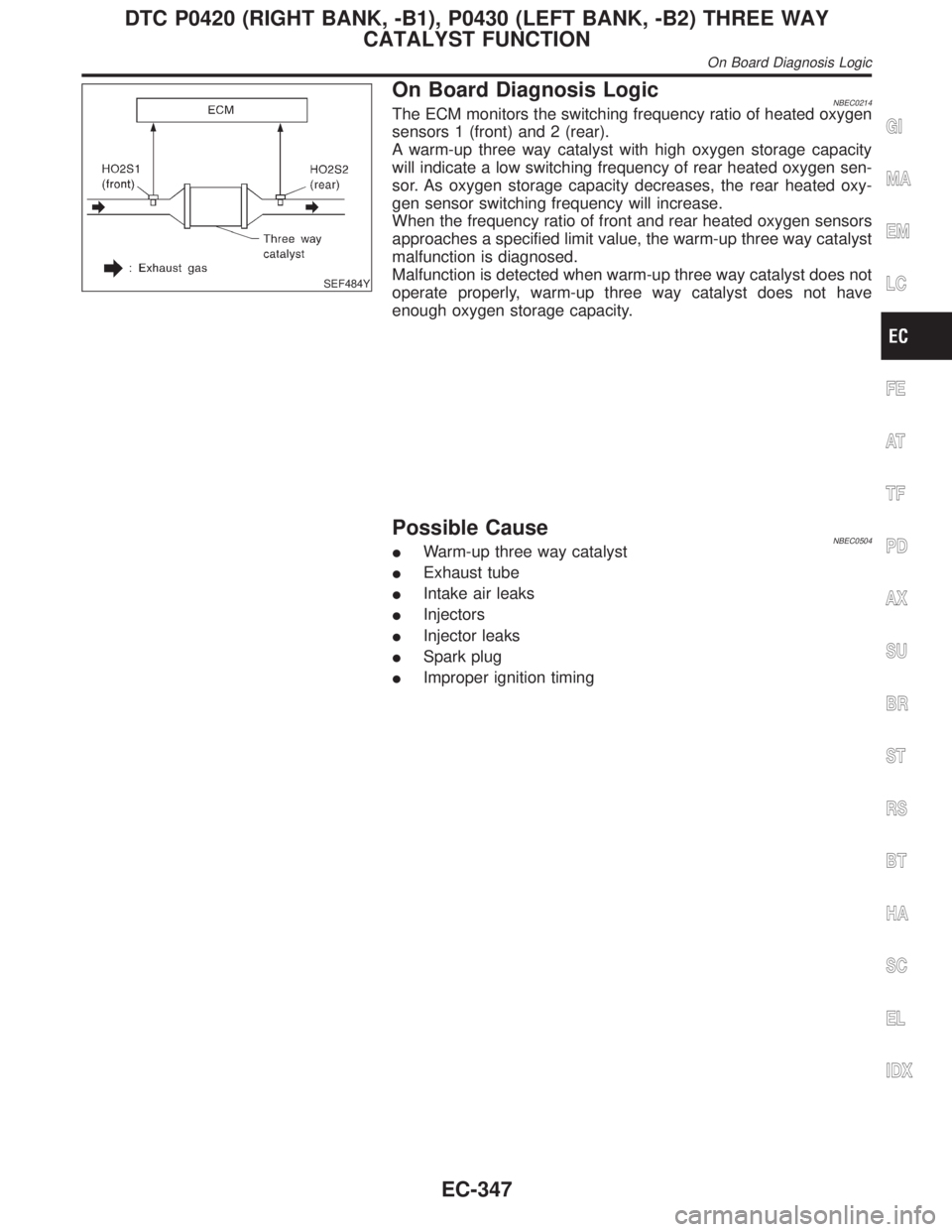
SEF484Y
On Board Diagnosis LogicNBEC0214The ECM monitors the switching frequency ratio of heated oxygen
sensors 1 (front) and 2 (rear).
A warm-up three way catalyst with high oxygen storage capacity
will indicate a low switching frequency of rear heated oxygen sen-
sor. As oxygen storage capacity decreases, the rear heated oxy-
gen sensor switching frequency will increase.
When the frequency ratio of front and rear heated oxygen sensors
approaches a specified limit value, the warm-up three way catalyst
malfunction is diagnosed.
Malfunction is detected when warm-up three way catalyst does not
operate properly, warm-up three way catalyst does not have
enough oxygen storage capacity.
Possible CauseNBEC0504IWarm-up three way catalyst
IExhaust tube
IIntake air leaks
IInjectors
IInjector leaks
ISpark plug
IImproper ignition timing
GI
MA
EM
LC
FE
AT
TF
PD
AX
SU
BR
ST
RS
BT
HA
SC
EL
IDX
DTC P0420 (RIGHT BANK, -B1), P0430 (LEFT BANK, -B2) THREE WAY
CATALYST FUNCTION
On Board Diagnosis Logic
EC-347
Page 883 of 2395
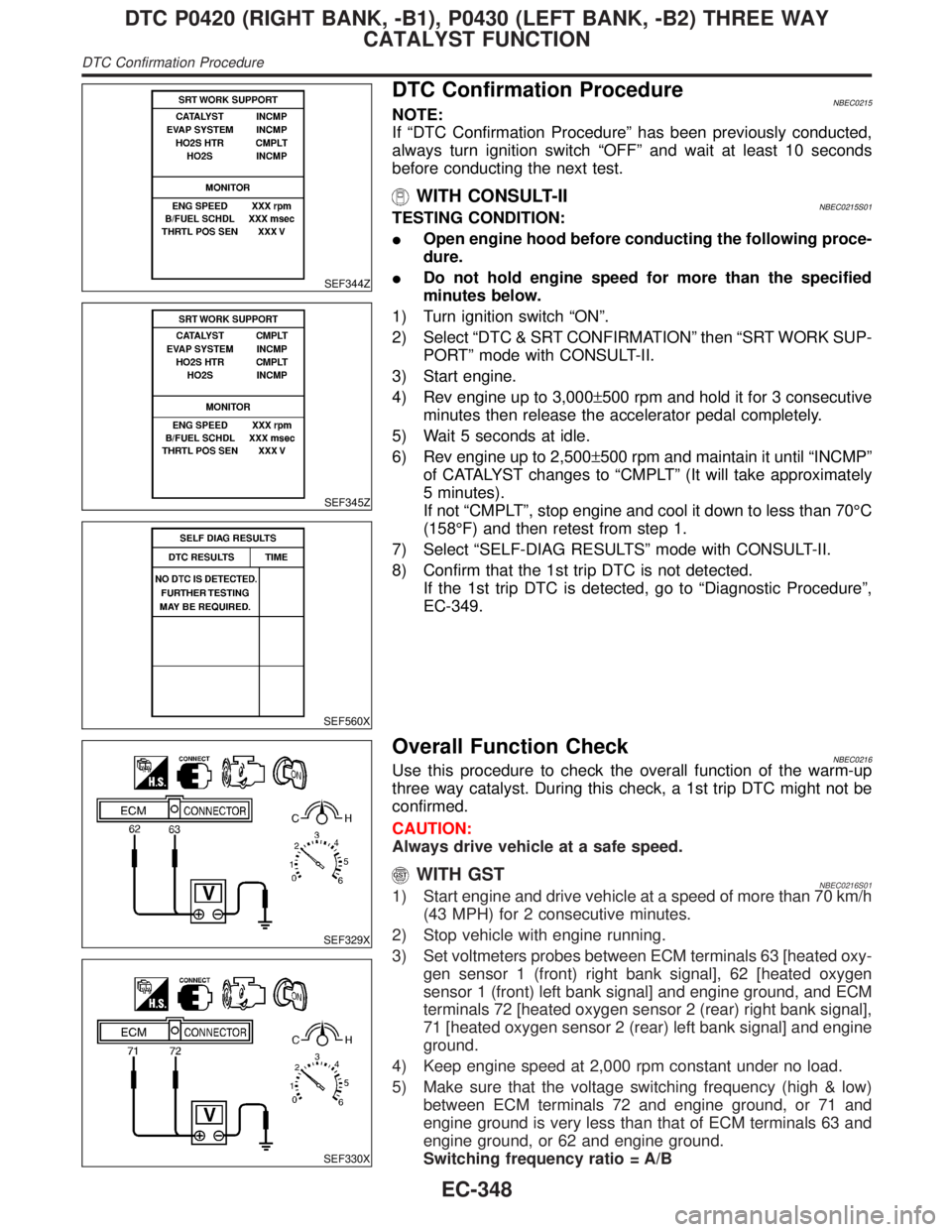
SEF344Z
DTC Confirmation ProcedureNBEC0215
SEF345Z
SEF560X
NOTE:
If ªDTC Confirmation Procedureº has been previously conducted,
always turn ignition switch ªOFFº and wait at least 10 seconds
before conducting the next test.
WITH CONSULT-IINBEC0215S01TESTING CONDITION:
IOpen engine hood before conducting the following proce-
dure.
IDo not hold engine speed for more than the specified
minutes below.
1) Turn ignition switch ªONº.
2) Select ªDTC & SRT CONFIRMATIONº then ªSRT WORK SUP-
PORTº mode with CONSULT-II.
3) Start engine.
4) Rev engine up to 3,000±500 rpm and hold it for 3 consecutive
minutes then release the accelerator pedal completely.
5) Wait 5 seconds at idle.
6) Rev engine up to 2,500±500 rpm and maintain it until ªINCMPº
of CATALYST changes to ªCMPLTº (It will take approximately
5 minutes).
If not ªCMPLTº, stop engine and cool it down to less than 70ÉC
(158ÉF) and then retest from step 1.
7) Select ªSELF-DIAG RESULTSº mode with CONSULT-II.
8) Confirm that the 1st trip DTC is not detected.
If the 1st trip DTC is detected, go to ªDiagnostic Procedureº,
EC-349.
SEF329X
SEF330X
Overall Function CheckNBEC0216Use this procedure to check the overall function of the warm-up
three way catalyst. During this check, a 1st trip DTC might not be
confirmed.
CAUTION:
Always drive vehicle at a safe speed.
WITH GSTNBEC0216S011) Start engine and drive vehicle at a speed of more than 70 km/h
(43 MPH) for 2 consecutive minutes.
2) Stop vehicle with engine running.
3) Set voltmeters probes between ECM terminals 63 [heated oxy-
gen sensor 1 (front) right bank signal], 62 [heated oxygen
sensor 1 (front) left bank signal] and engine ground, and ECM
terminals 72 [heated oxygen sensor 2 (rear) right bank signal],
71 [heated oxygen sensor 2 (rear) left bank signal] and engine
ground.
4) Keep engine speed at 2,000 rpm constant under no load.
5) Make sure that the voltage switching frequency (high & low)
between ECM terminals 72 and engine ground, or 71 and
engine ground is very less than that of ECM terminals 63 and
engine ground, or 62 and engine ground.
Switching frequency ratio = A/B
DTC P0420 (RIGHT BANK, -B1), P0430 (LEFT BANK, -B2) THREE WAY
CATALYST FUNCTION
DTC Confirmation Procedure
EC-348
Page 884 of 2395
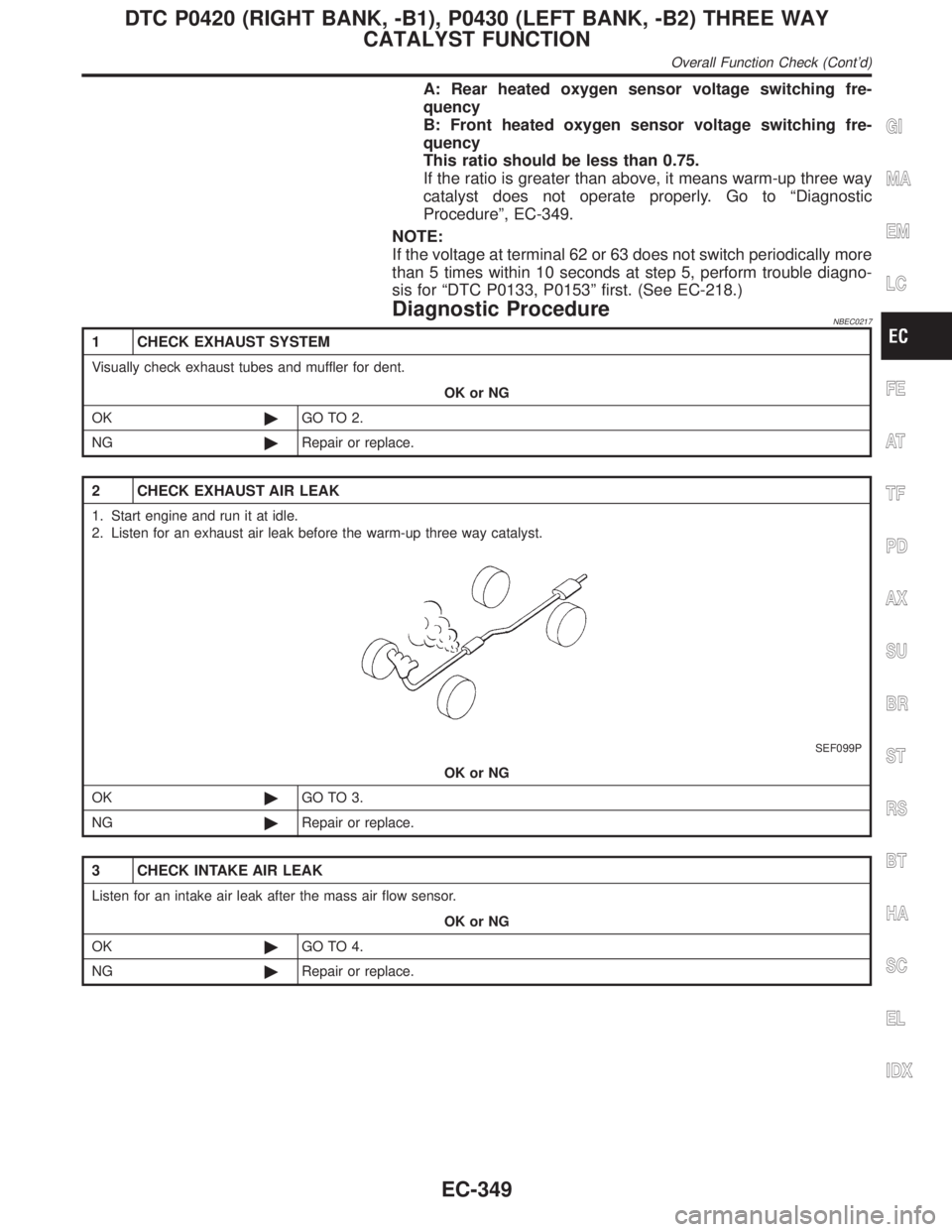
A: Rear heated oxygen sensor voltage switching fre-
quency
B: Front heated oxygen sensor voltage switching fre-
quency
This ratio should be less than 0.75.
If the ratio is greater than above, it means warm-up three way
catalyst does not operate properly. Go to ªDiagnostic
Procedureº, EC-349.
NOTE:
If the voltage at terminal 62 or 63 does not switch periodically more
than 5 times within 10 seconds at step 5, perform trouble diagno-
sis for ªDTC P0133, P0153º first. (See EC-218.)
Diagnostic ProcedureNBEC0217
1 CHECK EXHAUST SYSTEM
Visually check exhaust tubes and muffler for dent.
OK or NG
OK©GO TO 2.
NG©Repair or replace.
2 CHECK EXHAUST AIR LEAK
1. Start engine and run it at idle.
2. Listen for an exhaust air leak before the warm-up three way catalyst.
SEF099P
OK or NG
OK©GO TO 3.
NG©Repair or replace.
3 CHECK INTAKE AIR LEAK
Listen for an intake air leak after the mass air flow sensor.
OK or NG
OK©GO TO 4.
NG©Repair or replace.
GI
MA
EM
LC
FE
AT
TF
PD
AX
SU
BR
ST
RS
BT
HA
SC
EL
IDX
DTC P0420 (RIGHT BANK, -B1), P0430 (LEFT BANK, -B2) THREE WAY
CATALYST FUNCTION
Overall Function Check (Cont'd)
EC-349
Page 888 of 2395
IEVAP purge line rubber tube bent.
IBlocked or bent rubber tube to EVAP control system pressure
sensor
ILoose or disconnected rubber tube
IEVAP canister vent control valve and the circuit
IEVAP canister purge volume control solenoid valve and the
circuit
IAbsolute pressure sensor
IFuel tank temperature sensor
IO-ring of EVAP canister vent control valve is missing or dam-
aged.
IWater separator
IEVAP canister is saturated with water.
IEVAP control system pressure sensor
IFuel level sensor and the circuit
GI
MA
EM
LC
FE
AT
TF
PD
AX
SU
BR
ST
RS
BT
HA
SC
EL
IDX
DTC P0440 EVAP CONTROL SYSTEM (SMALL LEAK) (NEGATIVE PRESSURE)
Possible Cause (Cont'd)
EC-353
Page 899 of 2395
18 CHECK ABSOLUTE PRESSURE SENSOR
1. Remove absolute pressure sensor with its harness connector connected.
SEF961Y
2. Remove hose from absolute pressure sensor.
3. Install a vacuum pump to absolute pressure sensor.
4. Turn ignition switch ªONº and check output voltage between ECM terminal 80 and engine ground under the following
conditions.
SEF300XA
CAUTION:
IAlways calibrate the vacuum pump gauge when using it.
IDo not apply below þ93.3 kPa (±700 mmHg, ±27.56 inHg) or over 101.3 kPa (760 mmHg, 29.92 inHg) of pressure.
OK or NG
OK©GO TO 19.
NG©Replace absolute pressure sensor.
19 CHECK FUEL TANK TEMPERATURE SENSOR
1. Remove fuel level sensor unit.
2. Check resistance between fuel level sensor unit and fuel pump terminals 1 and 2 by heating with hot water or heat gun
as shown in the figure.
SEF974Y
OK or NG
OK©GO TO 20.
NG©Replace fuel level sensor unit.
DTC P0440 EVAP CONTROL SYSTEM (SMALL LEAK) (NEGATIVE PRESSURE)
Diagnostic Procedure (Cont'd)
EC-364
Page 900 of 2395
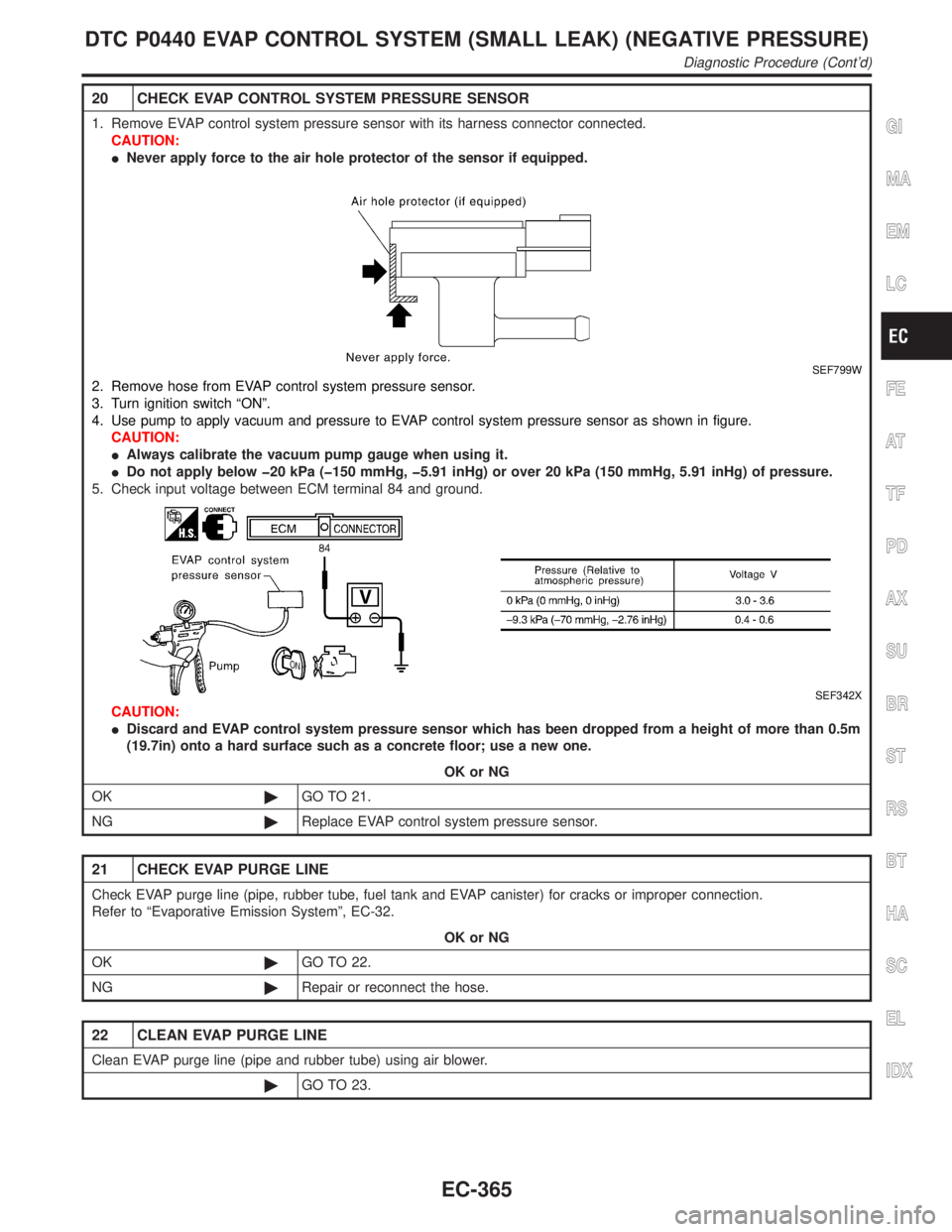
20 CHECK EVAP CONTROL SYSTEM PRESSURE SENSOR
1. Remove EVAP control system pressure sensor with its harness connector connected.
CAUTION:
INever apply force to the air hole protector of the sensor if equipped.
SEF799W
2. Remove hose from EVAP control system pressure sensor.
3. Turn ignition switch ªONº.
4. Use pump to apply vacuum and pressure to EVAP control system pressure sensor as shown in figure.
CAUTION:
IAlways calibrate the vacuum pump gauge when using it.
IDo not apply below þ20 kPa (þ150 mmHg, þ5.91 inHg) or over 20 kPa (150 mmHg, 5.91 inHg) of pressure.
5. Check input voltage between ECM terminal 84 and ground.
SEF342X
CAUTION:
IDiscard and EVAP control system pressure sensor which has been dropped from a height of more than 0.5m
(19.7in) onto a hard surface such as a concrete floor; use a new one.
OK or NG
OK©GO TO 21.
NG©Replace EVAP control system pressure sensor.
21 CHECK EVAP PURGE LINE
Check EVAP purge line (pipe, rubber tube, fuel tank and EVAP canister) for cracks or improper connection.
Refer to ªEvaporative Emission Systemº, EC-32.
OK or NG
OK©GO TO 22.
NG©Repair or reconnect the hose.
22 CLEAN EVAP PURGE LINE
Clean EVAP purge line (pipe and rubber tube) using air blower.
©GO TO 23.
GI
MA
EM
LC
FE
AT
TF
PD
AX
SU
BR
ST
RS
BT
HA
SC
EL
IDX
DTC P0440 EVAP CONTROL SYSTEM (SMALL LEAK) (NEGATIVE PRESSURE)
Diagnostic Procedure (Cont'd)
EC-365