Page 413 of 557
6E1-22 ENGINE AND EMISSION CONTROL SYSTEM (TBI FOR G10)
( ) for reference kΩ
TEMPERATURE 0
3220
6840
10460
14080C
176F (5.74)
2.28–2.61
(1.15)
(0.584)
0.303–0.326
1. ECT sensor
2. Distributor
INSPECTION
Immerse temperature sensing part of ECT sensor in water (or ice)
and measure resistance between sensor terminals while heating
water gradually.
If measured resistance doesn’t show such characteristic as shown
in left figure, replace ECT sensor.
INSTALLATION
Reverse removal procedure noting the following.
Clean mating surfaces of ECT sensor and thermostat case.
Check O-ring for damage and replace if necessary.
Tighten ECT sensor to specified torque.
Tightening Torque
(a): 15 N
.m (1.5 kg-m, 11.0 lb-ft)
Connect coupler to ECT sensor securely.
Refill coolant referring to Section 6B.
Page 414 of 557
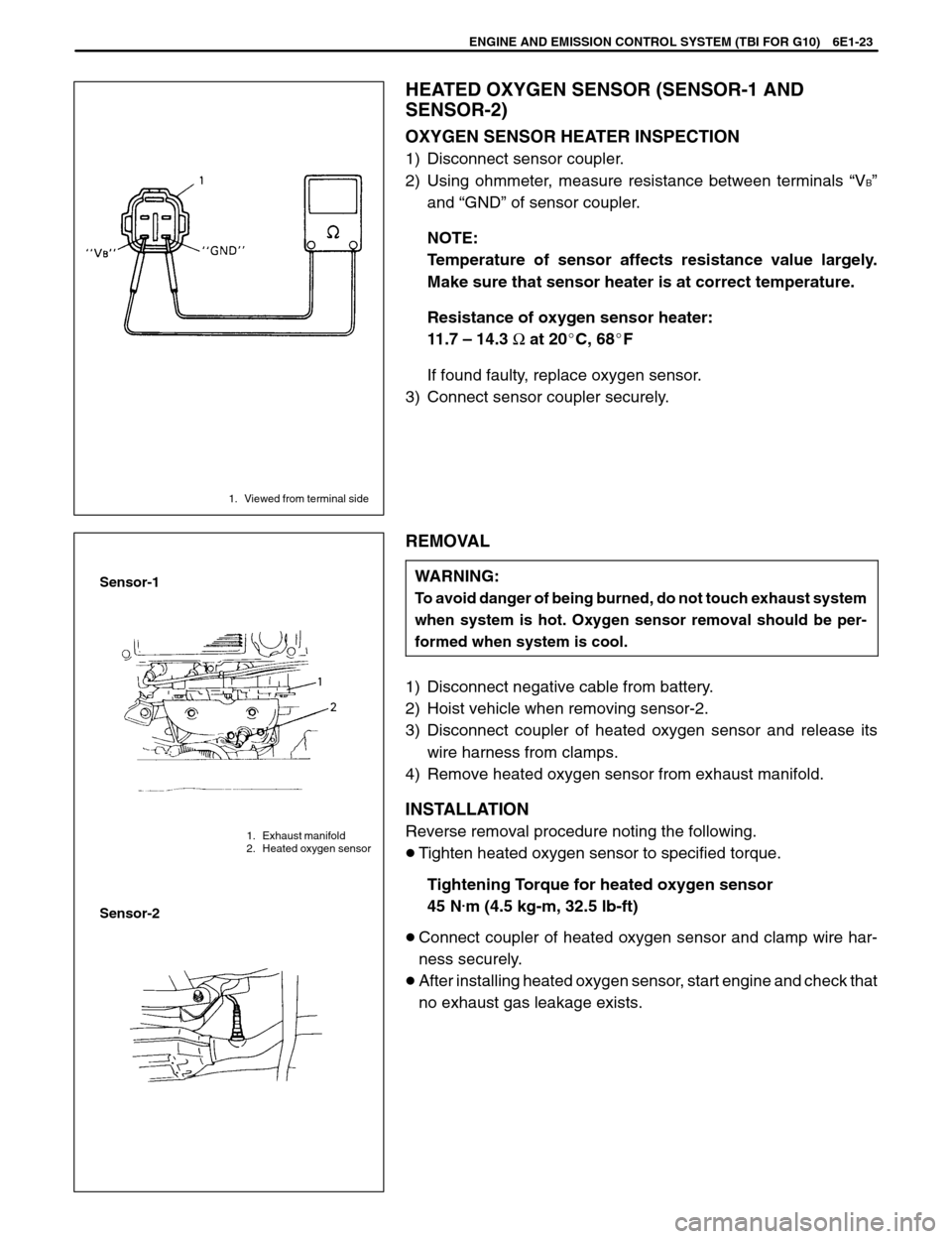
ENGINE AND EMISSION CONTROL SYSTEM (TBI FOR G10) 6E1-23
1. Viewed from terminal side
1. Exhaust manifold
2. Heated oxygen sensor
Sensor-1
Sensor-2
HEATED OXYGEN SENSOR (SENSOR-1 AND
SENSOR-2)
OXYGEN SENSOR HEATER INSPECTION
1) Disconnect sensor coupler.
2) Using ohmmeter, measure resistance between terminals “V
B”
and “GND” of sensor coupler.
NOTE:
Temperature of sensor affects resistance value largely.
Make sure that sensor heater is at correct temperature.
Resistance of oxygen sensor heater:
11.7 – 14.3 Ω at 20C, 68F
If found faulty, replace oxygen sensor.
3) Connect sensor coupler securely.
REMOVAL
WARNING:
To avoid danger of being burned, do not touch exhaust system
when system is hot. Oxygen sensor removal should be per-
formed when system is cool.
1) Disconnect negative cable from battery.
2) Hoist vehicle when removing sensor-2.
3) Disconnect coupler of heated oxygen sensor and release its
wire harness from clamps.
4) Remove heated oxygen sensor from exhaust manifold.
INSTALLATION
Reverse removal procedure noting the following.
Tighten heated oxygen sensor to specified torque.
Tightening Torque for heated oxygen sensor
45 N
.m (4.5 kg-m, 32.5 lb-ft)
Connect coupler of heated oxygen sensor and clamp wire har-
ness securely.
After installing heated oxygen sensor, start engine and check that
no exhaust gas leakage exists.
Page 415 of 557
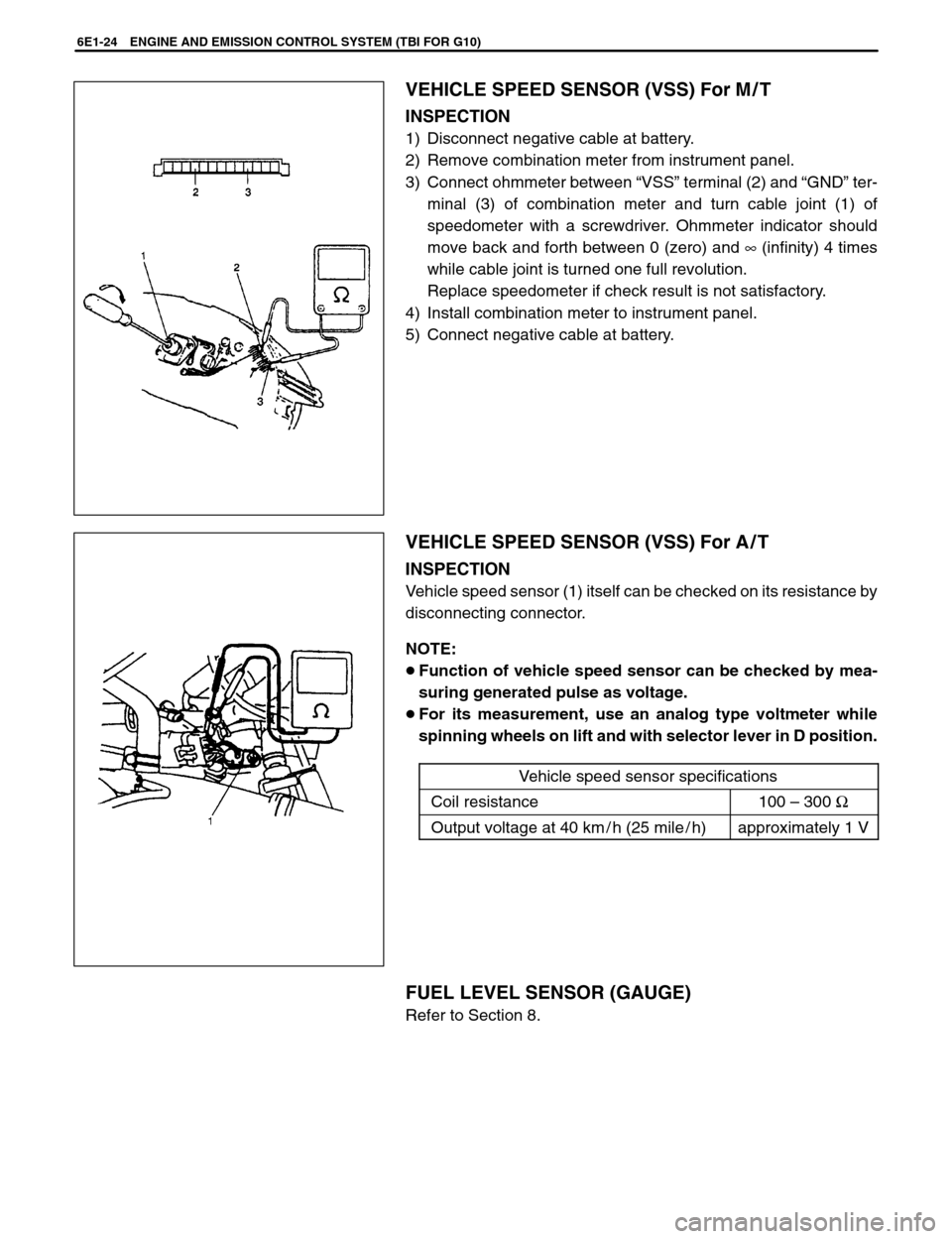
6E1-24 ENGINE AND EMISSION CONTROL SYSTEM (TBI FOR G10)
VEHICLE SPEED SENSOR (VSS) For M / T
INSPECTION
1) Disconnect negative cable at battery.
2) Remove combination meter from instrument panel.
3) Connect ohmmeter between “VSS” terminal (2) and “GND” ter-
minal (3) of combination meter and turn cable joint (1) of
speedometer with a screwdriver. Ohmmeter indicator should
move back and forth between 0 (zero) and ∞ (infinity) 4 times
while cable joint is turned one full revolution.
Replace speedometer if check result is not satisfactory.
4) Install combination meter to instrument panel.
5) Connect negative cable at battery.
VEHICLE SPEED SENSOR (VSS) For A / T
INSPECTION
Vehicle speed sensor (1) itself can be checked on its resistance by
disconnecting connector.
NOTE:
Function of vehicle speed sensor can be checked by mea-
suring generated pulse as voltage.
For its measurement, use an analog type voltmeter while
spinning wheels on lift and with selector lever in D position.
Vehicle speed sensor specifications
Coil resistance100 – 300 Ω
Output voltage at 40 km / h (25 mile / h)approximately 1 V
FUEL LEVEL SENSOR (GAUGE)
Refer to Section 8.
Page 416 of 557
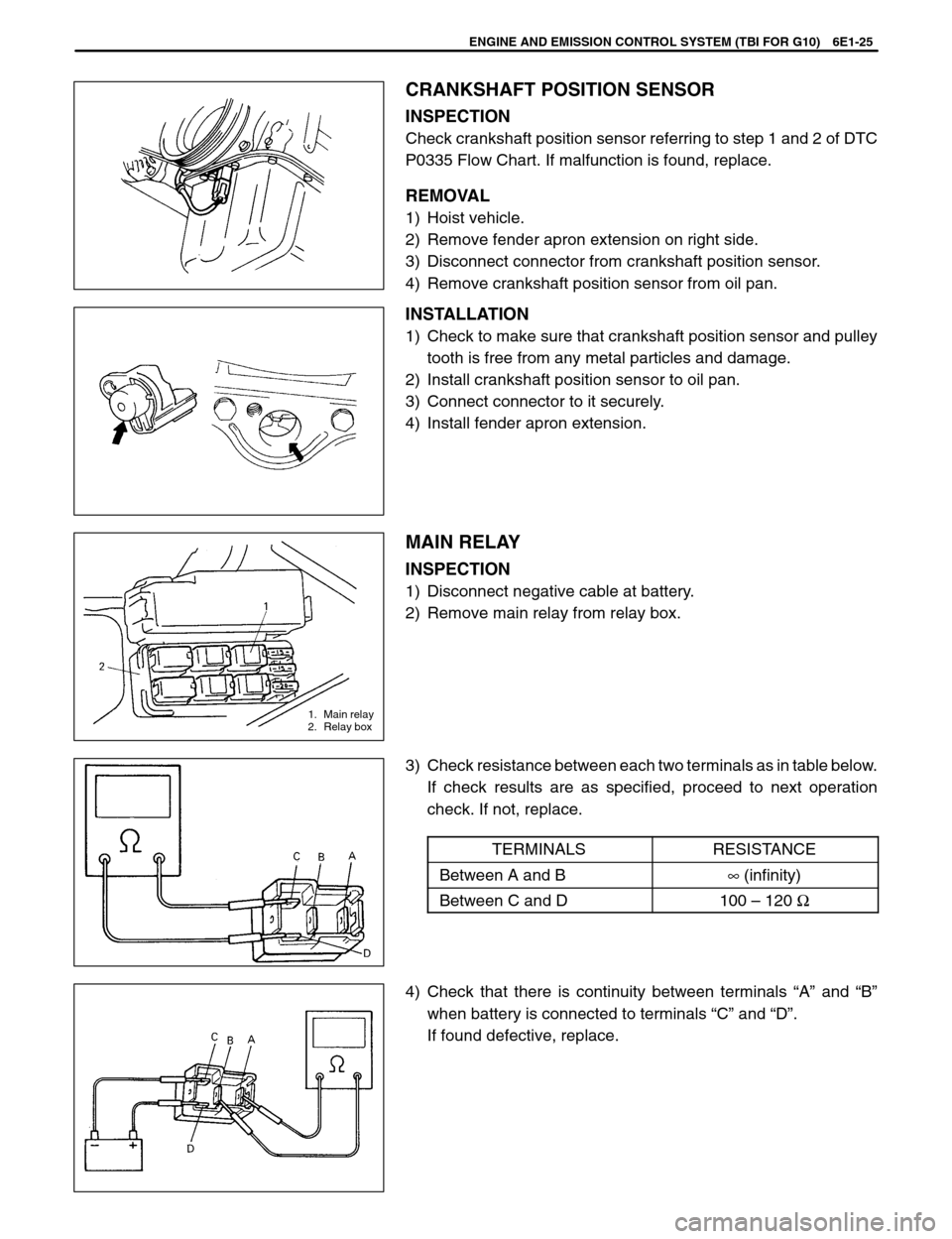
ENGINE AND EMISSION CONTROL SYSTEM (TBI FOR G10) 6E1-25
1. Main relay
2. Relay box
CRANKSHAFT POSITION SENSOR
INSPECTION
Check crankshaft position sensor referring to step 1 and 2 of DTC
P0335 Flow Chart. If malfunction is found, replace.
REMOVAL
1) Hoist vehicle.
2) Remove fender apron extension on right side.
3) Disconnect connector from crankshaft position sensor.
4) Remove crankshaft position sensor from oil pan.
INSTALLATION
1) Check to make sure that crankshaft position sensor and pulley
tooth is free from any metal particles and damage.
2) Install crankshaft position sensor to oil pan.
3) Connect connector to it securely.
4) Install fender apron extension.
MAIN RELAY
INSPECTION
1) Disconnect negative cable at battery.
2) Remove main relay from relay box.
3) Check resistance between each two terminals as in table below.
If check results are as specified, proceed to next operation
check. If not, replace.
TERMINALS
RESISTANCE
Between A and B∞ (infinity)
Between C and D100 – 120 Ω
4) Check that there is continuity between terminals “A” and “B”
when battery is connected to terminals “C” and “D”.
If found defective, replace.
Page 417 of 557
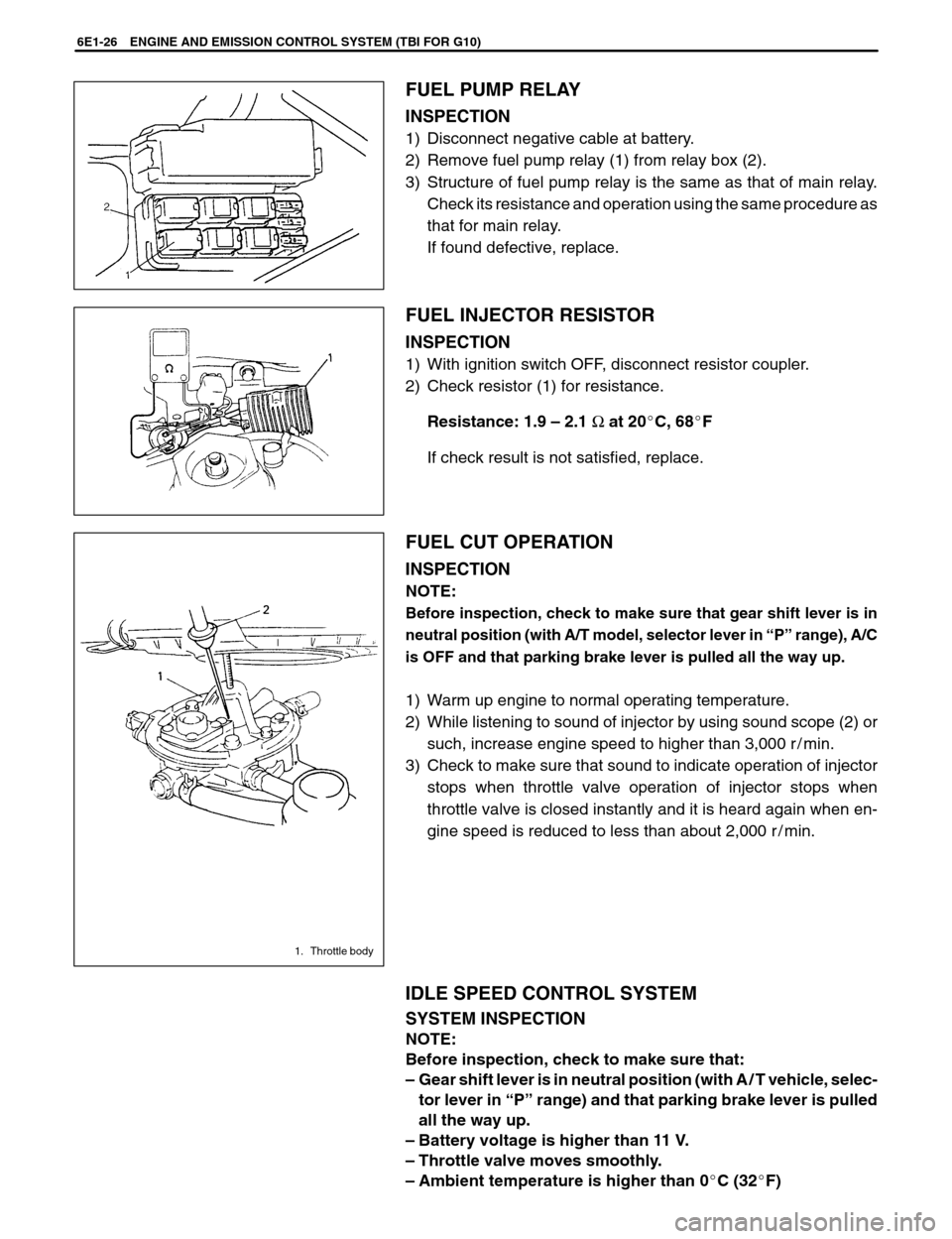
6E1-26 ENGINE AND EMISSION CONTROL SYSTEM (TBI FOR G10)
1. Throttle body
FUEL PUMP RELAY
INSPECTION
1) Disconnect negative cable at battery.
2) Remove fuel pump relay (1) from relay box (2).
3) Structure of fuel pump relay is the same as that of main relay.
Check its resistance and operation using the same procedure as
that for main relay.
If found defective, replace.
FUEL INJECTOR RESISTOR
INSPECTION
1) With ignition switch OFF, disconnect resistor coupler.
2) Check resistor (1) for resistance.
Resistance: 1.9 – 2.1 Ω at 20C, 68F
If check result is not satisfied, replace.
FUEL CUT OPERATION
INSPECTION
NOTE:
Before inspection, check to make sure that gear shift lever is in
neutral position (with A/T model, selector lever in “P” range), A/C
is OFF and that parking brake lever is pulled all the way up.
1) Warm up engine to normal operating temperature.
2) While listening to sound of injector by using sound scope (2) or
such, increase engine speed to higher than 3,000 r / min.
3) Check to make sure that sound to indicate operation of injector
stops when throttle valve operation of injector stops when
throttle valve is closed instantly and it is heard again when en-
gine speed is reduced to less than about 2,000 r / min.
IDLE SPEED CONTROL SYSTEM
SYSTEM INSPECTION
NOTE:
Before inspection, check to make sure that:
–Gear shift lever is in neutral position (with A / T vehicle, selec-
tor lever in “P” range) and that parking brake lever is pulled
all the way up.
–Battery voltage is higher than 11 V.
–Throttle valve moves smoothly.
–Ambient temperature is higher than 0C (32F)
Page 418 of 557
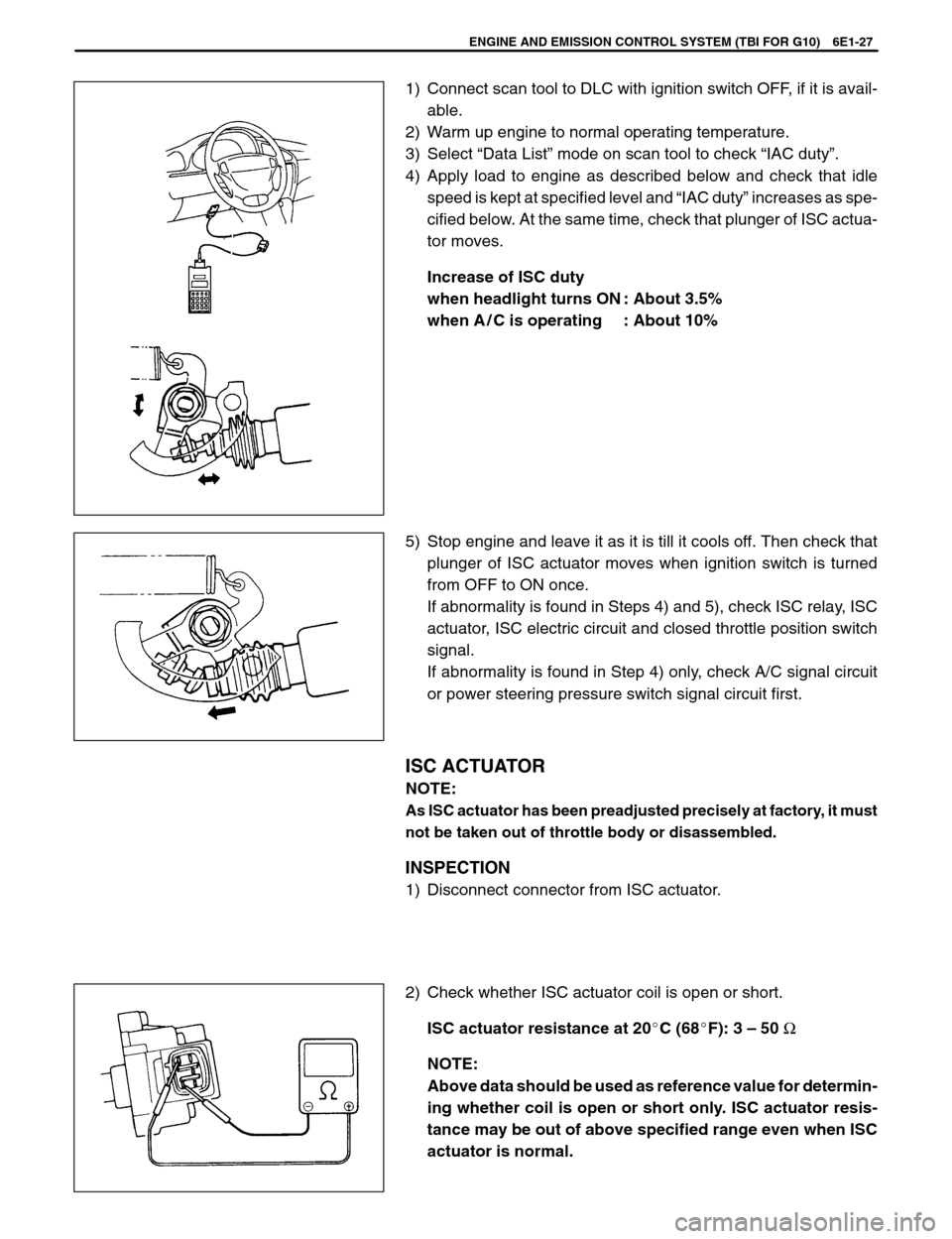
ENGINE AND EMISSION CONTROL SYSTEM (TBI FOR G10) 6E1-27
1) Connect scan tool to DLC with ignition switch OFF, if it is avail-
able.
2) Warm up engine to normal operating temperature.
3) Select “Data List” mode on scan tool to check “IAC duty”.
4) Apply load to engine as described below and check that idle
speed is kept at specified level and “IAC duty” increases as spe-
cified below. At the same time, check that plunger of ISC actua-
tor moves.
Increase of ISC duty
when headlight turns ON : About 3.5%
when A / C is operating : About 10%
5) Stop engine and leave it as it is till it cools off. Then check that
plunger of ISC actuator moves when ignition switch is turned
from OFF to ON once.
If abnormality is found in Steps 4) and 5), check ISC relay, ISC
actuator, ISC electric circuit and closed throttle position switch
signal.
If abnormality is found in Step 4) only, check A/C signal circuit
or power steering pressure switch signal circuit first.
ISC ACTUATOR
NOTE:
As ISC actuator has been preadjusted precisely at factory, it must
not be taken out of throttle body or disassembled.
INSPECTION
1) Disconnect connector from ISC actuator.
2) Check whether ISC actuator coil is open or short.
ISC actuator resistance at 20C (68F): 3 – 50 Ω
NOTE:
Above data should be used as reference value for determin-
ing whether coil is open or short only. ISC actuator resis-
tance may be out of above specified range even when ISC
actuator is normal.
Page 419 of 557
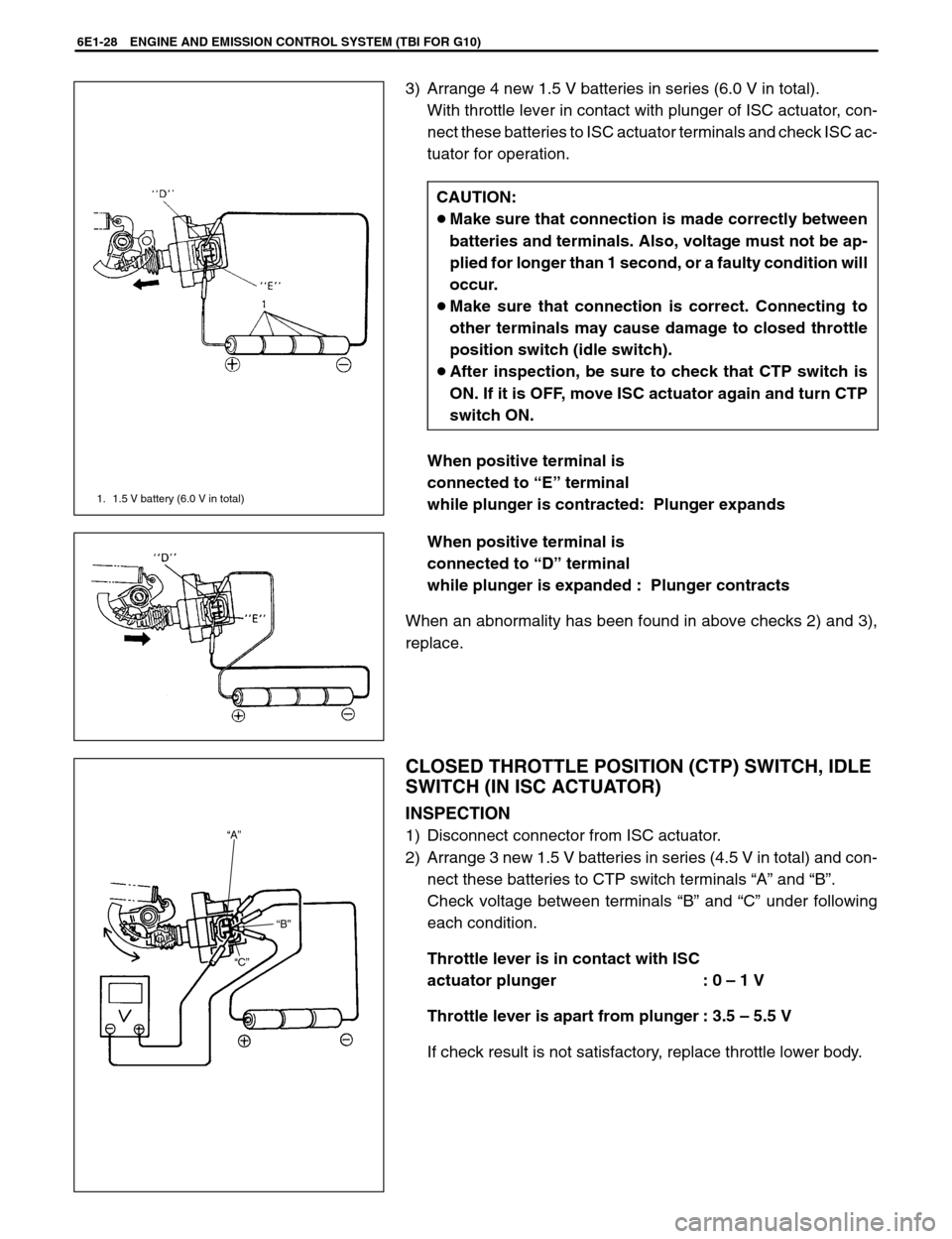
6E1-28 ENGINE AND EMISSION CONTROL SYSTEM (TBI FOR G10)
1. 1.5 V battery (6.0 V in total)
“A”
“B”
“C”
3) Arrange 4 new 1.5 V batteries in series (6.0 V in total).
With throttle lever in contact with plunger of ISC actuator, con-
nect these batteries to ISC actuator terminals and check ISC ac-
tuator for operation.
CAUTION:
Make sure that connection is made correctly between
batteries and terminals. Also, voltage must not be ap-
plied for longer than 1 second, or a faulty condition will
occur.
Make sure that connection is correct. Connecting to
other terminals may cause damage to closed throttle
position switch (idle switch).
After inspection, be sure to check that CTP switch is
ON. If it is OFF, move ISC actuator again and turn CTP
switch ON.
When positive terminal is
connected to “E” terminal
while plunger is contracted: Plunger expands
When positive terminal is
connected to “D” terminal
while plunger is expanded : Plunger contracts
When an abnormality has been found in above checks 2) and 3),
replace.
CLOSED THROTTLE POSITION (CTP) SWITCH, IDLE
SWITCH (IN ISC ACTUATOR)
INSPECTION
1) Disconnect connector from ISC actuator.
2) Arrange 3 new 1.5 V batteries in series (4.5 V in total) and con-
nect these batteries to CTP switch terminals “A” and “B”.
Check voltage between terminals “B” and “C” under following
each condition.
Throttle lever is in contact with ISC
actuator plunger : 0 – 1 V
Throttle lever is apart from plunger : 3.5 – 5.5 V
If check result is not satisfactory, replace throttle lower body.
Page 420 of 557
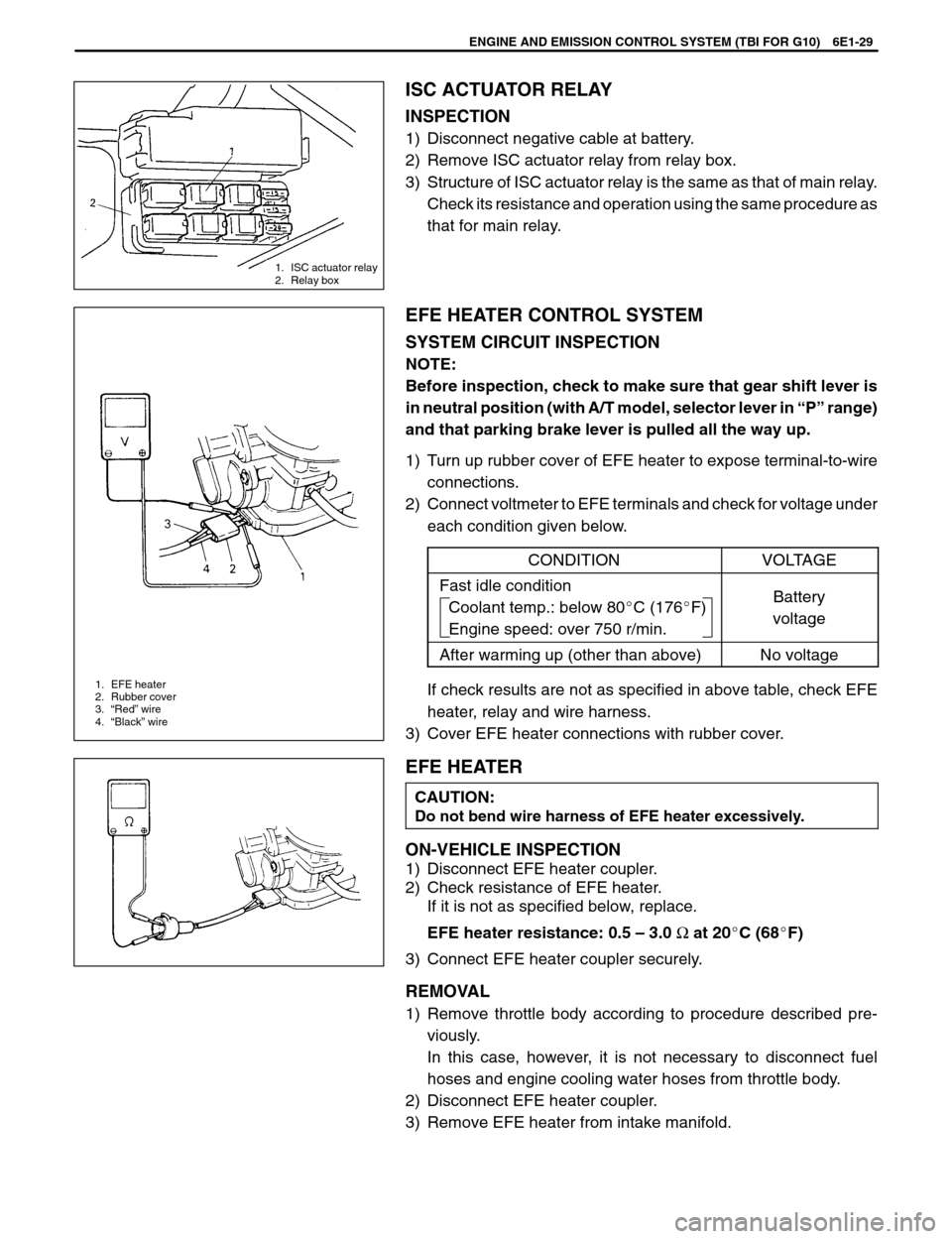
ENGINE AND EMISSION CONTROL SYSTEM (TBI FOR G10) 6E1-29
1. ISC actuator relay
2. Relay box
1. EFE heater
2. Rubber cover
3.“Red” wire
4.“Black” wire
ISC ACTUATOR RELAY
INSPECTION
1) Disconnect negative cable at battery.
2) Remove ISC actuator relay from relay box.
3) Structure of ISC actuator relay is the same as that of main relay.
Check its resistance and operation using the same procedure as
that for main relay.
EFE HEATER CONTROL SYSTEM
SYSTEM CIRCUIT INSPECTION
NOTE:
Before inspection, check to make sure that gear shift lever is
in neutral position (with A/T model, selector lever in “P” range)
and that parking brake lever is pulled all the way up.
1) Turn up rubber cover of EFE heater to expose terminal-to-wire
connections.
2) Connect voltmeter to EFE terminals and check for voltage under
each condition given below.
CONDITION
VOLTAGE
Fast idle condition
Coolant temp.: below 80C (176F)
Engine speed: over 750 r/min.Battery
voltage
After warming up (other than above)No voltage
If check results are not as specified in above table, check EFE
heater, relay and wire harness.
3) Cover EFE heater connections with rubber cover.
EFE HEATER
CAUTION:
Do not bend wire harness of EFE heater excessively.
ON-VEHICLE INSPECTION
1) Disconnect EFE heater coupler.
2) Check resistance of EFE heater.
If it is not as specified below, replace.
EFE heater resistance: 0.5 – 3.0 Ω at 20C (68F)
3) Connect EFE heater coupler securely.
REMOVAL
1) Remove throttle body according to procedure described pre-
viously.
In this case, however, it is not necessary to disconnect fuel
hoses and engine cooling water hoses from throttle body.
2) Disconnect EFE heater coupler.
3) Remove EFE heater from intake manifold.