Page 636 of 698
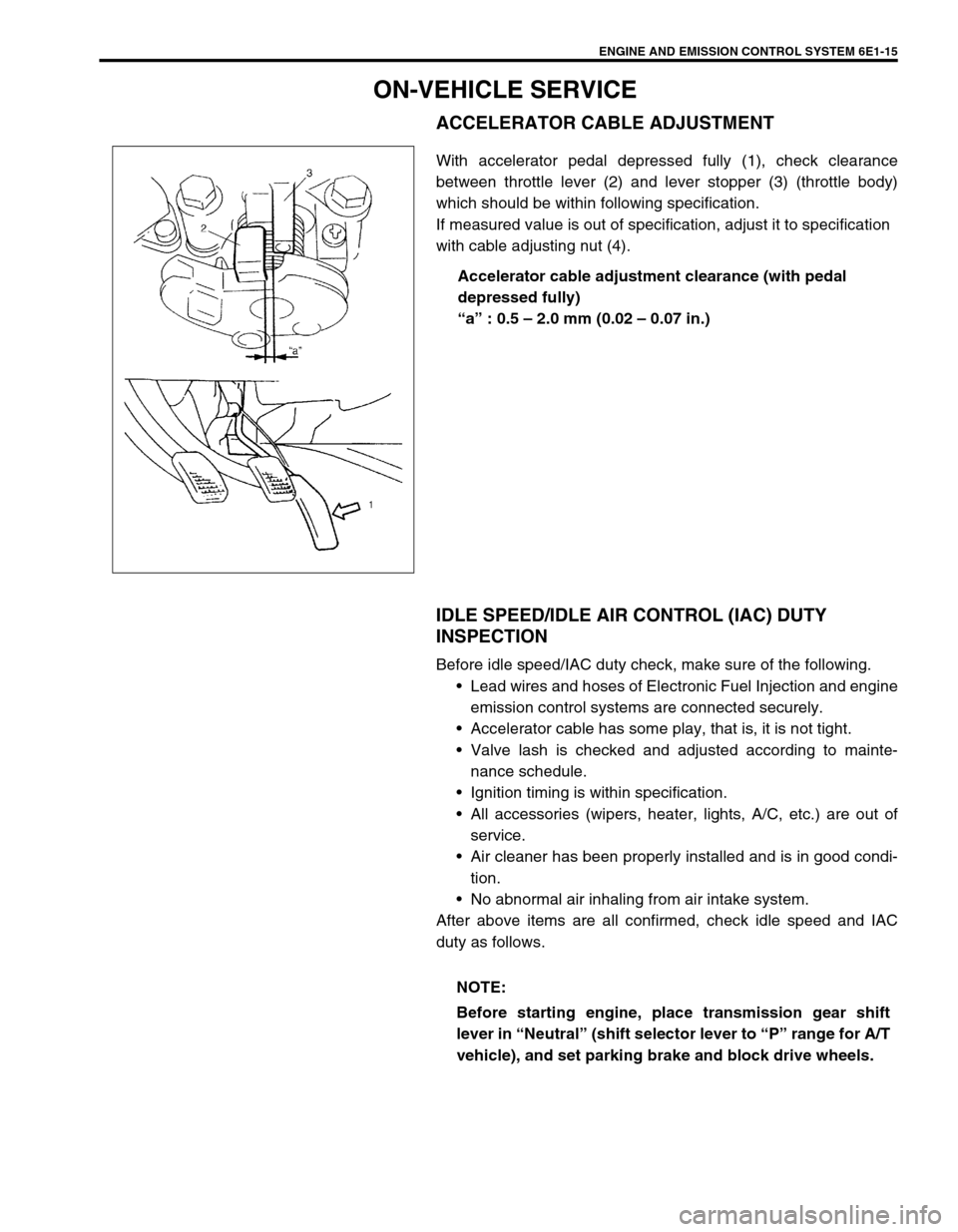
ENGINE AND EMISSION CONTROL SYSTEM 6E1-15
ON-VEHICLE SERVICE
ACCELERATOR CABLE ADJUSTMENT
With accelerator pedal depressed fully (1), check clearance
between throttle lever (2) and lever stopper (3) (throttle body)
which should be within following specification.
If measured value is out of specification, adjust it to specification
with cable adjusting nut (4).
Accelerator cable adjustment clearance (with pedal
depressed fully)
“a” : 0.5 – 2.0 mm (0.02 – 0.07 in.)
IDLE SPEED/IDLE AIR CONTROL (IAC) DUTY
INSPECTION
Before idle speed/IAC duty check, make sure of the following.
Lead wires and hoses of Electronic Fuel Injection and engine
emission control systems are connected securely.
Accelerator cable has some play, that is, it is not tight.
Valve lash is checked and adjusted according to mainte-
nance schedule.
Ignition timing is within specification.
All accessories (wipers, heater, lights, A/C, etc.) are out of
service.
Air cleaner has been properly installed and is in good condi-
tion.
No abnormal air inhaling from air intake system.
After above items are all confirmed, check idle speed and IAC
duty as follows.
NOTE:
Before starting engine, place transmission gear shift
lever in “Neutral” (shift selector lever to “P” range for A/T
vehicle), and set parking brake and block drive wheels.
Page 642 of 698
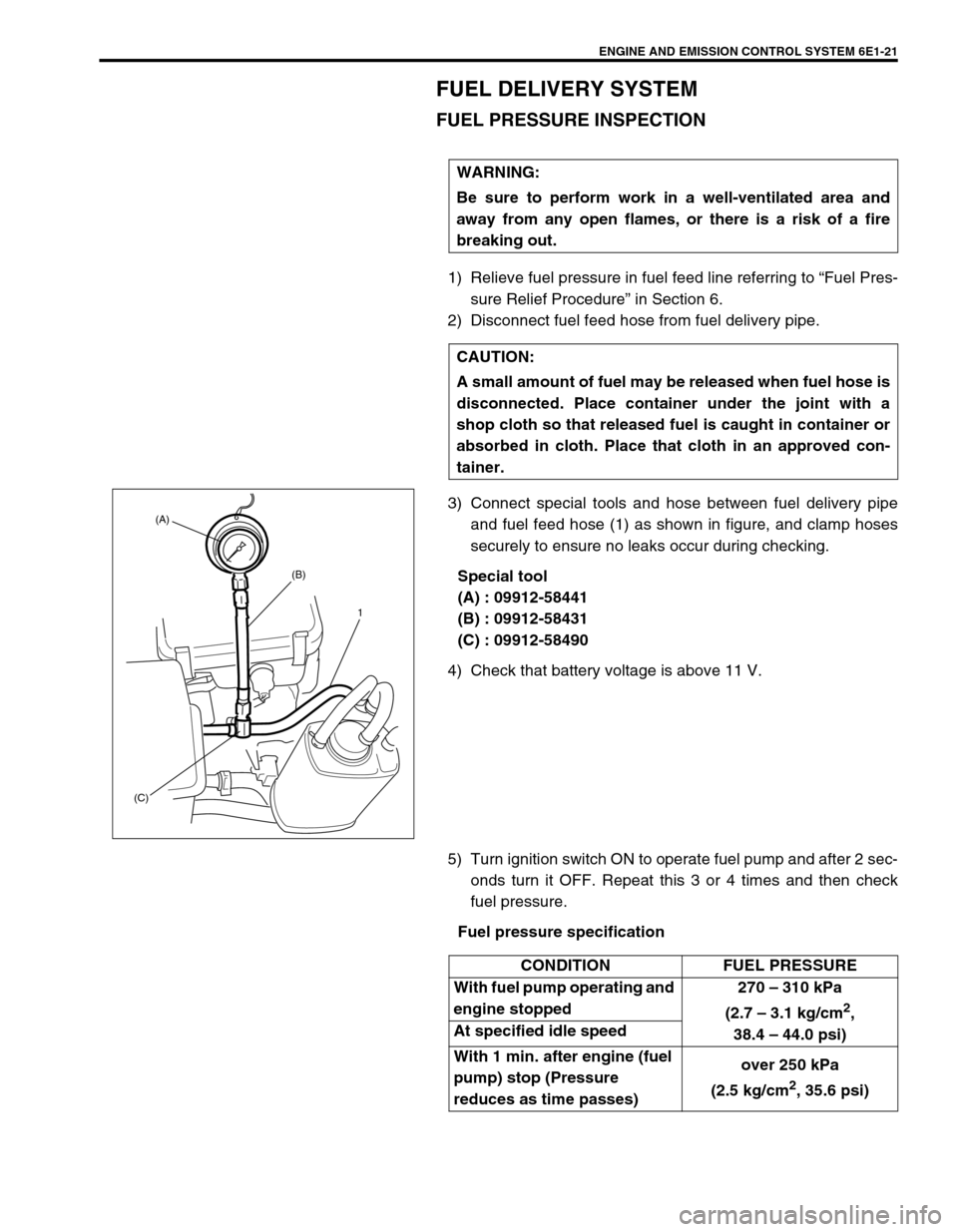
ENGINE AND EMISSION CONTROL SYSTEM 6E1-21
FUEL DELIVERY SYSTEM
FUEL PRESSURE INSPECTION
1) Relieve fuel pressure in fuel feed line referring to “Fuel Pres-
sure Relief Procedure” in Section 6.
2) Disconnect fuel feed hose from fuel delivery pipe.
3) Connect special tools and hose between fuel delivery pipe
and fuel feed hose (1) as shown in figure, and clamp hoses
securely to ensure no leaks occur during checking.
Special tool
(A) : 09912-58441
(B) : 09912-58431
(C) : 09912-58490
4) Check that battery voltage is above 11 V.
5) Turn ignition switch ON to operate fuel pump and after 2 sec-
onds turn it OFF. Repeat this 3 or 4 times and then check
fuel pressure.
Fuel pressure specification WARNING:
Be sure to perform work in a well-ventilated area and
away from any open flames, or there is a risk of a fire
breaking out.
CAUTION:
A small amount of fuel may be released when fuel hose is
disconnected. Place container under the joint with a
shop cloth so that released fuel is caught in container or
absorbed in cloth. Place that cloth in an approved con-
tainer.
(A)
(B)
(C)1
CONDITION FUEL PRESSURE
With fuel pump operating and
engine stopped270 – 310 kPa
(2.7 – 3.1 kg/cm
2,
38.4 – 44.0 psi) At specified idle speed
With 1 min. after engine (fuel
pump) stop (Pressure
reduces as time passes)over 250 kPa
(2.5 kg/cm
2, 35.6 psi)
Page 643 of 698
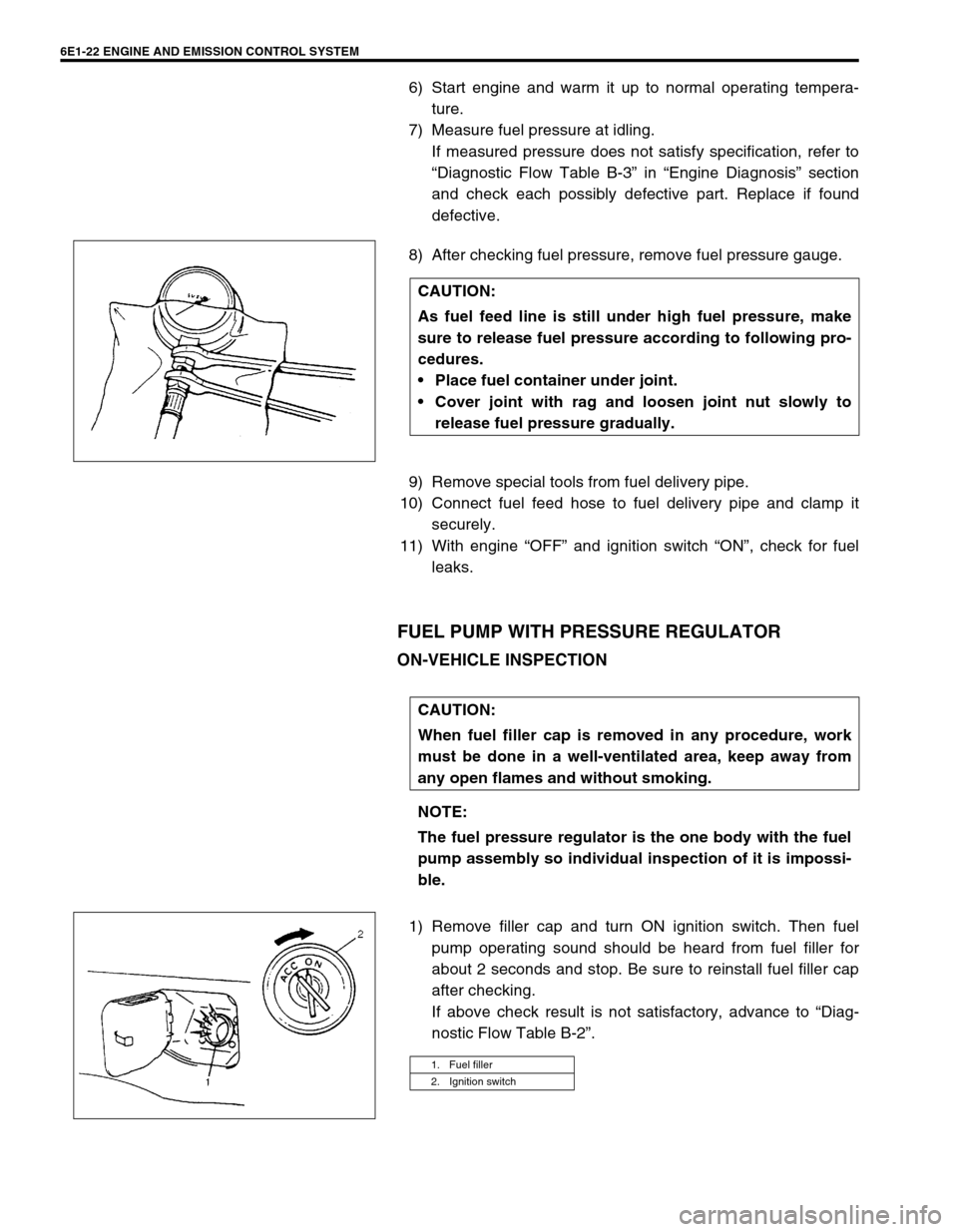
6E1-22 ENGINE AND EMISSION CONTROL SYSTEM
6) Start engine and warm it up to normal operating tempera-
ture.
7) Measure fuel pressure at idling.
If measured pressure does not satisfy specification, refer to
“Diagnostic Flow Table B-3” in “Engine Diagnosis” section
and check each possibly defective part. Replace if found
defective.
8) After checking fuel pressure, remove fuel pressure gauge.
9) Remove special tools from fuel delivery pipe.
10) Connect fuel feed hose to fuel delivery pipe and clamp it
securely.
11) With engine “OFF” and ignition switch “ON”, check for fuel
leaks.
FUEL PUMP WITH PRESSURE REGULATOR
ON-VEHICLE INSPECTION
1) Remove filler cap and turn ON ignition switch. Then fuel
pump operating sound should be heard from fuel filler for
about 2 seconds and stop. Be sure to reinstall fuel filler cap
after checking.
If above check result is not satisfactory, advance to “Diag-
nostic Flow Table B-2”. CAUTION:
As fuel feed line is still under high fuel pressure, make
sure to release fuel pressure according to following pro-
cedures.
Place fuel container under joint.
Cover joint with rag and loosen joint nut slowly to
release fuel pressure gradually.
CAUTION:
When fuel filler cap is removed in any procedure, work
must be done in a well-ventilated area, keep away from
any open flames and without smoking.
NOTE:
The fuel pressure regulator is the one body with the fuel
pump assembly so individual inspection of it is impossi-
ble.
1. Fuel filler
2. Ignition switch
Page 644 of 698
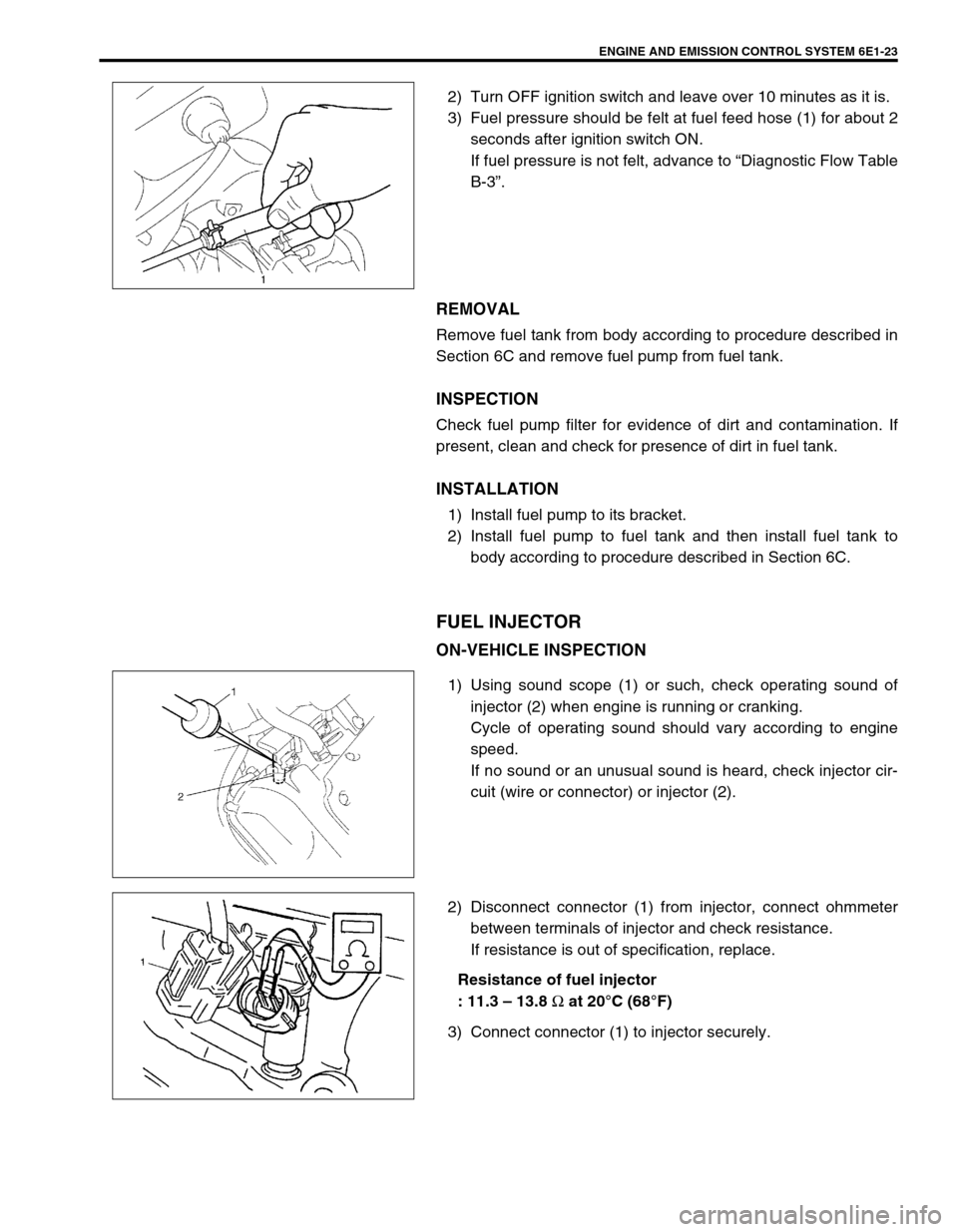
ENGINE AND EMISSION CONTROL SYSTEM 6E1-23
2) Turn OFF ignition switch and leave over 10 minutes as it is.
3) Fuel pressure should be felt at fuel feed hose (1) for about 2
seconds after ignition switch ON.
If fuel pressure is not felt, advance to “Diagnostic Flow Table
B-3”.
REMOVAL
Remove fuel tank from body according to procedure described in
Section 6C and remove fuel pump from fuel tank.
INSPECTION
Check fuel pump filter for evidence of dirt and contamination. If
present, clean and check for presence of dirt in fuel tank.
INSTALLATION
1) Install fuel pump to its bracket.
2) Install fuel pump to fuel tank and then install fuel tank to
body according to procedure described in Section 6C.
FUEL INJECTOR
ON-VEHICLE INSPECTION
1) Using sound scope (1) or such, check operating sound of
injector (2) when engine is running or cranking.
Cycle of operating sound should vary according to engine
speed.
If no sound or an unusual sound is heard, check injector cir-
cuit (wire or connector) or injector (2).
2) Disconnect connector (1) from injector, connect ohmmeter
between terminals of injector and check resistance.
If resistance is out of specification, replace.
Resistance of fuel injector
: 11.3 – 13.8
Ω at 20°C (68°F)
3) Connect connector (1) to injector securely.
Page 645 of 698
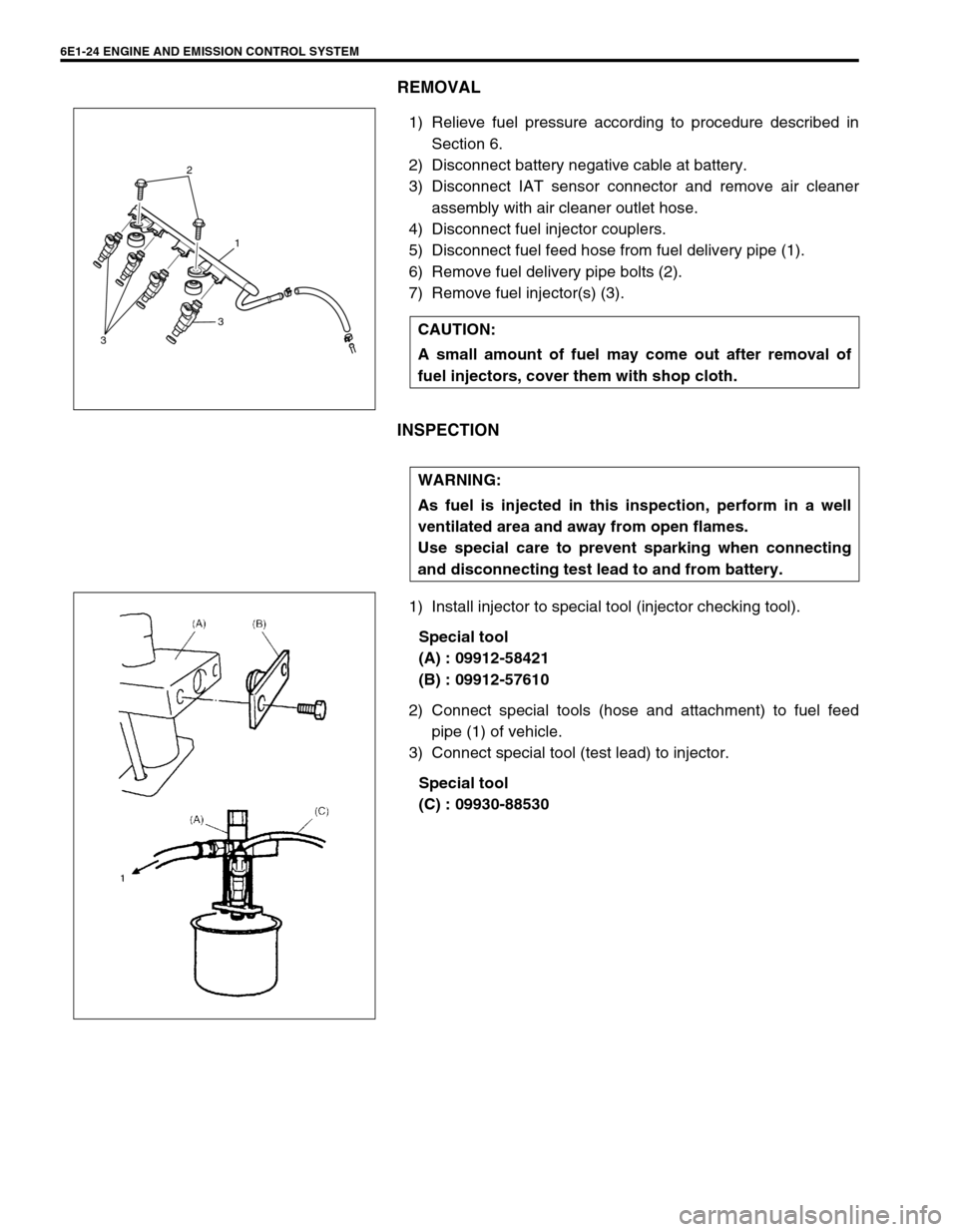
6E1-24 ENGINE AND EMISSION CONTROL SYSTEM
REMOVAL
1) Relieve fuel pressure according to procedure described in
Section 6.
2) Disconnect battery negative cable at battery.
3) Disconnect IAT sensor connector and remove air cleaner
assembly with air cleaner outlet hose.
4) Disconnect fuel injector couplers.
5) Disconnect fuel feed hose from fuel delivery pipe (1).
6) Remove fuel delivery pipe bolts (2).
7) Remove fuel injector(s) (3).
INSPECTION
1) Install injector to special tool (injector checking tool).
Special tool
(A) : 09912-58421
(B) : 09912-57610
2) Connect special tools (hose and attachment) to fuel feed
pipe (1) of vehicle.
3) Connect special tool (test lead) to injector.
Special tool
(C) : 09930-88530 CAUTION:
A small amount of fuel may come out after removal of
fuel injectors, cover them with shop cloth.
2
1
3
3
WARNING:
As fuel is injected in this inspection, perform in a well
ventilated area and away from open flames.
Use special care to prevent sparking when connecting
and disconnecting test lead to and from battery.
Page 646 of 698
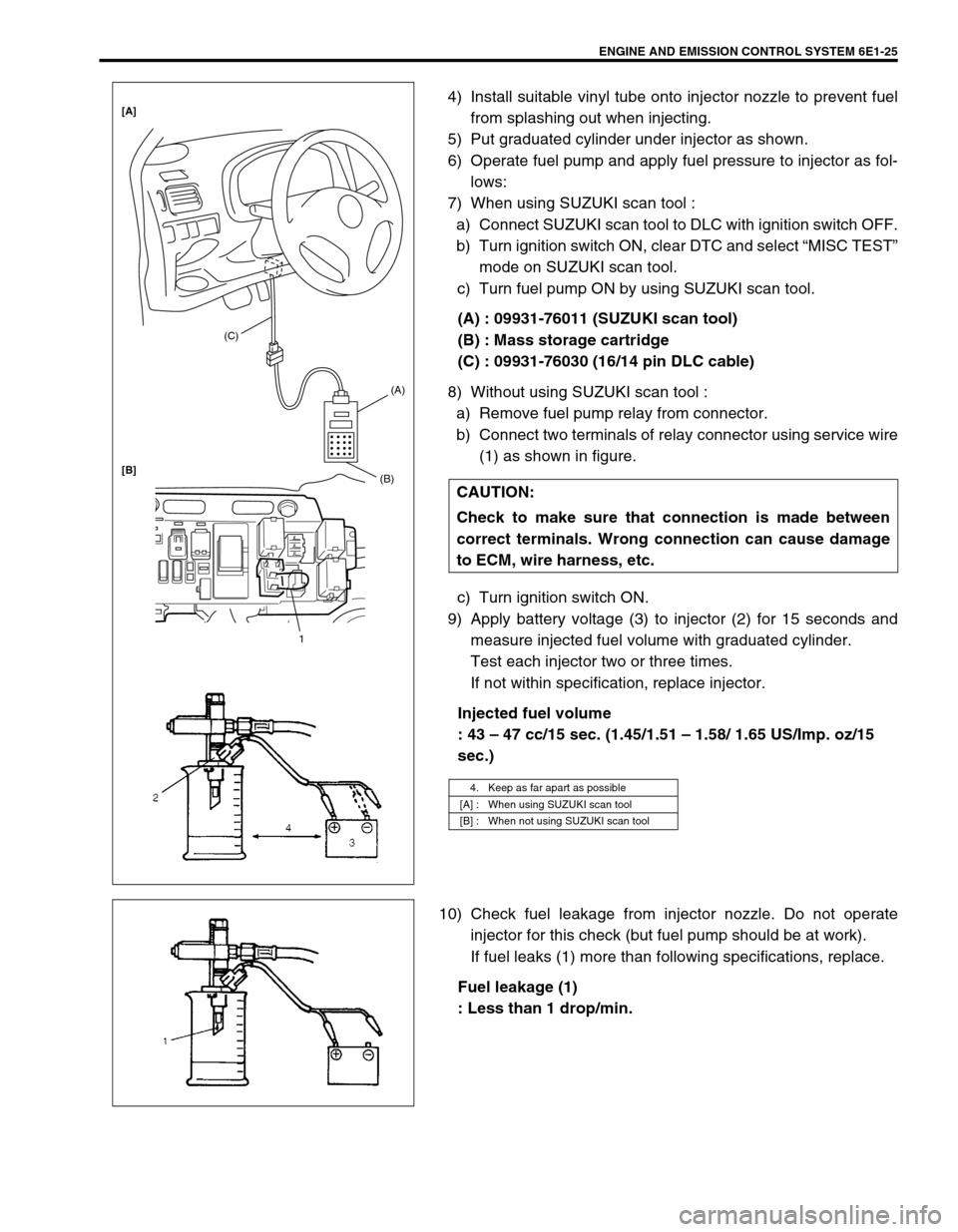
ENGINE AND EMISSION CONTROL SYSTEM 6E1-25
4) Install suitable vinyl tube onto injector nozzle to prevent fuel
from splashing out when injecting.
5) Put graduated cylinder under injector as shown.
6) Operate fuel pump and apply fuel pressure to injector as fol-
lows:
7) When using SUZUKI scan tool :
a) Connect SUZUKI scan tool to DLC with ignition switch OFF.
b) Turn ignition switch ON, clear DTC and select “MISC TEST”
mode on SUZUKI scan tool.
c) Turn fuel pump ON by using SUZUKI scan tool.
(A) : 09931-76011 (SUZUKI scan tool)
(B) : Mass storage cartridge
(C) : 09931-76030 (16/14 pin DLC cable)
8) Without using SUZUKI scan tool :
a) Remove fuel pump relay from connector.
b) Connect two terminals of relay connector using service wire
(1) as shown in figure.
c) Turn ignition switch ON.
9) Apply battery voltage (3) to injector (2) for 15 seconds and
measure injected fuel volume with graduated cylinder.
Test each injector two or three times.
If not within specification, replace injector.
Injected fuel volume
: 43 – 47 cc/15 sec. (1.45/1.51 – 1.58/ 1.65 US/Imp. oz/15
sec.)
10) Check fuel leakage from injector nozzle. Do not operate
injector for this check (but fuel pump should be at work).
If fuel leaks (1) more than following specifications, replace.
Fuel leakage (1)
: Less than 1 drop/min. CAUTION:
Check to make sure that connection is made between
correct terminals. Wrong connection can cause damage
to ECM, wire harness, etc.
4. Keep as far apart as possible
[A] : When using SUZUKI scan tool
[B] : When not using SUZUKI scan tool
(C)
(A)
(B)
1 [A]
[B]
Page 647 of 698
6E1-26 ENGINE AND EMISSION CONTROL SYSTEM
INSTALLATION
For installation, reverse removal procedure and note following
precautions.
Replace injector O-ring (1) with new one using care not to
damage it.
Check if cushion (2) is scored or damaged. If it is, replace
with new one.
Apply thin coat of fuel to O-rings (1) and then install injectors
(3) into delivery pipe (4) and intake manifold.
Make sure that injectors (3) rotate smoothly (6). If not, proba-
ble cause is incorrect installation of O-ring (1). Replace O-
ring (1) with new one.
Tighten delivery pipe bolts (5) and make sure that injectors
(3) rotate smoothly (6).
Tightening torque
Delivery pipe bolts (a) : 28 N·m (2.8 kg-m, 20.5 lb-ft)
After installation, with engine “OFF” and ignition switch “ON”,
check for fuel leaks around fuel line connection.5, (a)
4
1
3 2
Page 654 of 698
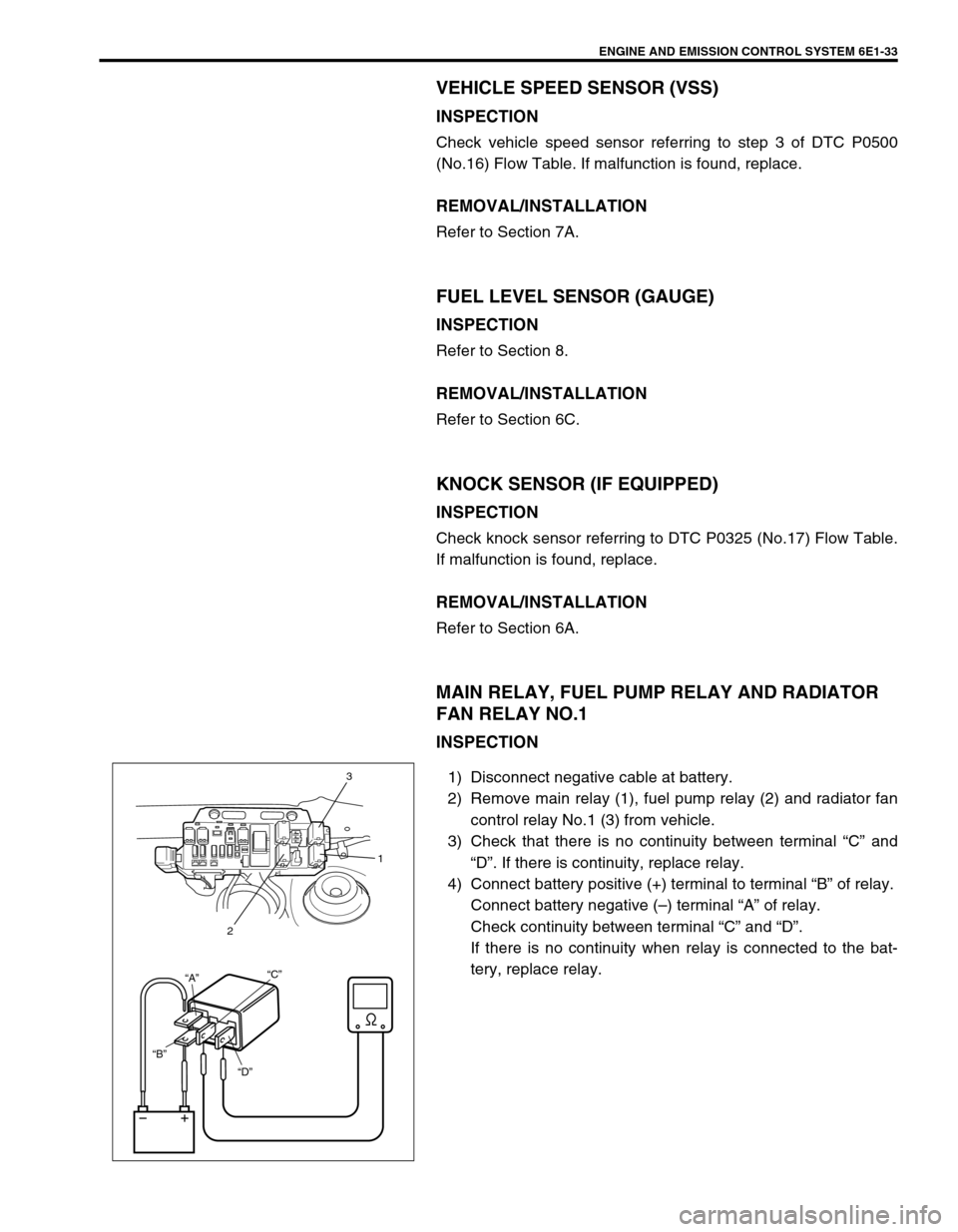
ENGINE AND EMISSION CONTROL SYSTEM 6E1-33
VEHICLE SPEED SENSOR (VSS)
INSPECTION
Check vehicle speed sensor referring to step 3 of DTC P0500
(No.16) Flow Table. If malfunction is found, replace.
REMOVAL/INSTALLATION
Refer to Section 7A.
FUEL LEVEL SENSOR (GAUGE)
INSPECTION
Refer to Section 8.
REMOVAL/INSTALLATION
Refer to Section 6C.
KNOCK SENSOR (IF EQUIPPED)
INSPECTION
Check knock sensor referring to DTC P0325 (No.17) Flow Table.
If malfunction is found, replace.
REMOVAL/INSTALLATION
Refer to Section 6A.
MAIN RELAY, FUEL PUMP RELAY AND RADIATOR
FAN RELAY NO.1
INSPECTION
1) Disconnect negative cable at battery.
2) Remove main relay (1), fuel pump relay (2) and radiator fan
control relay No.1 (3) from vehicle.
3) Check that there is no continuity between terminal “C” and
“D”. If there is continuity, replace relay.
4) Connect battery positive (+) terminal to terminal “B” of relay.
Connect battery negative (–) terminal “A” of relay.
Check continuity between terminal “C” and “D”.
If there is no continuity when relay is connected to the bat-
tery, replace relay.
“D” “B”“A”“C”
3
1
2