Page 216 of 557
6-1-60 ENGINE GENERAL INFORMATION AND DIAGNOSIS (SFI FOR G13)
To other sensor
Main
fuseIgnition
switch
Heater
To HO2S-1
heater
DTC P0136 HEATED OXYGEN SENSOR (HO2S) CIRCUIT MALFUNCTION
(SENSOR-2)
CIRCUIT DESCRIPTION
DTC DETECTING CONDITIONPOSSIBLE CAUSE
DTC will set when A or B condition is detected.
A. Max. output voltage of HO2S-2 is lower than specified value or
Min. output voltage is higher than specified value while vehicle
driving.
B. Engine is warmed up and HO2S-2 voltage is 4.5 V or more.
(circuit open)
2 driving cycle detection logic, monitoring once / 1 driving.Exhaust gas leakage
“G” or “R” circuit open or short
Heated oxygen sensor-2 malfunction
Fuel system malfunction
Page 219 of 557
ENGINE GENERAL INFORMATION AND DIAGNOSIS (SFI FOR G13) 6-1-63
To other sensor
Main
fuseIgnition
switch
Heater
To HO2S-1
heater
DTC P0141 HEATED OXYGEN SENSOR (HO2S) HEATER CIRCUIT
MALFUNCTION (SENSOR-2)
CIRCUIT DESCRIPTION
DTC DETECTING CONDITIONPOSSIBLE CAUSE
DTC will set when A or B condition it met.
A. Low voltage at terminal C02-4 for specified time after engine
start or while engine running at high load.
B. High voltage at terminal C02-4 while engine running under other
than above condition.
2 driving cycle detection logic, continuous monitoring.HO2S-2 heater circuit open or shorted
to ground
ECM (PCM) malfunction
DTC CONFIRMATION PROCEDURE
1) Turn ignition switch OFF once and then ON.
2) Clear DTC, start engine and warm up engine to normal operating temperature.
3) Keep it at 2000 r / min for 2 min.
4) Check pending DTC in “ON BOARD TEST” or “PENDING DTC” mode and DTC in “DTC” mode.
Page 220 of 557
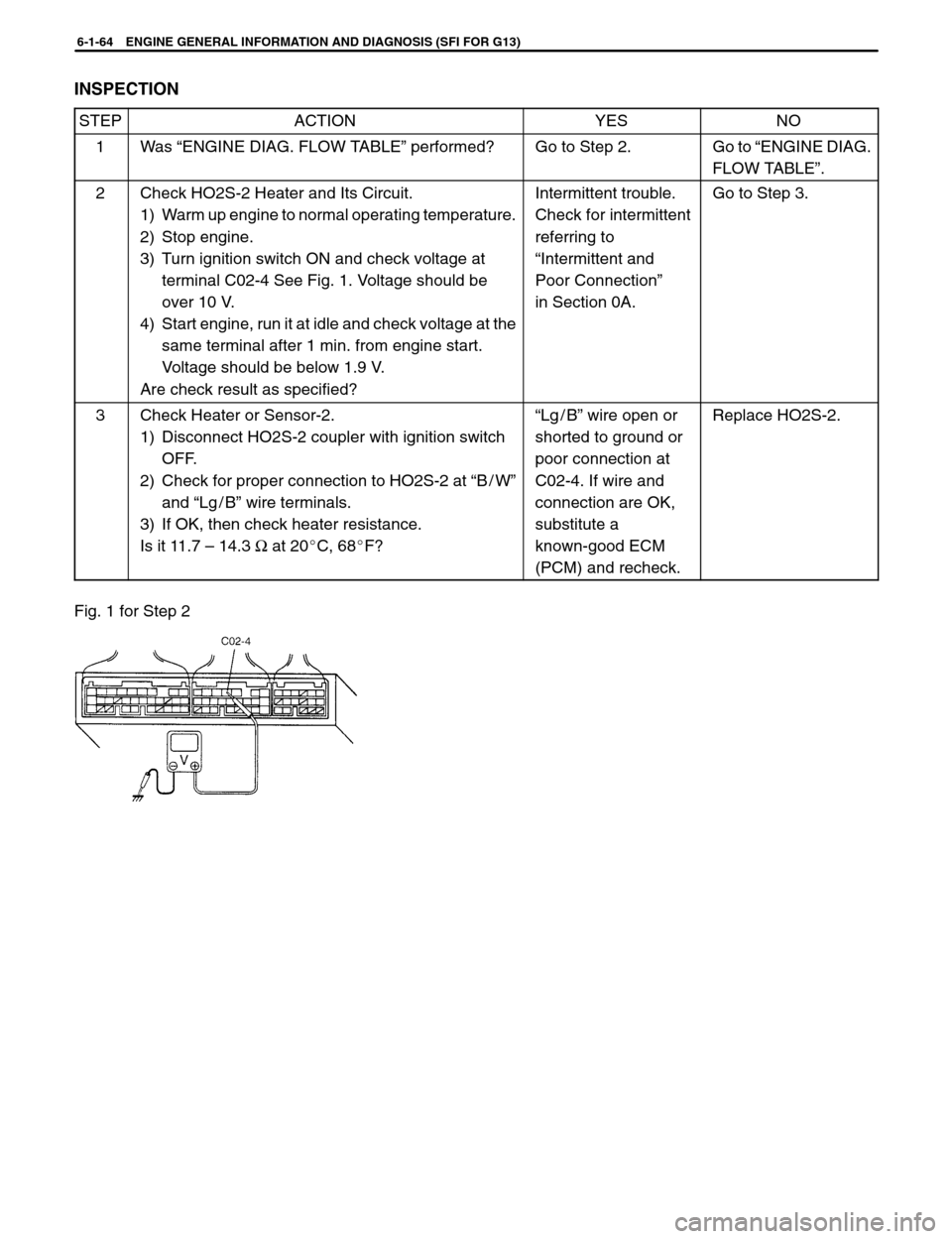
6-1-64 ENGINE GENERAL INFORMATION AND DIAGNOSIS (SFI FOR G13)
Fig. 1 for Step 2
INSPECTION
STEPACTIONYESNO
1Was “ENGINE DIAG. FLOW TABLE” performed?Go to Step 2.Go to “ENGINE DIAG.
FLOW TABLE”.
2Check HO2S-2 Heater and Its Circuit.
1) Warm up engine to normal operating temperature.
2) Stop engine.
3) Turn ignition switch ON and check voltage at
terminal C02-4 See Fig. 1. Voltage should be
over 10 V.
4) Start engine, run it at idle and check voltage at the
same terminal after 1 min. from engine start.
Voltage should be below 1.9 V.
Are check result as specified?Intermittent trouble.
Check for intermittent
referring to
“Intermittent and
Poor Connection”
in Section 0A.Go to Step 3.
3Check Heater or Sensor-2.
1) Disconnect HO2S-2 coupler with ignition switch
OFF.
2) Check for proper connection to HO2S-2 at “B/W”
and “Lg / B” wire terminals.
3) If OK, then check heater resistance.
Is it 11.7 – 14.3 Ω at 20C, 68F?“Lg / B” wire open or
shorted to ground or
poor connection at
C02-4. If wire and
connection are OK,
substitute a
known-good ECM
(PCM) and recheck.Replace HO2S-2.
Page 259 of 557
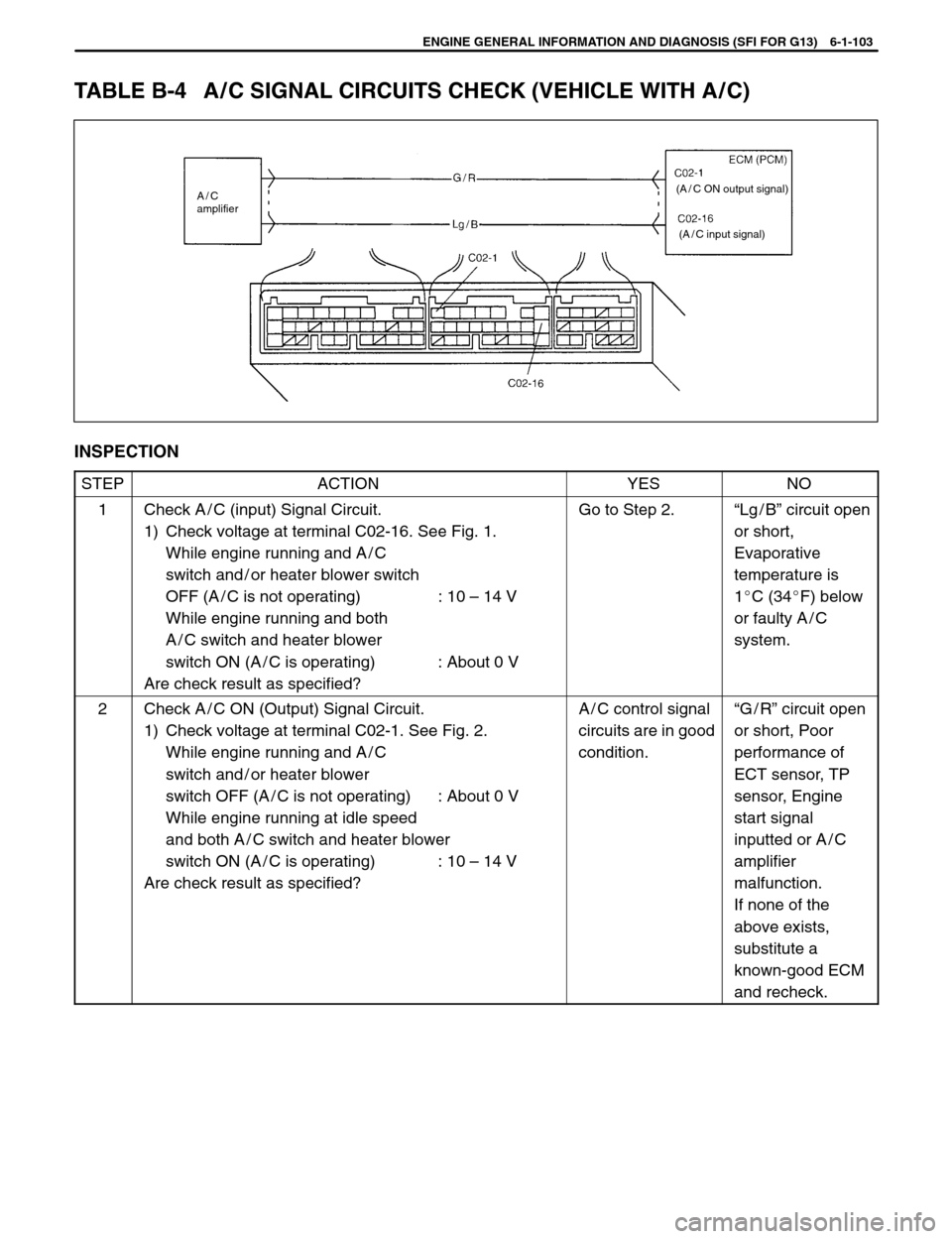
ENGINE GENERAL INFORMATION AND DIAGNOSIS (SFI FOR G13) 6-1-103
A/C
amplifier(A / C ON output signal)
(A / C input signal)
TABLE B-4 A / C SIGNAL CIRCUITS CHECK (VEHICLE WITH A / C)
INSPECTION
STEPACTIONYESNO
1Check A / C (input) Signal Circuit.
1) Check voltage at terminal C02-16. See Fig. 1.
While engine running and A / C
switch and / or heater blower switch
OFF (A / C is not operating) : 10 – 14 V
While engine running and both
A / C switch and heater blower
switch ON (A / C is operating) : About 0 V
Are check result as specified?Go to Step 2.“Lg / B” circuit open
or short,
Evaporative
temperature is
1C (34F) below
or faulty A / C
system.
2Check A / C ON (Output) Signal Circuit.
1) Check voltage at terminal C02-1. See Fig. 2.
While engine running and A / C
switch and / or heater blower
switch OFF (A / C is not operating) : About 0 V
While engine running at idle speed
and both A / C switch and heater blower
switch ON (A / C is operating) : 10 – 14 V
Are check result as specified?A / C control signal
circuits are in good
condition.“G/R” circuit open
or short, Poor
performance of
ECT sensor, TP
sensor, Engine
start signal
inputted or A / C
amplifier
malfunction.
If none of the
above exists,
substitute a
known-good ECM
and recheck.
Page 261 of 557
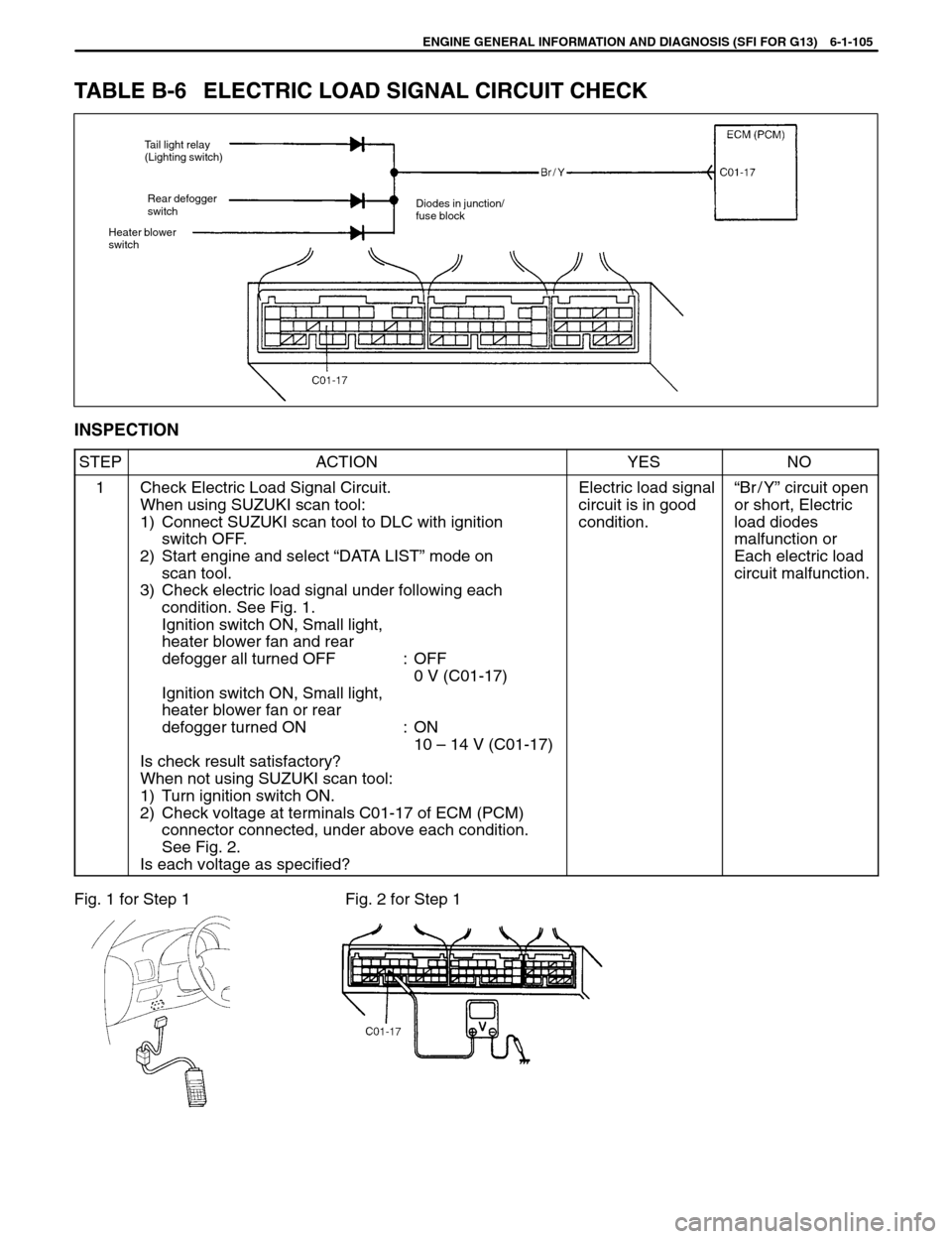
ENGINE GENERAL INFORMATION AND DIAGNOSIS (SFI FOR G13) 6-1-105
Heater blower
switchRear defogger
switch Tail light relay
(Lighting switch)
Diodes in junction/
fuse block
Fig. 1 for Step 1 Fig. 2 for Step 1
TABLE B-6 ELECTRIC LOAD SIGNAL CIRCUIT CHECK
INSPECTION
STEPACTIONYESNO
1Check Electric Load Signal Circuit.
When using SUZUKI scan tool:
1) Connect SUZUKI scan tool to DLC with ignition
switch OFF.
2) Start engine and select “DATA LIST” mode on
scan tool.
3) Check electric load signal under following each
condition. See Fig. 1.
Ignition switch ON, Small light,
heater blower fan and rear
defogger all turned OFF : OFF
0 V (C01-17)
Ignition switch ON, Small light,
heater blower fan or rear
defogger turned ON : ON
10 – 14 V (C01-17)
Is check result satisfactory?
When not using SUZUKI scan tool:
1) Turn ignition switch ON.
2) Check voltage at terminals C01-17 of ECM (PCM)
connector connected, under above each condition.
See Fig. 2.
Is each voltage as specified?Electric load signal
circuit is in good
condition.“Br / Y” circuit open
or short, Electric
load diodes
malfunction or
Each electric load
circuit malfunction.
Page 269 of 557
1. Stay
2. Throttle body
3. Gasket
4. EFE heater
5. Intake manifold
6. Gasket : Tightening Torque
: Do not reuse
ENGINE MECHANICAL (G10, 1-CAM 6-VALVES ENGINE) 6A-5
THROTTLE BODY AND INTAKE MANIFOLD
REMOVAL
1) Relieve fuel pressure according to procedure described in
“FUEL PRESSURE RELIEF PROCEDURE” of Section 6.
2) Disconnect negative cable at battery.
3) Drain cooling system.
WARNING:
To help avoid danger of being burned, do not remove
drain plug (2) and radiator cap while engine and radiator
(1) are still hot. Scalding fluid and steam can be blown out
under pressure if plug and cap are taken off too soon.
Page 270 of 557
1. Throttle body
1. Throttle body
2. ISC actuator
5. Clamp
6A-6 ENGINE MECHANICAL (G10, 1-CAM 6-VALVES ENGINE)
4) Remove air cleaner assembly.
5) Disconnect the following electric lead wires:
EGR valve
ISC actuator (2)
Ground wires from intake manifold
Fuel injector (4)
TP sensor (3)
EFE heater (5)
Engine coolant temp. gauge
6) Disconnect fuel return (4) and feed hoses (3) from fuel pipes.
7) Disconnect coolant hoses from intake manifold.
8) Disconnect the following vacuum hoses.
Canister purge hose from intake manifold.
EGR pressure transducer hoses from EGR valve.
EGR valve hose from EGR valve.
Pressure sensor hose from intake manifold.
Brake booster hose from intake manifold.
9) Disconnect breather hose from PCV valve.
10) Disconnect accelerator cable from throttle body.
11) Disconnect other connected to throttle body and intake man-
ifold, if any.
12) Remove intake manifold with throttle body from cylinder head.
13) Remove throttle body from intake manifold.
Page 271 of 557
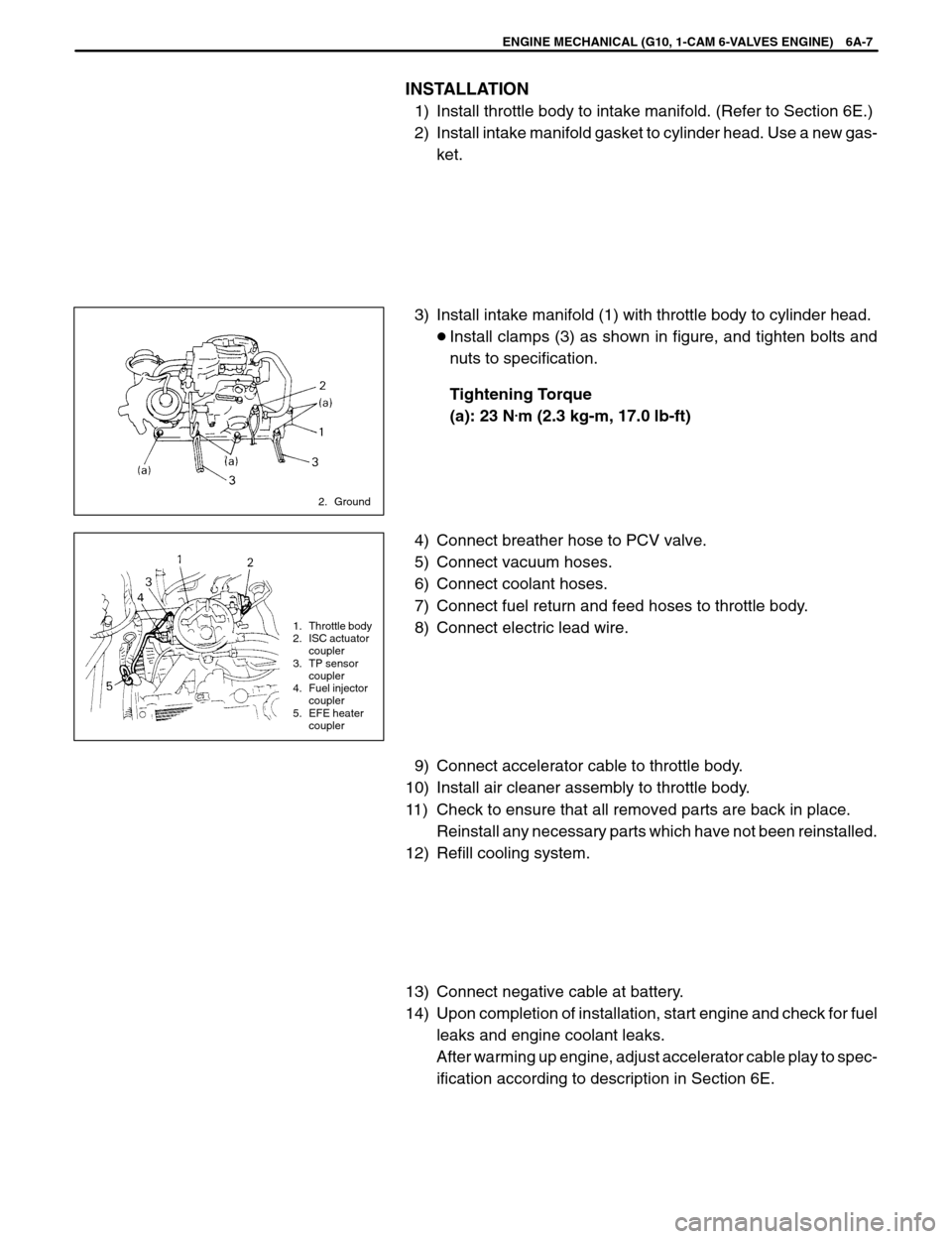
2. Ground
1. Throttle body
2. ISC actuator
coupler
3. TP sensor
coupler
4. Fuel injector
coupler
5. EFE heater
coupler
ENGINE MECHANICAL (G10, 1-CAM 6-VALVES ENGINE) 6A-7
INSTALLATION
1) Install throttle body to intake manifold. (Refer to Section 6E.)
2) Install intake manifold gasket to cylinder head. Use a new gas-
ket.
3) Install intake manifold (1) with throttle body to cylinder head.
Install clamps (3) as shown in figure, and tighten bolts and
nuts to specification.
Tightening Torque
(a): 23 N
.m (2.3 kg-m, 17.0 lb-ft)
4) Connect breather hose to PCV valve.
5) Connect vacuum hoses.
6) Connect coolant hoses.
7) Connect fuel return and feed hoses to throttle body.
8) Connect electric lead wire.
9) Connect accelerator cable to throttle body.
10) Install air cleaner assembly to throttle body.
11) Check to ensure that all removed parts are back in place.
Reinstall any necessary parts which have not been reinstalled.
12) Refill cooling system.
13) Connect negative cable at battery.
14) Upon completion of installation, start engine and check for fuel
leaks and engine coolant leaks.
After warming up engine, adjust accelerator cable play to spec-
ification according to description in Section 6E.