Page 180 of 557
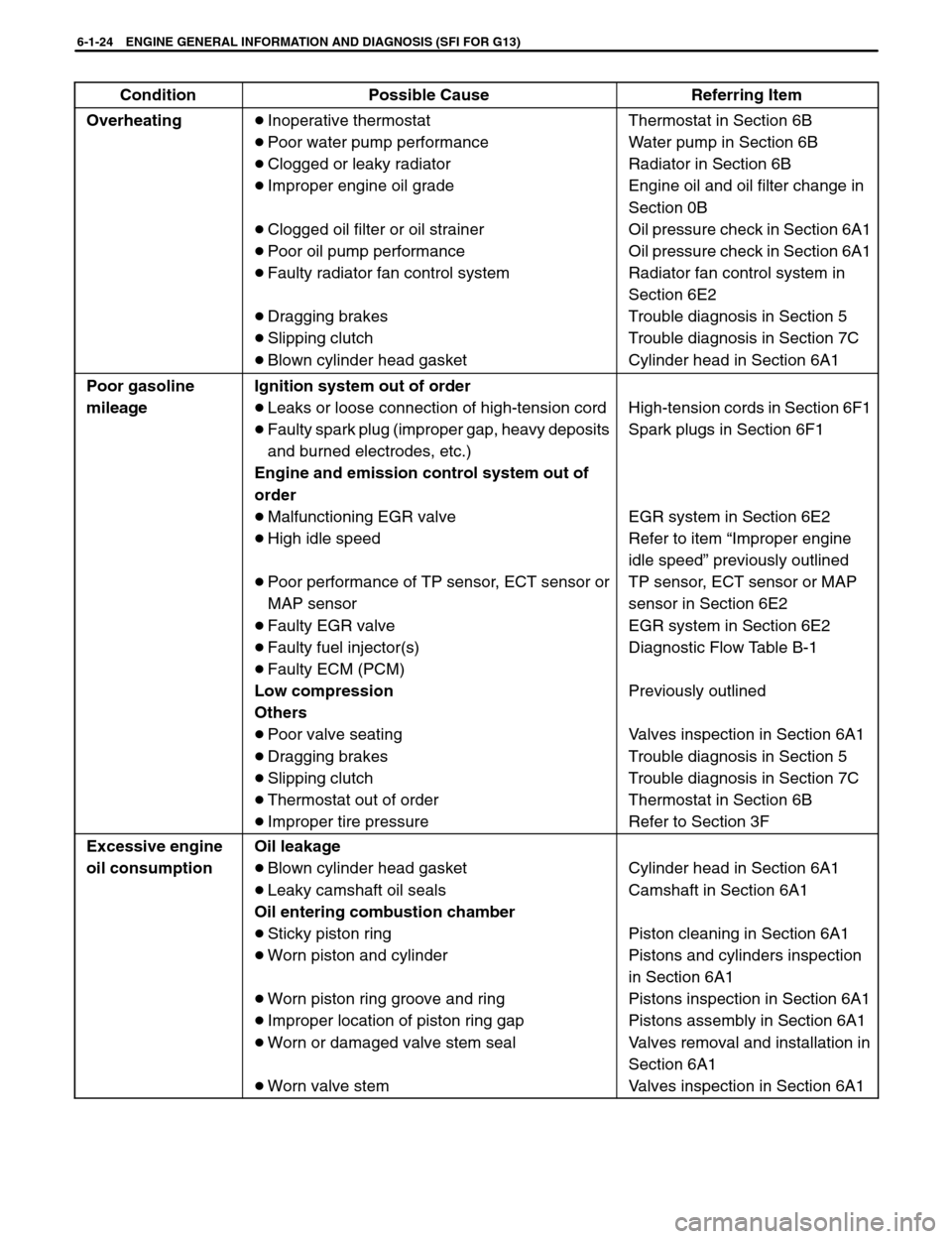
6-1-24 ENGINE GENERAL INFORMATION AND DIAGNOSIS (SFI FOR G13)
ConditionPossible CauseReferring Item
OverheatingInoperative thermostat
Poor water pump performance
Clogged or leaky radiator
Improper engine oil grade
Clogged oil filter or oil strainer
Poor oil pump performance
Faulty radiator fan control system
Dragging brakes
Slipping clutch
Blown cylinder head gasketThermostat in Section 6B
Water pump in Section 6B
Radiator in Section 6B
Engine oil and oil filter change in
Section 0B
Oil pressure check in Section 6A1
Oil pressure check in Section 6A1
Radiator fan control system in
Section 6E2
Trouble diagnosis in Section 5
Trouble diagnosis in Section 7C
Cylinder head in Section 6A1
Poor gasoline
mileageIgnition system out of order
Leaks or loose connection of high-tension cord
Faulty spark plug (improper gap, heavy deposits
and burned electrodes, etc.)
Engine and emission control system out of
order
Malfunctioning EGR valve
High idle speed
Poor performance of TP sensor, ECT sensor or
MAP sensor
Faulty EGR valve
Faulty fuel injector(s)
Faulty ECM (PCM)
Low compression
Others
Poor valve seating
Dragging brakes
Slipping clutch
Thermostat out of order
Improper tire pressure
High-tension cords in Section 6F1
Spark plugs in Section 6F1
EGR system in Section 6E2
Refer to item “Improper engine
idle speed” previously outlined
TP sensor, ECT sensor or MAP
sensor in Section 6E2
EGR system in Section 6E2
Diagnostic Flow Table B-1
Previously outlined
Valves inspection in Section 6A1
Trouble diagnosis in Section 5
Trouble diagnosis in Section 7C
Thermostat in Section 6B
Refer to Section 3F
Excessive engine
oil consumptionOil leakage
Blown cylinder head gasket
Leaky camshaft oil seals
Oil entering combustion chamber
Sticky piston ring
Worn piston and cylinder
Worn piston ring groove and ring
Improper location of piston ring gap
Worn or damaged valve stem seal
Worn valve stem
Cylinder head in Section 6A1
Camshaft in Section 6A1
Piston cleaning in Section 6A1
Pistons and cylinders inspection
in Section 6A1
Pistons inspection in Section 6A1
Pistons assembly in Section 6A1
Valves removal and installation in
Section 6A1
Valves inspection in Section 6A1
Page 285 of 557
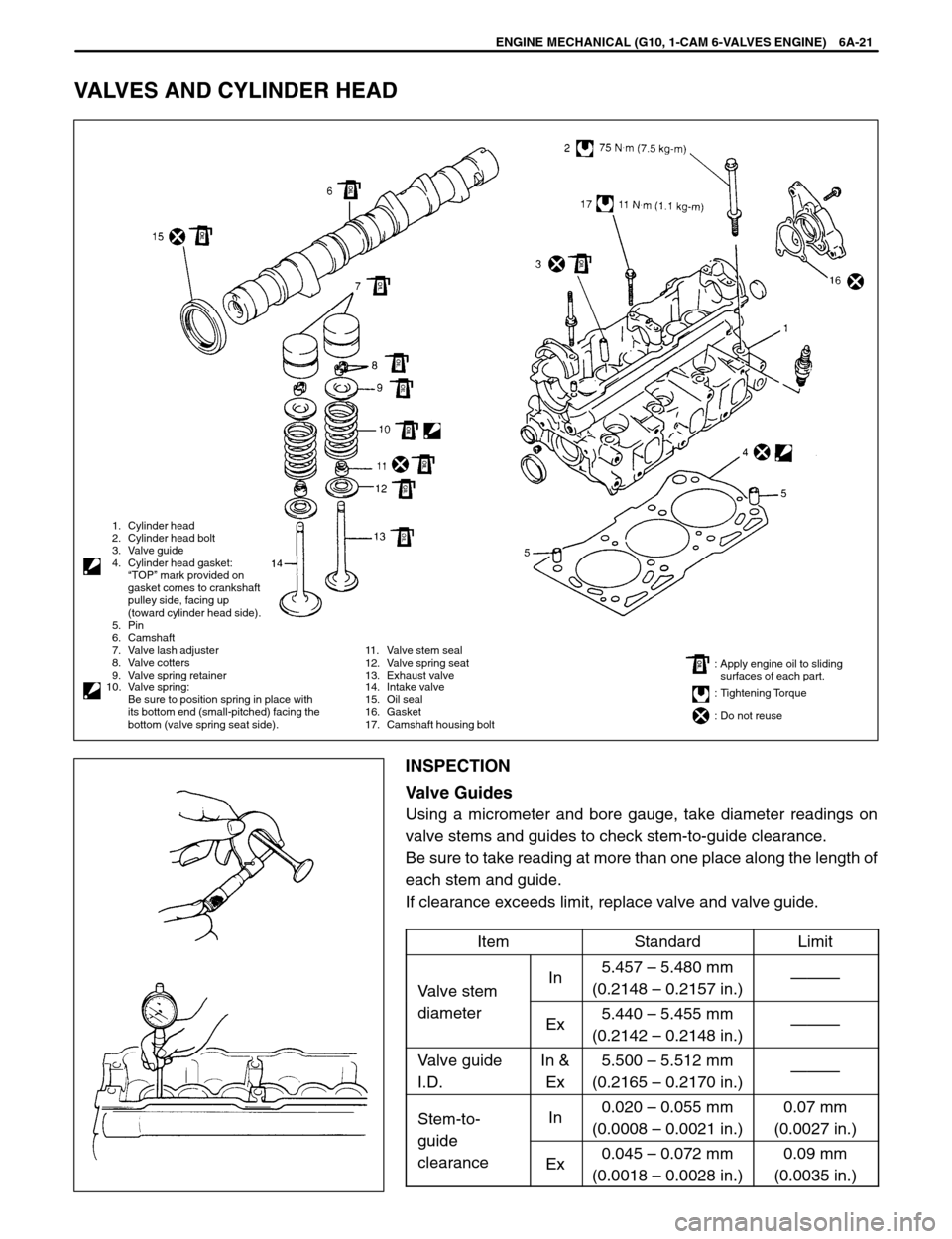
1. Cylinder head
2. Cylinder head bolt
3. Valve guide
4. Cylinder head gasket:
“TOP” mark provided on
gasket comes to crankshaft
pulley side, facing up
(toward cylinder head side).
5. Pin
6. Camshaft
7. Valve lash adjuster
8. Valve cotters
9. Valve spring retainer
10. Valve spring:
Be sure to position spring in place with
its bottom end (small-pitched) facing the
bottom (valve spring seat side).11. Valve stem seal
12. Valve spring seat
13. Exhaust valve
14. Intake valve
15. Oil seal
16. Gasket
17. Camshaft housing bolt: Tightening Torque
: Do not reuse
: Apply engine oil to sliding
: surfaces of each part.
ENGINE MECHANICAL (G10, 1-CAM 6-VALVES ENGINE) 6A-21
VALVES AND CYLINDER HEAD
INSPECTION
Valve Guides
Using a micrometer and bore gauge, take diameter readings on
valve stems and guides to check stem-to-guide clearance.
Be sure to take reading at more than one place along the length of
each stem and guide.
If clearance exceeds limit, replace valve and valve guide.
Item
StandardLimit
Valve stemIn5.457 – 5.480 mm
(0.2148 – 0.2157 in.)———
diameterEx5.440 – 5.455 mm
(0.2142 – 0.2148 in.)———
Valve guide
I.D.In &
Ex5.500 – 5.512 mm
(0.2165 – 0.2170 in.)———
Stem-to-
guide
In0.020 – 0.055 mm
(0.0008 – 0.0021 in.)0.07 mm
(0.0027 in.)
guide
clearanceEx0.045 – 0.072 mm
(0.0018 – 0.0028 in.)0.09 mm
(0.0035 in.)
Page 286 of 557
6A-22 ENGINE MECHANICAL (G10, 1-CAM 6-VALVES ENGINE)
Valve Springs
Referring to data given below, check to be sure that each spring
is in sound condition, free of any evidence of breakage or weak-
ening. Remember, weakened valve springs can cause chatter,
not to mention possibility of reducing power output due to gas
leakage caused by decreased seating pressure.
Item
StandardLimit
Valve spring
free length42.29 mm
(1.6649 in.)41.0 mm
1.6142 in.)
Valve spring
preload
209 – 235 N
(20.9 – 23.5 kg) at
32.6 mm (46.1 –
51.8 lb at 1.28 in.)187 N (18.7 kg)
at 32.6 mm
(41.2 lb at 1.28 in.)
Spring squareness:
Use a square and surface plate to check each spring for square-
ness in terms of clearance between end of valve spring and
square. Valve spring found to exhibit a larger clearance than limit
must be replaced.
Valve spring
2 0 mm (0 079 in )g
squareness limit.2.0 mm (0.079 in.)
Page 336 of 557
: Do not reuse
1. Valve cotters
2. Valve spring retainer
3. Valve spring:
be sure to position
spring in place with its
bottom end (small-pitch
end) facing the bottom
(valve spring seat side).
4. Valve stem seal
5. Valve spring seat
6. Exhaust valve
7. Intake valve
8. Cylinder head bolt
9. Camshaft housing bolt10. Camshaft housing:
Apply sealant to mating surface of
No.1 and No.6 housings.
11. Valve guide
12. Oil venturi plug
13. Cylinder head gasket:
“TOP” mark provided on gasket comes to
crankshaft pulley side, facing up
(toward cylinder head side).
14. Dowel pin
: Tightening Torque
: Apply engine oil to sliding
: surfaces of each part.
3.5 N.m (0.35 kg-m)
ENGINE MECHANICAL (G13B, 1-CAM 16-VALVES ENGINE) 6A1-41
VALVES AND CYLINDER HEAD
REMOVAL
1) Relieve fuel pressure according to procedure described in Sec-
tion 6.
2) Disconnect negative cable at battery.
3) Drain cooling system.
4) Remove air cleaner outlet hose as previously outlined.
Page 339 of 557
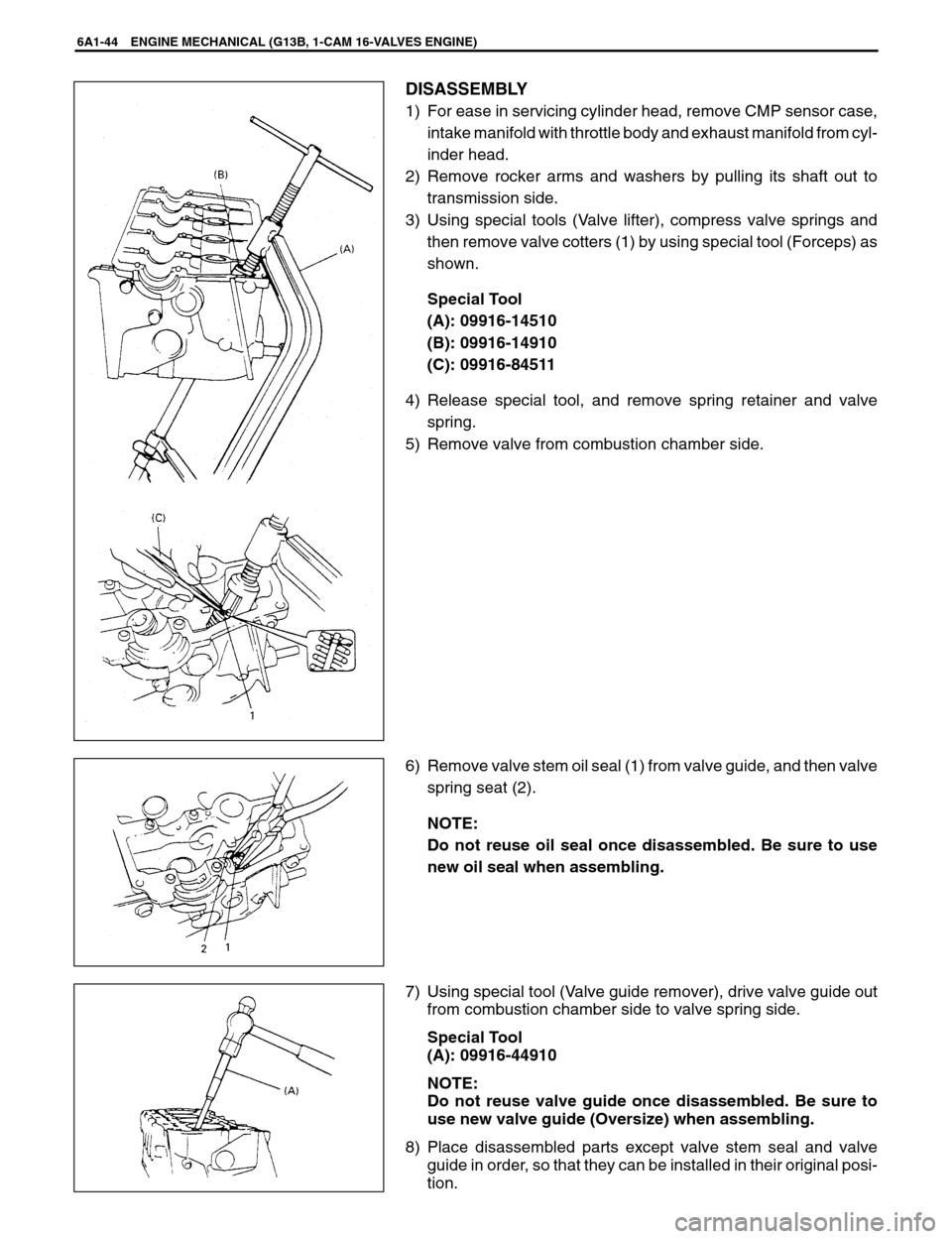
6A1-44 ENGINE MECHANICAL (G13B, 1-CAM 16-VALVES ENGINE)
DISASSEMBLY
1) For ease in servicing cylinder head, remove CMP sensor case,
intake manifold with throttle body and exhaust manifold from cyl-
inder head.
2) Remove rocker arms and washers by pulling its shaft out to
transmission side.
3) Using special tools (Valve lifter), compress valve springs and
then remove valve cotters (1) by using special tool (Forceps) as
shown.
Special Tool
(A): 09916-14510
(B): 09916-14910
(C): 09916-84511
4) Release special tool, and remove spring retainer and valve
spring.
5) Remove valve from combustion chamber side.
6) Remove valve stem oil seal (1) from valve guide, and then valve
spring seat (2).
NOTE:
Do not reuse oil seal once disassembled. Be sure to use
new oil seal when assembling.
7) Using special tool (Valve guide remover), drive valve guide out
from combustion chamber side to valve spring side.
Special Tool
(A): 09916-44910
NOTE:
Do not reuse valve guide once disassembled. Be sure to
use new valve guide (Oversize) when assembling.
8) Place disassembled parts except valve stem seal and valve
guide in order, so that they can be installed in their original posi-
tion.
Page 341 of 557
6A1-46 ENGINE MECHANICAL (G13B, 1-CAM 16-VALVES ENGINE)
Inspect valve stem end face for pitting and wear. If pitting or wear
is found there, valve stem end may be resurfaced, but not so
much as to grind off its chamfer. When it is worn so much that its
chamfer is gone, replace valve.
Seating contact width:
Create contact pattern on each valve in the usual manner, i.e., by
giving uniform coat of marking compound to valve seat and by ro-
tatingly tapping seat with valve head. Valve lapper (tool used in
valve lapping) must be used.
Pattern produced on seating face of valve must be a continuous
ring without any break, and the width “a” of pattern must be within
specified range.
Standard seating width
revealed by contact
In1.1 – 1.3 mmrevealed by contact
pattern on valve faceEx(0.0433 – 0.0512 in.)
Page 342 of 557
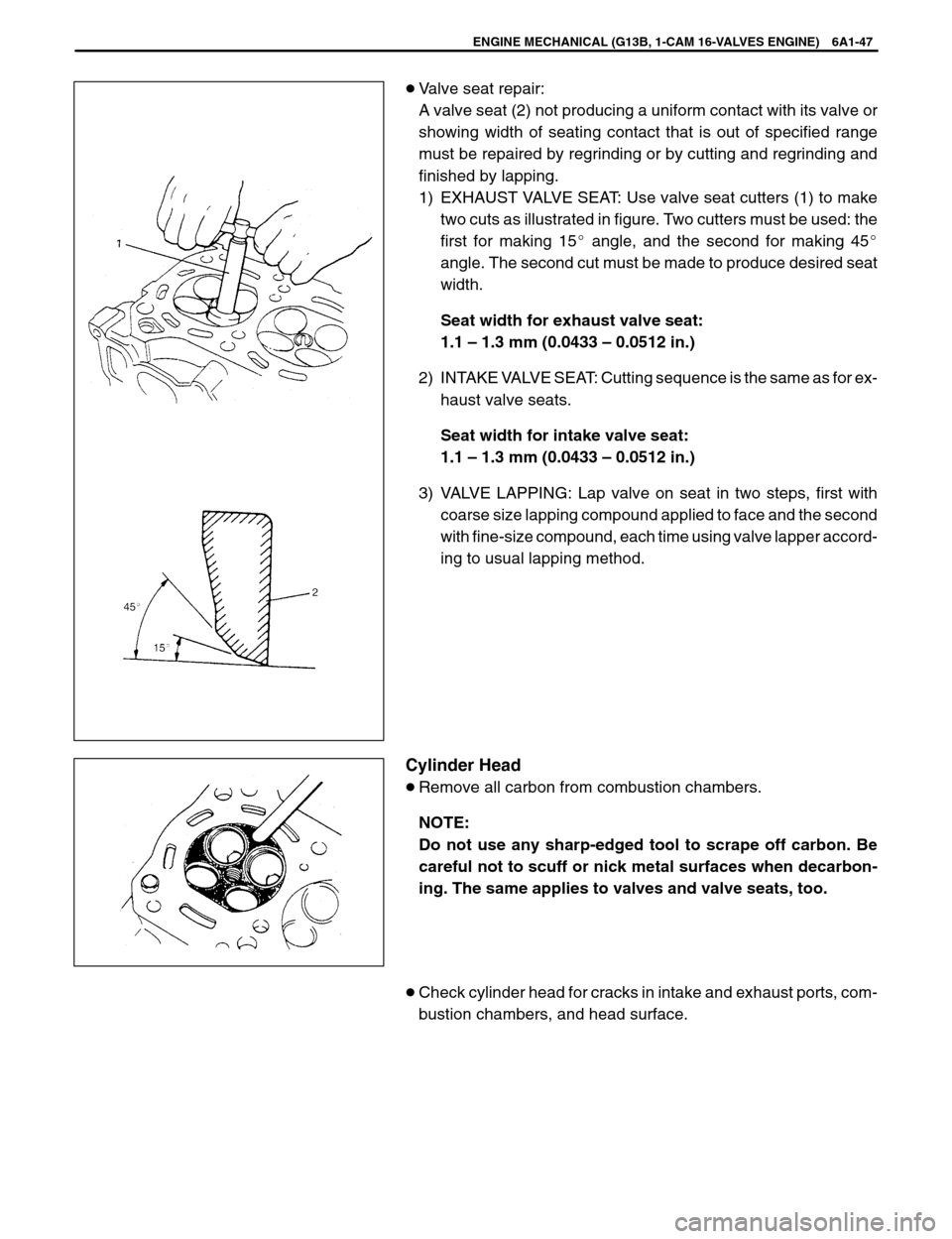
ENGINE MECHANICAL (G13B, 1-CAM 16-VALVES ENGINE) 6A1-47
Valve seat repair:
A valve seat (2) not producing a uniform contact with its valve or
showing width of seating contact that is out of specified range
must be repaired by regrinding or by cutting and regrinding and
finished by lapping.
1) EXHAUST VALVE SEAT: Use valve seat cutters (1) to make
two cuts as illustrated in figure. Two cutters must be used: the
first for making 15 angle, and the second for making 45
angle. The second cut must be made to produce desired seat
width.
Seat width for exhaust valve seat:
1.1 – 1.3 mm (0.0433 – 0.0512 in.)
2) INTAKE VALVE SEAT: Cutting sequence is the same as for ex-
haust valve seats.
Seat width for intake valve seat:
1.1 – 1.3 mm (0.0433 – 0.0512 in.)
3) VALVE LAPPING: Lap valve on seat in two steps, first with
coarse size lapping compound applied to face and the second
with fine-size compound, each time using valve lapper accord-
ing to usual lapping method.
Cylinder Head
Remove all carbon from combustion chambers.
NOTE:
Do not use any sharp-edged tool to scrape off carbon. Be
careful not to scuff or nick metal surfaces when decarbon-
ing. The same applies to valves and valve seats, too.
Check cylinder head for cracks in intake and exhaust ports, com-
bustion chambers, and head surface.
Page 343 of 557
6A1-48 ENGINE MECHANICAL (G13B, 1-CAM 16-VALVES ENGINE)
Flatness of gasketed surface:
Using a straightedge and thickness gauge, check surface at a to-
tal of 6 locations. If distortion limit, given below, is exceeded, cor-
rect gasketed surface with a surface plate and abrasive paper of
about #400 (Waterproof silicon carbide abrasive paper): place
paper on and over surface plate, and rub gasketed surface
against paper to grind off high spots. Should this fail to reduce
thickness gauge readings to within limit, replace cylinder head.
Leakage of combustion gases from this gasketed joint is often
due to warped gasketed surface: such leakage results in reduced
power output.
Limit of distortion: 0.05 mm (0.002 in.)
Distortion of manifold seating faces:
Check seating faces of cylinder head for manifolds, using a
straightedge and thickness gauge, in order to determine whether
these faces should be corrected or cylinder head replaced.
Limit of distortion: 0.10 mm (0.004 in.)