Page 231 of 557
ENGINE GENERAL INFORMATION AND DIAGNOSIS (SFI FOR G13) 6-1-75
To ignition
switch
Signal rotor
on CamshaftCamshaft
position
sensor
Waveforms at specified idle speed
Oscilloscope Waveforms
2 V / Div.
Crank
angle20 ms / Div.
180
720
DTC P0340 CAMSHAFT POSITION (CMP) SENSOR CIRCUIT
MALFUNCTION
CIRCUIT DESCRIPTION
DTC DETECTING CONDITIONPOSSIBLE CAUSE
No CMP sensor signal during engine running
(CKP sensor signal is inputted).CMP sensor circuit open or short.
Signal rotor teeth damaged.
CMP sensor malfunction, foreign material being
attached or improper installation.
ECM (PCM) malfunction.
Reference
Connect oscilloscope between terminals C01-11 of ECM (PCM) connector connected to ECM (PCM) and body
ground and check CKP sensor signal.
DTC CONFIRMATION PROCEDURE
1) Clear DTC.
2) Start engine and keep it at idle for 1 min.
3) Select “DTC” mode on scan tool and check DTC.
Page 232 of 557
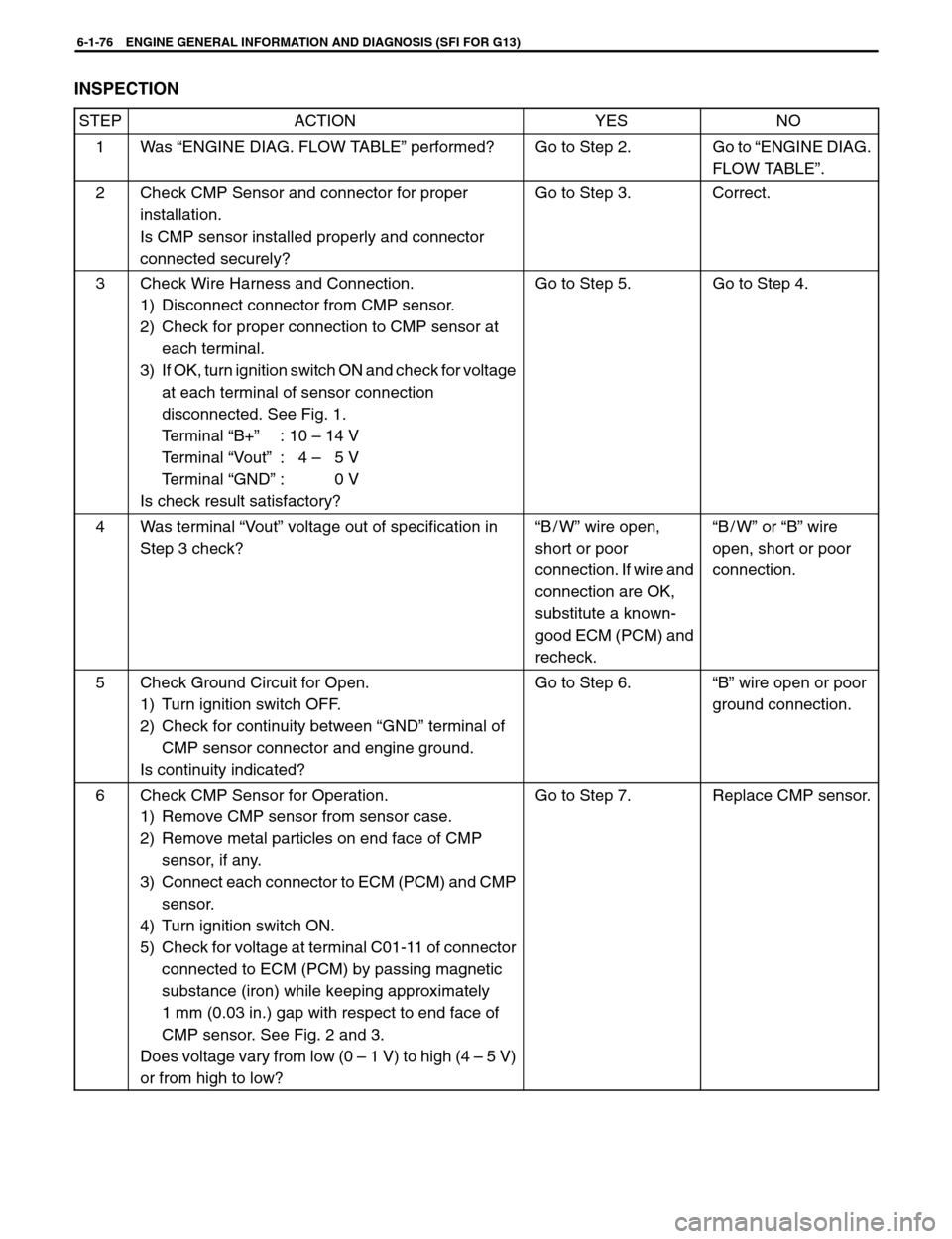
6-1-76 ENGINE GENERAL INFORMATION AND DIAGNOSIS (SFI FOR G13)
INSPECTION
STEPACTIONYESNO
1Was “ENGINE DIAG. FLOW TABLE” performed?Go to Step 2.Go to “ENGINE DIAG.
FLOW TABLE”.
2Check CMP Sensor and connector for proper
installation.
Is CMP sensor installed properly and connector
connected securely?Go to Step 3.Correct.
3Check Wire Harness and Connection.
1) Disconnect connector from CMP sensor.
2) Check for proper connection to CMP sensor at
each terminal.
3) If OK, turn ignition switch ON and check for voltage
at each terminal of sensor connection
disconnected. See Fig. 1.
Terminal “B+”: 10 – 14 V
Terminal “Vout”: 4 – 5 V
Terminal “GND”: – 0 V
Is check result satisfactory?Go to Step 5.Go to Step 4.
4Was terminal “Vout” voltage out of specification in
Step 3 check?“B/W” wire open,
short or poor
connection. If wire and
connection are OK,
substitute a known-
good ECM (PCM) and
recheck.“B/W” or “B” wire
open, short or poor
connection.
5Check Ground Circuit for Open.
1) Turn ignition switch OFF.
2) Check for continuity between “GND” terminal of
CMP sensor connector and engine ground.
Is continuity indicated?Go to Step 6.“B” wire open or poor
ground connection.
6Check CMP Sensor for Operation.
1) Remove CMP sensor from sensor case.
2) Remove metal particles on end face of CMP
sensor, if any.
3) Connect each connector to ECM (PCM) and CMP
sensor.
4) Turn ignition switch ON.
5) Check for voltage at terminal C01-11 of connector
connected to ECM (PCM) by passing magnetic
substance (iron) while keeping approximately
1 mm (0.03 in.) gap with respect to end face of
CMP sensor. See Fig. 2 and 3.
Does voltage vary from low (0 – 1 V) to high (4 – 5 V)
or from high to low?Go to Step 7.Replace CMP sensor.
Page 233 of 557
ENGINE GENERAL INFORMATION AND DIAGNOSIS (SFI FOR G13) 6-1-77
GND Vout
B+
Magnetic substance (iron)
Mirror
STEPACTIONYESNO
7Check signal rotor for the following, using mirror.
See Fig. 4.
Damage
No foreign material attached
Is it in good condition?Intermittent trouble or
faulty ECM (PCM).
Check for intermittent
referring to
“Intermittent and
Poor Connection” in
Section 0A.Clean rotor teeth or
replace CMP sensor.
Fig. 1 for Step 3 Fig. 2 for Step 4 Fig. 3 for Step 6
Fig. 4 for Step 7
Page 329 of 557
1. Oil plug
6A1-34 ENGINE MECHANICAL (G13B, 1-CAM 16-VALVES ENGINE)
4) Disconnect CMP sensor coupler from CMP sensor.
5) Remove CMP sensor case (1) from cylinder head.
Place a container or rag under CMP sensor case, for a small
amount of oil flows out during removal of case.
6) After loosening all valve adjusting screw lock nuts (2), turn ad-
justing screws (1) back all the way to allow all rocker arms (3) to
move freely.
7) Remove camshaft housing and camshaft.
NOTE:
To remove camshaft housing bolts, loosen them in such or-
der as indicated in figure, a little at a time.
8) Remove timing belt inside cover (2).
9) Remove intake rocker arm (1) with clip (2) from rocker arm shaft
(3).
NOTE:
Do not bend clip when removing intake rocker arm.
Page 335 of 557
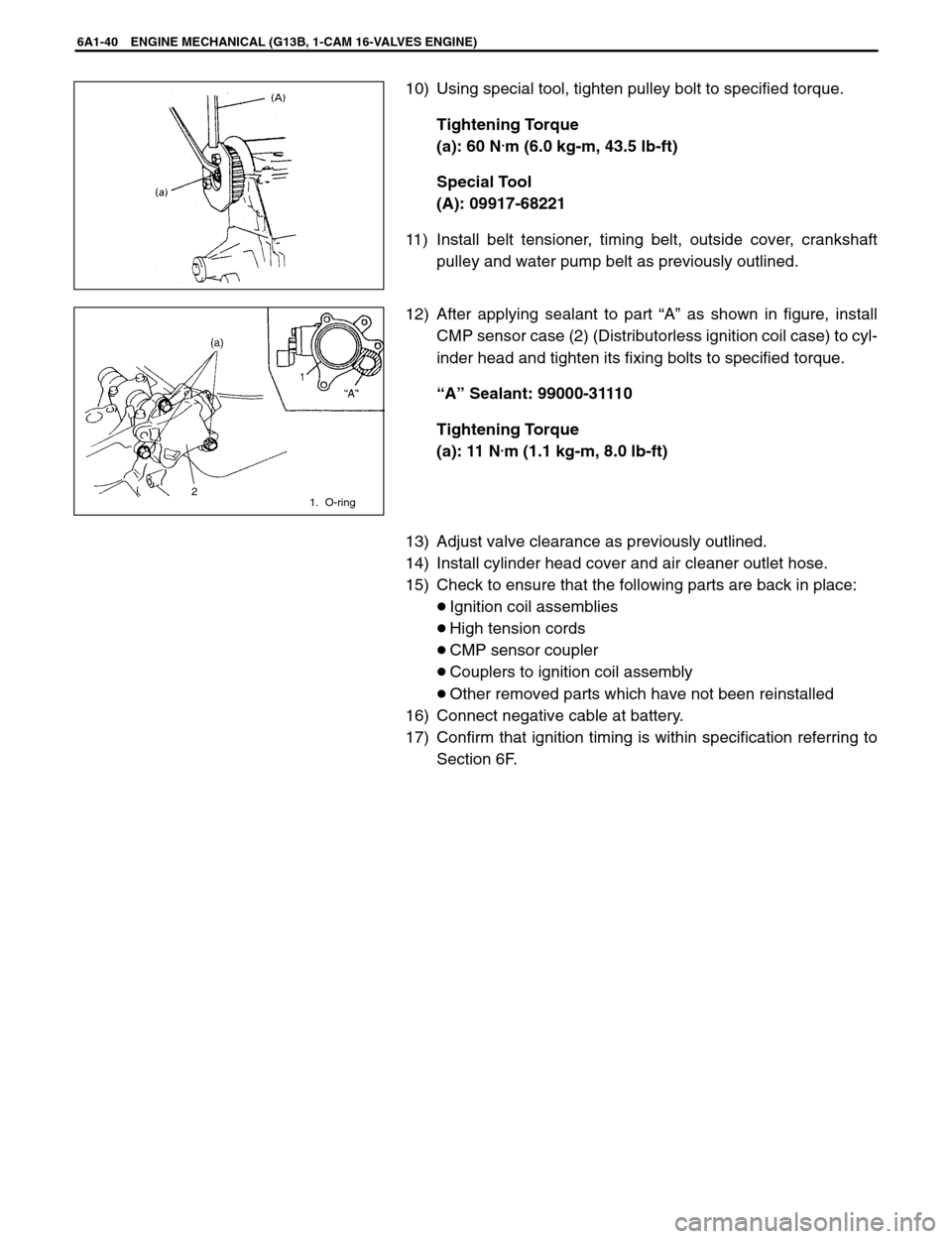
6A1-40 ENGINE MECHANICAL (G13B, 1-CAM 16-VALVES ENGINE)
1. O-ring2
10) Using special tool, tighten pulley bolt to specified torque.
Tightening Torque
(a): 60 N
.m (6.0 kg-m, 43.5 lb-ft)
Special Tool
(A): 09917-68221
11) Install belt tensioner, timing belt, outside cover, crankshaft
pulley and water pump belt as previously outlined.
12) After applying sealant to part “A” as shown in figure, install
CMP sensor case (2) (Distributorless ignition coil case) to cyl-
inder head and tighten its fixing bolts to specified torque.
“A” Sealant: 99000-31110
Tightening Torque
(a): 11 N
.m (1.1 kg-m, 8.0 lb-ft)
13) Adjust valve clearance as previously outlined.
14) Install cylinder head cover and air cleaner outlet hose.
15) Check to ensure that the following parts are back in place:
Ignition coil assemblies
High tension cords
CMP sensor coupler
Couplers to ignition coil assembly
Other removed parts which have not been reinstalled
16) Connect negative cable at battery.
17) Confirm that ignition timing is within specification referring to
Section 6F.
Page 338 of 557
3
2. Breather hose
3. PCV valve4. High-tension cords
5. Ignition coil assembly
6. Ignition coil coupler
A: Camshaft pulley side
B: CMP sensor case side
ENGINE MECHANICAL (G13B, 1-CAM 16-VALVES ENGINE) 6A1-43
9) Remove cylinder head cover (1) as previously outlined.
Loosen all valve lash adjusting screws fully.
10) Remove timing belt and camshaft as previously outlined.
11) Disconnect exhaust pipe from exhaust manifold and remove
exhaust manifold stiffener (if equipped).
12) Loosen cylinder head bolts in such order as indicated in figure
and remove them.
13) Check all around cylinder head for any other parts required to
be removed or disconnected and remove or disconnect what-
ever necessary.
14) Remove cylinder head with intake manifold, exhaust manifold
CMP sensor case, using lifting device if necessary.
Page 339 of 557
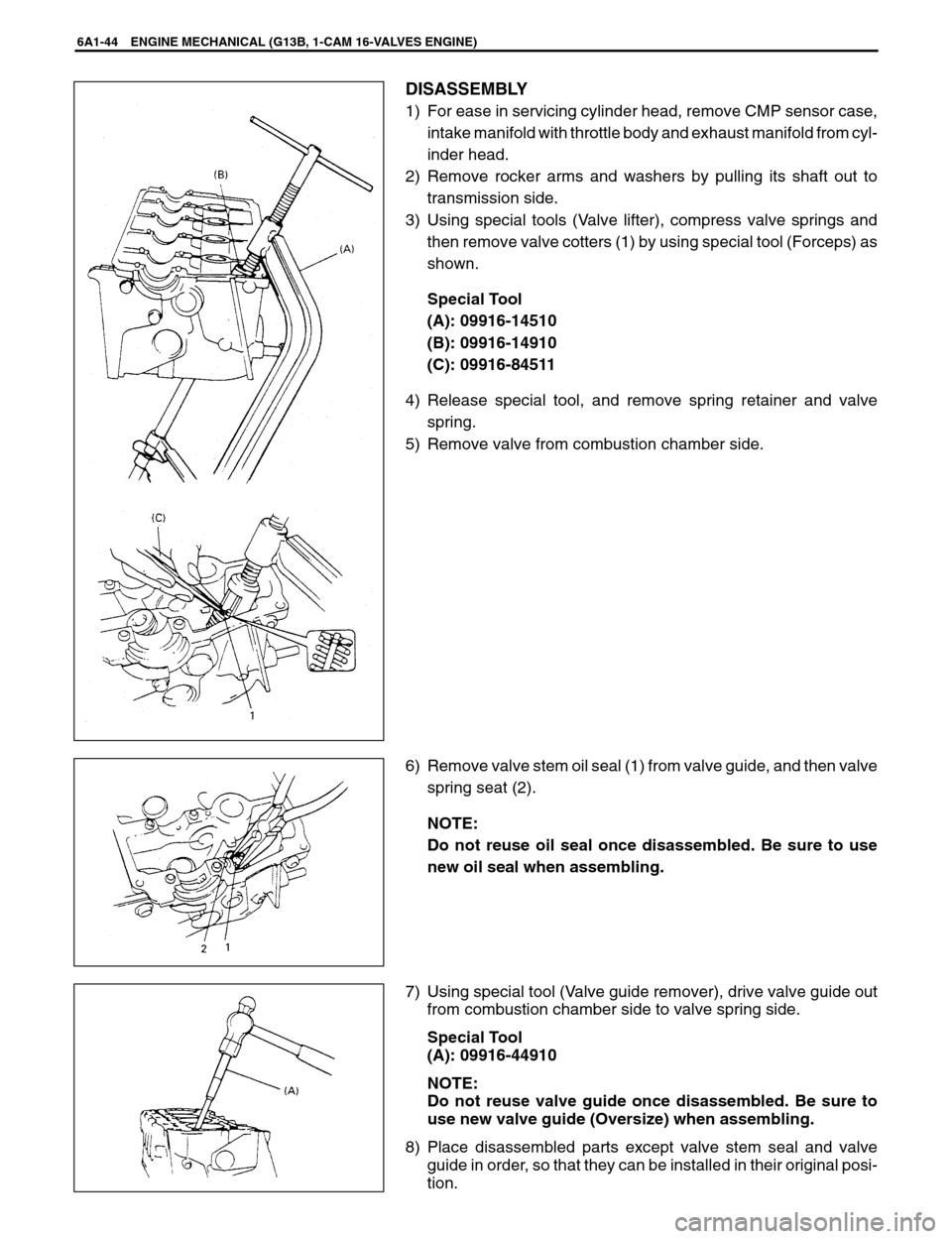
6A1-44 ENGINE MECHANICAL (G13B, 1-CAM 16-VALVES ENGINE)
DISASSEMBLY
1) For ease in servicing cylinder head, remove CMP sensor case,
intake manifold with throttle body and exhaust manifold from cyl-
inder head.
2) Remove rocker arms and washers by pulling its shaft out to
transmission side.
3) Using special tools (Valve lifter), compress valve springs and
then remove valve cotters (1) by using special tool (Forceps) as
shown.
Special Tool
(A): 09916-14510
(B): 09916-14910
(C): 09916-84511
4) Release special tool, and remove spring retainer and valve
spring.
5) Remove valve from combustion chamber side.
6) Remove valve stem oil seal (1) from valve guide, and then valve
spring seat (2).
NOTE:
Do not reuse oil seal once disassembled. Be sure to use
new oil seal when assembling.
7) Using special tool (Valve guide remover), drive valve guide out
from combustion chamber side to valve spring side.
Special Tool
(A): 09916-44910
NOTE:
Do not reuse valve guide once disassembled. Be sure to
use new valve guide (Oversize) when assembling.
8) Place disassembled parts except valve stem seal and valve
guide in order, so that they can be installed in their original posi-
tion.
Page 347 of 557
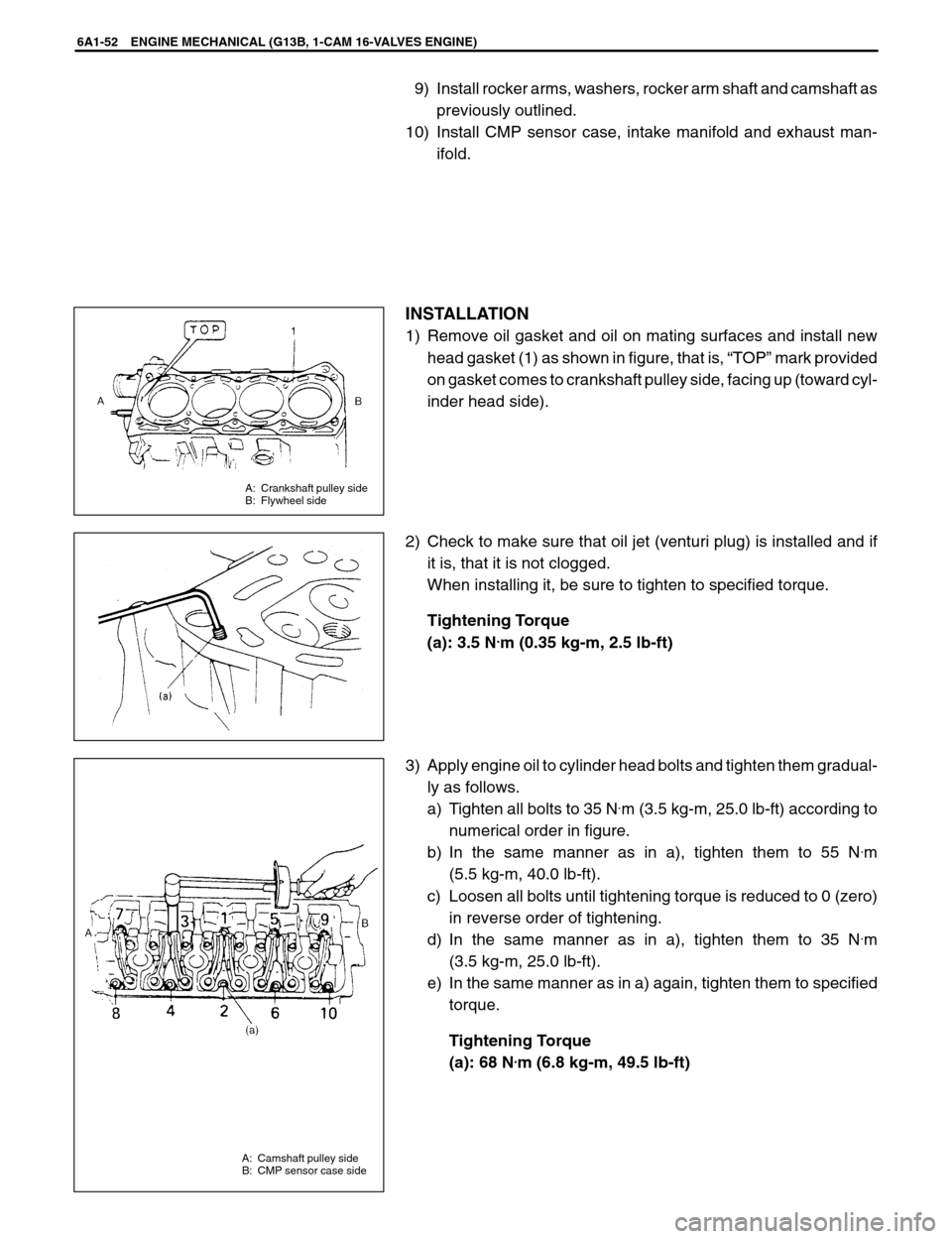
A: Crankshaft pulley side
B: Flywheel side
A: Camshaft pulley side
B: CMP sensor case side
6A1-52 ENGINE MECHANICAL (G13B, 1-CAM 16-VALVES ENGINE)
9) Install rocker arms, washers, rocker arm shaft and camshaft as
previously outlined.
10) Install CMP sensor case, intake manifold and exhaust man-
ifold.
INSTALLATION
1) Remove oil gasket and oil on mating surfaces and install new
head gasket (1) as shown in figure, that is, “TOP” mark provided
on gasket comes to crankshaft pulley side, facing up (toward cyl-
inder head side).
2) Check to make sure that oil jet (venturi plug) is installed and if
it is, that it is not clogged.
When installing it, be sure to tighten to specified torque.
Tightening Torque
(a): 3.5 N
.m (0.35 kg-m, 2.5 lb-ft)
3) Apply engine oil to cylinder head bolts and tighten them gradual-
ly as follows.
a) Tighten all bolts to 35 N
.m (3.5 kg-m, 25.0 lb-ft) according to
numerical order in figure.
b) In the same manner as in a), tighten them to 55 N
.m
(5.5 kg-m, 40.0 lb-ft).
c) Loosen all bolts until tightening torque is reduced to 0 (zero)
in reverse order of tightening.
d) In the same manner as in a), tighten them to 35 N
.m
(3.5 kg-m, 25.0 lb-ft).
e) In the same manner as in a) again, tighten them to specified
torque.
Tightening Torque
(a): 68 N
.m (6.8 kg-m, 49.5 lb-ft)