Page 130 of 557
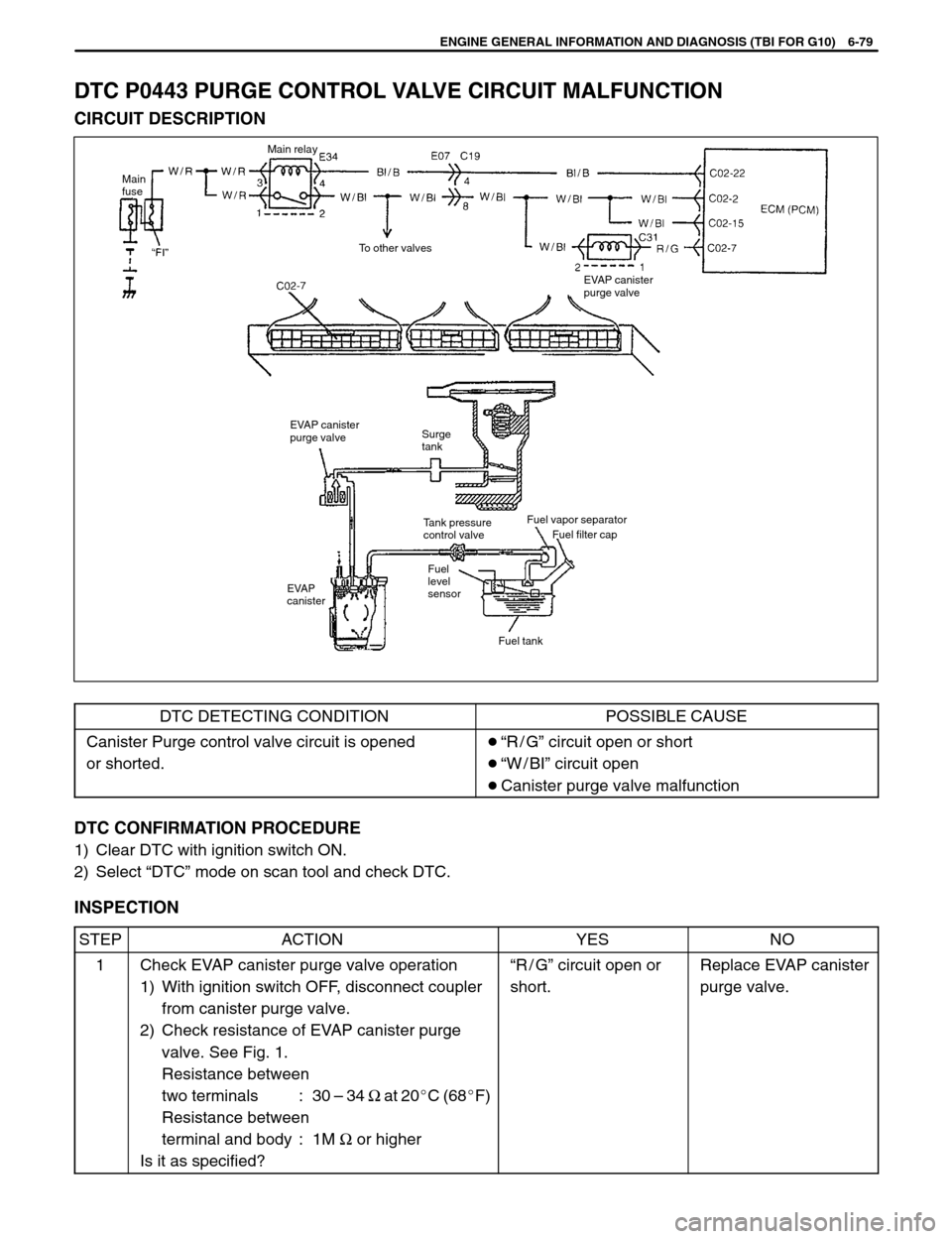
ENGINE GENERAL INFORMATION AND DIAGNOSIS (TBI FOR G10) 6-79
Main
fuseMain relay
To other valves
EVAP canister
purge valve
EVAP canister
purge valveSurge
tank
Tank pressure
control valveFuel vapor separator
Fuel filter cap
Fuel
level
sensor
Fuel tank EVAP
canister
DTC P0443 PURGE CONTROL VALVE CIRCUIT MALFUNCTION
CIRCUIT DESCRIPTION
DTC DETECTING CONDITIONPOSSIBLE CAUSE
Canister Purge control valve circuit is opened
or shorted.“R/G” circuit open or short
“W/BI” circuit open
Canister purge valve malfunction
DTC CONFIRMATION PROCEDURE
1) Clear DTC with ignition switch ON.
2) Select “DTC” mode on scan tool and check DTC.
INSPECTION
STEPACTIONYESNO
1Check EVAP canister purge valve operation
1) With ignition switch OFF, disconnect coupler
from canister purge valve.
2) Check resistance of EVAP canister purge
valve. See Fig. 1.
Resistance between
two terminals : 30 – 34 Ω at 20C (68F)
Resistance between
terminal and body : 1M Ω or higher
Is it as specified?“R/G” circuit open or
short.Replace EVAP canister
purge valve.
Page 161 of 557
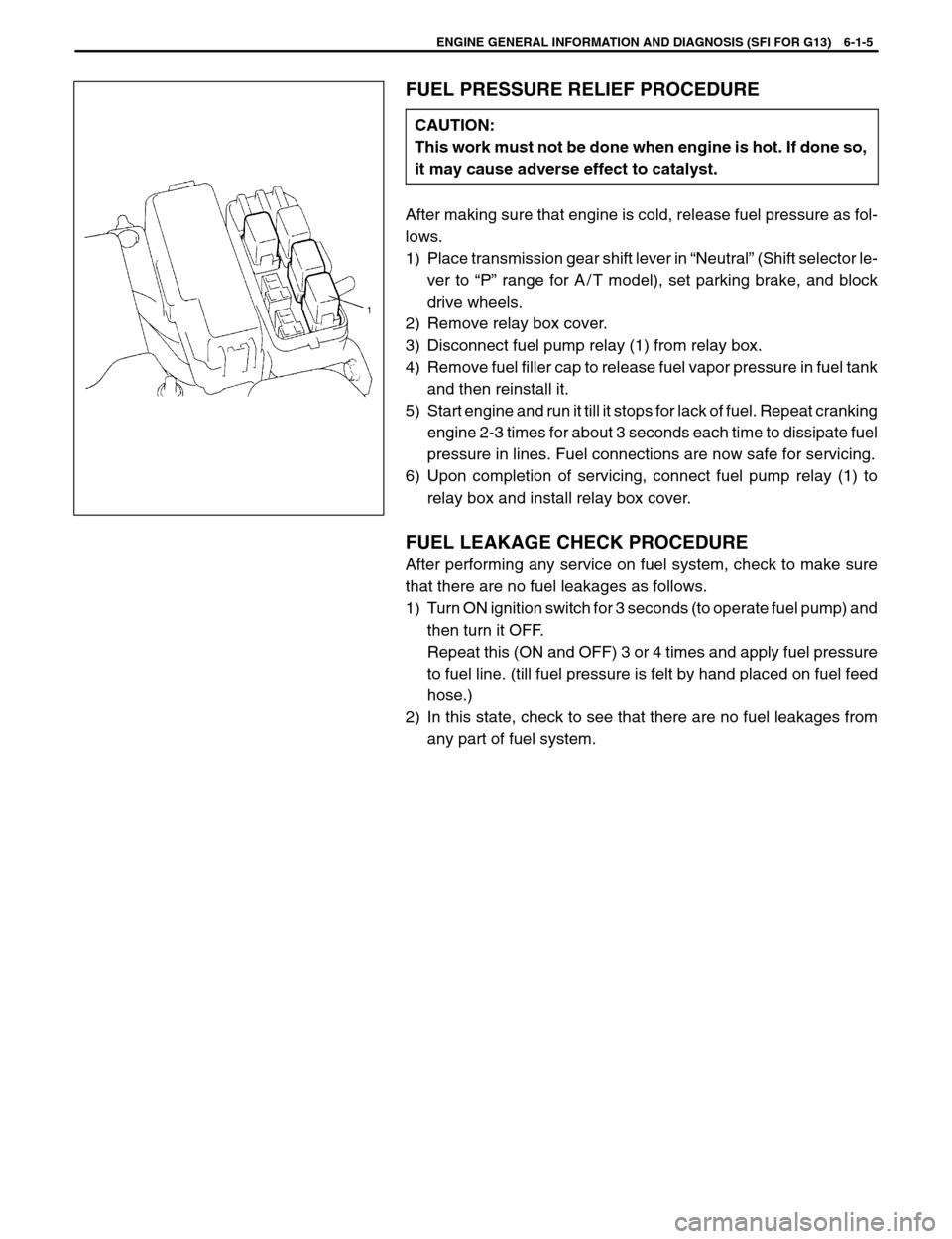
ENGINE GENERAL INFORMATION AND DIAGNOSIS (SFI FOR G13) 6-1-5
FUEL PRESSURE RELIEF PROCEDURE
CAUTION:
This work must not be done when engine is hot. If done so,
it may cause adverse effect to catalyst.
After making sure that engine is cold, release fuel pressure as fol-
lows.
1) Place transmission gear shift lever in “Neutral” (Shift selector le-
ver to “P” range for A / T model), set parking brake, and block
drive wheels.
2) Remove relay box cover.
3) Disconnect fuel pump relay (1) from relay box.
4) Remove fuel filler cap to release fuel vapor pressure in fuel tank
and then reinstall it.
5) Start engine and run it till it stops for lack of fuel. Repeat cranking
engine 2-3 times for about 3 seconds each time to dissipate fuel
pressure in lines. Fuel connections are now safe for servicing.
6) Upon completion of servicing, connect fuel pump relay (1) to
relay box and install relay box cover.
FUEL LEAKAGE CHECK PROCEDURE
After performing any service on fuel system, check to make sure
that there are no fuel leakages as follows.
1) Turn ON ignition switch for 3 seconds (to operate fuel pump) and
then turn it OFF.
Repeat this (ON and OFF) 3 or 4 times and apply fuel pressure
to fuel line. (till fuel pressure is felt by hand placed on fuel feed
hose.)
2) In this state, check to see that there are no fuel leakages from
any part of fuel system.
Page 179 of 557
![SUZUKI SWIFT 2000 1.G SF310 Service Workshop Manual ENGINE GENERAL INFORMATION AND DIAGNOSIS (SFI FOR G13) 6-1-23
ConditionPossible Cause]Referring Item
Low oil pressureImproper oil viscosity
Malfunctioning oil pressure switch
Clogged oil strainer
SUZUKI SWIFT 2000 1.G SF310 Service Workshop Manual ENGINE GENERAL INFORMATION AND DIAGNOSIS (SFI FOR G13) 6-1-23
ConditionPossible Cause]Referring Item
Low oil pressureImproper oil viscosity
Malfunctioning oil pressure switch
Clogged oil strainer
](/manual-img/20/7602/w960_7602-178.png)
ENGINE GENERAL INFORMATION AND DIAGNOSIS (SFI FOR G13) 6-1-23
ConditionPossible Cause]Referring Item
Low oil pressureImproper oil viscosity
Malfunctioning oil pressure switch
Clogged oil strainer
Functional deterioration of oil pump
Worn oil pump relief valve
Excessive clearance in various sliding partsEngine oil and oil filter change in
Section 0B
Oil pressure switch inspection in
Section 8
Oil pan and oil pump strainer
cleaning in Section 6A1
Oil pump in Section 6A1
Oil pump in Section 6A1
Engine noise
Note: Before
checking mechanical
noise, make sure
that:
Specified spark
plug in used.
Specified fuel is
used.Valve noise
Improper valve lash
Worn valve stem and guide
Weak or broken valve spring
Warped or bent valve
Piston, ring and cylinder noise
Worn piston, ring and cylinder bore
Connecting rod noise
Worn rod bearing
Worn crank pin
Loose connecting rod nuts
Low oil pressure
Crankshaft noise
Low oil pressure
Worn bearing
Worn crankshaft journal
Loose bearing cap bolts
Excessive crankshaft thrust play
Valve lash in Section 6A1
Valves inspection in Section 6A1
Valve springs inspection in
Section 6A1
Valves inspection in Section 6A1
Pistons and cylinders inspection
in Section 6A1
Crank pin and connecting rod
bearing inspection in Section 6A1
Crank pin and connecting rod
bearing inspection in Section 6A1
Connecting rod installation in
Section 6A1
Previously outlined
Previously outlined
Crankshaft and bearing
inspection in Section 6A1
Crankshaft and bearing
inspection in Section 6A1
Crankshaft inspection in
Section 6A1
Crankshaft thrust play inspection
in Section 6A1
Page 188 of 557
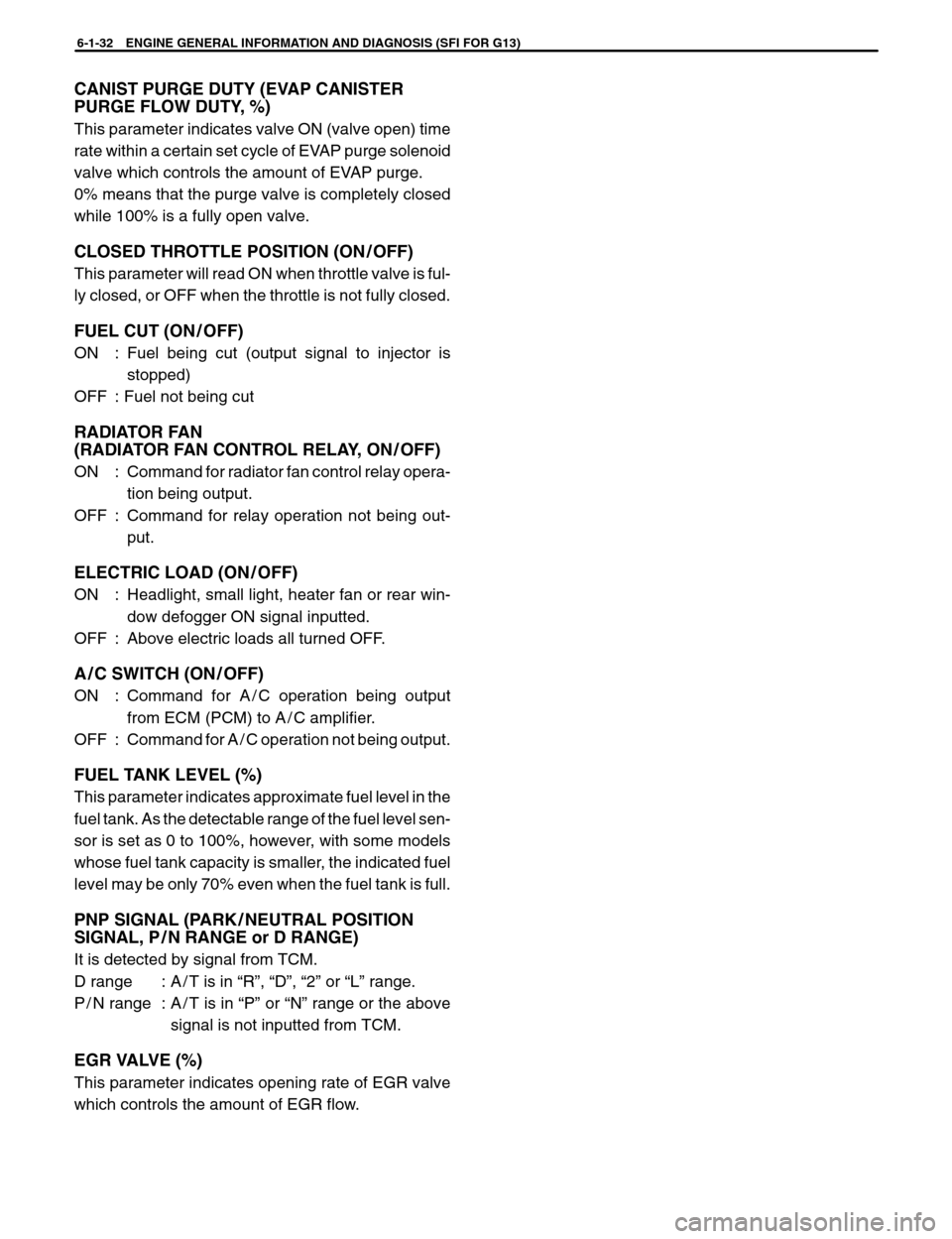
6-1-32 ENGINE GENERAL INFORMATION AND DIAGNOSIS (SFI FOR G13)
CANIST PURGE DUTY (EVAP CANISTER
PURGE FLOW DUTY, %)
This parameter indicates valve ON (valve open) time
rate within a certain set cycle of EVAP purge solenoid
valve which controls the amount of EVAP purge.
0% means that the purge valve is completely closed
while 100% is a fully open valve.
CLOSED THROTTLE POSITION (ON / OFF)
This parameter will read ON when throttle valve is ful-
ly closed, or OFF when the throttle is not fully closed.
FUEL CUT (ON / OFF)
ON : Fuel being cut (output signal to injector is
stopped)
OFF : Fuel not being cut
RADIATOR FAN
(RADIATOR FAN CONTROL RELAY, ON / OFF)
ON : Command for radiator fan control relay opera-
tion being output.
OFF : Command for relay operation not being out-
put.
ELECTRIC LOAD (ON / OFF)
ON : Headlight, small light, heater fan or rear win-
dow defogger ON signal inputted.
OFF : Above electric loads all turned OFF.
A / C SWITCH (ON / OFF)
ON : Command for A / C operation being output
from ECM (PCM) to A / C amplifier.
OFF : Command for A / C operation not being output.
FUEL TANK LEVEL (%)
This parameter indicates approximate fuel level in the
fuel tank. As the detectable range of the fuel level sen-
sor is set as 0 to 100%, however, with some models
whose fuel tank capacity is smaller, the indicated fuel
level may be only 70% even when the fuel tank is full.
PNP SIGNAL (PARK / NEUTRAL POSITION
SIGNAL, P / N RANGE or D RANGE)
It is detected by signal from TCM.
D range : A / T is in “R”, “D”, “2” or “L” range.
P / N range : A / T is in “P” or “N” range or the above
signal is not inputted from TCM.
EGR VALVE (%)
This parameter indicates opening rate of EGR valve
which controls the amount of EGR flow.
Page 269 of 557
1. Stay
2. Throttle body
3. Gasket
4. EFE heater
5. Intake manifold
6. Gasket : Tightening Torque
: Do not reuse
ENGINE MECHANICAL (G10, 1-CAM 6-VALVES ENGINE) 6A-5
THROTTLE BODY AND INTAKE MANIFOLD
REMOVAL
1) Relieve fuel pressure according to procedure described in
“FUEL PRESSURE RELIEF PROCEDURE” of Section 6.
2) Disconnect negative cable at battery.
3) Drain cooling system.
WARNING:
To help avoid danger of being burned, do not remove
drain plug (2) and radiator cap while engine and radiator
(1) are still hot. Scalding fluid and steam can be blown out
under pressure if plug and cap are taken off too soon.
Page 309 of 557
1. Intake manifold
2. Throttle body
3. Gasket
4. EGR valve
5. Fuel delivery pipe
6. Fuel injector7. Fuel pressure regulator
8. EVAP canister purge valve
9. MAP sensor
10. O-ring
11. Gasket
12. Cushion : Tightening Torque
: Do not reuse
1
2
6A1-14 ENGINE MECHANICAL (G13B, 1-CAM 16-VALVES ENGINE)
THROTTLE BODY AND INTAKE MANIFOLD
REMOVAL
1) Relieve fuel pressure according to procedure described in Sec-
tion 6.
2) Disconnect negative cable at battery.
3) Drain cooling system.
WARNING:
To help avoid danger of being burned, do not remove
drain plug (2) and radiator cap while engine and radiator
(1) are still hot. Scalding fluid and steam can be blown out
under pressure if plug and cap are taken off too soon.
4) Disconnect IAT sensor at coupler.
5) Remove air cleaner outlet hose (2) with resonator.
6) Disconnect accelerator cable (1) from throttle body.
Page 359 of 557
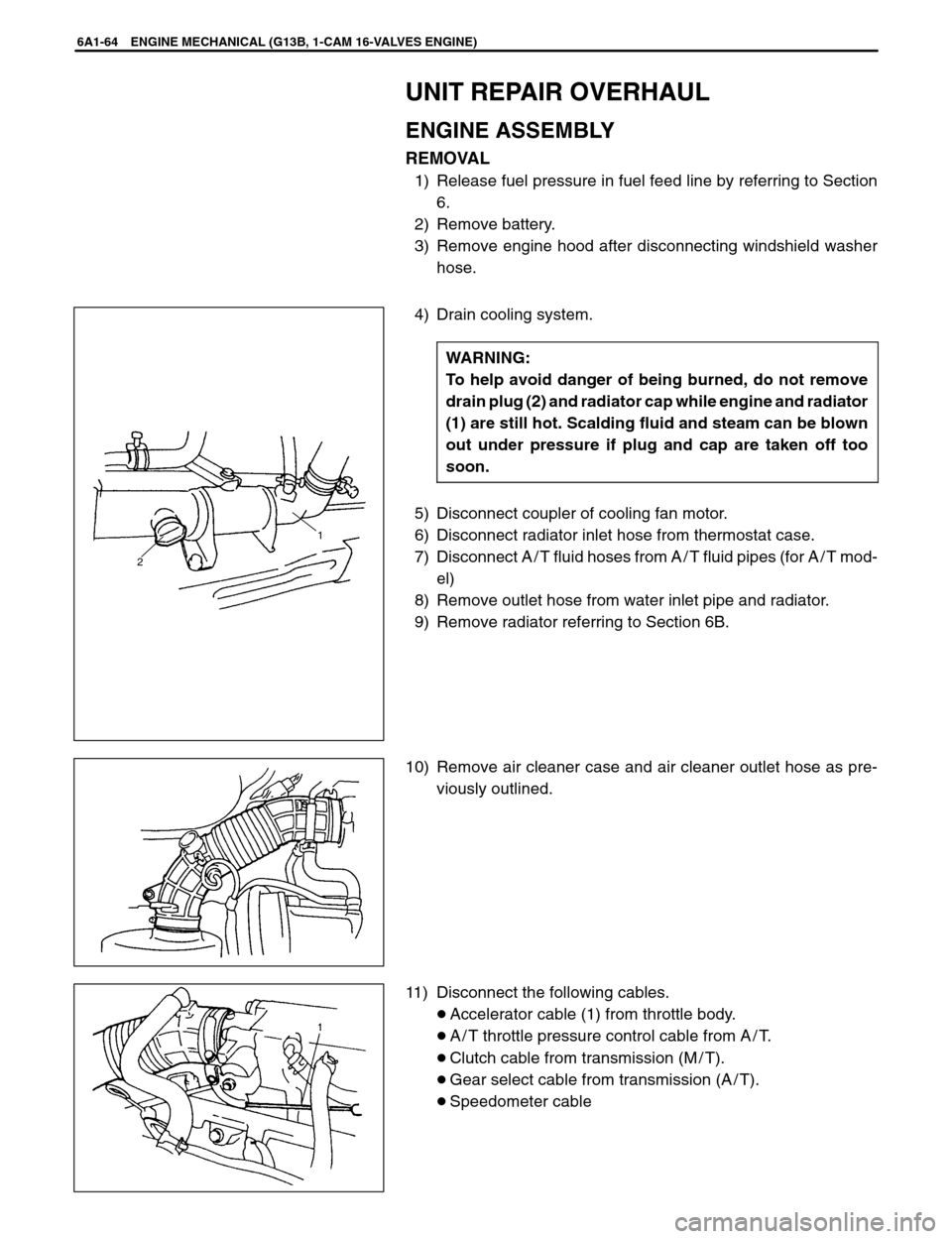
1
2
6A1-64 ENGINE MECHANICAL (G13B, 1-CAM 16-VALVES ENGINE)
UNIT REPAIR OVERHAUL
ENGINE ASSEMBLY
REMOVAL
1) Release fuel pressure in fuel feed line by referring to Section
6.
2) Remove battery.
3) Remove engine hood after disconnecting windshield washer
hose.
4) Drain cooling system.
WARNING:
To help avoid danger of being burned, do not remove
drain plug (2) and radiator cap while engine and radiator
(1) are still hot. Scalding fluid and steam can be blown
out under pressure if plug and cap are taken off too
soon.
5) Disconnect coupler of cooling fan motor.
6) Disconnect radiator inlet hose from thermostat case.
7) Disconnect A / T fluid hoses from A / T fluid pipes (for A / T mod-
el)
8) Remove outlet hose from water inlet pipe and radiator.
9) Remove radiator referring to Section 6B.
10) Remove air cleaner case and air cleaner outlet hose as pre-
viously outlined.
11) Disconnect the following cables.
Accelerator cable (1) from throttle body.
A / T throttle pressure control cable from A / T.
Clutch cable from transmission (M / T).
Gear select cable from transmission (A / T).
Speedometer cable
Page 389 of 557
1. Fuel tank
2. Fuel pump and level gauge
3. Fuel filler cap
4. 2-way check valve
5. Breather hose
6. Fuel feed line
7. Fuel return line
8. Fuel vapor line
9. Fuel cut valve
10. Fuel tank pad
11. Fuel tank fixer bolt
: Tightening Torque
6C-2 ENGINE FUEL
ON-VEHICLE SERVICE
FUEL LINES
INSPECTION
Visually inspect fuel lines for evidence of fuel leakage, hose crack
and deterioration, or damage.
Make sure all clamps are secure.
Replace parts as needed.
FUEL TANK
REMOVAL
1) Relieve fuel pressure in fuel feed line according to procedure de-
scribed in Section 6.
2) Disconnect negative cable at battery.
3) Remove rear seat cushion referring to Section 9.
4) Disconnect connectors (1) of fuel tank wire harness.
5) Hoist vehicle.
6) Disconnect fuel filler hose (3) from fuel tank and breather hose
(2) from filler neck (1).