Page 143 of 698
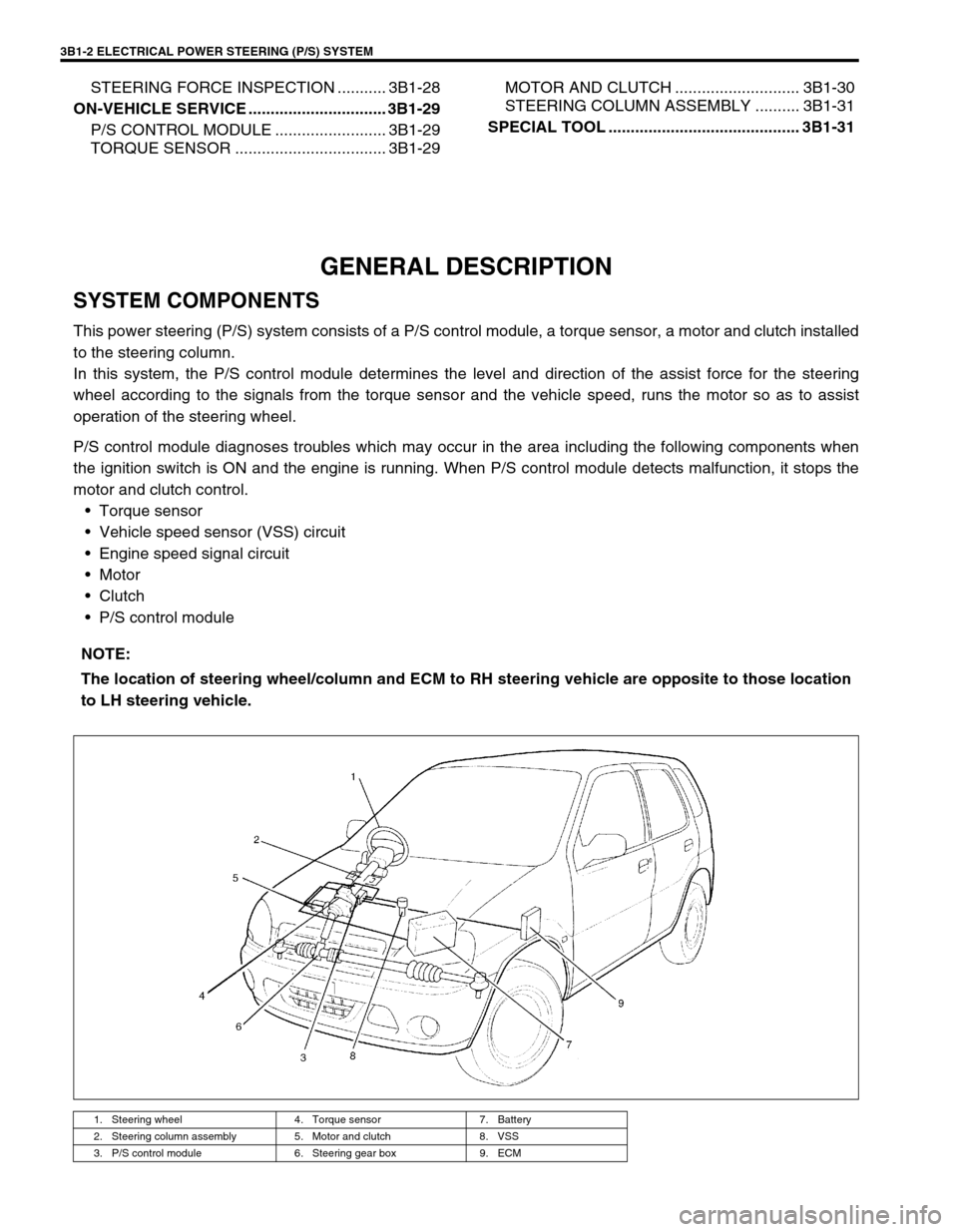
3B1-2 ELECTRICAL POWER STEERING (P/S) SYSTEM
STEERING FORCE INSPECTION ........... 3B1-28
ON-VEHICLE SERVICE ............................... 3B1-29
P/S CONTROL MODULE ......................... 3B1-29
TORQUE SENSOR .................................. 3B1-29MOTOR AND CLUTCH ............................ 3B1-30
STEERING COLUMN ASSEMBLY .......... 3B1-31
SPECIAL TOOL ........................................... 3B1-31
GENERAL DESCRIPTION
SYSTEM COMPONENTS
This power steering (P/S) system consists of a P/S control module, a torque sensor, a motor and clutch installed
to the steering column.
In this system, the P/S control module determines the level and direction of the assist force for the steering
wheel according to the signals from the torque sensor and the vehicle speed, runs the motor so as to assist
operation of the steering wheel.
P/S control module diagnoses troubles which may occur in the area including the following components when
the ignition switch is ON and the engine is running. When P/S control module detects malfunction, it stops the
motor and clutch control.
Torque sensor
Vehicle speed sensor (VSS) circuit
Engine speed signal circuit
Motor
Clutch
P/S control module
NOTE:
The location of steering wheel/column and ECM to RH steering vehicle are opposite to those location
to LH steering vehicle.
1. Steering wheel 4. Torque sensor 7. Battery
2. Steering column assembly 5. Motor and clutch 8. VSS
3. P/S control module 6. Steering gear box 9. ECM
Page 167 of 698
3B1-26 ELECTRICAL POWER STEERING (P/S) SYSTEM
INSPECTION OF P/S CONTROL MODULE
AND ITS CIRCUITS
P/S control module (1) and its circuits can be checked at P/S con-
trol module wiring couplers (2) by measuring voltage and resis-
tance.
Voltage Check
1) Remove steering column lower cover with ignition switch
OFF position.
2) Check voltage at each terminal with connectors (2) con-
nected P/S control module. CAUTION:
P/S control module cannot be checked by itself. It is
strictly prohibited to connect voltmeter or ohmmeter to
P/S control module with connector disconnected from it.
NOTE:
As each terminal voltage is affected by the battery volt-
age, confirm that it is 11V or more when ignition switch is
ON.
Page 168 of 698
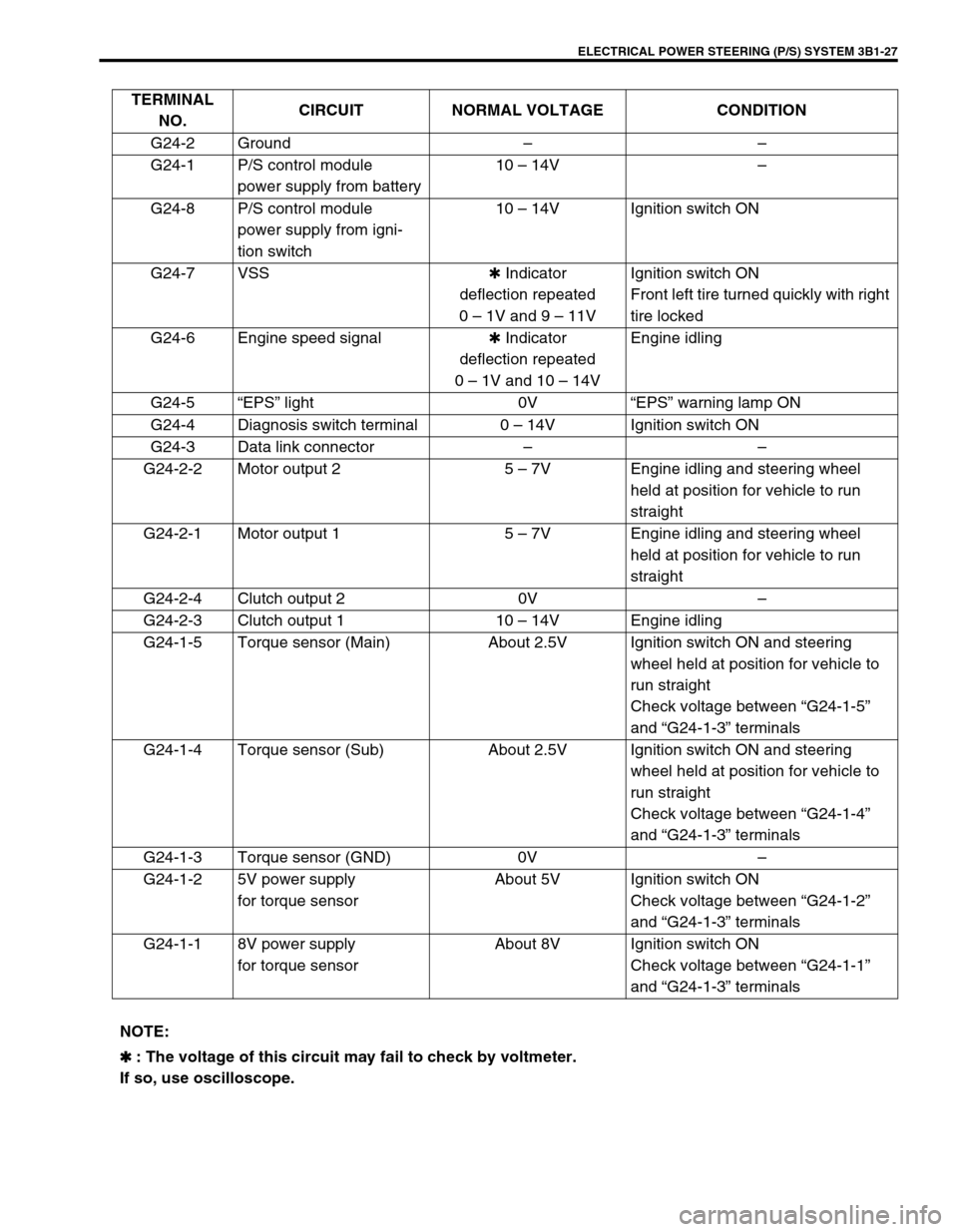
ELECTRICAL POWER STEERING (P/S) SYSTEM 3B1-27
TERMINAL
NO.CIRCUIT NORMAL VOLTAGE CONDITION
G24-2 Ground––
G24-1 P/S control module
power supply from battery10 – 14V–
G24-8 P/S control module
power supply from igni-
tion switch10 – 14V Ignition switch ON
G24-7 VSS✱ Indicator
deflection repeated
0 – 1V and 9 – 11VIgnition switch ON
Front left tire turned quickly with right
tire locked
G24-6 Engine speed signal✱ Indicator
deflection repeated
0 – 1V and 10 – 14VEngine idling
G24-5“EPS” light 0V“EPS” warning lamp ON
G24-4 Diagnosis switch terminal 0 – 14V Ignition switch ON
G24-3 Data link connector––
G24-2-2 Motor output 2 5 – 7V Engine idling and steering wheel
held at position for vehicle to run
straight
G24-2-1 Motor output 1 5 – 7V Engine idling and steering wheel
held at position for vehicle to run
straight
G24-2-4 Clutch output 2 0V–
G24-2-3 Clutch output 1 10 – 14V Engine idling
G24-1-5 Torque sensor (Main) About 2.5V Ignition switch ON and steering
wheel held at position for vehicle to
run straight
Check voltage between “G24-1-5”
and “G24-1-3” terminals
G24-1-4 Torque sensor (Sub) About 2.5V Ignition switch ON and steering
wheel held at position for vehicle to
run straight
Check voltage between “G24-1-4”
and “G24-1-3” terminals
G24-1-3 Torque sensor (GND) 0V–
G24-1-2 5V power supply
for torque sensorAbout 5V Ignition switch ON
Check voltage between “G24-1-2”
and “G24-1-3” terminals
G24-1-1 8V power supply
for torque sensorAbout 8V Ignition switch ON
Check voltage between “G24-1-1”
and “G24-1-3” terminals
NOTE:
✱
✱✱ ✱ : The voltage of this circuit may fail to check by voltmeter.
If so, use oscilloscope.
Page 170 of 698
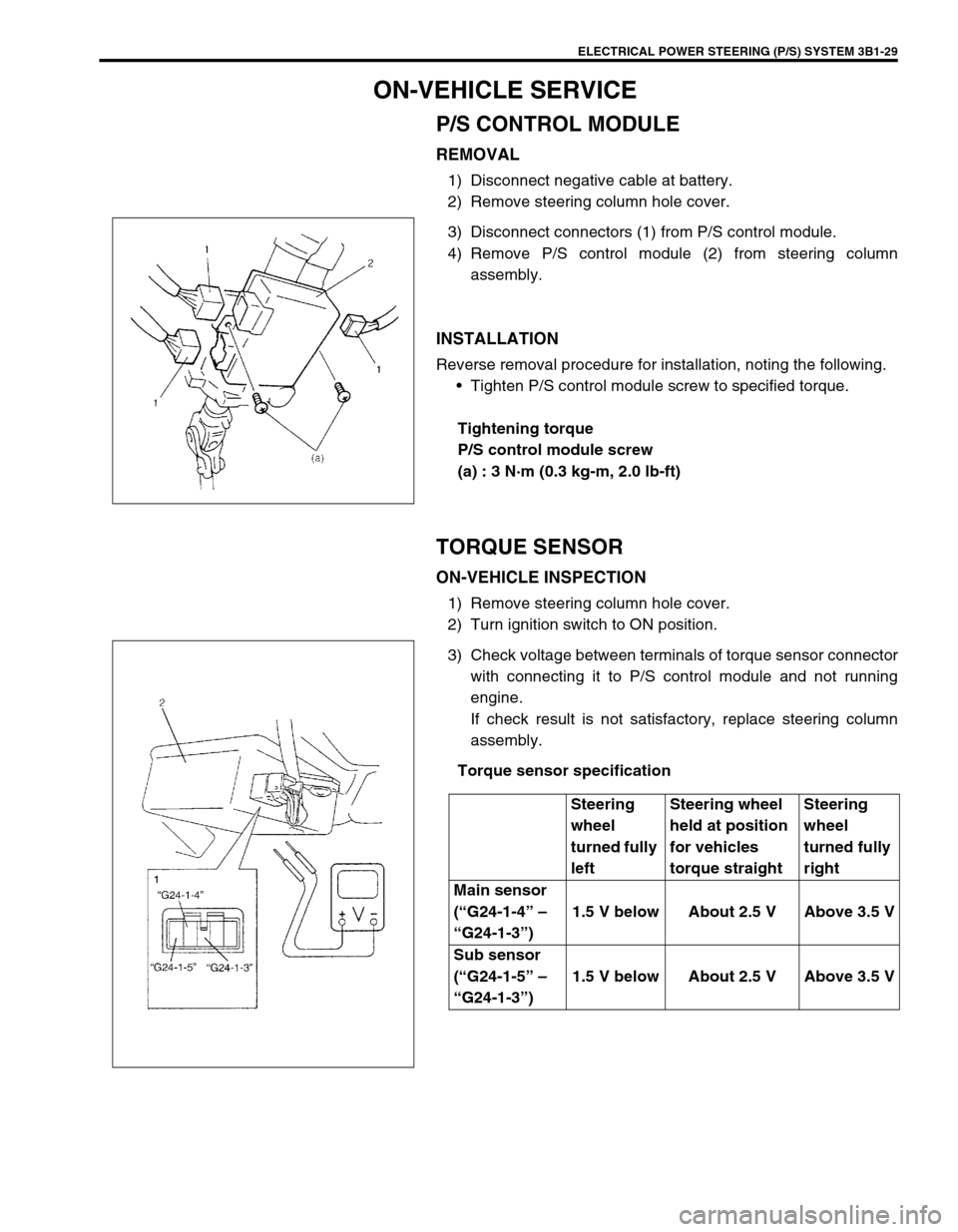
ELECTRICAL POWER STEERING (P/S) SYSTEM 3B1-29
ON-VEHICLE SERVICE
P/S CONTROL MODULE
REMOVAL
1) Disconnect negative cable at battery.
2) Remove steering column hole cover.
3) Disconnect connectors (1) from P/S control module.
4) Remove P/S control module (2) from steering column
assembly.
INSTALLATION
Reverse removal procedure for installation, noting the following.
Tighten P/S control module screw to specified torque.
Tightening torque
P/S control module screw
(a) : 3 N·m (0.3 kg-m, 2.0 lb-ft)
TORQUE SENSOR
ON-VEHICLE INSPECTION
1) Remove steering column hole cover.
2) Turn ignition switch to ON position.
3) Check voltage between terminals of torque sensor connector
with connecting it to P/S control module and not running
engine.
If check result is not satisfactory, replace steering column
assembly.
Torque sensor specification
Steering
wheel
turned fully
leftSteering wheel
held at position
for vehicles
torque straightSteering
wheel
turned fully
right
Main sensor
(“G24-1-4” –
“G24-1-3”)1.5 V below About 2.5 V Above 3.5 V
Sub sensor
(“G24-1-5” –
“G24-1-3”)1.5 V below About 2.5 V Above 3.5 V
Page 171 of 698
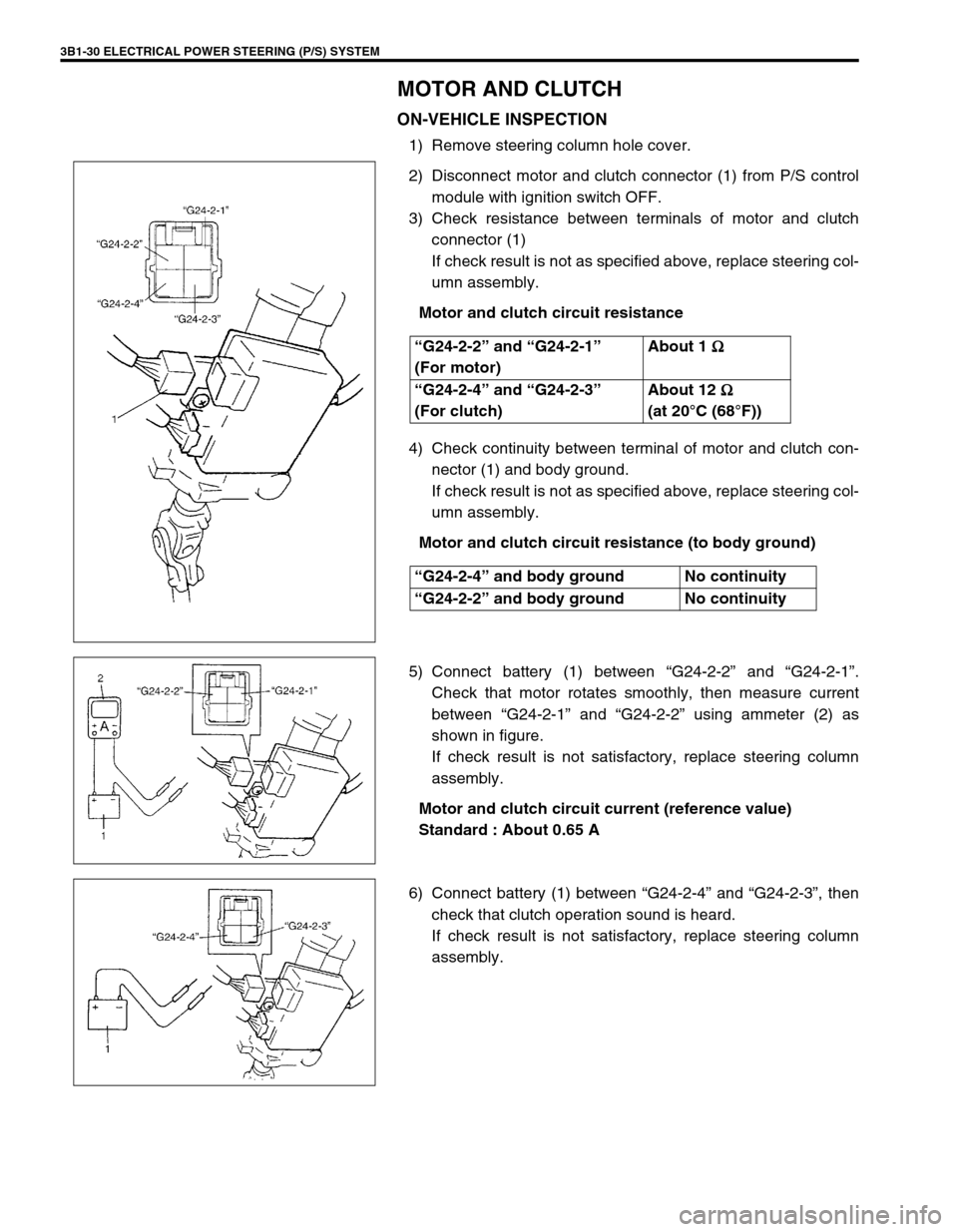
3B1-30 ELECTRICAL POWER STEERING (P/S) SYSTEM
MOTOR AND CLUTCH
ON-VEHICLE INSPECTION
1) Remove steering column hole cover.
2) Disconnect motor and clutch connector (1) from P/S control
module with ignition switch OFF.
3) Check resistance between terminals of motor and clutch
connector (1)
If check result is not as specified above, replace steering col-
umn assembly.
Motor and clutch circuit resistance
4) Check continuity between terminal of motor and clutch con-
nector (1) and body ground.
If check result is not as specified above, replace steering col-
umn assembly.
Motor and clutch circuit resistance (to body ground)
5) Connect battery (1) between “G24-2-2” and “G24-2-1”.
Check that motor rotates smoothly, then measure current
between “G24-2-1” and “G24-2-2” using ammeter (2) as
shown in figure.
If check result is not satisfactory, replace steering column
assembly.
Motor and clutch circuit current (reference value)
Standard : About 0.65 A
6) Connect battery (1) between “G24-2-4” and “G24-2-3”, then
check that clutch operation sound is heard.
If check result is not satisfactory, replace steering column
assembly. “G24-2-2” and “G24-2-1”
(For motor)About 1
Ω
ΩΩ Ω
“G24-2-4” and “G24-2-3”
(For clutch)About 12
Ω
ΩΩ Ω
(at 20°C (68°F))
“G24-2-4” and body ground No continuity
“G24-2-2” and body ground No continuity
Page 177 of 698
3C-4 STEERING WHEEL AND COLUMN
HANDLING AND STORAGE
For handling and storage, refer to “HANDLING AND STORAGE” under “SERVICE PRECAUTIONS” in Section
10B.
DISPOSAL
For disposal, refer to “DISPOSAL” under “SERVICE PRECAUTIONS” in Section 10B.
DRIVER AIR BAG (INFLATOR) MODULE
REMOVAL
1) Disconnect negative cable at battery.
2) Disable air bag system. Refer to “DISABLING AIR BAG
SYSTEM” under “SERVICE PRECAUTIONS” in Section
10B.
3) Loosen 2 bolts (1) mounting driver air bag (inflator) module
on its both side.
4) Remove driver air bag (inflator) module (3) from steering
wheel.
5) Disconnect yellow connector (1) of driver air bag (inflator)
module and horn connector (2) in order a) – d) shown in fig-
ure. WARNING:
When handling an air bag (inflator) module, be sure to
read “SERVICE PRECAUTIONS” in Section 10B and
observe each instruction. Failure to follow them could
cause a damage to the air bag (inflator) module or result
in personal injury.
Page 178 of 698
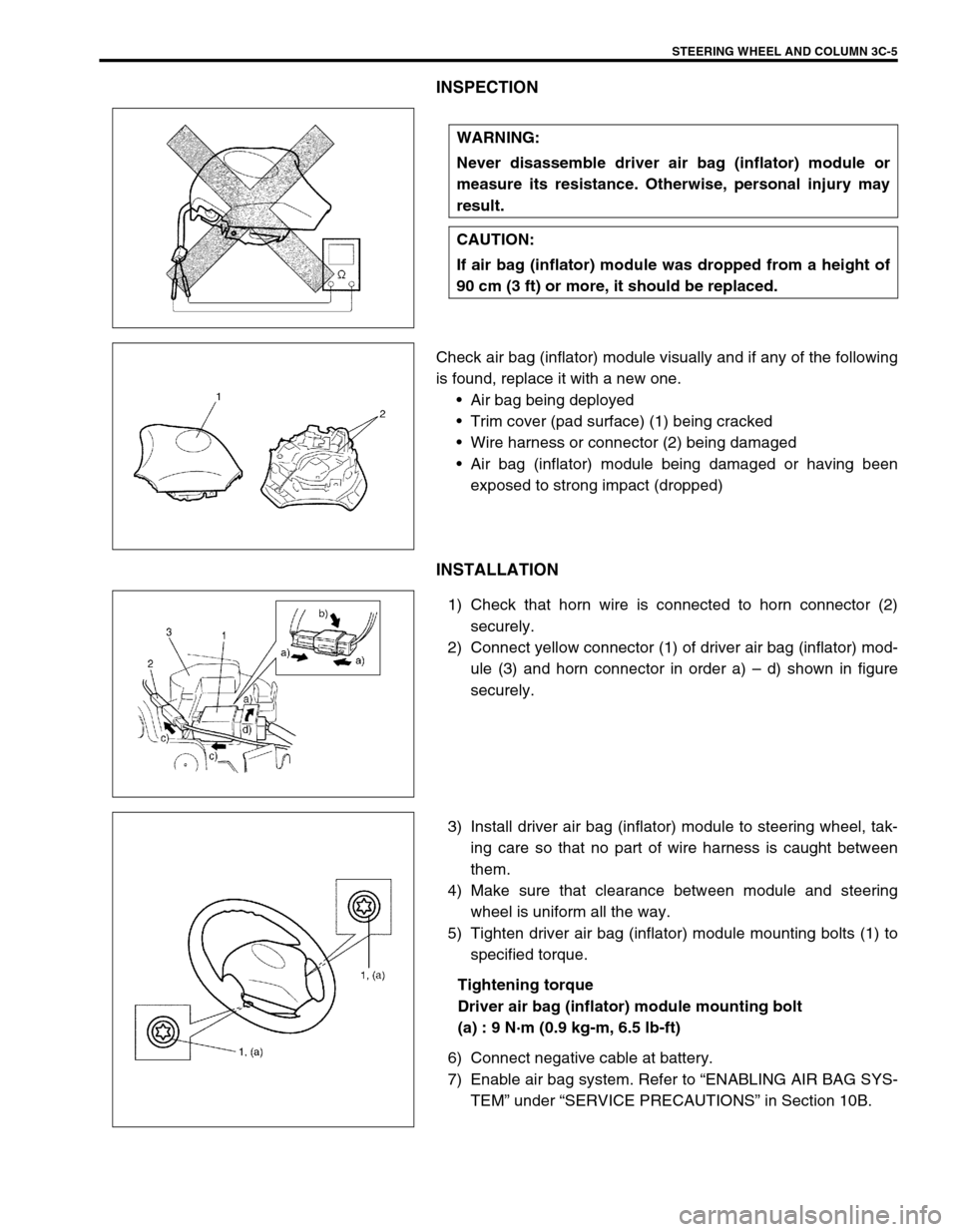
STEERING WHEEL AND COLUMN 3C-5
INSPECTION
Check air bag (inflator) module visually and if any of the following
is found, replace it with a new one.
Air bag being deployed
Trim cover (pad surface) (1) being cracked
Wire harness or connector (2) being damaged
Air bag (inflator) module being damaged or having been
exposed to strong impact (dropped)
INSTALLATION
1) Check that horn wire is connected to horn connector (2)
securely.
2) Connect yellow connector (1) of driver air bag (inflator) mod-
ule (3) and horn connector in order a) – d) shown in figure
securely.
3) Install driver air bag (inflator) module to steering wheel, tak-
ing care so that no part of wire harness is caught between
them.
4) Make sure that clearance between module and steering
wheel is uniform all the way.
5) Tighten driver air bag (inflator) module mounting bolts (1) to
specified torque.
Tightening torque
Driver air bag (inflator) module mounting bolt
(a) : 9 N·m (0.9 kg-m, 6.5 lb-ft)
6) Connect negative cable at battery.
7) Enable air bag system. Refer to “ENABLING AIR BAG SYS-
TEM” under “SERVICE PRECAUTIONS” in Section 10B. WARNING:
Never disassemble driver air bag (inflator) module or
measure its resistance. Otherwise, personal injury may
result.
CAUTION:
If air bag (inflator) module was dropped from a height of
90 cm (3 ft) or more, it should be replaced.
Page 184 of 698
STEERING WHEEL AND COLUMN 3C-11
REMOVAL
1) Disconnect negative cable at battery.
2) Disable air bag system. Refer to “DISABLING AIR BAG
SYSTEM” under “SERVICE PRECAUTIONS” in Section
10B.
3) If it is necessary to remove steering wheel and contact coil
and combination switch assembly, remove them, referring to
“STEERING WHEEL” and “CONTACT COIL AND COMBI-
NATION SWITCH ASSEMBLY”.
If it is not necessary to remove steering wheel and contact
coil and combination switch assembly, perform the following
procedure.
a) Turn steering wheel so that vehicle’s front tires are at
straight-ahead position.
b) Turn ignition switch to “LOCK” position and remove key.
4) Remove steering column hole cover (1).
5) Loosen steering column mounting nuts (“A”, “B”). WARNING:
Never rest a steering column assembly on the steering
wheel with the air bag (inflator) module face down and
column vertical. Otherwise, personal injury may result.
1