Page 442 of 557
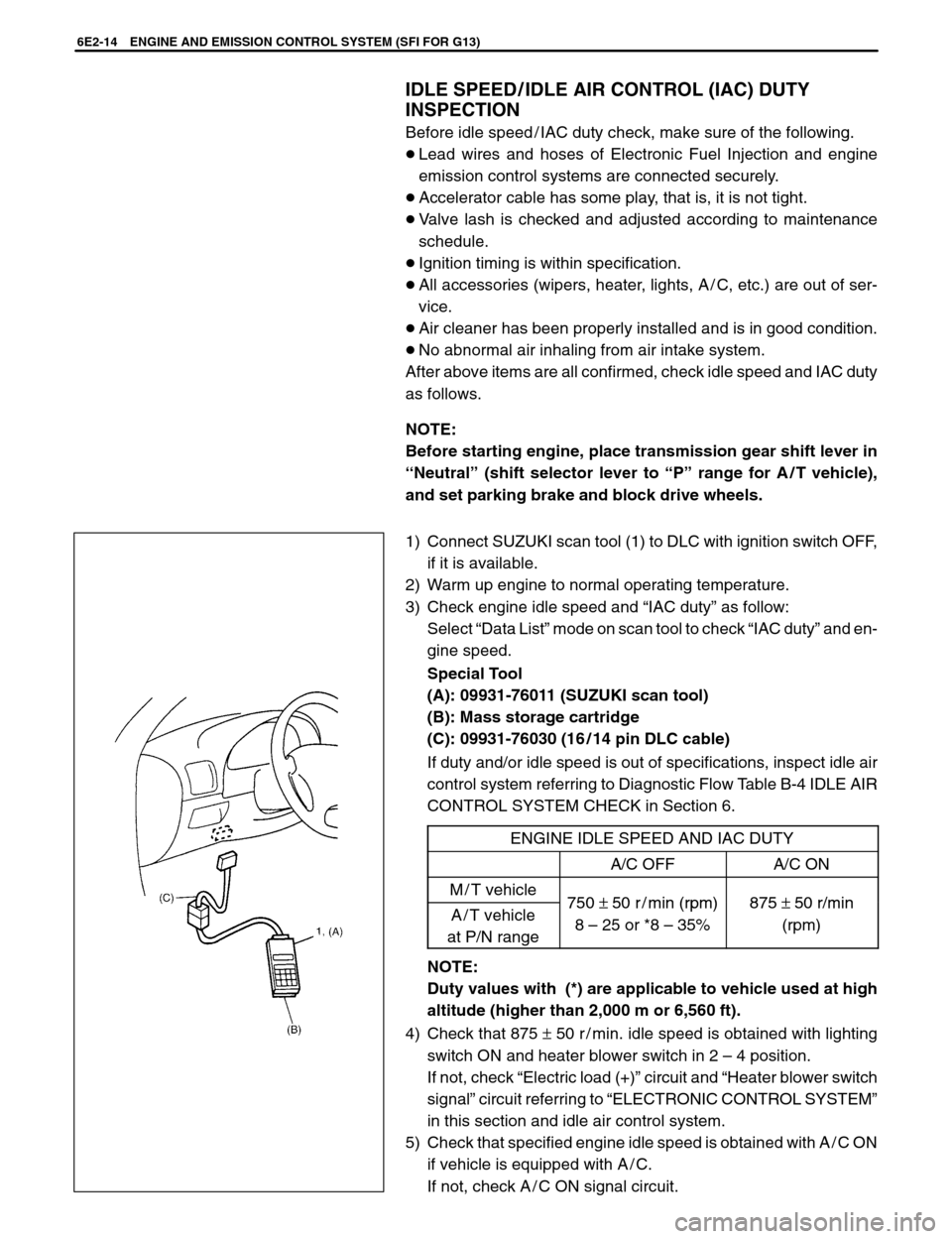
6E2-14 ENGINE AND EMISSION CONTROL SYSTEM (SFI FOR G13)
IDLE SPEED / IDLE AIR CONTROL (IAC) DUTY
INSPECTION
Before idle speed / IAC duty check, make sure of the following.
Lead wires and hoses of Electronic Fuel Injection and engine
emission control systems are connected securely.
Accelerator cable has some play, that is, it is not tight.
Valve lash is checked and adjusted according to maintenance
schedule.
Ignition timing is within specification.
All accessories (wipers, heater, lights, A / C, etc.) are out of ser-
vice.
Air cleaner has been properly installed and is in good condition.
No abnormal air inhaling from air intake system.
After above items are all confirmed, check idle speed and IAC duty
as follows.
NOTE:
Before starting engine, place transmission gear shift lever in
“Neutral” (shift selector lever to “P” range for A / T vehicle),
and set parking brake and block drive wheels.
1) Connect SUZUKI scan tool (1) to DLC with ignition switch OFF,
if it is available.
2) Warm up engine to normal operating temperature.
3) Check engine idle speed and “IAC duty” as follow:
Select “Data List” mode on scan tool to check “IAC duty” and en-
gine speed.
Special Tool
(A): 09931-76011 (SUZUKI scan tool)
(B): Mass storage cartridge
(C): 09931-76030 (16 / 14 pin DLC cable)
If duty and/or idle speed is out of specifications, inspect idle air
control system referring to Diagnostic Flow Table B-4 IDLE AIR
CONTROL SYSTEM CHECK in Section 6.
ENGINE IDLE SPEED AND IAC DUTY
A/C OFFA/C ON
M / T vehicle750±50 r / min (rpm)875±50 r/minA / T vehicle
at P/N range750 ±50 r/min (rpm)
8 – 25 or *8 – 35%
875 ±50 r/min
(rpm)
NOTE:
Duty values with (*) are applicable to vehicle used at high
altitude (higher than 2,000 m or 6,560 ft).
4) Check that 875 ± 50 r / min. idle speed is obtained with lighting
switch ON and heater blower switch in 2 – 4 position.
If not, check “Electric load (+)” circuit and “Heater blower switch
signal” circuit referring to “ELECTRONIC CONTROL SYSTEM”
in this section and idle air control system.
5) Check that specified engine idle speed is obtained with A / C ON
if vehicle is equipped with A / C.
If not, check A / C ON signal circuit.
Page 445 of 557
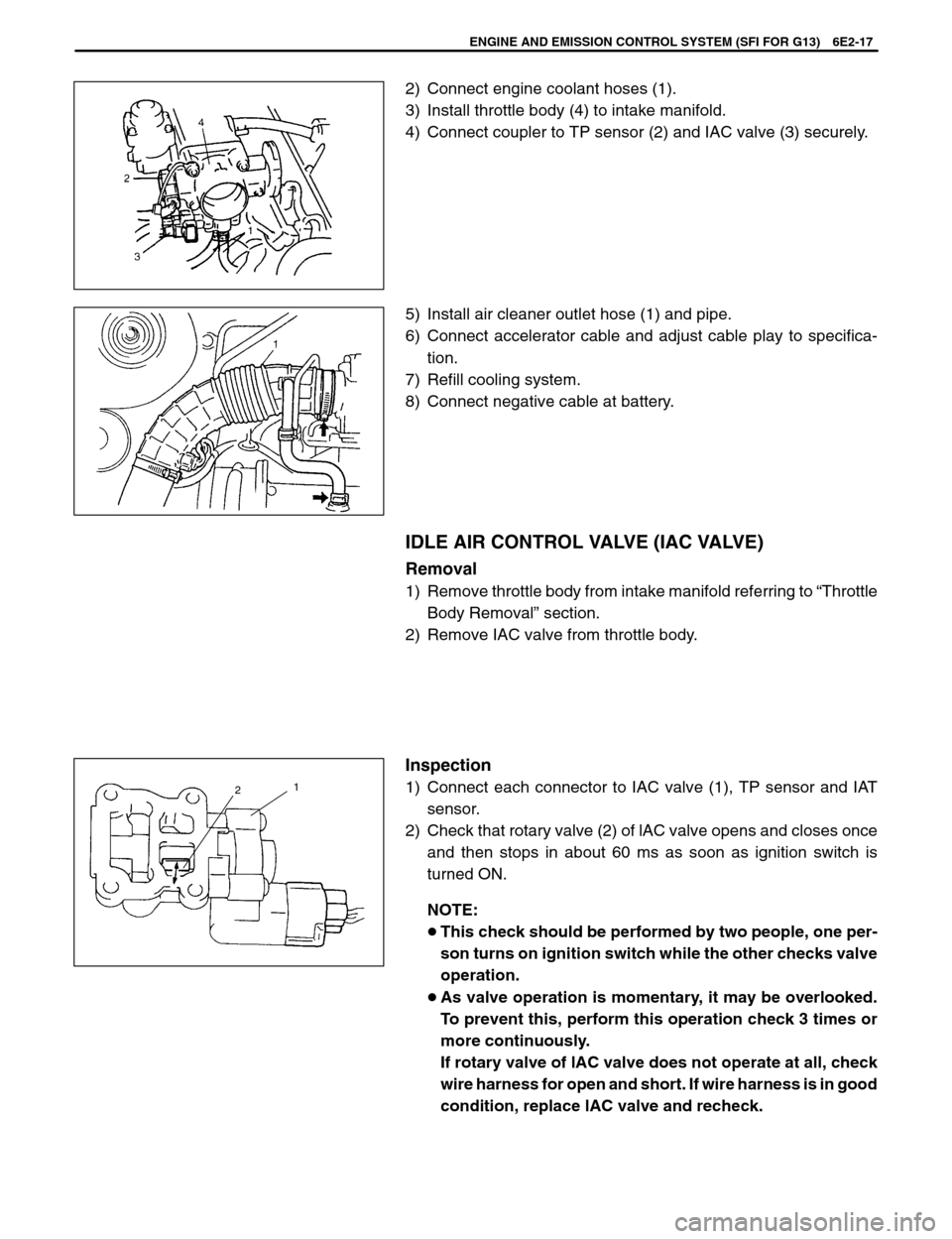
21
ENGINE AND EMISSION CONTROL SYSTEM (SFI FOR G13) 6E2-17
2) Connect engine coolant hoses (1).
3) Install throttle body (4) to intake manifold.
4) Connect coupler to TP sensor (2) and IAC valve (3) securely.
5) Install air cleaner outlet hose (1) and pipe.
6) Connect accelerator cable and adjust cable play to specifica-
tion.
7) Refill cooling system.
8) Connect negative cable at battery.
IDLE AIR CONTROL VALVE (IAC VALVE)
Removal
1) Remove throttle body from intake manifold referring to “Throttle
Body Removal” section.
2) Remove IAC valve from throttle body.
Inspection
1) Connect each connector to IAC valve (1), TP sensor and IAT
sensor.
2) Check that rotary valve (2) of lAC valve opens and closes once
and then stops in about 60 ms as soon as ignition switch is
turned ON.
NOTE:
This check should be performed by two people, one per-
son turns on ignition switch while the other checks valve
operation.
As valve operation is momentary, it may be overlooked.
To prevent this, perform this operation check 3 times or
more continuously.
If rotary valve of lAC valve does not operate at all, check
wire harness for open and short. If wire harness is in good
condition, replace lAC valve and recheck.
Page 447 of 557
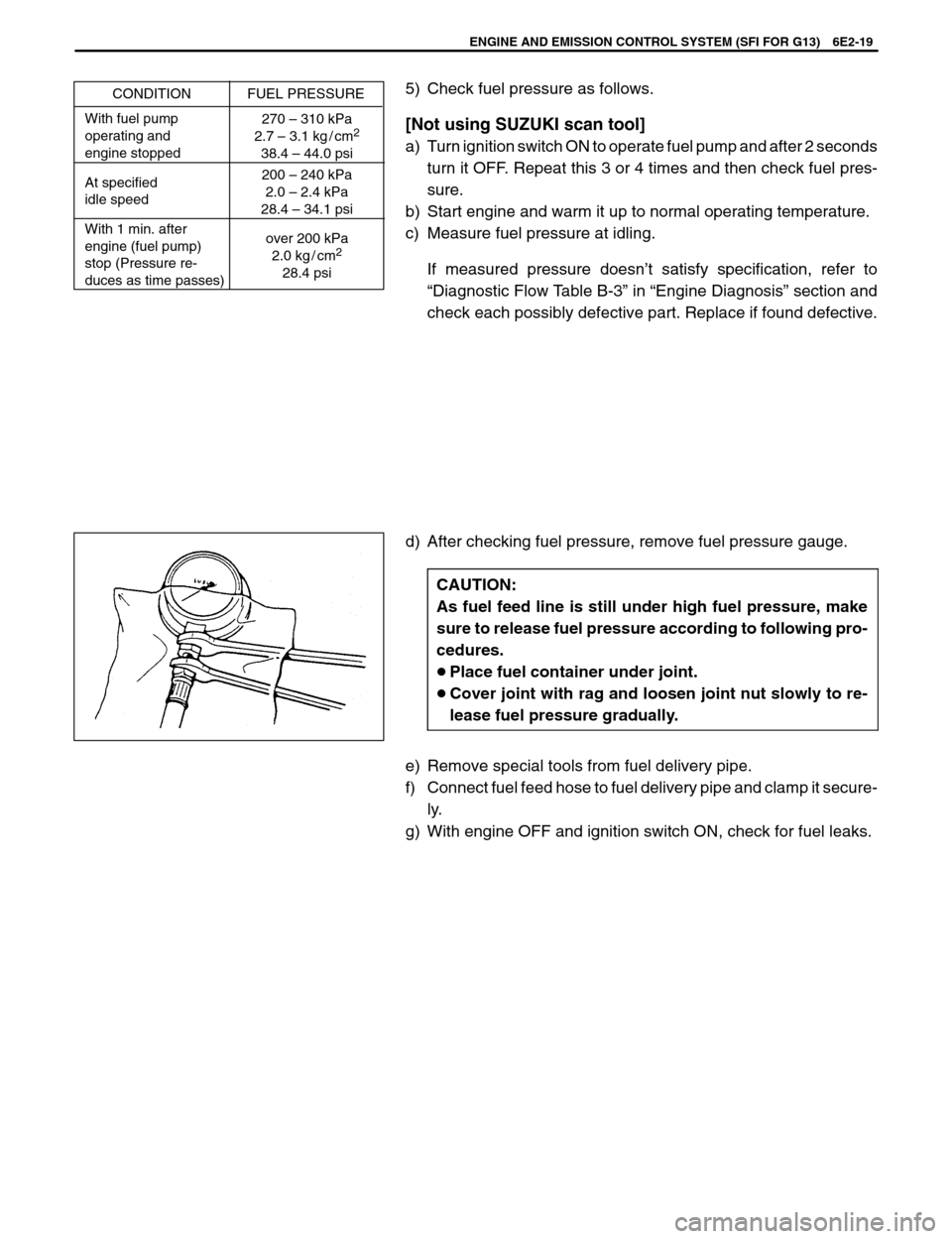
270 – 310 kPa
2.7 – 3.1 kg / cm2
38.4 – 44.0 psi
At specified
idle speed
With 1 min. after
engine (fuel pump)
stop (Pressure re-
duces as time passes)over 200 kPa
2.0 kg / cm
2
28.4 psi
CONDITION FUEL PRESSURE
With fuel pump
operating and
engine stopped
200 – 240 kPa
2.0 – 2.4 kPa
28.4 – 34.1 psi
ENGINE AND EMISSION CONTROL SYSTEM (SFI FOR G13) 6E2-19
5) Check fuel pressure as follows.
[Not using SUZUKI scan tool]
a) Turn ignition switch ON to operate fuel pump and after 2 seconds
turn it OFF. Repeat this 3 or 4 times and then check fuel pres-
sure.
b) Start engine and warm it up to normal operating temperature.
c) Measure fuel pressure at idling.
If measured pressure doesn’t satisfy specification, refer to
“Diagnostic Flow Table B-3” in “Engine Diagnosis” section and
check each possibly defective part. Replace if found defective.
d) After checking fuel pressure, remove fuel pressure gauge.
CAUTION:
As fuel feed line is still under high fuel pressure, make
sure to release fuel pressure according to following pro-
cedures.
Place fuel container under joint.
Cover joint with rag and loosen joint nut slowly to re-
lease fuel pressure gradually.
e) Remove special tools from fuel delivery pipe.
f) Connect fuel feed hose to fuel delivery pipe and clamp it secure-
ly.
g) With engine OFF and ignition switch ON, check for fuel leaks.
Page 448 of 557
![SUZUKI SWIFT 2000 1.G SF310 Service Workshop Manual 6E2-20 ENGINE AND EMISSION CONTROL SYSTEM (SFI FOR G13)
[Using SUZUKI scan tool]
a) Connect SUZUKI scan tool to DLC with ignition switch OFF.
b) Turn ignition switch ON and then select “DATA LIST” SUZUKI SWIFT 2000 1.G SF310 Service Workshop Manual 6E2-20 ENGINE AND EMISSION CONTROL SYSTEM (SFI FOR G13)
[Using SUZUKI scan tool]
a) Connect SUZUKI scan tool to DLC with ignition switch OFF.
b) Turn ignition switch ON and then select “DATA LIST”](/manual-img/20/7602/w960_7602-447.png)
6E2-20 ENGINE AND EMISSION CONTROL SYSTEM (SFI FOR G13)
[Using SUZUKI scan tool]
a) Connect SUZUKI scan tool to DLC with ignition switch OFF.
b) Turn ignition switch ON and then select “DATA LIST” mode on
scan tool.
c) Make sure that vehicle condition is as following.
Vehicle speed = 0 KPH
Engine speed = 0 RPM
Fuel tank level 15%
d) Clear DTC by using “CLEAR INFO” mode.
e) Check fuel pressure by using “FUEL PUMP CONT” mode in
“MISC TEST” menu.
CONDITIONFUEL PRESSURE
With fuel pump operating
2.7 – 3.1 kg / cm2
270 – 310 kPa
38.4 – 44.0 psi
Within 1 min. after fuel pump
stop (Pressure reduces as
time passes)Over 2.0 kg / cm2
200 kPa
28.4 psi
If measured pressure doesn’t satisfy specification, refer to
“Diagnostic Flow Table B-3” and check each possibly defective
part. Replace if found defective.
f) Start engine and warm it up to normal operating temperature.
And then check fuel pressure.
CONDITIONFUEL PRESSURE
At specified idle speed
2.0 – 2.4 kg / cm2
200 – 240 kPa
28.4 – 34.1 psi
If measured pressure doesn’t satisfy specification, refer to
“Diagnostic Flow Table B-3” and check each possibly defective
part. Replace if found defective.
g) After checking fuel pressure, remove fuel pressure gauge.
CAUTION:
As fuel feed line is still under high fuel pressure, make
sure to release fuel pressure according to following pro-
cedures.
Place fuel container under joint.
Cover joint with rag and loosen joint nut slowly to re-
lease fuel pressure gradually.
h) Remove special tools from fuel delivery pipe.
i) Connect fuel feed hose to fuel delivery pipe and clamp it secure-
ly.
j) With engine OFF and ignition switch ON, check for fuel leaks.
Tightening Torque
Fuel pressure regulator bolt: 11 N
.m (1.1 kg-m, 8.0 lb-ft)
Page 449 of 557
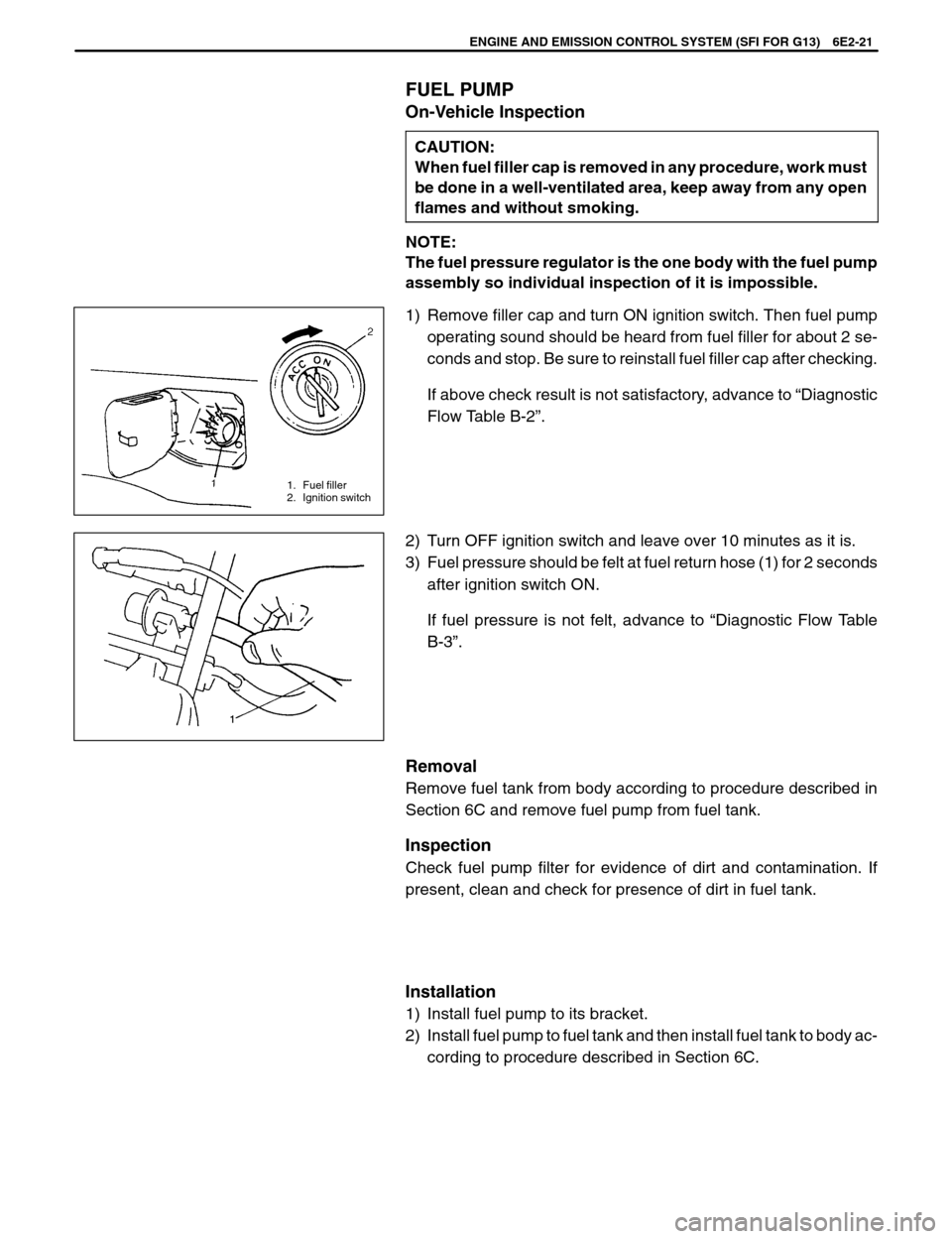
1. Fuel filler
2. Ignition switch
ENGINE AND EMISSION CONTROL SYSTEM (SFI FOR G13) 6E2-21
FUEL PUMP
On-Vehicle Inspection
CAUTION:
When fuel filler cap is removed in any procedure, work must
be done in a well-ventilated area, keep away from any open
flames and without smoking.
NOTE:
The fuel pressure regulator is the one body with the fuel pump
assembly so individual inspection of it is impossible.
1) Remove filler cap and turn ON ignition switch. Then fuel pump
operating sound should be heard from fuel filler for about 2 se-
conds and stop. Be sure to reinstall fuel filler cap after checking.
If above check result is not satisfactory, advance to “Diagnostic
Flow Table B-2”.
2) Turn OFF ignition switch and leave over 10 minutes as it is.
3) Fuel pressure should be felt at fuel return hose (1) for 2 seconds
after ignition switch ON.
If fuel pressure is not felt, advance to “Diagnostic Flow Table
B-3”.
Removal
Remove fuel tank from body according to procedure described in
Section 6C and remove fuel pump from fuel tank.
Inspection
Check fuel pump filter for evidence of dirt and contamination. If
present, clean and check for presence of dirt in fuel tank.
Installation
1) Install fuel pump to its bracket.
2) Install fuel pump to fuel tank and then install fuel tank to body ac-
cording to procedure described in Section 6C.
Page 450 of 557
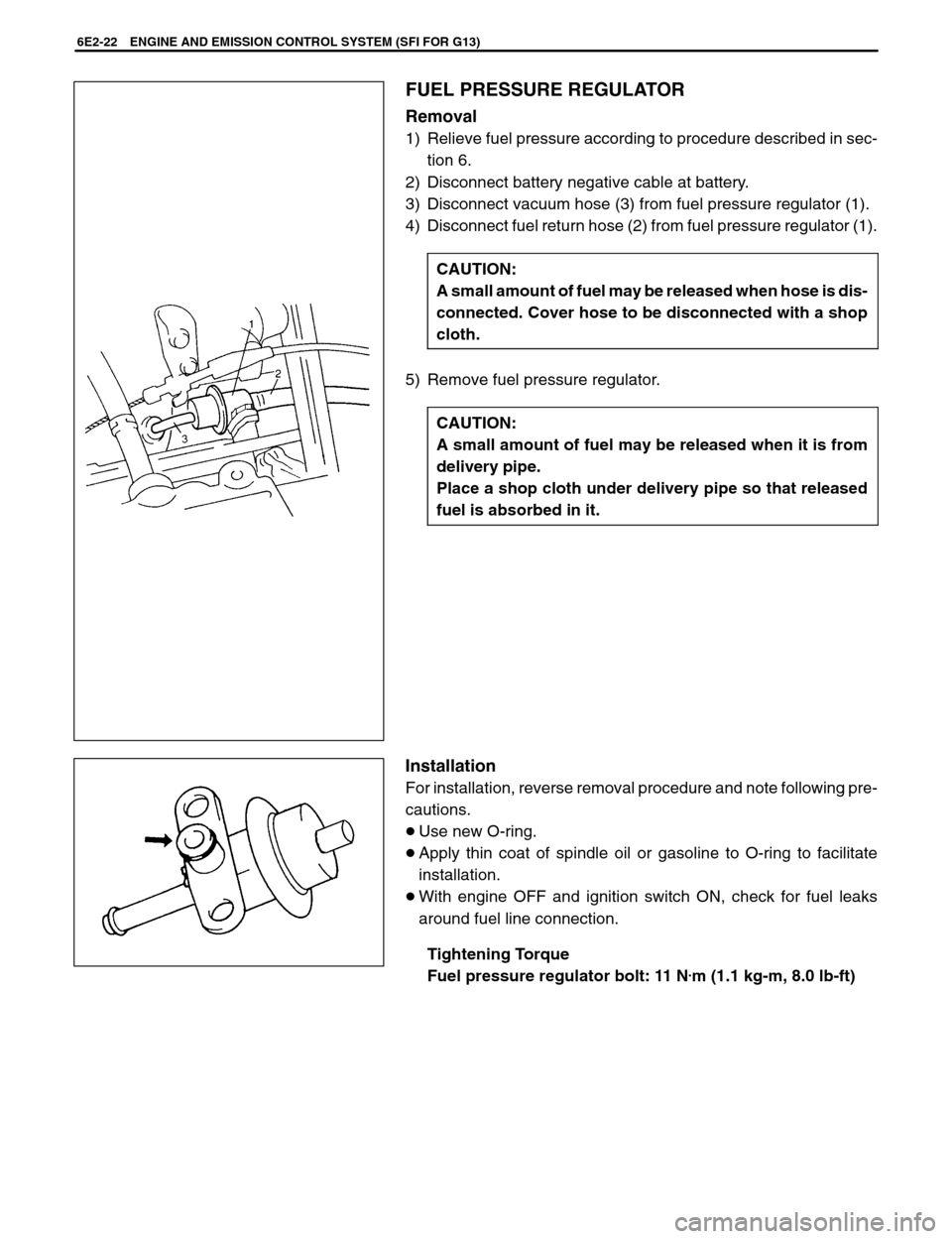
6E2-22 ENGINE AND EMISSION CONTROL SYSTEM (SFI FOR G13)
FUEL PRESSURE REGULATOR
Removal
1) Relieve fuel pressure according to procedure described in sec-
tion 6.
2) Disconnect battery negative cable at battery.
3) Disconnect vacuum hose (3) from fuel pressure regulator (1).
4) Disconnect fuel return hose (2) from fuel pressure regulator (1).
CAUTION:
A small amount of fuel may be released when hose is dis-
connected. Cover hose to be disconnected with a shop
cloth.
5) Remove fuel pressure regulator.
CAUTION:
A small amount of fuel may be released when it is from
delivery pipe.
Place a shop cloth under delivery pipe so that released
fuel is absorbed in it.
Installation
For installation, reverse removal procedure and note following pre-
cautions.
Use new O-ring.
Apply thin coat of spindle oil or gasoline to O-ring to facilitate
installation.
With engine OFF and ignition switch ON, check for fuel leaks
around fuel line connection.
Tightening Torque
Fuel pressure regulator bolt: 11 N
.m (1.1 kg-m, 8.0 lb-ft)
Page 453 of 557
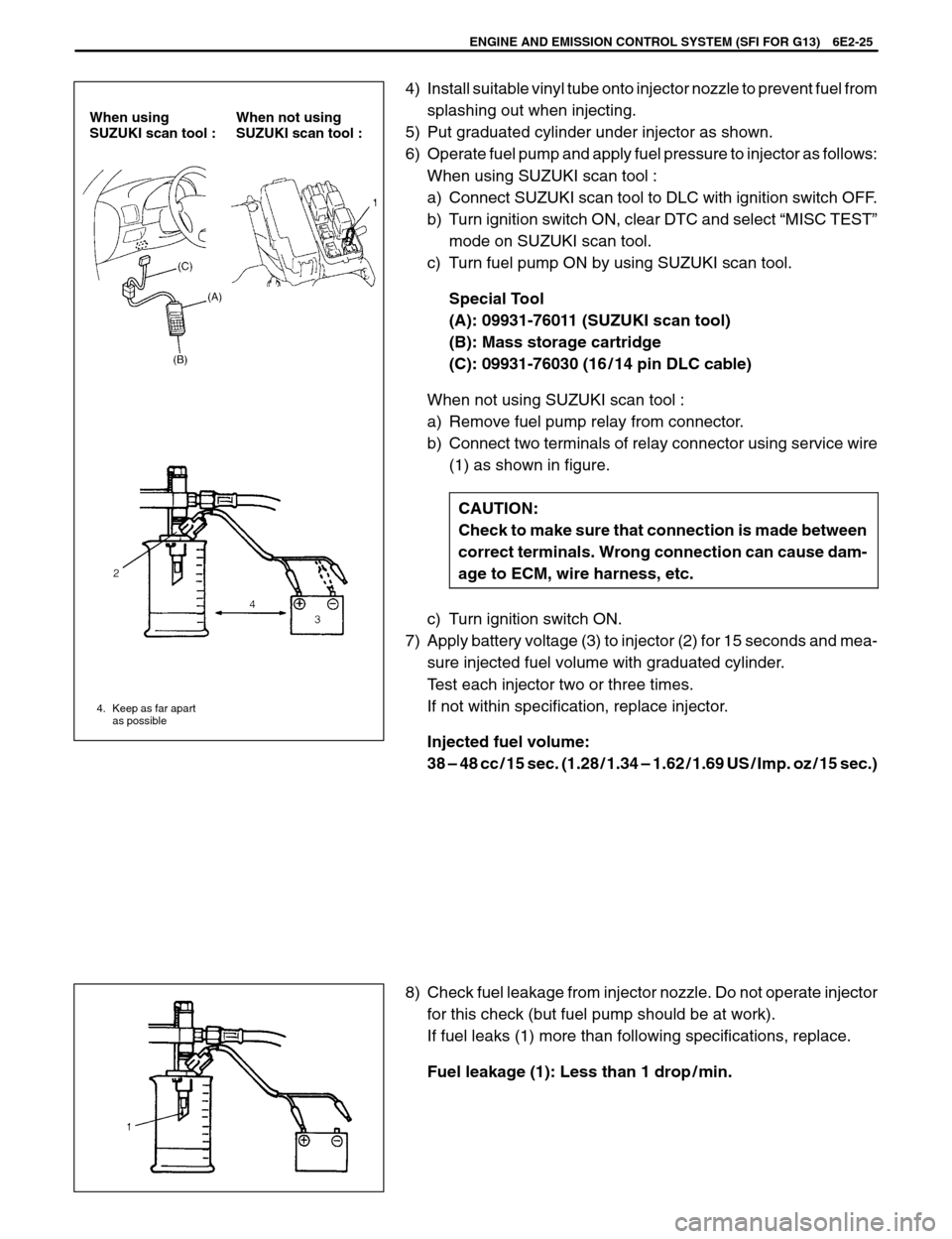
When not using
SUZUKI scan tool : When using
SUZUKI scan tool :
4. Keep as far apart
as possible
ENGINE AND EMISSION CONTROL SYSTEM (SFI FOR G13) 6E2-25
4) Install suitable vinyl tube onto injector nozzle to prevent fuel from
splashing out when injecting.
5) Put graduated cylinder under injector as shown.
6) Operate fuel pump and apply fuel pressure to injector as follows:
When using SUZUKI scan tool :
a) Connect SUZUKI scan tool to DLC with ignition switch OFF.
b) Turn ignition switch ON, clear DTC and select “MISC TEST”
mode on SUZUKI scan tool.
c) Turn fuel pump ON by using SUZUKI scan tool.
Special Tool
(A): 09931-76011 (SUZUKI scan tool)
(B): Mass storage cartridge
(C): 09931-76030 (16 / 14 pin DLC cable)
When not using SUZUKI scan tool :
a) Remove fuel pump relay from connector.
b) Connect two terminals of relay connector using service wire
(1) as shown in figure.
CAUTION:
Check to make sure that connection is made between
correct terminals. Wrong connection can cause dam-
age to ECM, wire harness, etc.
c) Turn ignition switch ON.
7) Apply battery voltage (3) to injector (2) for 15 seconds and mea-
sure injected fuel volume with graduated cylinder.
Test each injector two or three times.
If not within specification, replace injector.
Injected fuel volume:
38 – 48 cc / 15 sec. (1.28 / 1.34 – 1.62 / 1.69 US / Imp. oz / 15 sec.)
8) Check fuel leakage from injector nozzle. Do not operate injector
for this check (but fuel pump should be at work).
If fuel leaks (1) more than following specifications, replace.
Fuel leakage (1): Less than 1 drop / min.
Page 454 of 557
6E2-26 ENGINE AND EMISSION CONTROL SYSTEM (SFI FOR G13)
Installation
For installation, reverse removal procedure and note following pre-
cautions.
Replace injector O-ring (1) with new one using care not to dam-
age it.
Check if cushion (2) is scored or damaged. If it is, replace with
new one.
Apply thin coat of fuel to O-rings (1) and then install injectors (3)
into delivery pipe (4) and intake manifold.
Make sure that injectors (3) rotate smoothly (6). If not, probable
cause is incorrect installation of O-ring (1). Replace O-ring (1)
with new one.
Tighten delivery pipe bolts (5) and make sure that injectors (3) ro-
tate smoothly (6).
Tightening Torque
(a): 25 N
.m (2.5 kg-m, 18.0 lb-ft)
After installation, with engine OFF and ignition switch ON, check
for fuel leaks around fuel line connection.